Купить строительное оборудование, инструменты и садовый инвентарь. Технология устройства бетонных полов
Устройство промышленных бетонных полов

Бетонный промышленный пол довольно прочен, способен выдерживать высокие эксплуатационные нагрузки. Технологии устройства подобных покрытий хорошо изучены, просты в реализации и не вызывают слишком высоких затрат. Это оптимальное решение для производственных условий, как внутри, так и снаружи помещений.
Основные требования
Полы промышленных помещений всегда подвержены высоким нагрузкам. Технология реализуется исключительно за счет применения бетонных, цементно-песчаных растворов. В процессе работ используются современные армирующие материалы, специальные добавки, усиливающие прочность и конечные характеристики покрытия.
При выборе типа конструкции учитывают условия эксплуатации и специальные требования, предъявляемые к промышленным полам. Это может быть скользкость, теплоусвоение, беспыльность, антистатичность и проч. Работы нормируются действующими техническими условиями, нормами СниП.
В производственных условиях задействуются следующие разновидности:
- бетонные промышленные полы для мест с умеренной нагрузки;
- бетонные промышленные полы для мест с высокой нагрузкой;
- бетонные промышленные полы для мест со сверхвысокой нагрузкой.
Особенности технологии зависят от того, на какое основание проводится укладка. Если основой выступает грунт, конструкция пола становится более сложной.
По плитам перекрытия работать легче за счет меньшего количества слоев
Устройство бетонного пола в промышленном здании по грунту
Такие полы устраиваются повсеместно, — в цехах по производству бытовой химии, текстиля, пищевой промышленности и т.д.
Возможно два варианта развития событий:
- на подготовленное основание (уплотненный грунт) заливается плита, жестко связанная с основанием;
- на подготовленное основание заливается плита, не связанная с основанием – плавающая стяжка.
Уплотнение и подготовка
Технология уплотнения грунта должна соблюдаться максимально точно. В противном случае конструкция даст усадку и трещинообразование. Грунт не должен допускать деформации готового промышленного пола вследствие сил пучения и просадки.
Засыпное основание – песок проливают водой и трамбуют слоями 10-15 см. Чтобы обеспечить максимальное уплотнение, применяют щебеночную засыпку на основе крупнофракционного материала. При проходке трамбовки он способствует возникновению локального удара, что работает на глубинное доуплотнение нижних слоев.
Для засыпки песчаной подушки применяют песок с коэффициентом уплотнения 0.96-0.98. Толщина подсыпки составляет 30-150 см. Дополнительно используется щебень фракции 5-20 мм, слоем до 15 см. Контролируется послойная трамбовка.
Этот этап выглядит следующим образом:
- на грунт раскидывают песок 10-15 см;
- слой сначала уплотняют насухо;
- проводится проливка слоя методом распыления воды;
- проводится уплотнение виброплитами в два рабочих подхода со сменой ориентации трамбовки;
- поверхность еще раз увлажняется и трамбуется в 2-3 подхода;
- засыпается и уплотняется щебень.
На практике количество слоев песка может варьироваться в зависимости от фактических условий работ. В любом случае должна обеспечиваться толщина подложки – не менее 100 мм. Песок увлажняется на 7-10%, не более, поэтому его рекомендовано поливать водой методом распыления, а не полива.
Жесткий подстилающий слой
По технологии жесткий подстилающий слой может устраиваться вместо песчано-щебеночной засыпки. Он заливается на основе высокопрочного бетона. Прочность на сжатие не должна быть ниже 30 МПа. В рецептуру можно вводить модификаторы, способствующие повышению водонепроницаемости и водостойкости. Минимальная толщина слоя – 120 мм.
Жесткий подстилающий слой укладывают полосами, шириной не более 4.5 м по рейкам. Стяжка обязательно уплотняется глубинными вибраторами или виброрейками, заглаживается. Вместо виброуплотнения допустимо использовать вибровакуумирование. После монтажа в течение 7-10 суток бетон должен находиться под слоем п/э пленки.
Если впоследствии будет устраиваться обмазочная или оклеечная гидроизоляция, поверхность следует прогрунтовать растворами на основе битума. Материал разводится в растворителе 1:2 и наносится краскопультом через 30 минут после укладки раствора. Эта пленка предотвратит быстрое высыхание слоя, тогда укрывной материал не требуется.
Деформационные швы нарезают спустя 48 часов твердения бетона
Необходимо предусмотреть устройство деформационных швов. Для этого проводятся пропилы бетона фрезой на глубину на 1/3 от толщины слоя.
Гидроизоляция
После трамбовки подложки или устройства жесткого слоя приступают к монтажу гидро-, пароизоляции. Для устройства промышленного пола по грунту достаточно использовать плотную п/э пленку, толщиной 150-200 мкм.
Материал настилается внахлест 15-20 см, с последующей проклейкой стыков водостойким скотчем. Допустимо укладывать изоляцию в два слоя. Обязателен заход на стены и контроль качества укладки по углам.
В качестве альтернативного материала можно использовать битумно или битумно-полимерные мастики (жидкая, рулонная гидроизоляция). Материал укладывается или наносится в 3-4 слоя.
Чтобы обеспечить защиту от действия химии и агрессивных жидкостей, защита выполняется на основе клеевых мастик и рулонных материалов, для которых характерна химическая стойкость.
Утепление
Требуется применение материалов высокой плотности. Это могут быть плиты экструзионного пенопласта или минваты, стекловолокна на синтетической связке (плотностью до 150 кг/м3). Чтобы достичь высокой теплоизоляционной эффективности выполняется слой, толщиной от 50 мм. Оптимально – 100 мм. Плиты и маты укладывают насухо так, чтобы была обеспечена плотность стыков между ними.
В ряде случаев допустимо использовать кварцевый или керамзитовый песок. Материал рассыпают слоями, разравнивают и уплотняют. В местах примыканий устраивают зазор не менее 2 см. Он заполняется лентой из звукоизоляционного материала, например, пенополиэтилена, пенополиуретана (демпферная лента).
Вторая черновая стяжка армированная (прослойка)
Раствор укладывается по уложенной стальной арматурной сетке. Размер ячейки 10*10 см. Материал усилит прочность готового пласта. Бетон должен быть рассчитан на нагрузку 30 МПа. Минимальная толщина слоя – 100 мм. Чтобы усилить запас прочности в рецептуру можно вводить металлическую фибру длиной 50-80 мм, d 0.3-1 мм. При этом бетон должен содержать максимально крупный заполнитель – 20 мм.
Рекомендовано предусмотреть нарезку деформационных швов, которые должны совпадать со швами подстилающего слоя, с осями колонн, с границами слоя арматуры. Ширина швов принимается за 3-5 мм, глубина – 1/3 от толщины покрытия.
Чистовая стяжка
Стяжка может быть реализована в монолитном и сборном варианте. В промышленных условиях наиболее востребована первая технология. Для монолитной стяжки допустимо применять бетонные, растворные смеси, в том числе на основе гипса и асфальтобетона. Если принято решение о заливке бетонной стяжки, крупным заполнителем выступает гравий или щебень фракции 5-15 мм, портландцемент М500.
Готовая стяжка может быть подвергнута дополнительной обработке (шпатлеванию, затирке, упрочнению)
Толщина слоя может варьироваться от 30 до 50 мм. Для устройства самовыравнивающихся систем рекомендовано использовать сухие смеси заводского изготовления.
Напольное покрытие
Перед нанесением покрытия поверхность фрезеруется или обрабатывается дробеструйными установками. Деформационные швы, которые были устроены ранее, предварительно заполняются эпоксидной шпатлевкой. Рабочий состав наносится на бетон методом налива или по послойной технологии. Лицевые слои обрабатываются игольчатым валиком, — прокатка необходима для удаления вовлеченных пузырьков воздуха.
Используемые материалы должны иметь санитарно-эпидемиологическое заключение, сертификаты по пожарной безопасности.
Особенности устройства промышленных полов для высоких нагрузок
К подобным помещениям относятся производственные цеха (по изготовлению мебели, пластика, резины, целлюлозы, бумаги), ангары, парковки, стоянки. Такие полы должны справляться с интенсивными нагрузками, поэтому для работы привлекаются более прочные материалы. Технология содержит дополнительные этапы.
Структура промышленного пола с высокими эксплуатационными нагрузками:
- черновая армированная стяжка – тут необходим армированный бетон прочностью 35 МПа. Армирование может быть реализовано при помощи металлической фибры, введенной в раствор или при помощи сетки с размером ячейки 10*10;
- гидроизоляция – укладывается два и более слоя рулонной гидроизоляции или три слоя жидкой мастики. Оптимально применять полимер-битумные или битумные материалы;
- вторая армированная черновая стяжка – применяется бетон прочностью 35 МПа. Толщина не может быть меньше 150 мм. Раствор замешивается с крупнофракционным наполнителем. Требуется уплотнение вибраторами;
- чистовая стяжка – выполняется на основе цементно-песчаных растворов высшей марочной прочности;
- напольное покрытие – слой должен обеспечить высокую прочность, потому выполняется на основе эпоксидных составов с кварцевым наполнителем.
