3.3. Определение сроков схватывания цемента. Время схватывания цементного раствора таблица
3.3. Определение сроков схватывания цемента
Большое практическое значение имеет определение сроков схватывания так как все работы с цементными растворами и бетонами необходимо вести с учётом начала и конца схватывания.
Оборудование: прибор Вика, чаши, лопатки, весы электронные, мерные цилиндры, ножи, секундомеры.
Определение начала и конца схватывания цементного теста производится на тесте нормальной густоты с помощью прибора Вика. В этом случае в нижнюю часть подвижного стержня вставляется стандартная игла. Последняя должна быть ровной, её поверхность необходимо отшлифовать.
Методика определения.
1. Для определения сроков схватывания иглу прибора доводят до соприкосновения с поверхностью теста, приготовленного и уложенного в кольцо так же, как при определении нормальной густоты, закрепляют стержень винтом.
2. Освобождают стержень и дают игле свободно погружаться в тесто. В начале опыта, пока тесто жидкое, следует иглу при погружении слегка придерживать во избежание её изгиба.
3. Иглу погружают через каждые 10 мин. до начала схватывания и через 15 мин. в последующее время, каждый раз передвигая кольцо и тщательно вытирая иглу.
За начало схватывания принимают время, истекшее от момента затворения до момента, когда игла не будет доходить до дна на 1-2 мм. Концом схватывания считают время от момента затворения до момента, когда игла будет опускаться в тесто не более чем на 1-2 мм.
Определение сроков схватывания производится при температуре 20°± 5°С, кольцо не должно подвергаться сотрясениям, сквознякам, солнечным лучам.
Полученные данные занести в таблицу.
% опыта | Начало схватывания | Конец схватывания |
1. | ||
2. | ||
3. | ||
Среднее |
3.4. Определение равномерности изменения объёма цемента
Оборудование: металлические чашки, лопатки, мерные цилиндры на 250мл, весы с разновесами, стеклянные пластинки, ванна для хранения образцов, бачок для пропаривания образцов.
Изменение объёма цемента при твердении может происходить равномерно и неравномерно. Неравномерность изменения объёма цемента может привести к образованию трещин в твердеющих бетонах и растворах, что повлечёт за собой снижение прочности или разрушение. Это может быть вызвано избытком в цементе свободной окиси кальция СаО или окиси магния МgО, повышенным содержанием сернистых примесей.
Определение равномерности изменения объёма цемента производят на лепёшках диаметром 7-8 см и толщиной в средней части 1 см, изготовленных из теста нормальной густоты.
Методика определения
1. Приготавливают тесто нормальной густоты.
2. Отвешивают 4 навески по 75 г каждая, скатывают из них шарики и помещают их на стеклянные пластинки, предварительно протёртые машинным маслом
3. Легким постукиванием о стол встряхивают пластинки до расплыва шариков в лепёшки диаметром 7-8 см.
4. Для получения гладкой закруглённой поверхности лепёшки заглаживают влажным ножом от краёв к центру.
5. Приготовленные лепёшки помещают на (24 ± 2) ч в ванну с гидравлическим затвором на сетку над водой. Ванну закрывают крышкой.
6. После этого лепешки снимают с пластинок. Четыре лепёшки помещают в бачок так, чтобы две из них находились в воде, а две другие - на полочке над водой. Воду в бачке кипятят в течение 3 часов. После остывания воды лепёшки из бачка вынимают и тщательно осматривают. Если в цементе содержится МgО более 5%, то равномерность изменения объёма проверяется в автоклаве. В автоклав загружаются две лепёшки, выдержавшие кипячение. Время обработки 2 ч, давление до 0,2 МПа
Цемент признают доброкачественным, то есть обладающим равномерностью изменения объёма, если на лицевой стороне лепешек после испытания не будет обнаружено радиальных, доходящих до краёв трещин или сетки мелких трещин, а также каких-либо искривлений, устанавливаемых при помощи линейки (рис. 4). Появляющиеся иногда волосяные трещины усыхания, не доходящие до краёв лепёшек, не являются признаком плохого качества цемента и их не принимают во внимание.
