Дефекты сварного шва: классификация и способы устранения. Что называют трещиной
Какая сталь обыкновенного качества относится к кипящей? — КиберПедия
БИЛЕТ 1
Какая сталь обыкновенного качества относится к кипящей?
А)Сталь не полностью раскисленная марганцем при выплавке, и содержащая не более 0,05% кремния.
Б) Содержащая кремния от 0,05 до 0,17%.
В) Содержащая более 10 мл. водорода на 100 г. металла.
Какая сталь обыкновенного качества относится к спокойной?
А) Сталь, полностью раскисленная при выплавке и содержащая 0,15-0,3% кремния.
Б) Содержащая не менее 0,3 % кремния и 1 % марганца.
В) Содержащая менее 0,5 мл. водорода на 100 г. металла.
Какая сталь обыкновенного качества относится к полуспокойной?
А) Сталь, раскисленная при выплавке только марганцем и содержащая не более 0,05% кремния.
Б) Сталь, не полностью раскисленная при выплавке только марганцем и кремнием и содержащая 0,05 - 0,15% кремния и до 1% марганца.
К какому классу сталей относятся сварочные проволоки Св-08, Св08А, Св-08ГА, Св-10ГА?
А) Низкоуглеродистому.
Б) Легированному.
В) Высоколегированному.
Что такое легированные стали?
А) Содержащие один или несколько элементов в определенных концентрациях, которые введены в них с целью придания заданных физико-химических и механических свойств.
Б) Обладающие определенными физико-химическими свойствами за счет снижения содержания углерода, серы, фосфора или термической обработки.
В) Обладающие определенными физико-химическими свойствами после специальной термомеханической обработки.
БИЛЕТ 2
Какой свариваемостью обладают низкоуглеродистые стали?
А) Хорошей.
Б) Удовлетворительной.
В) Плохой.
Что обозначают буквы и цифры в маркировке низколегированных сталей?
А) Клейма заводов-изготовителей.
Б) Обозначения номера плавки и партии металла.
В) Обозначение химических элементов и их процентный состав.
Какие из перечисленных сталей относятся к углеродистым?
А) Ст3сп, сталь10, сталь 15, сталь 18кп.
Б) 09Г2С, 17Г1С, 09Г2ФБ.
В) 08Х18Н9, 10Х2М, 15ХМ.
Какой буквой русского алфавита обозначают углерод и никель в маркировке легированных сталей?
А) Углерод «У» ;никель «Н».
Б) Углерод — «С»; никель — «Л».
В) Углерод не обозначают буквой; никель — «Н».
Какие изменения свойств происходят при закалке малоуглеродистых сталей?
А) Пластичность увеличивается, прочностные характеристики не меняются.
Б) Возрастают прочностные характеристики, пластичность уменьшается.
В) Возрастает и прочность, и пластичность.
БИЛЕТ 3
Какие основные характеристики приняты для оценки механических свойств металлов?
А) Временное сопротивление разрыву, предел текучести, относительное удлинение и сужение, твердость, ударная вязкость.
Б) Жаропрочность, жаростойкость и хладостойкость металла.
В) Твердость, сопротивление изгибу и количество циклов ударного нагружения до разрушения металла.
Для чего в сталь вводятся легирующие элементы?
А) Для придания стали специальных свойств.
Б) Для улучшения свариваемости стали.
В) Для снижения содержания вредных примесей (серы и фосфора) в стали.
Укажите, чем отличается Ст3кп от Ст3сп?
А) Содержанием углерода.
Б) Содержанием кремния.
В) Содержанием вредных примесей S и P и газов.
4. Для чего производится предварительный и сопутствующий подогрев?
А) Для снижения количества дефектов в сварном шве и ЗТВ.
Б) Для выравнивания неравномерности нагрева при сварке, снижения скорости охлаждения и уменьшения вероятности появления холодных трещин.
В) Для снижения содержания водорода в металле шва.
Какие характеристики можно определить при испытаниях образцов металла на растяжение?
А) Предел текучести, предел прочности.
Б) Угол загиба.
В) Предел текучести, предел прочности, относительные удлинение и поперечное сужение.
БИЛЕТ 4
Какая характеристика определяется при статическом изгибе?
А) Угол загиба.
Б) Ударная вязкость при изгибе.
В) Предел прочности при изгибе.
2. Какие характеристики металла определяются при испытаниях на изгиб (плоских образцов) и сплющивание (труб)?
А) Прочность.
Б) Пластичность.
В) Прочность и пластичность.
Какие характеристики определяют при ударном изгибе?
А) Предел прочности при ударном изгибе.
Б) Ударную вязкость.
В) Относительное удлинение при ударном изгибе.
БИЛЕТ 5
Как влияет неравномерность нагрева при сварке на величину деформации основного металла?
А) Увеличивает величину деформации.
Б) Не влияет на величину деформации.
В) Уменьшает величину деформации.
БИЛЕТ 6
БИЛЕТ 7
1.Что обозначают цифры возле букв на чертеже с указанием сварного шва?
А) Порядковый номер шва по ГОСТ (ОСТ).
Б) Метод и способ сварки.
В) Методы и объем контроля.
БИЛЕТ 8
Что называют включением?
А) Обобщенное наименование пор, шлаковых и вольфрамовых включений.
Б) Неметаллическая несплошность.
В) Скопление нескольких пор.
БИЛЕТ 9
Что называют трещиной?
А) Дефект сварного соединения в виде разрыва металла в сварном шве и/или прилегающих к нему зонах.
Б) Нарушение сплошности металла.
В) Недопустимое отклонение от требований Правил контроля.
Что называют прожогом?
А) Цилиндрическое углубление в сварном шве.
Б) Сквозное отверстие в сварном шве.
В) Воронкообразное углубление в сварном шве.
Что такое пора?
А) Дефект сварного шва в виде замкнутой полости, заполненной инородным металлом.
Б) Дефект сварного шва в виде полости сферической формы, заполненной шлаком.
В) Дефект сварного шва в виде замкнутой полости, заполненной газом.
БИЛЕТ 10
Что такое подрез?
А) Углубление по линии сплавления шва с основным металлом.
Б) Острые конусообразные углубления на границе поверхности шва с предыдущим валиком шва или основным материалом.
В) Острые конусообразные углубления на границе поверхности сварного шва с основным материалом.
Что такое «непровар»?
А) Дефект в виде отсутствия сплавления между металлом шва и основным металлом по кромке разделки.
Б) Дефект в виде несплавления в сварном соединении вследствие неполного расплавления кромок или поверхностей ранее выполненных валиков сварного шва.
В) Дефект в виде несплавления в сварном соединении вследствие неполного расплавления кромок или поверхностей ранее выполненных валиков сварных швов.
4. Как необходимо произвести заварку удаленного дефектного участка шва, если сварка производилась с предварительным подогревом?
А) С замедленным охлаждением после сварки.
Б) На увеличенных режимах сварки.
В) С подогревом.
5. Какие требования предъявляются к качеству исправленного участка шва?