Укладка чистовой стяжки ведется после схватывания предыдущего слоя. Толщина – 30-50 мм
Особенности устройства промышленных полов со сверхвысокими нагрузками
Сверхвысокие нагрузки присутствуют в цехах по производству тяжелых машин, судо-, авиастроения, на рампах, на предприятиях металлообработки. Тут присутствуют статические, ударные и вибрационные, шумовые нагрузки от автоматических линий, станков, оборудования.
Для устройства полов применяются сверхпрочные бетоны, специальные добавки. В обязательном порядке проводится армирование каждого чернового слоя.
Структура конструкции:
- армированная черновая стяжка – используется бетон прочностью 35-40 МПа. В рецептуру вводятся модификаторы прочности, металлическая фибра. Допустимо вводить фибру от целлюлозного или стекольного производства. Слой стабилизирует грунт и служит основой для гидроизоляции;
- гидроизоляция – выполняется типичным образом, но количество слоев можно увеличить до 3-4-х;
- вторая армированная черновая стяжка – основа – высокопрочный бетона с прочность 40 МПа на сжатие, 1.5 МПа – на разрыв. Толщина – 150 мм. Готовая поверхность должна быть подвергнута фрезеровке;
- специальное напольное покрытие – применяется эпоксидный состав с песчаным наполнителем размером до 1 мм. Толщина – 5-10 мм. Поверхность в обязательном порядке грунтуется.
Устройство теплого пола на бетонном основании + перекрытии
Технология реализуется в том случае, если такие нагрузки предусмотрены перекрытием и его несущими элементами. Если нет необходимости в утеплении, система содержит меньшее количество слоев. Если перекрытие расположено над неотапливаемым помещением, теплоизоляции не избежать, — в этом случае материал укладывается на основу.
Промышленные полы, устраиваемые по перекрытиям, должны соответствовать требованиям по звукоизоляции, в соответствии с нормами СниП.
Общая конструкция выглядит так:
- подготовленная основа;
- гидроизоляция, утепление;
- черновая стяжка — этот этап необходим, если плита характеризуется существенными отклонениями, которые не способна перекрыть чистовая стяжка. Основа – раствор из мелкофракционного наполнителя, толщиной 30 мм. Прочность – 30 МПа;
- слой армирования + система теплого пола;
- чистовая стяжка — Толщина слоя – 40-80 мм. Укладка производится стандартным образом, требуется выравнивание и выглаживание.
- напольное покрытие — слой выполняется с применением современных наливных составов в основе которых лежат синтетические смолы, полимеры.
Принципы проектирования
Резонно устраивать напольное отопление в открытой центральной части помещения, свободной от оборудования
Изначально следует определить площадь поверхности и схему размещения труб с теплоносителем. Система теплого пола не должна занимать все помещение, исключаются участки под оборудованием и проч.
Следует рассчитать толщину «пирога». На практике высота конструкции варьируется между 120-200 мм, в зависимости от механической и тепловой нагрузки (торговое помещение, склад, ангар и т.д.). Обязательным является наличие армирующей основы.
Диаметр используемых труб должен составлять не менее 20 мм. Следует привлекать материал с кислородозащищенным слоем, соблюдая шаг укладки 20-22 мм.
Подготовка
Если в помещении есть старая стяжка, ее осматривают на предмет целостности. Поводом к демонтажу могут послужить выбоины, сколы, перепады по высоте, а главное — укладка теплого пола. Работы проводятся с участием бетонорезов, углошлифовальных машин, перфораторов, отбойных молотков. На труднодоступных участках действуют вручную, используя бетоноломы, зубила и молотки.
Если работа ведется по готовому бетонному основанию, его осматривают на предмет повреждений и трещин. Если таковые имеются, проводится ремонт. Важный этап подготовки — выравнивание. Для этого устраивается тонкая сухая стяжка, например, на основе керамзита или традиционная черновая стяжка, толщиной 30 мм.
Пренебрегать качественным выравниванием нельзя, так как все оставшиеся неровности в течение эксплуатации будут провоцировать просадку системы, повреждение финишного покрытия, образование тепловых ям. Далее реализуется монтаж пароизоляции и утеплителя. Это слой п/э пленки, плит минеральной ваты либо стекловаты. Толщина теплоизоляции не должна быть ниже 10 см.
Если основание неровное, устраивается выравнивающая стяжка, толщиной 10-15 см, что зависит от механической нагрузки (электрокары, погрузчики). Обязательно устраиваются термошвы, на глубину 5-7 см, — они снимут внутренние напряжения. По периметру помещения и по всем вертикальным конструкциям пускают демпферную ленту.
Разметка труб
Третьим шагом целесообразно провести разметку труб, с учетом мест подключения. Предпочтительно использовать трубы на основе сшитого полиэтилена. Материалы первого поколения оснащены кислородозащищенным слоем и дают высокое качество и надежность. Такие трубы достаточно жесткие, хорошо держат углы. Благодаря тому, что отсутствует алюминиевый слой, можно говорить о высоком коэффициенте удельного расширения. При монтаже обязательно заключение труб в гофру на границе выхода двух сред.
При больших объемах работ удобно работать бухтами до 600 м. Так можно реализовать монтаж различных по длине контуров, не имея при этом стыков. Но, требуется установить коллекторы с расходомерами.
Как определиться с методами регулировки
Первое решение: подача теплоносителя идет непосредственно из магистрали. Рабочая температура – 60-70 градусов. Требуется установка насоса, обратного клапана, накладного температурного датчика. На обратной стороне датчика регулируется включение-выключение системы. По мере остывания теплоносителя, включается насос и в трубы подается новая порция горячей воды.
Подключение системы к центральной тепломагистрали экономически выгодное в виду невысоких финансовых затрат
Второе решение: реализуется система регулировки с монтажом клапана + термостатической головки с выносным температурным датчиком, насоса. Головка с датчиком фиксируются на обратной стороне коллектора. Регулировка происходит путем подмеса горячей воды по мере остывания теплоносителя. В зависимости от установленной температуры, срабатывает датчик, клапан открывается и подается горячая вода.
Третье решение: система регулировки реализуется за счет сборного модуля подвеса. Он монтируется непосредственно перед распределительным коллектором системы теплого пола. Это тоже эффективно, удобно, не очень затратно. Узел размещается в распределительном шкафу, который может иметь внутреннее или наружное исполнение.
Четвертое решение: регулировка происходит за счет трехкодового клапана. Это может происходить вручную или при помощи сервопривода. Последний вариант с жк-дисплеем весьма удобен, но дорог. Обязательным является наличие насоса. Плюс, предпочтительно озаботиться наличием мониторинга температуры за счет погружных термометров. Сэкономить на эксплуатации позволят энергосберегающие насосы. Эта система контроля позволяет автоматически настраивать работу системы теплый пол, что очень удобно, но опять же – дорого.
Дополнительная регулировка температур в каждом отдельном помещении может быть реализована посредством монтажа сервиприводов закрытого или открытого типа. Установка осуществляется непосредственно на коллекторе с подключением терморегуляторов с датчиками температуры воздуха и пола. Это потребует дополнительных финансовых вливаний, но принесет выгоду в процессе эксплуатации.
Схема укладки
На практике схема укладки определяется с опорой на оптимальное расположение контуров отопления и коллекторной группы. Схема должна исключать нахлест труб. Более целесообразным шагом в этом плане становится укладка «улиткой» с шагом 150 мм. Таким образом, обеспечивается равномерное распределение тепла по всей площади. Метод позволяет уменьшить шаг краевых зон до 100 мм. Второй популярный тип – змейка актуален на малых площадях.
Монтаж ведется на арматурную сетку с ячейкой 100*100 мм. Крепление труб может осуществляться любым удобным способом. На готовую систему заливается стяжка. Это проверенная и надежная практика. Толщина стяжки в системе теплого пола – минимум 40 мм над трубой, оптимально – 60-80 мм, если соблюден шаг трубы 150 мм.
Чем плотнее стяжка, тем лучше. Это обеспечит эффективную теплопередачу, по сравнению с более пористыми материалами. За основу предпочтительно взять песчано-цементную смесь. Цемент и песок берутся в соотношении 1:3. В рецептуру вводится фиброволокно 1 кг на 1 куб.м. раствора, пластификаторы.
Не лишним будет озаботиться установкой клапанов автоматического удаления воздуха, так как для теплых водяных полов – это извечная головная боль
Залог длительной эксплуатации – пневматическая или гидравлическая опрессовка системы перед заливкой.
Основные нормы техники безопасности
Устройство промышленных бетонных полов реализуется специализированными бригадами, имеющими лицензию на производство таких работ. Рабочие должны пройти медосмотр, обучение нормам ТБ, мерам пожарной безопасности. Проведение инструктажа фиксируется в журнале под роспись.
При работе с электроинструментом и механизмами создаются все меры по безопасной работе. У оборудования, имеющего пожарную опасность, выставляются соответствующие таблички.
В месте ведения работ выставляют бытовые вагончики, устраивают участки складирования материалов, места приготовления растворов и мастик. Для безопасного замеса требуется обеспечить максимальную механизацию всех процессов.
Оборудование и инструмент
Оборудование и инструмент выбираются с опорой на технологию укладки конструкции.
