ВТОРИЧНОЕ ИСПОЛЬЗОВАНИЕ ПЕНОПОЛИСТИРОЛА ВОЗМОжНО. Использование отходов пенопласта для изготовления пеноблоков
ВТОРИЧНОЕ ИСПОЛЬЗОВАНИЕ ПЕНОПОЛИСТИРОЛА ВОЗМОжНО
Переработка изношенных автомобильных покрышек в России
В некоторых источниках информации освещаются попытки вторичного использования пенополистирола в виде гранул, которые получают после дробления упаковки, однако такое применение весьма ограничено.
Вместе с тем пенополистирол может быть экономически эффективно использован для получения связующих и клеев широкого назначения, в том числе для приготовления формовочных и стержневых песчаных смесей, покрытий литейных форм для производства отливок из чёрных и цветных сплавов. Важно, что эти связующие могут от - верждаться при комнатной температуре, а также при подсушке температурой не выше 180-200° С. Это показали нижеописанные разработки Физико - технологического института металлов и сплавов НАН Украины (г. Киев), в результате которых созданы указанные связующие - растворы полистирола (изначально пенополистирола) в органическом растворителе. Исследования состояли в обоснованном выборе растворителя, оптимизации составов, эксплуатационных свойств связующих и песчаных смесей.
Известно, что пенополистирол легко растворяется во многих растворителях, в частности, в бензоле, толуоле, ксилоле, сольвенте, однако они имеют очень низкий предел допустимых концентраций (ПДК, мг/м3) в атмосфере рабочих помещений (цехов, участков), что резко ухудшает условия труда при их использовании. Так, ПДК бензола всего 5 мг/м3, толуола, ксилола, сольвента - по 50 мг/м3. Высокая летучесть этих растворителей также усложняет их применение в производстве.
Имеется другая группа растворителей с более высоким ПДК, который достигает 100-200 мг/м3. Это ацетон, этилацетат, бутилацетат, метилэтилкетон, тетралин и др. Однако у них, за исключением дорогого и дефицитного тетралина, очень высокая летучесть. Так, летучесть ацетона по серному эфиру равняется всего 2,1, летучесть этилацетата - 2,9. Применение этих растворителей для приготовления раство - ров пенополистирола с целью их использования в открытой атмосфере рабочих помещений, с точки зрения ухудшения условий труда, является весьма проблематичным и на практике не применяется. Очевидно, что для получения растворов из отходов пенополистирола, в том числе связующих песчаных формовочных и стержневых смесей для литейного производства, необходимы растворители с более высоким ПДК и низкой летучестью как обязательное условие создания малотоксичных смесей.
Поставленная задача решена нами установлением того факта, что растворителем отходов пенополистирола может быть живичный скипидар, на что и получен Институтом Патент Украины. Живичный скипидар - это углеводород растительного происхождения (ГОСТ 1571-82). Его получают из живицы (из надрезов коры сосны), которую перегоняют с паром и разделяют на летучую фракцию - скипидар и нелетучий осадок - канифоль. Скипидар содержит в основном бицикличный монотерпеноид пинен. Живичный скипидар представляет собой прозрачную бесцветную или чуть окрашенную жидкость с плотностью 0,855 - 0,863 г/см3. До появления уайт-спирита скипидар был основным растворителем лаков и красок, его также применяют в фармакологии, так как он обладает бактерицидными свойствами. Ежегодный объём производства живичного скипидара в мире составляет около 300 000 т.
Живичный скипидар имеет ПДК, равное 300 мг/м3, то есть значительно выше упомянутой группы растворителей с ПДК не более 200 мг/м3. Он хорошо растворяет отходы пенополистирола и имеет низкую летучесть. Если принять скорость испарения живичного скипидара за единицу, то ацетон испаряется в 15,1 раза быстрее, бензин «Калоша» в 9,87 раз, этилацетат в 7,66 раз, уайт-спирит в 2,28 раз.
Исследуя растворяющую способность живичного скипидара по отношению к отходам пенополистирола, в нашем институте разработали технологию получения растворов из отходов пенополисти - рола в живичном скипидаре практически любой концентрации вплоть до 50%. В лаборатории получены растворы с концентрацией 25%, 30%, 40% и 50%.
Приготовление растворов пенопо - листирола в органических растворителях сопровождается многократным уменьшением его исходного объёма и увеличением объёма раствора по сравнению с объёмом растворителя. Приготовление растворов пенополистирола является удобным способом его компактирования, эти отходы занимают вследствие низкой плотности (около 25 кг/м3) значительный объём в окружающей среде. По нашей технологии для увеличения объёма раствора на одну единицу требуется растворить многие десятки единиц объёмов пенополистирола.
Разработанная технология рециклин - га пенополистирола из его отходов позволяет перевести его в раствор, а затем, например, изготавливать современные малотоксичные связующие материалы для производства песчаных формовочных и стержневых смесей, а также покрытий литейных форм, что даёт возможность совершенствовать и разрабатывать новые более эффективные и экономичные процессы литья металлов. Кроме того, использование отходов пенополистиро - ла имеет важное экологическое значение, так как речь идёт об уменьшении содержания этих отходов в окружающей человека среде обитания.