А) Те же, что и к основному шву.
Б) Дополнительные требования, предусмотренные нормативно-технической документацией.
В) Специальные требования, предусмотренные нормативно-технической документацией.
БИЛЕТ 11
БИЛЕТ 12
БИЛЕТ 13
БИЛЕТ 14
БИЛЕТ 15
БИЛЕТ 16
БИЛЕТ 17
В каких пределах изменяется стандартный угол разделки кромок V- образных соединений деталей стальных конструкций, свариваемых ручной дуговой сваркой, сваркой в защитных газах и под флюсом, замеряемый после сборки?
А) 10 – 30 град.
Б) 50 – 60 град.
В) 60 – 90 град.
А) Повышенное содержание в металле шва углерода, кремния, серы, фосфора, глубокая и узкая сварочная ванна.
Б) Пониженное содержание в металле шва углерода, кремния, серы, фосфора, глубокая и узкая сварочная ванна.
В) Повышенное содержание в металле шва углерода, кремния, серы, фосфора, широкая сварочная ванна.
5. Как за счет технологии сварки можно предупредить образование горячих трещин?
А) Уменьшением числа проходов за счет увеличения погонной энергии, увеличением амплитуды поперечных колебаний электрода при сварке.
Б) Выбором оптимальной формы разделки кромок, снижением погонной энергии.
В) Применением узкой разделки кромок, проведением термической обработки после сварки.
БИЛЕТ 18
БИЛЕТ 19
1. Что представляет собой дефект, называемый "кратер шва"?
А) Углубление, образующееся в конце валика под действием давления дуги и объемной усадки металла шва.
Б) Воронкообразная впадина на поверхности шва.
В) Место окончания сварки (обрыва дуги).
2. Укажите причины образования непроваров при ручной дуговой сварке.
А) Большая скорость ведения сварки, недостаточная величина сварочного тока.
Б) Малая скорость ведения сварки, повышенная величина сварочного тока.
В) Малая скорость ведения сварки, оптимальная величина сварочного тока.
3. Укажите основные причины образования прожога.
А) Завышен сварочный ток относительно толщины свариваемого металла.
Б) Низкая квалификация сварщика.
В) Большая сварочная ванна, а следовательно, и её масса.
Билет 20
Что такое «газовая сварка»?
А) Дуговая сварка, при которой защита сварочной ванны осуществляется за счет подачи газа.
Б) Сварка плавлением, при которой для нагрева используется тепло пламени смеси газов, сжигаемой с помощью горелки.
В) Дуговая сварка проволокой сплошного сечения в среде инертного газа.
БИЛЕТ 21
1.При каких номинальных напряжениях не требуется заземление или зануление электроустановок:
А) До 36 В переменного тока и до 120 В постоянного тока.
Б) До 42 В переменного тока и до 110 В постоянного тока.
В) До 24 В переменного тока и до 140 В постоянного тока.
БИЛЕТ 22
БИЛЕТ 23
БИЛЕТ 1
Какая сталь обыкновенного качества относится к кипящей?
А)Сталь не полностью раскисленная марганцем при выплавке, и содержащая не более 0,05% кремния.
Б) Содержащая кремния от 0,05 до 0,17%.
В) Содержащая более 10 мл. водорода на 100 г. металла.
cyberpedia.su
Дефекты сварных швов и соединений. Способы их устранения
От качества сварки зависит дальнейшая эксплуатация конструкции, поэтому дефекты сварных соединений не допускаются. Возникновению дефектов способствует множество факторов, например:
- нарушение технологии работ;
- халатность;
- невысокая квалификация сварщика;
- применение неисправного оборудования;
- производство работ без надлежащей подготовки, в неблагоприятных погодных условиях.
Различают допустимые и не допустимые значения дефектов сварных швов от степени снижения технических параметров изделия по прочности. При допустимых нарушениях исправление дефектов сварки не производится, во втором случае их устранение необходимо. Пригодность изделия к эксплуатации, определение соответствия шва нормам производится по ГОСТ 30242-97.
Виды дефектов сварки
Правильный сварочный шов подразумевает однородность состава основного и присадочного материала, образование нужной его формы, отсутствие трещины, непровара, наплыва, наличием чужеродных веществ. Различают следующие виды дефектов сварных соединений:
- наружные;
- внутренние;
- сквозные.
Что собой представляют наружные дефекты?
Наружные дефекты сварных швов и соединений обнаруживаются визуально. Нарушения режима сварки, не соблюдение точности направления и движения электрода из-за спешки или безответственности сварщика, колебания напряжения электричества при производстве сварочных работ приводят к образованию шва неправильного размера и формы.
Характерными признаками наружного вида брака являются: различие ширины продольных швов и катетов угловых, резкость перехода от основной стали к наплавленной.
При ручном способе сварки нарушения происходят вследствие ошибок в подготовке кромок, пренебрежения режимом и скоростью сварки, отсутствия своевременного контрольного обмера. Дефекты сварных швов и причины их образования при ведении автоматического или полуавтоматического способа сварочных работ кроются в чрезмерных скачках напряжения электричества, ошибках в режиме. Различают следующие наружные виды дефектов сварных швов:
Трещины швов бывают горячие и холодные, продольные, поперечные, радиальные. Первые из них имеют место при применении высоких температур от 1100 до 1300°С, воздействующих на свойства металла в плане снижения пластичности, появления деформаций растяжения. Этот вид дефектов сварных швов сопровождается увеличением в составе стали нежелательных химических элементов. Холодные трещины могут появляться при температуре до 120°С во время остывания, позже – под воздействием нагрузок во время эксплуатации. Причиной данного вида брака может стать снижение прочности стали из-за сварочных напряжений или присутствие растворенных атомов водорода.
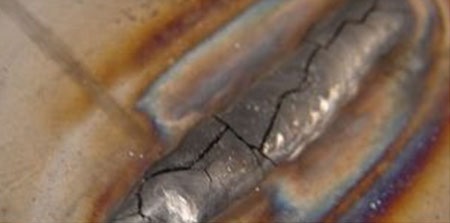
Трещина в сварочном шве
Подрез характеризуется наличием углубления между сплавленной и основной сталью. Этот вид дефекта сварочного шва встречается больше других. Увеличение напряжения дуги при быстрой сварке, приводит к утончению толщины стали, снижению прочности. Более глубокая проплавка одной из кромок является причиной стекания жидкой стали на другую поверхность, из-за чего канавка сварки не успевает заполниться. В данном случае, дефекты сварки и способы их устранения определяются визуально. Недостатки в работе устраняются путем зачистки, с последующей переваркой.

Подрез сварочного шва
Наплыв возникает, когда сплавленный металл натекает на поверхность основной стали без образования однородной массы с ним. Этому виду брака характерно образование очертания шва без обретения достаточной прочности, что сказывается в общей выносливости металла. Причина брака в применении низкого напряжения дуги, наличие окалин на кромках частей, натекание проплавленной стали при сварке горизонтальных швов, когда поверхность свариваемых конструкций вертикальна. Чрезмерно медленная сварка также приводит к образованию наплывов, из-за появления излишек расплавленного металла.

