Изготовление керамзитобетонных блоков своими руками. Керамзитоблока состав
Керамзитобетонные блоки своими руками: состав и технология изготовления
Возвести дом своими руками — одна из важных целей жизни настоящего мужчины. Если бюджет не ограничен, можно нанять строительную бригаду, а если хочется сэкономить — даже производство материала придется взять в свои руки. В последнее время в строительстве нередко применяются керамзитобетонные блоки, имеющие высокие звуко- и теплоизоляционные свойства, абсолютно экологичный состав.
Изготовить керамзитобетонные блоки своими руками совсем несложно, главное — соблюдать технологию производства, купить нужное количество компонентов. Вы будете приятно удивлены полученным результатом, а еще сохраните свои деньги.
Технология изготовления
Цемент, песок и вода являются связующими веществами, а главные качества готовому материалу придает керамзит. Цемент нужен марки М400 и выше, песок должен быть чистым и мелким. Можно добавить в состав обычный стиральный порошок, он способен увеличить пластичные свойства замеси. В домашних условиях также можно использовать средство для мытья посуды или жидкое мыло на замену ПАВ, которые образуют воздушные поры, повышают морозо- и влагоустойчивость материала. Бетон лучше готовить в бетономешалке (ее можно арендовать) или же вручную, когда требуется малое количество стройматериала. С помощью совковой лопаты или мастерка следует аккуратно всыпать сначала сухие компоненты, а затем, помешивая, добавить воду.
Керамзитобетонная смесь должна некоторое время постоять, затем нужно тщательно перемешать все до однородной массы, напоминающей пластилин.
Вернуться к оглавлениюПодготовка материалов и инструментов
Для того, чтобы сделать керамзитобетон своими руками вам понадобятся:
- керамзит;
- цемент;
- песок;
- вода;
- доски;
- металлический лист;
- мастерок;
- лопата;
- бетономешалка.
Подготовка опалубки
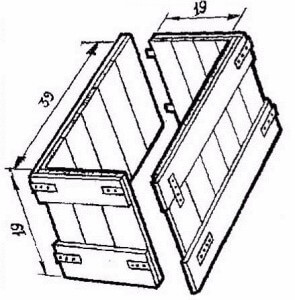
Чтобы придать форму будущему изделию, понадобятся деревянные доски толщиной не менее 2-х см, тонкий металлический лист, ножовка, рулетка, карандаш. Что касается размеров, то обычно выбирают стандартные, например, кирпича или шлакоблока. Определившись с размером, можно приступать к разметке, а затем ножовкой вырезать из досок 3 части: поддон и 2 половины в виде буквы «Г», далее соединить все металлическими уголками. Чтобы блоки было легче вытягивать, к доскам с внутренней стороны прибивается лист металла, а если его не нашлось, форма изнутри тщательно обрабатывается машинным маслом. А чтобы форма не меняла своих размеры, на торцах половинок делаются специальные затворы.
Вернуться к оглавлениюВыбор пропорции керамзитобетона для раствора
- Портландцемент М400 -одна часть.
- Керамзит — 6-8 частей или 350-500 кг на 1м3. Отмерять можно ведрами, учитывая, что в такой десятилитровой емкости поместится 3-5 кг керамзита.
- Песок фракцией менее 5 мм — две части.
- Вода — 0,8-1 часть; количество воды на 1м3 для фактурного слоя нужно определять по консистенции на месте.
- Стиральный порошок — одна часть.
Формовка
Отливать блоки нужно в большом помещении с максимально ровными полами. Внутри не должно быть сыро, а рекомендуемая температура воздуха составляет около 15-18°С. Теперь нужно поставить готовую опалубку для керамзитобетонных блоков на ровную твердую металлическую поверхность и желательно под навесом, обеспечивая защиту от попадания прямых солнечных лучей и дождя.
