Огнеупорный бетон – способ держать жар под контролем. Огнеупорный бетон состав
Огнеупорный бетон – разновидности и характеристики + Видео
Несколько вводных слов об огнеупорном бетоне
Как правило, такой вариант бетона используется при возведении печей, дымовых труб, как в жилищном, так и в промышленном строительстве. Изготовленный согласно всем правилам, материал обеспечивает надежную защиту и безопасность. В зависимости от назначения специалисты закупают различные варианты бетона – ячеистый, плотный или легкий.
Такой бетон также может использоваться в качестве теплоизоляционного материала. Благодаря тому, что работать с материалом нужно точно так же, как с обычным бетоном, снижаются затраты на проведение строительных работ. Этот материал прекрасно выдерживает перепады температур, не меняет своих качеств после нагревания, вот почему жаростойкий бетон становится лучшим вариантом при строительстве специализированных объектов.
Разработки для критических температурных условий
На практике обычные бетонные смеси плохо переносят высокие температуры. Даже те варианты, которые считаются одними из самых качественных и дорогостоящих, не могут гарантировать сохранность при температуре, превышающей 150 градусов. Материал начинает крошиться, терять форму, вследствие чего страдает вся конструкция.
Именно поэтому специалисты разработали особые составы, сохраняющие свойства в условиях повышенных температур. На сегодняшний день существуют так называемые высокоогнеупорные бетоны, применяющиеся в условиях, где температура превышает 1770 градусов, огнеупорные варианты, которые работают с температурами от 1580 до 1770 градусов, и жаростойкие, их предел 1580 градусов.
Любой бетон жаростойкий состоит из основы и наполнителя, при изготовлении такого материала используются специфические элементы: жидкое стекло, алюминиевый цемент, керамзиты и другое.
Огнеупорный вариант, в состав которого входит глинозем, не реагирует на кислоты, что дает ему дополнительные преимущества.
Оценивая эффективность материала, можно уверенно сказать, что использование жаростойкого бетона намного экономичнее, чем покупка жаростойких плит. Дело в том, что при укладке плиток, специалист вынужден использовать особый раствор, разрушающийся под действием температур. В отношении бетона таких неожиданностей происходить не может.
Особенности выбора жаростойкого бетона
Для того чтобы сделать бетон огнеупорным и пригодным для использования в местах с повышенными температурами, например, для возведения печи, в состав добавляется асбест, глиноземный цемент, жидкое стекло, а также бариевый цемент. Все эти добавления становятся одним целым с общей твердеющей составляющей, а также являются огнеупорными.
В состав обычного бетона входят элементы, которые при нагревании проходят процесс дегидрации или обезвоживания. Подвергшаяся такому испытанию бетонная конструкция быстро трескается, разрушается, остановить процесс бывает практически невозможно. Чтобы таких неприятностей не происходило, в местах с повышенной температурой нужно использовать огнеупорные составы.
Рассматривая жаропрочный бетон, можно отметить повышенное содержание примесей в его составе. Каждый элемент выполняет свою роль, связывая материал при повышении температуры, делая его более прочным. В зависимости от требований выбирают материал с добавлением конкретного элемента, так, некоторые заполнители выдерживают температуру лишь до 1580 градусов, а другие прекрасно показывают себя и при воздействии температуры в 1770 градусов.
ogodom.ru
ОГНЕУПОРНЫЕ И ЖАРОСТОЙКИЕ БЕТОНЫ
ОГРАЖДЕНИЯ ПАРОВЫХ КОТЛОВ
Широкое распространение жаростойких бетонов для обмуровки топочных камер н газоходов мощных котлов позволило в большинстве случаев избавиться от кирпичной кладки и дорогостоящих фасонных огнеупоров. Применение бетонов значительно снизило стоимость монолитных блоков, изготовляемых заблаговременно, трудозатраты и сроки выполнения работ. Для ограждений современных мощных котлов с высокой степенью экранирования огнеупорность и жаростойкость шамотобетонов оказались вполне достаточными для длительной эксплуатации. Ввиду особой важности бетонов как основных материалов для ограждений целесообразно остановиться на них более подробно. Бетонами называются камнеподоб - ные массы, которые состоят из смеси так называемых заполнителей из щебенки и песка с вяжущими веществами. Крупным заполнителем является щебенка, изготавливаемая дроблением основного огнеупорного материала, входящего в состав бетона, до размера фракций от 10 до 25 мм, а мелким — щебенка в виде песка из того же материала с размером фракций до 5 мм. При затворении водой смеси определенного весового состава из заполнителей с цементом или другим гидравлическим вяжущим масса схватывается и постепенно твердеет, превращаясь в монолит. Форма опалубки, в которую масса предварительно укладывается, определяет требуемую конструкцию изделия. Скорость отвердения зависит от вяжущего вещества и температуры. Наибольшее распространение для ограждений котлов получили шамотобетоны, состоящие из шамотных заполнителей и цемента в качестве вяжущего вещества. Шамотобетоны иа обычных цементо - вяжуших веществах являются жаростойкими, так как их огнеупорность меиее 1580°С, а рабочая температура не превышает 1100—1300°С. В качестве вяжущего вещества применяются цементы глиноземистый и портландский. Соответственно этим вяжущим бетоны называют «ша - мотобетон на глиноземистом цементе» и «шамотобетон на портландцементе».
Бетон на портландцементе
Портландцемент имеет в своем составе от 40 до 50% трехкальциевого силиката 3CaOSiC>2, который является основным вяжущим. Реакция гидратации происходит с выделением свободной окиси кальция (СаО):
3Ca0Si02 - f 5Н.20 = 2CaSi02-4h30 + Са(ОН)2.
Остальные компоненты при твердении свободного гидрата извести не выделяют. В дальнейшем при нагревании происходит потеря воды гидратом окиси кальция: Са (ОН)2->- СаО + Н20.
