Газоблок: пористая шуба для нашего дома. Газоблок производство
технические характеристики и технология производства ячеистых бетонов, видео и фото
Ячеистые бетонные материалы, такие как пеноблок или газоблок, сегодня медленно, но уверенно вытесняют со строительного рынка полнотелые бетонные блоки, кирпичи и другие изделия с меньшей энергоэффективностью. Производятся газобетонные блоки по достаточно простой технологии, при этом относительно небольшие затраты на изготовление материала обеспечивают доступную стоимость.
В статье я опишу технологию производства газоблоков, их ассортимент, а также приведу аргументы за и против их использования в строительных и теплоизоляционных работах.
Блоки из газобетона не только прочны, но и энергоэффективны
Обзор материала
Структура и основные компоненты
Строительный газоблок – это материал, который производится из газобетона. При изготовлении этого сырья в бетонный раствор в результате химической реакции вовлекается водород, который равномерно распределяется в толще изделия, формируя микроскопические поры.
Технология производства газобетона предполагает использование таких компонентов:

Основные ингредиенты
- Связующее — портландцемент марки не ниже М400, а лучше – М500. Качество связующего играет первостепенную роль, поскольку от него напрямую зависит прочность материала.
Почти всегда в состав связующего добавляют известь.
- Наполнитель – песок размерами 0,5 – 1,5 мм, с минимальным содержанием глинистой фракции и органики. Перед использованием песок обязательно просеивается для удаления крупных частиц.
- Вода – чистая, с пониженным содержанием солей (сульфаты, хлориды, карбонаты) и органики (масла, нефтепродукты). Настоятельно рекомендуется использовать воду, соответствующую требованиям ГОСТ 23732-79.

Газообразующий компонент на основе алюминиевой пудры
- Газообразующий компонент – алюминиевая пудра или паста на ее основе. При производстве ячеистых бетонов вода вступает в реакцию с алюминиевым составом, и выделяющийся в результате водород обеспечивает формирование пористой структуры.

Такой материал формируется в результате внутреннего пенообразования
Кроме четырех основных компонентов в состав раствора, из которого будет делаться газоблок, включают и дополнительные ингредиенты – пластификаторы, отвердители, модификаторы прочности и т.д. Все они улучшают свойства материала и его эксплуатационные параметры.
Производство газоблока
Пенобетон и газобетон делают по сходным методикам, но все же некоторые отличия в технологиях присутствуют.
При изготовлении газобетона:

Технологическая схема производства
- Сначала смешиваются сухие компоненты – цемент, известь и песок.
- После этого выполняется затворение смеси водой, в результате чего получается однородная масса с хорошей текучестью.
- Затем в емкость подается газообразующий компонент, который начинает реагировать с водой. В результате раствор насыщается газом, увеличиваясь в объеме.
- Пролеченный газобетон можно использовать для заливки в опалубку при монолитном строительстве или же применять для изготовления штучных блоков.

Форма для отливки штучных изделий
Сами газоблоки делаются по двум основным технологиям:
- Штучные изделия фиксированной формы и размера получают путем заливки раствора в кассетные формы. Металлическую форму смазывают машинным маслом, заполняют раствором и оставляют до полимеризации связующего. После этого детали извлекают из формы и подают на этап сушки.

Формы с монолитами
- Распиловочный газоблок делают несколько иначе. Сначала в форме отливается монолит большого размера, который затем высушивается и распиливается на отдельные блоки. Распиловка может выполняться как в заводских условиях, так и непосредственно на объекте – во втором случае детали точно подгоняются под необходимые габариты с целью минимизации объема отходов.

Резка монолита на станке
В любом случае изделия, полученные путем отливку в форму, нужно высушить.
В зависимости от того, какая технология производства использовалась, различают газобетонные блоки естественной сушки и автоклавные изделия:
- При естественной сушке изделия набирают прочность на поддонах в хорошо проветриваемом помещении в течение примерно 28 суток (время полной гидратации цемента). Такой материал стоит дешевле, поскольку на его производство не требуется затрат электроэнергии, но блоки отличаются меньшей прочностью.