Рис. 4. Характер изменения объема лепешек (разрушение и радиальные трещины)
studfiles.net
4.6 Сроки схватывания цемента
Схватывание цемента - процесс загустевания цементного теста вследствие взаимодействия цемента с водой. Сроки схватывания определяют на цементном тесте нормальной густоты с помощью прибора Вика (п. 4.5), но вместо пестика на конце стержня закрепляют иглу 4 (рисунок 4.2 б), а пестик устанавливают сверху; при этом масса подвижной части остается равной (300 ± 2) г. Перед началом испытаний проверяют, свободно ли опускается стержень прибора, чистоту поверхности иглы и отсутствие ее искривлений, а также нулевое показание прибора.
Цементное тесто готовят по методике, описанной в п. 4.5, из 400 г цемента и воды, взятой в количестве, которое соответствует нормальной густоте цементного теста. Готовое тесто помещают в кольцо прибора Вика и устанавливают на столик прибора. Стержень опускают до соприкосновения иглы с поверхностью теста и в этом положении закрепляют винтом. Затем винт освобождают, давая стержню с иглой свободно погружаться в тесто.
В начале испытания, пока тесто находится в жидком состоянии, во избежание сильного удара иглы о пластину рекомендуется слегка придерживать ее при погружении в тесто. Иглу можно свободно опускать, как только тесто загустеет настолько, что опасность повреждения иглы будет исключена. Момент начала схватывания определяют при свободном опускании иглы. Иглу погружают в тесто через каждые 10 мин, при этом кольцо после каждого погружения передвигают таким образом, чтобы игла не попадала в прежнее место. После каждого погружения иглу вытирают.
Во время испытаний прибор должен находиться в затененном месте, где нет сквозняков, и не должен подвергаться сотрясениям.
Началом схватывания цементного теста считается время, прошедшее от начала затворения теста (момента приливания воды к цементу) до момента, когда игла не доходит до пластины на 1...2 мм; концом схватывания — время от начала затворения до момента, когда игла опускается в тесто не более чем на 1...2 мм.
4.7 Определение марки (активности) цемента
Марку цемента или его активность определяют по прочности на сжатие и изгиб стандартных образцов размером 40х40х160 мм, изготовленных из цементно-песчаного раствора состава 1:3 нормальной консистенции после необходимого срока твердения (для портландцемента, шлакопортландцемента и пуццоланового цемента — 28 сут, для быстротвердеющего портландцемента — 3 и 28 сут, для глиноземистого — 3 сут) в стандартных условиях (ГОСТ 310.4-81). Ниже рассмотрена методика определения марки (активности) портландцемента.
При определении марки используют стандартный песок, что позволяет исключить влияние качества песка на прочность испытуемого цемента. Стандартный песок (ГОСТ 6139-91) представляет собой чистый кварцевый песок (содержание SiO2 > 98 %; потери при прокаливании <0,05 %; влажность <0,2 %). Стандарт предполагает возможность использования двух вариантов зернового состава песка:
• монофракционного: содержание зерен фракции 0,9...0,5 мм -не менее 91 %;
• полифракционного, который готовят смешиванием фракций в следующем количестве:
Фракция, мм 2,0...1,0 1,0...0,5 0,5...0,16 0,16...0,08
Частный остаток, % ..33±5 34±5 10±5 12+1
Приготовление цементного раствора нормальной консистенции. Для приготовления необходимого количества цементно-песчаного раствора состава 1:3 (по массе) отвешивают 500 г испытуемого цемента и 1500 г стандартного песка и высыпают их в предварительно протертую мокрой тканью чашу (рисунок 4.3 а). Цемент с песком перемешивают в течение 1 мин. Затем в центре сухой смеси делают лунку, вливают в нее воду в количестве 200 г (В/Ц = 0,4) и дают ей впитаться в течение 0,5 мин, после чего смесь перемешивают вручную в течение 1 мин.
По окончании перемешивания определяют консистенцию раствора. Для этого применяют встряхивающий столик 4 (рисунок 4.5), представляющий собой металлический диск, покрытый шлифованным стеклом. При вращении кулачка второй диск с помощью штока 3, скользящего в направляющих, поднимается на 10 мм, а затем резко падает. Таким образом имитируется виброуплотнение раствора.
На стекло столика ставят коническую форму 5 с загрузочной воронкой 6. Внутреннюю поверхность конуса и стекло перед укладкой раствора протирают влажной тканью.
Рисунок 4.4 – Встряхивающий столик:
1 – станина; 2 – кулачок; 3 – шток; 4 – столик; 5 – форма-конус; 6 - насадка
Для определения консистенции раствор укладывают в форму-конус в два приема (слоями равной толщины). Каждый слой уплотняют штыковкой из нержавеющей стали диаметром 20 мм, массой (350 ± 20) г. Нижний слой штыкуют 15 раз, верхний — 10 раз. Штыкование ведут от периферии к центру, придерживая форму рукой. Далее снимают загрузочную воронку, излишек раствора срезают ножом и осторожно снимают форму-конус.