При остыванин бетона на его поверхности снова происходит гидратация окиси кальция за счет поглощения влаги нз воздуха. Так как известь СаО при гидратации резко увеличивает свой объем (до 2,5 раз), то происходят растрескивание и разрушение бетона. Внутри бетона при образовании СаО из гидрата Са(ОН)2 происходят испарение воды, усадка цементного камня, в результате чего появляются трещины и разрывы. Эти процессы в бетоне происходят при сравнительно низких температурах— в пределах 550°С. Таким образом, применение ша - мотобетонов на портландцементах без особых мероприятий— введения в их состав специальных компонентов, устраняющих описанные процессы, исключается. Для предотвращения образования свободной извести СаО при нагревании бетона предложен способ связывания ее в твердой фазе. Для этого в состав бетона вводится тонкомолотая добавка из кремнезема или шамота, вследствие чего при нагревании происходит связывание СаО в конечное соединение CaSi02. В интервале температур от 500 до 800°С реакция ндет медленно, при температуре более 800°С скорость реакции возрастает. Для обеспечения этих реакций в твердой фазе тонкость помола добавки должна соответствовать тонкости помола цемента, т. е. быть не более 40—60 мкм. Минимальное количество добавки практически должно составлять не менее 30% массы цемента. Шамотобетоны на портландцементе с тонкомолотой добавкой уступают бетонам на глиноземистом цементе: максимальная рабочая температура их применения не должна превышать 1100°С.
Уральским филиалом ВТИ предложен состає шамо - тобетоиа на портландцементе с введением в него 3—5% триполифосфата натрия (Na5P3Oio) взамен тонкомолотой добавки. При наличии в составе бетона триполифосфата натрия в нем происходят химические реакции, связывающие свободную известь. Разработано два состава бетонов, которые называются ПФБТ'—тяжелый бетоне объемной массой 1,8 т/м3 и ПФБЛ—легкий с объемной массой 1,3 т/м3. Легкий бетой, помимо шамотного заполнителя, имеет в своем составе около 10—12% асбеста. Наибольшая рабочая температура применения обоих бетонов не более 1200° С. Бетоны ПФБ удобны при приготовлении и в укладке.
Бетон иа глиноземистом цементе
По химическому составу глиноземистый цемент отличается от пор^глаидского высоким содержанием глинозема А1203 и малым содержанием окиси кальция СаО. Основной вяжущей частью является однокальциевый алюминат СаО ■ АЬОг, второстепенной — двухкальциевый силикат 2Ca0-Si02, при затвореиии происходит следующая реакция:
2(Са0-А1203) + 10Н20 = 2СаОА12Оя ■ 7НгО + 2А1(ОН):1.
В глиноземистом цементе не содержится трехкальци - евый силикат, поэтому свободная известь почти не выделяется, и он не имеет недостатков бетона на портландцементе. Жаростойкий шамотобетон на глиноземистом цементе для своего приготовления не требует ВВОДИТЬ В его состав каких-либо дополнительных компонентов. Такой бетон удобен в работе, быстро затвердевает и применяется при температурах до 1300°С. При нагревании До 300°С его прочность почти не меняется, в интервале от 400 до 600°С прочность составляет 50% прочности при 110°С, которая принимается за 100%, при температуре более 900°С прочность бетона увеличивается. Снижение прочности до 50% в процессе нагревания ие исключает его применения в обмуровке ограждений, так как при нормальной прочности бетона 100—110 кгс/см2 даже сниженная на 50% прочность оказывается достаточной. Кроме того, шамотобетон на глиноземистом цементе имеет более удовлетворительную структуру. Поэтому при сушке и первом разогреве бетона не возникает трещин и разрывов в обмуровке, которые часто имеют место у бетонов на портландцементе (см. гл. 12). Шамотобетон на глиноземистом цементе применяется с 1950 г. и зарекомендовал себя наилучшим образом, особенно при ремонтных работах, когда требуются быстрое затвердение и нарастание прочности. Практически уже через сутки его прочность достигает примерно 70% конечной и позволяет укладывать иа него последующие слои других материалов. Эти свойства шамотобетона на глиноземистом цементе позволяют его рекомендовать как вполне проверенный и надежный жаростойкий материал.
Бетон на шлакопортландцементе
К группе шамотобетонов на портландцементе относятся бетоны на шлакопортландцементе. Эти бетоны обладают низким качеством и применяются при температуре до 600—700"С. Несмотря иа недостатки, шамотобе - тоиы на шлакопортландцементах иногда находят применение при низких рабочих температурах, однако этого следует избегать.
Бетон на жидком стекле
Бетоны на жидком стекле имеют в своем составе шамотный заполнитель и в качестве вяжущего жидкое натриевое стекло Na2Si03. Максимальная рабочая температура применения для бетона иа жидком стекле составляет примерно 900°С. Установлено, что затвердевание бетона иа жидком стекле по всему массиву происходит только в присутствии кремнефторнстого натрия NaaSiFe. Оптимальное количество кремиефтористого натрия должно составлять около 12% массы жидкого стекла. Для обеспечения затвердевания бетона на жидком стекле необходима точная дозировка Na2SiFe по всей массе, а сам крем нефтористый натрий должен быть качественно чистым.
Затвердевание бетона происходит - только в теплой воздушно-сухой атмосфере. Оптимальной температурой затвердевания является температура 30—40°С. Необходимые условия затвердевания для бетона на жидком стекле на монтажных площадках обеспечить не всегда возможно, по этим причинам применение таких бетонов в ограждениях котлов не получило распространения. Преимуществом бетона на жидком стекле является повышение его прочности с увеличением температуры.
