Шпала железобетонная Ш-1 (для КБ-65) новая. Жб шпала
Шпалы железобетонные
Шпалы железобетонные - это специальные балочные конструкции, которые применяются при строительстве железнодорожной колеи в качестве опор для рельсов, по которым перемещается типовой подвижной состав с нагрузками и скоростями, установленными для общей сети железных дорог, без ограничения по грузонапряженности. Шпалы обеспечивают неизменность взаимного расположения рельсовых нитей, воспринимают давление, которое исходит от рельсов и проезжающего по ним транспорта, от промежуточных креплений, и передают его на подшпальное основание (в железнодорожном строительстве это, как правило, балластный слой, в метрополитене - бетонное основание).
Первые упоминания о колейных дорогах из рельсов и шпал относятся к середине XVI века. Рельсы представляли собой деревянные брусья и применялись в рудниках и угольных шахтах, по которым перемещались вагонетки. Деревянные брусья быстро изнашивались, что приводило к тому, что повозки, проходящие по рельсам, сходили с пути. Для того чтобы уменьшить износ, деревянные рельсы стали укреплять полосами, которые укладывались поперек колеи. Срок службы деревянных рельсов и шпал, в зависимости от типа древесины, внешних условий и интенсивности эксплуатации, составлял от семи до сорока лет. Несмотря на такие достоинства, как упругость, хорошее сцепление с щебеночным балластом, легкость обработки, существовал главный недостаток - дерево в местах крепления рельсов и шпал просто гнило из-за накапливающейся влаги. Первая железнодорожная колея, выполненная полностью из чугуна, появилась в XVIII веке, в Петрозаводске.
Тем не менее, учитывая развитие железнодорожного транспорта (появление быстроходных составов, увеличивающаяся скорость передвижения), инженеры столкнулись с быстрым износом чугунной колеи. С открытием новых сплавов на основе металла было установлено, что рельсы из стали меньше и равномернее подвергаются износу по сравнению с другими металлами. С тех пор и по настоящее время во всех мире применяются только стальные рельсы. В годы Великой Отечественной войны (1941-1945 гг.) развитие железных дорог было приостановлено. Однако после нее, в ходе выполнения работ по восстановлению железнодорожного транспорта, были предложены нововведения, призванные усилить железнодорожные пути - бесстыковой путь колеи, снижающий удельное сопротивление движению поездов, расходы электроэнергии и топлива, и железобетонные шпалы, срок службы которых достигает порядка 60 - 70 лет. Сегодня, в строительстве железных дорог применяются исключительно железобетонные шпалы.
Какие же есть преимущества у железобетона в качестве материала для изготовления шпал? Во-первых, долговечность железобетона, позволяющая подвергать шпалы длительной эксплуатации. Во-вторых, высокая степень механической прочности, благодаря которой железобетонные шпалы имеют повышенную несущую способность и могут сопротивляться многочисленным и длительным нагрузкам без потерь первоначальных физических свойств. Помимо этого, железобетонные шпалы устойчивы к агрессивным факторам окружающей среды, в том числе - к влаге, гниению. Простота конструкций высокотехнологична - их можно использовать повторно. По сравнению с другими материалами (дерево, металл) шпалы легко справляются с высокой степенью грузонапряженности. Это основные и очевидные причины высокой актуальности железобетона в сфере строительства.
Железнодорожные железобетонные шпалы представляют собой цельнобрусковые балки специального профиля, имеющие переменное сечение. В конструкции шпал предусмотрены специальные площадки, которые позволяют производить монтаж рельсов, а также отверстия для установки крепежных болтов для рельсошпального крепления, что позволяет также использовать промежуточные скрепления железобетонных шпал. В последнее время для скрепления рельсов и шпал все чаще используется анкерное соединение.
Шпалы в зависимости от типа рельсового скрепления подразделяют на:
- тип I - для раздельного клеммно-болтового рельсового скрепления с резьбовым прикреплением рельса и подкладки к шпале;
- тип II - для нераздельного анкерного рельсового скрепления с безрезьбовым прикреплением рельса к шпале;
- тип III - для нераздельного клеммно-болтового рельсового скрепления с резьбовым прикреплением рельса к шпале.
Шпалы железобетонные подразделяются на классы по наличию или отсутствию электроизолирующих характеристик и виду используемой арматуры напрягаемого типа. По электроизолирующим параметрам шпалы железобетонные выпускаются следующих типов:
- изолированными. Предполагается установка специальных вкладышей изолирующего типа, которые называются пустообразователями;
- неизолированными. Наличие вкладышей не предусмотрено.
По применимости в кривых участках железнодорожного пути разного радиуса шпалы всех типов относят к двум видам:
- для прямых и кривых участков железнодорожного пути радиусом 350 м и более;
- для кривых малого радиуса (менее 350 м) и переходных кривых.
Также основными признаками, по которым выполняется классификация изделий, являются степень трещиностойкости, качество, а также точность геометрических параметров данного типа железобетонных изделий. Принято выделять шпалы 1го и 2го сорта. Шпалы из железобетона второго сорта имеют более низкую степень трещиностойкости, меньшие требования к геометрическим параметрам изделия, пониженное качество изготовления, что обуславливает возможность использования только при обустройстве подъездных и внутризаводских железнодорожных путей пятого класса, которые отличаются невысокой степенью нагрузки и интенсивности эксплуатации.
Железобетонные шпалы изготавливаются в соответствии с номами и требованиями, установленными ГОСТ 10629-88 и ГОСТ Р 54747-2011, из тяжелого бетона класса прочности на сжатие не ниже В40 (по ГОСТ 26633). Фактическая прочность бетона (в проектном возрасте, передаточная и отпускная) должна соответствовать требованиям ГОСТ 13015.0. Нормируемую передаточную прочность бетона следует принимать равной 32 МПа (326 кгс/см2). Отпускную прочность бетона принимают равной передаточной прочности бетона. Марка бетона по морозостойкости должна быть не ниже F200. Для бетона шпал следует применять щебень из природного камня или щебень из гравия фракции 5 - 20 мм по ГОСТ 10268. Допускается по согласованию изготовителя с потребителем применять: щебень фракции 20 - 40 мм в количестве не более 10 % от массы щебня фракции 5 - 20 мм по ГОСТ 10268; щебень из природного камня фракции 5 - 25 мм по ГОСТ 7392 при соответствии его всем другим требованиям ГОСТ 10268.
Железобетонные шпалы армируются предварительно напряженной арматурой, для придания дополнительной прочности, необходимой для железнодорожных путей с большими динамическими нагрузками.
Согласно ГОСТ 10629-88 в качестве арматуры шпал применяется стальная проволока периодического профиля класса Вр диаметром 3 мм по ГОСТ 7348 и ТУ 14-4-1471-87. Номинальное число арматурных проволок в шпале - 44. Расположение проволок, контролируемое на торцах шпалы, должно соответствовать проекту. Расстояние по вертикали в свету между парами или отдельными проволоками, в случае их отклонения от проектного положения, не должно быть менее 8 мм. Допускается разворот пар проволок на 90° при сохранении указанного выше расстояния. Для обеспечения проектного расположения проволок могут применяться разделительные проставки, остающиеся в теле бетона шпалы. Допускается по согласованию изготовителя с потребителем применять проставки, отличающиеся от проектных.