Наиболее технологичны составы песчаных литейных смесей на 40- процентном растворе, содержащие 2% полистирола в сухом остатке. Эти смеси прекрасно формуются и отверждаются кратковременной сушкой при температуре до 200° С. Институтом в настоящее время патентуется состав смеси, отверждаемой при комнатной температуре.
В процессе развития технологии ре - циклинга отходов пенополистирола путём получения его растворов в живичном скипидаре и последующем использовании в качестве связующего в литейном производстве была предложена технологическая схема опытно-промышленного процесса с перечнем несложного оборудования, включающего реактор в виде герметично закрываемого сосуда, снабжённого мешалкой для ускоренного растворения пенополистирола и получения однородного по концентрации раствора.
Как показали экспериментальные работы, в растворах пенополистирола в живичном скипидаре, независимо от концентрации раствора, наблюдается седиментация мелких загрязнений, занесённых с отходами пенополистирола. После приготовления раствора заданной концентрации выполняли операцию отстаивания для осаждения этих загрязнений и их последующего удаления. При промышленном рециклинге это может служить удобным способом очистки по- листирольного раствора.
Полученные данные исследования степени уменьшения насыпного объёма отходов пенополистирола при растворении в живичном скипидаре показывают весьма замечательные возможности его компактирования. В 1 единице объёма 40-процентного раствора помещается 19- 20 объёмных единиц отходов пено- полистирола, а по отношению к исходному объёму растворителя - живичного скипидара - этот объём отходов больше в 29- 30 раз.
Физико-механические свойства формовочных стержневых смесей на основе полистирольных связующих превосходят (или равны) аналогичные характеристики холодно-твердеющих смесей на основе жидкого стекла, феноло-формаль - дегидных, карбомидо-фурановых смол. Это обстоятельство позволило рекомендовать полистирольные связующие с жи - вичным скипидаром для замены вышеупомянутых связующих и, в особенности, дорогостоящих смол (со стоимостью на порядок выше раствора полистирола) в производственном процессе литья заготовок из чёрных и цветных сплавов.
В Физико-технологическом институте металлов и сплавов, кроме создания новых связующих песчаных смесей, ведётся поиск партнёров для участия в программах разработки технологии получения из растворённого полистирола твёрдых пластмасс и изделий, а также его использования в качестве сырья для производства недорогих высокопрочных кле - ев и лаков, строительных и теплоизолирующих пен. Водоотталкивающие свойства полученных растворов имеют перспективу применения для гидроизоляционной защиты, дренажной гидроизоляции и защиты от атмосферного воздействия деревянных и фасадных поверхностей зданий и сооружений. Бактерицидные свойства полученного из древесины хвойных пород живичного скипидара вместе с клеевыми свойствами описанного раствора можно использовать для производства клейкой ленты, герметика, а также на предприятиях по производству продуктов и медикаментов.
Рис. 1 - Стержни, изготовленные из смеси с полистирольным связующим |
.
02.06.09 Единый экологический фонд предложила создать Бурятии Иркутская область с тем, чтобы средства этого фонда направлялись на решение острых экологических проблем и решение природоохранных вопросов. Планируется, что в фонд будут …
На сегодняшний день нет никаких чётких законодательных правил обращения с отходами, которые можно переработать с помощью современных технологий. Единственным инструментом сдачи отходов на переработку является добровольное желание природопользователей применить нулевой …
С 30 июня 2009 г. вступают в законную силу изменения, трактованные в № 309-ФЗ «О внесении изменений в статью 16 федерального закона «Об охране окружающей среды» и отдельные законодательные акты …
msd.com.ua
Использование отходов газобетона. Производство газоблоков, пеноблоков
В процессе производства ячеистых и легких бетонов возникает необходимость решения проблемы, связанной с утилизацией отходов, образующихся при торцевании массива и срезании «горбушки». При высокой производительности предприятия актуальность данного вопроса безусловна.Зачастую предприятия решают эту проблему самым простым способом – отправляют отходы в отвал, забывая, что это нерационально. На сегодняшний день существуют технические решения, которые позволяют использовать отходы в качестве вторичного сырья для производства и при этом получать дополнительную прибыль.