Высокотемпературная сушка в автоклавах
- Автоклавный газоблок помещают в специальные камеры (автоклавы), где вначале обрабатывают горячим паром, а затем высушивают. Сушка занимает не более 10 часов, после чего примерно сутки уходят на остывание и созревание материала. В результате модули приобретают дополнительный запас прочности, но и цена изделий возрастает.
Размеры и эксплуатационные характеристики

Наиболее распространённые изделия
Сегодня производители предлагают широкий ассортимент строительного материала на основе ячеистого бетона. Габариты основных типов газобетонных блоков я приведу в таблице ниже:
Тип изделия | Габариты, мм | ||
Длина | Ширина | Высота | |
Блок прямой | 625 | 200 300 | 250 300 |
Блок с ручками | 625 | 375 400 | 250 |
Блок с системой «гребень – паз» | 625 | 300 375 400 | 250 |
Блок перегородочный | 625 | 100 150 | 250 |
Блок U-образный для перемычки | 500 | 200 300 400 | 250 |
И литьевые, и монолитные блоки легко режутся как на распиловочных станках, так и специальными ножовками, так что проблем с подгонкой деталей по габаритам обычно не возникает.

Поры меньше, чем у пенобетона, но их суммарный объём примерно сопоставим
Технические характеристики изделия напрямую определяются объемом вовлечённого воздуха. Чем больше этот объем, тем ниже плотность материала, соответственно, тем выше его теплоизоляционный потенциал. При этом снижение плотности способствует уменьшению несущей способности, и прочности на сжатие. Потому нам придется балансировать между механическими свойствами и способностью к энергосбережению.

Различие между материалами разной плотности
Для облегчения выбора материалов блоки из газобетона делят на несколько групп по плотности:
Назначение изделий | Плотность, кг/м3 | Пористость, % | Прочность на сжатие, МПа | Теплопроводность, ВТ/м*С |
Возведение капитальных сооружений | 1000 — 1400 | не более 50 | 12 — 15 | 0,4 |
Возведение малонагруженных конструкций с ограниченной несущей способностью | 700 — 900 | 60 — 75 | 5 – 8,5 | 0,16 – 0,28 |
Сооружение перегородок внутри помещений | 400 — 600 | 80 | 1,2 – 4,5 | 0,12 – 0,15 |
Теплоизоляция при отделке несущих конструкций из других материалов | 200 — 300 | до 95 | 0,5 – 1,2 | 0,08 – 0,1 |
Как видите, большой «размах по плотности» позволяет производить изделия с самыми разными эксплуатационными параметрами. Это облегчает подбор материала для решения конкретных задач: так, даже поризованный керамический блок, сочетающий хорошую теплоизоляцию с неплохой несущей способностью, проигрывает перегородочным и теплоизоляционным моделям по теплопроводности: у керамики этот показатель равен 0,14 — 0,24, у газобетона – 0,08 – 0,15.

Разные материалы – разные характеристики
Еще одним материалом, который предлагают рассматривать в качестве альтернативы газоблоку, является теплокирпич Warm Stein. По уверениям продавцов, эти изделия обладают прочностью, сравнимой с полнотелым керамическим кирпичом, но превосходят по сопротивлению теплопередаче и поризованные блоки, и пенобетон, и газоблок.

«Инновационный» теплокирпич Warm Stein. На срезе материал уж очень похож на обыкновенный полистиролбетон…
Лучше не спешить с инновационным материалом – вполне возможно, мы имеем дело с маркетинговой «пустышкой» или привычным материалом (полистиролбетон, газосиликатный блок), который нам пытаются продать под красивым названием.
За и против
Достоинства
Сравнение газобетонных изделий с другими материалами для кладки стен позволяет выявить целый ряд преимуществ.
Основными плюсами для меня являются:
- Точные размеры изделий и возможность подгонки под нужные габариты. Это касается как деталей, произведенных по литьевой технологии, так и нарезных блоков. Благодаря этому кладку можно выполнять с тонкими швами, что позволяет избавиться от мостиков холода – участков стены с большей плотностью и большей теплопроводностью.