На стройплощадке потребуется следующее:
- трамбовочные машины – для уплотнения грунта и подстилающих слоев;
- виброрейки или виброплатформы – для уплотнения бетонной заливки;
- гладилка для бетона, заглаживающие, фрезеровальные машины – для выглаживания, обработки поверхности;
- затирочные, шлифовальные машины – для финишной обработки конструкции;
- нарезчик швов – необходим при устройстве деформационно-усадочных швов;
- промышленные пылесосы;
- профили для деформационных швов;
- бетономешалки;
- лопаты, чистая тара, шпатели, правило, уровень.
Стоимость устройства промышленных бетонных полов
Цена на производство работ складывается на основе нескольких статей расхода.
Ориентировочные затраты складываются следующим образом:
- работы по уплотнению грунтов, устройство песчано-гравийной подготовки – от 180 р/куб.м;
- укладка тепло-, гидроизоляционных слоев – от 18 р/кв.м;
- устройство черновых стяжек + армирование – от 1020 р/кв.м;
- устройство напольных промышленных покрытий – от 220 р/кв.м;
- укладка теплого пола – от 480 р/кв.м.
Необходимо принимать во внимание затраты на покупку или аренду оборудования, покупку и транспортировку материалов.
Выводы
Качественное устройство промышленных бетонных полов возможно только с участием профессионалов. Специализированные бригады осуществляют поэтапный контроль, проверяя качество подготовки основания, подстилающих, гидро-, теплоизоляционных слоев. Готовая конструкция будет соответствовать требованиям строительных норм, правил, действующих технических условий.
Процесс устройства промышленных бетонных полов показан в видео:
obetone.com
Особенности и нюансы технологии устройства бетонных полов
Бетонные полы по праву считаются оптимальным решением, как для загородного строительства, так и в городских условиях. Они обладают высокой прочностью и долговечностью, ровной поверхностью и относительно невысокой стоимостью. Это позволяет применять бетон для сооружения полов не только в жилых или офисных, но и в производственных или промышленных зданиях, сооружениях и помещениях. Тем более, что на такой пол можно уложить абсолютно любое напольное покрытие.
Технология устройства бетонных полов, в принципе, достаточно универсальна и практически не зависит от типа строения, условий эксплуатации или площади помещения. Однако, она таит в себе несколько важных тонкостей и нюансов.
Подготовка основы
Независимо от того, будет ли пол уложен на уже существующее бетонное основание, или на грунтовую «подушку», необходимо провести комплекс определенных подготовительных работ. Устройство полов из бетона требует ровного и плотного основания.
Если пол монтируется на старую бетонную подкладку, то необходимо сначала заполнить все трещины специальным составом на основе песчано-цементной смеси или полимеров. Кроме того, важно устранить все неровности при помощи шлифовального инструмента или специальных заплаток.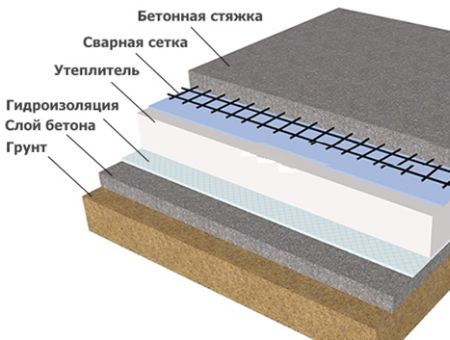
Немного по-другому происходит устройство бетонного пола по грунту. Для начала грунт тщательнейшим образом утрамбовывают. После чего на него укладывается щебеночная или песчаная подушка.
Очень важным этапом является обустройство слоя гидроизоляции при помощи полимерных или битумных материалов. Только после укладки такого слоя можно приступать непосредственно к основной конструкции.
Процесс укладки пола из бетона
Перед укладкой раствора нужно возвести опалубку и, если это предусмотрено проектом, расположить армирующие элементы – стальные прутья, металлическую сетку и так далее.
Как правило, технология устройства бетонного пола подразумевает два способа разравнивания смеси:
- при помощи «маячков», лопат и другого инсрумента;
- с помощью виброрейки.
При использовании виброрейки можно обойтись и без опалубки. Устройство пола в доме из газобетона, например, часто осуществляется именно таким образом. Главным условием в этом случае является обеспечение непрерывного поступления рабочей смеси на объект.
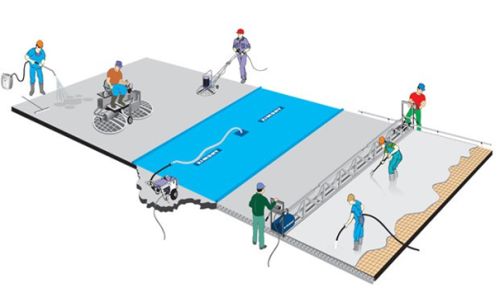
Финишная отделка бетонного пола
После укладки бетонной смеси в стяжку, ее необходимо оставить для предварительного схватывания. В зависимости от показателей температуры и влажности, этот процесс может занять от 3 до 7 часов. К затирке подсохшего пола специальной машиной – «вертолетом» - можно приступать тогда, когда человек среднего веса оставляет в схватившемся бетоне отпечаток глубиной 3-4 мм.
Затирочная машина должна пройти по полу в двух направлениях: вдоль и поперек. Помимо всего прочего, устройство шлифованного бетонного пола позволяет значительно увеличить прочность бетона, его долговечность и сопротивление механическим нагрузкам.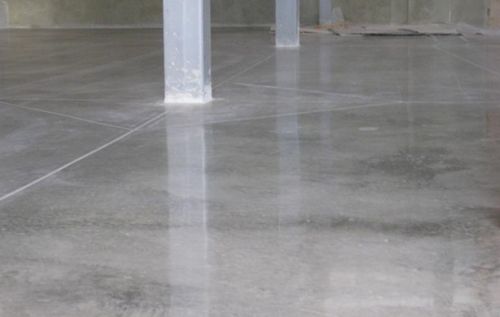
После того, как глубина следа человека снижается до 1 мм, можно приступать к окончательной финишной затирке, которая осуществляется лопастями затирочной машины.
Типы швов
Устройство бетонного пола в частном доме, в городской квартире или в промышленных цехах, подразумевает необходимость обустройства швов. Устройство бетонного пола в бане, например, или в совсем небольших помещениях, зачастую обходится и без швов. Но при сооружении полов в средних по размерам, а тем более – в больших помещениях, без швов обойтись практически невозможно.
Бетон не обладает такой пластичностью, как дерево или пластик. При существенной нагрузке и деформации бетон не прогибается, а растрескивается и разрушается.
Применяют три главных вида швов, препятствующих деформации:
- изоляционные швы;
- усадочные борозды;
- конструкционные швы.
Изоляционные предотвращают контакт стяжки пола с другими бетонными элементами постройки. Усадочные швы препятствуют хаотичному растрескиванию в случае усадки. Конструкционные швы позволяют разбить работы по сооружению пола на отдельные участки.