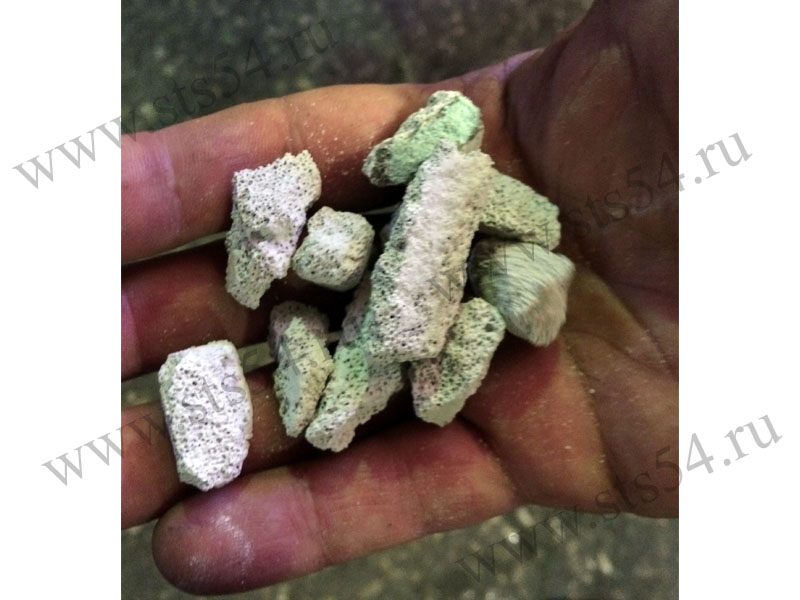
Применение отходов производства газобетона
В основе реализации технических решений, направленных на использование отходов в качестве вторичного сырья лежит процесс измельчения этих отходов до фракции требуемой величины. При дроблении отходов с помощью шаровых или щековых дробилок возможно получить материал с размером частиц от 0.1 до 1,0 мм. Такой материал можно эффективно использовать в качестве минерального заполнителя при производстве газобетона. Данный вариант решает проблему утилизации отходов и позволяет снизить расход цемента и кремнеземистого компонента (песок, зола-уноса) при производстве газобетона. В итоге, достигается снижение себестоимости готовой продукции при сохранении качественных характеристик газобетона.
www.sts54.ru
Сырье для пенопласта: переработка, дробилка, утилизация отходов
Содержание статьи
Среди многообразия полимеров мы чаще всего сталкиваемся с пенопластом беспрессовым полистирольным. Обычным стало использование сырья для пенопласта в качестве упаковочного при перевозке различных приборов, техники, электроники, посуды и даже мебели. В некоторых случаях он используется как хороший материал для осуществления теплоизоляции.
Среди множества положительных качеств и свойств существует и качество отрицательное. Оно очень важно, ведь имеет отношение к защите окружающей среды. Дело в том, что он практически не разлагается в естественной среде и становится причиной ее загрязнения. Пенополистирол не причинит вреда растениям, а вот животные могут получить отравление, если будут этот материал жевать и глотать.
Зачем перерабатывать
Ответ на это вопрос прост. Накопившийся за годы материал, который служил когда-то упаковкой, лотками, декоративными украшениями некуда девать. Сжигать как ненужные деревянные изделия его нельзя. Это связано с выделением большого количества токсичных газов. Выбрасывать некуда, сдавать на утилизацию пенопласт тоже некуда.
Единственно верным способом избавиться от подобного мусора является переработка пенопласта дома. Для того чтобы правильно и результативно выполнить все работы необходимо:
- Определить цель, с которой проводится переработка.
- Выбрать место, где будет удобно осуществлять переработку. Данный материал не просто летает, он еще и прекрасно электризуется. Поэтому возможно потребуется специальное помещение, в котором можно будет заниматься переработкой.
- Выбрать способ воздействия на имеющиеся в наличии отходы пенопласта.
Конечно, в первую очередь стоит подумать о том, что этот материал может пригодиться в качестве упаковочного материала, но с его хранением связаны определенные трудности. В таком случае его измельчают, но для этого нужна дробилка пенопласта, а вот что делать дальше? Тут каждый принимает решение самостоятельно.
Способы переработки и использования:
- Дробилка пенопласта. Измельчить его можно с помощью специальной дробилки, но при ее отсутствии это делают вручную. Важно продумать ход процесса, ведь маленькие частички пенополистирола имеют слишком малый вес и легко разлетаются в разные стороны. Поэтому, измельчая пенополистирол вручную, его помещают в мешок или иную емкость.
- Сырье, подлежащее утилизации, занимает достаточно много места и пространства. Одна из важнейших задач – уменьшить его размеры. С этой целью используют концентрат цедры цитрусовых (его второе название «лимоне»). Под воздействием этого вещества пенополистирол становится не только меньше, он превращается в жидкое вещество.
- Переплавить можно только путем нагрева.
Использовать измельченное сырье можно на садовом участке или в загородном доме. Его добавляют в почву на клумбах, смешивают с грунтом на грядках для выращивания зелени. Это связано с тем, что гранулы способствуют впитыванию и сохранению влаги в земле, даже при сильной засухе не давая почве растрескиваться. И вода, и воздух легче проникают в почву, обеспечивая питание и вентиляцию корням растений. Но свойства этого материала таковы, что в этих почвах отсутствует гниение.
Переработанный пенопласт в загородном доме
Загородное строительство тоже не обходится без этого материала. Фракции разного размера используют для заполнения различных неровностей или впадин на участке, где ведется строительство. Конечно, с помощью него дорогу не выровнять, но небольшие неровности можно заполнить. Скважины, отверстия, полости удобно заполнять именно пенополистиролом. Ведь он многие годы, не меняясь, сохраняется в том месте, где был расположен. Он легко впитывает влагу и также легко ее отдает. Поэтому емкости, заполненные пенопластом, в малой степени подвержены коррозии.
В строительном бизнесе тоже нашлось применение переработанному пенополистиролу. Именно из него изготавливают облегченный кирпич, который из-за фактуры называют дырчатым. По предложению ученых появился и облегченный бетон, который по своей прочности и долговечности не уступает обычному составу.
