Газобетон своими руками — экономим бюджет строительства. Состав пропорции газобетона
Неавтоклавный газобетон: состав и технология производства
Газобетон, как разновидность ячеистых бетонов, является популярным строительным материалом за счет своих существенных преимуществ. Подразделяется он на два вида: автоклавный и неавтоклавный. Применение второго вида газобетона позволяет использование его при монтаже монолитных сооружений. Неавтоклавный газобетон — относительно недорогой материал, применяемый для возведения несущих стен и перегородок.
Сферы использования
Неавтоклавные газобетоны применяются при возведении в малоэтажных зданиях и сооружениях несущих стен и перегородок. Применение неавтоклавного ячеистого бетона возможно при строительстве зданий и сооружений с большим количеством этажей в качестве наполнителя для каркасов стен из железобетона.
Состав
В неавтоклавном газобетоне имеются следующие составы:
- наполнители в виде чистого песка с включением золы, мела или гипса. Песок не должен содержать ил и глину;
- портландцементы;
- алюминиевая пудра для порообразования;
- хлорид кальция для ускорения процесса затвердевания, а также другие различные химические добавки, применяемые для регулировки газообразования и быстроты набора прочности;
- вода, преимущественно из поверхностных источников без содержания соли и мягкой жесткости.
Плюсы и минусы
Неавтоклавному газобетону присущи следующие преимущественные характеристики:
Неавтоклавный газобетон имеет следующие недостатки:
- Недостатки газобетона.
прочность меньше, чем у автоклавного ячеистого бетона и зависит от пропорций цемента;
- происходит снижение свойств теплоизоляции при заполнении водой пористой структуры материала, что способствует применению гидроизоляции;
- существует риск приобрести некачественную продукцию у производителей, которые экономят на материалах и технологии изготовления;
- происходит постепенное разрушение ячеистого бетона в результате механических нагрузок, что обязывает использование армопоясов в местах с наибольшей нагрузкой;
- усадка газобетона относительно большая и обязывает оттягивать с окончательными отделками поверхности;
- отсутствует возможность в эксплуатации блоков сразу после их изготовления.
Технология производства
Технология изготовления неавтоклавного газобетона состоит из следующих этапов:
- подготовка к заливке форм;
- заливка раствора;
- резка на блоки;
- выдержка раствора до набора его прочностных характеристик;
- сортировка и упаковка продукции.
Подготовка и заливка смеси
Начинают изготовление ячеистого бетона с подготовки компонентов смеси. Для этого берут цемент, известь, газообразователи, гипс и при необходимости специальные добавки для ускорения процесса застывания и увеличения прочности материала. Все компоненты в нужных пропорциях погружают в автоматизированный смеситель, в котором происходит перемешивание цемента, извести и остальных ингредиентов до консистенции, напоминающей сметану.
Перемешивание компонентов продукции происходит по заданной программе. Готовый раствор разливают в емкости наполовину, где и происходит образование пористой структуры газобетонных изделий, и оставляют затвердевать в естественных условиях. Такой способ изготовления существенно сокращает затраты на электроэнергию и транспортные услуги.
Вернуться к оглавлениюРезка материала на блоки
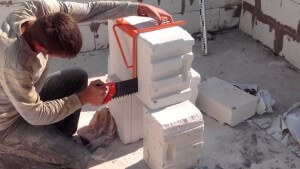
После заливки раствора выжидают полтора часа, при необходимости два часа, до приобретения его прочностных характеристик. Как только раствор приобрел распалубочную прочность, приступают к резке материала на плиты, блоки или панели.
Разрезают массив газобетона на различные формы и геометрические размеры. При небольших объемах работ применяют ручное оборудование, при больших – механическое, в виде электрических инструментов. Если отсутствует возможность приобретения специального инструмента для резки, изготавливают собственноручно ножовку, однако срок службы ее невелик. Профессиональные инструменты для резки – это рубанок, резец и штроборез.
Вернуться к оглавлениюВыдержка
После заливки емкости раствором срезают образовавшиеся верхушки с помощью металлической струны. После этого оставляют газобетонные блоки для выдержки на протяжении двенадцати часов. Оставляют заполненные емкости в помещении или на площадке с предусмотренным накрытием. Важно обеспечить защиту от проникновения прямых солнечных лучей и перегрева залитого раствора. Попадание атмосферных осадков на застывающую массу также нежелательно.
По окончании выдержки блоки извлекают и оставляют досыхать еще на несколько часов. Такая необходимость обусловлена набором прочности, нужной для их складирования. Газобетон достигнет максимальной прочности спустя двадцать восемь дней.
Вернуться к оглавлениюСортировка и упаковка
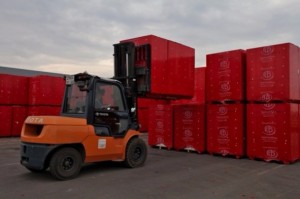
Сортируют газоблоки тремя способами, с помощью которых получают продукцию нужного типоразмера:
- формовка и сушка в емкостях кассетного типа;
- заливка раствора в емкости особой конструкции;
- заливка раствора в металлические емкости без внутренних перегородок.
Упаковку изделий осуществляют после окончательного затвердевания газоблоков. Укладывают их на поддоны и упаковывают с помощью термопленок, после чего перемещают на склад.