Согласно ГОСТ Р 54747-2011 для армирования шпал следует применять: стальную холоднодеформированную проволоку гладкую и периодического профиля диаметром от 3 до 8 мм, не ниже класса прочности В1200; холоднодеформированную арматуру гладкую и периодического профиля диаметром от 8 до 10 мм, не ниже класса прочности 1400К; горячекатаную и термомеханически упрочненную гладкую арматуру и периодического профиля диаметром от 8 до 10 мм, не ниже класса прочности А1200К; арматурные канаты диаметром от 6 до 14 мм, не ниже класса прочности К1500К. Гладкая арматура может применяться только с концевыми анкерами. Диаметр и класс прочности арматуры, число и расположение арматурных элементов, отклонения от номинального числа арматурных элементов и величина начального натяжения всей арматуры должны быть указаны в технической документации на изделие. Допускается по согласованию с заказчиком применять другие виды арматуры.
Шпалы обозначают марками в соответствии с требованиями ГОСТ 23009. Марка шпалы состоит из двух буквенно-цифровых групп, разделенных тире. Первая группа содержит обозначение типа шпалы. Во второй группе указывают вариант исполнения подрельсовой площадки.
www.block-gbi.ru
Железобетонная шпала
Изобретение относится к верхнему строению железнодорожного пути и предназначено для обеспечения скоростного движения пассажирских и грузовых поездов. Железобетонная шпала выполнена в виде армированного бруса с переменным подлине поперечным сечением. Шпала имеет концевые участки (1), участки (2) для крепления рельсов и участки (3) сопряжения со средним участком (4), имеющим ширину меньше ширины других участков. Средний участок (4) в поперечном сечении выполнен в виде трапеции, а участки (2) для крепления рельсов выполнены с сопряженными между собой наклоненными к горизонтали гранями (5) и (6). Гранями (5) образованы грани соответствующих концевых участков (1), а участки (3) сопряжения со средним участком (4) выполнены с наклоненными к горизонтали гранями (7) и (8). Грани (7) участков (3) сопряжены с гранями (6) участков (2) для крепления рельсов. Достигается снижение материалоемкости железобетонной шпалы и повышение ее эксплуатационных характеристик. 5 з.п. ф-лы, 15 ил.
Изобретение относится к верхнему строению железнодорожного пути и предназначено для обеспечения скоростного движения пассажирских и грузовых поездов.
Известна железобетонная шпала, содержащая концевые участки, участки для крепления рельсов и участки сопряжения со средним участком, имеющим ширину меньше ширины других участков (см. патент №2293810 от 20.02.2007).
Недостатком известной железобетонной шпалы является повышенная материалоемкость, обусловленная наличием верхней трапеции по всей длине шпалы.
Технический результат, на достижение которого направлено изобретение, заключается в уменьшении материалоемкости железобетонной шпалы и повышении ее эксплуатационных характеристик:
- осевые нагрузки 4-х осных грузовых вагонов до 400 кН;
- скорости движения пассажирских поездов не менее 350 км/ч;
- скорости движения грузовых поездов не менее 120 км/ч. Указанный технический результат достигается тем, что в железобетонной шпале, содержащей концевые участки, участки для крепления рельсов и участки сопряжения со средним участком, имеющим ширину меньше ширины других участков, средний участок в поперечном сечении выполнен в виде трапеции, а участки для крепления рельсов выполнены с сопряженными между собой наклоненными к горизонтали гранями, одними из которых образованы грани соответствующих концевых участков, при этом участки сопряжения со средним участком выполнены с наклоненными к горизонтали гранями, одни из которых сопряжены с другими гранями участков для крепления рельсов.
Все грани для оптимизации прочностных характеристик и объема бетона, необходимого для изготовления шпалы имеют разный угол наклона к горизонтали.
Концевые участки выполнены с наклоненными к горизонтали расширяющимися к торцам площадками, сопряженными с торцами и с верхними поверхностями участков для крепления рельсов или с их крайними выступами.
В одном варианте торцы выполнены с наклоненными к горизонтали поверхностями, средняя из которых выполнена в виде трапеции, а крайние - в виде фасок треугольной формы.
Во втором варианте торцы выполнены вогнутыми и образованы наклоненными к горизонтали поверхностями в виде трапеций, при этом меньшие основания крайних поверхностей сопряжены с соответствующими сторонами средней поверхности.
В третьем варианте торцы выполнены в виде расположенной в вертикальной плоскости трапеции.
Конструкция шпалы обеспечивает возможность установки закладных элементов для различных конструкций промежуточных рельсовых скреплений.
Сущность изобретения поясняется чертежами.
На фиг.1 показана железобетонная шпала по первому варианту, вид сбоку; на фиг.2 - то же, вид сверху; на фиг.3 - вид А на фиг.1; на фиг.4 сечение Б-Б на фиг.1; на фиг.5 - сечение В-В на фиг.1; на фиг.6 показана железобетонная шпала по второму варианту, вид сбоку; на фиг.7 - то же, вид сверху; на фиг.8 - вид А на фиг.6; на фиг.9 сечение Б-Б на фиг.6; на фиг.10 - сечение В-В на фиг.6; на фиг.11 показана железобетонная шпала по третьему варианту, вид сбоку; на фиг.12 - то же, вид сверху; на фиг.13 - вид А на фиг.11; на фиг.14 сечение Б-Б на фиг.11; на фиг.15 - сечение В-В на фиг.11.
Железобетонная шпала выполнена в виде армированного бруса с переменным подлине поперечным сечением. Шпала имеет концевые участки 1, участки 2 для крепления рельсов и участки 3 сопряжения со средним участком 4, имеющим ширину меньше ширины других участков.
Средний участок 4 в поперечном сечении выполнен в виде трапеции, а участки 2 для крепления рельсов выполнены с сопряженными между собой наклоненными к горизонтали гранями 5 и 6. Гранями 5 образованы грани соответствующих концевых участков 1, а участки 3 сопряжения со средним участком 4 выполнены с наклоненными к горизонтали гранями 7 и 8. Грани 7 участков 3 сопряжены с гранями 6 участков 2 для крепления рельсов.
Концевые участки 1 выполнены с наклоненными к горизонтали расширяющимися к торцам площадками 9, сопряженными в одном из вариантов выполнения с крайними выступами 10 участков 2 для крепления рельсов и с наклоненными к горизонтали поверхностями 11 и 12 торцов. Средняя поверхность 11 выполнена в виде трапеции, а крайние поверхности 12 - в виде фасок треугольной формы.
Во втором варианте торцы выполнены вогнутыми и образованы наклоненными к горизонтали поверхностями в виде трапеций, при этом меньшие основания крайних поверхностей 13 сопряжены с соответствующими сторонами средней поверхности 14.
В третьем варианте торцы выполнены в виде расположенной в вертикальной плоскости трапеции 15.
Во втором и третьем вариантах площадки 9 сопряжены с верхними поверхностями 16 участков 2 для крепления рельсов, выступы на которых образованы соответственно углублениями 17 и закладными элементами 18.
Все грани для оптимизации прочностных характеристик и объема бетона, необходимого для изготовления шпалы имеют разный угол наклона к горизонтали. Например, боковые грани 19 среднего участка 4 наклонены к горизонтали под углом 78,69° или 78,37°, а грани 5 и 6 участка 2 имеют соответственно наклон 75° и 70,67° или 74,29° и 70,74°. В первом варианте шпалы поверхности 11 и 12 ограничены боковыми сторонами, соответственно расположенными к вертикали под углом 80,04°и 75.° Во втором варианте большие основания соответствующих крайних поверхностей торцов наклонены к вертикали под углом 74,29°, при этом в третьем варианте под указанным углом наклонены к вертикали боковые стороны трапеции 15.