Наплыв
Кратеры появляются из-за резкого отрыва дуги. Они имеют вид углублений, где может образоваться непровар, рыхлость материала с усадочным свойством, приводящим к появлению трещин. Кратеры возникают из-за погрешностей сварщика. Так как кратер обычно является причиной появления трещин, из-за чего не допускается, при его обнаружении следует зачистить, затем заваривать повторно.
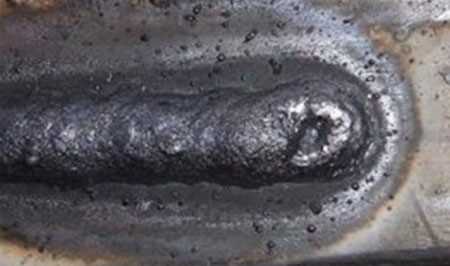
Образовавшийся кратер в сварочном шве
Свищи имеют вид воронок с углублением на теле шва. Они образуются из раковин или пор достаточно больших размеров, при недостаточной подготовке поверхности элементов сварки и присадочной проволоки. Данный вид дефекта также можно увидеть при визуальном осмотре и подлежат немедленному устранению.
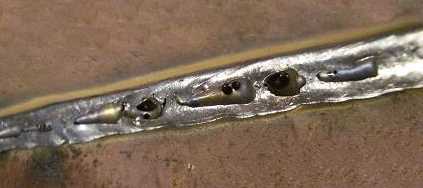
Типичные воронки свища
Внутренние дефекты сварочных швов
Внутренние недостатки сварки визуально обнаружить невозможно. Обычно появляются из-за нарушения технологического процесса сварки и не надлежащего качества материала. При внутренних дефектах также могут появиться трещины, но они не видны или малы, но со временем могут раскрыться. Скрытые трещины опасны тем, что их трудно обнаружить, а напряжение может возрастать постепенно, и может привести к скоротечному разрушению конструкции, поэтому чрезмерно опасны. Причиной брака могут быть огромные напряжения, быстрое охлаждение при использовании углеродистых и легированных сталей. Наиболее распространенные виды данного рода дефектов следующие:
Непровар происходит при недостаточном сплавлении свариваемых частей шва на местах. Причина кроется в ненадлежащей подготовке кромок, связанных с наличием ржавчины, окалины, недостатком зазора и притуплением кромок. Кроме этого, спешка и быстрая скорость ведения сварки, малая сила тока или смещение электрода от оси шва тоже могут привести к непровару шва. Из-за уменьшения сечения сварного шва появляется концентрация напряжений, что отражается в снижении прочности соединений, которая составляет при вибрационных нагрузках до 40%, а большие участки непроваров – до 70%. При превышении допустимых значений требуется зачистка шва и ее переварка.
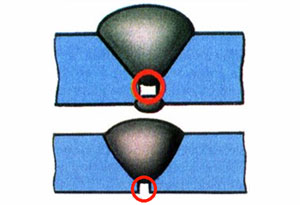
Непровар и незаполнение
Поры – это свободные пространства сварного шва, заполненные газом, преимущественно, водородом. Причиной этого вида брака является наличие чужеродных примесей в свариваемых материалах, сырость, недостаточная защита сварочной ванны. При превышении допустимых концентраций пор сварочный шов подлежит переварке.
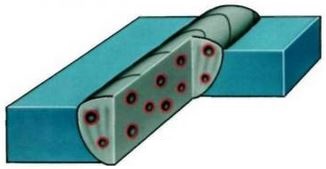
Поры в сварном шве
Кроме этого, можно отметить шлаковые, вольфрамовые, оксидные включения, также возникающие при нарушении технологии сварочного процесса.
Сквозные дефекты
Этот вид брака подразумевают наличие пор, проходящих через всю толщину сварки, также обнаруживаются визуально. Преимущественно возникают при ведении сквозной сварки. При данном виде дефекта возможно появление прожогов и трещин.
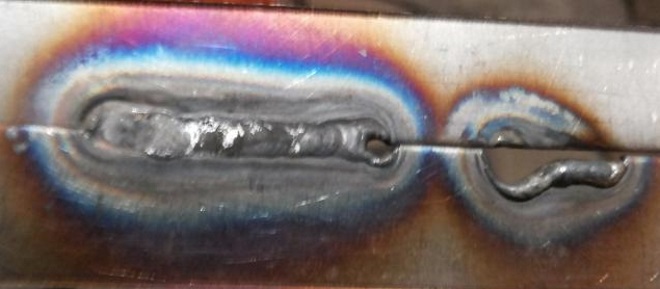
Прожог
Прожог возникает от применения большого тока и медленной сварки. Причина – чрезмерная открытость зазора у кромок, неплотное прилегание подкладок, вследствие чего происходит утечка сварочной ванны. Проверка шва на наличие брака проводится визуально, при его превышении допустимой нормы, требуется зачистка и переварка сварки.
Методы обнаружения, контроля и устранения дефектов
Чтобы обнаружить дефекты сварного шва применяются следующие способы:
- визуальный осмотр – проводится с применением увеличительных приборов;
- цветная дефектоскопия – основан на изменении цвета специального материала при соприкосновении с текучим материалом, например, с керосином;
- магнитный метод – измерение искажения магнитных волн;
- ультразвуковой метод – применение ультразвуковых дефектоскопов, измеряющих отражение звуковых волн;
- радиационный метод – просвечивание сварных швов рентгеном и получение снимка со всеми деталями дефекта.
Для обеспечения качества сварного шва проводится маркировка и клеймение. Каждый сварщик ставит свое клеймо на своем участке сварки.
При обнаружении брака необходимо провести устранение дефектов сварки. Для этого применяют следующие виды работ:
- заварка – используют для ликвидации крупных трещин, предварительно подготовив трещину сверлением и зачисткой при помощи зубила или абразивного инструмента;
- внутренние мелкие трещины, непровары и включения подлежат полной зачистке или вырубке с повторной сваркой;
- неполные швы и подрезы сварного шва устраняют наплавкой или заваркой тонкими слоями;
- удаление наплывов производят механическим путем с помощью абразивного инструмента;
- перегрев металла устраняют путем термической обработки.
svarkagid.ru
Дефекты сварного шва: классификация и способы устранения
Сварка – один из наиболее важных производственных процессов. С ее помощью выполняется соединение стальных деталей в самых разнообразных конструкциях. Как и в случае прочих производственных процессов, иногда встречается брак. Под ним подразумеваются дефекты сварного шва, которые могут резко снизить качество готового изделия, а то и вовсе сделать его эксплуатацию смертельно опасной.
Классификация
Кстати, а как их можно разделить? Все дефекты сварного шва делятся на три большие группы:
- Наружные.
- Внутренние.
- Сквозные.
