Применение стяжных болтов для сборки опалубки. Монтажные болты
Высокопрочные болты – требования ГОСТ и особенности изделий + Видео
Высокопрочные болты представляют собой крепеж, сопротивление которого равняется не менее 800 МПа. Изготавливаются они по ГОСТ Р 52644, имеют разный вес, диаметр и другие параметры.
1 Основная информация о болтах высокой прочности
Интересующие нас метизы производятся из низкоуглеродистых легированных сталей, в которых содержится не больше 0,4 % углерода. При их изготовлении применяется технология холодной либо горячей высадки исходных заготовок. Резьбу на высокопрочные болты (ВПБ) накатывают на специально предназначенных для этих целей станках-автоматах. Обязательной частью производства описываемых крепежных изделий является их термообработка в электрических печах. Эта операция выполняется с целью придания ВПБ высокой антикоррозионной защиты и повышенной прочности. Кроме того, термическая обработка предохраняет болты от старения.

Высокопрочные болты
Рекомендуем ознакомиться
Класс прочности ВПБ не может быть ниже 8.8. Данный показатель обозначается на головке крепежа. Там же могут присутствовать литеры ХЛ, У и S. Первое обозначение указывает на то, что изделия разрешается использовать в низкотемпературных условиях (до -60 °С). Метизы с буквой У предназначены для эксплуатации при температурах не ниже -40°. А литера S указывает на увеличенные параметры головки ВПБ.
Используются рассматриваемые нами изделия в сфере производства автомобилей, машиностроении, строительстве, при возведении железных дорог и мостов для соединения разнообразных деревянных и металлических конструкций. Особые свойства такого крепежа (стойкость к экстремальным температурам, противодействие влиянию агрессивных соединений, прочность) делают его незаменимым при выполнении ряда промышленных работ. ВПБ применяются и в бытовых условиях. В подобных ситуациях они используются в качестве надежных анкеров, позволяющих зафиксировать в стеновых поверхностях из бетона практически любые конструкции и предметы.
2 Требования Госстандарта Р 52644–2006 – вес, длина, сечение ВПБ
ВПБ выпускаются с диаметром резьбы М16, М20, М24, М30, М36, М42, М48, классами прочности – 8.8, 9.8, 10.9, 12.9. Длина болтов варьируется в пределах 40–300 мм. Вес изделий зависит от их длины и диаметра. Он колеблется в достаточно широких пределах. Вес 1000 штук ВПБ М16 равняется 116–514 кг, М20 – 204–804 кг, М24 – 377–1210 кг. Масса болтов М30–М42 изменяется от 633 до 3830 кг. А вот вес 1000 ед. М48 равняется 2495–5002 кг. Изделия высокой прочности производятся со специальным покрытием либо без такового. Толщина дополнительно слоя регламентируется ГОСТ. Для метизов М16 она должна быть не выше 25 мкм, для М20 – 30, для М24 – 40, М30–М48 – не более 50 мкм.

Высокопрочные болты М 20
Теоретический вес 1000 единиц ВПБ, который мы указывали выше, рассчитывается для изделий без специального покрытия. Высокопрочные метизы обязаны изготавливаться с постоянным уровнем качества резьбовой поверхности. Это является гарантией требуемого обеспечения затяжки соединений, выполняемых посредством ВПБ. Уровень качества обуславливается показателем закручивания (так называемый коэффициент или момент затяжки). Его величина зависит от типа смазки и дополнительного покрытия болтов. Высокопрочные изделия с произвольным покрытием должны иметь коэффициент закручивания в пределах 0,11–0,2. Метизы со стандартной смазкой и покрытием – 0,14–0,2. Проверяют коэффициент закручивания по Госстандарту Р 52643.
ВПБ чаще всего выпускаются из сталей 40Х и 40Х Селект. Второй из указанных сплавов по своему химическому составу является максимально качественным. Он, по сути, представляет собой выборку из нескольких партий 40Х. Сплавы с маркировкой Селект имеют стабильные механические показатели. Достигаются они именно за счет проведения выборки. Болты из стали 40Х Селект используются для соединения конструкций высокой степени ответственности (эксплуатируемых в особых условиях, имеющих большой вес). В остальных случаях применяются ВПБ из обычных сплавов 40Х. Выборка стали 40Х Селект осуществляется непосредственно на литейном производстве.
Покрытие описываемых болтов бывает следующих видов:
- электролитическое кадмиевое;
- электролитическое цинковое;
- горячее цинковое.
При наличии на крепежных изделиях любого из этих покрытий обязательным является их обработка смазывающим составом.
3 Соединения на ВПБ – ключевые положения СниП III-18-75
Указанные Саннормы описывают правила производства металлических конструкций. В них рассматриваются все существующие соединения на высокопрочных болтах:
- С несущими метизами. В них передача сдвигающих усилий осуществляется через смятие, срез и трение.
- Фрикционное. В этом случае усилия передаются исключительно посредством трения.
- Болтосварное, болтозаклепочное и болтоклеевое.
- Фланцевое. Такие соединения на высокопрочных болтах используются в конструкциях, в которых крепеж работает только на изгиб (фланцы податливого типа) либо на растяжение (жесткие фланцы).
Отдельно отметим, что любое фрикционное соединение проектируется по спецнормативам. Они изложены в СНиП II-В.3-72. Прочие виды соединений разрабатываются по техусловиям конкретного производителя работ. Они могут быть разными. Все болтовые соединения имеют собственное обозначение на чертежах. Оно остается неизменным, начиная с 1968 года, когда был введен в действие Госстандарт 2.315.

Крепление высокопрочных болтов
Обозначение ВПБ при фрикционном соединении имеет вид обычного треугольника. В чертежах металлоконструкций, которые собираются при помощи ВПБ, указываются методы просверливания отверстий и их номинальные сечения, а также вид соединения. Эти данные присутствуют в первую очередь. Кроме того, в чертежах СНиП требуют указывать следующие характеристики:
- марку сплава, из которого делаются болты (40Х Селект или другие стали), а также ГОСТ на изготовление последних;
- осевое усилие и способ натяжения ВПБ;
- коэффициент трения;
- вариант обработки соприкасающихся деталей;
- спецификацию болтов, шайб и гаек;
- коэффициент сопротивления (временного) на разрыв крепежных элементов.
СНиП выдвигают специальные требования к отправочным частям металлоконструкций, которые соединяются рассматриваемыми в статье болтами. Они обычно собираются в предназначенных для этого приспособлениях (чаще всего в кондукторах), располагающих крепежными фиксаторами. Отверстия для монтажа метизов высверливаются под проектное сечение ВПБ (оно указывается на чертежах). Диаметры отверстий подбираются с учетом условий эксплуатации конструкции. Также в данном случае принимается во внимание коэффициент сдвигоустойчивости сооружений.
Для болтов М20 из стали 40Х Селект допускается высверливать отверстия сечением 21, 23 и 25 мм, для М24 – 25, 28 и 30 мм. Возможное отклонение от указанных параметров – не более +1,5 мм. Края отверстий в обязательном порядке обрабатываются с целью удаления с них заусенец. При этом фаски не снимаются.
4 Как крепить высокопрочные метизы – какова технология?
Операция состоит из пяти отдельных этапов. Они приведены далее:
- Производится обработка поверхностей деталей и элементов, которые соприкасаются друг с другом.
- Выполняется подготовка крепежа.
- Осуществляется сборка соединений.
- Делается затяжка (натяжение) ВПБ.
- Соединения герметизируются.
Обработка соприкасающихся деталей по СНиП выполняется механическими либо стальными щетками, многопламенными ацетиленовыми горелками (огневая методика), металлическим или кварцевым песком (пневматический способ). Эта операция производится максимально тщательно, так как она изменяет коэффициент трения, а значит, от нее зависит, какая у соединения будет несущая способность. После обработки сборка конструкции должна выполняться в минимальные сроки. По истечению 72 часов выполнять соединение деталей запрещается. В подобных случаях соприкасающиеся поверхности СНиП требуют обрабатывать повторно, используя ранее применявшуюся методику.