Вернуться к оглавлениюВывод
Усовершенствование неавтоклавного газобетона происходит постоянно и благодаря этому его применение становится целесообразней, чем использование автоклавного. Но перед выбором строительного материала и его технологического изготовления, важно обратить внимание на преимущества и недостатки газобетонов. Ведь при необходимости использования материала с высокими прочностными характеристиками, к сожалению, неавтоклавный ячеистый бетон не годится. Зато он отлично подойдет для быстрого возведения малоэтажных построек.
kladembeton.ru
Газобетонные блоки своими руками: технология изготовления
Сегодня для строительства все чаще применяются материалы, которые можно сделать своими руками, закупив только необходимые ингредиенты. Все они характеризуются отличными эксплуатационными особенностями, прочностью; стоимость их выходит в итоге не слишком большая. Одним из таких материалов является газобетон. Укладка блоков простая, а сам материал отличается многочисленными достоинствами включая хорошие теплоизоляционные свойства, важные для строительства дома.
Газобетонные блоки имеют хорошие теплоизоляционные свойства.
Газобетон не является новинкой на рынке, впервые он использовался для строительства еще в начале прошлого века. Активное его применение в сооружении зданий началось около 10 лет назад. Хотя сама технология изготовления газобетона была запатентована Эриксоном, архитектором из Швеции, в далеком 1924 году.
Ранее газобетон изготавливался только в заводских условиях, так как для этого требовалось в точности соблюдать технологию и подбор пропорции для замешивания. Само производство несложное, но вес одного блока, который получается после заливки, не самый малый, поэтому работы надо выполнять хотя бы вдвоем.
Для производства газобетона потребуются:
Таблица производства газобетонных блоков.
- портландцемент;
- кварцевый песок;
- алюминиевая пудра;
- вода;
- известь.
Сам процесс изготовления основан на использовании одного из 2-х методов:
- автоклавного;
- неавтоклавного.
Первый метод применяется в заводских условиях, так как для него необходимо наличие спецоборудования. Блоки после заливки спекаются при специально созданных условиях. Самостоятельно создать их не получится, поэтому практичнее использовать 2-й метод. Бетон заливается в формы и высыхает в естественных условиях. Газобетонный блок затем извлекается и при необходимости разрезается на части. Хотя лучше сразу использовать для заливки формы, которые соответствуют требуемым размерам.
Компоненты для изготовления смеси
Чтобы сделать газобетонные блоки своими руками, необходимо приготовить следующие ингредиенты:
Таблица размеров газобетонных блоков.
- На каждый кубометр готового газобетона (по выходу) требуется примерно 250-300 л воды. Это должна быть чистая питьевая воды. Лучше всего ее брать из поверхностных слоев любых чистых источников.
- На кубометр готового газобетона требуется примерно 260-320 кг цемента. Для самостоятельного изготовления используются марки M500D0, M400D0.
- Карьерный песок, речной, очищенный. Количество его на кубометр готовой смеси составляет 250-350 кг. Лучше всего брать мелкий, размер частиц которого составляет до 2 мм. Ни в коем случае не допускается содержание веток, мусора, глины.
- Специальные добавки для газобетона. Количество 1-3 кг на каждый кубометр готовой смеси.
- Газообразователь, т. е. алюминиевая пудра. Достаточно 0,5-0,7 кг на каждый готовый кубометр бетона. Пудра нужна для того, чтобы в смеси началась реакция, необходимая для газообразования. Во время замешивания начинает выделяться газ, внутри бетона образуются пузырьки, ячейки, которые и придают составу необходимые ему качества.
- Смазка для контейнеров в количестве 0,3-0,5 кг на куб. Перед тем как начать заливку эмульсиями тщательно смазываются формы. Нельзя применять отработанные масла, так как они содержат большое количество сажи.
Сделать газобетон своими руками не так сложно, но важно в точности соблюдать все этапы производства, подобрать ингредиенты для будущей смеси в правильной пропорции.
Список оборудования:
- Формы для заливки будущих газобетонных блоков, которые могут иметь различный размер. Лучше всего приобретать уже готовые контейнеры.
- Струны, которые необходимы для удаления излишков смеси с поверхности форм.
- Бетономешалка, которая будет использована для перемешивания смеси.
Требования к ингредиентам
Таблица сравнения характеристик газобетона и пенобетона.
Самостоятельно сделать большой объем строительного материала не получится, но для сооружения небольшого дома их вполне хватит. Вес одного блока стандартного размера может составлять примерно 650 кг. Поэтому необходимо присутствие нескольких человек не только для выполнения кладки стен, но и для заливки форм, вытаскивания газобетонных блоков из контейнеров. При выполнении всех условий газобетонные блоки получатся прочными и качественными, стоимость их будет меньше, чем при покупке уже готового материала.
Можно использовать специальные установки, которые замешивают газобетон в автоматическом режиме. Их можно арендовать, но зато оборудование самостоятельно дозирует ингредиенты, выполняет замешивание бетона именно того качества, которое необходимо. Расходы на аренду будут оправданы.
Пропорции газобетона могут быть различными, но лучше всего придерживаться следующей формулы (для газобетона D-600):
- портландцемент ПЦ500 D0 – 65%;
- очищенный песок – 30%;
- доломит – 5%;
- В/Т – до 0,48.
Известковая мука, т. е. доломит, может содержать примерно до 10% газобетона, но важно определиться с тем, какой цвет блоков необходим. При большем количестве извести цвет газобетонных блоков будет более светлым. Большое количество пудры также не требуется, она выступает в качестве катализатора реакции газообразования.
Процесс изготовления газобетона
Схема дома из газобетонных блоков.
Чтобы сделать ячеистый бетон, необходимо выполнить несколько этапов, которые включают:
- дозировку ингредиентов, перемешивание сухой смеси;
- добавление воды, замешивание раствора;
- заполнение получившейся массой форм для заливки;
- выдержку смеси для набора прочности, высыхание газобетонных блоков и их извлечение из форм.
