Влияние дисперсного армирования на деформационно-прочностные свойства бетона Текст научной статьи по специальности «Строительство. Архитектура». Дисперсное армирование
Дисперсное армирование - Большая Энциклопедия Нефти и Газа, статья, страница 1
Дисперсное армирование
Cтраница 1
Дисперсное армирование при оптимальной объемной концентрации фибры ( проценте армирования) 1 5 % обеспечивает примерно 9 - 10 кратное повышение ударной выносливости бетона и является наиболее эффективным приемом ударного упрочнения бетона. [1]
Дисперсное армирование бетона повышает его трещиностойкость, прочность на растяжение, ударную вязкость, сопротивление истиранию. Эффективность применения волокон в бетоне зависит от их содержания. Дисперсное армирование приостанавливает развитие волосяных трещин лишь при расстоянии между отдельными волокнами не более 10 мм, поэтому применение в бетоне крупного заполнителя снижает эффективность подобного армирования. Стальные фибры вводят в бетонную смесь в количестве 1 - 2 5 % объема бетона ( 3 - 9 % по массе), что обычно составляет 70 - 200 кг на 1 м3 бетона. При этом повышаются прочность бетона на растяжение ( на 10 - 30 %), ударная прочность, износостойкость. [2]
Предложено обоснование механизма действия дисперсного армирования, обусловливающего повышение прочности на растяжение, трещино-стойкости, ударной выносливости цементных бетонов. [3]
Показано, что позитивное влияние дисперсного армирования, на стадиях структурообразования и нагружения бетона начинает реализовываться после достижения объемной концентрации фибры, обусловливающей начальную объемно-пространственную связность фиброструктуры. [4]
Так как волокна используют для дисперсного армирования тампонажных материалов в широком диапазоне температур ( от - 5 до 250 С), они должны быть термостойкими. Исследования, проведенные с волокнами разных типов, дали положительные результаты. В качестве армирующей добавки наиболее целесообразно использовать минеральные волокна. [5]
Так как волокна используют для дисперсного армирования тампонажных материалов, применяемых в широком диапазоне температур ( от 0 до 250 С), они должны быть термостойкими. [6]
В настоящее время широко применяется метод дисперсного армирования материалов, позволяющий существенно повысить их прочностные свойства. [7]
Разработаны производственные составы бетонов высокой ударной выносливости на основе дисперсного армирования голов свай стальной, стекловолоконной, полипропиленовой фиброй, грубым базальтовым волокном. [8]
Четвертый раздел содержит данные исследований физико-механических свойств цементных бетонов с дисперсным армированием различными видами фибры. [9]
Цель работы состоит в обосновании критериев ударной выносливости бетонов и изучении роли дисперсного армирования в повышении ударной выносливости и статической прочности фибробетонов. [10]
В рамках опытно - промышленного эксперимента были отработаны несколько составов тяжелых бетонов с дисперсным армированием в виде металлической и синтетической фибры. [11]
Расчеты показали, что армирование водопропускных колец может быть выполнено из стальной фибры при проценте дисперсного армирования) ifv 0.8; 1.0; 1.2; 1.4 с полным отказом от стержневой арматуры. [12]
Комплексное использование кристаллохимиче-регулирования процессов твердения тампонажных минерализации среды затворения и модифицирова-азы в сочетании с оптимизацией ее гранулометри-и дисперсным армированием системы твердеюще-дает предпосылки для получения высокой технике-эффективности при промышленном применении ных тампонажных растворов для цементирования жных условиях. [13]
Производство гипсокартонных листов включает в себя следующие процессы: приготавливают пеногипсо-вую смесь сухим смешиванием вяжущего, ускорителя и добавок, а в ряде случаев и компонента для дисперсного армирования; сухую смесь, воду или пульпу волокнистого материала дозируют, затем приготавливают и дозируют пену и перемешивают все компоненты с выдачей пеногипсового раствора на лицевой картон. [14]
Основные технологические свойства минерализованных тампо-нажных растворов могут быть значительно улучшены в результате оптимизации гранулометрического состава твердой фазы в процессе промышленного изготовления тампонажных смесей де-зинтеграторным способом и применения метода дисперсного армирования твердеющей системы. Промышленное применение таких растворов базируется на существующей технике и технологии цементирования скважин и может осуществляться в любом регионе страны со сложными геолого-техническими условиями цементирования, обусловленными наличием в разрезе скважины многолетнемерзлых пород или хемогенно-терригенных отложений. [15]
Страницы: 1 2
www.ngpedia.ru
Дисперсное армирование бетонов
В настоящее время получает всё более широкое распространение применение специальных дисперсноармирующих волокон вместо традиционного армирования.
В конце мая 2007 года нам, Санкт-Петербургскому политехническому университету и компании «Северсталь-метиз», удалось провести научно-практическую конференцию по современным методам армирования. Присутствовало достаточно много специалистов и производителей (главным образом — стальной фибры). В кулуарах итог подвёл профессор ГАСУ Юрий Владимирович Пухаренко: «Надо более широко применять фибру в различных видах конструкций, а уж если это нам удастся, то без работы не останется ни один наш отечественный производитель».
Несмотря на значительный рост объёмов потребления стальной фибры российским строительным рынком, он по-прежнему недостаточно оценён. В Европе ежегодно производится и потребляется около 300 тыс. т фибры, тогда как в России — всего около 7 тыс. т.
При этом, к сожалению, на нашем строительном рынке применение фибры традиционно ограничено. Так, если в Европейских странах, той же соседней Финляндии, данный материал используется в разнообразных областях: в гражданском, дорожном строительстве, строительстве гидросооружений, тоннелей, аэропортов, то основная сфера применения фибры (90 %) в России — это укладка полов. Дальше, чем для использования при устройстве горизонтальных плоскостей, фибра не применяется.
Увы, но даже сейчас приходится признать, что данный вид армирования в нашей стране постоянно сталкивается с одной и той же проблемой — отсутствие достаточно внятных рекомендаций, инструкций по расчёту и применению тех или иных видов фибры, а как следствие, невозможность применения данного материала в более широких технологических схемах армирования бетонных конструкций.
Эффективность применения сталефибробетона доказывает зарубежный опыт. Это щирокий ассортимент стальной фибры и большое количество (более 25) фирм и корпораций, производящих фибру на постоянной основе. Надо заметить, что это мощные производители обычной стержневой и проволочной арматуры или металлоизделий.
Впереди — Япония, где 7 крупных фирм выпускают стальную фибру, рубленную из листа или проволоки, фрезерованную из сляба или вытянутую из расплава. Производителями предлагается фибра различных форм, профилей, размеров и прочности, в том числе из коррозионно-стойкой стали.
Уже в 1981 году Япония применила порядка 3 тыс. т стальной фибры, из которых 500 т — из нержавеющей стали. Отставание России от Японии в этой области — 25 лет.
То, что мы имеем на данный момент в России, это армирование фиброй именно бетонных полов, в частности запущенных в производство у нас аналогов производимых на Западе материалов.
Но не всё так печально. Прогресс не стоит на месте, и кому как не нам стать первыми. Тем более, что работы в данной области начинали наши учёные. Хотя ни для кого не секрет, что фибру, в частности различные виды волокон, применяли весьма давно, до того момента, когда она получила самое широкое распространение как в мире в целом и в Европе в частности.
Трудно догнать такие передовые страны как Япония и Германия. Но оценивая потенциал и перспективы наших научных разработок, мы с полной уверенностью можем сказать, что благодаря пытливому уму, незакостенелости мышления и опоре на производственный опыт мы ещё сможем занять, если уже не занимаем, одни из первых позиций в данной области. Это касается именно разработок, но увы не внедрения.
Также известно, что арматурная сетка уменьшает количество усадочных трещин только на 6 %, металлическая фибра — на 20–25 %, а полимерные волокна — на 60–90 %.
Переходя к практической части, необходимо оценить складывающуюся ситуацию по использованию данного вида армирования в строительстве.
Что и зачем?
Фибробетон — это бетон, армированный дисперсными волокнами (фибрами). Такой бетон представляет собой обычную смесь цемента, песка, крупного заполнителя и воды, дополненную определённым количеством стальных или других волокон (фибр). Иногда добавляется пластифицирующая добавка, чтобы улучшить обрабатываемость смеси. Дискретные волокна производятся из различных материалов — от полипропилена до стали, в различных конфигурациях, длинах и поперечных сечениях. (табл. 1).
В настоящее время наибольшая эффективность фибробетона как композита достигается при правильном подборе и сочетании компонентов. Самым эффективным материалом в этом плане, ввиду его относительной стоимости, является стальная арматура.
Модуль упругости арматуры в 56 раз больше аналогичного показателя бетона, однако при достаточной анкеровке в бетоне не может быть полностью использована прочность и получен наибольший вклад арматуры в работу самого материала как до, так и после образования трещин.
Если мы используем стальную фибру то проблема с анкеровкой не стоит вовсе, так как анкернение фибры достаточно высокое.
В отличие от проволочной сетки или арматуры, которая устанавливается в одной плоскости, стальная фибра одинаково распространяется по всей бетонной матрице (диспергирует). Стальная фибра выполняет множество функций в зависимости от пропорций, которые могут варьировать в пределах 15–120 кг/м3. Одна из первоначальных функций — уменьшение микро- и макротрещин. Определяя трещины на начальной стадии их появления, стальная фибра препятствует их распространению. Традиционная классическая арматура, или проволочная сетка, предназначена для того, чтобы предохранить бетон от образования самых первых усадочных трещин, а не предотвратить их распространение.
Многие производители имеют и продают компьютерные программы, которые позволяют пересчитывать и применять определённые пропорции фибры для замены арматуры или арматурной сетки. Данные программы предоставляет «Арселор» и другие импортные производители.
В дальнейшем мы более подробно рассмотрим основные технико-физические показатели на примере различных фибр, производимых как в нашей стране, так и за рубежом. Основным показателем считается вр?менное сопротивление разрыву, или, как его ещё называют, прочность на растяжение.
Основные свойства и показатели различных видов волокон приведены ниже в табл. 1.
В зависимости от вида материала и способа изготовления мы имеем различные значения параметров и, как следствие, различные дозировки и способы применения.
Волокно | Плотность, г/см3 | Прочность на растяжение, МПа | Модуль упругости, МПа | Удлинение при разрыве, % |
Полипропиленовое | 0,90 | 400–700 | 3500–8000 | 10–25 |
Полиэтиленовое | 0,95 | 600–720 | 1400–4200 | 10–12 |
Нейлоновое | 1,10 | 770–840 | 4200–4500 | 16–20 |
Акриловое | 1,10 | 210–420 | 2100–2150 | 25–45 |
Полиэфирное | 1,40 | 730–780 | 8400–8600 | 11–13 |
Хлопковое | 1,50 | 420–700 | 4900–5100 | 3–10 |
Асбестовое | 2,60 | 910–3100 | 68 000–70 000 | 0,6–0,7 |
Стеклянное | 2,60 | 1800–3850 | 7000–8000 | 1,5–3,5 |
Стальное | 7,80 | 600–3150 | 190 000–210 000 | 3–4 |
Углеродное | 2,00 | 2000–3500 | 200 000–250 000 | 1,0–1,6 |
Карбоновое | 1,63 | 1200–4000 | 280 000–380 000 | 2,0–2,2 |
Полиамидное | 0,90 | 720–750 | 1900–2000 | 24–25 |
Вискозное сверхпрочное | 1,20 | 660–700 | 5600–5800 | 14–16 |
Базальтовое | 2,60–2,70 | 1600–3200 | 7000–11 000 | 1,4–3,6 |
Таблица 1. Свойства различных видов волокон для изготовления фибры
Подробно мы остановимся на стальной, базальтовой и полипропиленовой фибрах.