Маркировка высокопрочных болтов
Под подготовкой болтов высокой прочности понимают их расконсервацию, прогонку резьбы метизов, которые отбраковываются, очистку изделий от коррозии и грязи. Удаление смазочного слоя (он наносится на все ВПБ, его задача – выравнивать коэффициент закручивания крепежных элементов) осуществляется посредством их кипячения. Для этих целей используется обычная вода. После кипячения болты окунаются в раствор автола (15 %) и неэтилированного бензина (85 %). Подготовленные описанным способом изделия нельзя хранить более 10 суток из-за того, что коэффициент закручивания болтов может увеличиться.
Прогонка резьбы ВПБ производится специальным гайковертом пневматического типа. После этого можно приступать непосредственно к сборке соединения.
Процедура выполняется по следующей схеме:
- Осмотр металлоконструкции.
- Совмещение и фиксация монтажных отверстий (используются особые пробки) в положениях, указанных на чертежах.
- Установка болтов в свободные отверстия.
- Анализ параметров (геометрических) собранного сооружения.
- Стяжка (максимально плотная) пакетов.
- Затяжка ВПБ на оговоренное в проекте усилие.
- Демонтаж пробок, монтаж на их место крепежных элементов, затяжка установленных болтов. Она, опять же таки, производится на заданное усилие.
Все высокопрочные болты монтируются в металлоконструкции с двумя шайбами (они также изготавливаются высокопрочными, в противном случае несущая способность соединения снижается). Одна из них предназначена под гайку, вторая – под головку крепежного изделия. СНиП запрещают размещать две шайбы (и более) под один пакет. При монтаже болтов высокой прочности гайки обязаны накручиваться на резьбу от руки (свободно). Другие варианты не допускаются. Если гайка наворачивается с трудом, ее следует заменить (как вариант – установка другого ВПБ).
Пробки освобождаются исключительно после монтажа болтов во все свободные отверстия и затяжки крепежа на заданное усилие. При этом следует поочередно вынимать пробки и сразу же ставить на их место ВПБ. Финальное натяжение высокопрочных болтов всех видов (М20, М24) на предусмотренное в проекте усилие выполняется только после тщательного анализа геометрических параметров металлоконструкции. Подробнее о правилах затяжки метизов далее.
5 Как выполняется натяжение болтов?
Усилие при натяжении ВПБ может регулироваться несколькими способами. Мы приводим их ниже:
- По числу ударов гайковерта.
- По осевому натяжению крепежного изделия.
- По углу поворота гайки.
- По моменту закручивания.
Здесь нужно знать, что вне зависимости от варианта затяжки высокопрочного крепежа обязательно необходимо использовать стяжные болты. На начальном этапе натяжения головку ВПБ следует придерживать. Сам процесс выполняется от самого жесткого участка соединения либо от его середины. Для натяжения болта на определенное усилие пользуются динамометрическим ключом. Этот инструмент позволяет четко определять момент (коэффициент) затяжки соединения.
Порядок натяжения соединения динамометрическим ключом таков:
- производится стягивание пакета стяжными изделиями;
- все болты (в том числе и стяжные) затягиваются на заданное усилие;
- пробки выбиваются, на их место монтируются ВПБ.
После этого установленный крепеж затягивается до отказа ключом. Болты М24 часто натягиваются посредством гайковерта, который тарируется по повороту гайки на определенный угол. Такой инструмент позволяет получить момент закручивания не ниже 1600 Нм. Тарировку приспособления для болтов М24 осуществляют перед началом выполнения работ. Описанный гайковерт может снабжаться сменными конусными головками. Они имеют повышенный вес. За счет этого удается снижать потери мощности от скручивания. Большой вес головок – это не единственная их особенность. Кроме того, их обязательно подвергают термообработке. Причем выполняется она так, чтобы сменные приспособления имели твердость по шкале HRC в пределах 35–45 единиц.

Натяжение выспокопрочных болтов
Болты М24 могут затягиваться не одним ключом, а сразу двумя. Такая методика дает возможность получать максимально точный момент закручивания. Используется она достаточно часто. В данном случае первым ключом (его называют малым) создают момент закручивания не более 200 Нм. После этого берут второй инструмент (большой). И уже этим ключом выполняют финальную затяжку. Он обеспечивает момент закручивания на уровне 1600 Нм. Натяжение высокопрочных болтов М20, М16, М30 и так далее (всех, кроме М24) осуществляют в большинстве случаев с ориентиром на осевое усилие. Операция выполняется электрическим либо пневматическим ключом. Его обязательно тарируют перед сборкой металлоконструкции.
Можно выполнять натяжение ВПБ М20 и других размеров, корректируя усилие на момент закручивания. Методика достаточно сложная. Для ее реализации нужно высчитать момент закручивания и постоянно измерять его при затяжке болта динамометрическим ключом. Последний способ натяжения предполагает применение ударного электрического гайковерта. Этот инструмент применяется для болтов М24 и М20. Методика проста. Все смонтированные крепежные изделия затягиваются указанным ключом посредством нанесения на гайки трех ударов (единичных). После этого производится затяжка болтов тем же способом. Но теперь уже наносится столько ударов, сколько требуется для получения в стержнях высокопрочного крепежа заданного осевого натяжения. Их число обычно находится в пределах 14–18.
6 Особенности разных видов соединений на крепежных элементах высокой прочности
Фрикционное соединение при проектировании считают неподатливым. А продольное усилие (точнее – его распределение между отдельными элементами металлоконструкции) рассматривается, как равномерное. На основании этих фактов и рассчитывают фрикционное соединение. Расчет осуществляется по усилиям. Причем обязательно принимаются во внимание усилия между разными участками рассматриваемого элемента.
Несущая способность такого соединения обязана составлять более 75 % способности детали, которая прикрепляется к конструкции. Важно! Несущая способность каждого элемента рассчитывается отдельно. При этом проводятся вычисления его прочности, выносливости и устойчивости, которые учитывают вес и другие параметры детали. Несущие высокопрочные болты применяются для сборки конструкций нескольких типов:
- Постоянные и временные сооружения, расчет которых выполняется на подвижные либо динамические нагрузки.
- Постоянные конструкции, рассчитанные исключительно на статические нагрузки.
- Временные сооружения, проектируемые на нагрузки статического плана.
Болтоклеевые соединения производятся тогда, когда следует учитывать изгибающий момент и иные сдвигающие усилия (обычно под таковыми понимают поперечные и продольные силы). В таких конструкциях на контактные изделия наносится специальная клеевая пленка, которую обжимают ВПБ. В качестве клея обычно используют составы ЭД-20 и ЭД-16. Они включают в себя пластификатор, эпоксидную смолу, отвердитель и корунд в качестве специального наполнителя.
Болтоклепаные соединения используются при необходимости монтажа высокопрочных крепежных изделий вместо применявшихся ранее заклепок. Отдельным типом монтажа они не являются. Следует ответственно подбирать высокопрочные болты для установки их вместо заклепок. Существуют специальные таблицы, в которых указывается соответствие диаметров заклепочных и болтовых соединений. Например, вместо заклепок сечением 21 мм необходимо использовать болты с сечением 20 мм. А вот крепежом М24 заменяют заклепочные элементы диаметром 23 мм.
tutmet.ru
Высокопрочные болты

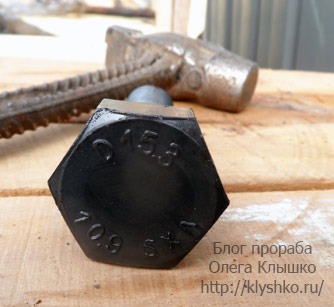
В начале моей трудовой деятельности я не вникал в марки болтов, их прочность приоритет был размеры болтов и гаек, но конечно в заявках я указывал болты с характеристиками из проекта. Как выяснилось, это было не правильно и кроме размеров необходимо обращать внимание и на характеристики болтов.
Технической литературы вроде вот этой «Рекомендации по надзору и технической эксплуатации монтажных соединений на высокопрочных болтах стальных строительных конструкций зданий и сооружений Министерства металлургии СССР» или «ГОСТ Р 52644-2006 Болты высокопрочные с шестигранной головкой с увеличенным размером под ключ» не читал, если и читал в институте, то не помню.
Давайте разберемся, что такого необычного в высокопрочных болтах. К данной группе болтов относятся изделия, у которых сопротивление к временным нагрузкам равно 800 МПа. Класс прочности начинается с 8.8 для болтов и 8 для гаек.