Полученный конус цементного раствора встряхивают на столике 30 раз в течение (30 ± 5) с. Затем штангенциркулем или металлической линейкой измеряют диаметр конуса по нижнему основанию в двух взаимно перпендикулярных направлениях и берут среднее значение.
Консистенция раствора считается нормальной, если расплыв конуса составляет 106...115 мм. Если расплыв конуса менее 106 мм или раствор при встряхивании рассыпается, приготовляют новую порцию раствора, увеличивая количество воды до получения расплыва конуса 106...115 мм. Если расплыв конуса более 115 мм, то испытание повторяют с меньшим количеством воды, добиваясь расплыва 106...115 мм. Водоцементное отношение, полученное при достижении расплыва конуса 106...115 мм, принимают для проведения дальнейших испытаний. Погрешность определения В/Ц не более 0,01.
Изготовление образцов. Разъемные формы, в которых изготовляют образцы, рассчитаны на три образца (рисунок 4.6 а). Детали форм выполнены из стали или чугуна с твердостью по Бринеллю не менее НВ140. Продольные и поперечные стенки форм, скрепляемые зажимным винтом, отшлифованы и плотно прилегают к отшлифованной поверхности поддона.
Рисунок 4.5 – Форма для образцов-балочек (а) и насадка к ней (б)
Перед заполнением формы растворной смесью ее внутренние поверхности слегка протирают машинным маслом, а стыки наружных стенок с поддоном и одна с другой смазывают техническим вазелином. На форму устанавливают металлическую насадку (рисунок 4.5 б), облегчающую укладку раствора. После этого форму жестко закрепляют в центре виброплощадки.
Виброплощадка (рисунок 4.6) состоит из станины 1, к которой пружинами 5 прикреплена рама 4 с установленной на ней площадкой 3. Колебательные движения площадки создает прикрепленный к ней электродвигатель 2, на валу которого находится дебаланс (эксцентрично закреплен груз).
Рисунок 4.6 – Лабораторная виброплощадка: 1 – станина, 2 – электродвигатель, 3 – площадка, 4 – рама, 5 – пружины
Форму заполняют приблизительно на 1 см раствором и включают виброплощадку. Затем в течение 2 мин вибрации все три гнезда формы равномерно небольшими порциями заполняют раствором. По истечении 3 мин от начала вибрации виброплощадку отключают и снимают с нее форму. Далее смоченным водой ножом срезают излишек раствора, заглаживают поверхность образцов и маркируют их.
Образцы в формах хранят (24 ± 2) ч на столике 3 в ванне с гидравлическим затвором (рисунок 4.7). Затем образцы осторожно расформовывают и укладывают в горизонтальном положении в ванну с водой так, чтобы они не соприкасались один с другим. Воду, которая должна покрывать образцы не менее чем на 2 см, меняют через каждые 14 сут. Температура воды весь срок хранения должна быть (20 ± 2) °С.
Образцы, прочность которых через 24 ч недостаточна для расформовывания их без повреждений, допускается вынимать из форм через 48 ч с отметкой об этом в рабочем журнале.
По истечении срока хранения образцы извлекают из воды и не позднее чем через 1 ч подвергают испытанию. Непосредственно перед испытанием образцы-балочки насухо вытирают и испытывают на изгиб, а затем каждую из полученных половинок балочки — на сжатие.
При испытании глиноземистого цемента образцы в форме хранят первые 6 ч в ванне с гидравлическим затвором, а затем в воде комнатной температуры. Через (24 ±2) ч с момента изготовления образцы вынимают из формы и часть их испытывают, а оставшиеся хранят в воде до последующих испытаний 3 сут.
Определение предела прочности при изгибе. Это испытание производят на машинах, обеспечивающих нарастание нагрузки в среднем (50±10)Н в секунду. Образец устанавливают на опорные элементы машины таким образом, чтобы его горизонтальные при изготовлении грани находились в машине в вертикальном положении (рисунок 4.8). Испытание образцов и расчет предела прочности при изгибе выполняют в соответствии с инструкцией, прилагаемой к испытательной машине. Предел прочности при изгибе испытуемого цемента вычисляют как среднее арифметическое из двух наибольших значений результатов испытания трех образцов.