Высокотемпературные бетоны
В связи с необходимостью применения жаростойких бетонов для рабочих температур выше 1300°С, например для футеровки горелочиых амбразур, предложены и разработаны иовые составы бетоиов, которые проходят промышленное освоение. Такими бетонами являются:
1. Высокотемпературный бетон для применения при рабочих температурах до 140(^0 с шамотным заполнителем на связке с ортофосфорной кислотой.
2. Бетон для рабочей температуры до 1500°С с высокоглиноземистым заполнителем и цементом.
3. Хромомагиезитовый бетон для рабочей температуры до 1600°С со связкой на жидком стекле с добавлением кремнефторнстого натрня. Этот бетон устойчив по отношению к шлакам, содержащим в избытке основные окислы.
Прн выборе этих бетонов следует иметь в виду дефицитность высокоглиноземнстого цемента н таких же заполнителей. При назначении рецептуры (состава) этих бетонов и технологии выполнения из них футеровки необходимо в каждом случае получать указания от специализированных организаций (НИИЖБ, ОРГРЭС и др.).
Полный механический расчет ограждений современных энергетических котлов связан с расчетами несущего каркаса для накаркасных обмуровок и трубной системы под давлением для иатрубных обмуровок. Отдельно рассчитывается каркас с учетом воздействий на …
17* Первое опробование натрубной изоляции для газоплотных экранов было проведено ЗиО совместно с комбинатом Центроэнерготеплонзоляция (ЦЭТИ) и трестом ОРГРЭС на цельносварной панели СРЧ котла ПК-38 Березовской ГРЭС [12-13]. Рис. 12-11. …
Основной величиной, определяющей расчет ограждений, является температура иа внутренней поверхности обмуровки. Материал футеровки выбирается по максимальной температуре, а расчет потерь теплоты и распределения температур по слоям производятся по средним температурам. …
msd.com.ua
Огнеупорные бетоны :: Огнеупорные материалы в металлургии
ОПРЕДЕЛЕНИЕ Огнеупорными бетонами называют безобжиговые композиционные материалы с огнеупорностью от 1580°С и выше, состоящие из огнеупорного заполнителя, вяжущего материала, добавок и пор, затвердевающие при нормальной или повышенной температуре и обладающие ограниченной усадкой при температуре применения. Огнеупорные мелкоштучные (нормальных размеров) изделия как массовые огнеупорные материалы, несмотря на высокие показатели свойств, имеют и свои специфические технико-экономические недостатки. Производство мелкоштучных огнеупорных изделий трудно поддается механизации и автоматизации, и в настоящее время уровень механизации на огнеупорных заводах составляет немного больше 50%. Механизация кладки различных промышленных печей из нормальных изделий не превышает 5 % и, что особенно важно отметить, требует высококвалифицированного труда каменщиков и часто выполняется в неблагоприятных санитарно-гигиенических условиях. В результате развития техники строительства и эксплуатации печей выявилась целесообразность производства огнеупорных бетонов и замена ими мелкоштучных изделий. Такая замена позволяет полностью механизировать и автоматизировать производство огнеупоров и индустриализировать строительство печей, заменив труд каменщика трудом монтажника. Огнеупорный бетон по структуре является аналогом строительных бетонов. Он состоит из заполнителя и вяжущего и отличается от обычного строительного тем, что имеет огнеупорность выше 1580 °С и сохраняет достаточную строительную прочность в службе, т.е. огнеупорный бетон изготовлен из огнеупорных материалов. Огнеупорные бетоны отличаются от обычных огнеупоров тем, что в результате применения специальных вяжущих материалов образуется прочная камнеподобная структура при нормальной или несколько повышенной температурах, которая не разрушается при высоких температурах службы. Таким образом, при производстве огнеупорных бетонов отпадает необходимость высокотемпературного обжига. В этом отношении огнеупорные бетоны и безобжиговые мелкоштучные огнеупорные изделия аналогичны. Огнеупорные бетоны имеют некоторые преимущества перед обожженными изделиями. При монолитной бетонной футеровке полностью отсутствуют швы в кладке. Обжиг изделий, как правило, происходит в окислительной атмосфере, и фазовый состав обожженных изделий характеризуется соответственно оксидными формами тех или иных компонентов. Служат же эти огнеупоры во многих случаях в восстановительной среде или при температурах, когда оксидные формы становятся неустойчивыми, поэтому в обожженных изделиях любого типа в службе происходят изменения фазового состава, сопровождающиеся часто изменением объема минералов, приводящим к разупрочнению изделий. В технологии обожженных изделий, в процессе их охлаждения, происходит кристаллизация минералов из жидкой фазы, образовавшейся при высоких температурах. В службе наблюдается обратный процесс — растворение этих минералов в жидкой фазе. Поскольку объемы жидкого и твердого состояний различны (для оксидных веществ объем расплава примерно на 10—15 % больше, чем твердого состояния), то при кристаллизации образуется субмикроскопическая пористость, обусловливающая повышение свободной энергии огнеупора. Другими словами, структура и фазовый состав обожженных изделий часто не соответствуют условиям службы. В огнеупорных бетонахструктура и фазовый состав в значительной степени создаются в службе и поэтому находятся в соответствии (равновесии) с условиями службы. Огнеупорные бетоны всегда более термостойки и менее теплопроводны, чем соответствующие обожженные изделия. Во многих случаях огнеупорные бетоны оказываются лучше, чем обожженные изделия. Вместе с тем огнеупорные бетоны всегда менее прочны, особенно к истиранию. Поэтому вообще нельзя противопоставлять огнеупорные бетоны обожженным изделиям.