Что обозначают цифры 8.8? Первое число, умноженное на 10 показывает величину минимального временного сопротивления в кгс/мм2, второе число так же умноженное на 10 указывает отношение предела текучести к временному сопротивлению в процентах.
Например, первая цифра 8х10=80 кгс/мм2 это значение минимального временного сопротивление металла σв, отношение предела текучести σт к временному сопротивлению σв в процентах равно 8×10 = 80 %.
Предел текучести рассчитывается умножением первой цифры маркировки на вторую 8х8=64 кгс/мм2.
На наших болтах соединяющие балку имеется обозначение:
- D15.3 болт щелковского завода.
- 10.9 – минимальное временное сопротивление болта равно 10.9 кгс/мм2
- SXЛ – S обозначает увеличенный размер шестигранной головки под ключ, ХЛ – обозначает, что данные болты могут использоваться в районах с температурой опускающейся от -40 до -65 градусов.
Если вы не смогли найти болты с заданными характеристиками по проекту, то разрешается их замена в большую сторону, например вместо 8.8 использовать болты 10.9.
Особенностью соединений высокопрочных болтов является то, что усилия воспринимаются не срезом болтов и смятием стенки, а силами трения между соединенными поверхностями. Исходя из этого, большое внимание необходимо уделять к поверхностям соединений удалять ржавчину и грязь.
Недостаточное натяжение болтов приведет к «проскальзыванию» элементов и болты будут работать на срез, а элементы на смятие, что приведет к деформации конструкции и разрушению бо
klyshko.ru
15. болтовые монтажные соединения рекомендации по монтажу стальных строительных конструкций- методическая документация в строительстве- мдс 53-1-2001 (утв- Госстроем РФ) (2018). Актуально в 2018 году
размер шрифта
+7 812 627 17 35
+7 499 350 44 79
8 (800) 333-45-16 доб. 100
РЕКОМЕНДАЦИИ ПО МОНТАЖУ СТАЛЬНЫХ СТРОИТЕЛЬНЫХ КОНСТРУКЦИЙ- МЕТОДИЧЕСКАЯ ДОКУМЕНТАЦИЯ В СТРОИТЕЛЬСТВЕ- МДС 53-1-2001 (утв-... Актуально в 2018 году
15.1. Монтажные соединения без контролируемого натяжения болтов.
15.1.1. К монтажным соединениям без контролируемого натяжения болтов относятся срезные, в которых внешние усилия воспринимаются за счет сопротивления болтов срезу и соединяемых элементов смятию.
15.1.2. Под гайки болтов необходимо устанавливать не более одной круглой шайбы (ГОСТ 11371). Допускается установка одной такой же шайбы под головку болта. В необходимых случаях следует устанавливать косые шайбы (ГОСТ 10906).
15.1.3. При сборке соединений отверстия в деталях конструкций должны быть совмещены и зафиксированы от смещения деталей сборочными пробками (не менее двух), а собранные пакеты плотно стянуты болтами. В соединениях с двумя отверстиями сборочную пробку устанавливают в одно из них.
15.1.4. Максимальная разница между номинальными диаметрами отверстия и болта в срезных соединениях не должна превышать 3 мм.
15.1.5. В собранном пакете болты заданного в проекте диаметра должны пройти в 100% отверстий. Допускается прочистка 20% отверстий сверлом, диметр которого равен диаметру отверстия, указанному в проекте. В срезных соединениях допускается чернота (несовпадение отверстий в смежных деталях собранного пакета): до 1 мм - в 50% отверстий и до 1,5 мм в 10% отверстий.
В соединениях, где болты установлены конструктивно, чернота не должна превышать разности диаметров отверстия и болта.
15.1.6. Резьба болтов не должна входить в глубь отверстия более чем наполовину толщины крайнего элемента пакета со стороны гайки.
15.1.7. Решения по предупреждению самоотвинчивания гаек - постановка пружинной шайбы (ГОСТ 6402) или контргайки - должны быть указаны в проекте. Применение пружинных шайб не допускается при овальных отверстиях.
15.1.8. Гайки и контргайки следует закручивать до отказа от середины соединения к его краям.
15.1.9. Плотность стяжки собранного пакета надлежит проверять щупом толщиной 0,3 мм, который в пределах зоны, ограниченной шайбой, не должен проходить между собранными деталями на глубину более 20 мм. Стержень болта должен выступать из гайки не менее чем на 3 мм.
15.1.10. Качество затяжки постоянных болтов следует проверять отстукиванием их молотком массой 0,4 кг, при этом болты не должны смещаться.
15.2. Монтажные соединения на высокопрочных болтах с контролируемым натяжением
15.2.1. К монтажным соединениям на высокопрочных болтах с контролируемым натяжением относятся: фрикционные или сдвигоустойчивые соединения, в которых внешние усилия воспринимаются за счет сопротивления сил трения, возникающих по контактным плоскостям соединяемых элементов от предварительного натяжения болтов; фрикционно-срезные соединения, в которых внешние усилия воспринимаются, главным образом, за счет преодоления сопротивления сжатию фланцев от предварительного натяжения высокопрочных болтов.
15.2.2. Фрикционные и фрикционно-срезные соединения
15.2.2.1. Во фрикционных и фрикционно-срезных соединениях соприкасающиеся поверхности деталей должны быть обработаны способом, предусмотренным в проекте. С поверхностей, подлежащих обработке, необходимо предварительно удалить масляные загрязнения.
Состояние поверхностей после обработки и перед сборкой следует контролировать и фиксировать в журнале.
До сборки соединений обработанные поверхности необходимо предохранять от попадания на них грязи, масла, краски и образования льда. При несоблюдении этого требования или начале сборки соединения по прошествии более трех суток после подготовки поверхностей их обработку следует повторить.
15.2.2.2. Перепад поверхностей (депланация) соединяемых элементов свыше 0,5 и до 3 мм должен быть ликвидирован механической обработкой с образованием плавного скоса с уклоном не круче 1:10.
При перепаде свыше 3 мм необходимо устанавливать прокладки требуемой толщины, обработанные тем же способом, что и детали соединения. Применение прокладок требует согласования с организацией - разработчиком проекта.
15.2.2.3. Отверстия в деталях при сборке должны быть совмещены и зафиксированы от смещения пробками. Число пробок определяют расчетом на действие монтажных нагрузок, но их должно быть не менее 10% при числе отверстий 20 и более и не менее двух при меньшем числе отверстий.
В собранном пакете, зафиксированном пробками, допускается чернота (несовпадение отверстий), не препятствующая свободной без перекоса постановке болтов. Калибр диаметром на 0,5 мм больше номинального диаметра болта должен пройти в 100% отверстий каждого соединения.
Допускается прочистка отверстий плотно стянутых пакетов сверлом, диаметр которого равен номинальному диаметру отверстия, при условии, что чернота не превышает разницы номинальных диаметров отверстия и болта.
Применение воды, эмульсий и масла при прочистке отверстий запрещается.
15.2.2.4. Максимальная разность номинальных диаметров отверстий и болтов допускается: для фрикционных соединений - не более 6 мм, для фрикционно-срезных - не более 3 мм.
15.2.2.5. Заданное проектом усилие натяжения высокопрочных болтов следует обеспечивать закручиванием гайки требуемым расчетным крутящим моментом (натяжение по моменту закручивания).
Допускается осуществлять натяжение высокопрочных болтов по углу поворота гайки. Этот способ допустим только для болтов диаметром 24 мм с временным сопротивлением разрыву не менее 1100 МПа при толщине стягиваемых деталей до 140 мм и числе тел в пакете до 7.
Допускается применение других способов натяжения высокопрочных болтов, гарантирующих получение заданного усилия их натяжения. Каждый из этих способов должен быть представлен в специальных технических условиях и чертежах металлических конструкций (КМ).
15.2.2.6. Расчетный момент закручивания М, необходимый для натяжения болта, следует определять по формуле:
где К - среднее значение коэффициента закручивания, установленное для каждой партии болтов в сертификате предприятия-изготовителя либо определяемое на монтажной площадке с помощью контрольных приборов в соответствии с требованиями ГОСТ 22356;
Р - расчетное усилие натяжения болта, заданное в рабочих чертежах, кН;
d - номинальный диаметр болта, мм.