Стены формы перед тем, как заливать керамзитобетон, надо смазать обычным машинным маслом изнутри, а основание слегка посыпать песком и только тогда залить смесь. Чтобы в дальнейшем облегчить кладку керамзитоблоков, следует класть небольшое количество керамзитобетона. Керамзитобетонный блок, как правило, формуется лицевой стороной вниз и выкладывается на поддон.
Вернуться к оглавлениюУплотняем раствор
Так как керамзит обладает большим количеством воздушных пор, он легче, чем состав бетона, и будет всплывать на поверхность, делая блоки неровными, поэтому в самом начале затвердевания керамзит нужно утрамбовать внутрь блока. По ГОСТу керамзитоблоки сначала нужно подвергнуть вибрационному прессованию, используя специальный станок, а затем высушить в печи. В домашних условиях станок можно заменить похожими движениями лопаты, а затем трамбовать деревянным бруском до тех пор, пока на поверхности не появится «цементное молоко». Верхнюю часть блока в форме можно выравнять при помощи мастерка.
Демонтаж опалубки
Через 24 часа можно разобрать форму, расцепив затворы, и вытащить утрамбованный блок. Если это не удается сделать с первого раза, на дне формы можно просверлить небольшое отверстие, чтобы к блоку поступал воздух и он быстрее вышел.
Вернуться к оглавлениюСушка
Время высыхания составляет примерно двое суток, но чтобы придать нужную прочность, блокам лучше дать постоять еще 28 дней, накрыв полиэтиленом, чтобы избежать испарения жидкости. Через месяц затвердевания блоки будут полностью готовы для кладки стен. Из 100 кг керамзитобетонной смеси получится 9-10 пустотелых блоков стандартного размера (190*190*390 мм) весом по 16-17 кг, но если их размер уменьшить, количество, соответственно, увеличится.
Вернуться к оглавлению
Специальное оборудование
Если вам не жалко своих денег, для качественного материала не лишней будет покупка специального оборудования. Оно облегчит изготовление керамзитоблоков своими руками, повысит их качество, уменьшит время сушки. Прежде всего надо выбрать ровное, желательно бетонное основание, которое уменьшит вибрацию, способную разрушить готовые блоки. Специальную площадку можно заменить поддонами.
Бетономешалка — незаменимая вещь при замесе бетонного раствора, она сделает его идеально однородным. Лучше покупать механизм объемом не менее 130 литров. Станок для вибропрессования. Состоит из корпуса, в котором уже имеются емкости с пустотами, и вибратора. Процесс производства одного блока занимает не более 3 минут. Используя такой станок, возможно изготовить тротуарную плитку, бордюры, стеновые блоки с минимальными затратами
Имея хотя бы этот перечень оборудования, за один день можно здорово набить руку и приготовить около 150 керамзитоблоков своим трудом. Если пригласить бригаду, результативность увеличится вдвое, а то и втрое.
kladembeton.ru
Как выбрать хорошие керамзитоблоки

Сейчас на строительном рынке так много предложений о продаже керамзитоблоков, что у покупателя разбегаются глаза. Цены на блоки могут сильно отличаться, и это вызывает вопросы о причине снижения цен.
Чтобы помочь вам разобраться и не ошибиться с выбором при покупке, мы провели исследование блоков разных производителей и сравнили их свойства.
Состав керамзитоблока
Блок состоит из 4 компонентов, каждый из которых выполняет определенные функции:
- Дробленый керамзит - повышает свойства теплопроводности, делает блок "теплым". Мелкофракционный материал лучше сцепляется с цементным раствором и повышает прочность блока.
- Цемент - увеличивает прочность блока.
- Песок и вода - служат для "сцепки" компонентов.
Многие "гаражные" производители, стремясь предложить более низкую цену, экономят на составляющих блока. Как следствие, снижается качество блоков, и строительство из них будет ненадежным или даже не безопасным.
Есть несколько способов, с помощью которых производители могут экономить на себестоимости блока.
качественный
некачественный
Больше песка, меньше керамзита и цемента.