Огнеупорные порошки называют заполнителями (крупный, мелкий, тонкомолотый).В качестве огнеупорных заполнителей применяют материалы, устойчивые в условиях воздействия высоких температур и не образующие с вяжущим легкоплавких эвтектик. В принципе всякий огнеупорный безусадочный материал может быть заполнителем. Размер зерен заполнителя находится в пределах 2—30 мм. Огнеупорные порошки, содержащие все фракции, необходимые для производства бетона, и сухие вяжущие вещества, называют бетонными смесями. Смеси вместе с водой или жидкими затворителями называют бетонными массами.Огнеупорные бетоны классифицируют по типу изделий: бетонные блоки, бетонные смеси, бетонные массы, и виду вяжущих. ВЯЖУЩИЕ МАТЕРИАЛЫ. КЛАССИФИКАЦИЯ Под вяжущим веществом огнеупорных бетонов понимают дисперсионную систему, состоящую из дисперсной фазы (огнеупорного материала крупностью ниже 0,09 мм — цемента) и дисперсионной среды — химической связки. Вяжущее(дисперсная система) = огнеупорный цемент(дисперсная фаза) + химическая связка (дисперсионная среда). Таким образом, вяжущее для огнеупорных бетонов — это дисперсная система, состоящая из огнеупорного цемента и химической связки и обеспечивающая твердение бетонов при низких температурах, сохранение прочности при средних температурах и формирование износоустойчивой структуры вплоть до высоких температур с минимальным снижением огнеупорности.К таким вяжущим предъявляются следующие требования: они должны обладать адгезионными свойствами, обеспечивать достаточную прочность бетона при твердении; не разупрочняться при нагревании; способность формированию износоустойчивой структуры бетона; не снижать огневых свойств бетона. Для каждого вида огнеупорных цементов существует свой, наиболее рациональный состав химической связки, обусловливающий получение огнеупорных бетонов с наилучшими свойствами. Выбор рационального состава цемента и химической связки — один из основных вопросов в технологии огнеупорных бетонов. Вяжущие для огнеупорных бетонов классифицируются на 5 видов: гидратационные, силикатные, фосфатные, сульфатно-хлоридные и органические. Каждый из этих видов вяжущих состоит из огнеупорного цемента и химической связки. 1. Гидратационные вяжущие представляют собой дисперсные системы, в которых дисперсная фаза представлена высокоглиноземистым, глиноземистым, барийалюминатным, периклазоалюминатным и портландским цементами, а дисперсионная среда — водой. 2. Силикатные вяжущие — дисперсные системы, в которых дисперсная фаза представлена различными огнеупорными цементами, а дисперсионная среда — щелочными силикатами, этилсиликатами, кремнезолем и другими растворами, содержащими золи кремнекислоты, стабилизированные различными (главным образом щелочными) добавками. 3. Фосфатные вяжущие — дисперсные системы, в которых в качестве дисперсной фазы используют различные огнеупорные цементы, а в качестве дисперсионной среды — ортофосфорную кислоту (Н3РО4) или водные растворы фосфатов. Обычно в фосфатных вяжущих используют растворы следующих фосфатов: Аl(h3РО4)3, А12(НРO4)3, AlPO4 — алюмофосфатные связки, (А1, Сr)2 (НРO4)3— алюмохромофосфатная связка, Mg(Н2РO4)2 — магнийфосфатная связка, Са(Н2РO4)2 —кальцийфосфатная связка, (NаРO3), — полифосфат натрия, Na5P3O10 — триполифосфат натрия. Кроме этих основных солей, используют технические смеси ортофосфорной кислоты с глиной (глинистофосфатная связка), с доломитом (доломитофосфатная связка) и др. 4. Сульфатно-хлоридные вяжущие — это дисперсные смеси, в которых дисперсная фаза представлена преимущественно магнезиальными цементами, а дисперсионная среда — сульфатами или хлоридами магния, железа и алюминия. Кроме этих соединений, могут быть использованы отработанные растворы травильных ванн. 5. Органические вяжущие — дисперсные системы, в которых дисперсная фаза представлена различными огнеупорными цементами, а дисперсионная среда — органическими соединениями — термореактивными смолами, пеками, СДБ и др. Возможны комбинированные вяжущие, состоящие из смесей различных цементов и химических связок.
markmet.ru
Огнеупорный бетон —– какой лучше выбрать?
При изготовлении доменных и промышленных печек, дымовых труб, пылевых камер, коллекторов, а также различных строительных конструкций часто используется огнеупорный бетон. Он способен выдерживать температуру более 1800° С. Плюс ко всему имеет ряд других преимуществ, которые опишем в статье.
Огнеупорный бетон — разбираем существующие виды ↑
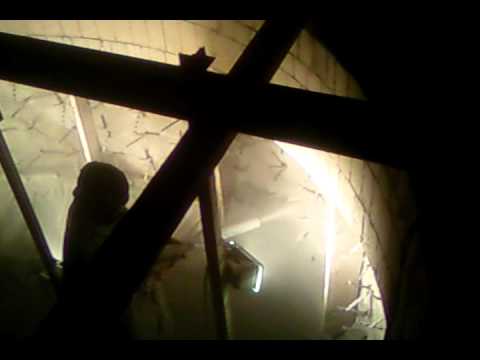
Жаропрочный бетон (иначе его называют огнеупорным или жаростойким) — материал, который сохраняет свои свойства при высоких температурах. Объясняется это тем, что в состав кладут специальные огнеупорные добавки. Обычно, вяжущим компонентом в смеси служит шлакопортландцемент и портландцемент. В качестве заполнителей могут быть различные ингредиенты. Так, для материала, используемого до температуры 800° С, применяют различные материалы:
- Кирпичный бой;
- доменные шлаки;
- горные породы (андезит, диабаз, диорит, натуральные пористые вулканические заполнители и искусственные пористые компоненты (перлит, шлаковая пемза, керамзит).