Необходимо тщательно отмерить все сухие ингредиенты, нужные для производства газобетонных блоков. Основными материалами являются цемент, известь, песок. Чтобы запустить процесс газообразования, необходимо использовать алюминиевую пудру. После реакции с водой она провоцирует выделение водорода, смесь начинает вспениваться. Пропорции очень важны, так как именно от них зависит прочность, пористость и другие характеристики будущего газобетона.
Схема производства газобетона.
На втором этапе осуществляется перемешивание компонентов. Масса должна получиться однородной. От качества замеса зависит и то, каким будет газобетон после приготовления. Для замешивания необходимо использовать только специальное оборудование. Подойдут бетономешалки, вручную этот процесс не производится.
Когда будущий бетон перемешан, необходимо начинать его заливку по формам.
Формы применяются специальные, лучше всего приобрести уже готовые, которые полностью соответствуют всем требованиям.
Заливка проводится только до половины форм, ни в коем случае нельзя заливать их полностью. Это объясняется тем, что в процессе газообразования смесь сильно увеличивается в объемах, полностью заполняя все формы. После того как увеличение объема закончено, при помощи металлического прута необходимо сверху все излишки смеси убрать, чтобы верхняя часть получилась ровной и гладкой. Производится это примерно через 6 часов после того, как заливка была выполнена.
Как происходит сушка газобетонных блоков?
Правильная и неправильная отделка домов из газобетона.
Далее будущие блоки выдерживаются в формах примерно 12 часов, при этом держать их надо на закрытой площадке. Затем их можно извлекать из контейнеров, далее их на пару суток оставляют на ровной поверхности для набора прочности. Для полного приобретения всех необходимых показателей газобетонный блок надо выдерживать 28 дней.
Во время заливки можно использовать контейнеры различных форм и размеров. Во время планирования надо учесть и то, что некоторое количество материала может уйти на подбор правильной пропорции, так как универсального рецепта нет. Еще некоторое количество может уйти на брак. В любом случае изготовление газобетонных блоков своими руками будет более дешевым, чем покупка уже готовых или использование других материалов для строительства, например, традиционного кирпича.
После того как весь материал готов, может начинаться его укладка. Для этого применяется специальный клеевой раствор, который обеспечивает не такую большую толщину шва, как при цементном растворе. В итоге теплопотери будут меньшие, а прочность выше. Начинается кадка от угла, обязательно надо для каждого ряда соблюдать перевязку, чтобы стена получилась прочной и надежность. Во время кладки необходимо использовать металлические пруты для армирования. Процесс этот несложный, следует заранее проделать в блоках пазы – в них и будут устанавливаться пруты. После этого сверху укладывается слой раствора, начинается кладка следующего ряда.
Газобетонные блоки представляют собой прочный и качественный строительный материал, который используется для различных целей. Сегодня он стал популярен для малоэтажного частного строительства. Некоторые умельцы предпочитают не покупать такие блоки в уже готовом виде, а делать их своими руками. Для этого необходимо в точности соблюдать разработанную технологию изготовления.
opt-stroy.net
Как сделать газобетон своими руками
Можно ли изготовить газобетон своими руками? Этот вопрос сегодня часто звучит на интернет-форумах. Все дело в том, что загородные застройщики, которые отдали предпочтение именно этому строительному материалу, хотят немного сэкономить. Кстати, самостоятельное производство газобетона уменьшает его себестоимость на 30%.
Что такое газобетон? ↑
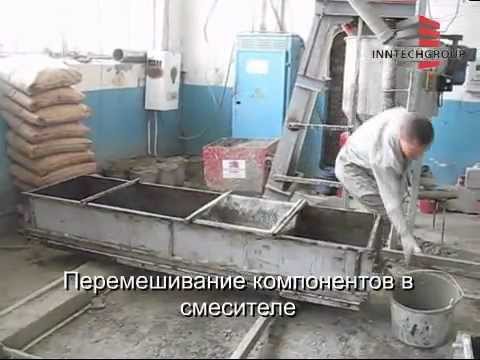
Это одна из разновидностей пористого ячеистого бетона. Чтобы качество было высоким, в процессе производства газобетона в домашних условиях необходимо добиться равномерного распределения пор по всему объему материала.
В настоящее время используется два способа его изготовления: автоклавный и неавтоклавный. В нашем случае выбираем второй вариант. Он, во-первых, не требует использования специального оборудования. Во-вторых, он проще.
Для производства газобетона неавтоклавным способом необходимо использовать четыре основных материала: цемент, песок (можно заменить шлаком или золой), известь (добавляется в небольшом количестве), алюминиевая пудра.
Изготовление газобетона в домашних условиях — сырье и технология ↑
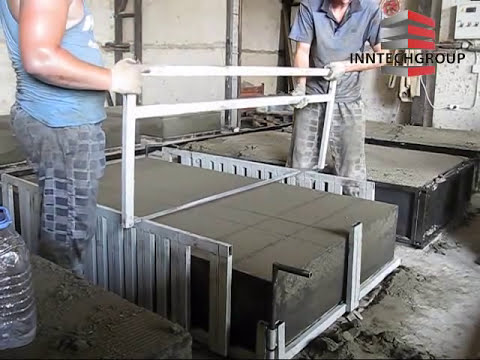
Технология производства газобетона неавтоклавным методом разделяется на несколько этапов:
- Смешивание компонентов сырья в определенных пропорциях;
- тщательное перемешивание смеси в воде;
- заполнение приготовленных форм получившимся раствором;
- подгонка материала под формы и выдерживание его для набора необходимой марочной прочности.
Первый этап заключается в том, что все четыре основных компонента необходимо тщательно перемешать и сделать так, чтобы алюминиевая пудра равномерно распределилась по всему объему сухой смеси. А затем сухая смесь закидывается во вращающийся барабан бетономешалки, в котором заранее налита вода.