Привлек пенополистирол и внимание дизайнеров. Если говорить о переработке в домашних условиях, то здесь мастерам предоставлен широкий простор для полета фантазии. Пенопласт хорошо и довольно быстро плавится, поэтому его используют для создания таких дизайнерских вещиц, как оригинальные цветочные горшки или кашпо. С помощью специальной формы делают мастера хэнд-мэйда прекрасные неповторимые садовые фигурки, подставки под стаканы или те же цветочные горшки.
Полезное использование
Пересаживая цветы, стоит задуматься о качестве грунта и позаботиться о качественном дренаже в цветочных горшках. И здесь на помощь придет пенопласт. Кусочки пенополистирола укладывают на дно горшка, поверх специально подобранных камней. Он будет непросто прекрасным дренажом, занимающим меньше места чем керамзит и позволяющим корням растения дышать, но и сохранит влагу, не допуская пересыхания грунта.
Декоративные детали интерьера, изготовленные своими руками в домашних условиях, не боятся времени и воздействия различных химических веществ, а вот под воздействие «лимона» или живичного скипидара пенопласт принимает форму жидкого вещества и может быть использован в качестве супер клея. Эти свойства, плюс приготовленная смесь измельченного пенопласта с частицами более твердого вещества могут стать основой для садовой мебели сделанной своими руками в домашних условиях.
Пенопласт относится к числу материалов дешевых, но очень нужных. Он легко перерабатывается, ему находится множество вариантов применения в быту, в доме, на даче. Он совершенно безвреден, а для растений даже полезен, так как хорошо сохраняет тепло. Не стоит выбрасывать пенопласт на свалки и оставлять на точках сбора мусора. Нужно вспомнить о том, что он не разлагается в окружающей среде, но это качество можно использовать с пользой для себя и своего хозяйства.
Рекомендуем к прочтению:
vtorothodi.ru
Как делают пенопласт (технология изготовления, производство пенополистирола)
Рассмотрены все этапы технологии производства пенопласта. Перечислено оборудование, необходимое для изготовления этого материала. Даны рекомендации, с которыми нужно обязательно ознакомиться перед покупкой.
Многие из нас не раз встречали пенополистирол, пробовали его на ощупь, что-то изготавливали из него, использовали его в строительстве, для обустройства дома. Однако далеко не все знают, какова технология изготовления пенопласта, каковы ее особенности.
Как ни странно, но в производстве этого материала нет ничего сверхсложного. И примечательно то, что сейчас на рынке появилось довольно много некачественного пенополистирола, который изготовлен без учета соответствующих норм и правил.
Некоторые умельцы умудряются создать небольшую производственную линию даже в обычном гараже. Да, не удивляйтесь.
И это нужно обязательно учитывать при покупке — не все Васи Пупкины строго придерживаются предписанных технологических норм. Да и какие нормы могут быть в гараже?
Итак...
Как изготавливают пенопласт
Ранее мы рассказывали, что такое пенополистирол. Помним, что этот материал состоит из многочисленных ячеек, заполненных воздухом. Значит — процесс изготовления должен включать вспенивание материала.
Так и есть: процесс вспенивания — один из важных в производстве пенополистирола.
Однако это еще не всё.
Рассмотрим:
Этапы технологии изготовления пенопласта
Обычно процесс включает в себя:
Теперь детальнее:
1. Вспенивание. В ходе выполнения этого процесса сырье помещают в специальную емкость (пенообразователь), где под действием давления (используется парогенератор) гранулы увеличиваются примерно в 20-50 раз. Операция выполняется в течение 5 минут. Когда гранулы достигают необходимого размера, оператор выключает парогенератор и выгружает вспененный материал из емкости.
2. Сушка полученных гранул. На данном этапе главная цель — удаление лишней влаги, оставшейся на гранулах. Делается это с помощью горячего воздуха — он направляется снизу вверх. При этом для лучшего просушивания гранулы встряхиваются. Этот процесс также длится недолго — около 5 минут.
3. Стабилизация (отлеживание). Гранулы помещают в бункеры, где и проходит процесс вылеживания. Продолжительность процесса — 4...12 часов (зависит от температуры окружающего воздуха, величины гранул).
Важное примечание: технология изготовления пенополистирола может исключать 2-й этап (сушку). В таком случае стабилизация (отлеживание) будет длиться дольше — до 24 часов.
4. Выпекание. Этот этап производства пенопласта часто называют формованием. Суть заключается в том, чтобы соединить между собой полученные ранее гранулы. Для этого они помещаются в специальную форму, после чего под давлением и под действием высокой температуры водяного пара проходит процесс спекания гранул. Длится примерно 10 минут.
5. Созревание (вылеживание). Цель — избавить полученные листы пенополистирола от лишней влаги, а также от оставшихся внутренних напряжений. Для этого листы располагают в свободном месте производственного цеха на несколько суток. В ряде случаев созревание может проходить до 30 суток.
6. Резка. Изготовленные блоки пенопласта кладут на спецстанок, на котором блоки разрезаются на листы соответствующей толщины, длины, ширины. Этот производственный процесс выполняется с помощью нихромовых струн, нагретых до определенной температуры. Соответственно, проводят как горизонтальную, так и вертикальную резку блоков.