Стальные фибры
Стальная фибра представляет собой отрезки стальных волокон специальной формы и длины, в определённых дозировках (от 20 кг/м3) добавляемых в бетонную матрицу для осуществления объёмного армирования.
В результате фибрового армирования создаётся композитный материал — сталефибробетон, обладающий рядом преимуществ перед неармированным бетоном и бетоном с традиционными видами армирования. Повышается:
— прочность на растяжение при изгибе — в 2–3 раза;
— прочность на сжатие — до 10–50 %;
— прочность на осевое растяжение — до 10–40 %;
— ударная прочность — в 8–12 раз;
— сопротивление истираемости — до 2 раз;
— трещиностойкость — в 2–3 раза;
— морозостойкость и водонепроницаемость — не менее чем на класс.
Использование технологии фибрового армирования позволяет существенно снизить время выполнения и трудоёмкость работ за счёт отказа от вязки арматуры и укладки сеток, а в ряде случаев — сэкономить строительные материалы за счёт достижения проектных характеристик при меньшей толщине и/или металлоёмкости конструкций.
Рассмотрим перспективные направления применения стальной фибры.
В случае применения в бетонных полах. Снижение трудоёмкости и времени выполнения работ, существенное повышение долговечности и межремонтных интервалов.
В дорожном строительстве. Повышенная устойчивость трещинообразованию, образованию ям и рытвин, более ровная поверхность, меньшее количество швов и стыков, повышенное шумопоглощение, существенная экономия на ремонте.
Взлётно-посадочные полосы. Повышение долговечности, более ровная поверхность, меньшее количество швов и стыков, повышение безопасности взлётов и посадок, понижение износа деталей шасси самолетов, устойчивость к воздействиям внешней среды и сложным условиям эксплуатации.
В мостостроении. Повышение эксплуатационной надёжности, снижение трудоёмкости за счёт частичного или полного отказа от традиционного армирования, улучшение гидроизоляционных свойств, армирование труднодоступных участков.
В гидротехнических сооружениях. Повышение прочностных характеристик, водонепроницаемости и сроков эксплуатации, снижение трудоёмкости строительства.
Изготовление свай и шпунтов. Применение свай с оголовком из сталефибробетона обеспечивает возможность забивки свай до проектной отметки без повреждений, отпадает необходимость забивки свай-дублёров.
Изготовление сборных железобетонных конструкций. Применение сталефибробетона в кольцах стеновых колодцев, водоотпускных и коллекторных трубах, плитах перекрытий позволяет увеличить срок эксплуатации изделий при существенном снижении трудозатрат и экономии материалов.
Прочие области применения: взрыво- и взломоустойчивые сооружения, элементы фундаментов, трубопроводы, тонкостенные и декоративные конструкции, ёмкости для воды и других жидкостей.
Базальтовая фибра
В настоящий момент в России существует несколько производителей базальтовой фибры.
Наиболее «узнаваемы» два типа материала: микрофибра и рубленое волокно.
Микрофибра базальтовая модифицированная (МБМ)
МБМ получается путём пропитки измельченной минеральной ваты, производимой из расплава базальтовых пород. Рекомендуемое содержание — 1,5–20 %, в зависимости от вида и назначения композиционного материала.
Для обеспыливания МБМ применяют органические вещества, перечень которых приведён ниже.
В качестве модификатора используют углеродный наномодификатор фуллероидного типа по ТУ 2166-001-13800624-2003.
Состав МБМ, в масс. %:
Вата базальтовая с органической пропиткой 99,3–99,6
Наномодификатор 0,0001–0,01
Едкий натр 0,05–0,10
Вода 0,3–0,5
Основные характеристики МБМ приведены в табл. 2.
Характеристика | Норма |
Средний диаметр волокна, мкм | 8–10 |
Средняя длина волокна, мкм | 100–500 |
Содержание неволокнистых включений, % по массе | ?10 |
Плотность насыпная, кг/м3 | ?800 |
Влажность, % по массе | ?2 |
Содержание органических веществ, % по массе | ?2 |
Цвет | От жёлтого до коричневого |
Содержание наномодификатора, % по массе | 0,01–0,0001 |
Модуль на разрыв, ГПа | 18 |
Таблица 2. Основные характеристики МБМ
МБМ предназначена для дисперсного армирования пластмасс, бетонов, асфальтобетонов, минеральных смесей и т. д. с целью улучшения их свойств — прочность на сжатие, растяжение, изгиб, срез, водопоглощение, морозостойкость, трещиностойкость и т. п.
МБМ термоустойчива вплоть до 300 °С.
Рекомендуемое содержание микрофибры — 1,5–20% от массы цемента, в зависимости от вида, назначения и стоимости композиционного материала.
Методика введения и конкретное содержание микрофибры в композите регламентируется специализированными инструкциями.
При армировании минеральных смесей и бетонов используется смеситель принудительного действия, причём микрофибра добавляется в сухую смесь непосредственно перед добавлением жидких компонентов. Время перемешивания — не менее 10 мин.
При армировании асфальтобетонов и пластмасс МБМ добавляется в расплав материала, и принудительное перемешивание осуществляется до получения однородной массы.
Добавка | Нормативный документ | Вредные вещества |
Битумы нефтяные строительные Битумы нефтяные дорожные вязкие Масла индустриальные Масла цилиндровые тяжелые Масло сланцевое топливное Экстракты нефтяные Эмульсии битумные дорожных марок ЭБА-1 и ЭБА-2 | ГОСТ 6617-76 ГОСТ 22245-90 ГОСТ 20799-88 ГОСТ 6411-76 ГОСТ 4806-79 ТУ 38-101714-84 ГОСТ 18659-81 | Пары углеводородов То же То же. Масляный туман Пары углеводородов То же То же То же |
Таблица 3. Органические вещества, применяемые в качестве обеспыливающих добавок
Базальтовое рубленое волокно (чопсы).
Данная фибра производится методом рубки базальтового ровинга на волокна заданной длины.
Свойства:
— высокая прочность и долговечность;
— высокая термостойкость, абсолютная негорючесть;
— стойкость к агрессивным средам;
— экологическая чистота.
Базальтовая фибра, как и любая фибра, обеспечивает трёхмерное упрочнение (традиционная арматура — лишь двухмерное).
Имеет следующие сферы применения.
Возведение объектов гражданского строительства.
Реконструкция хранилищ и банковских сейфов.
Сооружение мостов, взлётно-посадочных полос, гидротехнических сооружений (береговых дамб и плотин, шлюзов и каналов рек).
Изготовление реакторных отделений атомных электростанций, контейнеров для захоронения радиоактивных отходов.
Укрепление и ремонт сводов шахт и тоннелей.
Создание различных видов дорожных покрытий, сборных и монолитных плит, бордюров, разделительных полос и тротуарной плитки.
Изготовление деталей объёмного промышленного оборудования — прокатные станы, молоты, гидравлические прессы и др.
Характеристика | Значение |
Диаметр единичного волокна, мкм | 13, 17 |
Длина, мм | 6; 12; 18; 24 |
Тип замасливателя | 4С* |
Диапазон рабочих температур, °С | –260...+700 |
Массовая доля замасливателя, % | ?0,3 |
Массовая доля влаги, % | ?1,0 |
Гигроскопичность, % | ?0,2 |
Таблица 4. Технические характеристики базальтовой фибры
* По согласованию с потребителем возможен выпуск ровинга с другим типом замасливателя
Длина, мм | Область применения | Количество фибры, кг/м3 |
6 | Лёгкие бетоны Сухие смеси | 0,5–1,0 |
12 | Тяжёлые бетоны | 0,5–1,0 |
Таблица 5. Рекомендации к применению
Чопсы поставляются в полипропиленовых мешках весом 25 кг.
Полипропиленовое волокно
Микроармирующее волокно из полипропелена применяется в гражданском, промышленном и дорожном строительстве как компонент строительных растворов и смесей, модифицирующий структуру вяжущих веществ и предотвращающий образование и развитие внутренних дефектов цементных композиций. Материал носит наименование волокно строительное микроармирующее (ВСМ).
Рис. 1.
В ходе экспериментов выяснено, что добавление в бетонную смесь ВСМ приводит к изменению следующих параметров:
— уменьшение расслаивания бетонной смеси — на 25 %;
— сокращение времени первичного и окончательного твердения, то есть ускорение оборота форм — на 45 %;
— увеличение марочной прочности бетона — на 25 %; то есть при добавлении в марку бетона М300 волокна в количестве 600 г получаем марку М350.
Такое применение ВСМ позволяет повысить производительность предприятий, занимающихся производством бетонных конструкций, качество и долговечность строительных конструкций и сооружений, снизить номинальную стоимость строительного продукта.
Основные области применения микроармирующего волокна — такие же, как и у любой фибры.
Монолитное и высотное домостроение.
Наливные полы и стяжки.
Сваи забивные фундаментные.
Сухие монтажно-ремонтные смеси, штукатурные смеси, торкрет-бетон.
Монолитное дорожное покрытие, дорожные плиты, шпалы железных дорог.
Фундаменты динамического и ударного действия.
Строительство сооружений с повышенными требованиями к пожароустойчивости.
Производитель разделяет ВСМна следующие типоразмеры:
— ВСМ-II-20/18 (резка волокна длиной 18 мм) — микроармирующий компонент для жёстких и сверхжёстких бетонов, изготавливаемых с применением крупного и среднего заполнителя (песок, гравий, щебень) и применяемых для гидротехнических сооружений, дорожных покрытий, мостостроения.
— ВСМ-II-20/12 (резка волокна длиной 12 мм) — для плит перекрытия, наливных бетонных полов, гидротехнических сооружений, фундаментной и свайной продукции и других тяжёлых и лёгких бетонов.
— ВСМ-II-20/6 (резка волокна длиной 6 мм) — для применения в цементно-песчаных (кладочных, штукатурных, затирочных, монтажно-ремонтных и др.) растворах и сухих смесях на основе цемента, в пенобетонах для улучшения геометрической формы.
ВСМ способно перемешиваться в любом типе смесителей (гравитационного или принудительного действия), может вводится как непосредственно после добавления воды, так и в сухую или готовую бетонную смесь, может добавляться в бетонную смесь, транспортируемую бетоновозами (автомиксер). Подача бетононасосом смеси, содержащей ВСМ, не составляет труда.
Дозировка:
— ВСМ-II-20/18 в особо тяжёлые и тяжёлые и жёсткие бетоны — 0,9–2,0 кг/м3;
— ВСМ-II-20/12 в бетон — 0,6–1,2кг/м3;
— ВСМ-II-20/6 в строительные смеси, штукатурки и т. д. — 0,6 кг/м3.
Если бетон для работы готовится на предприятии по изготовлению сборных бетонных и железобетонных конструкций и изделий, то сухие компоненты смеси смешиваются в технологическом порядке, предусмотренном рецептом изготовления бетона и дозатором, либо необходимое количество ВСМ добавляется иным способом. Рекомендуемая продолжительность перемешивания бетонных смесей (ГОСТ 7474-94) увеличивается на 10–20 % для получения смеси бетона, в котором отдельные элементарные волокна распределены гомогенно.
ВСМ может быть добавлено в готовые (товарные) бетонные смеси. Хорошего диспергирования можно достичь в смесителях гравитационного или принудительного действия.
ВСМ может добавляться к смесям на основе цемента в смесители типа «миксер», установленном на автомобиле и доставляющем готовую бетонную смесь непосредственно на место укладки.