Для производства блоков потребуются формы, которые необходимо изготовить из металлического листа. Оптимальный вариант — это разборные формы, с помощью которых процесс выемки блоков производится быстро и без лишних проблем.
Заливать газобетон в формы нужно наполовину— в процессе химической реакции алюминиевой пудры и воды происходит выделение газа, который и будет создавать пузырьки внутри раствора. С появлением пузырьков раствор начнет расширяться практически в два раза.
Начинать четвертый этап нужно по прошествии шести часов, когда закончится химическая реакция. Может случиться так, что раствор поднимется над краями форм. Для того чтобы выровнять блоки точно по форме, необходимо выступившую массу срезать металлической струной. После чего блочный материал в формах складируется в закрытое помещение или под навес. Материал должен простоять так не менее двенадцати часов.
Затем формы распаковываются, и готовые блоки складируются в один ряд. В течение двух суток газобетон наберет необходимую прочность для складирования. А вот использовать блоки в процессе строительства можно только через двадцать восемь дней, когда сам материал наберет свою марочную прочность.
Дополнительная информация ↑
Изменяя размеры и конструкцию форм, можно изготавливать газобетонные блоки различных конфигураций. Это можно отнести к достоинствам производства данного материала. Конечно, по прочностным характеристикам газобетон, произведенный неавтоклавным способом, уступает автоклавному. Но для личных нужд, когда ведется небольшое строительство, вполне подходит.
Изменяя пропорции каждого компонента, можно добиться разных прочностных показателей бетонного раствора. Но стандартная рецептура соответствует нижеследующим показателям, которые измеряются в процентах:
- Цемент 51-71;
- Песок 20-40;
- Известь 1-5;
- Алюминиевая пудра 0,04-0,09;
- Вода 0,25-0,8.
И чтобы закрепить полученные знания, можно посмотреть учебные ролики, в которых показано как сделать газобетон — видео есть на нашем сайте.
mastter.ru
Технология производства газобетона
Благодаря автоклавированию, непосредственно после его окончания газобетон имеет соответствующую прочность, долговечность и морозостойкость. Автоклавирование исключает возможность усадки, а также обеспечивает долговечность газобетона.
Газобетон хорошо подлежит обработке простейшими инструментами: пилится, сверлится, строгается. В него легко забиваются гвозди, скобы. Со временем газобетон становится твёрже. Дома из газобетона сегодня очень популярны в России. К тому же, проекты домов из газобетона и цена на него, доступны всем.
Автоклавная обработка газобетона производится не только для того, чтобы ускорить процесс твердения смеси. Основной смысл состоит в том, что в автоклаве при температуре +180 °С и давлении до 14 бар в газобетоне образуется новый минерал — доберморит. Благодаря этому повышается прочность материала и, что особенно важно, в несколько раз уменьшается усадка. За счет своих характеристик автоклавный бетон имеет гораздо больше способов применения. Он может использоваться, например, в армированных конструкциях — перемычках, панелях, и др. Ячеистый бетон автоклавного твердения имеет пониженную трещиностойкость и морозостойкость. Автоклавная обработка позволяет в более короткие сроки получать изделия с достаточно высокой прочностью при пониженном расходе вяжущего. У автоклавной обработки имеются и недостатки: дорогостоящее оборудование, специфика его эксплуатации, требующая высококвалифицированного обслуживающего персонала, высокая металлоемкость автоклавов, низкий коэффициент использования внутреннего объема автоклава. Мелкосерийное производство при автоклавном способе оказывается экономически невыгодным.
Автоклавный газобетон производится на крупных заводах и на стройплощадку попадает в виде готовых блоков. Изготовление этого материала на малом производстве или изготовление газобетона автоклавного своими руками - невозможны.
Основными компонентами этого материала являются цемент, кварцевый песок (либо зола унос), газообразователи, также возможно добавление гипса и извести. В качестве специализированных газообразователей используются алюминиевые пасты и пудры. Сырьё смешивается с водой заливается в форму и происходит реакция воды и газообразователя, приводящая к выделению водорода, который и образует поры, смесь поднимается как тесто. После набора пластической прочности, массив разрезается на блоки, плиты и панели. Ипользование высокотехнологичного резательного оборудования позволяет разрезать полученный массив с высокой точностью на блоки и плиты.
После этого изделия подвергаются закалке паром в автоклаве, где они приобретают необходимую жёсткость, либо высушиваются в условиях электроподогрева.
Процесс производства ячеистого бетона напоминает выпекание хлеба: в смесителе замешивается вода, цемент, молотый кварцевый песок, тщательно размельченная известь и гипс (не на всех производствах), добавляется газообразователь. В теплой влажной камере смесь поднимается.
Процесс газообразования происходит вследствие химической реакции между гидратом окиси кальция и алюминием; выделяющийся при этом водород вызывает вспучивание раствора, который, затвердевая, сохраняет пористую структуру.
При определении состава газобетона необходимо обеспечить заданную объемную массу и его наибольшую прочность при минимальных расходах порообразователя и вяжущего вещества. При этом структура газобетона должна характеризоваться равномерно распределенными мелкими порами правильной шаровидной формы.
Объемная масса газобетона и его пористость зависят главным образом от расхода порообразователя и степени использования его порообразующей способности. Некоторое влияние на них оказывают температура смеси и количество воды, принятое для затворения смеси, т.е. водотвердое отношение В/Т. Увеличение В/Т повышает текучесть смеси, а следовательно улучшает условия образования пористой структуры, если обеспечивается достаточная пластичная прочность смеси к концу процесса газообразования.