Вот так делают пенопласт.
Разумеется, после перечисленных 6-ти этапов может выполняться 7-й этап — переработка оставшихся обрезков. В результате чего они смешиваются с другими гранулами, которые потом будут подвергаться тем же процессам — спеканию, вылеживанию...
Оборудование, которое используется в ходе производства пенополистирола, показано в виде таблицы:
Технология изготовления пенопласта напрямую влияет на качество
Как мы говорили выше, сейчас рынок наполнен немалым количеством низкокачественного материала. Его могут производить в гаражах, каких-то складских помещениях.
Но основная проблема заключается не в том, где изготавливают материал (хотя окружающая среда также влияет на качество), главная проблема — не соблюдение всех правил изготовления пенопласта.
Какие могут быть отклонения от правильного производства пенополистирола?
Самые различные — начиная от некачественной грануляции и заканчивая плохой, неточной нарезкой блоков пенопласта на листы.
Некоторые умники вообще не проводят как таковую стабилизацию, вылеживание. Для них важна исключительно скорость изготовления пенополистирола.
«Чем больше — тем лучше — больше денег заработаем!»
Из-за этого характеристики пенопласта сильно ухудшаются:
- он может получиться хрупким, непрочным,
- гранулы могут быть плохо соединены между собой,
- плотность может быть неравномерной.
Это может также происходить из-за низкокачественного, неисправного оборудования, которое использовалось при производстве — вспениватели, сушильные установки, компрессоры, парогенераторы и т.д.
И еще немаловажный момент: при плохой технологии изготовления пенопласт может иметь резкий, неприятный запах. Возможна такая картина: привезли новенькие листы пенополистирола домой, уложили в гараж или другое помещение и... вскоре услышали, что помещение наполнилось каким-то едким, неприятным запахом.
Это очень плохо. Это значит, что пенопласт еще во всю «парит», выделяя вредные вещества. Особенно опасно, когда такой низкосортный материал складывается в жилых помещениях.
Выводы по изготовлению пенопласта
- Технология довольно проста, но требует обязательного соблюдения всех предписанных норм и правил.
- Материал (который внешне будет похож на качественный) можно получить даже при значительных отклонениях от правил производства. И этим пользуются «кустарные» фирмы (нехорошие люди).
Поэтому: покупайте только продукцию надежных, проверенных производителей (которые следят за качеством). Проверяйте наличие у продавцов соответствующих сертификатов качества.
Теперь вы знаете, как делают пенопласт, знаете основные особенности технологии изготовления и какому материалу нужно отдавать предпочтение. Успехов!
vyborstm.ru
Инструкция по сборке линии по производству пенопласта
пенопласт
Компоновка
Котёл (Рис.1 п.2) устанавливается таким образом чтобы дымоход не имел изгибов и выходил за уровень «конька» здания на высоту 0,5-1 м.. Распологать котёл желательно поближе к аккумулятору пара (Рис.1 п.3). На трубопроводе соединяющем котёл и ресивер устанавливается обратный клапан (Рис.1 п.4). Паротрассы от аккумулятора пара к блок форме (Рис.1 п.5), а так-же от котла к предвспенивателю (Рис.1 п.6) должна быть как можно короче, минимум изгибов и обязательно утеплена минеральной ватой.
Предспениватель устанавливается по средине бункеров вылёживания, как показано на (Рис. 2а), при наличии четырёх бункеров и одного предвспенивателя.
При наличии двух предвспенивателей и шести бункеров вылёживания предвспениватели распологают по обе стороны бункеров как показано на (Рис. 2б).
При прокладке пневмотрассы используется оцинкованная труба ø200 мм. Оцинкованная труба соединяется при помощи эл. сварки (на прихватках) с последующей изоляцией стыков лентой «скотч». При прокладке пневмотрассы нельзя допускать соединений труб под прямым углом, резких сужений. Следить за тем чтобы не было «подсоса» воздуха на стыках.
Рис. 1. Схема процесса производства пенополистирольных плит.
Рис. 2. Схема установки бункеров и предвспенивателей.
Котел
В наших линиях мы применяем котёл РИ-5М. Паровой котёл РИ-5М (Рис.3 п.2) предназначен для получения пара давлением 4 кгс/см². Котлы работают на твёрдом топливе (дрова, торфяные и угольные брикеты), а также на маловязком жидком топливе (дизельное топливо, солярное масло). При использовании газогенераторной установки (Рис.3 п.1.) в качестве топлива используются дрова, тирса, щепа. Если есть газогенератор, то котёл устанавливается сверху на газогенератор. Топливо (тирса, щепа) загружается в бункер (Рис.3 п.3.) и при помощи шнека подаётся в сжигатель. Дрова загружаются через загрузочное окно спереди на сжигателе. При помощи Эл. насоса вода закачивается в котёл (уровень контролируется по водомерному стеклу). Разжигается котёл и доводит давление пара до уровня 3,5-4 атм..
Рис. 3. Схема установки котла.