Если же бетон, будет эксплуатироваться при температуре до 1700° С, то можно использовать следующие заполнители: обожженный каолин, кирпич шамотный, магнезит, корунд, хромит и другие. Если говорить о классификации, то данный материал подразделятся: по структуре (ячеистый, легкий, тяжелый), по назначению (теплоизоляционный, конструкционный), по типу заполнителя, по виду вяжущего компонента (может быть не только портландцемент, но и некоторые его разновидности), по условиям твердения. Чтобы выбрать подходящий, достаточно знать условия, при которых он будет использоваться.
Жаростойкий бетон — сфера применения ↑
Демонстрация сборно—блочной печи из огнеупорного бетонаКонечно, первое, для чего необходим данный бетон, — производство всевозможных фундаментов для тепловых конструкций, изготовления промышленных и бытовых печей, коллекторов, камер. Однако сказать, что этот бетон используется лишь для изготовления печей и дымовых труб нельзя. На самом деле его применяют и во многих других сферах. Так, жаростойкий бетон используется в химической промышленности, при производстве строительных материалов, в энергетической отрасли и других.
Подобный материал применяют и для строительства различных сооружений и зданий. Это могут быть: перекрытия и стены, пролетные мосты, плавучие конструкции, фермы. Основной плюс этого материала заключается в том, что он облегчает сооружение, делает его прочным и надежным. Например, огнеупорный бетон позволяет на 40% уменьшить вес конструкции. Объясняется это тем, что кладут в данные смеси обычно пористые заполнители. Кстати, с такими типами бетонов сокращаются транспортные расходы и трудозатраты.
Технология изготовления огнеупорного материала ↑
Производится данный бетон из вяжущих, воды и всевозможных жаропрочных заполнителей. Сама методика изготовления имеет некоторые особенности. Так, добавляемые ингредиенты должны обладать повышенной чистотой, запрещается засорение тугоплавких и жаропрочных заполнителей песком, гранитом или известняком. В дальнейшем это может привести к разрушению материала. Поэтому в процессе закупки и хранения важно следить за чистотой исходных ингредиентов.
Существует 2 методики производства этого материала — из готовой сухой смеси (уже содержащей все необходимые компоненты) и из отдельных ингредиентов (которые перемешиваются в определенных пропорциях). Наиболее предпочтительным считается первый способ, поскольку производят смесь в заводских условиях с применением только лучших компонентов. Причем исключается их засорение. Таким образом, вы получаете смесь наивысшего качества, готовую к применению. Достаточно лишь добавить затворитель или воду.
Чтобы высокопрочный бетон был более устойчив к воздействию огня, в его состав добавляют тонкомолотые компоненты (андезит, шамотный бой, хромитовую руду, кирпич магнезитовый). При правильном выборе ингредиентов и соблюдении пропорций можно получить материал наилучшего качества, который будет выдерживать высокую температуру, не разрушаясь.
Если вы решили купить готовую смесь, то приобретайте ее только от сертифицированных производителей. В процессе приготовления следуйте всем указанным на упаковке рекомендациям. Как правило, там написан способ изготовления и дальнейшего использования материала. А также описаны условия, при которых он может эксплуатироваться. После использования смесь необходимо хранить в темном месте.
mastter.ru
Огнеупорный бетон - Большая Энциклопедия Нефти и Газа, статья, страница 3
Огнеупорный бетон
Cтраница 3
Огнеупорные бетоны готовят на основе: глиноземистого цемента с песком и щебнем из хромита; жидкого стекла с кремнефтори-стым натрием и тонкомолотой добавкой, песка и щебня из боя магнезитового кирпича или хромита. [31]
Плотные огнеупорные бетоны ( условные марки 8 и 9) предназначены для футеровки отдельных участков шахтной печи. Бетоны имеют различную прочность после сушки, не разрушаются при обжиге, характеризуются повышенными высокотемпературной прочностью и термостойкостью, выдерживают без изменений испытание на устойчивость к СО в течение 500 ч при 500 С. Легковесные огнеупорные бетоны ( условные марки 20 и 21) кажущейся плотностью 1 40 - 1 55 г / см3 с открытой пористостью - 40 % используют для внутренней теплоизоляции трубопроводов нагретого воздуха, футеровки крышек и других элементов рекуператора. [32]
Однако огнеупорные бетоны исследованы недостаточно. Данные о них не систематизированы, что затрудняет проектирование футеровок тепловых агрегатов из огнеупорных бетонов. [33]
Раствор огнеупорного бетона готовится предварительно тщательным перемешиванием вышеперечисленных компонентов с последующим добавлением воды до необходимой консистенции. [35]
Схватывание огнеупорного бетона на глиноземистом цементе происходит в течение двух-четырех часов, после чего его прочность быстро нарастает; через сутки она достигает почти 70 % от прочности двадцативосьмисуточного срока. Температура в бетоне для жаростойких конструкций и изделий должна повышаться медленно, пока бетон не будет достаточно высушен. [36]
Подачу огнеупорных бетонов к месту укладки производят в бункерах, которые транспортируют в рабочую зону при помощи монтажных кранов. [37]
Применение огнеупорных бетонов позволяет получить существенный технико-экономический эффект. [38]
Маркировка огнеупорных бетонов производится в следующем порядке ( табл. 3): на первое место ставится буква ( буквы), обозначающая минеральный состав заполнителя, на второе - вид бетона ( блоки, массы, смеси), на третье - способ изготовления его. Далее через дефис ставится цифра, обозначающая номер огнеупорного цемента в соответствии с табл. 3, затем цифра, обозначающая номер химической связки, и на последнее место - цифра, обозначающая особенность технологии изготовления бетона. [39]
Разупрочнение огнеупорных бетонов в области средних температур ( 600 - 1000 С) связано с потерей химически связанной воды, разрушением кристаллизационно-конденсационной структуры и превращением ее в кристаллизационную структуру. [40]