Рекомендуем почитать:
Цементные полы – особенности и преимущества
Универсальные полы из бетона: современно, надежно, недорого
svoi-pol.ru
![]() 1. ПОДГОТОВКА ОСНОВАНИЯУкладка пола может производиться как по грунтовому, так и по существующему бетонному основанию. Полы также можно укладывать и на другие виды оснований, но при этом необходимо выполнить определенные расчеты, чтобы проверить соответствие имеющейся основы требованиям к основанию под бетонный пол.Не допускается применять в качестве основания под полы торф, чернозем и другие растительные грунты, а также насыпные и естественные грунты без предварительного их уплотнения при несоответствии степени уплотнения требованиям СНиП 3.02.01–87*При укладке бетонного пола на грунтовое основание необходимо сначала хорошо утрамбовать грунт, чтобы избежать в дальнейшем растрескивания пола вследствие просадки основания. Если грунты слабые, то сначала производится выемка пучинистого грунта, замена его на непучинистый согласно СНиП 2.02.01–83 с последующим трамбованием. Обычно выемка грунта производится на глубину 0,5–1,0 м.После трамбовки на грунт укладывается песчаная подушка. Ее толщина может быть различной в зависимости от видов грунтов основания, степени их промерзания, высоты поднятия грунтовых вод и т.п. В основном, толщина песчаной подушки колеблется в пределах от 0,5 до 1,0 м. Песчаную подушку также необходимо уплотнить. Для этого изначально укладывается подушка, толщина которой приблизительно на 1/4 больше расчётной. Затем песок проливают водой, и с помощью катков или вибротрамбовок толщина подушки приводится к расчётной.При укладке пола на существующее бетонное основание следует произвести его тщательную подготовку. Если в основании есть трещины, то их необходимо расширить и заполнить ремонтным составом, состоящим либо из полимера, либо из цементно-песчаной смеси на напрягающем цементе. Толщина бетонного основания должна быть не менее 10 см. Участки бетонного основания, не поддающиеся ремонту, необходимо полностью демонтировать и уложить новый бетон.Имеющиеся на отдельных участках основания перепады по высоте снимаются шлифовально-мозаичной или фрезеровочной машиной по бетону. Образовавшуюся пыль удаляют при помощи промышленных пылесосов.В случае, когда перепады высоты на старом бетонном основании превышают 3 см, его необходимо выровнять подбетонкой. 2. УСТРОЙСТВО ГИДРОИЗОЛЯЦИИПосле того как песчаная подушка утрамбована, либо отшлифовано и обеспыленно старое бетонное основание, укладывают гидроизоляционный слой. Гидроизоляцию от сточных вод и других жидкостей следует предусматривать по бетонному основанию, перекрытию или ц/п стяжке. Гидроизоляцию от капиллярного поднятия грунтовых вод следует выполнять по уплотненному грунту или монолитной стяжке.Различают обмазочную, оклеечную и гидроизоляцию мембранного типа. Тип материалов выбирается на основании результатов гидрогеологических исследований. В особых случаях требуется комплексный подход, то есть применение разных типов гидроизоляции. В качестве обмазочной гидроизоляции рекомендуется использовать однокомпонентную мастику на основе гидрофобных полиуретановых смол «Гипердесмо».Поверхности, на которые планируется наносить мастику, следует обеспылить, очистить от наплывов раствора, грязи, жировых пятен, следов других химических веществ (краски, клея, битума и прочих). Поверхность грунтуется мастикой «Аквадюр» или «Гипердесмо D» с использованием резиновых ракелей или длинноворсных валиков. Расход грунтовочного материала 0,3–0,6 кг/м в зависимости от впитывающей способности основания. Далее не ранее чем через 3–8 часов (в зависимости от условий среды) после нанесения грунтовочного слоя поверхность покрывается мастикой «Гипердесмо» с помощью резиновых ракелей, кистей, валиков или методом безвоздушного распыления. Мастика наносится в два рабочих приема с расходом материала 0,6 кг/м на каждый слой. Временной промежуток между нанесением слоев должен составлять от 3 до 24 часов, в противном случае может быть ухудшена адгезия между слоями. Для контроля равномерности нанесения материала рекомендуется применять для разных слоев мастику контрастных цветов.Гидроизоляцию рекомендуется выполнять из рулонных битумных гидроизоляционных материалов либо полимерных мембран.Если влаги в основании нет, или ее подсос для конструкции пола не критичен, достаточно выполнить подстилающий слой из полиэтиленовой пленки по бетонному основанию. 3. УСТАНОВКА ОПАЛУБКИНа объектах с большими площадями устройство бетонной стяжки пола осуществляется «картами» – прямоугольниками определенного размера. Размер «карты» определяется площадью пола, уложенного за рабочую смену, т.е. производительностью. По периметру карты устанавливается опалубка.Опалубку можно сделать из деревянных досок толщиной не менее 2 см. Также в качестве опалубки могут использоваться направляющие для виброрейки. Линия опалубки, по возможности, должна совпадать с рисунком деформационных швов, так как в большинстве случаев это место стыка уже схватившегося и свежеуложенного бетона.Направляющие рекомендуется устанавливать параллельно длинной стороне стены на маяки из цементно-песчаного раствора с ориентацией на метку, вынесенную на стену. При этом первый ряд направляющих следует размещать на расстоянии 0,4–0,6 м от стены (в зависимости от расположения колонн у стены).Укладку бетонной смеси можно производить и без установки опалубки, но только при условии непрерывности процесса. В этом случае установка опалубки потребуется лишь в том месте, где будет завершена дневная работа по укладке бетонной смеси. 4. УКЛАДКА АРМАТУРЫБетонные полы толщиной от 70 до 100 мм рекомендуется армировать одним слоем металлической сетки. Чаще всего используется дорожная сетка из арматуры класса В-1 диаметром стержней 5 мм с размером ячейки 150х150 мм или 100х100 мм. При толщине бетонного пола от 100 до 180 мм целесообразно применить вместо дорожной сетки или вместе с ней арматурный каркас. Арматурный каркас состоит из двух слоев металлической сетки, сваренных армированными стержнями на определенном расстоянии друг от друга. Нижний слой металлической сетки, как правило, вяжется на месте из стержней арматуры диаметром от 8 до 16 мм. Под эту сетку подкладываются прокладки толщиной не менее 20 мм, чтобы компенсировать нагрузки на растяжение и защитить конструкцию от коррозии металла при возможном нарушении гидроизоляции. Верхний слой кладется картами 6х6 м, а в особых случаях 3х3 м на опоры, приваренные к нижнему слою сетки. В тех же случаях, когда на пол воздействуют высокие динамические нагрузки (падение тяжелого оборудования, изделий и т.п.), для повышения ударной вязкости и стойкости бетона к растяжению при изгибе в качестве арматуры можно применить стальную фибру длиной 50–80 мм и диаметром 0,3–1 мм.При устройстве полов с дисперсным армированием (фиброй) перед укладкой бетонной смеси непосредственно на объекте необходимо засыпать фибру в автобетоносмеситель из расчета 30–35 кг/м бетонной смеси и перемешивать ее в течение 10–15 минут. 5. УКЛАДКА БЕТОННОЙ СМЕСИПосле того как в соответствии с проектом установлена опалубка и уложена арматура, приступают к укладке бетонной смеси. При этом желательно обеспечить её бесперебойную подачу на строительную площадку. Подвоз бетонной смеси на объект осуществляется в автобетоно-смесителях с ближайшего способного производить бетонную смесь соответствующего качества завода товарного бетона.Обычно укладываемая в стяжку бетонная смесь имеет подвижность П3, что соответствует осадке конуса от 12 до 14 см. Подача бетонной смеси на объект осуществляется различными способами в зависимости от того, насколько близко автобетоносмеситель может подъехать к месту выгрузки бетона, а также от того, на каком этаже ведутся работы. В случае, если бетоносмеситель можно подогнать вплотную к месту укладки, выгрузку бетонной смеси производят непосредственно на подготовленное основание. Если же работы производятся не на первом этаже или когда миксер нельзя подогнать к месту укладки из-за недостаточной ширины или высоты проезда, используют бетононасос.Работы по укладке бетонной смеси следует выполнять при температуре воздуха на уровне пола не ниже +5°С. Эта температура должна поддерживаться до обретения бетоном 50%-ной проектной прочности.Для производства работ при отрицательных температурах предусмотрен ряд мероприятий:-Если работы ведутся на открытой площадке, то устраиваются тепляки площадью 200–300 м2 с каркасом из пиломатериала и ограждающей конструкции из армированной пленки и утеплителя.Площадь тепляков ограничивается: – интенсивностью производства работ;– количеством и мощностью тепловых пушек, способных обогреть данную площадь. -Если работы ведутся в закрытом контуре, то отопление может производиться также тепловыми пушками или посредством электропрогрева бетона в стяжке. Скорость бетонирования пола в этих условиях зависит от способности оборудования поддерживать температуру воздуха на уровне пола не ниже +5°С до обретения бетоном 50%-ной проектной прочности. Перед укладкой бетонной смеси нижележащий слой бетона должен быть очищен от грязи и пыли, а жировые пятна удалены промывкой 5%-ным раствором кальцинированной соды с последующей промывкой водой.Нижние части стен и колонн на высоту равную толщине покрытия рекомендуется обклеить гидроизоляционным рулонным материалом или в случае устройства в данных местах деформационных швов – листовым вспененным полиэтиленом. 6. ВИБРОМЕХАНИЧЕСКАЯ ОБРАБОТКА И РАЗРАВНИВАНИЕ БЕТОННОЙ СМЕСИУкладку и разравнивание бетонной смеси можно производить тремя способами:-с помощью виброрейки Enar по направляющим; -с помощью правила по «маякам»;-с применением бетоноукладчика Copperhead Laser Screed.