Наружные дефекты сварного шва зачастую являются наиболее многочисленной категорией. В нее входят: излишне малые размеры, а также смещение линии шва, различные наплывы, «надрезы», раковины усадки и не заделанные в процессе сварки кратеры, пористость или трещины. Неравномерная ширина шва также относится к этой разновидности. Считается, что внешние дефекты сварных швов относятся к наименее опасной категории.
Соответственно, к внутренним относятся: поры, многочисленные включения шлака, не полностью проваренные места, а также трещины в толще сваренного металла. Что касается сквозных дефектов, то это свищи, проходящие через всю толщину детали трещины, а также пережог.
Основные причины возникновения сварочных дефектов
- Практически всегда они появляются в случае, когда стараются использовать исключительно дешевые и низкосортные материалы.
- То же самое можно сказать в отношении низкокачественного сварочного оборудования. Кроме того, частота возникновения дефектов нередко возрастает после некачественного ремонта используемых специалистами приборов.
- Разумеется, подобное сплошь и рядом происходит при нарушениях технологии работы.
- Серьезные дефекты сварного шва нередко встречаются у неопытных специалистов с низкой квалификацией.
Несложно понять, что наиболее качественные изделия получаются в случае использование полностью автоматизированного оборудования. Не стоит забывать и об удобстве рабочего пространства. Так, крупная чешуйчатость шва и нарушения его ширины очень часто встречаются в тех случаях, когда сварщик (пусть даже опытный) работает в неудобном положении.
Собственно, не случайно в требованиях к выполнению сварочных работ имеются пункты, которые особо оговаривают полноценное оснащение рабочего места, предусматривающее его качественную эргономику.
Немаловажное замечание
Даже начинающим сварщикам прекрасно известно, что для обеспечения максимальной прочности шов должен иметь небольшое усиление высотой порядка 1-2 мм. В то же время те же сварщики нередко допускают грубую ошибку, когда делают усиление высотой 3-4 мм. В принципе, в простых случаях ничего страшного в этом нет, но не тогда, когда дело касается изделий, постоянно находящихся в состоянии динамической нагрузки. Все это приводит к концентрации напряжений и резкому повышению вероятности поломки.
Подрезы
Как мы уже и говорили, дефекты сварных швов и соединений крайне опасны. Нетрудно представить себе, что произойдет в случае, если они будут иметься в детали, предназначенной для установки, к примеру, в опорную конструкцию железнодорожного моста. Особенно они опасны в случае сварки деталей из легированной стали, которые будут эксплуатироваться в условиях постоянных перепадов температур.
Наиболее опасными являются подрезы, так как они являются естественным «аккумулятором» напряжений, которые будут концентрироваться в наиболее слабом месте шва. Кроме того, они значительно уменьшают его рабочее сечение, что также крайне отрицательно сказывается на прочности всего соединения.
Как правило, эти наружные дефекты сварных швов в большинстве случаев не исправляются. Связано это с тем, что металл (чаще всего) все равно будет иметь малозаметный брак, который может привести к весьма существенным последствиям.
Как возникают подрезы?
Основной причиной является выставление слишком большой силы тока. В сочетании с длинной дугой этот фактор дает практически стопроцентную вероятность их появления. Кроме того, в некоторых случаях подрезы возникают при излишне быстром перемещении источника нагрева над поверхностью металла.
Если конструкция хоть сколь-нибудь важная, даже мельчайшие дефекты сварных швов и соединений этого типа совершенно недопустимы. Исправляют их при помощи аккуратной наварки тонкого шва. В случае наличия таковой возможности деталь все же лучше полностью заменить (заметим, что последнее замечание относится ко всем дефектам).
Участки непроваренного металла
Если таковой участок располагается прямо в толще шва, это крайне опасно. Во-первых, отыскать такой дефект можно только при помощи дефектоскопа. Во-вторых, они опять-таки являются аккумулирующими местами естественных напряжений в металле. В сочетании с нарушением сварной структуры все это приводит к риску преждевременной поломки детали. Особенно часто такие внутренние дефекты сварных швов возникают в случае использования легированной стали и плохого сварочного оборудования.
Пористость (вне зависимости от ее локализации) резко снижает прочностные характеристики до недопустимых величин, приводит к «расслоению» металла, то есть к нарушению его естественной структуры. Детали даже с незначительной пористостью в несколько раз чаще разрушаются под нагрузкой даже в начале эксплуатации. Возникают поры по вине газов, которые попросту не успевают выйти из слоя расплавленного металла.
Как и все виды дефектов сварных швов, они чрезвычайно часто возникают в случае использования некачественных сырых электродов. Нередко бывает так, что пористость возникает по причине каких-то посторонних примесей в защитных газах. Как и в прошлом случае, этот тип дефектов также может наблюдаться при излишне высокой скорости сварки, когда банально нарушается целостность газовой защитной «ванны».
Включения шлака
Включения шлака в значительной степени портят однородность металлической структуры. Классическая причина образования – небрежная зачистка поверхности шва от остатков ржавчины и окалины. Вероятность их возникновения стремится к нулю при условии сварки в слое защитных газов. Редкие включения округлой формы опасности не представляют, изделия с ними могут пройти ОТК.
Заметим, что если при сварке использовался вольфрамовый электрод, то в деталях могут быть обнаружены частицы этого металла. Степень их опасности – как и в предыдущем случае (т. е. это допустимые дефекты сварных швов).
Трещины
Бывают поперечными и продольными, идущими как по самому шву, так и по металлу вдоль или около него. Они крайне опасны тем, что в некоторых случаях снижают механическую и вибрационную прочность изделия практически до нуля. В зависимости от свойств свариваемого материала, трещина может как сохранять свою изначальную локализацию, так и распространиться на всю длину обрабатываемой детали за очень короткое время.
Неудивительно, что это наиболее опасные дефекты сварных швов. ГОСТ в большинстве случаев требует немедленной отбраковки таких деталей вне зависимости от ее предназначения (за исключением совсем уж маловажных изделий).
Неравномерность швов
Так называется грубое несоответствие геометрических параметров соединений требуемым в нормативных документах характеристикам. Проще говоря, если сварка идет «змейкой», наискосок и т. п., речь как раз идет о подобном типе дефектов.
Чаще всего они появляются при работе неопытных сварщиков, а также при значительных скачках напряжения, некачественном оборудовании и банальной спешке. Опасен этот дефект тем, что зачастую комбинируется с недоваром, который уже куда опаснее. Если отклонение от осевой линии соединения незначительно и не вызывает снижения прочности изделия, деталь может быть допущена к эксплуатации.
В этом случае всегда следует помнить одну простую вещь: чем меньше угол перехода от основного металла к слою наплавления, тем хуже становится механическая прочность свариваемого изделия. Конечно же, при изготовлении каких-то бытовых конструкций (каркас теплицы, к примеру) в условиях недостаточного напряжения обойтись без неравномерности швов просто нереально. Впрочем, в таком случае они и не представляют особой опасности.
Основные способы устранения, исправления дефектов
Сразу скажем следующее: в большинстве случаев способы устранения дефектов сварных швов обсуждать не имеет смысла, так как в условиях более-менее строгого ОТК все изделия с какими-то изъянами попросту бракуются. Но порой действительно бывает так, что дефект не слишком серьезный, а потому его можно устранить. Как это делать?