Прочность газобетона зависит также от характера его пористости, размеров и структуры пор и прочности межпоровых оболочек. С увеличением В/Т до оптимального значения, обеспечивающего наилучшие условия формирования структуры смеси, прочность газобетона повышается. Прочность оболочек, в свою очередь, зависит от оптимального соотношения основного вяжущего и кремнеземистого компонента, В/Т, а также условий тепловлажностной обработки. Из этого следует, что применение смесей с минимальным значением В/Т при условии образования высококачественной структуры (например виброспучиванием) позволяет получить газобетон более высокой прочности.
Для изготовления газобетона применяют портландцемент марок 300, 400, 500, удовлетворяющий требованиям ГОСТ 970-61. Производство газобетона предъявляет специальные требования к портландцементу в отношении щелочности цементного теста – рН теста не должна быть ниже 12. Щелочность цемента определяется количеством свободной СаО и суммой Na2О и K2О. По данным работы газобетонных заводов, содержание щелочей (Nа2О, К20) в 1 л раствора цемента не должно быть менее 75 мг. В случае недостаточной щелочности раствора в газобетонную массу следует дополнительно вводить известь или щелочь в виде каустической соды (NаОН).
При применении в качестве основного вяжущего извести особое внимание уделяют значительному количеству активных окиси кальция (СаО) и магния (МgО). Общая активность извести не должна быть менее 75%, количество МgО - не более 1,5%. В производстве можно применять известь. Известь должна быть равномерно обожженной.
Введение извести как добавки к цементу сокращает расход цемента и одновременно увеличивает щелочность раствора, обеспечивая энергичное протекание реакции газообразования:
3 Са(ОН)2 + 2 Аl + 6 Н2О 3 СаО·Аl2О3·6Н2О + 3 Н2
В качестве кремнеземистого компонента в производстве газобетона применяют речной или горный кварцевый песок, золу-унос тепловых электростанций, маршалит и другие материалы. Кварцевый песок для изготовления газобетона и газосиликата должен быть чистым, без примесей глины и органических веществ, с содержанием SiO2 не менее 80%. Присутствие глины замедляет твердение газобетона и уменьшает его прочность. Органические примеси вредно сказываются на протекании реакции газовыделения; вспучивание газобетона при наличии органических примесей ухудшается. Зола-унос может применяться в производстве газозолобетона при содержании SiО2 более 55%. Зола-унос должна иметь незначительное количество сернистых соединений, несгоревших частиц угля и карбонатов кальция.
Важнейшей технологической особенностью получения высококачественных газобетонных изделий максимальной пористости и достаточной прочности является создание оптимальных условий для двух одновременно протекающих процессов газовыделения и газоудержания. Необходимо обеспечить соответствие между скоростью реакции газовыделения и скоростью нарастания структурной вязкости цементного теста или раствора. При этом выделение газа должно как можно полнее закончиться к началу схватывания системы цемент - вода. Протекание процесса газообразования определяется большим количеством различных факторов. Наибольшее влияние на скорость этого процесса оказывают вид, количество и свойства газообразователя, щелочность и температура среды и т. д.
Изготовление газобетона осуществляется мокрым или сухим способом. Экономически более целесообразным является мокрый способ, при котором помол кремнеземистого компонента или его смеси с известью производится в присутствии воды с получением шлама. При сухом способе помол и смешение компонентов осуществляются в шаровых мельницах в сухом виде. Песок размалывают в шаровых мельницах. Для осуществления мокрого помола в мельницу вводят подогретую воду. При применении в производстве извести, последнюю вводят в мельницу для совместного помола с песком. Из мельницы шлам пропускают через сито для отделения от крупных включений. Далее шлам собирают в сборнике и с помощью мембранного насоса или путем передавливания сжатым воздухом подают в шламовый бассейн или шламовый силос. Для предотвращения разделения шлама, т. е. осаждения частиц песка, шлам в бассейнах и силосах подвергают непрерывному перемешиванию. Одновременно производят барботаж шлама.
Дозировка шлама, подогрев и предварительное смешение осуществляются в ванне-дозаторе. Для подогрева шлама до 40-45° применяют острый пар. Дозировка цемента – весовая. Газообразователь взвешивают и подают в бачок с клееканифольной эмульсией, снабженный пропеллерной мешалкой.
Окончательное интенсивное смешение всех компонентов газобетонной массы происходит в передвижной самоходной пропеллерной газобетономешалке. Материалы в газобетономешалку загружают в определенной последовательности. Сначала заливают песчаный шлам, затем немолотый песок (в случае необходимости) и в последнюю очередь – цемент. После этого в течение 2-3 мин перемешивают всю массу. Введение алюминиевой суспензии определяет начало перемешивания газобетонной массы. Одновременно с этим газобетономешалка начинает передвигаться. Перемешивание газобетонной массы должно продолжаться 2-3 мин. Тщательное перемешивание массы обеспечивает однородность смеси и равномерность вспучивания. Излишняя продолжительность перемешивания вредна, так как возможно начало интенсивного газообразования в газобетономешалке. При этом теряется часть выделившегося газа и три заливке в формы газобетонная масса не даст нужного вспучивания. Разливают массу в формы через отверстия в нижней части мешалки при помощи гибких резинотканевых рукавов. Формы до заливки газобетона смазывают минеральным маслом или специальными эмульсиями для предотвращения сцепления газобетона с металлом форм. Газобетонную массу заливают с учетом вспучивания на 2/3 или 3/4 высоты формы.
После заливки газобетонной массы начинается вспучивание. процесс вспучивания продолжается 30-40 мин. После вспучивания происходит схватывание и твердение газобетона. Для ускорения схватывания и твердения газобетона, а также для ускорения процесса газовыделения в цехе по производству газобетонных тонных изделий температура воздуха должна поддерживаться не ниже +25°. Формы, в которых вспучивается и твердеет газобетон, нельзя передвигать, подвергать сотрясениям и ударам, так как вспученная, но не затвердевшая масса может при этом осесть. При вспучивании газобетонная масса образует так называемую горбушку, которую после затвердевания срезают ручными или механическими ножами. Затем застывшую массу разрезают на изделия нужного размера, формы устанавливают на автоклавные вагонетки в 2-3 яруса по высоте и загоняют в автоклав для ускоренного твердения.