15.2.2.7. Натяжение болтов с регулированием усилий по величине крутящего момента осуществляют в два этапа: на первом этапе болты затягивают при помощи гайковертов на 50 - 80% расчетного усилия для обеспечения плотности деталей пакета; на втором - болты дотягиваются до полного расчетного усилия динамометрическими ключами статического действия с контролем натяжения по величине прикладываемого крутящего момента.
Применение на втором этапе натяжения инструмента динамического действия (ударно-импульсные, редкоударные и т.п.) не допускается.
При натяжении болтов за их головку величину крутящего момента следует увеличивать на 5%.
15.2.2.8. Натяжение болтов по углу поворота гайки следует производить в следующем порядке:
- затянуть вручную все болты в соединении до отказа монтажным ключом с длиной рукоятки 0,3 м;
- повергнуть гайки болтов на угол 180° +- 30°.
15.2.2.9. Натяжение болтов следует контролировать:
- при числе болтов в соединении до 4 - все болты, от 5 до 9 - не менее трех болтов, 10 и более - 10% болтов, но не менее трех в каждом соединении;
- фактический момент закручивания должен быть не менее расчетного, определенного по формуле (1), и не превышать его более чем на +15%. Отклонение угла поворота гайки допускается в пределах +- 30°;
- при обнаружении хотя бы одного болта, не удовлетворяющего этим требованиям, контролю подлежит удвоенное число болтов. В случае обнаружения при повторной проверке одного болта с меньшим значением крутящего момента или с меньшим углом поворота гайки должны быть проверены все болты с доведением момента закручивания или угла поворота гайки до требуемой величины;
- порядок натяжения болтов должен исключать образование неплотностей в стягиваемых пакетах. Щуп толщиной 0,3 мм не должен входить в зазоры между деталями соединения.
15.2.3. Фланцевые соединения
15.2.3.1. Подготовку контактных поверхностей фланцев следует осуществлять в соответствии с указаниями проектной документации. При отсутствии таких указаний контактные поверхности очищают ручными или механическими стальными щетками от грязи, наплывов грунтовки и краски, рыхлой ржавчины, снега и льда.
15.2.3.2. Во фланцевых соединениях следует применять болты только исполнения ХЛ, а также гайки, шайбы к ним, выполненные в соответствии с требованиями ГОСТ 22353, ГОСТ 22356.
15.2.3.3. Натяжение высокопрочных болтов фланцевых соединений следует выполнять от наиболее жесткой зоны (жестких зон) к его краям.
15.2.3.4. Натяжение высокопрочных болтов фланцевых соединений следует осуществлять только по месту закручивания, величина которого определяется по формуле:
М = 0,9 К Р d, Н х м. | (2) |
Отклонение фактического момента закручивания от момента, определяемого по формуле (2), должно быть не менее расчетного и не превышать его более чем на 10%.
15.2.3.5. Качество выполнения фланцевых соединений ответственное лицо проверяет путем пооперационного контроля. Контролю подлежит:
- качество подготовки (расконсервации) болтов; качество подготовки контактных поверхностей фланцев;
- соответствие устанавливаемых болтов, гаек, шайб требованиям ГОСТ 22353 - ГОСТ 22356, а также требованиям, указанным в проектной документации;
- наличие шайб под гайками и головками болтов; длина части болта, выступающей над гайкой;
- наличие клейма монтажника, осуществляющего сборку соединения.
15.2.3.6. Контроль усилия натяжения следует осуществлять во всех установленных высокопрочных болтах тарированными динамометрическими ключами. Контроль усилия натяжения следует производить не ранее чем через 8 ч после выполнения натяжения всех болтов соединении, при этом усилия в болтах должны соответствовать значениям, указанным в таблице 15.1. Если при контроле обнаружатся болты, не отвечающие этому условию, то усилие натяжения этих болтов должно быть доведено до требуемого значения.
Таблица 15.1
Усилие натяжения болтов (контролируемое), кН (тс) | ||
Номинальные диаметры высокопрочных болтов с временным сопротивлением не менее 1100 МПа (110 кгс/мм2), исполнения ХЛ по ГОСТ 22353-ГОСТ 22356 | ||
М20 | М24 | М27 |
167 (17) | 239 (24,4) | 312 (31,8) |
15.2.3.7. Документация, предъявляемая при приемке готового объекта, кроме предусмотренной п.1.22. СНиП 3.03.02, должна содержать сертификаты или документы завода-изготовителя, удостоверяющие качество стали фланцев, болтов, гаек и шайб, документы завода-изготовителя о контроле качества сварных соединений фланцев в присоединяемыми элементами, журнал контроля за выполнением монтажных фланцевых соединений на высокопрочных болтах.
15.3. Общие требования к выполнению монтажных соединений на высокопрочных болтах с контролируемым натяжением
15.3.1. Подготовку и сборку соединений необходимо проводить под руководством лица (мастера, прораба), назначенного приказом по монтажной организации ответственным за выполнение этого вида соединения на объекте.
15.3.2. К выполнению соединений допускаются рабочие, прошедшие специальное обучение, подтвержденное соответствующим удостоверением.
15.3.3. Запрещается применение болтов, не имеющих на головке заводской маркировки временного сопротивления, клейма предприятия-изготовителя, условного обозначения номера плавки, а на болтах климатического исполнения - букв "ХЛ".
15.3.4. Перед сборкой соединений болты, гайки и шайбы должны быть подготовлены. Традиционный способ подготовки метизов должен включать: очистку от грязи и ржавчины; прогонку резьбы отбракованных болтов и гаек; нанесение смазки. Нанесение тонкого слоя смазки следует производить путем кипячения их в воде с последующей промывкой в смеси, состоящей из 85% неэтилированного бензина и 15% машинного масла.
Подготовленные таким образом метизы к постановке следует хранить в закрытых ящиках не более 10 дней. При превышении этого срока метизы должны быть обработаны повторно.
15.3.5. Перед сборкой соединений метизы с целью снижения коэффициента закручивания следует подготавливать с применением способа парафинированного покрытия. Очистку крепежных изделий и нанесение на них покрытия необходимо выполнять в следующей последовательности:
- высокопрочные болты и гайки уложить в сетчатый контейнер и установить его в ванну с кипящим раствором моющего средства (МС-15, концентрация 15 г/дм3; МС8, концентрация 20 г/дм3; кальцинированная сода, концентрация 30 г/дм3) и выдержать в течение 20 мин;
- нанести покрытие путем 3 - 4-кратного погружения контейнера с горячими очищенными крепежными изделиями (каждое погружение 1 - 2 мин) в ванну с расплавленным парафиновым составом (70 - 80°С), состоящим из следующих компонентов, % по массе:
парафин марки Т (ГОСТ 23683) 90 +- 1,0
атактический полипропилен 10 +- 0,5;
- извлечь контейнер из ванны с расплавленным парафиновым составом и охладить до температуры окружающей среды;
- обработанные крепежные изделия уложить в тару для подачи на рабочее место.
На таре указать типоразмер обработанных крепежных изделий, дату обработки, номера сертификатов и партий. Крепежные изделия с покрытием можно хранить в защищенном от атмосферных воздействий месте до четырех месяцев. Крепежные изделия, промытые в моющем растворе, можно хранить в тех же условиях не более 10 сут.
15.3.6. Для всех типов соединений под головку болта и гайку должно быть установлено по одной шайбе. Допускается для фрикционных соединения при разности диаметров отверстия и болта не более 4 мм установка одной шайбы только под элемент (гайку или головку болта), вращение которого обеспечивает натяжение болта. Выступающая за пределы гайки часть стержня болта должна иметь не менее одной нитки резьбы.
15.3.7. Для всех типов болтовых соединений запрещается закрепление гаек путем забивки резьбы болта или приварки их к стержню болта.
15.3.8. Для соединений с контролируемым натяжением высокопрочных болтов после окончания их сборки старший рабочий-сборщик (бригадир) обязан в предусмотренном месте поставить клеймо (присвоенный ему номер или знак).
15.3.9. После контроля натяжения и приемки соединения все наружные поверхности, включая головки болтов, гайки и выступающие из них части резьбы болтов, должны быть очищены, огрунтованы, окрашены, а щели в местах перепада толщин и зазоры в стыках зашпатлеваны.