Рисунок 4.7 – Ванна с гидравлическим затвором: 1 – ванна; 2 – герметичная крышка; 3 - столик | Рисунок 4.8 – Схема расположения образцов-балочек на опорных элементах |
Определение предела прочности при сжатии. Полученные после испытания на изгиб шесть половинок балочек сразу же подвергают испытанию на сжатие на прессах с предельной нагрузкой 200...500 кН. Для того, чтобы результаты испытаний половинок балочек были сопоставимы, несмотря на разный размер, используют металлические пластинки (рисунок 4.9 а), через которые нагрузка от плит пресса передается на образец. Пластинки, изготовляемые из нержавеющей стали, имеют плоскую полированную поверхность; площадь поверхности пластинки, соприкасающейся с образцом, равна 25 см2.
Половинку балочки 3 помещают между двумя пластинками 7 (рисунок 4.9 б) таким образом, чтобы боковые грани, которые при изготовлении прилегали к продольным стенкам формы, находились на плоскостях пластинок, а упоры пластинок плотно прилегали к торцовой гладкой грани образца. Образец вместе с пластинками центрируют на опорной плите 4 пресса. Средняя скорость нарастания нагрузки на образец при испытании должна составлять (5± 1,25) кН в секунду.
а б
Рисунок 4.9 – Испытание половинок балочек на сжатие:
а – пластинки; б – схема испытания;
1 – пластинки; 2, 4 – плиты пресса; 3 – образец (балочка)
Предел прочности при сжатии Rсж (МПа) каждого образца вычисляют по формуле
Rсж=10(Fраз/S), (4.2)
где Fраз — разрушающая нагрузка, кН; S — площадь металлических пластинок, см2.
Предел прочности при сжатии цемента вычисляют по результатам шести испытаний как среднее арифметическое четырех наибольших результатов.
Полученное таким образом значение называют активностью цемента.
Определение марки цемента. Марку цемента находят по результатам определения пределов прочности цемента при сжатии и изгибе, сравнивая эти результаты с требованиями ГОСТа на соответствующий цемент. Для каждой марки портландцемента и его разновидностей пределы прочности при изгибе и при сжатии образцов, твердевших 28 сут (для быстротвердеющих цементов также и 3 сут), не должны быть ниже значений, указанных в таблице 4.1.
Таблица 4.1
Зависимость марок цементов от пределов прочности стандартных образцов
Наименование цемента | Марка цемента | Предел прочности при изгибе, МПа (кгс/см2), в возрасте, сут | Предел прочности при сжатии, МПа (кгс/см2), в возрасте, сут | ||
3 | 28 | 3 | 28 | ||
Портландцемент, портландцемент с минеральными добавками, шлакопорт-ландцемент Быстротвердеющий портландцемент Быстротвердеюший шла-копортландцемент | 300 400 500 550 600 400 500 400 | 3,9(40) 4,4(45) 3,4(35) | 4,4(45) 5,4(55) 5,9(60) 6,1(62) 6,4(65) 5,4(55) 5,9(60) 5,4(55) | 24,5(250) 27,5(280) 19,6(200) | 29,4(300) 39,2(400) 49,0(500) 53,9(550) 58,8(600) 39,2(400) 49,0(500) 39,2(400) |
Определение прочности цемента при пропаривании. Бетонные и железобетонные изделия изготовляют, ускоряя твердение бетона с помощью его тепловлажностной обработки (пропаривания). Поэтому ГОСТ 10178-85 предусматривает определение прочности цемента при пропаривании. Образцы для этого испытания готовят так же, как и для стандартных определений, но их твердение протекает по специальному режиму. Формы с образцами для твердения помещают в пропарочную камеру при температуре (20±3)°С при отключенном подогреве на (120 ± 10) мин. Затем включают подогрев и в течение 11 ч образцы пропаривают по следующему режиму:
Равномерный подъем температуры до (80 + 5) °С................ 180±10 мин;
Изотермический прогрев при (85±5)°С.............................. 360±10 мин;
Остывание при отключенном подогреве .............................. 120+10 мин.
После этого крышку камеры открывают. Через (24 ± 2) ч с момента изготовления образцы вынимают из форм и испытывают по методике, используемой при определении марки цемента.
studfiles.net
Свойства цемента | СКМ ТЕХГРУПП
Основными требованиями, которые предъявляют строители или производители строительных материалов к цементам, являются:
1. прочность и активность цемента;
2. сроки схватывания цемента;
3. нормальная густота и водопотребность цемента;
4. тонкость помола цемента и др.