Такие блоки отличаются "более желтым" цветом и большим весом. Т.к. доля керамзита и цемента снижена, такой блок будет не теплым и менее прочным.
Часто для того, чтобы скрыть излишнюю «желтушность» блока, производители используют органический метиленовый синий краситель, больше известный как синька.
качественный
некачественный
Ультрамариновая синька - это синяя минеральная краска в виде порошка, известная своей способностью уничтожать желтизну.
Внешний вид такого блока уже не так сильно отличается от качественного. Однако, если внимательно присмотреться, можно заметить синие разводы.
Минимум керамзита
качественный
некачественный
За счет большого количества цемента, эти блоки очень крепкие, но не теплые. Их использование увеличивает нагрузку на фундамент. Кроме того, за счет большего веса доставка таких блоков обходится значительно дороже.
Чтобы отличить такие блоки, достаточно их взвесить. Чем меньше керамзита и больше цемента в блоке, тем более тяжелым он будет. Примерный вес нормального блока – 13 кг.
Слишком много керамзита
Встречаются также случаи, когда производитель не экономит на сырье, а наоборот. У некоторых продавцов в блоках превышена норма содержания керамзита.
Если блок перенасыщен керамзитом, то он получается слишком хрупким. Нет сомнений, это самые теплые блоки, но для несущих стен они не подойдут, т.к. ломаются простым ударом кулака.
Мы советуем покупать блоки только у проверенных производителей, ведь, как известно, "скупой платит дважды". Сэкономив на блоках, вы рискуете качеством вашего строения, его безопасностью и надежностью.
rosblok56.ru
Керамзитобетонный блок по ГОСТу
Но чтобы такой строительный материал служил долго и обладал нужными параметрами, он должен изготавливаться согласно ГОСТ.
Детальная информация содержится в документе 6133–99, основную суть которого и раскроем дальше. Это разрешит понять основные требования к готовой единице каждого элемента без необходимости искать специальную документацию.
Подбор состава: рекомендации и таблица
Существуют такие рекомендации общего характера, которые всегда стоит учитывать, выбирая керамзитобетон для конкретного строительства:
- Для производства блоков предпочтительно использовать портландцемент с маркой 400 и больше.
- Если подразумевается тепловая обработка элементов, то в качестве вяжущего компонента раствора применяется алитовый цемент.
- Можно применять гравий керамзитовый (без песка), кварцевый песок (повышает прочность и упругость), цемент гидрофобный – это снижает уровень водопоглощения блоком.
При изготовлении материала с максимально высокой прочностью в его состав не входят пластификаторы – они его делают менее прочным.
Также стоит учитывать, что для увеличения прочности материала добавляется больше вяжущего вещества, а это в свою очередь способствует увеличению массы. Именно поэтому рекомендуется при изготовлении использовать портландцемент высоких марок.
Для точной ориентации с пропорциями, которые используются при производстве блочного керамзита можно воспользоваться следующей таблицей.
1700 | 0.38 | 0,62 | 700 | 720 | 140 | 0.83 |
1700 | 0.41 | 0,56 | 600 | 0.88 | ||
1600 | 0.40 | 0,72 | 700 | 0.64 | ||
1600 | 0.43 | 0,68 | 600 | 0.68 | ||
1500 | 0.43 | 0,8 | 700 | 0.42 | ||
1000 | 0.25 | — | 700 | — |
Какой бывает керамзитобетон по ГОСТ
Блок из керамзита – строительный материал для сооружения стен. Создается способом формирования каждого элемента со смеси, составляющие которой наделяют блоки нужными свойствами для эксплуатации. Имеет вертикальные пустотные образования (сквозные и несквозные).
Виды блоков из керамзита по ГОСТ:
- Полнотелый. Такой элемент может иметь небольшие пустоты для удобства переноса и укладки или вообще изготавливаться без них.
- Рядовой. Стеновой материал для сооружения конструкций, поверхность стен которых будет после возведения отделываться.