Точный размер блоков позволяет подгонять их друг к другу с минимальными зазорами
- Малый удельный вес, способствующий снижению нагрузки на фундамент. С этой точки зрения ответ на вопрос, что лучше — кирпич или газобетон – вполне очевиден: даже конструкционные блоки с высокой плотностью легче кирпича, так что затраты на устройство основания будут в разы ниже.
- Прочность, достаточная для использования в малоэтажном строительстве. Используя конструкционные разновидности газобетона, вполне можно возводить двух-трехэтажные дома с достаточным запасом надежности и долговечности.

Для малоэтажного строительства механической прочности хватает с запасом
- Отличные эксплуатационные свойства – это и звукоизоляция, которая обеспечивается пористой структурой блока, и, конечно же, теплоизоляция. Низкая теплопроводность является ключевой особенностью ячеистых бетонов (собственною ради нее их и придумывали), а газобетон – один из лучших представителей этой обширной группы материалов.

Сравнительная теплопроводность разных групп материалов
- Стойкость к внешним воздействиям – газоблок не горит, не гниет, не разрушается под воздействием ультрафиолета, не повреждается бактериями и грибками. Резкие перепады температур могут оказывать влияние на материал, но большое количество внутренних пор обеспечивает эффективную компенсацию этих воздействий, так что для снижения прочности нужны действительно серьезные нагрузки.
А если обеспечить газобетонной кладке защиту от контакта с внешней средой, оштукатурив ее или обшив каким-либо фасадным материалом, то стойкость конструкции возрастет на порядок.

Блок распиливается идеально!
- Кроме того, нельзя забывать и об удобстве в монтаже: блоки получаются легкими (относительно, но все-таки!), практически без усилий переносятся, режутся, сверлятся, шлифуются и т.д. В общем, работать с газобетонными изделиями — одно удовольствие.
Недостатки
Теперь о минусах – куда без них:

На фото – трещина в кладке, возникшая при подвижке фундамента
- Хорошей прочности изделий на сжатие сопутствует определенная хрупкость материала. Из этого следует два вывода: работать с блоками нужно аккуратно, стараясь не отколоть грани, а фундамент может быть не слишком мощным, но обязательно должен быть жестким. В противном случае при подвижках основания стены могут дать трещину – особенно часто этим «грешат» крупноформатные блоки.
- Влагоемкость, как и у любого пористого бетона, значительно выше средней. Поскольку материал «тянет» воду очень активно, его необходимо защищать наружной отделкой. Кроме того, активное водопоглощение создает проблемы при оштукатуривании, поскольку стена забирает влагу из штукатурного состава очень интенсивно.

Этот блока а) делали с нарушением технологии и б) не защищали от воздействия влаги
Рецепт решения этой проблемы найден достаточно давно. Сначала огрунтованная поверхность начерно оштукатуривается дешевым гипсовым составом, который прочно схватывается, но в 90% случаев растрескивается из-за активного водопоглощения и быстрого высыхания. После этого сверху наклеивается армирующий стеклохолст или стекловолоконная сетка и укладывается либо слой маскирующей шпатлевки, либо слой декоративной штукатурки.
- Третий минус – сложность крепления. Гвозди и саморезы выпадают с гарантией, раскрывающиеся металлические дюбели разрушают стенки отверстия и при малейших нагрузках начинают расшатываться. Для фиксации на поверхностях из газоблока желательно использовать специальные анкера из металла или пластика, а также химические анкера, которые затвердевают уже внутри стены.

Для крепления в пористых бетонах используются специальные анкера

Сравнение распорного крепежа и химического анкера
В общем, набор минусов, которыми обладает газоблок, во многом типичен для материалов на основе пористого бетона. Но мне кажется, что плюсы их перекрывают, так что для использования в строительстве такие изделия вполне подойдут.
Реклама
Кладка газобетонных блоков

Тонкошовная кладка имеет свои особенности
Монтируя газоблоки своими руками, нужно помнить, что материал этот специфический, и потому подходить к нему с теми же стандартами, что и к кирпичу или шлакоблоку, явно не стоит.
Ниже я сформулировал несколько правил, следовать которым если и не обязательно, то, как минимум, желательно:
- Любая кладка возводится на основании с обустроенной отсечной гидроизоляцией. Это значит, что и на цоколь, и на фундамент нужно вначале настелить два-три слоя рубероида или уложить специальную мембрану – эти слои предотвратят капиллярный подсос и защитят газобетон от увлажнения.