Основные преимущества новой шпалы заключаются в следующем:
1 Возможность изготовления в длинных и коротких формах;
2 Возможность применения универсальных форм;
3 Изготовление шпалы возможно по технологии с постняжением и преднатяжением арматуры по малопрогревной или беспропарочной технологии с применением добавок и снижением времени тепловой обработки.
4 Повышение сопротивления сдвигу в балласте в поперечном к оси пути направлении за счет увеличения высоты торца, площади опорной поверхности, выраженного сопряжения уступом со средним сечением;
5 Изменение размеров поперечного сечения шпалы в подрельсовом и среднем сечениях дает возможность менять армирование с увеличением количества арматурных стержней (проволок) и их расположением для повышения трещиностойкости и выносливости шпал.
7 Возможность использования шпал на участках с повышенными осевыми нагрузками и высокой грузонапряженностью.
Технология укладки и эксплуатация шпал новой конструкции не имеет отличий от существующих технологий.
8 зависимости от типа скрепления при изготовлении шпалы используются типовые закладные элементы, свои для каждого крепления, изготавливаемые в соответствии с техническими условиями.
Шпалы имеют увеличенный срок службы в среднесетевых условиях эксплуатации за счет обеспечения улучшенных показателей механической прочности и трещиностойкости.
1. Железобетонная шпала, содержащая концевые участки, участки для крепления рельсов и участки сопряжения со средним участком, имеющим ширину меньше ширины других участков, отличающаяся тем, что средний участок в поперечном сечении выполнен в виде трапеции, а участки для крепления рельсов выполнены с сопряженными между собой наклоненными к горизонтали гранями, одними из которых образованы грани соответствующих концевых участков, при этом участки сопряжения со средним участком выполнены с наклоненными к горизонтали гранями, одни из которых сопряжены с другими гранями участков для крепления рельсов.
2. Железобетонная шпала по п.1, отличающаяся тем, что все грани имеют разный угол наклона к горизонтали.
3. Железобетонная шпала по п.1 или 2, отличающаяся тем, что концевые участки выполнены с наклоненными к горизонтали расширяющимися к торцам площадками, сопряженными с торцами и с верхними поверхностями участков для крепления рельсов или с их крайними выступами.
4. Железобетонная шпала по п.3, отличающаяся тем, что торцы выполнены с наклоненными к горизонтали поверхностями, средняя из которых выполнена в виде трапеции, а крайние - в виде фасок треугольной формы.
5. Железобетонная шпала по п.3, отличающаяся тем, что торцы выполнены вогнутыми и образованы наклоненными к горизонтали поверхностями в виде трапеций, при этом меньшие основания крайних поверхностей сопряжены с соответствующими сторонами средней поверхности.
6. Железобетонная шпала по п.3, отличающаяся тем, что торцы выполнены в виде расположенной в вертикальной плоскости трапеции.
www.findpatent.ru
Шпалы железобетонные, бетонные шпалы, прайс на железобетонные шпалы ГОСТ 10629-88 – РемСтройПуть
шт | по запросу | ![]() | ||
шт | по запросу | ![]() |
Шпала железобетонная, выполненная из высокотехнологичного армированного материала, уверенно вытесняет традиционные деревянные изделия. Это связано с простотой монтажа и обслуживания, долговечностью и прочностью этого типа шпал.
Ж/б шпалы Ш-1: прочность и долговечность железнодорожного пути
В процессе строительства, реконструкции или ремонта железнодорожного пути железобетонные шпалы укладываются на балластный верхний слой пути (подушку из гравия/щебня). Выполненная в соответствии со стандартами шпала ш1 принимает давление от рельсов и/или промежуточных скреплений, передает его на балластный слой или подшпальное соединение, обеспечивая тем самым неизменность расположения рельсовой нити.
На всех этапах работ в сфере обслуживания железнодорожного пути неизменной популярностью пользуются шпалы ш 1 — железобетонные изделия, выполненные из тяжелых марок бетона и дополнительно армированные стальной проволокой. Шпала является основным элементом для обустройства железнодорожных путей с шириной рельсовой нити до 1520 мм.
В зависимости от прочности, трещиностойкости, качества бетона и геометрических параметров выделяется жб шпала 1 и 2 сорта. Изделия 2 сорта применяются для обустройства станционных, малодеятельных и подъездных путей, а изделия 1 сорта актуальны при обустройстве путей с повышенной проходимостью.
Если сравнивать бетонные шпалы с деревянными аналогами, то ж/б изделия значительно выигрывают по техническим и эксплуатационным параметрам: прочность, морозостойкость, простота обслуживания и длительный период эксплуатации (не менее 50 лет).
Все жб шпалы, представленные в каталоге компании «Ремстройпуть», выполнены в полном соответствии с ГОСТ 10629-88 и отраслевыми стандартами. Каждая партия шпал из прочного железобетона сертифицирована для продажи и эксплуатации на территории РФ, стран СНГ и Таможенного Союза.
Стоимость, варианты и сроки оплаты, способ доставки — это индивидуальные предложения для каждого заказчика: самовывоз с территории складов компании или доставка любым типом транспорта, наличный/безналичный расчет и скидки для крпунооптовых покупателей.
Заказать железобетонные шпалы можно в офисе компании "Ремстройпуть" (г. Екатеринбург, ул. Таганская, д. 55 а, 3 этаж). Наши менеджеры готовы предоставить качественную консультацию при выборе шпал по телефону (343) 228-34-34, а также по электронной почте - [email protected].