Помимо перечисленных, также важны и другие свойства, не регламентированные в соответствующих ГОСТ на цементы: водоотделение, водопроницаемость, морозостойкость, плотность и другие. Необходимо отметить, что требования предъявляются к цементам, но испытания для проверки этих свойств производят на цементном растворе, цементном камне, бетонном растворе или бетоне.
В связи с тем, что температура и влажность окружающей среды влияют на многие свойства цемента, испытания производят в лабораториях — специальных помещениях с постоянной температурой (20±2°С) и относительной влажностью: не менее 50% при изготовлении образцов для определения прочности; не менее 65% при определении сроков схватывания и равномерности изменения объёма; не более 65% при определении тонкости помола.
ПРОЧНОСТЬ ЦЕМЕНТА.
Твердение цемента, которое наступает в процессе схватывания цементного теста, сопровождается набором прочности с образованием камневидного тела. Прочность — свойство материала сопротивляться разрушению под действием внутренних напряжений, возникающих от внешних сил. Прочность и скорость её нарастания являются одними из самых важных характеристик цемента, т.к. влияют на продолжительность распалубки изделий, а значит, на быстроту возведения строительных объектов и оборачиваемость форм. (Для увеличения скорости набора прочности часто используют прогрев бетона – чем выше температура, тем выше скорость набора прочности). Для всех цементов предъявляется требование по величине прочности (в МПа) после определенного интервала времени (для цементов класса прочности 22,5Н и 32,5Н после 7 и 28 суток, а для цементов класса прочности 32,5Б, 42,5Н, 42,5Б, 52,5Н и 52,5Б – после 2 и 28 суток), но набор прочности идёт гораздо дольше и растягивается на года.
По скорости набора прочности цементы разделяются на два подкласса – нормальнотвердеющие (Н) и быстротвердеющие (Б). Этот показатель как раз и определяется на промежуточных сроках твердения. Так, например, для класса цемента 42,5 показатель прочности на 2-е сутки для нормальнотвердеющего цемента должен быть не менее 10 МПа, а для быстротвердеющего – не менее 20 МПа. На 28-е же сутки показатели прочности нормальнотвердеющего и быстротвердеющего цемента должны соответствовать одинаковым требованиям и быть не менее 42,5 МПа, но не более 62,5 МПа.
Таблица 1. Требования по прочности цемента по ГОСТ 31108-2003:
Класс прочности цемента | Прочность на сжатие, МПа, при возрасте | |||
2 суток не менее | 7 суток не менее | 28 суток | ||
Не менее | Не более | |||
22,5Н | — | 11 | ||
32,5Н | — | 16 | 32,5 | 52,5 |
32,5Б | 10 | — | ||
42,5Н | 10 | — | 42,5 | 62,5 |
42,5Б | 20 | — | ||
52,5Н | 20 | — | 52,5 | — |
52,5Б | 30 | — |
Прочность цемента выражается его активностью — фактический предел прочности при испытании нагрузки, при котором цемент начинает разрушаться. Активность цемента определяют путём испытания образцов-балочек затвердевшего цемента с размерами 40*40*160 мм. По активности цемента его соотносят к определенному классу или марке (класс по ГОСТ 31108-2003 и 55224-2012, марка по ГОСТ 10178-85). Чем выше активность цемента, тем более высокому классу или марке цемента он может соответствовать. С увеличением активности цемента нарастание прочности происходит более интенсивно. На активность цемента влияют водоцементное отношение (В/Ц) и температура окружающей среды. С уменьшением В/Ц активность цемента и рост прочности увеличиваются. С увеличением температуры окружающей среды активность цемента и рост прочности увеличиваются. Для определения класса прочности цемента (ГОСТ 31108-2003 и 55224-2012) используют В/Ц, равное 0,5, а для определения марки цемента (ГОСТ 10178-85) используют В/Ц, равное 0,4. При хранении цемент набирает влагу и теряет свою активность, в связи с чем для цементов устанавливается гарантийный срок хранения, который почти для всех цементов составляет не более 60 суток с момента отгрузки. Однако по истечении 60 суток цемент не считается непригодным для строительства, а просто может не соответствовать указанной в документах на него прочности. При использовании цемента с длительным сроком хранения его расход на бетон необходимо увеличить. Поэтому не стоит использовать цемент с неизвестными сроками и условиями хранения, т.к. невозможно гарантировать прочность получаемого бетона.