В случае со стальными конструкциями испорченную поверхность срезают (плазменно-дуговая сварка), тщательно зачищают место неудачного соединения, а затем повторяют попытку. Если имеются незначительные внешние дефекты сварных швов (неравномерность соединения, неглубокие оспины), то их можно попросту зашлифовать. Конечно же, при этом не стоит увлекаться и снимать слишком большой слой металла.
Важное замечание
Если речь идет об изделиях из легированной стали, которые должны пройти обязательную термическую обработку, то исправление дефектов сварных швов должно производиться только (!) после отпуска в температурном диапазоне от 450 до 650 °С.
Исправление прочих разновидностей
Проще всего исправлять наплывы и механическую неравномерность шва. В таком случае место соединения просто зачищают (о чем мы уже писали). Об исправлениях подрезов мы уже говорили выше, но еще раз заметим – с такими дефектами деталь более целесообразно сразу выбраковать, так как ее эксплуатация может быть опасна!
Если имеется прожог (что встречается не так часто), то устранение дефектов сварных швов провести довольно просто: сперва поверхность как следует зачищается, а затем ее повторно проваривают. Приблизительно так же поступают и с кратерами.
Основные условия «косметического ремонта»
При устранении дефектов нужно соблюдать определенные технологические условия. Во-первых, нужно следовать простому правилу: длина дефектного участка должна соответствовать его ширине, плюс 10-20 мм стоит оставить «на всякий случай».
Важно! Ширина сварочного шва после его повторной проварки не должна превышать двукратного его размера до начала работ. Не ленитесь перед исправлением огрехов хорошо подготовить поверхность. Во-первых, это предотвратит попадание в металл кусочков шлака. Кроме того, данная нехитрая мера поможет ускорить работу и повысить качество ее результатов.
Очень важно подготовить выборку под вновь заделываемый участок. Если вы используете УШМ («болгарку»), то лучше взять диск самого маленького диаметра. Боковые грани выборки нужно делать как можно более ровными, без заусениц и прочих выступающих частей, которые в процессе сварки могут превратиться во все тот же шлак.
Если речь идет о соединениях алюминия, титана, а также сплавах этих металлов, то к делу стоит подойти еще более ответственно. Во-первых, при устранении дефектов в этом случае допускается использовать только (!) механические методы, применение же дуговой сварки недопустимо. Предпочтительнее всего вырубать испорченный участок, зачищать и заново заваривать шов.
Замечание по исправленным дефектам
Места с исправленными - повторно заваренными соединениями, должны вновь пройти процедуру ОТК. Если дефект в той или иной степени сохранился, его можно попробовать устранить опять. Важно! Количество исправлений зависит от марки стали и характеристик самого изделия, но в нормальных условиях переделывать работу можно не более двух-трех раз, так как в противном случае наблюдается резкое снижение прочностных качеств детали.
Вот мы и обсудили основные виды дефектов сварных швов.
fb.ru
Виды дефектов сварных швов и методы их устранения
Что такое дефекты сварных швов?
Дефекты бывают нескольких видов - наружные и внутренние. Наружными являются дефекты, которые можно обнаружить визуально при осмотре сварочного шва.
Внутренние дефекты, наоборот, находятся внутри сварочных соединений и их можно увидеть лишь после дефектоскопии, включая рентген и механическую обработку.
Дефекты бывают допустимыми и не допустимыми, в зависимости от требований, предъявляемых к сварочным соединениям и конструкции в целом.
Однако, исходя из самого определения, любые дефекты являются дефектами и требуют их полного устранения либо сведения к минимуму их количества и размеров.
Так как дефекты сварных швов являются причиной, в результате которой есть риск поставить под угрозу стабильность соединения и функциональность сварной конструкции, есть ряд операций, чтобы их устранить. Чтобы свести к минимуму вероятность появления дефектов следует обязательно учитывать:
- 1) Технологию сварки и квалификацию сварщика
- 2) Присадочный материал и свариваемый металл
- 3) Подготовку поверхности под сварку и защитный газ
- 4) Режимы и применяемое сварочное оборудование
Наружные дефекты
К наружным дефектам относятся нарушения геометрических размеров (подрезы, наплывы), непровары и прожоги, незаваренные кратеры.
Основной причиной непроваров является недостаточный сварочный ток, так как он в большей степени влияет на проникновение в металл.
Устранение дефектов этого вида обычно происходит путем повышения мощности сварочной дуги, уменьшением длины дуги и увеличением её динамики.
Также причиной непроваров может быть большая скорость сварки или недостаточная подготовка кромок сварного соединения.
Непровары могут быть нескольких видов:
- - когда сварочный шов проникает не на всю толщину металла при односторонней сварке (см. верхнюю часть на рисунке)
- - при двусторонней сварке встык швы не стыкуются друг с другом, образуя несплавление между собой (см. нижнюю часть на рисунке)
- - при сварке в тавр сварочный шов не проникает вглубь, а лишь цепляется за свариваемые кромки
Также причиной непроваров может быть большая скорость сварки или недостаточная подготовка кромок сварного соединения.
Подрезом называется дефект в виде канавки в основном металле по краям сварочного шва.
Это наиболее распространенный дефект при сварке тавровых или нахлесточных соединений, но может также возникнуть и при сварке стыковых соединений. Этот вид дефекта обычно вызван неправильно подобранными параметрами, особенно скоростью сварки и напряжением на дуге.
При угловой сварке (например при сварке длинных швов при сварке балок) подрезы часто возникают из за того, что сварочная дуга направлена больше на вертикальную поверхность.
Расплавленный металл стекает на нижнюю кромку и его не хватает для заполнения канавки.
При слишком высокой скорости сварки и повышенном напряжении, сварной шов образуется «горбатым». Из-за быстрого затвердевания сварочной ванны, в этом случае также образуются подрезы. Уменьшение скорости сварки постепенно сокращает размер подреза и в конечном итоге устраняет этот дефект.
На подрезы влияет также длина сварочной дуги. При слишком длинной сварочной дуге ширина шва увеличивается, тем самым увеличивая количество расплавленного основного металла. Так как при увеличении длины дуги тепловложение остается прежним, его не хватает на весь сварочный шов, кромки быстро остывают, образуя подрезы. Уменьшение длины дуги не только избавляет от подрезов, но и увеличивает проплавление и устраняет такие дефекты, как непровар.
Данный дефект появляется в результате натекания присадочного материала на основной металл без образования сплавления с ним. Обычно причиной этого дефекта является неправильно подобранные режимы сварки и окалина на свариваемой поверхности. Подбор правильного режима (соответствие сварочного тока со скоростью подачи присадочного материала, повышение напряжения на дуге) и предварительная очистка кромок устраняют появления наплывов.
Данный дефект – отверстие насквозь в сварочном шве. В основном причинами прожога являются большой ток, медленная скорость сварки или большой зазор между кромками сварного соединения. В результате происходит прожог металла и утечка сварочной ванны.