15.3.10. Все работы по натяжению и контролю натяжения следует регистрировать в журнале выполнения соединений на болтах с контролируемым натяжением в соответствии с требованиями СНиП 3.03.01.
www.zakonprost.ru
характеристики, монтаж по шагам, цены
Опалубка для бетонных работ должна быть достаточно прочной, ведь раствор на нее оказывает немалое давление. В большинстве случаев хватает вбитых в землю подкосов и колышков с обвязкой, которые не дают щитам расползаться в стороны. Но при отливке мощных конструкций понадобится крепление посерьезнее – стяжной винт.
Оглавление:
- Что такое стяжной винт?
- Комплектация и руководство по установке
- Средние цены
Описание
Речь идет об анкерном стержне – профилированной арматуре с нарезанной резьбой диаметром 17 мм. Длина шпильки может быть любой – от полуметра до 6 м – все зависит от толщины отливки. Такое устройство незаменимо при строительстве монолитных сооружений и подходит для усиления как горизонтальной опалубки, так и вертикальной.
Одновременно стяжка позволяет регулировать ширину бетонной формы с точностью до миллиметров, оптимизировать расход раствора (не говоря уже о снижении его потерь при вытекании через щели). Элементы проще и быстрее демонтируются, после чего их можно использовать повторно. Также существует более современное устройство – монтажные зажимы.
Характеристики и назначение стяжки
Стяжные болты изготавливаются из стали – черной (Ст20, Ст35, 35ГЛ) или с защитной оцинковкой. Они довольно тяжелые по весу (1,2-1,4 кг/п.м), но долговечны и способны выдержать большую нагрузку от 11 до 16 т. На строительном рынке есть и композитные винты, сделанные из легкого стеклопластика. Эти отличаются низкой стоимостью, устойчивостью к коррозии и не проводят электрический ток. Но у них средние прочностные характеристики – одна шпилька держит всего 600 кг, а при повторном использовании – 250 кг.
Сопротивление на срез у композитных болтов невелико, и под действием поперечных сил они просто разламываются. Расход их оказывается куда больше – на 1 м2 щитов потребуется 4-8 винтов. Среди таких приспособлений можно отыскать недорогие одноразовые комплекты для использования вместе с несъемными формами.
Стяжка в первую очередь необходима, чтобы уменьшить давление бетонной смеси на нее. Благодаря использованию такой системы нагрузка равномерно распределяется на параллельные стенки формы. Без жесткой связки раствор просто выдавит щиты и вытечет наружу. Крепление можно устанавливать на любом ярусе несъемной опалубки, чтобы увеличить надежность и качество отливки будущих стен.
Комплектация и особенности монтажа
Сам по себе анкерный стержень не способен удержать стенки формы под давлением бетона, поэтому в комплект всегда входят стяжные винты для опалубки, гайки и шайбы. Для защиты металлической арматуры от контакта с раствором на него надевается специальный кожух. Это ПВХ-трубка диаметром 22 мм, которая остается в монолите после распалубливания.
Стяжные гайки отливаются из чугуна ВЧ-40 либо из стали 35ГЛ. Они тоже имеют антикоррозионное покрытие из оцинковки и способны удерживать нагрузку до 14 т при собственном весе 570-650 г. Их различают по диаметру плоской опорной площадки (80, 90 или 100 мм), но характеристики метизов от этого не меняются.
Что же касается шайбы, то ее функции стандартны. От плоского куска листового железа 100х100 или 150х150 мм требуется только не дать гайке на винте врезаться в поверхность фанерного щита, а равномерно распределить давление по всей своей площади. Квадратные накладки обычно идут толщиной 4-5 мм и весом от 0,4 до 1 кг.
Всего для надежной связки двух стандартных противопоставленных плит требуется приобрести минимум 3-4 комплекта стяжки. В пересчете на их площадь расход на 1 м2 получается невелик – достаточно устанавливать винты через полметра в два ряда. На каждый из них уйдет дополнительно по 2 шайбы и 2 гайки.
Порядок монтажа:
- Перед установкой палуб в них просверливают сквозные отверстия диаметром 22 мм (чтобы поместилась ПВХ-трубка).
- Внутрь пластикового кожуха заводят стяжной болт для опалубки, прошивая параллельные щиты.
- С двух сторон на стержень нанизывают шайбы и наживляют фланцевые гайки.
- Закручивая метизы по резьбе, регулируют расстояние между стенками в соответствии с толщиной будущей отливки.
Винты требуется размещать не у самых кромок щитов, а с отступом хотя бы в 10 см. Парная стяжка монтируется в верхней и центральной части палубы, а снизу ее просто распирают подкосами, чтобы уменьшить расход анкеров.
Стоимость
Количество стяжек определяется размерами будущего монолита и давлением цементной смеси. Зная характеристики винтов и гаек, можно рассчитать шаг их установки и число. Строители ориентируются на показатели для тяжелого бетона – он действует на щиты с усилием 370 кг/п.м.
Наименование | Количество | Цена, рубли |
Стяжной болт стальной | 1 м | 100 |
Гайка ВЧ-40 (d-90 мм) | 1 шт. | 90 |
Гайка ВЧ-40 (d-100) | 1 шт. | 130 |
Гайка 35ГЛ | 1 шт. | 260 |
Трубка ПВХ (d-22) | 1 м | 18 |
Шайба | 1 шт. | 50 |
Стеклопластиковая стяжка | комплект | 132 |
Покупать материалы лучше с запасом, особенно ПВХ-кожух – он останется в монолите даже после демонтажа опалубки. Все прочие элементы можно будет использовать повторно. Если же они вам нужны только для разовой работы, лучше купить стяжные комплекты б/у – их стоимость почти вдвое ниже.
stroitel-lab.ru
Конструкции стальные строительные. Болтовые соединения. Изготовление и монтаж
Документы по стандартизации Конструкции металлические
ЗАО «ЦНИИПСК им. Мельникова»
ОАО НИПИ «Промстальконструкция»
стандарт организации
КОНСТРУКЦИИ СТАЛЬНЫЕ СТРОИТЕЛЬНЫЕБОЛТОВЫЕ СОЕДИНЕНИЯИзготовление и монтаж
СТО 0051-2006 (02494680, 01408401)
Москва 2006
1 РАЗРАБОТАН ЗАО Центральный ордена Трудового Красного Знамени научно-исследовательский и проектный институт строительных металлоконструкций им. Н.П. Мельникова (ЗАО «ЦНИИПСК им. Мельникова»).
ОАО Научно-исследовательский и проектный институт «Промстальконструкция»
2 ВНЕСЕН организациями-разработчиками стандарта
3 ПРИНЯТ на Научно-техническом Совете ЦНИИПСК им. Мельникова от 26 января 2006 г. с участием представителей организации-разработчика стандарта
4 ВВЕДЕН впервые
5 Разработка, согласование, утверждение, издание (тиражирование), обновление (изменение или пересмотр) и отмена настоящего стандарта производятся организациями-разработчиками
Настоящий стандарт разработан в соответствии с Федеральным законом «О техническом регулировании» № 184-ФЗ и предназначен для применения всеми подразделениями ЗАО «ЦНИИПСК им. Мельникова» и ОАО НИПИ «Промстальконструкция», специализирующимися на разработке проектов КМ и КМД, диагностике, ремонте и реконструкции промышленных зданий и сооружений различного назначения.
Стандарт может применяться другими организациями, если эти организации имеют сертификаты соответствия, выданные Органами по сертификации в системе добровольной сертификации, созданными организациями-разработчиками стандарта.
Организации-разработчики не несут никакой ответственности за использование данного стандарта организациями, не имеющими сертификатов соответствия.
Необходимость разработки стандарта продиктована тем, что опыт, накопленный организациями-разработчиками стандарта, а также отечественными предприятиями и организациями в области проектирования, изготовления и выполнения стальных конструкций с монтажными соединениями на болтах, содержится в различных нормативных документах, рекомендациях, ведомственных правилах и других, частично устаревших и не охватывающих в целом проблему безопасной эксплуатации промышленных зданий и сооружений различного назначения.
Основной целью разработки стандарта является создание современной нормативной базы по вопросам изготовления и монтажа стальных конструкций с соединениями на болтах.