Так как ВСМ хорошо диспергируется в смеси, при производстве бетона или раствора, содержащего волокно, не происходит комкования ВСМ в смеси.
Несмотря на то, что при введении волокна в бетонную смесь осадка конуса несколько уменьшается, удобоукладываемость смеси даже возрастает, так как увеличивается эластичность, пластичность и гомогенность смеси. Следовательно, после введения волокна не требуется добавление воды затворения для увеличения осадки конуса.
Пенобетон.
ВСМ-II-R0,02-20/6, дозировка 0,6 кг на 1 м3 — улучшение геометрической формы изделия.
ВСМ-II-R0,02-20/12, дозировка 0,9 кг на 1 м3 — улучшение геометрической формы изделия и повышение прочности.
ВСМ-II-R0,02-20/18, дозировка 0,9 кг на 1 м3 — улучшение геометрической формы изделия, повышение прочности и адгезионной способности к наносимому материалу (при оштукатуривании стен).
Заключение
В заключении хотелось бы отметить, что данный способ армирования хорошо зарекомендовал себя при производстве работ на промышленных объектах как в Санкт-Петербурге, так и в других регионах.
Наиболее яркий пример из моей практики — это выполнение работ по устройству монолитных полов на заводе тяжёлых грузовиков «Яровит-Моторс».
Раньше здание эксплуатировалось как бетонный узел, его продукция поставлялась непосредственно на строительство Ленинградского металлического завода. Срок его эксплуатации продолжался с 1946 по 1979 год. Впоследствии цеха использовались по разному назначению. В 90-х годах, в эпоху безвременья, цех совсем обветшал и в начале XXI века был выкуплен серьёзным инвестором, для того чтобы впоследствии быть перепрофилированным под производства тяжёлых грузовиков.
Был произведён капитальный ремонт старого бетонного основания. Выполнен частичный демонтаж старого бетонного покрытия, а в тех местах, где образовались пустоты и размывы, произведена засыпка щебнем и выполнена стяжка с применением арматуры, так как эти места обладали определённой нестабильностью грунтов.
Основным материалом несущей плиты было предложено выбрать бетон армированный стальной и полипропиленовой фиброй. Исходя из предварительных данных и опираясь на зарубежный и отечественный опыт, было решено использовать фибру анкерного типа в количестве 25 кг. На 1м3 бетона полипропиленовую фибру дозировали в количестве 0,6 кг/м3. Толщина плиты составляла 200 мм. Также был применён пластификатор «FM», который позволил правильно регулировать водоцементное отношение и улучшить удобоукладываемость смеси.
Верхнее покрытие плиты было выполнено по технологии «Топ-Бетон» методом внесения сухого упрочнителя с последующей затиркой бетоноделочными машинами.
Были получены хорошие результаты, подтверждённые лабораторными испытаниями. Единственным недостатком применения полипропиленовой фибры стало появление на поверхности отдельных волокон, которые впоследствии были удалены газовой горелкой.
Очень хочется надеяться, что благодаря нашим общим усилиям по популяризации фибры, удастся расширить круг её применения.
www.allbeton.ru
Дисперсное армирование - Большая Энциклопедия Нефти и Газа, статья, страница 2
Дисперсное армирование
Cтраница 2
Кроме перечисленных суперпластификаторы обладают способностью улучшать другие свойства бетонов, например благодаря существенному снижению водоцементного отношения повышать долговечность; расширяется возможность использования шлакопортландце-мента, золоцемента и бетонов с дисперсным армированием, а также изготовления легких бетонов. Таким образом, действие суперпластификаторов распространяется не только на портландцемент, но и на другие цементные системы. [16]
Анализ полученных на основе экспериментов линейных зависимостей относительного уровня динамических напряжений от количества ударов до разрушения в полулогарифмических координатах, характеризуемых количественно коэффициентами динамического упрочнения и выносливости, показал, что повышенная ударная выносливость бетонов с дисперсным армированием предопределяется повышенными упруго-вязкими свойствами названных бетонов и повышенным коэффициентом динамического упрочнения. [17]
Новожилова, B.C. Стерина), обладающего высокой ударостойкостью. Дисперсное армирование позволяет в значительной степени повысить всю совокупность физико-механических характеристик бетона, таких как статическая прочность, трещиностойкость, ударная стойкость. [18]
Электроизоляционные бетоны подвергают армированию неметаллической арматурой в виде стеклопластиковых стержней с использованием способа предварительного напряжения. Возможно применение дисперсного армирования стеклянными и базальтовыми волокнами изделий из электроизоляционного бетона. Требования в отношении оптимизации структуры цементного камня, как матрицы, и бетона в полной мере сохраняются, как для других ИСК. Объемная пропитка мономерами и их полимеризация, а также вторичная просушка, активизация поверхности зернистого заполнителя являются эффективными мерами повышения диэлектрических свойств бетона. [19]
В случае использования компонентов, резко различающихся по скоростям твердения, возможно получение камня, обладающего достаточно высокими физико-механическими свойствами. При опережении процесса формирования гидрогроссуляров над образованием гидросиликатов кальция происходит дисперсное армирование гидрогроссуляров гидросиликатами кальция. Однако следует отметить, что дисперсное самоармирование возможно лишь до отношения оксидов в вяжущем А. [20]
Описание механических свойств композитных материалов, которые могут обладать весьма высокой прочностью ( особенно статической и ударной), можно производить двумя путями. В первом случае композитные материалы рассматриваются как квазиоднородные ( гомогенные), обладающие в случае объемного дисперсного армирования изотропией деформационных и прочностных свойств, а в случае армирования волокнами, плоскими сетками или тканями - определенного типа анизотропией. Обычно применяют модели ортотропного или трансверсально-изотропного тела. При таком подходе речь идет о механических характеристиках, осред-ненных в достаточно больших объемах, содержащих много однотипных армирующих элементов. Другой, несравненно более сложный, но и более информативный путь состоит в раздельном рассмотрении механических свойств каждой фазы с последующим теоретическим прогнозированием свойств всего композита в целом. При этом приходится рассматривать фактически еще одну дополнительную фазу зоны сопряжения основных фаз, например, матрицы с армирующими волокнами. Механизм повреждений, развивающихся на границах фаз, обычно весьма сложен и определяется помимо свойств основных компонентов гетерогенной системы еще рядом дополнительных факторов, таких как адгезия фаз, технологические и температурные местные напряжения, обычно возникающие вблизи границ, наличие дефектов и др. Границы фаз как зоны концентраций напряжений играют особенно важную роль в развитии много - и малоцикловых усталостных повреждений композитов. [21]
Для условий цементирования скважин в хемогенно-терриген-ных отложениях нгпболсе эффективны минерализованные термосолестойкие тампонажные растворы на оксидной основе ( нормальной плотности и облегченные) со значительным расширением, а также супероблегченные пеноцементные тампонажные растворы типа аэротам; разработаны основные принципы проектирования рациональных составов таких цементов для различных условий применения и промышленная технология их изготовления. Основные технологические свойства минерализованных тампо-нажных растворов могут быть значительно улучшены в результате оптимизации гранулометрического состава твердой фазы в процессе промышленного изготовления тампонажных смесей де-зинтеграторным способом и применения метода дисперсного армирования твердеющей системы. Промышленное применение таких растворов базируется на существующей технике и технологии цементирования скзажин и может осуществляться в любом регионе страны со сложными геолого-техническими условиями цементирования, обусловленными наличием в разрезе скважины многолетнемерзлых пород или хемогенно-терригенных отложений. [22]
Известные работы в этом направлении свидетельствуют о его эффективности и имеющихся резервах повышения ударной выносливости бетонов, что обусловливает необходимость в углублении представлений о природе статического и динамического упрочнения при дисперсном армировании, в количественном изучении влияния дисперсного армирования на повышение ударной выносливости фибробетонов. [23]
Известные работы в этом направлении свидетельствуют о его эффективности и имеющихся резервах повышения ударной выносливости бетонов, что обусловливает необходимость в углублении представлений о природе статического и динамического упрочнения при дисперсном армировании, в количественном изучении влияния дисперсного армирования на повышение ударной выносливости фибробетонов. [24]
Фибры повышают ударную вязкость бетона, уменьшают истираемость, повышают прочность при растяжении, препятствуют раскрытию трещин. Разрушение бетона происходит постепенно. Дисперсное армирование наиболее эффективно в мелкозернистых бетонах, в особых случаях эксплуатации, имеется опыт его применения для бетонирования оголо вков свай. [25]
Дисперсное армирование бетона повышает его трещиностойкость, прочность на растяжение, ударную вязкость, сопротивление истиранию. Эффективность применения волокон в бетоне зависит от их содержания. Дисперсное армирование приостанавливает развитие волосяных трещин лишь при расстоянии между отдельными волокнами не более 10 мм, поэтому применение в бетоне крупного заполнителя снижает эффективность подобного армирования. Стальные фибры вводят в бетонную смесь в количестве 1 - 2 5 % объема бетона ( 3 - 9 % по массе), что обычно составляет 70 - 200 кг на 1 м3 бетона. При этом повышаются прочность бетона на растяжение ( на 10 - 30 %), ударная прочность, износостойкость. [26]
Однако при абсолютной химической стойкости, сравнительно высокой прочности на сжатие, изгиб и растяжение, равной приблизительно прочности труб из асбестоцемента, стеклянные трубы хрупки и обладают очень низкой сопротивляемостью ударным нагрузкам. Трубы изготовляют незначительной длины, что усложняет монтаж трубопроводов. Дисперсное армирование стекломассы является, видимо, одним из направлений повышения качества труб, обеспечивающим условия для применения стеклянных труб в системах газоснабжения. [27]
Страницы: 1 2
www.ngpedia.ru
Основы дисперсного армирования
Использование дисперсно-армированных цементных композиций позволяет выпускать облегченные строительные конструкции с повышенной прочностью на изгиб и ударной прочностью. Кроме экономических соображений, выбор волокна обусловливается тем, какими, свойствами должна обладать композиция для удовлетворения заданным требованиям. Существуют многочисленные разновидности изделий из фиброцемента, которые находят разнообразное применение. Повышенная ударная прочность требуется преимущественно для контроля за процессом трещинообразования. Применение некоторых видов волокон позволяет получить экономию за счет сокращения размеров сечений. Если нагрузка приложена к телу представляющему собой матрицу с включенными в нее волокнами, то паток, очевидно, повышают его несущую способность. Нагрузка передается через матрицу к волокну при сдвиговой деформации в контактной зоне волокна и матрицы. Причем передача нагрузки; обусловливается различием между физическими характеристиками армирующих волокон […]
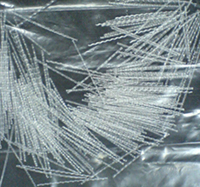
Роль волокон в цементных композитах
Использование дисперсно-армированных цементных композиций позволяет выпускать облегченные строительные конструкции с повышенной прочностью на изгиб и ударной прочностью. Кроме экономических соображений, выбор волокна обусловливается тем, какими, свойствами должна обладать композиция для удовлетворения заданным требованиям. Существуют многочисленные разновидности изделий из фиброцемента, которые находят разнообразное применение. Повышенная ударная прочность требуется преимущественно для контроля за процессом трещинообразования. Применение некоторых видов волокон позволяет получить экономию за счет сокращения размеров сечений.