Обязательной является отсечная гидроизоляция
- Далее формируем подушку – укладываем на гидроизоляцию цементный раствор слоем около 20 – 30 мм. На эту подушку устанавливаем первый ряд блоков, тщательно выравнивая их по вертикали и горизонтали.
- Для кладки газобетонных изделий может применяться либо стандартный кладочный раствор на основе высокомарочного цемента, либо специальный клей. Второй вариант мне кажется предпочтительным: да, стоит клей дороже, но к его плюсам можно отнести и лучшую адгезию, и высокую скорость полимеризации, и возможность монтажа с минимальной толщиной шва.

Использование таких клеевых составов позволяет формировать тонкошовную кладку
- Перед укладкой каждого следующего ряда поверхность уже уложенных блоков зачищаем специальной теркой. Это позволит убрать все неровности, кроме того, обеспечит нужную для сцепления с клеевым раствором шероховатость.

Терка для зачистки поверхности
- Клей или раствор наносим на блоки с помощью зубчатого шпателя или специального дозатора (каретки). Излишки материала, выступающие по бокам при кладке, убираем кельмой или шпателем.

Нанесение клея кареткой
- В процессе кладки каждый блок вначале укладываем на место и выравниваем вручную, а затем окончательно выставляем ударами резиновой киянки. При этом постоянно контролируем положение детали с помощью уровня. В качестве дополнительного ориентира можно использовать натянутый шнурок.

Кладка газоблока
- Если используются блоки с торцами, выполненными в виде замков «гребень – паз», то их можно соединять насухо, без клея. В этом случае при оштукатуривании поверхности внутри кладки формируется тонкая воздушная прослойка, которая обеспечивает куда лучшую теплоизоляцию, чем слой раствора. Если же оштукатуривание не планируется, то клеить, естественно, надо!
- Кладка ведется с перевязкой, т.е. со смещением блоков в ряду во избежание совпадения вертикальных швов. Инструкция рекомендует выдерживать минимальное смещение шва не менее 8 — 12 см.

Нарезка штробы под армирование
- Первый и каждый четвертый ряд кладки желательно армировать. Для этого с помощью ручного или электрического штробореза на расстоянии не менее 60 мм от боковых поверхностей блока вырезаются канавки, в которые закладывается пруток диаметром 8 мм. Размещение армирования в канавках позволяет избежать увеличения толщины шва между блоками и снизить теплопотери.

Армирование стальным прутком
При укладке блоков шириной от 500 мм желательно использовать не два, а три контура армирвоания.
- После завершения кладки поверхность желательно обработать теркой для формирования шероховатости (у литиевых блоков стенки достаточно гладкие), после чего стенка грунтуется и штукатурится. Можно использовать специальные штукатурки для пористых бетонов, а можно работать обычными составами по многослойной технологии, описанной выше.