Свойства огнеупорных бетонов были определены как стандартными, так и нестандартными методами, применяемыми в настоящее время для исследований свойств традиционных огнеупорных материалов. Перечень методик, использованных при исследовании свойств огнеупорных бетонов, приведен ниже. [41]
Ползучесть огнеупорных бетонов определяют при сжимающих осевых нагрузках образцов-цилиндров высотой 50 мм и диаметром 36 - 38 мм. Испытания проводят на стандартном приборе для определения температуры деформации под нагрузкой. Образец помещают в криптоловую печь, прикладывают к нему определенную нагрузку ( 0 2 - 0 4 МПа) и нагревают до заданной температуры. [43]
Производство огнеупорных бетонов и неформованных огнеупоров в настоящее время сосредоточено на следующих предприятиях: Первоуральском динасовом заводе, Христофоровском заводе огнеупорных блоков и бетонов, Боровичском комбинате огнеупоров, комбинате Магнезит, Пантелеймоновском огнеупорном заводе, Семи-лукском огнеупорном заводе, Суворовском рудоуправлении, Новомосковском огнеупорном заводе, Кузнецком металлургическом комбинате. [44]
Приготовление огнеупорного бетона осуществляется в обычных бетономешалках, применяемых для строительных бетонов. Предварительно в бетономешалку заливается вода, количество которой определяется опытным путем с таким расчетом, чтобы осадка конуса бетона была бы в пределах 3 - 5 см. Затем загружается мелкий заполнитель, цемент и крупный заполнитель. При малых расходах бетона приготовление его может производиться вручную. В этом случае отмеренные компоненты перелопачивают на бойке в сухом состоянии до однородного состава смеси, после чего заливают при непрерывном перемешивании водой, взятой в количестве с учетом заданной осадки конуса. [45]
Страницы: 1 2 3 4
www.ngpedia.ru
Применение связующих в производстве огнеупорных и жаростойких бетонов и масс
Применение связующих в производстве огнеупорных и жаростойких бетонов и масс
Жаростойкие и огнеупорные бетоны и массы используются при возведении и эксплуатации сооружений, конструкций и агрегатов, работающих в условиях повышенных и высоких температур.
Главные области применения огнеупорных и жаростойких бетонов и масс: черная и цветная металлургия, теплоэнергетика, химическая промышленность, керамическое производство.
Различие между бетонами и массами при одинаковых составах заключается в том, что бетоны используются в виде заранее отформованных изделий, конструкций, деталей, а массы применяются для проведения ремонтных работ, в том числе по бетону, а также в качестве поверхностной защиты, наносимой разбрызгиванием (набрызг-бетон) или в принудительном режиме (торкрет-массы).
Согласно официальной номенклатуре (ГОСТ 20910, ГОСТ 25192), по допустимой температуре применения бетоны делятся на классы от «3» (до 300 °С) до «18» (до 1800 °С). По огнеупорности бетоны и массы подразделяются на жароупорные с огнеупорностью ниже 1580 °С и огнеупорные — выше 1580 °С. Бетоны и массы, используемые при повышенных и высоких температурах, различаются также термической стойкостью — количеством воздушных и водных теплосмен, которые они способны выдержать без разрушения.
Вещественный состав жаростойких и огнеупорных бетонов и масс такой же, как у обычных материалов: связующие (вяжущие) компоненты, заполнители, возможно использование добавок различного назначения — пластификаторов, регуляторов схватывания и т. д.
Твердение жаростойких и огнеупорных бетонов происходит за счет химического взаимодействия компонентов при температурах от комнатных до 600 °С.
По объемной массе бетоны делятся на тяжелые (более 1500 кг/м3) и легкие (менее 1500 кг/м3). Процесс производства жаростойких и огнеупорных бетонов и масс аналогичен производству обычного бетона.
Наиболее распространенным и широко освоенным связующим для жаростойких бетонов является жидкое стекло. Основным видом жидкого стекла, применяемого для производства жаростойких (огнеупорных) бетонов, является натриевое жидкое стекло (ГОСТ 13078). В некоторых разработанных рецептурах рекомендовано использование измельченной силикат-глыбы (ГОСТ 13079).
Для отверждения жидкого стекла в состав жаростойких бетонов вводят кремнефтористый натрий, а также вещества, содержащие двухкальциевый силикат,—нефелиновый шлам (попутный продукт переработки щелочных алюмосиликатов на глинозем), шлаки феррохрома, ферромарганца, некоторые виды сталерафинировочных шлаков, содержащих у-форму Ca2Si04.
Взаимодействие отвердителей с жидким стеклом обеспечивает необходимую сырую (манипуляторную) прочность, а также требуемую конструкционную прочность, в формировании которой участвует также термоупрочнение за счет прогрева бетона. В дальнейшем, в ходе высокотемпературной эксплуатации, наблюдается характерное терморазупрочнение бетона, составляющее для бетонов на жидком стекле 20—30%. Это связано с дегидратацией продуктов твердения жидкого стекла и в определенной степени может компенсироваться процессами высокотемпературного спекания.
Несмотря на низкую собственную огнеупорность (-800 °С) жидкостекольной связки, огнеупорные бетоны различного состава на ее основе могут характеризоваться высокой огнеупорностью (до 1600 °С), определяемой результатами взаимодействия в системе жидкое стекло — наполнитель в области высоких температур, а также макроструктурой сформировавшегося спека. Высокотемпературные процессы, протекающие в силикатной связке при высоких температурах, зависят от вида примененного от-вердителя и включают удаление адсорбционной воды (воды, связанной гелем кремнекислоты), дегидратацию гидросиликатов натрия и гидросиликатов кальция, а также образование натриево-кальциевых силикатов и, вероятно, низкоосновных силикатов кальция. При температуре выше 1000 °С в системе появляется расплав, при охлаждении образующий стеклосвязку.