На сайте Вы можете найти информацию: видео о газобетоне, возведение стен, стоимость газобетона, производители газобетона, что лучше - газобетон или пенобетон, отзывы, а также купить газобетон.
litebeton.ru
Состав газобетона: виды, изготовление в домашних условиях,
Из чего состоит газобетон
Газобетон – это искусственный камень, который используют для возведения стен в индивидуальном строительстве. Он подходит для сооружения несущих конструкций, внутренних перегородок и заполнения межкаркасных пространств. Газоблоки не дают большой нагрузки на фундамент, поскольку имеют ячеистую структуру и малый вес. Это экономичный стройматериал, обладающий высокими теплоизоляционными свойствами.
Состав и способ получения газобетона
Существует несколько типов классификации ячеистого бетона: в зависимости от назначения, формы, технологии производства и состава.
1. По способу обработки различают автоклавный и неавтоклавный газобетон.
2. По назначению газоблоки могут быть теплоизоляционным, конструкционным или конструкционно-теплоизоляционным. Они имеют определенную маркировку, например, газобетон d500 относится к классу конструкционно-теплоизоляционных блоков.
3. По форм-фактору делятся на U-образные, прямые и паз-гребневые.
Газоблоки изготавливают из песка, цемента, извести, воды, гипса и алюминиевой пудры. Также в производстве могут использоваться вторичные и побочные промышленные материалы, такие как шлак и зола. В зависимости от состава газобетона, его классифицируют на:
В искусственно синтезированный камень строительная смесь преобразуется лишь при определенных условиях. Для его получения используют технологию автоклавного затвердения. В этом случае состав застывает под влиянием насыщенного пара и высокого давления, меняя свою структуру. В смеси образуется минерал тоберморит, который придает материалу прочность. Таким образом получают автоклавный газобетон.
Бетон, затвердевающий в естественных условиях, называют неавтоклавным. Он имеет ячеистую структуру, но отличается по своим свойствам от газоблоков, изготовленных по специальной технологии. Этот стройматериал больше подвержен усадке при эксплуатации, поэтому его целесообразно применять в случае небольших нагрузок. Чтобы увеличить прочностные характеристики неавтоклавных блоков, в исходный состав добавляют различные армирующие вещества и наполнители. Снизить усадочную деформацию позволяет применение полиамидных пластмасс при армировании.
Производство неавтоклавных блоков не требует дорогостоящего оборудования, поэтому их можно сделать самому.
Газобетон своими руками
Процесс производства состоит из нескольких этапов:
- подбор и смешивание компонентов;
- заполнение форм раствором;
- выдержка состава для набора прочности;
- извлечение из форм.
В универсальном составе для получения газобетона содержится цемент, песок, известь, алюминиевая пудра. Исходные добавки и их пропорции могут меняться, в зависимости от наличия сырья и требований к готовому стройматериалу. Например, в автоклавном производстве песок иногда заменяют золой или шлаком. А для получения стройматериала с меньшей плотностью можно делать газобетоны на основе смол ТЭС.
При изготовлении газобетона в домашних условиях необходимо правильно рассчитать соотношение расходных материалов и учесть особенности укладки и погрешности замеров. Но существуют и стандартные рецепты смеси для газоблоков, в которых указаны следующие пропорции:
Данные вещества используются и при автоклавном производстве. Ориентируясь на приведенное в рецептуре соотношение, можно рассчитать приблизительное количество компонентов, которые войдут в состав на 1 м3 газобетона:
- Портландцемент – 90 кг;
- Вода – 300 л;
- Газообразователь – 0,5 кг;
- Известь – 35 кг;
- Песок – 375 кг.
Однако идеального состава в домашних условиях можно добиться лишь опытным путем, поскольку многое зависит от качества исходных компонентов. Повлиять на течение химической реакции может как температура воды, так и марка цемента.
Инструкция по самостоятельному изготовлению неавтоклавного газобетона
Для получения газоблока дома не потребуются сложная аппаратура и инструменты. Главное – четко следовать пунктам приведенного ниже пошагового руководства и использовать компоненты в определенном соотношении, а не «на глаз».
1. Исходя из указанных пропорций вычислить необходимое количество ингредиентов.
2. В первую очередь, необходимо смешать портландцемент с предварительно просеянным песком.
3. В полученную смесь влить воду и все тщательно перемешать.
4. Добавить в раствор другие компоненты. Алюминиевая пудра всыпается в последнюю очередь. В приготовлении как неавтоклавного, так и автоклавного газобетона одинаково важен процесс смешивания ингредиентов. Для равномерного распределения воздушных пузырьков лучше использовать бетономешалку.
УМЕНЬШИТ РАСХОД до 50%! Это нужно знать каждому!
5. Полученный раствор разливается в специальные формы, которые изготавливаются из металлических листов или деревянных досок. Чтобы застывший газобетон было легче достать, лучше использовать разборные конструкции. Кроме того, форму рекомендуют смазывать машинным маслом, разведенным с водой.
6. Заливать смесь нужно наполовину, поскольку она в процессе химической реакции расширяется практически вдвое. Этот процесс занимает около шести часов, после чего можно выравнивать блоки, срезая выступившую массу.