Замечания и предложения по дополнению и изменению настоящего стандарта просим направлять по адресам:
117393 Москва, ул. Архитектора Власова, 49, ЗАО «ЦНИИПСК им. Мельникова», факс 960-22-77, телефоны для справок: 128-77-77, 120-10-21;
127473 Москва, ул. Садовая Самотечная, 13, ОАО НИПИ «Промстальконструкция», телефоны (факс) для справок 200-17-02, 684-32-65.
Конструкции стальные строительные |
болтовые соединения |
Изготовление и монтаж |
Утвержден и введен в действие:
Приказом ЗАО «ЦНИИПСК им. Мельникова» от 26 января 2006 г. № 20
Приказом ОАО НИПИ «Промстальконструкция» от 26 января 2006 г. №5
Дата введения - 2006-03-01
Настоящий стандарт распространяется на изготовление и монтаж несущих и ограждающих стальных строительных конструкций с монтажными соединениями на болтах, в том числе высокопрочных, предназначенных для стационарных, сборно-разборных и передвижных зданий и сооружений различного назначения, воспринимающих постоянные, временные и особые нагрузки типа подвижных, вибрационных, взрывных, сейсмических в климатических районах с расчетной температурой до -65°С и сейсмичностью до 9 баллов, эксплуатируемых как в слабоагрессивных, так и в среднеагрессивных и агрессивных средах с применением защитных металлических и лакокрасочных покрытий.
В настоящем стандарте использованы ссылки на следующие нормативные документы:
Федеральный закон «О техническом регулировании» от 27 декабря 2002 г. № 184-ФЗ
СТО 0031-2004 Стандарт организации. Конструкции стальные строительные. Болтовые соединения. Сортамент и области применения
СТО 0041-2004 Стандарт организации. Конструкции стальные строительные. Болтовые соединения. Проектирование и расчет
СП 53-101-98 Изготовление и контроль качества стальных строительных конструкций
СНиП 2.09.03-85 Сооружения промышленных предприятий
СНиП 3.03.01-87 Несущие и ограждающие конструкции
СНиП II-23-81* Стальные конструкции. Нормы проектирования
ГОСТ 8.541-86 ГСИ. Государственный первичный эталон и государственная поверочная схема для средств измерений крутящего момента силы
ГОСТ 1759.4-87 Болты, винты и шпильки. Механические свойства и методы испытаний
ГОСТ 18107-72 Калибры для метрической резьбы. Допуски
ГОСТ 20799-88 Масла индустриальные. Технические условия
ГОСТ 22353-77 Болты высокопрочные класса точности В. Конструкция и размеры
ГОСТ 23118 Конструкции стальные строительные. Общие технические условия
ГОСТ 23683-89 Парафины нефтяные твердые. Технические условия
ГОСТ 24379.0-80 Болты фундаментные. Общие технические условия
ГОСТ 24379.1-80 Болты фундаментные. Конструкция и размеры
ГОСТ 25726-83 Клейма ручные буквенные и цифровые. Типы и основные размеры
ГОСТ Р 51254-99 Ключи моментные. Общие технические условия
Рекомендации по применению высокопрочных болтов, покрытых составом на основе парафина, в монтажных соединениях стальных конструкций, Москва, 1989 г.
Рекомендации по расчету, проектированию, изготовлению и монтажу фланцевых соединений стальных строительных конструкций, Москва, 1989 г.
3.1 Изготовление и монтаж стальных строительных конструкций с соединениями на болтах осуществляют предприятия и организации, имеющие государственные лицензии РФ, дающие право на изготовление и монтаж конструкций соответствующих групп согласно классификации, принятой в СТО 0031-2004.
3.2 Стандарт распространяется на изготовление и монтаж конструкций с соединениями на болтах следующих видов:
- фрикционных, в которых сдвигающие усилия воспринимаются силами трения, действующими на контактных поверхностях соединяемых элементов в результате натяжения болтов на расчетное усилие;
- срезных, в которых сдвигающие усилия воспринимаются сопротивлением болтов срезу, а соединяемых элементов - смятию;
- фрикционно-срезных, в которых учитывается вся совокупность сопротивлений - болтов срезу, соединяемых элементов смятию и трению;
- фланцевых, в которых предварительно затянутые болты работают на растяжение при жестких фланцах или на растяжение с изгибом при гибких фланцах;
- болтозаклепочных, применяемых при ремонте клепаных конструкций, в которых снижение несущей способности компенсируется силами трения после замены дефектных заклепок болтами, затянутыми на расчетное усилие.
3.3 Стальные конструкции должны изготавливаться и монтироваться в соответствии с рабочей документацией КМ (конструкции металлические) и КМД (конструкции металлические деталировочные). Проектирование и расчет соединений на болтах должны производиться в соответствии с требованиями СТО 0041-2004.
3.4 На чертежах КМ должны быть указаны:
- виды соединений;
- номинальные диаметры отверстий и болтов;
- стандарты на болты, гайки и шайбы;
- классы прочности болтов и гаек;
- осевые усилия натяжения болтов;
- способ натяжения болтов - по моменту закручивания;
- способ подготовки контактных поверхностей с указанием расчетной величины коэффициента трения;
- детали и зоны, не подлежащие огрунтовке или окраске на заводе-изготовителе металлоконструкций;
- дополнительные требования к изготовлению и монтажу металлоконструкций;
- нормативные документы по изготовлению конструкций и технологии выполнения соединений на болтах.
3.5 При разработке чертежей КМД следует учитывать технологические возможности предприятия-изготовителя и особенности выполнения монтажных работ.
3.6 Организация, разработавшая чертежи КМД, несет ответственность за их соответствие проектным решениям, принятым в чертежах КМ, за надежность не расчетных соединений и узлов. Отступления от чертежей КМ должны быть согласованы с разработчиком проекта.
3.7 Изготовление конструкций должно производиться в соответствии с требованиями рабочих чертежей КМ и КМД, ГОСТ 23118, СП 53-101-98, технологических карт предприятия-изготовителя; монтаж в соответствии с проектом производства работ, СНиП 3.03.01 и настоящим стандартом.
3.8 В процессе изготовления и монтажа конструкций должен быть обеспечен контроль за выполнением требований настоящего стандарта с занесением результатов контроля в заводскую приемо-сдаточную документацию, а также в исполнительную документацию на монтажные работы.
3.9 Контроль качества изготовления конструкций осуществляет ОТК предприятия-изготовителя, монтажа - линейный инженерно-технический персонал.
4.1 Материалы
4.1.1 В зависимости от степени ответственности отдельных групп конструкций зданий и сооружений, а также от условий их эксплуатации и климатического района строительства, для элементов конструкций с соединениями на болтах следует применять листовой и фасонный стальной прокат по табл. 50 и 51 СНиП II-23-81* (издание 2000 года).
4.1.2 Для фланцев, подверженных растяжению, изгибу или их совместному действию, следует применять листовую сталь с гарантированными механическими свойствами в направлении толщины проката (см. пп. 8.4-8.6 СТО 0041-2004).
4.1.3 Применяемая технология сварки и сварочные материалы должны обеспечивать значения временного сопротивления металла сварных швов не ниже нормативных значений временного сопротивления основного металла.
4.1.4 Предприятие-изготовитель стальных конструкций осуществляет комплектацию крепежными изделиями в соответствии с требованиями СТО 0031-2004. Фундаментальные болты должны соответствовать ГОСТ 24379.0-80 и ГОСТ 24379.1-80.
4.2 Требования к изготовлению
4.2.1 Прокат перед запуском в производство должен быть проверен на соответствие сопроводительной документации, отсутствие недопустимых прогибов, местных вмятин, трещин, расслоений, отклонений от геометрических размеров.
4.2.2 Резка заготовок фасонного и листового проката допускается как механическим, так и термическим способом. При этом кромки элементов конструкций, работающих на растяжение, а также выполненных из стали с нормативным пределом текучести свыше 350 МПа, должны быть подвергнуты механической обработке на глубину не менее 20% от толщины элемента.
4.2.3 Все отверстия для болтовых монтажных соединений должны быть образованы на проектный диаметр на предприятии-изготовителе стальных конструкций за исключением оговоренных в проектной документации.