Многослойное оштукатуривание по сетке
Заключение
Газоблок, образно выражаясь – один из достойнейших представителей благородного семейства ячеистых бетонов. Изделия из этого материала можно применять как для возведения капитальных конструкций (пусть и в основном в малоэтажном строительстве), так и для теплоизоляции новых и только что возведённых зданий.
Видео в этой статье позволит вам более подробно ознакомиться с особенностями газобетонных блоков. А если после просмотра что-то покажется неясным или вы захотите узнать больше – милости прошу на форум и в комментарии с любыми вопросами по этой теме!
klademkirpich.ru
10 крупнейших производителей газобетонных блоков России
ЗАО «Кселла-Аэроблок-Центр»
- офис: г. Москва, ул. Рабочая, д. 93, стр. 2, подъезд 3
- телефон: +7 (495) 710 70 23
- сайт: ytong.ru
Известная фирма из Германии, которая имеет свои производственные мощности в России. Компания Xella является первым производителем и поставщиком строительных материалов на немецком рынке данной продукции, а также имеет не последние позиции на мировом рынке стройматериалов. Основан производитель в 2003 году, благодаря слиянию трех компаний — Haniel-BauIndustrie GmbH, Ytong AG и Fels-Werke GmbH. За свое довольно короткое существование Xella быстро утвердилась в сфере производства стройматериалов на мировом рынке. Ее продукция обладает высочайшим качеством, благодаря применению последних разработок в строительной сфере. Три основных направления компании включают в себя добычу и переработку сырья, остальные относятся к производству стройматериалов, одно из которых специализируется на изготовлении газобетонных блоков.
ЗАО «ЕвроАэроБетон»
- офис: г. Санкт-Петербург, ул. Смолячкова, дом 19, БЦ «ГАП», офис 506
- телефон: +7 (812) 385-03-06
- сайт: euroaerobeton.ru
Новое предприятие, которое выпустило первый газобетонный блок в 2008 году и на данном этапе своего развития производитель имеет мощный завод, расположенный в городе Сланцы, ленинградской области. Завод спроектирован и оснащен передовыми технологиями производства инжиниринговой компанией из Германии – PHILCO. Автоматические производственные процессы стали возможны благодаря оборудованию SIEMENS, WEHRHAHN, PFISTER, CEMTEC, SCHOLZ, HOKA, LOOS. Весь процесс изготовления контролируется специалистами высочайшего класса. Помимо этого предприятие имеет свои лаборатории, где проверяется качество выходящей продукции, которое имеет очень высокий уровень. Не смотря на свое недолгое существование фирма «ЕвроАэроБетон» крепко закрепилась на рынке газобетонной продукции.
ЗАО «Воронежский комбинат строительных материалов»
- офис: г. Воронеж, Советский р-н, ул. Тихий Дон, 57
- телефон: +7 (473) 224-89-92
- сайт: vksm.ru
Крупное предприятие воронежской области, обеспечивающее практически весь спрос на строительные материалы, типа кирпича и газобетонных блоков по всему региону. Довольно старая компания с 55-ти летним периодом существования, многократно расширялась, пока не достигла объемов производства 140 миллионов кирпичей формата 50x120x65 и 250х120х88 мм в год. На данный момент имеет современное оборудование и сотрудников с колоссальным опытом работы. Газобетонные блоки предприятие начало производить с 2010 года и достигло довольно больших объемов в этом направлении, которое достигает 288 тыс. куб. метров в год. Качество продукции не вызывает сомнения, благодаря регулярной модернизации производственных мощностей по последнему слову техники и высокому профессионализму сотрудников.
ООО «ЛСР. СТРОИТЕЛЬСТВО-УРАЛ»
- офис: г. Екатеринбург, ул. 40 лет ВЛКСМ, 34
- телефон: +7 (343) 215-99-33
- сайт: lsrconstruction-ural.ru
Крупнейшая российская группа LSR, которая является одним из лидеров среди подобных предприятий Урала, специализируется на возведении строительных конструкций и производстве строительных материалов для них. Завод «Бетфор», как он назывался ранее вошел в состав LSR в 2013 году. Предприятие имеет богатую 50-ти летнюю историю и на данном этапе обладает всеми возможностями для осуществления индустриального домостроения и не только. Оборудование немецкой фирмы ЕВАWЕ, которое установлено на производственных мощностях предприятия позволяют добиваться хороших темпов производства. Множество реализованных проектов из собственных строительных материалов говорят об отличном качестве изготавливаемой продукции и внимательному подходу к поставленным задачам.
ООО «Казанский завод силикатных стеновых материалов»
- офис: г.Казань, ул.Тэцевская, 3
- телефон: +7 (843) 571-93-02
- сайт: kzssm.ru
Казанский завод селикатных стеновых материалов является лидером в Республике Татарстан и всего региона Поволжье. Предприятие выпускает 230 млн. штук простого кирпича и 100 тыс. куб. метров газобетонных блоков автоклавного твердения. Большой ассортимент продукции включает и лицевой кирпич, имеющий десять вариантов цветового решения. Немецкое оборудование, которое используется на заводе, удалось достичь прекрасных результатов в изготовлении качественной и востребованной по всему региону продукции. Газобетонные блоки компания начала выпускать с 2004 года и имеет большой опыт и высококлассных специалистов в данной области. Предприятие существует уже 80 лет и вобрала лучшие традиции в производстве строительных материалов, которые проверены временем и имеют высокий уровень качества.