Если нагрузка приложена к телу представляющему собой матрицу с включенными в нее волокнами, то паток, очевидно, повышают его несущую способность. Нагрузка передается через матрицу к волокну при сдвиговой деформации в контактной зоне волокна и матрицы. Причем передача нагрузки; обусловливается различием между физическими характеристиками армирующих волокон и матрицы, и прежде всего между значениями их модулей упругости. Частично замещают асбест в цементных настилах, бетонных трубах; ремонтные материалы. Выражения для расчета напряжения сдвига волокна относительно матрицы и для растягивающего напряжения волокна относительно матрицы можно получить, рассматривая равновесия сил, действующих на участок волокна. Различия в механических и геометрических характеристиках как волокон, так и матрицы, приводят к различным механизмам разрушения композита, например, к выдергиванию волокон из матрицы.
В цементных композитах волокна часто распределены прерывисто по матрице и непрерывно по всему образцу от одного конца до другого. Исследования показали, что непрерывные волокна в гидратированных цементных матрицах в противоположность прерывистым можно считать объединенными вместе только матрицей, которая почти совсем не переносит или совсем не передает на них нагрузки при ее нормальном приложении. Растягивающее напряжение волокна, в сущности, является постоянным по всей его длине.
Роль волокон в цементных композитах.
Волокна вводятся в хрупкую структуру цементной матрицы для повышения ударной прочности и вязкости разрушения композитов в результате торможения процесса трещинообразования и повышения прочности при растяжении и изгибе. Знание свойств волокон важно для проектирования. Для хорошего эффекта армирования необходима высокая прочность фибры при растяжении. Большое значение отношения модуля упругости фибры к модулю упругости матрицы облегчает передачу напряжения от матрицы к фибре. Волокна с большим значением деформации при разрушении придают композитам хорошую растяжимость. Проблем, возникающих при нарушении связи фибры в зоне контакта фибры и матрицы, можно избежать при более низком коэффициенте Пуассона. На практике большинство волокон получает поверхностные трещины при транспортировке, обработке, производстве, хранении и т. д.
Шлакопортландцементы.
КОРРОЗИЯ БЕТОНА В МОРСКОЙ ВОДЕ
Теории карбонизационной усадки бетона
УСАДКА ПРИ КАРБОНИЗАЦИИ
Механизм действия морозного разрушения бетона.
ВОЗДЕЙСТВИЕ МОРОЗА
НЕДОСТАТКИ ЦЕМЕНТОВ, СОДЕРЖАЩИХ MgO И СаО
БИОЛОГИЧЕСКАЯ КОРРОЗИЯ БЕТОНА
Способы предупреждения щелочной коррозии.
Кремнеземистые заполнители.
ЩЕЛОЧНАЯ КОРРОЗИЯ ЗАПОЛНИТЕЛЯ
Жаростойкий бетон.
Глиноземистый цемент содержит заметное количество алюмоферрита кальция.
ГЛИНОЗЕЛНИСТЫЙ ЦЕМЕНТ
ФОСФАТНЫЕ ЦЕМЕНТЫ
Стирол
СЕРНЫЙ БЕТОН
Повторное использование бетона
Портландцементный бетон
Справедливость законов смеси применительно к прочности пропитанного бетона
Раствор и бетон пропитанный серой
Техника полимеризации
Пропитанный полимером раствор и бетон
Армирование асбестовыми волокнами композитов на основе цемента
Свойства зоны контакта проволоки и цемента
Механические свойства дисперсно-армированных цементных композитов
Основы дисперсного армирования
Высокоподвижная бетонная смесь
Свежеприготовленная бетонная смесь
Затвердевший бетон
Литая бетонная смесь
Замедлители схватывания бетона
Микроструктурные аспекты
Оценка количества хлорида
Хлорид кальция и коррозия.
Хлорид кальция и свойства бетона.
Химические добавки в бетон
Сорбция воды и модуль упругости.
Явления сорбции и изменения длины: теоретическое рассмотрение
Бетон.
971 просмотров
moimozg.ru
Дисперсное армирование для получения высококачественного бетона Текст научной статьи по специальности «Строительство. Архитектура»
УДК 627.8
ДИСПЕРСНОЕ АРМИРОВАНИЕ ДЛЯ ПОЛУЧЕНИЯ ВЫСОКОКАЧЕСТВЕННОГО БЕТОНА
О.М. Смирнова, Р.В. Корпош
FIBER-REINFORCEMENT FOR PRODUCTION OF HIGH-PERFORMANCE CONCRETE
O.M. Smirnova, R.V. Korposh
Аннотация. Рассмотрена технология дисперсного армирования полипропиленовой микрофиброй для получения высококачественного бетона с использованием экспериментальных данных, методов сравнения и обобщения. Показано влияние способа введения микрофибры на оптимальный расход микрофибры, структуру бетона на различных уровнях (макроуровень, микроуровень) и на свойства затвердевшего бетона. Установлена зависимость прочности бетона на растяжение при изгибе от объемного содержания микрофибры при различных способах введения микрофибры. Для исследованных способов введения микрофибры установлены минимальные расходы микрофибры по объему.
Ключевые слова: высококачественный бетон; дисперсное армирование; микрофибра; способ введения; прочность на растяжение.
Abstract. Technology of polypropylene microfiber reinforcement for production a highperformance concrete using experimental data, methods of comparison and generalization are considered in the paper. The influence of the introduction way of microfiber on the optimal microfiber amount, on the concrete structure at different levels (macro-level, micro-level) as well as on the properties of hardened concrete are shown. Dependence of tensile in bending strength of concrete from the volume content of microfiber at various ways of microfiber introduction are stated. The minimum microfiber volume is established for the studied ways of microfiber introduction.
Key words: high-performance concrete; microfiber reinforcement; microfiber; ways of microfiber introduction; tensile in bending strength.
Введение
Требования к высококачественному бетону, который является конструкционным материалом, заключаются не только в высокой прочности. Как правило, бетонные смеси для получения высококачественного бетона имеют высокую подвижность (или растекаемость), а сам затвердевший бетон имеет высокие показатели технических свойств при низком расходе портландцемента на 1 МПа прочности [1-3]. Достижение таких показателей возможно за счет применения современных суперпластификаторов, дисперсного армирования, использования минеральных добавок природного и техногенного происхождения по тонкости помола, превышающих тонкость помола портландцемента.
В последние годы разрабатывается большое количество новых видов бетона: самоуплотняющиеся, высокопрочные, дисперсноармированные, реакционно-порошковые, легкие, архитектурные бетоны и др. Составы этих бетонов разрабатываются в рамках концепции высококачественного бетона, т.е. одним из критериев оценки бетона является низкий показатель удельного расхода портландцемента на 1 МПа прочности [4,5]. Обычно при подборе состава традиционного цементного бетона подбирается расход портландцемента на 1 куб.метр бетона. В высококачественном бетоне повышение его технических свойств, в том числе прочностных, получают не за счет увеличения расхода портландцемента [6-9]. Одним из способов является технология дисперсного армирования
микрофиброй. Это способствует изменению структуры бетона на различных уровнях: макроуровне и микроуровне.
Постановка задачи и методы исследования
Способ введения микрофибры влияет на структуру бетона и соответственно на его свойства. Увеличение расхода микрофибры и ее равномерное распределение, без образования комков, будет способствовать значительному повышению прочности на растяжение бетона. Эти мероприятия следует проводить на этапах выбора материалов, приготовления и укладки бетонной смеси. В связи с этим целью работы является исследование способа введения микрофибры на ее расход и распределение в структуре бетона.
Способ введения полипропиленовой микрофибры был исследован с помощью смесителя «Digi Mortar Mixer». Было выбрано 3 способа введения микрофибры. По первому способу микрофибра вводилась в сухие компоненты, затем все сухие компоненты перемешивались в сухом виде в течение 0,5 мин., затем вводилась вода затворения с суперпластификатором. По второму способу, в сухие компоненты вводилась вода затворения с суперпластификатором, затем микрофибра. По третьему способу, в сухие компоненты вводилась вода затворения в количестве 70% от общей массы воды, затем микрофибра, затем вода затворения в количестве 30% с суперпластификатором.
Обсуждение результатов
Определение оптимального расхода микрофибры является важной задачей при разработке состава высококачественного бетона. Понятно, что с увеличением расхода микрофибры прочность бетона на растяжение будет повышаться, однако, большой расход микрофибры приводит к ее плохому распределению в структуре бетона и резкому снижению удобоукладываемости бетонной смеси и прочностных характеристик. В связи с этим можно предположить, что каждому способу введения микрофибры соответствует ее оптимальный расход, выше которого микрофибра будет распределяться неравномерно.
Определение оптимального расхода микрофибры, учитывающее способ введения микрофибры и ее распределение в цементной матрице, может быть предложено при проектировании состава высококачественного бетона. Суть этого определения состоит в нахождении экспериментальным путем минимального процента дисперсного армирования. Известно, что микрофибра незначительно влияет на прочностные характеристики при расходе меньше минимального процента дисперсного армирования. При более высоких расходах микрофибры наблюдается повышение прочности на растяжение.
Растворная смесь с водо-цементным отношением, соответствующим водо-цементному отношению бетонной смеси, может быть выбрана в качестве исходной смеси для экспериментального определения оптимального расхода микрофибры. Минимальный процент армирования бетона микрофиброй определяется с использованием такой растворной смеси.
Образцы без микрофибры, а также с микрофиброй по трем способам введения микрофибры, были изготовлены. График зависимости «прочность на растяжение при изгибе - объемное содержание микрофибры (процент армирования)» был построен по результатам испытаний образцов-балочек. Положение точки, которой соответствует значение минимального процента армирования, определялось с графика. Прирост прочности на растяжение наблюдался при значениях превышающих минимальный процент армирования. В данном эксперименте растворная смесь с водо-цементным отношением, равным 0,3, была выбрана в качестве исходной смеси, подвижность смеси регулировалась суперпластификатором. Минимальный процент армирования бетона микрофиброй определялся с использованием такой растворной смеси. Зависимости «прочность на растяжение при изгибе - объемное содержание волокон (процент армирования)» для
http://vestnik-nauki.ru
различных способов введения микрофибры представлены на рисунке. Положение точки, которой соответствует значение минимального процента армирования, определяется с графика. Значительный прирост прочности на растяжение при изгибе наблюдается при значениях соответствующих минимальному проценту армирования, который для смеси с водо-цементным отношением, равным 0,3, составил 0,31%; 0,57% и 0,42% соответственно для 1-го, 2-го и 3-го способа введения микрофибры.
Как видно с рисунка, для каждого способа введения существует минимальное объемное содержание микрофибры, соответствующее значительному приросту прочности на растяжение при изгибе. С увеличением этого значения прирост прочности незначителен или практически отсутствует. Это можно объяснить неравномерным распределением микрофибры при данном способе ее введения и образованием комков на уровне макроструктуры.
0) S I 0)
я м а «S
£ I
i У
о £1 С
8 7,5 7 6,5 6 5,5 5 4,5 4
1-ый способ
2-ой способ ■ 3-ий пособ
0,1 0,2 0,3 0,4 0,5 0,6 0,7 Объемное содержание микрофибры, %
0
Рисунок - Зависимость прочности бетона на растяжение при изгибе от объемного содержания микрофибры при различных способах введения микрофибры
Эффективность дисперсного армирования полипропиленовой микрофиброй во многом зависит от взаимодействия микрофибры и цементного камня на границе раздела фаз. Прочность сцепления микрофибры и цементного камня определяет характер разрушения дисперсноармированного бетона. При всех исследованных расходах армирования в первую очередь разрушался цементный камень. Затем разрушение происходило в результате выдергивания полипропиленовой микрофибры из цементной матрицы после нарушения связи на границе раздела фаз и последующего разрыва полипропиленовой микрофибры при максимальных напряжениях. При этом дисперсноармированный бетон покрывался сетью микротрещин при расходе микрофибры, превышающем 0,6%.