- Лицевой. Может обладать декоративным покрытием с 1 или 2 сторон, и применяется для строительства стен, а также в облицовочных целях.
Согласно нормативной документации, паз – специальное углубление, созданное для обеспечения максимального сцепления между элементами стены – повышает прочность кладки и общие характеристики конструкции.
Фактуры поверхностей:
- Колотая – дополнительно не обрабатывается и имеет неровности, превышающие 8 мм.
- Рифленая – имеет выступы вдоль продольной поверхности, которые чередуются правильным образом (вместо выступов могут быть впадины).
- Шлифованная – такие элементы поддаются однократной шлифовке, в результате чего стают шероховатыми и имеют следы обработки.
- Гладкая – покрытие с однообразной шероховатостью и полным отсутствием последствий обработки.
Керамзитобетонные блоки: их параметры и размеры
В документации ГОСТ 6133-99 можно найти информацию по блочному керамзиту:
- Назначение. Могут изготавливаться для лицевой, рядовой укладки, а также для возведения наружных, внутренних стен и перестенков.
- Лицевые поверхности. Строительный элемент, в зависимости от использования, имеет 1 облицовочную (лицевую) поверхность или 2: боковую и торцевую. Лицевая поверхность может изготавливаться с фактурой, обозначенной в конкретном ГОСТ, кроме шлифованной (только по желанию потребителя и предварительного согласования). Что касается цвета, то блочный материал бывает бесцветным или окрашиваться путем добавления в состав цветного цемента или специальных пигментов.
Производитель должен предоставлять зарегистрированные образцы керамзита в определенном цвете, которым готовый продукт будет точно соответствовать.
- Формы. Керамзитобетонные блоки могут производиться с формами и размерами, предпочтительными для условий конкретного строительства (определяется потребителем). В основном, они имеют формы прямоугольного параллелепипеда.
- Торцы. Они могут изготавливаться с плоской поверхностью, наличием пазов или шпунта и гребня. Можно производить материал, у которого только одна грань будет плоская – торцевая. Что касается углов, то они могут быть как прямыми, так и закругленными. Опорные же стороны блоков имеют плоскую поверхность или они изготавливаются с пазами (продольными).
Продольные пазы на опорной поверхности должны отступать от боковой поверхности керамзитового камня не менее, чем на 2 см. Если это правило не соблюдено, то производитель не придерживается строительных требований к изготовлению конкретного вида материалов.
- Наличие пустот. Блоки керамзитобетонные бывают полнотелые или пустотелые. Вне зависимости от конструкции масса одного камня не должна составлять больше 31 кг.
- Расположение пустот. Они могут быть сквозные и несквозные. Они расположены правильно, если проходят перпендикулярно опорной поверхности, а также правильно распределены.
- Толщина стенок. Если камень имеет в конструкции пустоты, то этот показатель равен 2 см для наружных стенок, аналогично для внутренних вертикальных перегородок. Для блоков с пустотами несквозного типа, горизонтальные перегородки должны быть не меньше 1 см.
- Прочность на сжатие. Они могут быть марок 50–300 и 100–25 при изготовлении из тяжелого и легкого бетона соответственно.
- Морозостойкость. Есть маркировка F15–200, где цифры означают количество размораживания/замораживания, которые выносит камень без потери эксплуатационных качеств.
По классам морозостойкости классифицируются все керамзитобетонные блоки, кроме элементов, которые будут использоваться для сооружения перегородок (они не будут поддаваться воздействию мороза).
Также ГОСТ нормируются и условные обозначения, которые нужны для оформления заказа и точного соответствия производимого продукта требованиям потребителя. Значение условных обозначений:
- К – камень.
- С – выполняют кладку стены.
- П – выполняют перегородки.
- Л – выполняют облицовку.
- П – укладывают в ряды.
- Пр – порядовочный.
- УГ – устанавливают по углам.
- ПЗ – применяют для перевязки.