4.2.4 Образование отверстий следует производить сверлением на поточных линиях, станках с числовым программным управлением (ЧПУ), по кондукторам, а в случае отсутствия оборудования - по шаблонам с обеспечением точности в соответствии с заданной в проекте КМ или настоящем стандарте. Для не расчетных конструктивных болтовых соединений допускается образование отверстий по намётке.
4.2.5 В не расчетных соединениях допускается образование отверстий продавливанием для сталей с нормативным пределом текучести до 350 Мпа при соотношении толщины металла t и диаметра отверстия d0 не более 0,7 при t ≤ 20 мм.
4.2.6 В расчетных соединениях допускается продавливание отверстий на меньший диаметр, но не более 0,75 d0, при толщине металла не более чем 0,8 d0 с последующим рассверливанием на проектный диаметр d0.
4.2.7 Предельное отклонение диаметра отверстий не должно превышать +0,6 мм для отверстий диаметром до 28 мм и +0,9 мм свыше 28 мм.
4.2.8 Предельные отклонения центров отверстий устанавливаются проектной документацией, исходя из условия собираемости конструкций на монтаже.
4.2.9 При отсутствии указаний в проектной документации, предельные отклонения размеров между центрами отверстий в группе назначают равными ± 1,0 мм, в том числе по диагонали, между группами ± 0,5 мм на каждый метр расстояния между ними.
4.2.10 Предельное отклонение размеров соединяемых элементов l должно составлять не более ± 3,0 мм при l ≤ 6 м и ± 0,5 мм на каждый метр длины при l > 6 м.
4.2.11 Толщины накладок не должны превышать:
- для болтов М12 - 12 мм;
- для болтов М16 - 16 мм;
- для болтов М20 - 20 мм;
- для болтов М24 - 25 мм;
- для болтов М27 - 30 мм.
При необходимости применения накладок большей толщины следует применять двухслойные накладки или болты большего диаметра.
4.2.12 Не рекомендуется применение соединений, в которых суммарная толщина элементов превышает:
- для болтов М12 - 40 мм;
- для болтов М16 - 50 мм;
- для болтов М20 - 60 мм;
- для болтов М24 - 100 мм;
- для болтов М27 - 140 мм.
4.2.13 Для фланцевых соединений следует, как правило, применять следующие сочетания диаметров болтов и толщин фланцев:
- М20 - 20 мм;
- М24 - 25 мм;
- М27 - 30 мм.
4.2.14 Сборку элементов конструкций с фланцевыми соединениями следует выполнять в кондукторах. Базовые поверхности кондукторов и внешние поверхности фланцев после сварки должны быть подвергнуты фрезерованию. Тангенс угла отклонения поверхности фланца не должен превышать величину 0,0007 в каждой из двух плоскостей.
4.2.15 Отправочные марки конструкций должны быть огрунтованы или окрашены (по соглашению с заказчиком) за исключением контактных поверхностей фрикционных и фрикционно-срезных соединений, а также контактных поверхностей фланцев в случае, если это оговорено проектной документацией.
4.3 Контрольная сборка
4.3.1 Контрольная сборка конструкций с соединениями на болтах должна выполняться на предприятии-изготовителе в случае, если это оговорено в проектной документации.
4.3.2 Контрольная сборка конструкций осуществляется в соответствии с требованиями проектной и технологической документации. Несовпадение отверстий (чернота) проверяется калибром диаметром на 0,5 мм больше номинального диаметра болта. Калибр должен проходить в 100 % отверстий каждого соединения.
4.3.3 Зазоры между соединяемыми элементами контролируются щупом толщиной 0,3 мм, между фланцами - щупом толщиной 0,1 мм. Щуп не должен проникать в зону, ограниченную радиусом 1,3 d0 от оси болта после затяжки всех болтов соединения на проектное усилие.
5.1 Требования к монтажной сборке соединений
5.1.1 Работы по возведению зданий и сооружений с соединениями на болтах следует производить в соответствии с утвержденным проектом производства работ (ППР), рабочей документацией и СНиП 3.03.01-87.
5.1.2 Данные о производстве монтажных работ следует ежедневно вносить в журналы работ по монтажу и выполнению соединений на болтах с контролируемым натяжением (приложение А).
5.1.3 Применяемые конструкции должны соответствовать требованиям рабочих чертежей, а метизы - стандартам или техническим условиям, указанным в СТО 0031. Каждая партия болтов, гаек и шайб должна быть снабжена сертификатом качества с указанием результатов механических испытаний.
5.1.4 В случае сомнений относительно качества поставленных крепежных изделий проводится входной контроль геометрических размеров или механических свойств, предусматривающий испытание болтов на твердость и разрыв с определением фактических значений временного сопротивления, гаек на испытательную нагрузку и твердость, шайб на твердость и неплоскостность. Качество резьбы болтов и гаек контролируется резьбовыми калибрами по ГОСТ 18107.
5.1.5 Крепежные изделия следует хранить в защищенном от атмосферных осадков месте, рассортированными по классам прочности, диаметрам и длинам, а высокопрочные болты и гайки - дополнительно по партиям.
5.1.6 При сборке монтажных элементов должны обеспечиваться устойчивость и неизменяемость их положения в пространстве на всех стадиях монтажа.
5.1.7 Выполнение соединений на болтах с контролируемым натяжением (фрикционные, фрикционно-срезные и фланцевые соединения) и их приемку следует производить под руководством лица, назначенного ответственным за выполнение этого вида соединений приказом по организации, производящей эти работы. К выполнению соединений допускается персонал, прошедший соответствующую подготовку и имеющий удостоверение о допуске к указанным работам. Рекомендуемая программа обучения и форма удостоверения приведены в приложении Б.
5.1.8 Технологический процесс выполнения соединений предусматривает следующие операции:
- подготовку болтов, гаек и шайб;
- подготовку контактных поверхностей элементов и деталей;
- сборку соединений;
- натяжение болтов на проектное усилие;
- контроль качества выполнения соединений;
- герметизацию соединений и огрунтовку стыков;
- установку клейма бригадира и ответственного лица;
- занесение результатов выполнения и контроля качества соединений в «Журнал выполнения монтажных соединений на болтах с контролируемым натяжением» (приложение А).
5.2 Подготовка болтов, гаек и шайб
5.2.1 Технологический процесс подготовки болтов, гаек и шайб, предназначенных для соединений с контролируемым натяжением болтов, включает расконсервацию, очистку от грязи и ржавчины, прогонку резьбы отбракованных болтов и гаек и нанесение смазки.
5.2.2 Расконсервацию болтов, гаек и шайб и нанесение смазки на болты и гайки следует производить кипячением в воде (10÷15 мин) с последующей промывкой в горячем состоянии в смеси, состоящей из 70÷75 % неэтилированного бензина и 30÷25 % минерального масла по ГОСТ 20799. Применяемое соотношение бензина и масла должно обеспечивать на поверхности болтов и гаек тонкий слой смазки.
5.2.3 При больших объемах работ применяется пост подготовки метизов, снабженный грузоподъемным оборудованием (рисунок 1).
5.2.4 Подготовленные метизы следует хранить в закрытых ящиках без доступа атмосферных осадков не более 10 дней, так как при более длительном хранении смазка испаряется, увеличивается трение в резьбе, снижается усилие натяжения болтов.
1 - ванна промывочная; 2 - подъемное устройство; 3 - ванна для кипячения;
4 - контейнеры; 5 - поддон; 6 - подставка
Рисунок 1 - Пост подготовки метизов
5.2.5 Для прогонки резьбы отбракованных болтов и гаек рекомендуется применять соответствующим образом оборудованные пневматические или электрические гайковерты, а также метчики и плашки соответствующего диаметра.
5.2.6 В случае превышения срока хранения, а также после прогонки резьбы, метизы должны быть обработаны повторно.
5.2.7 Ориентировочный расход бензина на 100 кг метизов составляет 2,2 л, масла - 0,8 л.
5.2.8 В качестве смазки резьбы допускается применение твердых сортов парафина по ГОСТ 23683. Очистка болтов, гаек и шайб от заводской консервирующей смазки в данном случае осуществляется кипячением в воде с добавлением моющего средства. Парафин может наноситься на весь комплект (болт, гайка и две шайбы) или только на гайки, предварительно нагретые до температуры не ниже +80°С Расход парафина составляет 3÷4 г на 1 кг крепежных изделий. Подробная технология приведена в «Рекомендации по применению высокопрочных болтов, покрытых составом на основе парафина, в монтажных соединениях стальных конструкций», Москва, 1989 г.