Заключение
Рассмотрено дисперсное армирование полипропиленовой микрофиброй для повышения предела прочности на растяжение при изгибе бетона. Исследованы различные способы введения микрофибры в смесь. По первому способу микрофибра вводилась в сухие компоненты, затем все сухие компоненты перемешивались в сухом виде в течение 0,5 мин., затем вводилась вода затворения с суперпластификатором. По второму способу, в сухие компоненты вводилась вода затворения с суперпластификатором, затем микрофибра. По третьему способу, в сухие компоненты вводилась вода затворения в количестве 70% от общей массы воды, затем микрофибра, затем вода затворения в количестве 30% с суперпластификатором. Установлено, что значительный прирост прочности на растяжение при изгибе наблюдается при значениях соответствующих минимальному проценту
армирования, который для смеси с водо-цементным отношением, равным 0,3, составил 0,31%; 0,57% и 0,42% соответственно для 1-го, 2-го и 3-го способа введения микрофибры.
ЛИТЕРАТУРА
1. Петрова Т.М., Смирнова О.М., Фролов С.Т. Свойства пластифицированных композиций портландцемент-доменный шлак с учетом электроповерхностных явлений // Вестник гражданских инженеров. 2011. № 2. С. 118-123.
2. Смирнова О.М., Макаревич О.Е. Расход и дисперсность молотого известняка для самоуплотняющегося бетона // Цемент и его применение. 2014. № 4. С. 76-78.
3. Смирнова О.М. Высококачественные бетоны для предварительно напряженных железобетонных подрельсовых конструкций: автореферат дис. ... кандидата технических наук: 05.23.05 / Санкт-Петербургский государственный архитектурно-строительный университет. Санкт-Петербург, 2013.
4. Смирнова О.М., Макаревич О.Е. Выбор водоредуцирующих добавок и их расходов для высокопрочных бетонов сборных конструкций // Ресурсоэнергоэффективные технологии в строительном комплексе региона. 2014. № 4. С. 74-77.
5. Smirnova O. Obtaining the high-performance concrete for railway sleepers in Russia // Procedia Engineering 12. "Modern Building Materials, Structures and Techniques" 2017. С. 10391043.
6. Беленцов Ю.А., Смирнова О.М., Шаманина Д.Д. Самоуплотняющийся бетон с использованием наполнителя из молотого известняка / СТРОИТЕЛЬСТВО-2016. Материалы II Брянского международного инновационного форума. Брянск, 2016. С. 22-25.
7. Smirnova O.M. Сompatibility of portland cement and polycarboxylate-based superplasticizers in high-strength concrete for precast constructions // Инженерно-строительный журнал. 2016. № 6 (66). С. 12-22.
8. Смирнова О.М. Использование минерального микронаполнителя для повышения активности портландцемента // Строительные материалы. 2015. № 3. С. 30-33.
9. Смирнова О.М. Зависимость прочности бетона с добавками на поликарбоксилатной основе от свойств портландцемента после низкотемпературной тепловлажностной обработки // Известия высших учебных заведений. Строительство. 2012. № 9 (645). С. 20-27.
REFERENCES
1. Petrova T.M., Smirnova O.M., Frolov S.T. Svoystva plastifitsirovannyih kompozitsiy portlandtsement-domennyiy shlak s uchetom elektropoverhnostnyih yavleniy [Properties of plasticized compositions of Portland cement-blast furnace slag]. Vestnik grazhdanskih inzhenerov. 2011. No. 2, pp. 118-123.
2. Smirnova O.M., Makarevich O.E. Rashod i dispersnost molotogo izvestnyaka dlya samouplotnyayuschegosya betona [Consumption and dispersion of ground limestone for self-compacting concrete]. Tsement i egoprimenenie. 2014. No. 4, pp. 76-78.
3. Smirnova O.M. Vyisokokachestvennyie betonyi dlya predvaritelno napryazhennyih zhelezobetonnyih podrelsovyih konstruktsiy [High-performance concrete for prestressed concrete of rail structures: abstract of diss. dr.]. Sankt-Peterburg, 2013.
4. Smirnova O.M., Makarevich O.E. Vyibor vodoredutsiruyuschih dobavok i ih rashodov dlya vyisokoprochnyih betonov sbornyih konstruktsiy [The choice of water-reducing admixtures and their amount for precast concrete] / Resursoenergoeffektivnyie tehnologii v stroitelnom komplekse regiona. 2014. No. 4, pp. 74-77.
5. Smirnova O. Obtaining the high-performance concrete for railway sleepers in Russia. Procedia Engineering 12. "Modern Building Materials, Structures and Techniques", 2017, pp. 10391043.
6. Belentsov Yu.A., Smirnova O.M., Shamanina D.D. Samouplotnyayuschiysya beton s ispolzovaniem napolnitelya iz molotogo izvestnyaka [Self-compacting concrete with filler of ground limestone]. STROITELЬSTVO-2016. Materialyi IIBryanskogo mezhdunarodnogo innovatsionnogo foruma. Bryansk, 2016, pp. 22-25.
7. Smirnova O.M. Sompatibility of portland cement and polycarboxylate-based superplasticizers in high-strength concrete for precast constructions. Inzhenerno-stroitelnyiy zhurnal. 2016. No. 6 (66), pp. 12-22.
8. Smirnova O.M. Ispolzovanie mineralnogo mikronapolnitelya dlya povyisheniya aktivnostiportlandtsementa [The use of mineral filler to increase the activity of Portland cement]. Stroitelnyie materialyi. 2015. No. 3, pp. 30-33.
9. Smirnova O.M. Zavisimost prochnosti betona s dobavkami na polikarboksilatnoy osnove ot svoystv portlandtsementa posle nizkotemperaturnoy teplovlazhnostnoy obrabotki [The dependence of the concrete strength with polycarboxylate-based admixture on the Portland cement properties under low-temperature heat-steaming]. Izvestiya vyisshih uchebnyih zavedeniy. Stroitelstvo. 2012. No. 9 (645), pp. 20-27.
ИНФОРМАЦИЯ ОБ АВТОРАХ
Смирнова Ольга Михайловна Санкт-Петербургский горный университет, г. Санкт-Петербург, Россия, кандидат технических наук, доцент кафедры «Строительство горных предприятий и подземных сооружений», Строительный факультет E-mail: [email protected]
Smirnova Olga Mikhailovna Saint-Petersburg Mining University, Saint-Petersburg, Russia, PhD., Assoc.Prof. of Department of Constructing Mining Enterprises and Underground Structures, E-mail: [email protected]
Корпош Роман Викторович Санкт-Петербургский горный университет, г. Санкт-Петербург, Россия, студент кафедры «Строительство горных предприятий и подземных сооружений», Строительный факультет
E-mail: [email protected]
Korposh Roman Victorovich Saint-Petersburg Mining University, Saint-Petersburg, Russia, Student of Department of Constructing Mining Enterprises and Underground Structures, E-mail: [email protected]
Корреспондентский почтовый адрес и телефон для контактов с авторами статьи: 199106, Санкт-Петербург, Васильевский остров, 21 линия, д.2, Санкт-Петербургский горный университет, кафедра «Строительство горных предприятий и подземных сооружений»,
Смирновой О.М. Тел .+7(905)2826022
cyberleninka.ru
Модифицирование поверхности стальной фибры для дисперсного армирования бетона Текст научной статьи по специальности «Строительство. Архитектура»
/->
МОДИФИЦИРОВАНИЕ ПОВЕРХНОСТИ СТАЛЬНОЙ ФИБРЫ ДЛЯ ДИСПЕРСНОГО АРМИРОВАНИЯ БЕТОНА
MODIFICATION OF THE STEEL FIBERS SURFACE FOR DISPERSE REINFORCEMENT OF CONCRETE
УДК 691.328; 669.697
Н.П. Матвейко1* В.Г. Зарапин1, В.С Артимович2 m. Matveika1* V. Zarapin1, V. Artimovich3
1 Белорусский государственный экономический 1 Belarusian State Economic University университет 2 se «BeldorNIl»
2 ГП «БелдорНИИ»
РЕФЕРАТ
ФИБРОБЕТОН, СТАЛЬНАЯ ФИБРА, МОДИФИЦИРОВАНИЕ ПОВЕРХНОСТИ, АНКЕРОВКА, ЗАЩИТА ОТ КОРРОЗИИ
Цель работы - разработка состава композиции для модификации поверхности стальной фибры, используемой в сталефибробетоне, позволяющей усилить анкеровку фибры в бетоне и создать на ней антикоррозионный пассивирующий защитный слой.
Разработан новый состав модифицированной антикоррозионной композиции для обработки стальной фибры. Использование разработанной композиции дает возможность защемления стальной нити фибр в объеме бетона по всей длине за счет связывания ее поверхности с бетонной матрицей и минимизации возможности беспрепятственного растяжения фибры под действием нагрузок с одновременной защитой фибры от коррозии.
Обработка стальной фибры модифицированной антикоррозионной композицией может быть использована для получения стальных арматурных элементов с усиленными анкерующими свойствами. Обработка поверхности фибры модифицированной антикоррозионной композицией позволяет существенно (более чем на 60 %) повысить предел прочности дисперсно-армированного бетона с одновременной защитой фибры от коррозии, что позволит увеличить долговечность дисперсно-армированных бетонов. V_
ABSTRACT
FIBER CONCRETE, STEEL FIBER, SURFACE MODIFICATION, ANCHORING, CORROSION PROTECTION
The purpose is to develop composition for surface modification of steel fibers used for steel fiber concrete to strengthen the anchoring fibres in concrete and create it corrosion passivating protective layer.
A new composition of modified anticorrosion compositions is developed for processing of steel fibers. The use of the developed composition allows for steel filament fibers to volume concrete throughout its length by binding the surface with a concrete matrix and to minimize the possibility of unimpeded stretching of the fibers under the action of loads, while still protecting the fibers from corrosion.
Processing of steel fibers modified anticorrosive composition can be used to receive reinforcing steel elements with reinforced anchoring properties. Surface treatment of fiber modified anticorrosion composition can significantly (more than 60 %) increase the tensile strength of dispersion-reinforced concrete, while still protecting the fiber from corrosion, which enables to increase durability dispersion-reinforced concrete.
У
* E-mail: [email protected] (M. Matveika)
вестник витебского государственного технологического университета, 2017, № 1 (32)
Большинство строительных сооружений в настоящее время возводится с использованием бетонов. Для увеличения ударной прочности, сопротивления на разрыв, прочности при растяжении и изгибе используют вторичное армирование бетона. В конструкционном бетоне для этих целей применяют стальную арматуру, а в бетонных перекрытиях - металлическую сетку. Однако присутствие в цементных бетонах электролитов приводит к коррозии стальной арматуры, что обусловливает образование пустот, которые являются концентраторами напряжений, ведущими к снижению эксплуатационных свойств. Для улучшения коррозионных свойств конструкций, одного из условий обеспечения качества возводимых зданий и сооружений, применяют новые эффективные строительные материалы, в том числе бетоны, армированные при помощи фибры. Такой бетон (фибробетон) представляет собой композиционный материал, состоящий из цементной матрицы с равномерным или заданным распределением по ее объему ориентированных, но чаще хаотично расположенных волокон (фибр) различного происхождения. В качестве дисперсного армирующего материала (фибр) широко применяют различные волокна. Материалом таких волокон или фибр могут быть металлы, базальт, минеральные, искусственные и синтетические полимеры [1].