При укладке и разравнивании бетонной смеси с помощью виброрейки Enar необходимо сначала установить направляющие под нее на уровне нулевой отметки и тщательно выставить их по горизонту. Направляющие рекомендуется устанавливать параллельно длинной стороне стены, первый ряд направляющих следует размещать на расстоянии 0,4–0,6 м от стены, в зависимости от ширины колонн, расположенных у стен. При этом ширина полос выбирается с учетом технических характеристик применяемого оборудования, расстояния между колоннами в здании, а также планируемым расположением деформационных швов. Монтажные швы должны совпадать с деформационными швами. В процессе работы нужно следить за тем, чтобы направляющие не были сбиты. После этого на направляющие монтируется виброрейка Enar.Бетонная смесь заливается на подготовленное основание и разравнивается с таким расчетом, чтобы ее верх был немного выше уровня виброрейки Enar (зависит от степени уплотняемости бетонной смеси виброрейкой). После этого виброрейку тянут по направляющим. Бетонная смесь под действием вибрации оседает до нужного уровня и разравнивается. При этом нужно следить, чтобы виброрейка постоянно скользила по поверхности бетона. В тех местах, где бетонная смесь оседает ниже уровня виброрейки, бетонную смесь добавляют в необходимых количествах. Скорость передвижения виброрейки при 1–2 проходах должна составлять 0,5–1 м/мин. Предварительная подготовка виброрейки Enar – устройство опорных точек, установка и нивелировка направляющих – требует значительного времени, наличия в бригаде нескольких рабочих и как минимум одного инженера-геодезиста, контролирующего отметки направляющих и уложенного бетона.В основном уплотнение и разравнивание бетонной смеси выполняется виброрейками Enar серии Q. При ширине полосы от 3 до 4 м как правило используется виброрейка Enar серии Q 25/45, при ширине полосы от 4 до 6 м – виброрейка Enar серии Q 35/60. Производительность этих виброреек составляет в среднем 300 м2 в смену.При укладке бетонной смеси по «маякам» на основание устанавливается нивелир, и произвольно выбирается определенный уровень. Затем к колонне, на которой имеется отметка нулевого уровня пола, прикладывается рейка таким образом, чтобы ее низ совпадал с этой отметкой. На рейке ставится риска, соответствующая произвольно выбранному с помощью нивелира уровню.На основание заливается бетонная смесь немного выше необходимого уровня. Эта смесь вибрируется глубинным вибратором Enar AVMU, потом из неё делаются холмики-маяки приблизительно с шагом в 1,5 – 2 м. На каждый из холмиков устанавливается рейка с риской. Риску совмещают с установленным на нивелире уровнем. После этого вершину холмика подгоняют по низу рейки и бетонную смесь заравнивают правилом вровень с верхушками «маяков».Для ускорения процесса уплотнения и выравнивания бетонной смеси применяют плавающие виброрейки Enar, такие как: -реверсивная виброрейка серии QZ – способная двигаться как вперед, так и назад; -поверхностная виброрейка серии QX, движение только назад;-плавающая виброрейка серии TORNADO, с эргономичной рукоятью; -плавающая виброрейка серии HURACAN, с выносным двигателем Honda.При применении технологии укладки смеси по «маякам» производительность в восьмичасовую смену с учетом закладки арматуры составляет в среднем 500 м2. Для быстрой укладки промышленных бетонных полов применяется бетоноукладчик Copperhead Laser Screed с лазерной системой автоматического управления.Бетоноукладчик Copperhead Laser Screed позволяет с высокой скоростью автоматически укладывать бетонный пол точно по установленному уровню вне зависимости от неровностей основания.Основой нивелирующей системы бетоноукладчика является лазерная система автоконтроля, которая состоит из лазерного нивелира и двух приемников. Приемники напрямую связаны с гидравлической системой управления выравнивающей плитой.Такая система позволяет контролировать и корректировать уровень укладки бетона. Лазерный нивелир задает горизонтальную плоскость, запланированную проектом. Приемники фиксируют лазерную плоскость и контролируют положение выравнивающей плиты. В случае отклонения бетонной поверхности от проектной плоскости приемники посылают команду гидравлической системе управления выравнивающей плитой бетоноукладчика и таким образом регулируют уровень залитого бетона. Точность укладки бетонной поверхности от 2 до 5 миллиметров на трехметровой рейке.Работа бетоноукладчика имеет существенные преимущества по сравнению с применением, например, виброреек.Copperhead Laser Screed требует присутствия двух человек – оператора и подсобного рабочего. Производительность работ Copperhead Laser Screed составляет от 750 до 1000 м2в смену и в основном ограничивается скоростью подачи бетонной смеси.Применение дополнительных вибраторов для уплотнения бетона не требуется. 7. ЗАТИРКА ПОВЕРХНОСТИ ДИСКОВО-ЛОПАСТНЫМИ МАШИНАМИ Работа проводится в два этапа: сначала производится затирка поверхности бетона, затем наносится обеспыливающая упрочняющая пропитка «Ашфорд Формула». После вибро-механической обработки бетонной смеси на поверхность выступает бетонное «молочко». Для того чтобы это «молочко» не отслаивалось в процессе эксплуатации бетонных полов, производится затирка поверхности бетона. Для этих целей используются дисково-лопастные затирочные машины, т.н. «вертолеты». Во время затирки происходит уплотнение бетонной поверхности и ее доведение до зеркального блеска. При затирке бетона всегда должно быть в наличии запасное оборудование на случай, если основное выйдет из строя.В случаях, когда к поверхности пола предъявляются повышенные требования по прочности и истираемости, при затирке применяют топпинги. Топпинг – это сухая упрочняющая смесь на основе цемента с добавлением кварца или других компонентов, отличающихся повышенной твёрдостью и стойкостью к истиранию.В этом случае в свежеуложенный выровненный бетон втирается специальный топпинг «Refloor RF», затем для дополнительного обеспыливания наносится пропитка «Ашфорд Формула».«Ашфорд Формула» стабилизирует поверхность и сводит образование трещин к минимуму. Кроме того, она на химическом уровне связывает соли, находящиеся в матрице бетона и вызывающие появление пыли, и поверхность становится беспыльной. 7.1. ЧЕРНОВАЯ ЗАТИРКАПеред затиркой поверхности бетона необходимо сделать технологический перерыв, чтобы бетон мог набрать начальную прочность. В зависимости от влажности и температуры окружающей среды этот перерыв составляет от 4 до 20 часов. За это время бетон схватывается так, что человек, наступая на его поверхность, оставляет след глубиной 2–3 мм. В этот момент нужно приступать к грубой затирке поверхности.Грубая затирка поверхности свежеуложенного бетона осуществляется либо диском, либо плавающими лопастями затирочных машин Bartell(Канада) за два прохода. При этом направление движения затирочной машины при втором проходе перпендикулярно направлению движения при первом проходе.Поверхность бетона, примыкающая к колоннам, ямам, дверным проемам и стенам должна быть обработана в первую очередь, так как бетон в этих местах твердеет быстрее. Затирка бетона в местах примыканий производится при помощи краевых заглаживающих машин Bartell (модель В 424/H), оснащенных свободно вращающимся кругом. Топпинг «Refloor RF», при его использовании, аккуратно рассыпают по поверхности стяжки, стараясь достичь равномерной толщины слоя. Рассыпка топпинга «Refloor RF» производится либо вручную, либо с помощью специальной тележки для рассыпки топпинга. Такая тележка должна иметь:-контейнер – для загрузки в него топпинга;-шнеки – для помола застоявшейся смеси в контейнере;-заслонка-дозатор – для регулировки уровня рассыпки топпинга;-широкие колеса – для того, чтобы тележка не продавливала свежий бетон, не оставляла за собой глубокой колеи.Расход топпинга «Refloor RF» при первом внесении – около 2/3 от общего расхода на 1 м2. После внесения топпинга «Refloor RF» производится первая грубая затирка бетонозаглаживающей машиной Bartell. Затирку необходимо производить, как только топпинг впитает в себя влагу из бетона. Это будет видно по потемнению поверхности. После завершения первой грубой затирки следует немедленно внести оставшуюся 1/3 часть топпинга «Refloor RF», чтобы он успел пропитаться влагой из цементного молока до испарения воды.После того как смесь пропитается влагой, сразу же приступайте ко второй грубой затирке (так же, как описывалось выше).Расход топпинга «Refloor RF» натурального цвета составляет 3 - 5 кг/м2, цветного – 5 - 8 кг/м2.Пол с топпингом чаще всего устраивается для складских помещений с использованием тяжелой погрузочно-разгрузочной техники, производственных цехов, торговых центров, рынков, а также для паркингов и других объектов с повышенной пешеходной и транспортной нагрузкой. Бетонные полы с упрочненным верхним слоем включены в действующие СНиП 2.03.13–88. 7.2. ФИНИШНАЯ ЗАТИРКАВо время грубой затирки прочность бетона постепенно нарастает. Момент финишной затирки определяется визуально. Этот момент может определить только квалифицированный рабочий. Признак, по которому можно определить момент финишной затирки – бетонный пол после затирки диском имеет довольно гладкую поверхность, но при этом лопасти не собирают молочко с поверхности. Финишная затирка осуществляется финишными лопастями затирочных машин Bartell так же, как и при грубой затирке, минимум за два подхода. Лучшевсего для этого подходит затирочная машина Bartell TS 88, т.к. она имеет скрещивающиеся лопасти и значительно облегчает финишную затирку. При каждом подходе машина совершает два прохода. Направление движения затирочной машины при втором проходе перпендикулярно направлению движения при первом проходе. При первом подходе угол наклона лопастей выставляется на 5–10 мм от края лопасти до уровня пола. При втором подходе – на 20–25 мм от края лопасти до уровня пола. Именно на этой стадии пол доводится до зеркального блеска. Затирка производится до тех пор, пока бетон не наберет такую прочность, при которой человек, наступая на поверхность, не будет оставлять следы. На большой площади применяются двухроторные промышленные машины Bartell (такие как TS 78, TS 88). 