Аккумулятор пара
Аккумулятор пара (Рис.4) подключается через обратный клапан (Рис.1 п.4) непосредственно к котлу. Ресивер пара заполняется водой (половина ресивера), контролируется указательным краном (Рис.4 п.1). Вначале каждой смены проверяем уровень воды в аккумуляторе пара, вода должна заполнять ½ часть. Для уменьшения потерь при теплопередаче необходимо покрыть аккумулятор пара и паропроводы органической ватой. Для предотвращения появления ржавчины в аккумулятор пара помещена катодная защита (Рис.4 п.2), её необходимо менять раз в пол года. Давление в ресивере поддерживать не более 4 атмосфер.
Рис. 4. Аккумулятор пара.
Предспениватель.
Перед началом работы, предвспениватель прогревается до t°=100°C. Для этого открываем кран подачи пара. Прогрев предсвпениватель, перекрываем подачу пара перед вспенивателем и сливаем конденсат (конденсат необходимо сливать периодически в течении работы). Открываем подачу пара, включаем мешалку (Рис.4 п.1) и шнек (Рис.4 п.2), засыпаем сырьё, открываем верхнее или среднее окно (Рис.4 п.4) на вспенивателе, в зависимости от требуемой плотности, открываем подачу сырья. Далее включаем сушку «вентуре» (Рис.4 п.5) и даем пар в радиатор. Регулируя пар так, чтобы на выходе из радиатора тёк конденсат. Температура воздуха в пневмотрассе за трубой «вентуре» должна быть 40-50°С. Через 5-7 мин. появляется вспененный полистирол.
Контроль над плотностью осуществляется с помощью мерной посуды. Температуру внутри вспенивателя контролируют с помощью термодатчика (температура должна находится в пределах 95-105°С.). Подачей сырья добиваемся нужной плотности. В случае непредвиденной ситуации (пропадает питание) останавливаем мешалку, шнек, перекрываем подачу пара, открываем все окна и вычищаем вспениватель.
Из приёмного бункера сушки «вентуре» вспененный полистирол по пневмотранспорту распределяется по бункерам вылёживания. Вылёживается согласно тех. процесса. После вылё-живания, по пневмотранспорту, через пылевой вентилятор, гранулу можно подавать на повторное вспенивание, или в промежуточный бункер, расположенный над блок формой (Рис.6 п.2).
Рис. 5. Предспениватель.
Блок форма.
Блок форма (Рис.6 п.1) подключается к аккумулятору пара. На блок форме на задней и передней стенке есть коллектор. По средине коллектора есть штуцера ø38. Эти штуцера, при помощи армированного шланга (длинной примерно 0,5-0,8 м) соединяем с металлическими трубами, которые подключены к аккумулятору пара. С коллекторов при помощи шлангов, пар также поступает на верхнюю, нижнюю и боковые стенки.
Перед началом работы блок-форма предварительно прогревается до температуры 90-100°С. За тем с промежуточного бункера (Рис.6 п.2) (предварительно загруженного), мы заполняем блок-форму вспененными гранулами. Закрываем блок форму и производим спекание блока согласно технологического регламента.
Категорически запрещается поднимать давление в блок форме выше 0,8 атмосфер.
После того как блок спёкся, не открывая блок форму производим охлаждение блока. Для этого используем вакуумный насос.
Рис. 6. Блок форма.
Вакуумный насос
Вакуумный насос ВВН-1,3 (Рис.7) состоит из двигателя, насоса и водоотделительного бачка.
Фланец «забор воздуха» (Рис.7 п.7) соединяется с вакуумным ресивером или непосредственно с блок формой. На блок форме, на коллекторах, имеются штуцера (2 штуки) к которым при помощи шлангов и двухдюймовых труб подсоединяются вакуумный насос или вакуумный ресивер. Через штуцер (Рис.3 п.3) в вакуумный насос поступает вода. Расход воды 7л/мин. Вода проходит через насос попадает в водоотделительный бачок и через штуцер (Рис.7 п.6) сбрасывается в канализацию, а откаченный воздух через патрубок (Рис.7 п.5) выбрасывается в атмосферу. После того как блок охлаждён, открываем блок форму и извлекаем блок. После вылежки блок отправляют на порезку.
Рис. 7. Вакуумный насос.
Столы порезки
Мы поставляем два стола: горизонтальной и вертикальной порезки. Столы располагаются рядом на расстоянии 2-3 м. Сначала блок распускают на пластины заданного размера (от 10 до 400 мм.), затем пластины перелаживаются на вертикальный стол, и режутся по вертикали на заданный размер. Резка производится нихромовой проволокой °0,51-0,56 мм. Температура нихрома регулируется при помощи сварочного аппарата (входит в комплект). Температура подбирается в зависимости от плотности пенопласта, а также от скорости порезки. Скорость порезки регулируется вариатором на мотор-редукторе.
Рис. 8. Столы порезки.