Использование фибры позволяет избежать недостатков, которые связаны с коррозией арматуры вследствие минимизации верхнего защитного слоя бетона, поскольку фибра армирует бетон дисперсно и насыщает его по всему объему. В настоящее время самым распространенным вариантом фибры для армированного дисперсным способом бетона является стальная фибра, которая производится различными мировыми производителями в достаточно больших объемах. Использование стальной фибры обусловлено в первую очередь таким свойством стали, как технологическая возможность изготовления фибры различного профиля, размера и состава. Кроме того, стальные фибры имеют более высокие прочностные характеристики по сравнению с фибрами из полимерных материалов или минеральных волокон. Наконец, стоимость стальной фибры и ее производства существенно ниже стоимости фибр из других
материалов [2].
На показатели прочности сталефибробетона существенно влияет качество анкеровки фибр в бетонной матрице. Способов улучшения анке-ровки фибры в бетоне существует достаточно много, большинство из которых защищено патентами. Например, существует способ получения стальных арматурных элементов (фибр) для дисперсного армирования бетона с улучшенными анкерующими свойствами, состоящий в изготовлении металлического волокна в виде плоского протяженного основания со сквозной перфорацией, снабженного анкерами из кристаллитов металла [3]. Предлагаются также фибры в виде отрезка проволоки с равномерно деформированными участками, имеющими выступы и впадины в форме волны в трехмерном измерении [4]. Известны фибры в виде проволочного тора эллипсоидного или сферического профиля с выпусками-анкерами в виде усов [5]. Однако такие фибры имеют некоторые недостатки. Во-первых, сложность изготовления стальных арматурных элементов вследствие их непростой конфигурации. Во-вторых, из-за развитости формы такие фибры склонны к комкованию и имеют высокую способность сцепляться между собой с образованием «ежей». Это препятствует их равномерному распределению в бетонной смеси, и, как следствие, приводит к формированию в дисперсно-армированном бетоне областей с повышенным и пониженным содержанием фибры, в результате чего фибробетон состоит из участков с различными физико-механическими характеристиками.
Недостатком стальных фибр, изготовленных, как правило, из низкоуглеродистой стали, является также их низкая коррозионная стойкость, что с учетом малых поперечных сечений стальных арматурных элементов, даже при небольшом коррозионном разрушении фибр в процессе эксплуатации сталефибробетона приводит к существенному снижению его механических свойств. Для повышения коррозионно-защит-ных свойств поверхности стальной волоконной фибры предлагается, например, проводить ее обработку раствором фосфата цинка [6]. Однако такая обработка позволяет повысить коррозионную стойкость стальной фибры, находящейся в индивидуальном (изолированном) состоянии, а
не в составе фибробетона. Тонкий механически непрочный защитный слой, сформированный обработкой фибры раствором фосфата цинка, разрушается и теряет свои защитные свойства в процессе эксплуатации фибробетона вследствие механических воздействий, приводящих к растяжению и сжатию фибры.
Цель работы - разработка состава композиции для модификации поверхности стальной фибры, используемой в сталефибробетоне, позволяющей усилить анкеровку фибры в бетоне и создать на ней антикоррозионный пассивирующий защитный слой. МЕТОДИКА ЭКСПЕРИМЕНТА
Поскольку задачей исследований является исключение или минимизация возможности беспрепятственного растяжения фибры под действием внешних нагрузок, применяя защемление стальной нити фибры по всей ее длине в объеме бетона вследствие повышения ее сцепляемости с бетонной матрицей при одновременной защите от коррозионного разрушения, то в качестве основы композиции для модифицирования фибр использовали антикоррозионные составы, разработанные нами ранее [7]. В эти антикоррозионные составы вводили добавки,способствующие повышению сцепляемости поверхности стальной фибры с бетоном. В качестве таких модифицирующих добавок использовали жидкое стекло, мелкодисперсный кварцевый песок и тонкодисперсную порошковую глину, которые
вводили в антикоррозионные композиции в количестве до 20 мас. %.
Исследование величины сцепляемости стальной поверхности, обработанной модифицированной антикоррозионной композицией, с бетоном проводили на образцах из стали Ст3 (ГОСТ 380-71). Стальные образцы в форме прутьев диаметром 4 мм, обрабатывали модифицированными различными добавками антикоррозионными композициями, анкеровали в смесь, приготовленную из портландцемента ПЦ 500 -Д 20 (ГОСТ 31108-03) и песка в соотношении 1:4 при водоцементном соотношении 1:2 на глубину анкеровки в 25-30 мм. Величину прочности сцепления поверхности стали с бетоном определяли статическим выдергиванием анкерованных в бетон прутьев после достижения бетоном возраста в 28 суток и рассчитывали сцепляемость (S, МПа) как отношение нагрузки, необходимой для выдергивания анкерованного прута, к площади поверхности анкеровки.
Дисперсное армирование бетона для исследований влияния обработки фибры на прочность последнего проводили с использованием стандартной стальной фибры, производимой РУП «Белорусский металлургический завод». Фибра выполнена в виде металлической нити с прямолинейным протяженным средним участком и разнесенными от середины сопряженными с ним двумя анкерами (рисунок 1). Такая конструкция позволяет фиксировать элементы фибр за
счет анкеровки в бетоне концевых участков.
Поскольку более 80 % длины фибры составляет прямая металлическая нить, основной целью было усилить сцепление с цементным камнем этого прямолинейного участка. Для этого поверхность фибры обрабатывали модифицированной антикоррозионной композицией, усиливающей анкеровку и ингибирующей коррозию. Фибру до закладки в бетонную смесь предварительно обезжиривали, а затем погружали в модифицированную антикоррозионную композицию, извлекали и высушили на воздухе. Образцы сталефибробетона готовили на основе цементного раствора, состоящего из 5,5 кг песка, 1,8 кг цемента марки ПЦ-500 и 0,9 кг воды (водоцементное соотношение В/Ц = 0,5), в который вводили 0,285 кг фибры. Образцы готовили в форме балочек размером 40*40*160 мм, которые после формования хранились 28 суток в камере нормального твердения, после чего их испытывали на растяжение при изгибе в соответствии с ГОСТ 310.4 - 81. РЕЗУЛЬТАТЫ И ИХ ОБСУЖДЕНИЕ
По результатам проведенных исследований было установлено, что наилучшей модифицирующей добавкой к антикоррозионным составам для усиления сцепляемости поверхности стальных фибр с бетоном является тонкодисперсная глина. Антикоррозионные композиции с жидким стеклом и кварцевым песком не позволяют добиться достаточного эффекта увеличения сцеп-ляемости стальной фибры с бетоном.
Глина является наиболее перспективным модифицирующим компонентом антикоррозионной композиции для улучшения адгезивных свойств поверхности стали по отношению к бетону, во-первых, потому что она достаточно химически устойчива и способна образовывать с антикоррозионной композицией коллоидные дисперсные системы. Во-вторых, глина широко распространена, поэтому доступна и имеет низкую стоимость.
Глина представляет собой мелкозернистую осадочную горную породу, пылевидную в сухом состоянии, состоящую преимущественно из оксида кремния (~ 47 мас. %) и оксида алюминия (~ 39 мас. %) с диаметром частиц менее 5 мкм [8]. Поскольку глина является одним из видов сырья при производстве цемента, ее применение
в качестве наполнителя и создание на ее основе модифицированной антикоррозионной композиции в дисперсно-коллоидном состоянии представляется вполне обоснованным.
Экспериментально установлено, что среди антикоррозионных составов [7], наибольшую эффективность для получения модифицирующей композиции показал состав, содержащий 24 г/дм3 фосфата цинка, и 98 г/дм3 орто-фосфорной кислоты (75 %). В качестве модифицирующей добавки к антикоррозионной композиции использовали глину белую (анапскую), представляющую собой тонкодисперсный порошок светло-серого цвета, содержащий не более 1,5-2 % влаги. Введение глины к антикоррозионному составу выполняли при непрерывном перемешивании раствора, что позволило равномерно распределить частицы глины во всем объеме и перевести их во взвешенное, достаточно устойчивое во времени состояние. Частичная седиментация суспензии глины происходит примерно через 6-8 часов, однако при кратковременном перемешивании или встряхивании композиция вновь приобретет однородность.
На рисунке 2 приведена зависимость сцепляемости (S, МПа) бетонной смеси с поверхностью стальных образцов, обработанных модифицированной антикоррозионной композицией, от содержания в ней глины, полученная по результатам статического выдергивания анкеро-ванных в бетон стальных прутьев.
С увеличением содержания добавки-глины - в композиции вначале имеет место возрастание сцепляемости, а потом ее снижение. Добавка мелкодисперсной глины, компоненты которой в большинстве своем по отношению к компонентам антикоррозионной композиции являются инертными веществами, скорее всего, приводит к формированию более прочной и устойчивой пленки с более высокой шероховатостью поверхности. Кроме того, поскольку глина входит в состав портландцемента, из которого изготавливают бетонные смеси, адгезионные силы между компонентами бетона и фосфатными частицами, содержащими аналогичные компоненты, выше, чем без них. В результате получается плавное распределение микрочастиц кремнезема и глинозема между защитным слоем и объемом бетона. Все эти факторы, очевидно, приводят к
увеличению сил сцепления бетонной смеси со стальными поверхностями, обработанными модифицированными глиной антикоррозионными композициями. При достаточно высоком содержании глины в композициях, вероятно, количество микрочастиц глины превышает некоторый предел, после которого сцепление частиц защитной пленки на поверхности стали становится меньше, и при больших количествах глины в составе композиций образуется менее прочный слой, что приводит к снижению сцепляемости поверхности стали с бетоном.
Таким образом, установлено, что для обработки стали наиболее эффективно использовать модифицированную добавлением глины до 10 мас. % антикоррозионную композицию, что позволяет увеличить сцепляемость поверхности стали с бетоном в 1,85 раза по сравнению со сцепляемостью необработанной поверхности. Интересно отметить, что обработка поверхности стали антикоррозионной композицией, содержащий 24 г/дм3 фосфата цинка, и 98 г/дм3 ортофосфорной кислоты (75 %), но не модифицированной глиной также увеличивает сцепляемость с бетоном, но лишь на 16 %.
В таблице 1 представлены результаты испытаний на растяжение при изгибе образцов бетона без наполнителя и с тремя видами наполнителей: из стальной фибры, не подвергнутой обработке; из стальной фибры, обработанной
антикоррозионной композицией; из стальной фибры, обработанной модифицированной антикоррозионной композицией.
Актуальность проведенных исследований обусловлена тем, что стальная фибра, применяемая для дисперсного армирования бетона, не имеет химической связи с бетоном, обладает низкой сцепляемостью, и не позволяет в достаточной степени образовывать прочную анкеров-ку. Стальная фибра обладает малым поперечным сечением и при эксплуатации подвергается коррозии и разрушению, что существенно снижает прочность дисперсно-армированных бетонов. Эти недостатки устраняются использованием нового разработанного состава модифицированной антикоррозионной композиции для обработки стальной фибры.
Научной новизной проведенных исследований является возможность защемления стальной нити фибр в объеме бетона по всей длине за счет связывания ее поверхности с бетонной матрицей и минимизации возможности беспрепятственного растяжения фибры под действием нагрузок с одновременной защитой фибры от коррозии.