8. ПРОПИТКА БЕТОНА ОБЕСПЫЛИВАЮЩИМ И УПРОЧНЯЮЩИМ СОСТАВОМ «АШФОРД ФОРМУЛА»Для того, чтобы бетонный пол в процессе эксплуатации не пылил, а также для упрочнения и герметизации поверхности применяется полимерная пропитка «Ашфорд Формула». «Ашфорд Формула»– это бесцветный жидкий полимер на водной основе. Проникая в поры бетона, он химически взаимодействует с цементом и влагой, в результате чего образуется единая твердая масса. «Ашфорд Формула» наносится как на свежеуложенный, так и на сухой бетон 1 раз на весь срок службы бетона. Этот материал полностью впитывается и не образует на поверхности подверженную истиранию пленку. Нанесение пропитки на механически гладко затертую поверхность бетонного основания дает потребителю пол, который по мере эксплуатации приобретает мягкий «бархатный» блески прочность которого увеличивается. Перед нанесением пропитки бетонную поверхность надо очистить от загрязнений, произвести влажную уборку, высушить. «Ашфорд Формула» с избытком наносят на поверхность при помощи распылителя низкого давления или путем разлива его по поверхности. После этого необходимо в течение 30–45 мин. равномерно распределять материал по всей поверхности чистой мягкой щеткой пока состав «Ашфорд Формула»не пропитает поверхность бетона и не станет гелеобразным, клейким на ощупь, а сама поверхность– скользкой. В течение всего этого времени нельзя допускать, чтобы даже небольшие участки поверхности высохли.После того, как поверхность стала скользкой, следует немного смочить ее водой. Вода растворяет материал, и поверхность перестает скользить. Теперь необходимо еще раз распределить материал мягкой щеткой для улучшения его проникновения в бетон. И еще раз дождаться, пока поверхность станет скользкой, но не более 15 мин.Остатки пропитки удаляют с поверхности стяжки при помощи воды, ракли и ветоши. 9. ШВЫ В БЕТОННЫХ ПОЛАХБетон в стяжке, как и любой цементобетон, по своей структуре очень хрупкий материал, не способный к пластическим деформациям. При приложении к бетону нагрузки, превышающей его прочностные характеристики, он не деформируется без разрушения, как, например, в случае с пластмассой или другим пластичным материалом, а растрескивается как стекло. Также растрескивание происходит под воздействием внутренних напряжений в бетоне, вызванных усадочными деформациями при твердении и перепадами температур. Для того, чтобы ограничить растрескивание пола и контролировать места появления трещин в бетонной стяжке, необходимо нарезать деформационные швы.Существуют три основных типа деформационных швов в стяжке:1.Изоляционные швы.2.Усадочные швы.3.Конструкционные швы. 9.1. ТЕХНОЛОГИЯ НАРЕЗКИ ШВОВНарезанные швы должны быть прямыми и чистыми. Рабочий, нарезающий швы, должен знать, когда их нарезать, какой шов резать следующим, как глубоко резать и как предотвратить слишком быстрый износ лезвия при использовании в бетоне очень твердого заполнителя.Швы должны нарезаться, как только бетон наберёт достаточную прочность, чтобы не быть поврежденным лезвием, но до того, как в бетоне могут возникнуть произвольные трещины. При резке бетона обычным шоврезчиком – нарезку швов надоначинать не ранее, чем через 24 часа, и не позднее, чем через 72 часа после окончания финишной обработки бетона. При влажной нарезке (имеется ввиду нарезка по мягкому бетону специальным шоврезчиком Soft Cat) такие условия обычно возникают через 4–12 часов после окончания финишной обработки бетона. Хотя нарезка швов через 24 часа при определенных условиях также возможна. Рабочий должен сделать пробный шов через несколько часов после начала твердения бетона. Если при нарезке пробного шва частицы заполнителя вываливаются из бетона, то начинать нарезку ещё рано. Начинать нарезку следует тогда, когда лезвие вместе с бетоном разрезает зёрна заполнителя.Расположение каждого шва чаще всего намечают мелом по натянутой верёвке. В качестве ориентира для нарезки используют линейку, например, доску шириной минимум 4 см. При нарезке швов всегда должно быть в наличии запасное оборудование на случай, если основное выйдет из строя.В жаркую погоду или если существует опасность растрескивания необходимо нарезать каждый третий или четвертый шов перед нарезкой промежуточных швов.Обычно швы нарезаются в той же последовательности, в какой укладывался бетон.Швы должны нарезаться на глубину 1/3 толщины стяжки. Это создает в стяжке зону слабины и бетон при усадке даёт трещину именно в этой зоне, т.е. трескается направленно, а не хаотично. При этом края образовавшейся трещины имеют определённую шероховатость, что исключает вертикальные смещения краев до тех пор, пока трещина не станет слишком широкой. Технология нарезки швов, описанная выше, требует выдержки свежеуложенного бетона 4 и более часов и нарезки на 1/3 глубины стяжки для получения хорошего деформационного шва.Не так давно был изобретен способ сухой легкой нарезки швов, когда швы режутся сразу же после финишной обработки бетона. Используя длинную ручку, рабочий может нарезать до 10 м шва без хождения по бетону. Для нарезки более длинных швов рабочий, обутый в специальные сапоги с гладкой подошвой, может ходить по стяжке и использовать 2-метровую ручку. Этот тип швов режется только на 2–3 см в глубину. 9.2. ГЕРМЕТИЗАЦИЯ ШВОВЧтобы облегчить уборку и поддержать края шва при транспортных нагрузках, нарезанные швы необходимо загерметизировать.Герметизация позволяет защитить шов от проникновения воды и агрессивных сред, а также от засорения.Тип герметика зависит от нагрузок и условий эксплуатации. Например, на многих пищевых предприятиях полы должны легко мыться и выдерживать движение тяжелых грузовиков. Герметики для таких полов должны быть достаточно твердыми, чтобы предотвращать скалывание краев шва, и достаточно эластичными, чтобы выдержать усадочные и температурные колебания шва. Наиболее подходящим герметиком для швов является «Эмфимастика PU-40». Заполнение швов этим герметиком производится тогда, когда влажность бетона в шве не превышает 4% (обычно через 28 суток).В промышленных полах с высокой транспортной нагрузкой швы должны быть заполнены материалом «Эмфимастика PU-60». Он обеспечивает поддержку шва и выдерживает высокие нагрузки. Этот материал наносится минимум через 28 суток после укладки стяжки. Эластомерные (гибкие) герметики используются только там, где шов не будет подвержен колесным нагрузкам. Они быстро наносятся и могут выдерживать большие подвижки при открытии/закрытии шва.Перед герметизацией шов должен быть очищен от пыли и мусора путем продувки сжатым воздухом, механической очистки щеткой или пескоструйным аппаратом. При использовании компрессора необходимо убедиться, что он не оставляет масляную пленку в шве. |
texbeton.web-box.ru
Технология устройства бетонных полов: основные этапы работы
Технология устройства бетонных полов
Бетонные полы представляют собой надежное, прочное и долговечное напольное покрытие, которое пользуется большой популярностью на современных промышленных предприятиях. В этой статье мы рассмотрим технологию устройства бетонного пола, научимся правильно обрабатывать покрытие, ознакомимся с монтированием виброреек на направляющие, рассмотрим работу со швами и обратим внимание на мелкие нюансы работы с покрытием.
Схема утепления бетонного пола.
Схема устройства бетонного пола.
- трамбовочная техника;
- фрезеровочная машина по бетону;
- виброрейка;
- промышленный пылесос;
- затирочные машины;
- стальные шпатели;
- маячные рейки.
Итак, давайте более подробно рассмотрим все этапы укладки полов.
Подготовка основания
Если говорить об укладке промышленных полов, то эта технология может осуществляться несколькими способами, например, по грунтовому основанию, а также по цементобетонному основанию.
В первом случае нужно начать с хорошей утрамбовки грунта. Сделать это можно с помощью специальной трамбовочной техники, которую сегодня с легкостью можно взять напрокат. Грунт нужно тщательно утрамбовать, чтобы в дальнейшем покрытие не дало трещин. После этого на грунт лучше всего уложить песчаную либо щебеночную подушку, толщина которой зависит от вида грунта и степени его промерзания. По словам специалистов-строителей, такая подушка должна быть хорошенько уплотнена.
Схема стяжки бетонного пола.
Если же устройство пола производится на бетонное основание, то здесь необходимо произвести определенную подготовку. Например, нужно проверить то или иное основание на отсутствие трещин. Если же трещины все же обнаруживаются, тогда нужно их заполнить специальным составом из цемента определенных марок. Такой раствор может состоять из цементно-песчаной смеси, а также из полимеров. При наличии участков основания, которые трудно привести в порядок, лучше всего их полностью демонтировать, после чего уложить новый слой.
При наличии перепадов по высоте нужно воспользоваться фрезеровочной машиной по бетону либо не менее эффективной шлифовально-мозаичной машиной. С помощью данного оборудования вы с легкостью выровняете основание для устройства пола. Пыль, что образуется при данном процессе, можно удалять с помощью обыкновенных промышленных пылесосов. Не стоит забывать и о гидроизоляции, которую следует уложить на подушку. В основном в качестве гидроизоляции укладывают полимерные мембраны либо рулонные битумные гидроизоляционные материалы. Для тех, кто не является специалистом в этом вопросе, напомним, что технология гидроизоляции используется для того, чтобы влага не впитывалась из свежеуложенного бетона в основание. Еще благодаря гидроизоляции предотвращается капиллярный подсос влаги из грунта.