Шпалы Ш 1-1 (угол наклона упорных кромок подрельсовых площадок в шпалах 55º) | применяется для раздельного клеммно - болтового скрепления КБ с болтовым прикреплением подкладки к шпале | ГОСТ 10629-88 | ![]() |
Шпалы Ш 1-2 (угол наклона упорных кромок подрельсовых площадок в шпалах 72º) | применяется для раздельного клеммно - болтового скрепления КБ с болтовым прикреплением подкладки к шпале | ГОСТ 10629-88 | ![]() |
Шпалы Ш 2-1 | применяется для нераздельного клеммно-болтового рельсового скрепления БПУ с болтовым прикреплением подкладки или рельса к шпале | ГОСТ 10629-88 | ![]() |
Шпалы Ш 3 | применяется для нераздельного клеммно-болтового скрепления ЖБР65 с болтовым прикреплением рельса к шпале | ГОСТ 10629-88 | ![]() |
Шпалы ШС-АРС | применяется для анкерного рельсового скрепления | ![]() | |
Расположение арматурных элементов в железобетонных шпалах: | |||
Шпалы Ш 1-16*5 | шпалы с высокопрочной проволочной арматурой периодического профиля диаметром от 3 до 5 мм | ГОСТ 10629-88 | ![]() |
Шпалы Ш 1-4*10 | шпалы с высокопрочной стержневой арматурой периодического профиля диаметром стержней от 7 до 12 мм | ГОСТ 10629-88 | ![]() |
Классификация дефектов железобетонных шпал:
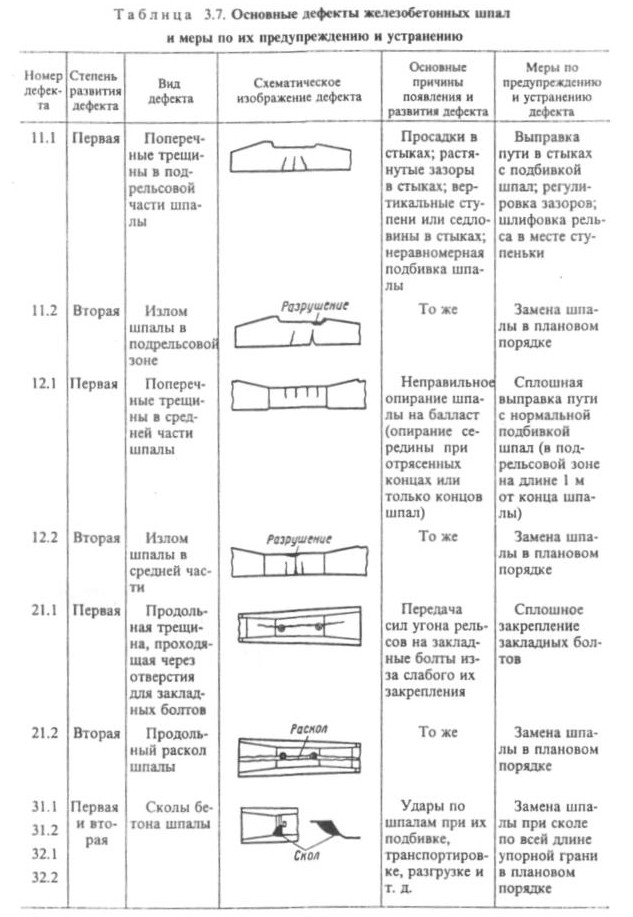
Требования к старогодным железобетонным шпалам приведены в табл. 3.8
Таблица 3.8
первой | второй | |
Тип рельсовых промежуточных скреплений | КБ | Всех типов |
Пропущенный по шпале тоннаж и срок ее службы с момента первой укладки | Без ограничений | Без ограничений |
Поперечные трещины в бетоне | Не допускаются | Наибольшее раскрытие трещин до 1 мм без разрушения бетона |
Продольные трещины в бетоне | Не допускаются | Наибольшее раскрытие трещин до 3 мм без разрушения бетона |
Отколы бетона: | ||
на кромках подрельсовых площадок | Допускается длиной не более 30 мм и глубиной не более 10 мм | Допускается длиной не более 100 мм и глубиной не более 30 мм |
на прочих кромках шпалы | Допускается длиной не более 100 мм и глубиной не более 30 мм без обнажения арматуры | Допускается длиной не более 300 мм и глубиной не более 60 мм |
рабочих кромок в отверстиях для закладных болтов | Не допускаются | Допускается |
Непрямолинейность подрельсовой площадки | Не более 1мм | Не более 5мм |
Толщина закладной шайбы в месте контакта с головкой закладного болта | Не менее 4мм | Не менее 2мм |
Продажа шпал - ЗАО "Ремстройпуть" +7(343) 228-34-34
www.rails.ru
Шпала железобетонная Ш-1 (для КБ-65) новая
Шпалы железобетонные Ш1 новые | 2 100 |
Расстояние между упорными кромками разных концов шпалы, мм | 2016 |
Угол наклона упорных кромок, ° | 55 |
Высота подрельсового сечения шпалы, мм | 193 |
Высота среднего сечения шпалы, мм | 145 |
Марка бетона по морозостойкости, не менее | F200 |
Тип скреплений | КБ-65 |
Чертеж:

Шпала жб для скреплений КБ-65, под закладной болт новая без скреплений.
Железобетонные шпалы Ш1 предназначены для путей с номинальной шириной рельсовой колеи 1520 мм, по которым обращается типовой подвижной состав с осевыми нагрузками и скоростями, установленными для общей сети железных дорог Российской Федерации. На шпалах предусмотрено применение рельсов типа Р75, Р65 и Р50 и рельсовых скреплений типа КБ.
Главное отличие шпалы железобетонные Ш-1-1, от деревянных, это то, что первые имеют существенно больший срок службы - от 30 до 60 лет. Изготавливаются железобетонные шпалы из напряженного железобетона, когда стальная арматура растягивается и, в таком состоянии, ее заливают бетоном. Благодаря такому способу производства, прочность шпал значительно увеличивается.
При производстве шпалы Ш-1-1 производители используют тяжелый бетон класса прочности на сжатие В40 (М500).
Данный вид железнодорожных железобетонных шпал необходим при укладки путей любой категории. Используют скрепление для данного вида шпал – раздельное клеммно–болтовое (КБ).
В состав изделия на одну шпалу входит:
- подкладки,
- болт клеммный с клеммой, двухвитковым гровером и гайкой,
- болт закладной с изоляцией, металлической скобой, гровером и гайкой,
- нашпальная резина,
- подрельсовый амортизатор.
При эксплуатации железобетонных шпал необходимо постоянное внимание, особенно в местах разжижения балласта, а так же в стыках, где повышенные динамические нагрузки, т.к. невнимательность может привести к излому шпалы.
Железобетонные шпалы с раздельным КБ скреплением стабильно удерживают шаблон как в прямых, так и кривых участках, не требуют особых затрат при регулировке пути по уровню и шаблону во время производства ремонтных работ.
www.vsp74.ru
Железобетонная шпала
Изобретение относится к верхнему строению железнодорожного пути, в частности к железобетонным шпалам, используемым преимущественно в бесстыковом пути. Цельнобрусковая железобетонная шпала предварительно напряженная содержит зубцы на выступах в подрельсовых зонах, при этом зубцы расположены симметрично относительно поперечной оси ложа шпалы. Достигается повышение фиксации шпалы в балластной призме. 5 ил.
Изобретение относится к конструкции рельсовых опор и может быть применено в конструкции шпал, в основном железобетонных, применяемых в верхнем строении железнодорожного пути, преимущественно бесстыкового.
Общеизвестна конструкция цельнобрусковой, предварительно напряженной, струнобетонной железобетонной шпалы, в которой нижняя постель плоская или в своей средней части она имеет выемку Название «струнобетонная» означает применение в рельсовых опорах не только проволочной арматуры, но также и арматуры стержневого типа.
Железобетонная шпала должна обладать высокой надежностью и долговечностью. Срок ее использования должен составлять 40-50 лет. Основным дефектом, ограничивающим срок эксплуатации рельсовых опор, является появление и развитие трещин в средней зоне, так как именно верх центральной части испытывает максимальные изгибающие моменты.
Железобетонные шпалы имеют переменное (по длине) поперечное сечение с относительно малой жесткостью в средней части по сравнению с подрельсовыми участками. Это позволяет уменьшить изгибающие моменты в междурельсовой зоне шпал, именно которая и испытывает максимальные нагрузки. Поэтому в 50-е годы прошлого века для исключения наиболее опасного из вариантов контакта со щебнем, а именно опирания шпалы на балласт своей средней частью, этот участок в конструкции рельсовой опоры специально подняли над поверхностью щебня на 10 мм, уменьшив ее высоту в этой зоне со 145 до 135 мм. Это позволило избежать или, по крайней мере, значительно ослабить растягивающие напряжения верха центральной зоны железобетонной шпалы. Для снижения давления на балласт ширина подошвы шпал у торцов была существенно увеличена - до 305 мм. В средней же части этот параметр меньше и равен 255 мм. Максимальная высота в подрельсовой зоне значительно выше, чем в центре шпалы, и составляет 229 мм. Эти изменения конструкции позволили сделать рельсовую опору высоконадежной и обеспечивающей работоспособность между капитальными ремонтами пути. В дальнейшем, после замены ГОСТ 10629-78 на ГОСТ 10629-88, габариты железобетонных шпал претерпели очень незначительные изменения.