Практическое значение результатов исследований заключается в том, что разработанная композиция для обработки стальной фибры для дисперсного армирования бетонов состоит из недорогих исходных компонентов, что позво-
Таблица 1 - Результаты определения предела прочности образцов бетона
№ обр. Тип фибры Дозировка фибры, масс. % Разрушающая нагрузка, Н Предел прочности, МПа
1 без фибры нет 2295,20 5,34
2 без фибры нет 2310,40 5,26
3 без фибры нет 2314,50 5,24
4 фибра без обработки 0,0285 3198,90 7,24
5 фибра без обработки 0,0285 2681,94 6,07
6 фибра без обработки 0,0285 3085,72 7,00
7 фибра,обработанная антикоррозионной композицией 0,0285 3008,47 6,97
8 фибра,обработанная антикоррозионной композицией 0,0285 2868,79 6,48
9 фибра, обработанная антикоррозионной композицией 0,0285 2845,09 6,36
10 фибра, обработанная модифицированной антикоррозионной композицией 0,0285 4824,11 11,20
11 фибра,обработанная модифицированной антикоррозионной композицией 0,0285 4139,26 9,61
12 фибра,обработанная модифицированной антикоррозионной композицией 0,0285 5551,65 12,00
ляет минимизировать денежные затраты на ее производство. Результаты работы могут быть внедрены в практику обработки стальной фибры для дисперсного армирования бетонов при производстве изделий и сооружений из стале-фибробетона в гражданском и промышленном строительстве, дорожном строительстве, мостостроении. ВЫВОДЫ
По результатам проведенных экспериментальных исследовательских работ установлено, что обработка стальной фибры модифициро-
ванной глиной антикоррозионной композицией может быть использована для получения стальных арматурных элементов с усиленными анке-рующими свойствами. Обработка поверхности фибры модифицированной глиной антикоррозионной композицией позволяет существенно (более чем на 60 %) повысить предел прочности дисперсно-армированного бетона с одновременной защитой фибры от коррозии, что позволит увеличить долговечности дисперсно-армированных бетонов.
СПИСОК ИСПОЛЬЗОВАННЫХ ИСТОЧНИКОВ
REFERENCES
1. Войлоков, И.А. (2007), Армирование фиброй как средство улучшения коррозионной стойкости бетона. Инфострой, 2007, № 3 (33), С. 4244.
2. Савченко, В. Сталефибробетон - новый конструкционный материал (2013), режим доступа: http://aLLby.tv/articLe/2167/ staLefibrobeton-novyiy-konstruktsionnyiy-materiaL (дата доступа: 20.01.2017).
3. Ахметшин, М.Р., Ахметшин, Р.Р., Ласковский, С.И., Подольский, В.А., Ткаченко, В.А., Штей-нерт, В.А. (2006), Металлическое волокно В.А. Шейнерта. Патент РФ № 2278180, МПК С 22 С 49/14, опубл. 20.06.2006.
4. Шеметов, Г.В., Аксанов, Р.М., Камалутдинов, И.М., Камалутдинов, М.К. (2011), Арматурный элемент для дисперсного армирования бетона. Патент РФ № 2433227, МПК Е 04 С 5/00, опубл. 10.11.2011.
5. Трофимов, В.И., Данилова, О.Г., Лопаков, Р.И., Соколов, Э.В. (2013), Арматурный элемент для дисперсного армирования бетона. Патент РФ № 2490406, МПК Е 04 С 5/03, опубл.
20.08.2013.
6. Son, M. (2014), Corrosion protection method of steeL fibers. Patent CN103787603 A, C04B 14/48, Suzhou Institute of TechnoLogy, China, pubL.
14.05.2014.
1. Voilokov, I.A. (2007), Reinforcement fiber reinforcement as a means of improving the corrosion resistance of concrete [Armirovanie fibroj kak sredstvo uluchshenija korrozionnoj stoikosti betona], Infostroj - Infostroy, 2007, № 3 (33), P. 42-44.
2. Savchenko, V. Stalefibrobeton - novyj konstruktsyonnyj material [Steel fiber reinforced concrete - a new construction material] (2013) [Electronic resource]. Access: http:// aLLby.tv/articLe/2167/staLefibrobeton-novyiy-konstruktsionnyiy-materiaL. Access Date: 20.01.2017.
3. Ahmetshin, M.R., Ahmetshin, R.R., Laskovskij, S.I., PodoLskij, V.A., Tkachenko, V.A., Shteinert, V.A. (2006), Metallicheskoe volokno V.A. Shteinerta [MetaLLic fiber V.A. Sheinart], Patent RF № 2278180, MPK C 22 C 49/14, pubL. 20.06.2006.
4. Shemetov, G.V., Aksanov, R.M., KaLamutdinov, I.M., KaLamutdinov, M.K. (2011), Armaturnyj element dlja dispersnogo armirovanija betona [Reinforcing eLement for dispersed reinforcement of concrete], Patent RF № 2433227, MPK E 04 C 5/00, pubL. 10.11.2011.
5. Trofimov, V.I., DaniLova, O.G., Lopakov, R.I., SokoLov, E.V. (2013), Armaturnyj element dlja dispersnogo armirovanija betona [Reinforcing eLement for dispersed reinforcement of concrete], Patent RF № 2490406, MPK E 04 C 5/03, pubL. 20.08.2013.
7. Матвейко, Н.П., Зарапин, В.Г., Бусел, Е.А. (2012), Антикоррозионная композиция для защиты арматуры и закладных деталей железобетона. ВестникВГТУ, 2012, Вып. 23, С. 113-119.
6. Son, M. (2014), Corrosion protection method of steeL fibers. Patent CN 103787603 A, C04B 14/48, Suzhou Institute of TechnoLogy, China, pubL. 14.05.2014.
8. Ceramic portaL.ru (2013), режим доступа: http: /ceramicportaL.ru/ articles/ keramicheskye_ massy. htm (дата доступа: 16.01.2017).
7. Matveiko, N.P., Zarapin, V.G., BuseL, E.A. (2012), Anticorrosive composition for protection of reinforcement and embedded parts of reinforced concrete [Antikorrozionnaja kompozicija dLja zaschity armatury i zakLadnyh
detalej zheLezobetona], Vestnik VGTU - Vestnik VSTU, 2012, Edit. 23, P. 113-119.
8. Ceramic portal.ru (2013) [Electronic resource]. Access: http: /ceramicportal.ru/ arti-cles/ keramicheskye_massy.htm. Access Date: 16.01.2017.
Статья поступила в редакцию 21. 02. 2017г.
178
cyberleninka.ru
Влияние дисперсного армирования на деформационно-прочностные свойства бетона Текст научной статьи по специальности «Строительство. Архитектура»
УДК 691.620.17: 691.327
МОСКОВСКИЙ С. В. НОСКОВ А. С. РУДНОВ В. С. АЛЕХИН В. Н.
Влияние дисперсного армирования на деформационно-прочностные свойства бетона
Одним из вариантов повышения надежности и увеличения сроков эксплуатации железобетонных конструкций может быть армирование всего объема бетона с помощью различных видов фибры. В статье представлены результаты комплексных исследований по изучению влияния параметров дисперсного армирования (длина волокон и вид фибры, дозировка по объему) и материала волокон фибры на прочность дисперсно-армированного бетона на растяжение при изгибе, дана оценка эффективности такого метода и возможность учета при расчете строительных конструкций.
Ключевые слова: фибробетон, дисперсное армирование, волокна фибры, прочностные и деформационные свойства бетона.
MOSKOVSKY S. V., NOSKOV A. S, RUDNOV V. S., ALECHIN V. N.
THE EFFECT OF PARTICULATE REINFORCEMENT ON THE DEFORMATION-STRENGTH PROPERTIES OF CONCRETE
One of the options to improve the reliability and increase the service life of concrete structures can be a reinforcement of the total volume of concrete using different fiber types. The article presents the results of complex researches on studying of influence of parameters of the dispersed reinforcement (fibre length and type of fiber, dosage by volume) and the material of the fibers of fibers on the strength fiber concrete tensile bending, the estimation efficiency and the possibility of taking into account in the calculation of building structures.
Keywords: thefiberconcrete, dispersed reinforcement, fibers fibers, the strength and deformation properties of concrete.
Использование традиционных методов армирования железобетона стальными плоскими или объемными каркасами приводит к неоднородности структуры, образованию пустот в бетоне, ухудшению деформационных характеристик конструкций. Равномерное распределенное армирование всего объема бетона исключает недостатки неармированных бетонов (низкая прочность на изгиб и усадочное трещинообра-зование при твердении и эксплуатации конструкций) и может существенно увеличить срок эксплуатации железобетонных конструкций.
Фибробетоном называют вид бетона при наличии в нем равномерно (дисперсно)
распределенной по всему телу искусственного камня микроарматуры (фибры) [1, 2, 7]. В начале XX в. российский инженер В. П. Некрасов впервые в мире предложил дисперсно-армированный бетон и провел исследования его строительных характеристик [5]. В качестве микроарматуры им были использованы отрезки проволоки малых диаметров. Микроармирование может быть применено во всех видах бетонов: тяжелый, ячеистый, бетон на легких заполнителях и др.
Как любой другой конструкционный материал, фибробетон имеет две основные группы качественных характеристик: прочностные и деформационные. Важнейшая характери-
стика (предел прочности на растяжение) является не только прямой, но и косвенной, свидетельствующей о сопротивляемости материала другим видам силового и структурного воздействий [3, 7]. По сравнению с бетоном без дисперсного армирования, фибробетон отличается высокой прочностью при различных видах воздействий: растяжение, срез, трещиностойкость — и характеризуется вязкостью разрушения. Прочностные свойства фибробетонов исследуются довольно давно, и они достаточно хорошо изучены российскими и зарубежными специалистами [6, 8, 10, 11]. Менее изучены деформационные параметры: износостойкость, коррозионная стойкость, трещиностойкость, морозостойкость, водонепроницаемость и др.
Фибробетон как композиционный материал характеризуется однородной более пластичной в сравнении с бетоном без дисперсного армирования структурой, для которой характерны высокая прочность на растяжение и изгиб, увеличенная трещиностойкость и вязкость разрушения. Эти конструкционные преимущества позволяют повысить долговечность строительных конструкций, уменьшить негативное влияние на них агрессивных факторов окружающей среды, сократить себестоимость железобетона за счет снижения доли стальной арматуры без изменения прочностных показателей [4, 9]. При этом конструкции могут иметь геометрическую форму любой сложности.
Положительное влияние дисперсного армирования бетона начинает сказываться после достижения объемной концентрации фибры, обусловливающей начальную объемно-пространственную связность фиброструктуры [6, 9]. Можно выделить два этапа механизма воздействия на структуру бетона и его физико-механические характеристики: ♦ на стадии структурообразования
фибра при пластической усадке
способствует перераспределению напряжений усадки от наиболее загруженных зон на весь объем бетона;
♦ при нагружении в процессе эксплуатации конструкций волокна фибры замедляют рост трещин, равномерно распределяют концентрации и снижают напряжения в местах макродефектов, контактной зоны разных компонентов бетона и точек приложения усилий.
Теории изменения деформаций ползучести и усадки на сегодняшний день следующие [1, 4, 10]:
♦ снижение деформаций усадки в фибробетоне достигается за счет распределенного взаимодействия волокон фибры с цементным камнем;
♦ в композитном материале с идеальным равномерным расположением фибры (фибробетон представлен участком с фиброй, окруженной тонким слоем цементного камня) ползучесть бетонной матрицы ограничивается поверхностным касательным напряжением между матрицей и фиброй за счет возникающих сил адгезии материалов.
В настоящее время проведено большое количество экспериментальных исследований для определенных производственных условий и видов бетона (ячеистый, тяжелый для транспортного строительства и т. п.). При этом отсутствует научно-теоретическая основа, объясняющая зависимости свойств фибробетона от дозировки и вида волокон фибры. Для прогнозирования возможных положительных эффектов необходимо провести исследование взаимодействия волокон дисперсного армирования с растворной матрицей, взаимосвязи характеристик различных видов бетона с целью изменения / корректировки прочностных и эксплуатационных характеристик при расчете конструкций. Для рас-
ширения области применения фибры при изготовлении железобетонных конструкций необходимо систематизировать накопленный производственный и научно-экспериментальный опыт, что позволит обосновать ее применение и задавать деформационные свойства конструкций из фибробетона. Для расширения областей расчета и применения дисперсно-армированных конструкций необходимо теоретическое обобщение и систематизация зависимостей между технологическими параметрами (свойства исходных материалов, состав и процесс изготовления изделий), формированием структуры и деформативно-прочностными характеристиками фибробетонов.