ЗАО «Липецкий силикатный завод»
- офис: г. Липецк ул. Астраханская, 1
- телефон: +7 (4742) 43-80-30
- сайт: zaolsz.ru
Предприятие включено в сотню лучших заводов по производству селикатного блока в России, поэтому является лидером в своем регионе. Основан завод в далеком 1938 году и имеет обширную историю развития. Потребителями продукции завода являются не только жители Липецкого региона, но и Московской, Рязанской, Тамбовской, Тульской, Брянской областей. Продукция предприятия имеет высочайшее качество и имеет все сертификаты соответствующего уровня. В 2012 году завод прошел сертификацию международного класса ИСО 9001:2008 и теперь без сомнений можно сказать, что селикатный кирпич из ЛСЗ действительно качественный и отвечает всем строительным нормам. Производственные мощности предприятия модернизируются отечественным и зарубежным оборудованием, которое оснащено по последнему слову техники.
ОАО «Главновосибирскстрой»
- офис: г. Новосибирск, ул. 2-я Станционная, 52 а
- телефон: +7 (383) 36-36-134
- сайт: ao-gns.ru
Крупнейшее предприятие, работающее на рынке с 1963 года. На данном этапе развития, холдинг включает в себя ряд предприятий строительной сферы, которые имеют в арсенале выполненных проектов более 13 млн. кв. метров жилья – это 16 жилмассивов и 500 объектов социально-промышленного строительства. С 2007 года увеличено производство газобетона и теперь совокупная производственная мощность составляет на данный момент 360 тыс. куб. метров в год. Компания имеет соглашения с немецкой строительной компанией «Хенкель-Баутехник» и совместно они продвигают всемирно известный бренд Ceresit. Основным направлением компании является все же строительство, но современные технологические мощности производства дают высокое качество продукции фирмы. На данный момент компания осваивает и начинает строительство жилого массива в Калининском районе города Новосибирск.
ОАО «Пермский завод силикатных панелей»
- офис: г. Пермь, ул. Докучаева, 31
- телефон: +7 (342) 270-11-77
- сайт: pzsp.ru
Предприятие начиналось, как небольшой гипсовый завод и в течении 50 лет разрослось до полноценного строительного комплекса, который является лидером Пермского края. Возглавляет предприятие известный в своей сфере Заслуженный строитель РФ Николай Иванович Демкин. Предприятие обеспечивает 5000 людей работой на собственном заводе и в смежных областях. Основным направлением деятельности компании является проектирование и осуществление строительных проектов. Особое внимание следует уделить социальной ответственности, которая является одним из принципов организации. Помимо частных проектов, компания участвует в государственных строительных проектах, которые обеспечивают жильем военнослужащих и других слоев населения за счет государства. Участие во всероссийских конкурсах принесло победу фирме в 2012-2013 годах в номинации «Сто лучших бригад строительного комплекса России 2012 года» и «Элита строительного комплекса России».
ЗАО «Саратовский завод стройматериалов»
- офис: 410022, г. Саратов, а\я 4195
- телефон: +7 (8452) 92-09-21
- сайт: szsm.ru
Предприятие имеет богатую историю и не раз заслуживало престижные награды за достижения в области производства строительных материалов. В 2001 году заводу присвоен «Золотой эталон» – награда, которая символизирует надежность и стабильность. Была вручена директору Малышеву Игорю Валерьевичу от руководителей международной программы «Партнерство ради прогресса». И уже в 2001 году производитель вошел в сотню лучших предприятий своей отрасли. 2007 год также был богат на призы, такие как «Европейский стандарт», выделяющий достижения предприятия в качестве выпускаемой продукции, а также отечественная номинация «Лидер отрасли». Все награды получены за безупречную работу компании и высочайшее качество ее продуктов. Применение последних технологических подходов в производственном процессе и высокий профессионализм специалистов делают компанию весьма заметной на рынке стройматериалов.
ОАО «Костромской силикатный завод»
- офис: г. Кострома, ул. Ярославская, д. 43
- телефон: +7 (4942) 33-00-33
- сайт: silikat.ru
Предприятие основано в 1930 году и является одним из старейших в России, сотрудники, которые проработали не один десяток лет, любят говорить, что это «Детище первой пятилетки». Богатая история предприятия имеет в своем арсенале в основном только взлеты. За много лет функционирования предприятия сформировалась четкая система и устав, по которому происходит производственный процесс. А в совокупности с применением новых технологий и иностранного оборудования качество выпускаемой продукции не подлежит сомнению. В своем регионе это лидер, который обеспечивает практически весь рынок данной строительной продукции. В последние годы завод значительно расширил область распространения своей продукции и вышел далеко за пределы региона. Репутация завода имеет только положительные отзывы и очень много потребителей безоговорочно доверяют своему поставщику.
Материалы по теме:
moscowsad.ru
Производство газобетонных блоков