Второй важной функцией рельсовых опор является способность оказывать сопротивление силам, вызывающим отклонение пути от проектного положения. То есть шпала должна хорошо фиксироваться в балласте и обладать значительным усилием сдвига. В противном случае всегда есть вероятность угона и выброса рельсошпальной решетки. Это особенно стало важным и необходимым после перехода на бесстыковую конструкцию пути.
В этом варианте верхнего строения железной дороги имеются очень важные особенности в поведении рельсовой плети при повышении температуры. Возникающие в ней продольные силы могут достигать 160 т. С учетом того, что шпальная решетка содержит два рельса, общее, суммарное значение усилий от их нагрева возрастает до 320 тс.
Кроме того, к этим продольным сжимающим рельсы температурным силам может добавиться и усилие от экстренного торможения поезда величиной до 70 тс и боковая сила от колесных пар, достигающая на прямых участках пути значений 6 тс, а в кривых 16 тс.
Поэтому для обеспечения устойчивости бесстыковой конструкции рельсошпальной решетки крайне необходимо значительное, принципиальное повышение усилия сдвига железобетонных шпал в балластной призме верхнего строения пути.
Для решения этой проблемы в соответствии с RU 2433218 С2 предложено выполнить выступ высотой 28 мм в средней части рельсовой опоры ее нижней постели.
Сделаем оценку эффективности этого технического решения. Если принять, что торец рельсовой опоры полностью засыпан щебнем, то эта минимальная величина заглубления составит 150 мм. Очевидно, что создание выступа увеличивает площадь поперечного сечения тела шпалы. Поэтому в этой конструкции к усилию сдвига балласта торцами рельсовой опоры необходимо добавить и усилие сдвига балласта за счет выступа. Его значение при равных значениях ширины со шпалой определяется отношением высоты выступа к стандартной величине заглубления рельсовой опоры в балласт. Таким образом, ожидаемое увеличение усилия поперечному сдвигу пути шпалой с выступом 28 мм и заглубление рельсовой опоры в балласт на 150 мм составит: (28:150)×100=18,7%.
В книге «Новые путевые машины», М., «Транспорт» 1984 г., стр. 192 под редакцией к.т.н. Ю.П. Сырейщикова на стр. 192 приведена формула по усилию сдвига Рс рельсошпальной решетки. В соответствии с ней Рс увеличивается в квадратичной зависимости от величины заглубления. Приняв это обстоятельство, в конечном итоге получим, что для шпалы, заглубленной на 150 мм и с выступом в средней части 28 мм, увеличение усилия поперечному сдвигу может составить лишь [(150+28):150]2×100%-100%=40%. Этого явно недостаточно для гарантированного исключения угона или выброса железнодорожного пути и недопустимости возникновения аварийной ситуации.
Кроме того, наличие выступа средней части рельсовой опоры требует при укладке рельсошпальной решетки на балластную призму верхнего строения пути создания ответного углубления, соответствующего по размерам высоте и длине выступа. Сделать это на щебне фракции 25-60 мм, зерна которого по размерам значительно превышают нужную величину углубления в 28 мм на поверхности балластной призмы, а тем более и на криволинейном участке пути, крайне затруднительно. Это приведет и к удорожанию строительства балластной призмы. Кроме того, наличие выступа предопределяет нежелательное и способствующее появлению дефектов опирание шпалы на щебень своей средней частью. Это означает существенное увеличение растягивающих напряжений и повышение вероятности появления трещин в верхней части центральной зоны рельсовой опоры и приведет к снижению ее долговечности, надежности и потребует значительного усиления, удорожания арматуры, воспринимающей значительно увеличившиеся изгибающие моменты.
Другой, близкой по конструкции рельсовой опорой является железобетонная шпала по SU 1772284 А1, имеющая выступ в подрельсовых зонах. Принимаем это техническое решение за прототип.
Целью предлагаемого изобретения является значительное увеличение силы сопротивления смещению шпалы в балласте и повышение надежности и трещиноустойчивости рельсовой опоры благодаря снижению изгибающих усилий в подрельсовой зоне, а также и в средней части.
Указанная цель достигается тем, что выступ содержит зубцы. Это позволяет значительно увеличить эффективность шпалы по ее сопротивлению перемещения в балласте верхнего строения пути и значительно уменьшить растягивающие кромочные напряжения по подошве и верхней части.
Осаживание, внедрение в балласт зубатой рельсовой опоры существенно облегчается.
На Фиг. 1 показана конструкция стандартной рельсовой опоры. При ремонтных работах верхнего строения пути производят выправку рельсошпальной решетки. Рассмотрим этот процесс при работе путевых машин, например, типа ВПР и Duomatig, имеющих подбивочные блоки с вертикально расположенными подбойками. При рабочем цикле происходит их заглубление в балласт. Лопатки подбоек опускаются в щебень под нижнюю поверхность шпалы и двигаясь к рельсовой опоре начинают обжимать балласт. При этом подбивка происходит только в участках, прилегающих к подрельсовой зоне подошвы. Середина не подбивается. В противном случае произойдет опасное опирание шпалы на балласт центральной частью, возникнет максимальный изгибающий момент и тогда неизбежно появление трещин в верхней средней части рельсовой опоры. В этом случае наибольшие напряжения возникают потому, что плечо действия силы Р1 и Р2 от колесной пары поезда получается максимально возможным и равным L=0,8 м. L - расстояние от продольной оси железнодорожного пути до середины головки рельса. Суммарное значение Р1+Р2=Р определяется допустимой статической нагрузкой на колпару, ее динамической составляющей при движении, ударным действием ползунов колесных пар, рельсовых стыков и составляет около 40 тс. Огромное усилие и максимально возможное плечо его действия предопределяет появление опасных напряжений в конструкции железобетонной шпалы при ее опирании на балласт своей средней частью.
Необходимо отметить, что и подрельсовая зона шпалы, в своей средней части, а именно по подошве, также испытывает растягивающие напряжения. Объясняется это тем, что лопатки подбоек путевых машин конструктивно не заходят внутрь подрельсовой зоны, а могут располагаться только справа и слева от нее. Поэтому при подъемке пути и при обжиме балласта рабочими органами подбивочного блока щебенки перемещаются из шпального ящика под подошву рельсовой опоры только в зоне расположения лопаток подбоек, то есть с торца до подрельсовой зоны и между подрельсовой зоной и средней частью шпалы. Следствием подъемки пути (обычно величина подъема 40-60 мм), локального размещения подбоек и перемещения ими щебенок не под всю подошву шпалы оказывается то, что рельсовая опора фактически опирается на четыре бугра 1…4. В подрельсовых же зонах и под средней частью рельсовой опоры образуются впадины 5…7, где балласта нет или его мало и он слабо уплотнен.
Причем углубления 5 и 7 расположены симметрично относительно действия сил Р1 и Р2. Очевидно, что нагрузка на шпалу от колесных пар величиной до 40 тс будет изгибать рельсовую опору вниз, в зону впадин 5 и 7. Именно в них вначале и образуются растягивающие напряжения. При проходе вагонов, под действием поездной нагрузки бугры сминаются, рельсошпальная решетка осаживается и глубина впадин уменьшается. Именно поэтому с течением времени впадина 6 постепенно заполняется щебенками и возникает опирание шпалы своей серединой на балласт. От этого возникают максимальные изгибные моменты в ее средней части.