Формирование в этом случае длится дольше, чем для автоклавного газобетона – требуется не менее 12 часов, чтобы смесь затвердела. Для ускорения процесса застывания состава рекомендуют добавить растворимые соединения натрия (соду) на этапе приготовления раствора. Марочную прочность материал набирает после 28 дней выдержки. Готовый неавтоклавный газоблок, приготовленный своими руками, подходит для малоэтажного строительства, например, для возведения одноэтажного дома или гаража.
Автор:Иван Яскевич
http://stroitel-list.ru
legkoe-delo.ru
СООТНОШЕНИЕ МЕЖДУ ВЯЖУЩИМ И ПУЦЦОЛАНОМ
ГАЗОБЕТОН НА ПЕРГИДРОЛЕ
Пропорции составляющих в газобетонной смеси устанавливаются опытным путем и изменяются в значительных пределах.
Соотношения между вяжущим и пуццоланом выбирают в зависимости от требуемой прочности и условий твердения изделий. Они колеблются в широких пределах, от пропорции 1:0 (чистые цементные шламы) до 1:4 по весу.
Для цементного газобетона, твердеющего в нормальных условиях или при пропаривании, пропорции составляющих могут изменяться от 1 :0 До 1: 1.
Естественно, что от расхода вяжущего зависит прочность газобетона —с увеличением доли наполнителя в составе сухой смеси прочность газобетона снижается — прочность при сжатии, Как чтО видно из табл. 17, падает па bU"/0, а при изгпое -■-на 50% (при изменении состава смеси от 1 :0 до 1:1).
Таблица 17 Зависимость прочности автоклавного газобетона от состава сухой смеси (',' = 1 т/м3)
|
Для автоклавного газобетона пропорции эти изменяются в более широких пределах и могут составлять от 1 : 2 до 1:4, чаще всего 1 :3. Расход вяжущих в данном случае определяется, с одной сторонк, требуемым объемным весом газобетона и соответствующей ;ему прочностью, с другой стороны, — минералогическим составом цемента.
При достаточном содержании силикатных минералов в цементе взаимодействие их с высокодисперспым пуццоланом в условиях автоклавной обработки идет, как это известно, вплоть до образования1 низкоосновных гидросиликатов со степенью основности 0,9. 'Таким образом, при наличии цемента с высоким содержанием силикатов кальция и тонкомолотого пуццолана большая часть1его при автоклавной обработке будет активно использована. 1
Как это видно из табл. 18, оптимальным соотношением су. хих составляющих в смеси Воскресенского цемента и молотого кварцевого песка следует считать 1 : 2.
Воскресенский цемент содержит C3S до 48%, C2S примерно 23%. :
' Т а б л и ц а 18 Зависимость прочности безавтоклавного газобетона (От состава сухой смеси (7=0,7 т/м')
|
Дли 'ііго чтооы повлечь в реакцию образования гидросили - катоз кальция большое количество пуццолана, следует в состав газобетона вводить добавки извести.
Добавки извести значительно увеличивают прочность автоклавного газобетона. В табл. 19 показано влияние добавок гидратной извести на прочность газобетона на Воскресенском цементе. Выше уже указывалось, что содержание силикатов кальция в этом цементе, особенно C3S, недостаточно для активного взаимодействия с большим количеством високодисперсного кремнезема.
Таблица 19
Влияние добавок гидратной извести на прочность автоклавного газобетона состава 1:2 (7=0,8 г/лі3)
Состав вяжущего в % | Проч ность | При сжатии | |
Цемент | Гндратнрованная | В кГ/см2 | J в % |
Известь | |||
100 | 0 | 49 | I 41 ,5 |
95 | 5 | 82 | 1 80 |
90 | 10 | 103 | I 100 |
Газобетон изготовляют не только на цементах с небольшими добавками извести-пушонки. Зачастую используется смешанное вяжущее, состоящее из цемента и 30—50% извести-ки - пелки. Применение подобного вяжущего в производстве автоклавных газобетонов весьма эффективно.
Изменение состава смеси влияет и на объемный вес получаемого газобетона. На рис. 27 показано, что с уменьшением рас-
Тт/»3 >,2
O,s
0,8
<0 II V2
Состой сухой смеси О
Рис. 27. Зависимость объемного веса от состава
Газобетонной смеси а —влияние соотношения между цементом и молотым песком; 1 — автоклавная обработка; 2 — пропаривание; б —влияние добавки Са(ОН)г на автоклавный газобетон состава 1 : 2
Хода цемента, т. е. с увеличением доли пуццолана до 1 : 2, увеличивается газоудерживающая способность смеси и падает объемный вес.