- ПС – имеет пустоты.
Отличные показатели материала не разрешают его использовать в прямом контакте с поверхностью грунта – в таких условиях он будет подвержен разрушительному воздействию влаги.
Дальше уже идут показатели длины, прочности, морозостойкости, плотности и номера стандарта, которым руководствовались при изготовлении материала. К примеру, приведем порядовочный камень с пустотами, произведенный для укладки стены и одновременно облицовки, а также имеет 100 марку прочности, 150 – по морозостойкости, среднюю плотность 1600 кг/м3 и длину 390 мм. Такой элемент будет иметь обозначение КСЛ-ПР-ПС-39–100–F150–1600 ГОСТ 6133-99.
Список технических требований
Строительные требования распространяются на внешний вид, физико-механические свойства и используемое сырье.
- Визуальные показатели.
Требования к виду камня следующие:
- Не должно быть дефектов на внешней поверхности.
- Обязательно соблюдение размерных и числовых показателей.
- Не допускается наличие на поверхности лицевой стороны жировых пятен, размеры которых составляют больше 1 см.
- В партии должно быть меньше 5% блоков из общей массы с пересекающими ребра трещинами, а также (входит в эти 5 процентов) половняка (треснутого на половину блока).
- Требования к физико-механическим показателям.
- Отгружаться потребителю должен материал, обладающий нужной прочностью для использования в определенных строительных целях и точно соответствующий ГОСТу 18105 – используя этот документ, производитель назначает изделие прочностью для определенного проектного возраста.
- При отгрузке на строительный объект материала его реальная прочность должна соответствовать проектной на (летом/зимой): 80/90% — легкий бетон М100 и меньше, 70/85% — тяжелый бетон М125 и меньше; 50/70% — бетон М150 и лучше.
- Изготовитель может гарантировать, что строительный материал наберет нужного показателя прочности за 28 дней с момента производства.
- Что касается морозостойкости блоков, то она исчисляется количеством замораживаний/оттаиваний, после которых керамзитобетон потеряет не более 20% прочности на сжатие и 1% массы.
- Камень, предназначенный для сооружения внешних стен конструкции, должен проходить дополнительные испытания уровня теплопроводности и плотности, которыми он будет обладать не как отдельный блок, а как составляющая уже возведенной стены.
- Требования к сырью и материалам.
- Производя блочный, вяжущий компонент должен соответствовать следующим ГОСТ: 965 – портландцемент белый, 10178, 25328, 22266 – обычный цемент и 15825 – портландцемент цветной.
- Показатель удельной эффективной активности естественных радионуклидов материала, из которого производят блоки, не должен превышать 370 Бк/кг.
- Можно использовать химические добавки, если они полностью соответствуют ГОСТ 24211. Такое соответствие определяется путем проведения опытов.
- Для производства в нужном цветовом исполнении можно применять неорганические добавки (неорганические пигменты). Для ознакомления с их списком нужно посмотреть приложение «В» главного документа, регламентирующего производство блоков из керамзита.
- Требования к воде указаны в строительных требованиях 23732.5.6.
В каждом пакете должно быть промаркировано 1 изделие в любом из рядов. Маркировка наносится на не лицевую поверхность. Для этого используется несмываемая краска. В штампе должно быть указано название производителя и также условные обозначения материала (использование, прочность, морозостойкость и т. д.)
Особые требования предоставлены и к наполнителям. Для точного ознакомления с ними следует подробно изучить пункт 5.5.2 строительных требований.
Также существуют требования ГОСТ, по которым регламентируется то, как должны приниматься и перевозиться керамзитобетонные блоки, храниться, а еще ка правильно проводить контроль их качества. Эти процессы трудно контролировать человеку, который закупает материал для частного использования. Если же все-таки есть необходимость подробно ознакомиться с этими моментами, то следует открыть свод строительных требований и посмотреть «Правила приемки блоков из керамзитобетона», «Методы контроля за блоками из керамзитобетона». Также полезным для ознакомления может оказаться пункт «Транспортирование и хранение блоков из керамзитобетона».