Для исключения опасных напряжений в подрельсовой зоне и в центре рельсовой опоры новой конструкции (см. Фиг. 2) предназначены зубатые выступы 8, которыми предлагаемая шпала отличается от общеизвестной, стандартной и от принятой за прототип. Благодаря им незатекание, непопадание щебенок в подрельсовые зоны при подбивке пути не отражается негативно на шпалу, не приводит к появлению изгибающих моментов по подошве опоры в подрельсовой зоне и в верху ее средней части. Объясняется это тем, что шпала на балласт теперь опирается зубатыми выступами 8, а впадины 5 и 7 исчезли, самоликвидировались. Зубатые выступы 8 расположены по центру подрельсовых зон и, следовательно, соосно с нагрузкой, с направлением действия сил Р1 и Р2 от действия колесных пар. Так как плечо действия сил Р1 и Р2 становится равным 0, то и изгибающие моменты в подрельсовых зонах исчезают. В свою очередь, отсутствие выступа в средней части шпалы при проведении выправки пути и подъемке, например, на 50 мм и наличие зубатых выступов 8 приводит к появлению зазора (появлению увеличенной по сравнению с Фиг. 1 впадины 6) между балластом и этой зоной шпалы. То есть наличие углубления 6 означает отсутствие опирания центральной части рельсовой опоры. Следовательно, нет и изгибающего момента и в средней части шпалы.
Таким образом, введение зубатых выступов 8 на подошве, симметрично и соосно расположенных относительно оси действия сил Р1 и Р2, симметрично и соосно относительно колесной нагрузки, симметрично поперечной оси подрельсового участка, симметрично ложу для установки подошвы рельса позволяет теоретически полностью исключить появление опасных напряжений в любой зоне и участке опоры новой конструкции, а практически помогает значительно их уменьшить, тем самым обеспечить высокую надежность, долговечность и работоспособность предлагаемой шпалы. На выступах расположены зубцы 9. Их оптимальное количество 10 штук на шпалу.
Некоторые варианты исполнения выступов, их формы и зубцов показаны на Фиг. 3, Фиг. 4, Фиг. 5.
Можно использовать предлагаемое изменение конструкции не только при изготовлении рельсовых опор, но, и это особенно ценно, для модернизации шпал, бывших в употреблении. При этом возможно самозалечивание неопасных мелких трещин в теле старогодной шпалы при заливке ее нижней постели высокопрочным бетоном для получения создаваемых выступов. Нужно отметить, что есть решения, позволяющие при необходимости создать и предварительное напряжение в добавляемом цементном слое.
Известно, что срок службы железобетонных рельсовых опор составляет 40-50 лет. Капитальный ремонт шпальной решетки (со сменой рельсов) производят через 18-25 лет. При этом одновременно с заменой рельсов приходится заменять и рельсовые опоры, которые выработали свой ресурс всего на 50%. Изобретение позволяет модернизировать демонтированные при капитальном ремонте пути шпалы с целью придания им повышенной устойчивости за счет увеличения усилия сдвига в балласте в 3-5 раз и «залечивания» имеющихся дефектов в виде мелких трещин.
Доработка заключается в получении «зубатого» выступа на подошве в подрельсовой зоне, который можно изготовить с помощью дополнительной пресс-формы, имеющей на своей рабочей поверхности соответствующие углубления.
Выбор оптимальных размеров предлагаемого местного утолщения шпалы зависит от многих факторов: величины подъемки пути выправочно-подбивочно-рихтовочной машиной, зазора между крайней лопаткой подбивочного блока и подрельсовой зоной, величиной заглубления подбойки в щебень, степенью загрязнения балласта и некоторыми другими.
На практике, рационально выбрать выступ, по ширине примерно равный размеру подошвы наиболее применяемого рельса P65, то есть 150 мм. Длину выступа лучше выполнить равной ширине стандартной шпалы, то есть 300 мм. Высоту принять равной средней величине подъемки при текущем содержании пути, то есть 50 мм. Зубцы необязательно размещать на нижней поверхности выступа. Он сам по себе является «зубом» шпалы и существенно увеличивает ее усилие сдвига в балласте. Кроме того, дополнительные зубья могут быть размещены и на других частях нижней, торцевой или боковой поверхности рельсовой опоры. Нижняя, то есть со стороны щебня, поверхность выступа может быть расположена, как вариант, и параллельно поверхности ложа шпалы для установки подошвы рельса, то есть параллельно подрельсовой части, то есть с уклоном 1:20. В общем случае, предлагаемое изобретение эффективно также для двухшарнирных трехблочных шпал и двухблочных с металлической соединительной поперечиной. Выступ может иметь и форму клина.
Зубцы нижней поверхности выступа в поперечном сечении имеют произвольную форму с эквивалентным диаметром от 5 до 150 мм, расположены друг от друга с зазором от 0 до 50 мм и имеют высоту от 10 до 100 мм. Размещение зубцов по подошве может быть как в шахматном порядке, так и произвольным, хаотичным, или упорядоченным с заданным шагом и интервалом по выбранному направлению. Высота зубцов может быть одинаковой или разной, вычисляемой по определенному закону или быть функцией случайной величины в диапазоне от 10 до 100 мм.
Целесообразно использовать предлагаемое техническое решение совместно с изобретением RU 2378444 C2, которое предполагает принудительное осаживание пути вертикальной силой 35-100 тс во время рабочего цикла выправки. Это позволит полностью вдавить выступы на подошве 10 шпалы в балласт 11 верхнего строения железнодорожного пути, исключить появление впадин 5 и 7 и гарантированно обеспечить такое дополнительное уплотнение щебня, которое способно выдержать максимальную поездную нагрузку.
Поэтому проектное положение рельсов сохраняется, теоретически, неизменным вне зависимости от пропущенного тоннажа. Объясняется это тем, что, щебень при выправке путевой машиной, работающей по принципу RU 2378444 C2, сжат под выступом и под подошвой шпалы (за исключением средней части) с такой силой, что способен без просадки воспринимать максимально возможную нагрузку от колесной пары поезда равную 40 тс. Это означает достижение идеального качества уплотнения балласта железнодорожного пути. Поэтому просадка рельсов вниз от проектного положения не происходит при любом пропущенном тоннаже. Надо отметить, достижение этого эффекта происходит по RU 2378444 C2 без снижения производительности путевой машины, при работе ее в штатном режиме. Таким образом, отпадает необходимость использования динамического стабилизатора пути (ДСП).
Но известно, что ДСП обеспечивает уплотнение балласта всего на 20-30% и при этом снижается точность установки рельсов в проектное положение, выполненное перед работой ДСП выправочно-подбивочно-рихтовочной машиной.
Научные исследования показали, что некоторое повышение стабилизации балласта при работе ДСП объясняется повышением площади опирания шпалы, так как при ее вибрации происходит разравнивание бугров 1…4. Дополнительного же уплотнения и сжатия щебенок верхнего строения пути практически не происходит.
Применение нового технического решения позволяет значительно увеличить усилие фиксации шпал в балластной призме, оказывать эффективное противодействие сжимающим температурным силам, исключить возможность выброса и угона пути, организовать безаварийное движение поездов на высокоскоростных магистралях, повторно использовать старогодные шпалы после их доработки не только на малодеятельных, но и на главных железнодорожных путях.