От свойств материала волокон фибры зависит область применения фибробетона и его характеристики. Волокна фибры могут быть нейлоновые, акриловые, стеклянные, стальные, полиэфирные, базальтовые, полипропиленовые, хлопковые и из других материалов (Таблица 1). В настоящее время за рубежом используют три основных вида дисперсной микроарматуры: волокна (фибры) в виде коротких отрезков тонкой стальной проволоки, стеклянные и полипропиленовые волокна. В Российской Федерации все более широкое применение находит фиброволокно на основе базальта. Различие свойств материалов дисперсного армирования обусловливает необходимость дифференцированного подхода к их применению в качестве арматуры [3, 7, 11].
Эффективность применения фибры кроме характеристик материала (временным сопротивлением растяжению ^ у, модулем упругости Е5 у , силой адгезии микроарматуры и бетонной матрицы) определяется свойствами самой дисперсной арматуры: геометрией (диаметр <1^, длина ¡^), формой сечения, конфигурацией (шероховатость поверхности и наличие анкеров у стальной арматуры). Физико-механические характе-
Таблица 1. Технические характеристики различных волокон фибры
Показатель Базальтовая фибра Полипропиленовая фибра Стекловолокон-ная фибра Стальная (металлическая) фибра
Материал Базальтовое волокно Полипропилен Стекловолокно Проволока из углеродистой стали
Диаметр волокна 13-17 мкм 10-25 мкм 13-15 мкм 0,5-1,2 мм
Длина волокна 3,2-15,7 мм 6-18 мм 4,5-18 мм 30-50 мм
Температура плавления, °С 1 450 160 860 1 550
Стойкость к щелочам и коррозии Высокая Низкая Низкая, у щелочестой-кого — средняя Средняя
Д.шнн фибры, МП
• доЗмм * де>5 мм «до 10 мм «до 15мм • до20 мм
Иллюстрация 1. Зависимость прочности при изгибе бетона с различной максимальной крупностью заполнителей от длины волокна базальтовой фибры
я 7,5 С
| 7 н
а: 6,5 6 5,5 5 4,5 4
к
1 ----- 4 1
А к ^^^
4 5 6
Объемная дозировка, %
• 2 мм • 8 мм 20 мм
Иллюстрация 2. Влияние объемной дозировки базальтовой фибры на прочность бетона при изгибе
Иллюстрация 3. Влияние расхода цемента на относительную прочность при изгибе
Таблица 2. Физико-механические характеристики волокон фибры
№ п/п Наименование Плотность, кг/ м3 Модуль упругости, МПа Я разрыва, МПа Относительное удлинение, % Прочность адгезии волокон с цементной матрицей, МПа
1 Цементная матрица 1800-2100 (2-2,5) • 104 3-5 0,01-0,03 —
2 Стальная фибра 7 800 2 • 105 540-580 15-18 4-6
3 Стекловолокно 2 400 «104 800-1200 2,5-3,5 6-9
4 Полипропиленовое волокно 900 (4-6) • 103 150-200 10-20 1-3
5 Грубое базальтовое волокно 2 600 «105 450-600 2-3 5-7
ристики разных видов волокон фибры приведены в Таблице 2 [7, 9].
Работами ряда исследователей [8, 9] установлено, что для получения высокопрочных композиций необходимо выполнение следующих условий:
♦ значительная часть прочности волокон должна сохраняться в технологическом процессе;
♦ необходимо высокое сцепление волокна с растворной матрицей и наиболее плотное их соприкосновение без защемленного воздуха в зоне контакта;
♦ оптимальное наиболее равномерное распределение волокон по всему объему матрицы при одновременном исключении непосредственного соприкосновения их друг с другом;
♦ материалы волокон должны обладать химической инертностью по отношению к цементной матрице;
♦ более высокий модуль упругости по сравнению с матрицей.
Более всего востребовано повышение прочности на изгиб распространенного конструкционного материала — тяжелого бетона, что возможно применением наиболее распространенных в РФ видов фиброволокна: стального, полипропиленового и базальтового. Однако для расчета несущей способности конструкции необходимо знать зависимости прочности при изгибе от параметров армирования. Комплексные исследовательские работы по созданию многофакторной математической модели фибробетона проводит коллектив авторов в Строительном институте УрФУ (Екатеринбург). Работа ведется по следующим направлениям:
♦ изучение макроструктуры дисперсно-армированного бетона: расположение, равномерность распределения, влияние фибры на окружающую структуру бетона;
♦ взаимодействие фибры и бетона, проявляющееся в прочностных характеристиках получаемой композиции;
♦ учет дисперсного армирования при проектировании прочностных и деформационных характеристик конструкций и прогнозировании внутренних напряжений, возникающих под действием эксплуатационных нагрузок.
В лабораторных экспериментах использовали несколько видов дисперсного армирования (характеристики приведены в Таблице 2), в качестве вяжущего — портландцемент класса ЦЕМ 42,5, мелкого заполнителя — мытый кварцевый песок фракции 0,3153,0 мм, крупного — мытый гранитный кубовидный щебень фракций 3-5, 3-10, 3-15 и 3-20 мм. Компоненты фибробетона (вяжущее, заполнители и дисперсная арматура) перемешивали в смесителях принудительного действия в два этапа: в сухом виде не менее 3 минут,
после добавления воды — не менее 3 минут. Такой режим позволяет пучкам волокон качественно расщепляться на отдельные единицы. Из дисперсно-армированного бетона изготавливали образцы размером 70 х 70 х 280 мм, на которых после твердения в нормальных условиях в течение 28 суток определяли предел прочности на растяжение при изгибе.
На первоначальном этапе исследований стояла цель выявить области наибольшей эффективности дисперсного армирования по величине абсолютной Визг (или относительной АВизг) прочности бетона на растяжение при изгибе. За относительную прочность бетона на растяжение при изгибе принимали изменение прочности бетона, армированного фиброй (В^)' отнесенное к прочности без фибры (Визг), рассчитываемое по формуле
ДВзг = Взг ~ Визг • 100%.
Визг
В реальных условиях прочностную модель бетонного композита строительной конструкции можно описать многофакторными параметрами. Для построения эмпирических и математических зависимостей по результатам проведенных экспериментов варьировали по два исходных параметра, оставляя остальные неизменными. Влияние на прочность бетона при изгибе волокон базальтовой фибры разной длины при различной максимальной крупности заполнителей изучали при объемной дозировке фибры 0,5 % и содержании цемента 300 кг в 1 м3 бетона (Иллюстрация 1).
По результатам приведенных экспериментов сделаны выводы о том, что при существенном увеличении длины волокон фибры заполнителя большей крупности происходит ухудшение структуры бетона и снижение прочностных показателей. Необходимая длина волокон фибры для получения наибольшей прочности при изгибе должна определяться максимальной крупностью заполнителя бетона, например, для мелкозернистого бетона — 2-6 мм, для крупнозернистого — 12-20 мм.
Экспериментально определяли и необходимую объемную дозировку базальтовой фибры разной длины для максимального повышения прочности на изгиб при содержании цемента 300 кг в 1 м3 бетона с максимальной крупностью заполнителя 15 мм (Иллюстрация 2).
В результате исследований установили, что оптимальная (дающая наибольший прирост прочности на изгиб) объемная дозировка фибры определяется ее длиной и варьируется в пределах от 3 % (для фибры длиной 20 мм) до 5 %% (длиной 2 мм). При превышении оптимальной объемной дозировки волокон прочностные характеристики бетона остаются практически неизменными.
Содержание цемента также является важной характеристикой, зависящей от материала волокон, что ис-
следовали при объемной дозировке волокон стальной, полипропиленовой или базальтовой фибры длиной 20 мм в количестве 3 % (Иллюстрация 3).
В результате установили, что для эффективной работы жесткая малоизгибаемая фибра требует большего содержания вяжущего (портландцемента), что объясняется необходимостью обеспечения контакта волокон с композитом.
В настоящее время эксперименты проводят при различных постоянных параметрах с целью охвата всех возможных сочетаний исходных условий. На следующем этапе исследований будут определены другие деформационные и прочностные характеристики дисперсно-армированных бетонов, необходимых с целью расчета модели конструкции. После систематизации полученных эмпирических данных будут рассчитаны зависимости прочностных свойств дисперсно-армированного бетона от всего комплекса исходных параметров для использования в математической модели для расчета прочностных характеристик этого вида бетона.
Заключение
1 В Строительном институте Уральского федерального университета имени первого Президента России Б. Н. Ельцина коллектив авторов проводит эксперименты по изучению зависимостей прочностных характеристик тяжелого фибробетона от свойств волокон дисперсной арматуры (базальтовой, полипропиленовой, стальной) и параметров армирования (объемная дозировка, содержание вяжущего в композите).
2 Исследования тяжелого фибробетона с базальтовой фиброй показали, что дисперсное армирование повышает прочность на растяжение при изгибе до 74 %, максимальная прочность достигается при объемной дозировке волокон в количестве 5 % вне зависимости от ее длины.
3 Использование металлической или базальтовой фибры с длиной, превышающей максимальную крупность заполнителя с дозировкой по объему от 3 до 5 % и содержании цемента более 400 кг / м3, позволяет получить прочность дисперсно-армированного бетона на растяжение при изгибе до 19,5 МПа, что в 3 раза больше по сравнению с бетоном без микроарматуры.
Список использованной литературы
1 Арончик В. Б. Исследование работы армирующего волокна в фибробетоне : автореф. дис. ... канд. техн. наук. Рига, 1983. 22 с.
2 Баженов Ю. М. Технология бетона. М. : АСВ, 2003. 500 с.
3 Клюев С. В. Экспериментальные исследования фиб-робетонных конструкций // Строительная механика инженерных конструкций и сооружений. 2011. № 4. С. 71-74.
4 Моргун Л. В. К вопросу о закономерностях формирования структуры бетонов при дисперсном армировании их волокнами // Известия ВУЗов. Строительство. 2003. № 8. С. 56-59.
5 Некрасов В. П. Новейшие приемы и задачи железобетонной техники: система свободных связей // Цемент, его производные и применение: XII съезд русских цементных техников. СПб., 1909. С. 294-348.
6 Пухаренко Ю. В. Принцип формирования структуры и прогнозирование прочности фибробетонов // Строительные материалы, оборудование, технологии XXI века. 2004. № 10. С. 47-50.
7 Рабинович Ф. Н. Композиты на основе дисперсно-армированных бетонов // Вопросы теории и проектирования, технологии, конструкции. М. : АСВ, 2004. 560 с.
8 Рыбасов В. П. К оценке прочности фибробетона // Фибробетон и его применение в строительстве : сб. науч. тр. М. : НИИЖБ, 1979. С. 125-130.
9 Талантова К. В. Основы создания сталефибробетон-ных конструкций с заданными свойствами // Бетон и железобетон. 2003. № 5. С. 4-8.
10 Brandt A. M. Cement-Based Composites : Materials, Mechanical Properties and Performance. London : Spon Press, 2009. 544 p.
11 Saje D., Bandelj B., Sustersic J. et al. Shrinkage and creep of steel fiber reinforced normal strength concrete // Journal of testing and evaluation. 2013. Vol. 41. № 6. P. 1-11.
cyberleninka.ru