Преимущество применения газобетона, как и других видов ячеистых бетонов, основано на возможности сооружать из него стены, толщина которых значительно меньше, чем у стен из других стеновых материалов. Это объясняется его …
Объемный вес газобетона определяется не только расходом газообразователя и количеством выделяющегося газа, но также и газоудерживающей способностью смеси. С увеличением расхода газообразователя до определенного предела происходит уменьшение объемного веса газобетона. …
msd.com.ua
В отличие от тяжелого бетона автоклавный газобетон имеет гораздо меньшую плотность. Благодаря автоклавной обработке при производстве газобетона при повышенной влажности, температуре и давлении химические реакции гидратации цемента успевают завершиться к концу автоклавирования газобетона. Кроме того, при производстве газобетона в условиях автоклава при образовании цементного камня газобетона протекают специфические реакции образования высокопрочных микрокристаллических структур (тоберморита 1), которые мало характерны для образования цементного камня в условиях атмосферного твердения. Поэтому, когда блоки или панели газобетона извлекают из автоклава и охлаждают – они практически готовы к использованию. Фактически 28-суточная прочность бетона может быть достигнута за 24 ч автоклавирования или даже меньший период времени. В отличие от тяжелого бетона автоклавный газобетон практически гомогенен в массе: его структура содержит лишь единичные микроскопические остатки (менее 50 мкм) непрореагироваших в процессе производства газобетона веществ (силикаты или алюминаты – в зависимости от состава). Все же основные компоненты смеси для производства автоклавного газобетона являются участниками химических реакций – даже мелкие инетрные при обычных условиях заполнители (песок, зола). Песок, всегда остающийся инертным при производстве обычного тяжелого бетона, принимает участие в химических реакциях образования газобетона из-за высокой температуры и давления при автоклавировании. Важно, что при автоклавировании достигаются улучшенные показатели бетона: повышенное сопротивление бетона сульфатной агрессии к другим формам химического воздействия, к циклам замораживания и оттаивания. Автоклавный бетон характеризуется низкой усадкой и пониженной влагопередачей. Технологические стадии производства автоклавного газобетона На первой стадии производства автоклавного газобетона смешиваются цемент, известь, песок (условно-усредненный состав) и газообразующее вещество (например, мелкодисперсный порошок алюминия) с добавлением воды и образованием суспензии. Также добавляется небольшое количество гипса для предупреждения немедленного загустевания смеси (ложного схватывания). Желаемая конченая плотность газобетонного блока зависит от количества газообразователя, который будет влиять на степень пористости газобетона. Схема основных этапов производства автоклавного газобетона |
На второй стадии производства газобетона полученную суспензию разливают в крупные формы, которые напоминают небольшие железнодорожные вагоны с откидывающимися стенками. На этой стадии производства газобетона в течение нескольких часов протекает реакция гидратации цемента 2 с образованием гидросиликата кальция и алюминатной кристаллической структуры эттрингита 3 и /или моносульфата кальция и алюминия. Бетонная смесь постепенно загустевает (схватывается), при этом «поднимаясь» в форме как пирог, из-за выделения в результате химических реакций алюминия с щелочами газообразного водорода. Эти пузырьки газа начинают создавать газовые поры в застывающей суспензии газобетона. Реакции даже на этой стадии протекают достаточно быстро из-за повышения температуры смеси при протекании реакций гидратаций с выделением тепла. На следующей стадии производства газобетона, через несколько часов, когда бетонная смесь увеличилась в объеме до определенной высоты в формах и достаточно сильно схватилась, формы движутся к проволочному резаку и нарезается на блоки необходимого размера. На этапе нарезки блоки еще мягкие и легко повреждаются, но в тоже время уже достаточно жесткие, чтобы сохранять форму после нарезки. На следующем этапе производства газобетона блоки загружаются в автоклав. Рабочая температура и давление автоклавирования достигаются за несколько часов, и затем блоки пропариваются в течение 8-10 или более часов (зависит от конкретного производителя и требуемой прочности газобетона). Главной особенностью химических реакций, протекающих при автоклавировании, является образование в структуре цементного камня микрокристаллического 1,1 нм тоберморита. Именно высокопрочная кристаллическая структура определяет высокие показатели автоклавного газобетона при кажущейся «легковесности» и «непрочности». Во время неавтоклавной стадии схватывания бетонной смеси при нормальной температуре и атмосферном давлении цемент в воде подвергается гидратации с образованием продуктов идентичных продуктам гидратации при производстве тяжелого бетона или неавтоклавного пенобетона: гидросиликата кальция, гидроксида кальция, эттрингита и / или моносульфата. На фазе автоклавирования при производстве газобетона основным конечным продуктом является тоберморит. Однако небольшое количество других гидратных фаз также будет присутствовать в готовом газобетоне. Также часть гидратных фаз образуется в виде промежуточных продуктов протекающих реакции при автоклавировании, в основном в кристаллической форме - CSH(l). Этот гидрат имеет слоистую структуру, аналогичную структуре некоторых глинистых минералов, таких как монтмориллонит и галлуазит. При соотношении кальция и кремния 0,8 до 1,0 образуется 1,4 нм нестойкий тоберморит (C5S6H9). Но уже при 55°С 1,4 нм тоберморит превращается в 1,1 нм тоберморит (C5S6H5). 1,1 нм тоберморит обладает большей плотностью, не стареет со временем и не дает усадки при нагревании даже до 300°С из-за того, что обладает двойными силикатными связями в своей структуре. Через несколько часов после начала автоклавирования по мере набора рабочей температуры и давления в бетонной смеси песок постепенно вступает в химические реакции и обычные продукты гидратации цемента исчезают: гидроксид кальция из извести и от гидратации цемента постепенно расходуется вступая в реакцию с доксидом кремния из песка, формируя главное промежуточное соединение - гидросиликат кальция CSH (I). При продолжении обработки газобетона в автоклаве из гидросиликата кальция CSH (I) образуется 1,4 нм тоберморит, разлагающийся до 1,1 нм тоберморита. При этом общая доля гидросиликата кальция CSH (I) снижается, а количество 1,1 нм тоберморита постепенно увеличивается. Виды тоберморита могут отличаться по своим свойствам. «Нормальный» 1,1 нм тоберморит, образующийся в автоклавном ячеистом бетоне, производимом из цемента, извести и песка подвержен небольшой усадке. Кристаллическая структура тоберморита образующегося при производстве автоклавного ячеистого бетона производимого из смеси цемента, извести и золы практически не подвержена усадке, и такой тоберморит называется «аномальным». В конченом продукте всегда содержатся различные пропорции «нормального» и «аномального» тоберморита. Итак, конечными продуктами автоклавирования газобетона главным образом являются:
Доля образовавшегося тоберморита и количество остаточных непрореагировавших веществ зависит от продолжительности и условий автоклавирования. После извлечения из автоклава газобетонные блоки остывают и упаковываются в полиэтиленовую пленку для хранения или транспортировки. |
dom.dacha-dom.ru