Железобетонная шпала, цельнобрусковая, предварительно напряженная, имеющая выступ в подрельсовых зонах, отличающаяся тем, что выступ содержит зубцы.
www.findpatent.ru
ШПАЛЫ ЖЕЛЕЗОБЕТОННЫЕ. Описание, технические характеристики – ГК РОСАТОМСНАБ
Задать вопрос
Железобетонные шпалы – главное составляющие железнодорожных путей. В настоящие время, они получили широкое применение в отличии от деревянных шпал. В железнодорожном пути опору укладывают на верхнее строение балластного слоя, что создаёт устойчивость в взаимном расположении рельсовых нитей. Давление воспринимаемое от промежуточных скреплений или от рельсов, передается на балластный слой (пошпальное основание). Основным преимуществом является создание наилучшей равно упругости рельсовых опор. Наряду с этим шпалы более устойчивы к гниению, а так же имеют большую прочность при смятии. Срок эксплуатации железобетонных шпал при ежедневной нагрузке достигает в среднем до 50 лет. Практика показывает, что движения поезда по железобетонным шпалам, более плавное, при этом отмечается создание наилучших условий для работы бесстыкового пути вследствие большой поперечной устойчивости. Изготовление шпал осуществляется непосредственно с требованиями указанными в ГОСТ. Существует ряд основных технических характеристик производства железобетонных шпал.
• Длина - 2700 мм. • Ширина - 300 мм. • Высота - 230 мм. • Устойчивость к морозу – не ниже F200 • Категория бетона – не менее B40 (М500)
Железобетонные шпалы представляют собой достаточно сложную конструкцию, которая подвержена различным погодным условиям, а так же эксплуатируется с ежедневными чрезвычайными нагрузками. Железобетонные шпалы современного типа – цельнобрусковые из напряженного железобетона, армированные высокопрочной проволокой, полностью удовлетворяющие ТУ 5864 – 019 - 11337151-95 и ГОСТу 10629-88.Классификация ЖБ шпал:
• ЖБ шпалы Ш 1-1 (угол наклона упорных кромок подрельсовых площадок в шпалах 55 град.o) применяются для раздельного клеммно - болтового скрепления КБ с болтовым прикреплением подкладки к шпале. Производятся они из тяжелого бетона класса по прочности на сжатие В40 (М500). Марка бетона по морозостойкости должна быть не ниже F200 (Мрз200). Для бетона шпал применяется щебень (из природного камня или гравия) фракция 5-20 мм. ГОСТ 10629-88. • ЖБ шпалы Ш 1-2 (угол наклона упорных кромок подрельсовых площадок в шпалах 72 град.o) используются для раздельного клеммно - болтового скрепления КБ с болтовым прикреплением подкладки к шпале. ГОСТ 10629-88. • ЖБ шпалы Ш 2-1 применяются для нераздельного клеммно-болтового рельсового скрепления БПУ с болтовым прикреплением подкладки или рельса к шпале. ГОСТ 10629. • ЖБ шпалы Ш 3 используются для нераздельного клеммно-болтового скрепления ЖБР65 с болтовым прикреплением рельса к шпале. • ЖБ шпалы ШС-АРС применяются для анкерного рельсового скрепления. • ЖБ шпалы Ш 1-16*5 - шпалы с высокопрочной проволочной арматурой периодического профиля диаметром от 3 до 5 мм. • ЖБ шпалы Ш 1-4*10 представляют собой шпалы с высокопрочной стержневой арматурой периодического профиля диаметром стержней от 7 до 12 мм. Для шпал широко используется в качестве арматуры стальная проволока периодического профиля. При этом к ее диаметр должен составлять 3 мм, а сама проволока иметь вид класса Вр. Число проволок в номинале шкалы составляет 44, при чем каждая натянута с особым усилием 8,1 кН. В отличии от трещино - стойкости, геометрические параметры и качество бетонных поверхностей разделяют на две категории: первая и вторая. Осуществление укладки на подъездных путях, а также на стационарных и малодеятельных производиться шпалами второго сорта. Причем поставка происходит только при согласии потребителя. На рельсах Р65 имея скрепление КБ, наработка тоннажа составляет минимум 2000 млн т брутто. Объем дефекта железобетонных шпал при общем выходе и ремонта всех видов не превышает 5-6 % после пропуска 1,0 млрд т брутто. Наиболее значительную экономию играет перекладка старых железобетонных шпал снятых с путей 1-ой и 2-ой категории при капитальном ремонте, на пути 3-4-го классов и подъездные пути промышленных предприятий. При транспортировке железобетонных шпал необходимо руководствоваться требованиями ГОСТ 13015-2003, так же это требование напрямую относиться и к методам хранения. Хранить шпалы необходимо в штабелях при этом ряды должны быть строго горизонтальные и подошвой вниз т.е в рабочем положении. Штабель должен быть высотой в 16 рядов, но не больше! Так же под шпалы и между ними необходимо уложить деревянные подкладки. Между шпалами их располагают в углублениях. Минимальная толщина подкладок составляет 50 мм. Допустимо отклонение применения деревянных прокладок с сечением минимально 40х40 мм, но лишь с согласованием потребителя. Транспортировка производиться в полувагонах или на грузовом авто. Недопустимо транспортировка разных марок в одном вагоне либо кузове авто. Изготовитель железобетонных шпал осуществляет гарантийный срок эксплуатации 3 года с момента укладки их на железнодорожные пути.
|
||
|
||
|
||
|
||
|
Задать вопрос
rosatomsnab.ru
Железобетонная шпала
Изобретение относится к железнодорожному пути, в частности к железобетонным шпалам. Железобетонная шпала содержит выступы на подошве. Подошва содержит зубья. Толщина выступа в подрельсовой зоне превышает на 20-70 мм толщину выступа на средней части подошвы. Достигается повышение долговечности и надежности шпалы. 2 з.п. ф-лы.
Изобретение относится к конструкции рельсовых опор и может быть применено для изготовления шпал, в основном железобетонных, применяемых в верхнем строении железнодорожного пути, преимущественно бесстыкового.
Общеизвестна железобетонная шпала, представляющая собой балку переменного трапецеидального сечения (см. «Общий курс железных дорог», стр. 56 / Под ред. Ю.И. Ефименко. М. 2005 г). Ее конструкция цельнобрусковая, предварительно напряженная, а нижняя постель плоская.
Недостатком этих рельсовых опор является появление трещин при эксплуатации под действием поездной нагрузки по верху средней части шпалы и по ее подошве в подрельсовой зоне, а также низкий коэффициент сцепления с балластом железнодорожного пути, приводящий к значительному снижению усилия сдвига.
Указанные недостатки сокращают долговечность шпал и снижают надежность железнодорожного пути от выброса рельсошпальной решетки под действием продольных температурных сил в рельсовых плетях, которые могут достигать значений 320 тс.
Для решения этих проблем предлагалось, например, увеличивать вес, делать рифления подошвы, уширять подрельсовую часть шпал и уменьшать их ширину в центральной части. Но практического применения эти технические решения не имели, так как затраты увеличивались существенно, а усилие сдвига повышалось незначительно, лишь на 5-10%.
Известно также техническое решение по изобретению SU 1772284 А1, в котором шпала имеет на подошве выступ в подрельсовых зонах. Такое изменение конструкции для стандартных железобетонных шпал позволяет снизить растягивающие напряжения и по подошве подрельсовых зонах и по верху средней части изделия, а следовательно, приводит к повышению трещиностойкости рельсовой опоры.
Подрельсовая зона постели по этому техническому решению не содержит зубцов.
Принимаем SU 1772284 А1 за прототип. Но по изобретению SU 1772284 А1 усилие сдвига шпал в балласте верхнего строения пути увеличивается незначительно и проблема предотвращения выброса от действия продольных температурных сил в рельсах бесстыковой железнодорожной колеи остается нерешенной.
Целью предлагаемого изобретения является значительное увеличение силы сопротивления смещению в балласте железобетонной шпалы с выступом на подошве в подрельсовой зоне и сохранение при этом высокой трещиностойкости.