Высокотемпературные процессы в системе жид-костекольная связка — огнеупорный наполнитель значительно более сложные и изучены недостаточно. Огнеупорный наполнитель в тонкодисперсном состоянии вступает в заметное взаимодействие с продуктами твердения жидкого стекла при температурах выше 600 °С. Продукты этого взаимодействия, как правило, не являются равновесными фазами в соответствующих системах (например, в системах MgO — Na20 — Si02, Al203-Na20-Si02 и т. д.) и представляют собой в ряде случаев аморфные фазы переменного состава, различные полупродукты, конгломераты трудноидентифицируемых соединений и др.
Жидкое стекло применяется для изготовления бетонов трех основных видов — кремнеземистых, алюмосиликатных и магнезиальных. В кремнеземистых бетонах заполнителями являются кварцит и динас, эти же вещества используются в качестве тонкомолотого компонента. В зависимости от конкретного состава содержание жидкого стекла в бетонной смеси находится в пределах 6,5—18,0 мас.. Важной практической характеристикой жидкого стекла является его плотность: с увеличением плотности от 1,2 до 1,4 г/см3 сроки схватывания кварцитовых бетонов увеличиваются, возрастает также прочность бетона на сжатие. Примеры составов и свойств огнеупорных бетонов приведены в табл. 85. Фазовый состав кремнеземистых бетонов, применяемых в условиях высоких температур, характеризуется кристаллическим сростком полиморфных модификаций Si02 и жидкой фазой, содержание которой пропорционально количеству связующего. При увеличении количества жидкого стекла от 4 до 15 огнеупорность бетона падает с 1700 до 1560 °С.
В алюмосиликатных бетонах используют шамотные, мулли-токремнеземистые и муллитовые заполнители, обеспечивающие температуру эксплуатации таких бетонов до 1600 °С. В высокоглиноземистых бетонах применение жидкого Стекла нецелесообразно.
К магнезиальным бетонам на жидком стекле относится группа составов, включающая в качестве заполнителей периклаз, магнезиально-шпинелидные заполнители (периклазохромитовые, хромитовые, периклазошпинелидные и др.), а также маг-незиально-силикатные заполнители (периклазофорстеритовые, форстеритохромитовые, форстеритовые и др.).
Из бетонных смесей, включающих жидкое стекло, огнеупорный наполнитель и добавки, изготавливают наряду с тяжелыми бетонами также легкие и ячеистые. В легких огнеупорных бетонах в качестве заполнителя используют керамзит. Пористая структура газобетона формируется за счет введения газообразо-вателя в состав тонкомолотой массы с последующим автоклавным твердением бетона.
Широко распространенной основой для получения жаростойких и огнеупорных бетонов и масс являются фосфатные вяжущие системы. Благодаря высокой химической активности и хорошей связующей способности фосфорнокислых растворов в таких системах в качестве порошковой составляющей чаще всего выступают собственно огнеупорные материалы, которые по отношению к воде, как правило, химически инертны. Взаимодействие компонентов в этих бетонах приводит к образованию цементирующих фаз, обладающих устойчивостью в условиях повышенных и высоких температур.
Таким образом, на основе фосфатных вяжущих систем изготавливаются жаростойкие и огнеупорные бетоны и массы, по своим техническим свойствам часто превосходящие другие виды аналогичной продукции.
Динасовые бетоны и массы изготавливают из размолотого динаса и концентрированной ортофосфорной кислоты или гли-ноземсодержащих связок с включением либо без включения крупного огнеупорного заполнителя. Для таких бетонов характерно высокое постоянство объема до 1700 °С, что является весьма ценным отличительным свойством, огнеупорность 1750 °С, температура деформации под нагрузкой 1660 °С, прочность при сжатии до 40 МПа. Материалы этого вида используются в качестве набивочных масс для сталеразливочных ковшей, индукционных печей, для изготовления блоков к мартеновским, нагревательным, стекловаренным печам.
Кварцевые бетоны на основе кварцитов, кварцевых песков в сочетании с фосфатными затворителями часто дополняются глиной и используются для футеровок сталеразливочных ковшей, фурм доменных печей и других конструкций. Недостатком таких бетонов является понижение их прочности при температурах 600—700 °С в связи с модификационным переходом силикатной основы а-кварц и в случаях образования AIPO4 (при участии глинистых минералов и (или) алюмофос-фатной связки) — а-А1Р04 -1/3-А1Р04- Как известно, AIPO4 является полным кристаллохимическим аналогом SiC>2. Температура деформации под нагрузкой у кварцевых бетонов составляет 1640 °С, прочность —до 25 МПа.
Шамотные бетоны и массы на основе молотого шамота и фосфатных затворителей, часто с включением в состав технического глинозема, характеризуются значительным ростом прочности при повышении температуры от 300 до 1300 °С, огнеупорностью 1660 °С, температурой деформации под нагрузкой 1410 °С, прочностью 40 МПа и более.
Высокими техническими свойствами обладают фосфатные бетоны на глиноземсодержащих материалах. Так, корундмулли-товый фосфатный бетон, представляющий собой композицию из корунд мулл итового шамота (95%), глины (5%) и фосфорной кислоты, обладает огнеупорностью до 1850 °С при деформации под нагрузкой при 1570 °С. Прочность при сжатии таких бетонов может достигать 80 МПа.
До сих пор мы рассматривали бетоны и массы, для отвердевания которых требуется повышение температуры (практики называют это не совсем правильно «сушкой») в пределах 100— 600 °С. Магнезиальные фосфатные бетоны, как правило, отвердевают при обычных комнатных температурах, так как в основе этого процесса лежит взаимодействие оксида магния с ортофосфорной кислотой, имеющее большую интенсивность. Главная химическая реакция при твердении магнийфосфатных вяжущих систем
MgO + h4P04+2h30 • MgHP04 • 3h30
протекает со значительным тепловыделением (105 кДж/моль).