Бункера вылёживания
Бункера вылёживания используются для вылежки вспененных гранул от 4 до 36 часов согласно технологического регламенту. С труб °42мм. сваривается каркас по размерам согласно тканевого «мешка». Мешок изготавливается из специальной ткани. По периметру прошиваются ленточки. При помощи этих ленточек мешок привязывается к металлическому каркасу. Каркас поднимается на высоту 1 м. Это свободное пространство мы используем для установки коробов (Рис.9 п.1) и прокладки пневмотрассы. Пневмотрасса выходящая из под бункеров вылёживания через пылевой вентилятор (Рис.1 п.10) доставляет вылеженные гранулы в блок форму (Рис.1 п.5) или на промежуточный бункер (Рис.1 п.11) на второе вспенивание.
Рис. 9. Бункера вылёживания.
Дробилка отходов
Дробилка отходов (Рис.1 п.9) устанавливается возле столов порезки (Рис.1 п.8). Отходы пенопласта образующиеся при порезке пенопластовых блоков, загружаются в дробилку. При помощи вентилятора (Рис.10 п.1) и пневмотрассы дробильные отходы попадают в бункера вылёживания (Рис.1 п.7). После чего с остальным сырьём попадает в блок форму (Рис.1 п.5).
Рис. 10. Дробилка отходов.
Оцинкованная труба соединяется при помощи эл. сварки (на прихватках) с последующей изоляцией стыков лентой «скотч».
Использовать ячеистый бетон застройщики сегодня стали довольно часто. Это вполне естественно, поскольку подобный материал проявляет очень большие возможности. Используя его правильно, удается достигать отличного эффекта. Но все-таки результат во многом …
Владельцы загородных домов используют сайдинг в целях облицовки фасада по многим причинам
msd.com.ua
Вторичное Использование Отходов Пенополистирола
Вторичное использование отходов пенополистирола для связующих материалов в литейном производстве В.С. Дорошенко, А.А. Стрюченко Физико-технологический институт металлов и сплавов НАН Украины, Киев
Пенополистирол (в обиходе называемый еще пенопластом) получил широкое применение в мире в качестве материала для упаковки и сохранения пищевых продуктов. Это обстоятельство подчеркивает гигиенические свойства пенополистирола, материала, свойства которого практически не меняются во времени. В упаковках из пенополистирола часто сохраняются мясо, рыба, замороженные или свежие овощи, а также напитки. В настоящее время практически вся упаковка бытовой электронной техники делается из пенополистирола. Также пенополистирол широко применяется в современном строительстве в качестве теплоизоляционного слоя в системах утепления домов и других строений, а также емкостных аппаратов и трубопроводов. Его применяют также в литейном производстве при получении моделей, которые в контакте с жидким металлом газифицируются при получении отливок из черных и цветных сплавов. Фактически пенополистирол можно встретить во многих сферах современной жизни. После использования упаковки, либо другим образом попадая в отходы, пенополистирол не находит применения. Он не подлежит утилизации подобно другим бытовым отходам, так как не взаимодействует с водой и не подлежит биологическому разложению, указанные характеристики его высокой стойкости и нейтральности превращаются во вредные при попытке утилизации. Пенополистирол нельзя сжигать подобно углю, дровам и т. п. в связи с тем, что при этом в процессе его деструкции в больших объемах выделяются очень вредные (токсичные) газы. Поэтому отходы пенополистирола накапливаются в большом количестве в окружающей человека среде, создавая одну из сложных экологических проблем. Так, только в одной Японии по данным за 1998 г. ежегодно используется около 400 тыс. тонн пенополистирола для упаковки рыбной продукции, пищевых лотков, упаковки бытовой электронной техники. В Интернете имеется много сайтов о попытках вторичного использования пенополистирола после дробления упаковки в виде гранул, однако такое применение весьма ограничено. Вместе с тем, пенополистирол может быть экономически эффективно использован для получения связующих и клеев широкого назначения, в том числе для приготовления формовочных и стержневых песчаных смесей, покрытий литейных форм для производства отливок из черных и цветных сплавов. Важно, что эти связующие могут отверждаться при комнатной температуре, а также при подсушке с температурой не выше 180-2000С. Это показали нижеописанные разработки Физико-технологического института металлов и сплавов НАН Украины (г. Киев), в результате которых созданы указанные связующие – это растворы полистирола (изначально пенополистирола) в органическом растворителе. Исследования состояли в обоснованном выборе растворителя, оптимизации составов, эксплуатационных свойств связующих и песчаных смесей. Известно, что пенополистирол легко растворяется во многих растворителях, в частности, в бензоле, толуоле, ксилоле, сольвенте, однако, они имеют очень низкий предел допустимых концентраций (ПДК, мг/м3) в атмосфере рабочих помещений (цехов, участков), это резко ухудшает условия труда при их использовании. Так, ПДК бензола всего 5 мг/м3, толуола, ксилола, сольвента – по 50 мг/м3. Высокая летучесть этих растворителей также усложняет их применение в производстве. Имеется другая группа растворителей с более высоким ПДК, который достигает 100-200 мг/м3. Это ацетон, этилацетат, бутилацетат, метилэтилкетон, тетралин и др. Однако, у них, за исключением дорогого и дефицитного тетралина, очень высокая летучесть. Так, летучесть ацетона по серному эфиру равняется всего 2,1, летучесть этилацетата 2,9. Применение этих растворителей для приготовления растворов пенополистирола с целью их использования в открытой атмосфере рабочих помещений с точки