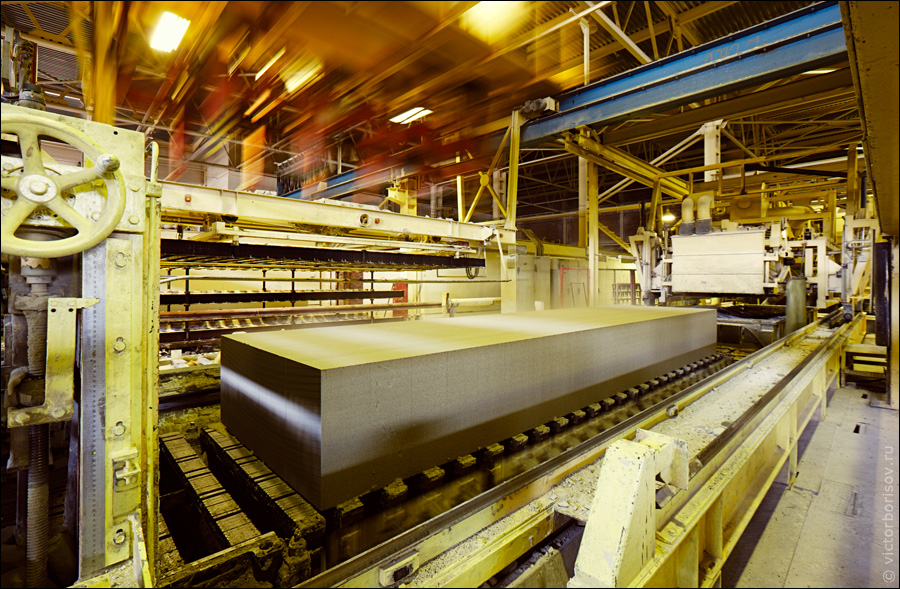
Чтобы более подробно увидеть процесс производства газобетона я отправился на завод Ytong в Можайске, начавший свою работу в 2008 году. По объемам произодства газобетона, это самый крупный завод в России. Смотрим!
2. Для производства газобетона используется натуральное сырье: цемент (~20%), известь (~20%), кварцевый песок (~60%), алюминиевая паста (~1%) и вода. Все компоненты смешиваются в определённых пропорциях, которая определяется требуемой прочностью готовой продукции.
3. Основу газобетона составляет песок, который нужно предварительно обработать.
4. Для этого используются шаровые мельницы.
5. Внутри барабана находятся вот такие шары, которые измельчают песок до превращения в пыль. Это нужно для того, чтобы после формовки блоки было легче обрабатывать.
6. После этого исходное сырье поступает в накопительные бункера на хранение. Затем в газобетоносмесителе происходит смешивание песка, цемента и извести.
7. А непосредственно перед заливкой к уже смешанным компонентам добавляется вода и суспензия алюминиевой пасты. Готовая смесь заливается в специальную прямоугольную форму (стенки формы не имеют жесткого соединения с дном) примерно на 2/3.
8. Именно на этом этапе происходит самое интересное. Алюминиевая паста вступает в реакцию с известью, в результате получается водород. Он образует в сырьевой массе огромное количество пор размером от 0,5 до 2 мм, разномерно распределённых внутри. Поддоны со смесью медленно продвигаются в герметичном помещении с запредельной влажностью (это единственный кадр, который я успел сделать до того, как запотел объектив) до тех пор, пока смесь не увеличится в объеме до верхней кромки поддона.
9. Через некоторое время (2-3 часа) транспортёр переносит форму с застывшей смесью на следующий этап. Показательно, что подъемник только за счёт ваккуума удерживает поддон без дна.
10. Теперь застывшую форму разрезают на блоки равного размера. Сначала в поперечном, а затем продольном направлениях. На заводе одна линия, которая единовременно может производить блоки только одного размера. Для производства блоков другого типоразмера просто заменяют ножи. Большая площадь для складирования готовой продукции позволяет всегда иметь в наличии полный ассортимент продукции.
11. После этого внешняя проверхность блоков шлифуется и затем они прижимаются друг к другу.
12. Кран захватывает поддон с блоками и переносит их на следующий этап производства.
13. И сразу же укладывается новый поддон в основание для следующей партии блоков. Да, очень важный факт — производство на заводе полностью автоматизировано и практически не требует участия человека. Люди работают только на линии упаковки (она пока еще не настолько автоматизирована), складе и в испытательной лаборатории. Всего на заводе работает менее 80 человек (завод работает круглосуточно).
14. Теперь блоки нужно поместить в автоклав. Слева «сырые» блоки, справа уже «готовые». Здесь хочу упомянуть следующий момент, после автоклавирования блоки имеют влажность порядка 30%, которая постепенно (в течение года) упадёт до 5-10%.