Проведение работ по укладке
Перед тем как будет произведена технология укладки бетонной смеси в стяжку, необходимо (согласно тому или иному проекту) установить опалубку, выполнить армирование. Для этого можно взять виброрейки и соорудить неплохую опалубку. Не стоит забывать и о том, что линия опалубки в любом случае должна быть подогнана с рисунком деформационных швов. Конечно же, можно укладывать смесь для промышленных полов даже без использования опалубки (только если этот процесс будет непрерывным).
Схема расположения слоев бетонного пола.
Если говорить непосредственно об укладе данной смеси, то здесь можно воспользоваться помощью «маяков» и виброрейки по направляющим. Стоит отметить, что и та, и другая технология являются эффективными. Разравнивание смеси из бетона с помощью виброрейки требует определенного порядка. В первую очередь нужно грамотно установить направляющие под виброрейку (уровень нулевой отметки). После этого необходимо направляющие выставить по горизонту. Окончательным этапом можно назвать монтирование виброреек на направляющие. Укладка смеси по так называемым «маякам» производится с помощью всем известного строительного нивелира.
По материалам сайта: http://1pobetonu.ru
fix-builder.ru
Устройство промышленных и бетонных полов. Технология устройства бетонных полов
Обычно устройство промышленных и бетонных полов подразделяется на четыре основные этапа:
1-й этап. Подготовка основания под полы.
2-й этап. Укладка бетонной смеси в стяжку пола с помощью бетононасоса.
3-й этап. Финишная обработка поверхности бетона, шлифовка.
4-й этап. Нарезка швов в бетоне и их герметизация.
Первый этап. Подготовка основания под полы
Обычно укладка бетонной смеси производится по специально подготовленному грунтовому основанию, в исключительных случаях при предполагаемой высокой нагрузке на полы по цементобетонному основанию. Перед укладкой бетонной смеси, для того чтобы исключить растрескивание пола от просадки нижележащих слоев сначала производится отсыпка песчано-гравийной смесью, щебнем и послойное уплотнение виброкатком основания пола.
В ходе послойного уплотнения грунта формируется песчаная или щебеночная подушка. Толщина подушки может быть различной в зависимости от характеристик грунтов в основании, глубине промерзания, уровня грунтовых вод и т.д.
На выполненное основание укладывается слой гидроизоляции. Обычно гидроизоляция выполняется из ПВХ пленки, при высоком уровне грунтовых вод из битумных гидроизоляционных материалов. Слои гидроизоляция необходим, чтобы основание пола не впитывало влагу из свежеуложенного бетона, а также для предотвращения капиллярного подсоса влаги из грунта.
Второй этап. Укладка бетонной смеси в стяжку пола с помощью бетононасоса
Перед бетонированием пола, весь пол здания разбивается на карты (заливки), устанавливается опалубка и выполняется армирование. Линия установки опалубки совпадает с деформационными швами, местами стыка уже затвердевшего и свежеуложенного бетона.
Для повышения прочности в промышленных бетонных полах используется арматурный каркас. Арматурный каркас, вяжется по месту из стержней арматуры диаметром от 8 до 16 мм. При воздействии на пол высоких динамических нагрузок для повышения ударной вязкости и стойкости бетона к растяжению при изгибе, в качестве арматуры применяется стальная фибра.
После установки опалубки и устройства арматурного каркаса, производится укладка бетонной смеси. При укладке смеси производится бесперебойная подача с помощью бетононасоса. Доставка бетонной смеси на объект производится в автобетоносмесителях с завода товарного бетона, способного производить бетонную смесь специального состава под бетононасос.
Бетонная смесь непрерывно подается из рукава бетононасоса. При укладке выполняется разравнивание бетонной смеси виброрейкой. Для контроля высоты укладываемой бетонной смеси относительно запланированной отметки используется прибор нивелир.
Третий этап. Финишная обработка поверхности бетона. Шлифовка
После завершения укладки и уплотнения бетонной смеси, выполняется финишная обработка свежеуложенной поверхности бетона. Для этого применяются специальные затирочные машины "вертолеты".
Перед финишной обработкой необходимо дать бетону набрать начальную прочность в среднем это период от 3 до 5 часов. За это время бетон схватывается и набирает прочность до 20%. Далее выполняется грубая затирка поверхности свежеуложенного бетона. Грубая затирка поверхности бетона выполняется лопастями затирочных машин за несколько проходов. Направление движения затирочной машины при следующем проходе, перпендикулярно направлению движения предыдущего прохода. Со временем прочность бетона постепенно возрастает.
Четвертый этап. Нарезка швов в бетоне и их герметизация
Бетон по своим физическим свойствам хрупкий материал, не способен без разрушения выдерживать пластические деформации. При приложении к бетону нагрузки, превышающей его прочностные характеристики, он растрескивается как стекло. Растрескивание происходит также и под воздействием внутренних напряжений в бетоне, вызванных усадочными деформациями при твердении и перепадом температуры. Для ограничения растрескивания пола в бетонной стяжке нарезаются деформационные швы.
Швы нарезаются, после того как бетон наберет достаточную прочность, обычно через 24 после укладки. Швы нарезаются в той же последовательности, в какой укладывался бетон. Швы нарезаются на глубину 1/3 толщины стяжки. После этого бетон трескается по шву, т.е. трескается направленно, а не хаотично. Для облегчения мытья и уборки полов и для защиты края шва от транспортных нагрузок, нарезанные швы герметизируются. Герметизация защищает шов от проникновения влаги, агрессивных жидкостей и засорения мусором.
stroy-trading.ru
Технология устройства промышленных бетонных полов
Технология устройства промышленных бетонных полов.
Бетонное покрытие – во многих планах выгодный вариант. Оно не требует особого ухода, отличается высокой прочностью, износостойкостью и долговечностью. Использование поверхностных упрочняющих материалов обеспечивает низкое влагопоглощение, адекватную химическую стойкость. Чтобы обеспечить полу высокое качество и длительный срок службы, главное полностью соблюдать технологию работы.
Бетон является достаточно дешевым, а оттого и доступным материалом, с ним довольно просто работать. При этом не требуется никаких особых навыков и знаний. Технология устройства промышленного бетонного пола проста.
Бетонное основание — одна из главных частей промышленного здания, несущих основные механические нагрузки. При строительстве новых зданий перед укладкой бетонного пола требуется тщательно изучить несущую способность основы и присутствие грунтовых вод. Такие исследования проводят профильные учреждения или специализированные компании. На основании полученных данных и технического задания выдается проектное решение конструкции бетонного пола, учитывающее такие параметры как: толщина бетона, марка бетона, схема армирования, схема температурных швов, наличие гидроизоляции, рекомендуемый тип покрытия, ровность пола и т.д.
Для того чтобы дать экономически целесообразное проектное решение конструкции пола, необходимо знать предполагаемые нагрузки на пол, такие как механические, динамические, статические, температурные и химические.
Устройство бетонных полов и оснований под полимерные покрытия регламентируются СНИП 2.03.13-88. Однако, для получения полов высокого качества, ряд положений этого документа требуют некоторых дополнений.
Этап I. Планирование и подготовка.
Технология устройства бетонных полов может выполняться как по грунтовому основанию, так и по существующему бетонному основанию. При укладке бетонного пола на грунт необходимо тщательно сделать основание. Это необходимо во избежание в дальнейшем растрескивания и разрушения бетонного пола, вследствие просадки некачественно сделанного основания.
Вначале для каждого основания производится анализ грунтов объекта и расчет необходимой толщины подушки. Общая толщина подушки из песка и щебня может быть различной в зависимости от видов грунтов в основании, степени их промерзания, высоты поднятия грунтовых вод и т.п. Величина основания для промышленного бетонного пола колеблется в пределах от 0,2 до 1 м. Состав и толщины основания указаны в проектной документации, если таковая вообще имеется))).
Верхний слой подушки основания должен быть обязательно утрамбован и расклинен мелким щебнем фракции 5-20, с помощью виброкатка или виброплиты.
Сначала песчаную подушку необходимо послойно уплотнить. Для этого изначально укладывается подсыпка, толщина которой приблизительно на четверть больше расчётной. Затем песок проливают водой, и с помощью виброкатков или виброплит толщина песчаной подушки приводится к расчётной. После укладки песчаной подушки, производится укладка щебеночной или гравийной подушки крупной фракции с последующим послойным уплотнением.
Существует мнение, что для получения качественной «расклинки» основания можно использовать песок вместо мелкого щебня. Песок не расклинивает крупный щебень, и он не трамбуется. Поэтому на нашем предприятии при подготовке грунтового основания обязательно используется мелкий щебень.
Традиционно для выполнения работ, необходимых для устройства грунтового основания, используется тяжелая строительная дорожная техника — грейдеры, погрузчики. Эта техника не имеет лазерных нивелирующих устройств. Поэтому, показатель уровня ровности поверхности основания получается с большими отклонениями от заданной отметки как мин ±5 см. При таких показателях ровности основания получится огромный перерасход бетона до 30%, что приводит к существенному удорожанию конечной стоимости бетонного пола.