Понижение сварочного тока, увеличение скорости сварки и соответствующая подготовка геометрии кромок позволяют устранить прожоги. Прожоги являются очень частым дефектом при сварке алюминия, из его низкой температуры плавления и высокой теплопроводности.
Кратер появляется в конце сварочного шва в результате резкого обрыва дуги. Выглядит он в виде воронки в середине сварочного шва при его окончании. Современное сварочное оборудование имеет специальные программы для заварки кратера. Они позволяют проводить окончание сварки на пониженных токах, в результате чего кратер заваривается.
Внутренние дефекты
К внутренним основным дефектам сварных швов относят трещины (холодные и горячие) и поры.
- Горячие трещины
Горячие трещины появляются в то время, когда металл сварного шва находится в состоянии между температурами его плавления и затвердевания. Они могут быть в двух направлениях – вдоль и поперек сварного шва. Горячие трещины обычно являются результатом использования неправильного присадочного материала (в частности, алюминиевых и CrNi сплавов) и его химического состава (например, высокое содержание в составе углерода, кремния, никеля и др.)
Горячие трещины могут появиться в результате неправильной заварки кратера, в результате резкого прекращения сварки.
- Холодные трещины
Трещины, которые возникают после того, как сварочный шов полностью остывает и затвердевает, называются холодными трещины. Эти дефекты также появляются тогда, когда сварочный шов не соответствует действующим на него нагрузкам и разрушается.
Пористость является одним из основных дефектов сварки, с которыми сталкиваются все сварщики при всех сварочных процессах. Пористость может быть вызвана загрязнением, плохой защитой ванны потоком сварочного газа, маслом, краской, сваркой несовместимых сплавов или даже ржавчиной и окислением металла.
Поры могут различаться по размеру и, как правило, распределяются в случайном порядке по сварочному шву. Они могут находиться как внутри шва, так и на его поверхности.
Основные причины появления пористости:
- 1) Недостаточный поток защитного сварочного газа
- 2) Чрезмерный поток защитного газа. Это может вызвать подсос воздуха в поток газа.
- 3) Сквозняк в зоне сварки. Он может сдувать защитный газ.
- 4) Засорение сварочного сопла или повреждение системы подачи газа (утечка в шлангах, соединениях и т.д.)
Надеюсь, что описанные в этой статье основные виды дефектов сварных швов и соединений, а так же методы их устранения сделают вашу сварку качественной и высокопроизводительной. Помните, что правильный выбор сварочного оборудования и технологии сварки имеет большое влияние как на весь процесс сварки в целом, так и в отдельности на каждые его составляющие.
© Смарт Техникс
Данная статья является авторским продуктом, любое её использование и копирование в Интернете разрешена с обязательным указанием гиперссылки на сайт www.smart2tech.ru
www.smart2tech.ru
Дефекты сварных швов
Когда имеются несоблюдения технических условий, возникают дефекты сварки. При этом наблюдается сильное ухудшение сварных соединений.

Корневые дефекты шва.
Швы теряют много положительных свойств, таких, как:
- механические;
- герметичность:
- сплошность.
Дефекты при сварке могут иметь разные причины:
- плохая свариваемость детали;
- качество электродов;
- флюс;
- режим сварки;
- квалификация сварщика;
- несоответствие технологии.

Виды дефектов при сварке.
В зависимости от места нахождения дефекты в шве подразделяются на:
- внешние;
- внутренние.
Дефекты сварочных соединений оказывают влияние на определенные характеристики изделия:
- прочность;
- форма;
- глубина расположения.
Опасными считаются дефекты при сварке, имеющие острые контуры. Дефекты сварочных швов, имеющие скругленные формы, практически неопасны. Глубина дефекта оказывает непосредственное влияние на показатель прочности соединения.
Когда варятся важные конструкции, дефекты шва не должны быть глубже 8% от толщины заготовки. Самыми опасными являются дефекты сварочных швов, которые находятся под углом в 90° по отношению к растягивающему усилию. Находящиеся под маленьким углом к основному усилию дефекты представляют минимальную опасность.
Именно поэтому начинает падать прочность сварных швов, когда образуются трещины при сварке. Причем наибольший негатив несут горячие трещины, когда они возникают вдоль оси шва. Отрицательно влияют и непровары большой глубины.
Внешние дефекты, трещины

Классификация сварных дефектов.
В основном это касается высоты шва и его ширины. Основными причинами считаются:
- Плохая обработка кромок. Образуются зазоры, которые приходится заливать расплавленным металлом.
- Перемещение электрода было прерывистым, в результате шов получился разным по высоте. Изменяется его ширина, причем все это наблюдается по всей длине.
- Игнорирование технологических условий.
Когда возникает такой дефект, швы плохо выглядят. Так как имеет место неравномерная усадка сварки, возможны появление деформации, образование напряжения. Дефект может быть обнаружен как визуальным осмотром, так и специальным шаблоном. Такие дефекты сварки можно устранить подваркой, удалением лишнего металла.
Наружные трещины подразделяются на:
- продольные;
- поперечные.
Трещины в швах можно обнаружить в наплавке и заготовке. В самой детали они располагаются ближе к району термического влияния. Основными причинами возникновения трещин считаются:
- напряжения;
- нарушение структуры материала, когда соединение делается сваркой;
- высокое содержание фосфора;
- воздействие водорода.
Вернуться к оглавлению
Что такое сварочная трещина?
Под трещиной понимается образование прерывистого шва, вызванного механическим воздействием, резким охлаждением. Этот дефект может иметь вид микротрещин. Обнаружить его можно специальными оптическими приборами, имеющими 50-кратное увеличение.

Схема сварочной трещины.
Продольные трещины можно видеть:
- в шве;
- в материале;
- в местах сплавления.
Скрытые трещины возникают из-за появления высокого напряжения. Они очень похожи на ступеньки. В основном такой дефект имеют сварные соединения большой толщины. Появление высоких напряжений в большинстве случаев вызывает несоблюдение сварочной технологии.
Продольные трещины делятся на несколько групп:
- Горячие трещины при сварке. Причиной появления считается высокотемпературная хрупкость, характерная для сплавов.
- Холодные. Появляются, когда металл начинает медленно разрушаться.
Поперечные трещины обычно составляют перпендикуляр оси сварочного шва. Обнаруживаются в заготовке, в районе температурного влияния.
Радиальные трещины начинаются в одной точке и расходятся в разные стороны. Получили второе название — «звездообразные». Располагаются в районе поперечных трещин.
Там, где дуга отходит от поверхности шва, появляется углубление, так называемая трещина в кратере. Она бывает:
- продольной;
- поперечной;
- звездоподобной.
Вернуться к оглавлению
Подрезы: особенности

Сварочные подрезы и наплывы.
Очень часто наблюдаются при сварочном процессе. Происходит углубление там, где шов соединяется с основным металлом.