Похожие статьи
kamedom.ru
Керамзитобетонные блоки: состав и принцип производства
Керамзитобетонные блоки бывают стандартных размеров — 190х190х390мм. Они получаются вибропрессованием керамзитобетонной смеси, которая состоит из цемента, керамзитового песка и керамзита. По экологичности керамзитные блоки сопоставляются с керамическим кирпичом, потому что производство блоков требует применение натуральных природных материалов. Между тем, по сравнению с кирпичом, керамзитобетонные блоки более хрупкие, обладают пористой структурой. Но, несмотря на это, использование керамзитобетонных блоков является выгодным решением для строительства, особенно малоэтажных зданий. К примеру, можно построить коттедж в два этажа, себестоимость строительных работ которого снизится на 30%, по сравнению с простым кирпичом. А самым выгодным решением может стать самостоятельное производство этого стенового материала.
Прочность блоков обеспечивается обогащенным песком, что позволяет также использование железобетонных плит перекрытия при строительстве домов из керамзитобетонных блоков. В перегородках без высокой нагрузки применяются блоки с керамзитовым песком. Вот какими методами производители часто экономят на производстве керамзитобетонных блоков
- в смесь добавляют значительно меньше керамзита, в результате — падает теплопроводность;
- вместо обогащенного песка добавляют обычный речной, из-за чего страдает прочность и меняется внешний вид;
- количество цемента сокращается, что действует на прочность изделия;
- сушка свежих блоков производится тепловыми пушками, от чего цемент просто высыхает и рассыпается.
В итоге, нужно отметить, что высокое качество блоков из керамзита доступно лишь немногим крупным специализированным заводам. Тщательно выбирайте производителя, от которого зависит надежность и долговечность вашего будущего строения. Если решитесь взяться за производство блоков самостоятельно, то значительно сэкономите на покупке этого стройматериала, а главное — будете четко знать о составе ваших керамзитовых блоков.
Керамзитобетонные блоки своими руками
Сегодня бетономешалку и вибростанок можно купить без проблем и сделать стеновые блоки своими руками. В таком случае, вы можете быть уверены, что производство 130-150 шт. керамзитовых блоков вам обеспечено, но не забывайте, что это довольно нелегкий физический процесс.
Постройка дома, гаража или перегородки между стенами абсолютно не требует от вас покупки готовых блоков. Кстати, если вам не хочется штукатурить внешнюю сторону стены в последствии, блоки нужно изготовить с защитным слоем. Для дальнейшего покрытия стен штукатуркой блоки делаются из обыкновенного раствора.
Какие составляющие необходимы для приготовления раствора?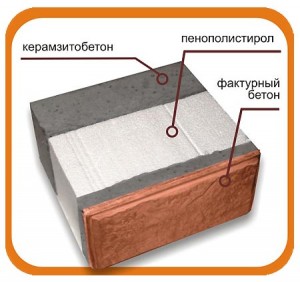
- вяжущие материалы (шлакопортландцемент или портландцемент М400) – 1 часть, и столько же для фактурного слоя;
- керамзитовый гравий — 300-500 кг/м куб. – 8 частей, для фактурного слоя его не используют;
- чистый песок (без ила) размером в 5 мм – 2/3 части, для фактурного слоя нужно использовать 3 части;
- вода – 220-230 л на м3, для фактурного слоя – на глаз.
Если вы добавите в воду раствора стиральный порошок (1 ч. л.) на ведро воды, бетон станет более пластичным. В бетономешалке вначале перемешиваются сухие составляющие, далее добавляется вода и вновь перемешивается до консистенции мягкого пластилина.
Форма для блоков
Блоки размером в 19 х 19 х 14 см и 39 х 19 х 14 см формируются из двух Г-образных частей- половинок и поддона. Половинки делаются из досок 20мм, обиваются изнутри жестью, затем соединяются защелками, которые состоят из полосок стали.