К группе магнезиальных фосфатных бетонов относятся сочетания MgO, а также магнезиальных минералов и пород, например форстерита (2MgO • SiC>2), дунита ((Mg, Fe)3Si205(OH)4), магнезиальных шпинелей (MgO • AI2O3; AI2O3 • СГ2О3) с орто-фосфорной кислотой или растворами алюмо-, алюмохром-, ам-монийфосфатов, щелочных полифосфатов. Температура деформации под нагрузкой таких бетонов ниже, чем силикатных или алюминатных, и составляет 1100—1200 °С, хотя огнеупорность их достаточно высока и достигает 1650 °С. Преимуществом этого вида огнеупоров, помимо твердения в обычных условиях, является высокая прочность, достигающая 80—120 МПа.
Кроме перечисленных выше огнеупорных и жаростойких фосфатных бетонов и масс, уже имеющих достаточно широкое распространение, следует указать и некоторые другие материалы, перспективность которых для практики доказана. Это прежде всего хромитовые бетоны. Их порошковая часть представлена хромитовой рудой или хромоглиноземистыми шлаками, а за-творитель — чистой кислотой, растворами алюминия или магния. Такие бетоны имеют высокую (до 70 МПа) прочность при температурах 800—1450 °С и деформации под нагрузкой при 1350-1400 °С.
Циркониевые бетоны на основе двуокиси циркония ZrC>2 или циркона ZrC>2 • SiC>2 также обладают высокой прочностью и при этом значительно большими значениями температуры деформации под нагрузкой (выше 1600 °С).
Огнеупорные и жаростойкие бетоны и массы на основе фосфатных вяжущих систем испытаны и могут применяться во многих промышленных конструкциях, агрегатах и узлах. Так, в доменных печах фосфатные бетоны используются для футеровки фурм, сопел, где температуры достигают 1000—1200 °С.
Фосфатные бетоны конкурируют с штучными огнеупорами при футеровке мартеновских печей и сталеразливочных ковшей, причем в последнем случае они используются в качестве набивочных масс, т. е. засыпка производится по месту.
Фосфатные бетоны и массы рекомендованы к применению в агрегатах индукционной плавки редких металлов, меди, цинка, алюминиевых сплавов. В этих случаях с применением фосфатных бетонов и масс изготавливаются тигли, футеруются печи, причем металло- и шлакоустойчивость таких объектов во многих случаях выше, чем при использовании традиционных материалов.
Имеется значительный опыт применения фосфатных огнеупорных бетонов и масс при футеровке нагревательных, шахтных и вращающихся печей в черной металлургии, при производстве глинозема и цемента.
Фосфатные бетоны и массы используются в стекловаренных печах, туннельных печах для обжига керамики. Варианты применения этих материалов различны: для торкретирования огнеупорных кладок с целью увеличения срока их службы; в качестве основы самой кладки. Особенно эффективны они при защите подин вагонеток, работающих в режиме до 1700 °С. Известны многочисленные примеры использования фосфатных бетонов и масс в качестве мертелей для огнеупорных кладок различного назначения.
Фосфатные бетоны и массы — прогрессивный, технически и технологически эффективный материал, позволяющий решать сложные задачи по сооружению и защите тепловых агрегатов различного назначения.
Читать далее:Кислотостойкие материалыЗубные цементыПрименение связующих в электродно-флюсовом производствеПрименение связующих в литейном производствеЗащитно-декоративные покрытия на основе неорганических связующихСвязующие для укрепления грунтовСвязующие для безобжигового окускования руд и рудных концентратовЗоли кремнеземаСухие щелочные силикатные связки (порошки)Силикаты органических оснований
stroy-server.ru
Бетоны огнеупорные - Справочник химика 21
Огнеупорный бетон. Наряду с кислотоупорными бетонами большое применение в про- мышленности находят огнеупорные бетоны. Огнеупорными. называются бетоны, приготовленные из вяжущих составов и огнеупорных наполнителей. т [c.188]Бетон огнеупорный Легковесный кирпич То же....... [c.80]
Производство доломита Производство плавленых огнеупоров Производство молотых материалов и бетонов Огнеупорные изделия в СРР [c.93]
Вертикальные стены газоходов выложены из огнеупорного кирпича виде газосборных стен-решеток. Перекрытия газоходных туннелей выполнен из муллито-коруидовых плит илн бетонных огнеупорных блоков. [c.352]
Временной метод прохождения (временной теневой метод, рис. 2.4, ) основан на измерении запаздывания импульса, вызванного огибанием дефекта. При этом в отличие от велосиметрическо-го метода тип упругой волны (обычно продольной) не меняется. В этом методе информационным параметром служит время прихода сквозного сигнала. Метод эффективен при контроле материалов с большим рассеянием УЗ, например бетона, огнеупорного кирпича и т.п. [c.133]Дня гидротехнических и подводных работ, в том числе аварийных для цементации грунта при зимнем и скоростном строительстве для изготовления ж оупорных бетонов. Огнеупорность с использованием шамота в качестве наполнителя (1200-1300 °С) [c.309]
Материалы неорганического происхождения — это цемент, бетон, торкрет-бетон, огнеупорный кирпич, кислотоупоры, керамические плитки, асбест, андезит, эмали и др. Материалы органического происхождения — это, прежде всего," пластические массы (фао-лит, винипласт, полиэтилен, текстолит, фторопласт и др.), графит и графитонласты, стеклопластики, замазки и лакокрасочные материалы. Они обладают повышенной коррозионной стойкостью к действию кислот и щелочей, позволяют обеспечить защиту аппаратов и строительных конструкций от атмосферной кор" розии. [c.255]
Наименование бетона Огнеупорность, °С Объемный вес, m M Коэффициент теплопроводности, KKajijM час °С Временное сопротивление сжатию, K3 M Максимально допустимая температура применения, °С Определение термостойкости [c.250]
chem21.info