зрения ухудшения условий труда есть весьма проблематичным и на практике не применяется. Очевидно, что для получения растворов из отходов пенополистирола, в том числе, как связующих песчаных формовочных и стержневых смесей для литейного производства, необходимы растворители с более высоким ПДК и низкой летучестью, как обязательное условие создания малотоксичных смесей. Поставленная задача решена нами установлением того факта, что растворителем отходов пенополистирола может быть живичный скипидар, на что и получен Институтом Патент Украины. Живичный скипидар – это углеводород растительного происхождения (ГОСТ 1571-82). Его получают из живицы (из надрезов коры сосны), которую перегоняют с паром и разделяют на летучую фракцию – скипидар и нелетучий осадок – канифоль. Скипидар содержит в основном бицикличный монотерпеноид пинен. Живичный скипидар представляет собой прозрачную бесцветную или чуть окрашенную жидкость с плотностью 0,855 – 0,863 г/см3. До появления уайт-спирита скипидар был основным растворителем лаков и красок, его также применяют в фармакологии, так как он обладает бактерицидными свойствами. Ежегодный объем производства живичного скипидара в мире составляет около 300000 т. Живичный скипидар имеет ПДК равное 300 мг/м3, то есть значительно выше упомянутой выше группы растворителей с ПДК не более 200 мг/м3. Он хорошо растворяет отходы пенополистирола и имеет низкую летучесть, в сравнимых условиях, если принять скорость испарения живичного скипидара за единицу, то ацетон испаряется в 15,1 раза быстрее, бензин "Калоша"в 9,87 раз, этилацетат в 7,66 раз, уайт-спирит в 2,28 раз. Исследуя растворяющую способность живичного скипидара по отношению к отходам пенополистирола, разработали технологию получения растворов из отходов пенополистирола в живичном скипидаре практически любой концентрации вплоть до 50 %. В лаборатории получены растворы с концентрацией 25 %, 30 %, 40 % и 50 %. Приготовление растворов пенополистирола в органических растворителях обусловлено многократным уменьшением его исходного объема и увеличением объема раствора по сравнению с объемом растворителя. Приготовление растворов пенополистирола является удобным способом его компактирования, эти отходы занимают вследствие низкой плотности (около 25 кг/м3) значительный объем в окружающей среде. По нашей технологии для увеличения объема раствора на одну единицу требуется растворить многие десятки единиц объемов пенополистирола. Разработанная технология рециклинга пенополистирола из его отходов позволяет позволяет перевести его в раствор, а затем, например, изготавливать современные малотоксичные связующие материалы для производства песчаных формовочных и стержневых смесей, а также покрытий литейных форм, что дает возможность усовершенствовать и разрабатывать новые более эффективные и экономичные процессы литья металлов. Кроме того, использование отходов пенополистирола имеет важное экологическое значение, так как речь идет об уменьшении этих отходов в окружающей человека экосфере. Наиболее технологичны составы песчаных литейных смесей на 40 –процентном растворе содержат 2% полистирола в сухом остатке. Эти смеси прекрасно формуются и отверждаются кратковременной сушкой при температуре до 200 град. С. Институтом получен Патент Украины на изобретение по составу этих смесей, вместе с тем сейчас патентуется состав смеси, отверждаемый при комнатной температуре. В развитие технологии рециклинга отходов пенополистирола путем получения его растворов в живичном скипидаре и последующем использовании в качестве связующего в литейном производстве предложена технологическая схема опытно-промышленного процесса с перечнем несложного оборудования, включающего реактор в виде герметично закрываемого сосуда, снабженного мешалкой для ускоренного растворения пенополистирола и получения однородного по концентрации раствора. Как показали экспериментальные работы, в растворах пенополистирола в живичном скипидаре, независимо от концентрации раствора, наблюдается седиментация мелких загрязнений, занесенных с отходами пенополистирола. После приготовления раствора заданной концентрации выполняли операцию отстаивания для осаждения этих загрязнений и их последующего удаления. При промышленном рециклинге это может служить удобным способом очистки полистирольного раствора. Физико-механические свойства формовочных стержневых смесей на основе полистирольных связующих превосходят или равны аналогичным характеристикам холодно-твердеющих смесей на основе жидкого стекла, феноло-формальдегидных, карбомидо-фурановых смол. Это обстоятельство позволило рекомендовать полистирольные связующие с живичным скипидаром для замены вышеупомянутых связующих и, в особенности, дорогостоящих смол (со стоимостью на порядок выше раствора полистирола), в производственном процессе литья заготовок из черных и цветных сплавов. В Физико-технологическом институте металлов и сплавов кроме создания новых связующих песчаных смесей ведется поиск партнеров для участия в программах разработки технологии получения из растворенного полистирола твердых пластмасс и изделий, а также его использования в качестве сырья для производства недорогих высокопрочных клеев, строительных и теплоизолирующих пен. Бактерицидные свойства полученного из древесины хвойных пород живичного скипидара вместе с клеевыми свойствами описанного раствора можно использовать для производства пластыря, герметика, а также на предприятиях по производству продуктов и медикаментов. Контакт для вопросов и предложений по адресу: [email protected], В. Дорошенко.
www.rusarticles.com