15. Автоклавирование очень важный этап, улучшающий свойства газобетонных блоков.
16. Разрезанные блоки помещают в специальные автоклавные камеры, где они в течение 12 часов при повышенном давлении в 12 кг/кв. см. обрабатываются насыщенным паром при температуре 190°C. При этом температура в начале и конце цикла плавно поднимается и опускается в течение определённого времени.
17. Каждый автоклав имеет длину более 30 метров. Использование автоклавирования позволяет повысить прочность газобетонных блоков и уменьшить его последующую усадку (менее 1 мм/м).
18. Каждая партия блоков после автоклавирования отправляется в лабораторию для проверки на соответствие заданным характеристикам. На этом станке нарезаются кубики правильной формы, которые затем отправятся на испытания.
19. А готовые блоки отправляются на линию упаковки. Здесь их складывают в 2 ряда. Позиционирование рядов блоков производят вручную.
20. Затем их переворачивают на бок под уже установленные деревянные паллеты. После чего блоки запечатываются в плёнку (чтобы защитить их от повреждений) и отправляются на склад.
21. Склад расположен под открытым небом, здесь всегда есть запас всей выпускаемой продукции. Ежедневно с завода отгружается покупателям более 2000 кубометров блоков.
22. Основная продукция завода это блоки толщиной от 50 до 500 мм с плотностью от 400 до 500 кг/кв.м.
И ещё несколько слов про различия газобетона и пенобетона. Понятно, что газобетон материал новый, но очень многие неосознанно их путают даже не понимая, что их характеристики существенно отличаются.
Во-первых, их различие кроется в названии. Для производства пенобетона используется пена, состоящая их вредных химических веществ (канифоль, клей, едкий натр и т.д.). А в производстве газобетона используется газ, образующийся в результате химической реакции извести и алюминиевой пасты, в результате получается просто водород. То есть газобетон является экологически чистым строительным материалом.
Во-вторых, пенобетон имеет очень низкие прочностные характеристики. А здесь, как известно, имеет место быть обратная зависимость. То есть, чем ниже плотность (и соответственно прочность), тем «теплее» материал. Но если газобетон плотностью D400 (400 кг/кв.м) можно использовать для несущих стен в домах до 3 этажей включительно и он будет обладать классом прочности В2,5 и морозстойкостью F100, то из пенобетона плотностью ниже D600 вообще нельзя делать несущие стены. Следовательно и теплопроводность пенобетона D600 будет значительно выше (то есть «холоднее»), чем газобетона D400.
В-третьих, технология производства пенобетона обычно не подразумевает использования автоклавов и нарезки блоков после застывания. Обычно его заливают сразу в готовые формы, а в результате блоки дают большую усадку (3-5 мм/м) после строительства. Не говоря уже о том, что сам процесс автоклавирования повышает прочность блоков в 3-4 раза.
Что уже сделано по строительству:1. Начало2. Подготовительный этап3. Стеклопластиковая арматура4. План дома5. Земляные работы (часть 1)6. Земляные работы (часть 2)7. Фундамент (часть 1)8. Фундамент (часть 2)
yablor.ru