Формирование керамзитовых блоков
На твердую и достаточно ровную поверхность устанавливаем опалубок, в котором формируются наши будущие блоки. Для более легкого снятия блока из опалубки стены формы изнутри смазываем машинным маслом, а основание формы посыпаем песком. Для тех блоков, у которых должен быть защитный слой, применяется поддон, сформированный из досок. Блок выкладывается на основание и поддон «лицом вниз». Для формирования блока в готовую форму наливаем керамзитовый раствор, затем утрамбовываем деревянным бруском до тех пор, пока появится цементное «молоко». После этого мастерком выравниваем поверхность блока. Оставляем на сутки, удаляем формы, но не трогаем блоки для лучшего затвердения. Через 28 дней керамзитовые блоки готовы к строительству.
Материалы по теме:
moscowsad.ru
Производство керамзитобетонных блоков: что нужно знать
Керамзитобетонные блоки становятся все более популярным материалом, применяемым в строительстве, так как они являются не только экологически чистым, прочным и долговечным материалом, но еще и экономически выгодным. Свойства их близки к бетонным конструкциям, за тем исключением, что вместо щебня используется керамзит. Это позволяет значительно уменьшить нагрузку на единицу площади фундамента, улучшить морозостойкость и снизить теплопроводность.
Керамзитобетонные блоки изготавливаются путем прессования керамзитобетонной смеси. Самый популярный размер блоков составляет 188х190х390 мм. Состав смеси для изготовления керамзитобетонных блоков состоит из цемента, песка, керамзита, что делает его структуру более пористой. Способ производства настолько прост, что их можно изготавливать самостоятельно. При этом необходимо следить за калькуляцией (процентным соотношением компонентов), чтобы получить определенные свойства блока.
Как производят блоки
Чтобы приготовить раствор для изготовления керамзитоблоков, необходима бетономешалка и формы с нужной геометрией. Состав раствора следующий: портландцемент марки М400 или М500 1 часть, керамзитовый гравий 8 частей, песок 2/3 части, вода из расчета 220-230л на 1 м3. Фракцию керамзита лучше всего использовать 5-10 мм, а песок должен быть очищенным. Для простоты расчета и экономии раствора можно взять пропорции для одного керамзитоблока и умножить на необходимое количество блоков из расчета, что на один блок, в зависимости от его размера, приходится от 11 до 15 кг раствора. Затем на основании расчётов необходимо приготовить смесь. Для этого в бетономешалку заливается вода, цемент и песок, которые тщательно перемешиваются до достижения однородной смеси. В последнюю очередь засыпается керамзит и замешивается до обволакивания раствором гранул.
Далее готовый раствор выливается в формы для блоков. Готовая смесь должна быть вязкой и при этом не разрушаться. Если смесь сухая, то следует добавить немного воды, а если излишне влажная, то необходимо подождать, пока она приобретет форму и начнет схватываться. После этого блоки достаются из форм и выкладываются на поддонах для дальнейшего высыхания. По истечению трех суток они полностью застывают, но окончательную прочность блоки набирают спустя 28 дней.
Какие нюансы следует учесть при покупке
Чтобы удешевить готовые блоки некоторые производители стараются изменить смесь для керамзитобетонных блоков следующим образом:
- Добавляют меньший объем керамзита, что негативно сказывается на теплопроводности;
- Используют песок низкого качества и уменьшают количество цемента, в результате чего ухудшается прочность изделия;
- Применяют методы быстрой сушки, для увеличения производства. При таком подходе цемент быстро сохнет, структура получается непрочной и блоки рассыпаются на стадии транспортировки.
Относительная простота производства керамзитобетонных блоков приводит к тому, что появляется множество «кустарных» производств. Чтобы не нарваться на откровенно некачественный товар, либо изготавливайте блоки самостоятельно, либо покупайте у крупных и проверенных производителей.
skb37.ru