5.2.9 Подготовка метизов с металлическими покрытиями допускается смазкой резьбы гаек посредством их окунания в емкость с минеральным маслом по ГОСТ 20799 не позже чем за 8 часов перед сборкой соединений, с последующим определением величины коэффициента закручивания (Кз) с помощью динамометрических контрольных приборов. Установка болтов с нарушенным покрытием, со следами ржавчины или при Кз > 0,2 не допускается.
5.3 Подготовка контактных поверхностей
5.3.1 Способ обработки контактных поверхностей фрикционных, фрикционно-срезных и фланцевых соединений указывается в чертежах КМ или КМД.
5.3.2 Рекомендуемые способы обработки и расчетные значения коэффициентов трения приведены в СТО 0041-2004.
5.3.3 Контактные поверхности элементов соединений на болтах без контролируемого натяжения должны быть очищены от загрязнений металлическими щетками.
5.3.4 Обработанные поверхности следует предохранять от попадания на них грязи, масла и краски, а также от образования льда. Грязь удаляется металлическими щетками, масло - растворителями, краска и лед - нагревом.
5.3.5 В случае превышения срока с момента подготовки контактных поверхностей до сборки соединения более 3-х суток, следует производить повторную обработку способом, применявшимся при первичной обработке.
5.3.6 Требования повторной обработки не распространяются на налет ржавчины, образующийся на контактных поверхностях после их очистки, а также в случае попадания на них атмосферных осадков в виде влаги или конденсации водяных паров.
5.3.7 Допускается повторная огневая обработка взамен пневматической, при этом в качестве горючего газа может быть использован пропан.
5.4 Сборка соединений
5.4.1 Технологический процесс сборки соединений предусматривает:
- осмотр конструкций и проверку соответствия геометрических размеров собираемых элементов требованиям рабочих чертежей;
- совмещение отверстий и фиксацию в проектном положении элементов и деталей соединения с помощью монтажных оправок;
- постановку болтов в свободные от оправок отверстия;
- натяжение поставленных болтов на усилие, предусмотренное в проекте;
- извлечение оправок, постановку в освободившиеся отверстия болтов и натяжение их на расчетное усилие.
Не допускается установка болтов в отверстия, образованные ручной газовой резкой или сваркой.
5.4.2 Перепад толщин перекрываемых накладками элементов, определяемый до постановки накладок с помощью линейки и щупа, не должен превышать 0,5 мм.
5.4.3 При перепаде плоскостей соединяемых элементов от 0,5 до 3,0 мм, для обеспечения плавного изгиба накладки, кромку выступающего элемента следует удалить наждачным камнем на расстоянии не менее 30 мм от края. При перепаде более 3,0 мм следует применять прокладки. Применение прокладок должно быть согласовано с разработчиком проекта,
5.4.4 Чернота (несовпадение отверстий в отдельных деталях собранного пакета) не должна превышать разности номинальных диаметров отверстий и болтов и не препятствовать свободной, без перекоса, постановке болтов в отверстия.
5.4.5 В собранном пакете болты заданного в проекте диаметра должны проходить в 100 % отверстий. Допускается прочистка 20 % отверстий сверлом или коническим райбером, диаметр которого на 1,0 мм превышает номинальный диаметр болта.
5.4.6 Запрещается применение в расчетных соединениях болтов, не имеющих клейма предприятия-изготовителя и маркировки, обозначающей класс прочности.
5.4.7 Каждый болт устанавливается в соединение с двумя круглыми шайбами (одна ставится под головку болта, другая - под гайку). Высокопрочные болты с увеличенным размером головки под ключ, при разности номинальных диаметров отверстий и болтов до 4 мм, допускается устанавливать с одной шайбой под вращаемым элементом (гайкой или головкой болта).
5.4.8 В срезных соединениях допускается установка под гайкой двух шайб.
5.4.9 В момент установки болтов гайки должны свободно, от руки, навинчиваться по резьбе, в противном случае гайку или болт следует заменить, а отбракованные болты и гайки отправить на прогонку резьбы и повторную подготовку.
5.4.10 При расчете соединений на действие монтажных нагрузок работу оправок и болтов допускается учитывать совместно. Количество оправок и болтов на каждой стадии устройства соединений должно приниматься по расчету на действие монтажных нагрузок.
5.4.11 Количество оправок по условию совмещения отверстий должно составлять 10 % от количества отверстий в соединении, но не менее 2-х штук, а количество стяжных болтов -15÷20 %.
5.4.12 Освобождение оправок допускается после установки во все свободные отверстия болтов и натяжения их на усилие не менее 30 % от проектного. Освобождение оправок ведут поочередно с постановкой заменяющих их болтов.
5.4.13 Места и стадии установки оправок указываются в проекте производства работ, а последовательность натяжения болтов - в соответствии с п. 5.5.2.
5.4.14 Длины болтов фрикционных и фланцевых соединений назначают в зависимости от суммарной толщины собираемого пакета в соответствии с таблицей 1. При этом выступающая над гайкой резьба должна иметь не менее одного, а под гайкой оставаться не менее двух витков с полным профилем.
5.4.15 Длины болтов фрикционно-срезных и срезных соединений подбирают таким образом, чтобы резьба не попадала в плоскости среза и отстояла от ближайшей из них на расстоянии не менее 5 мм или не менее половины толщины элемента, прилегающего к гайке.
5.4.16 Натяжение болтов на проектное усилие производят после выверки в пространстве и проверки геометрических размеров собираемых конструкций.
Таблица 1
Длина болта, мм |
Толщина пакета, при условии установки двух шайб, для болтов диаметром, мм |
|||||||||
12 |
16 |
20 |
22 |
24 |
27 |
30 |
36 |
42 |
48 |
|
30 |
0÷10 |
- |
- |
- |
- |
- |
- |
- |
- |
- |
40 |
13÷20 |
0÷16 |
0÷12 |
- |
- |
- |
- |
- |
- |
- |
50 |
23÷30 |
16÷26 |
8÷22 |
0÷18 |
0÷14 |
0÷11 |
- |
- |
- |
- |
60 |
33÷40 |
26÷36 |
18÷32 |
15÷28 |
11÷24 |
6÷21 |
0÷18 |
- |
- |
- |
aquagroup.ru
Монтажные соединения на высокопрочных болтах с контролируемым натяжением ~ Как бывает в монтаже!!
К монтажным соединениям на высокопрочных болтах с контролируемым натяжением относятся: фрикционные или сдвигоустойчивые соединения, в которых внешние усилия воспринимаются за счет сопротивления сил трения, возникающих по контактным плоскостям соединяемых элементов от предварительного натяжения болтов; фрикционно-срезные соединения, в которых внешние усилия воспринимаются, главным образом, за счет преодоления сопротивления сжатию фланцев от предварительного натяжения высокопрочных болтов. 1 Фрикционные и фрикционно-срезные соединения1.2. Во фрикционных и фрикционно-срезных соединениях соприкасающиеся поверхности деталей должны быть обработаны способом, предусмотренным в проекте. С поверхностей, подлежащих обработке, необходимо предварительно удалить масляные загрязнения.
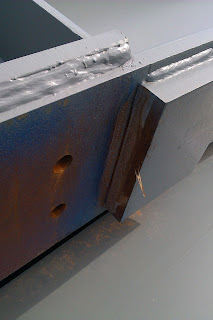
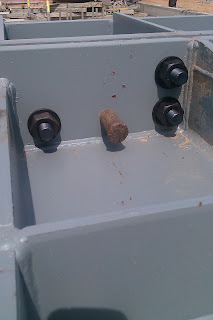
Допускается прочистка отверстий плотно стянутых пакетов сверлом, диаметр которого равен номинальному диаметру отверстия, при условии, что чернота не превышает разницы номинальных диаметров отверстия и болта.
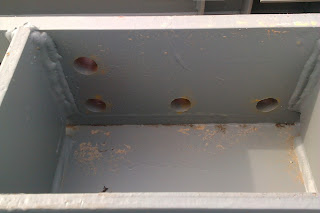
montagni.blogspot.com