После трамбовки мы выполняем работы по устройству верхнего тонкого слоя основания из гранитного отсева, фракции 0-4мм. Толщина слоя отсева 2-5см. Например, отметка основания, выполненная и передаваемая субподрядчиками, составляет в лучшем случае 3-5 см от нулевой отметки низа бетонного пола. Применяя лазерный нивелир для разравнивания и трамбовки гранитного отсева, достигается ровность верхнего слоя основания ± 5 мм. Такая ровность позволяет полностью избежать перерасхода бетона при устройстве пола и, даже при толщинах бетонного пола, к примеру, 80-130 мм получать абсолютно точные фактические толщины производимых полов.
Если полы устраиваются по песчаной, гравиево-песчаной основе, необходимо определить коэффициент уплотнения грунта. Если коефициент меньше 0,98, то основа уплотняется при помощи виброоборудования.
При укладке пола на старое существующее бетонное основание необходимо произвести его тщательную нивелировку и определить минимальные и максимальные отметки поверхности.После этого, необходимо определить возможную минимальную толщину нового пола, с учетом необходимых нагрузок на новый пол.
Если на старом бетонном основании есть крупные трещины, то их необходимо расширить и заполнить ремонтным составом, состоящим либо из полимера, либо из цементно-песчаной смеси на напрягающем цементе.Участки бетонного основания, не поддающиеся ремонту, необходимо полностью демонтировать и уложить новый бетон. Имеющиеся на отдельных участках основания, недопустимые перепады по высоте, не позволяющие сделать необходимую минимальную толщину пола снимаются шлифовально-мозаичной или фрезеровочной машиной по бетону. Образовавшуюся при этом пыль удаляют при помощи промышленных пылесосов.
Когда старое бетонное основание очищено и выровнено, на него следует нанести слой грунтовки. Грунтовку наносят валиком или кистью равномерно по поверхности. Затем грунтовка должна просохнуть в течении необходимого периода времени, которое указывает производитель.
Внимание! Независимо от времени года, для качественного возведения промышленного бетонного пола необходимо обеспечить оптимальные условия на месте проведения работ. Оптимальная температура в помещении, где выполняются работы от +5 до +25°С при влажности воздуха от 60 до 80%. Также необходимо устранить сквозняки, пыль и попадание на будущий бетонный пол прямых солнечных лучей. Для обеспечения оптимальных условий рекомендуется соорудить солнце- и ветрозащитные временные сооружения.
Устройство бетонной плиты пола осуществляется «картами» — прямоугольниками определенного размера. Размер «карты» определяется площадью пола, уложенного за рабочую смену, т.е. производительностью. По периметру карты устанавливается опалубка. Линия опалубки, по возможности, должна совпадать с рисунком деформационных швов, так как в большинстве случаев это место стыка уже схватившегося и свежеуложенного бетона.
Вдоль всего направления транспортного потока в эксплуатируемом помещении выставляются направляющие или согласно проекта, учитывая конструктивные особенности здания, расположения несущих элементов, колонн, фундаментов, ворот. На больших площадях предусматриваются температурные швы между технологическими картами. Уровень установки направляющих контролируется нивелиром, он должен обеспечивать минимальную толщину бетонного пола в пределах 60-70 мм. Крепление направляющих происходит электросваркой к металлическим анкерам. Вертикальные фрагменты конструкции отсекаются от бетонной плоскости пола, посредством демпферной изоляции вокруг фундаментов, колонн и по периметру всех стен. В качестве демпферной изоляции используется пенопласта, пенополиуретан или вспененный полиэтилен. При необходимости устраивается гидроизоляция.
Армирование в бетонных полах осуществляется в соответствии с проектом в зависимости от предполагаемой несущей нагрузки. Чаще всего в бетонных полах используется дорожная сетка из арматуры класса Вр-1 диаметром стержней 5 мм с размером ячейки 150X150 мм, или 100X100 мм. В тех случаях, когда пол подвергается воздействию повышенных нагрузок целесообразно применить вместо дорожной сетки или вместе с ней арматурный каркас. Арматурный каркас, как правило, вяжется по месту из стержней арматуры диаметром от 8 до 16 мм. Армирование может также производиться металлической фиброй.
В помещениях со средней и большой интенсивностью воздействия на пол жидкостей, уклоны полов, даже под монолитные полимерные покрытия, должны быть не менее 1,5%. Уклоны следует создавать измененяя толщину бетонного основания. Толщина бетонного покрытия должна быть минимум 80 мм, класс бетона по прочности на сжатие не ниже В22,5, как для чистых полов, так и для бетонных оснований.
Этап II. Приготовление бетона и его укладка.
Для устройства бетонных промышленных полов следует использовать бетонную смесь марки не ниже М300, процент вовлеченного воздуха которой составляет не более 3%. Бетон должен быть без воздухоулавливающих, солевых добавок, поскольку есть риск отслаивания топпинга и появления после затирки белого налета на поверхности.
Во время приемки бетона на одну карту не должно быть большого разрыва между миксерами, она должна идти непрерывно. В противном случае это может привести к появлению трещин. Если интервал принятия разных порций бетона в карту превышает 30 — 40 минут, то необходимо устройство технологических стыков с последующей их нарезкой.
Условия и площадь объекта не всегда позволяют миксеру подъехать вплотную к месту укладки, поэтому довольно часто используют бетононасос.
Уплотнение и разравнивание бетонной смеси производится: глубинным вибратором, поверхностным вибратором, виброрейкой или с помощью правила по «жидким маякам». При этом виброрейку следует применять осторожно, чтобы не допустить расслоения бетонной смеси. Обработка проводится на малых оборотах, не более чем за 2 прохода. В некоторых случаях для этих целей используют суперпластификатор.
При укладке и разравнивании бетонной смеси с помощью виброрейки необходимо сначала установить направляющие под виброрейку на уровне нулевой отметки и тщательно выставить их по горизонту. В процессе работы нужно следить за тем, чтобы направляющие не были сбиты. После этого на направляющие монтируется виброрейка.
Бетонная смесь заливается на подготовленное основание и разравнивается с таким расчетом, чтобы ее верх был немного выше уровня виброрейки (это зависит от степени уплотняемости бетонной смеси виброрейкой). После виброрейку тянут по направляющим. Бетонная смесь под действием вибрации оседает до нужного уровня и разравнивается. При этом нужно следить, чтобы виброрейка постоянно скользила по поверхности бетона. В тех местах, где бетонная смесь оседает ниже уровня виброрейки, бетонную смесь добавляют лопатой в необходимом количестве.
По окончанию протягивания проверяется отметка бетона при помощи нивелира или контрольного уровня.
Этап III. Затирка бетона.
После того, как завершен процесс укладки, уплотнения и разравнивания бетонной смеси, необходимо сделать технологический перерыв: бетон должен набрать определенную пластическую прочность. В зависимости от влажности и температуры окружающей среды этот перерыв составляет, как правило, от 2 до 7 часов. За это время бетон схватывается так, что взрослый человек, наступая на его поверхность, оставляет след глубиной 3мм. После этого, его поверхность обрабатывается затирочной машиной для бетона или как их ещё называют вертолетом для затирки бетона. Бетон, примыкающий к конструкциям, колоннам, дверным проемам и стенам, должен быть обработан в первую очередь, так как в этих местах он набирает прочность быстрее, чем на остальной площади.
Если проектом предусмотрено наличие упрочненного верхнего слоя — топпинга, то перед затиркой бетона по поверхности распределяют упрочнитель, представляющий собой сухую смесь из цемента, полимеров, пигментов и наполнителей: кварцевый, корундовый или металлический, в зависимости от нагрузок. Топпинг втирается в свежий бетон спустя несколько часов после его укладки, если применяется вакуумирование, время до укладки упрочнителей значительно сокращается, взаимодействуя с имеющейся в бетоне водой. При этом образуется монолитная структура с бетонным основанием.
Топпинг немного удорожает стоимость бетонного пола, но его применение позволяет получить массу преимуществ:
- Увеличение износостойкости бетонной поверхности;
- Стойкость к ударам и сильному абразивному износу;
- Отсутствие пыли;
- Повышение срока службы бетонного пола;
- Привлекательный внешний вид, широкая цветовая гамма;
- Верхний высокопрочный слой составляет единое целое с бетонным основанием и полностью исключает его отслоение;
- Получение готового к эксплуатации покрытия за один рабочий цикл;
- Не требуется особых условий для устройства полов;
- Снижает стоимость покрытия;
- Значительно сокращаются сроки проведения работ по сравнению с другими покрытиями;
- Позволяет раньше, чем при других покрытиях, начать эксплуатацию помещения.
Далее на обработанную поверхность вносится топпинг в количестве 50-60 % от нормы. Нанесение материала осуществляется при помощи тележки-дозатора, что обеспечивает равномерность нанесения топпинга.
Во время нанесения упрочняющего материала используются средства индивидуальной защиты респираторы, противопылевые очки, перчатки.
После того как нанесённый топпинг впитает влагу из бетонной плиты, и поверхность потемнеет, производится первая затирка диском. Затирку следует начинать около стен, колонн, дверных проемов. Затирать следует до получения однородно перемешанной смеси на поверхности, полного пропитывания смеси «цементным молоком» и полного соединения смеси с поверхностью бетона.
Рекомендуется делать движение диска «змейкой» или «лесенкой», т.е. начинают движение от начала бетонирования вправо, потом ниж
raketa.net.ua