Указанная цель достигается тем, что в железобетонной шпале с выступом на подошве в подрельсовой зоне:
подошва содержит зубья;
зубья закреплены на выступе, расположенном в средней части подошвы шпалы;
зубья закреплены на выступе, расположенном на подошве по бокам шпалы;
толщина выступа в подрельсовой зоне превышает на 20-70 мм толщину выступа на средней части подошвы;
толщина выступа на подошве по бокам шпалы превышает на 10-60 мм толщину выступа на средней части подошвы;
толщина выступа на подошве в подрельсовой зоне превышает на 10-60 мм толщину выступа по бокам шпалы.
Наличие выступа в подрельсовой зоне, то есть на участке проекции подошвы рельса на нижнюю поверхность шпалы, увеличивает момент сопротивления и прочность изделия.
Кроме того, расположение в этом месте утолщения рельсовой опоры способствует наибольшему уплотнению щебня под ним, максимальной ответной силе реакции балласта на действие поездной нагрузки, отсутствию изгибающего момента по подошве подрельсовой части и верхней поверхности средней зоны шпалы.
Для увеличения усилия сдвига необходимо введение в конструкцию зубьев. Установить их предпочтительнее на средней части подошвы шпалы. Допустимым вариантом места размещения зубьев являются и боковые части подошвы рельсовой опоры. Кроме того, возможен и совмещенный вариант с установкой зубьев и на средней части, и по бокам шпалы.
Выполнить все это можно, например, на стадии изготовления рельсовой опоры, установив их, например, на плоской подошве средней части и углубив в тело шпалы, или углубив в сформированное на подошве утолщение на стадии затвердевания бетона. Зубья можно закрепить, например, и в специально просверленные отверстия плоской, ровной подошвы готового изделия.
Критерием минимальной толщины выступа подрельсовой зоны является такое значение его высоты, при котором при воздействии поездной нагрузки сила реакции балласта на выступ не меньше силы реакции балласта на оставшиеся части подошвы. При высокой степени уплотнения щебня минимальная толщина выступа подрельсовой зоны стремится к нулю.
Прибетонированные по предлагаемому техническому решению выступы на подошве по ее средней зоне и бокам рельсовой опоры предназначены для установки зубьев на подошву готовой стандартной шпалы. Этот прием позволяет снизить концентрацию напряжений на подошве, повысить надежность и исключает какую-либо механическую доработку самой рельсовой опоры, изготовляемой по ГОСТ Р 54747-2011. Поэтому даже при повреждении или разрушении зубатого выступа прочность, работоспособность и неизменность тела самой шпалы полностью сохраняется на уровне указанных в стандарте значений. Это объясняется тем, что максимально возможным уровнем повреждений зубатого элемента является его отрыв от поверхности соприкосновения с подошвой, являющейся наиболее уязвимым местом соединения. Тело стандартной шпалы при этом не повреждается. Поэтому технология закрепления зубьев на прибетонированном к подошве готовой шпалы выступе гарантирует при испытаниях опытных изделий в пути сохранение прочности и трещиностойкости модернизированной рельсовой опоры на уровне, не ниже стандартного.
Увеличение усилия сдвига в балласте железнодорожной колеи предлагаемой рельсовой опоры зависит от степени уплотнения щебня, размеров и количества зубьев и может превышать аналогичный параметр обычного изделия в 10-15 раз.
Наиболее эффективна установка зубатого выступа в средней, центральной части шпалы. Здесь балласт не подбивается рабочими инструментами путевых выправочных машин и всегда находится уплотненном состоянии от трамбовки подошвой шпалы под действием нагрузки колесных пар поезда. Но выступ в центре может привести к наиболее опасному из вариантов контакта нижней поверхности рельсовой опоры с балластом верхнего строения пути: опиранию серединой подошвы. Поэтому его толщина (высота) должна быть меньше толщины (высоты) выступа подрельсовой зоны как минимум на 10-20 мм. В этом случае гарантируется зазор и отсутствие опасного опирания шпалы средней частью на балласт пути. Максимальное превышение толщина выступа в подрельсовой зоне по сравнению с толщиной выступа средней части подошвы определяется толщиной балластного слоя, прилагаемой нагрузкой и в большинстве случаев составляет 40-70 мм.
Количества зубьев, которые можно разместить на выступах средней зоны, достаточны для создания усилия сдвига, обеспечивающего безопасность движения поездов. Тем не менее допустима и их установка на выступе подошвы по бокам шпалы. Причем этот выступ во избежание опирания серединой рельсовой опоры на балласт должен быть выше выступа на средней части. Минимальное превышение толщины бокового выступа над средним составляет приблизительно 10 мм, а максимальное около 60 мм. Эти параметры также определяются необходимостью обеспечения минимального зазора под центральной частью шпалы и возможной максимальной величиной осадки слоя щебня, которая зависит от его толщины, степени уплотнения и действующей нагрузки. Кроме того, для исключения появления изгибающего момента в подрельсовой зоне подошвы шпалы и по верху ее средней части, также необходимо выполнение превышения толщины подрельсового выступа над выступами по бокам. В большинстве случаев диапазон значений этого параметра составляет 10-60 мм.
Предлагаемые соотношения толщин выступов на подошве модернизированной рельсовой опоры позволяют обеспечить высокую трещиностойкость при доработке старогодной или вновь изготовляемой шпалы. Наличие зубьев предопределяет значительное увеличение усилия сдвига шпалы в балласте. Поэтому при повышении надежности бесстыкового пути от выброса при использовании предлагаемого изобретения можно понизить температуру закрепления плетей и благодаря этому существенно сократить количество изломов рельсов из-за уменьшения растягивающих напряжений в плетях бесстыкового пути в зимний период. Экономический эффект значителен.
Затраты ОАО «РЖД», например, в 2014 г. на диагностику пути составили 10,1 млрд.р. Существенную долю в них составляют расходы на проверку геометрии колеи и определение дефектов рельсов, из которых наиболее опасными являются те, которые приводят к излому. Из-за опасности возможных аварий из-за изломов частота диагностики пути в ОАО «РЖД» чрезвычайно высока и превышает этот показатель на зарубежных железных дорогах в десятки раз.
Определенным преимуществом нового технического решения является и то, что наличие зубьев на средней части не требует изменения правил укладки рельсовых опор в штабеля, транспортировки пакетов рельсовых звеньев по платформам, рольгангам моторных платформ и укладочного крана УК 25/9-18. Кроме того, наличие именно сжимающих, а не растягивающих напряжений на подошве центральной зоны шпалы предопределяет высокую прочность и надежность работы бетонного тела изделия с закрепленными на подошве зубьями.
Применение предлагаемого изобретения позволяет значительно увеличить усилие сдвига шпал в балласте, уменьшить температурные силы в рельсах, исключить выбросы железнодорожной колеи, уменьшить частоту излома рельсов, повторно использовать старогодные шпалы не только на малодеятельных, но и на главных путях.
1. Железобетонная шпала с выступами на подошве, отличающаяся тем, что подошва содержит зубья, при этом толщина выступа в подрельсовой зоне превышает на 20-70 мм толщину выступа на средней части подошвы.
2. Железобетонная шпала по п. 1, отличающаяся тем, что толщина выступа на подошве в подрельсовой зоне, превышает на 10-60 мм толщину выступа по бокам шпалы.
3. Железобетонная шпала по п. 1, отличающаяся тем, что толщина выступа на подошве по бокам шпалы превышает на 10-60 мм толщину выступа на средней части подошвы.
www.findpatent.ru