Так как из-за появления подреза уменьшается толщина детали, она теряет свою прочность. Большую опасность несут подрезы, когда располагаются перпендикулярно возникшим рабочим напряжениям.
Появление подреза связано с высоким напряжением дуги, причем сварка проводится на повышенной скорости.
При этом одна кромка получает более глубокое проплавление, расплавленный металл начинает течь по горизонтальной плоскости. Количества такого расплава недостаточно, чтобы заполнить канавки.
Когда варятся угловые швы, возникновение подрезов связано со смещением электрода по направлению к вертикальной стенке. В результате металл получает очень сильный нагрев, начинает плавиться и стекать на горизонтальную поверхность.
Образование подрезов стыковых швов связано с подачей большого тока и неправильным расположением присадки.
Разделка трещин, когда сделаны большие углы, также приводит к появлению подрезов. Такой дефект бросается в глаза и требует полной переварки.
Если подрезы имеют небольшую длину, а сечение шва ослабляется только на 5%, конструкция имеет статические нагрузки, переварка не требуется. Запрещается наличие подрезов в конструкциях, которые работают под большим давлением.
Вернуться к оглавлению
Что представляет собой прожог?

Сварочные прожоги.
Причинами сквозного проплавления являются:
- большой ток;
- низкая скорость.
Обычно прожог представляет собой сквозное отверстие, образовавшееся при сварке. В случае многослойной сварки образование прожога выявляется в самом начале. Причинами возникновения прожога считаются:
- большой зазор между кромками;
- маленькая толщина подкладки;
- плохое прилегание;
- большая утечка расплавленного металла.
Возможно образование прожога, когда неожиданно останавливается подача инертного газа. Когда свариваются вращающиеся кольцевые стыки, прожог появляется из-за неправильной установки электрода. Этот дефект виден сразу, место зачищается и полностью заваривается.
Вернуться к оглавлению
Дополнительные проблемы
Могут возникнуть другие неполадки:
Незаваренный кратер. Возникает, когда дуга резко отрывается от поверхности в самом конце сварки. Образуется углубление, имеющее вид усадочных рыхлостей, становящихся трещинами. В большинстве случаев появление такого дефекта связано с непрофессионализмом сварщика. Когда выполняется автоматический сварочный процесс, кратер возникает в зоне выводных планок, там, где обрывается сварочный шов. Наличие кратеров категорически запрещено. Их необходимо зачистить и полностью заварить.
Поверхностное окисление. Речь идет о появлении окалины, закрывающей сварное соединение.
Причинами появления такого дефекта являются:
- плохая охрана сварочной зоны;
- обработка свариваемых кромок;
- настройки подачи инертного газа;
- его состав;
- размер вылета.
Свищ. Сварочный шов имеет воронкообразное углубление, которое появляется из-за крупной раковины. Причинами возникновения свища в основном считаются плохая обработка поверхности, применение нечистой присадочной проволоки. Данный дефект легко обнаруживается зрительно, исправляется полной переваркой.
Горящие трещины. Когда температура плавления достигает 1100° С, начинается кристаллизация металла. Как следствие ухудшаются пластические свойства, возникает растягивающая деформация. В основном горячие трещины располагаются на краях кристаллической решетки. Возникают они вследствие высокого содержания в самом шве, большого количества:
- углерода;
- кремния;
- водорода;
- никеля;
- серы;
- фосфора.
Располагаются горячие трещины обычно хаотично. Их можно наблюдать вдоль всего сварочного шва. Такие трещины могут выходить на поверхность или находиться внутри нее.
expertsvarki.ru
Билеты экзамена по проверке знаний специалистов сварочного производства 2 уровень
БИЛЕТ № 5
ВОПРОС 1
Что такое сварка плавящимся электродом?
1. Дуга горит между свариваемым изделием и плавящимся сварочным электродом или электродной про-волокой, а сварочная ванна защищается газом и шлаком
2. Сварочная ванна защищается газом и шлаком, которые образовались в процессе плавления основного и сварочного материалов.
3. Электрод плавится за счет тепла дуги или газового пламени.
ВОПРОС 2
При разливки какой стали имеется наибольшая возможность образования усадочной пористости?
1. В спокойной стали.
2. В полуспокойной стали.
3. В кипящей стали.
ВОПРОС 3
Какие основные параметры приняты для оценки механических свойств металлов?
1. Временное сопротивление разрыву, предел текучести, относительное удлинение и сужение, ударная вязкость.
2. Жаропрочность, жаростойкость и хладостойкость металла.
3. Твердость, сопротивление изгибу и количество циклов ударного нагружения до разрушения металла.
ВОПРОС 4
Какой тип кристаллической решетки имеет феррит?
1. Кубическую объемноцентрированную решетку.
2. Кубическую гранецентрированную решетку.
3. Гексагональную плотноупакованную решетку.
ВОПРОС 5
Как влияет присутствие легирующих элементов ( марганца и молибдена) в стали на ее прокаливаемость?
1. Увеличивает.
2. Снижает.
3. Не изменяет.
ВОПРОС 6
Какие химические соединения образуются в сварочной ванне при сварке низкоуглеродистых сталей в процессе взаимодействия жидкого металла с кислородом?
1. Сульфиды железа.
2. Оксиды железа.
3. Карбиды железа.
ВОПРОС 7
Что называют статической вольтамперной характеристикой дуги?
1. Зависимость напряжения на дуге от сварочного тока при переменной длине дуги и постоянстве ос-тальных параметров.
2. Зависимость напряжения на дуге от сварочного тока при постоянной длине дуги и постоянстве ос-тальных параметров.
3. Зависимость напряжения на дуге и сварочного тока от длины дуги.
ВОПРОС 8
Какими электроизмерительными приборами должно быть оснащено сварочные источники питания для ручной дуговой сварки(наплавки)?
1. Амперметром.
2. Амперметром и вольтметром.
3. Вольтметром и устройством для контроля скорости сварки.
ВОПРОС 9
Для повышения напряжения питающей системы как должны соединятся несколько сварочных источни-ков питания?
1. Параллельно
2. Последовательно
3. Последовательно-параллельно
ВОПРОС 10
Какие требования предъявляются к хранению сварочных материалов?
1. Сварочные материалы хранят в специально оборудованном помещении без ограничения температуры и влажности воздуха.
2. Сварочные материалы хранят в специально оборудованном помещении при положительной темпера-туре воздуха.
3. Сварочные материалы хранят в специально оборудованном помещении при температуре не ниже 150 С и относительной влажности воздуха не более 50%.
ВОПРОС 11
Для какого класса сталей применяют при сварке электроды типов Э- 50, Э-50А, Э-42А, Э-55, Э-60?
1. Для сварки конструкционных сталей повышенной и высокой прочности.
2. Для сварки углеродистых сталей.
3. Для сварки высоколегированных сталей.
ВОПРОС 12
Допускается ли длительный перерыв в процессе сварки низколегированных теплоустойчивых сталей перлитного и мартенситно-ферритного классов?
1. Допускается при положительной температуре окружающей среды.
2. Не допускается.
3. Допускается при выполнении сварки в помещении цеха.
ВОПРОС 13
Какое назначение имеет дежурная дуга при импульсно-дуговой сварке вольфрамовым электродом?
1.. . Поддерживает дуговой промежуток дуги в ионизированном состоянии
2. Исключает образование дефектов в кратере.
3. Увеличивает глубину проплавления основного металла.
ВОПРОС 14
Какую полярность тока дуги называют прямой?
1. На электроде плюс, на изделии минус.
2. На электроде минус, на изделии плюс.
3. Переменное изменение полярности на электроде и изделии.
ВОПРОС 15
В какой цвет окрашивают баллон для хранения аргона?
1. Серый.
2. Голубой.
3. Белый.
ВОПРОС 16
Укажите газы, которые смешивают с углекислым газом при механизированной сварке плавящимся элек-тродом соединений деталей из углеродистых и низколегированных сталей?
1. Кислород до 5%.
2. Гелий до 50%; азот до 75%.
3. Кислород до 40%.
ВОПРОС 17
Укажите, как влияет на сварной шов уменьшение диаметра сварочной проволоки (при неизменном токе) при сварке под флюсом ?
1. Увеличивается глубина провара, уменьшается ширина шва и коэффициент формы шва.
2. Увеличивается глубина провара.
3. Никакого влияния не оказывает.
ВОПРОС 18
Какие существуют основные способы электрошлаковой сварки и наплавки?
1. Сварка с применением проволочных электродов, плавящихся мундштуков, электродов большого се-чения и ленточных электродов.
2. Сварка с применением одного электрода и многоэлектродная.
3. Сварка с применением кристаллизаторов и водяного душа.
ВОПРОС 19
Какие способы резки применяют для подготовки деталей из аустенитных сталей?
1. Кислородная.
2. Кислородно-флюсовая, плазменно-дуговая, угольным электродом.
3. Воздушно-дуговая.
ВОПРОС 20
Какие условия охлаждения должны соблюдать для проведения нормализации стали?
1. Охлаждение вместе с печью.
2. Охлаждение на воздухе.
3. Принудительное охлаждение.
ВОПРОС 21
Изменяется ли плотность тока на контактной поверхности свариваемых деталей при различных методах контактной сварки?
1. Нет.
2. Да.
3. Зависит от параметров режима сварки.
ВОПРОС 22
При каком виде контактной сварки обеспечивается более высокое качество сварного соединения термоуп-рочняемой низколегированной стали?
1. При стыковой сварке оплавлением.
2. При точечной и роликовой сварке.
3. При стыковой сварке сопротивлением.
ВОПРОС 23
Допускается ли термообработка сварного соединения после сварки аустенитными электродами хромо-молибденовых сталей (12ХМ, 15ХМ и др.) ?
1. Последующая термообработка обязательна.
2. Не допускается.
3. Допускается при толщине более 36 мм.
ВОПРОС 24
Как влияет значительное увеличение скорости деформации на свойства металла сварных соединений при испытании на статическое растяжение?
1. Уменьшает прочность и увеличивает пластичность.
2. Увеличивает предел текучести и уменьшает прочность.
3. Увеличивает прочность и уменьшает пластичность.
ВОПРОС 25
Как определяют длительную пластичность материала?
1. По величине предела текучести при испытаниях образцов на длительную прочность.
2. По величине предела текучести при испытаниях образцов с постоянной скоростью деформирования.
3. По величине относительного удлинения при испытаниях образцов на длительную прочность.
ВОПРОС 26
Какое явление вызывает образование холодных трещин в сварных соединениях перлитных и мартенситных сталей?
1. Скопление неметаллических включений в элементах микроструктуры стали.
2. Сегрегация примесей на границах аустенитных зерен при 200-4000 С.
3. Мартенситное превращение аустенита в сварном шве и околошовной зоне.
ВОПРОС 27
Что называют трещиной?
1. Дефект в виде разрыва металла сварного соединения или наплавленной детали (изделия).
2. Нарушение сплошности металла.
3. Недопустимое отклонение от требований Правил Контроля.
ВОПРОС 28
С какой целью проводят визуальный контроль сварных соединений?
1. Для выявления недопустимых дефектов и качества зачистки выполненных швов и околошовной зоны.
2. Для выявления поверхностных дефектов.
3. Для выявления внутренних дефектов.
ВОПРОС 29
Какой род тока более опасен при поражении человека электрическими токами при одинаковых напряже-ниях и мощности электрической цепи?
1. Переменный ток 50 Гц.
2. Постоянный ток.
3. Ток высокой частоты.
ВОПРОС 30
Норма времени определяется как:
1. Затраты времени работника или бригады на выполнение единицы продукции в чел./час.
2. Затраты времени на производство партии продукции.
3. Затраты времени на годовой объем выпускаемой продукции.
Для перехода на следующую страницу воспользуйтесь постраничной навигацией ниже
Теги: билеты, сварщик
web-mechanic.ru
Дефекты сварочного производства и их причины.
Перечень дефектов и причины их возникновения
Виды дефектов | Причина возникновения | Ответственный за возникновение дефекта |
Непровар. Непроваром называют отсутствие расплавления основного металла и следовательно, соединения деталей по части толщины свариваемого металла. | 1.Уменьшение силы тока.2.Увеличение напряжения. 3. Увеличение скорости сварки. 4. Плохая подготовка кромок под сварку, наличие загрязнений, окалины и шлака на поверхности свариваемых кромок. 5. Неточное направление электрода по оси соединения. 6. Неправильное возобновление сварки после перерыва. | Сварщик |
Подрезы. При дуговой сварке подрезом называется местное уменьшение толщины металла у границы шва. | 1.Высокое напряжение дуги. 2. Недостаточно точное ведение электрода по оси соединения. | Сварщик |
Наплывы. При дуговой сварке наплывом называют натекание металла шва на поверхность основного металла на поверхность основного металла без сплавления с ним. |
1.Низкое напряжение. 2.Низкая скорость сварки. | Сварщик |
Прожоги. Прожогами называются пустоты в шве, образовавшиеся в результате вытекания сварочной ванны. | 1.Избыточный ток. 2.Изменение наклона электрода. 3.Неплотное прилегание флюсовой подушки. | Сварщик |
1.Увеличенный зазор между свариваемыми кромками. | Котельщик | |
1.Занижена толщина подкладного кольца | Мехобработка, ОТК, мастер. | |
Шлаковые включения. Шлаковыми включениями называют видимые невооружённым глазом округлые или вытянутые участки шлака, расположенные в металле шва у границы сплавления, между отдельными слоями или в его корне. |
1.Недостаточно тщательно очищена поверхность кромок или предыдущего слоя от шлаковой корки. |
Сварщик |
Газовые поры. Перенасыщение ванны расплавленного металла газами. | 1.Плохая зачистка кромок металла. 2.Масло на поверхности свариваемых кромок. 3.Попадание влаги в зону сварки. |
Сварщик |
Инженер по сварке В.А.Лапшов
lapshov.info