СРОКИ СХВАТЫВАНИЯ ЦЕМЕНТА.
Образованное при смешивании цемента с водой цементное тесто представляет собой пастообразную массу, обладающую подвижностью. Со временем оно постепенно уплотняется, теряет пластичность (загустевает) и твердеет — схватывается. Процесс схватывания характеризуется временем начала и конца схватывания цементного теста. Началом схватывания считается начало потери подвижности (пластичности) цементным тестом. В строительстве применять свежеприготовленные бетонные растворы можно только до начала схватывания, до которого он должен быть уложен в опалубку. Из схватившегося бетонного раствора формование изделий становится затруднительным после начала схватывания и невозможным после конца схватывания (нормированная степень затвердения цементного теста).
Для увеличения сроков сохранения подвижности бетонного раствора его перемешивают, и он не переходит в стадию твердения. При этом процесс схватывания растягивается (именно поэтому доставку бетонного раствора осуществляют в бетоносмесителях, осуществляющих постоянное перемешивание бетонного раствора). Но, здесь стоит отметить, что с удлинением сроков подвижности (за счет перемешивания бетонного раствора) в цементном тесте происходят необратимые процессы, существенно снижающие качество получаемых бетонов. В связи с этим для сохранения качественных характеристик цемента доставку бетонного раствора на строительный объект необходимо осуществлять в кратчайшие сроки.
Если после начала схватывания, но до конца схватывания, бетонному раствору необходимо придать подвижность, его перемешивают с добавлением воды. Бетонному раствору, прошедшему стадию конца схватывания, придать подвижность уже невозможно. Время схватывания бетонного раствора существенно зависит от температуры окружающей среды: с повышением температуры сроки схватывания ускоряются (при повышении температуры с 20 до 40°С сроки схватывания сокращаются вдвое). На сроки схватывания также влияет количество воды затворения — её уменьшение приводит к сокращению сроков схватывания. С целью регулирования сроков схватывания бетонных растворов применяют специальные добавки. Сроки схватывания цемента определяются в минутах от начала затворения цемента водой. Средние показатели начала и конца схватывания составляют 2–3 часов (при нормативе от 45 минут до 2-х часов) и 3–5 часов (при нормативе до 10 часов или не нормируется) соответственно. Как правило, норматив по началу схватывания не менее 2-х часов предъявляется для цементов со специальными свойствами (для цементов на основе клинкеров нормированных составов — дорожные цементы, сульфатостойкие цементы и др.
Иногда потеря подвижности бетонного раствора происходит почти сразу после затворения бетонной смеси водой с большим выделением тепла — данное явление называется ложным схватыванием. Бетонный раствор, проявивший ложное схватывание, необходимо перемешать, и он вновь становится подвижным. Ложное схватывание является негативным фактором, т.к. может происходить на этапе укладки бетонного раствора в опалубку, при котором его перемешать не представляется возможным.
ВОДОПОТРЕБНОСТЬ И НОРМАЛЬНАЯ ГУСТОТА ЦЕМЕНТА.
Водопотребность характеризуется количеством воды необходимой для придания бетонному раствору нормируемой подвижности и в зависимости от состава бетонного раствора колеблется от 40 до 70% (от массы цемента). Водопотребность бетонного раствора зависит от водопотребности цементного теста, выражающегося нормальной густотой цементного теста (НГЦТ). НГЦТ определяется водоцементным отношением (В/Ц), при котором достигается нормированная консистенция цементного теста. НГЦТ для различных цементов составляет 23–29%.
Производители бетона заинтересованы использовать цемент с пониженным водопотреблением, т.к. в процессе гидратации цемента (химическое взаимодействие цемента с водой) требуется 15–17% воды от массы цемента, а для придания бетонному раствору необходимой подвижности (пластичности) воды берётся значительно больше. Излишки воды повышают пористость цементного камня, что приводит к снижению плотности, прочности и долговечности бетона. Для уменьшения количества воды при сохранении подвижности бетонного раствора при его приготовлении используют поверхностно-активные вещества (ПАВ). Применение ПАВ позволяет снижать расход воды и соответственно, расход цемента. При сравнительной оценке одного вида цемента различных производителей потребитель отдаёт предпочтение цементу с более низкой НГЦТ, т.к. расход такого цемента при приготовлении бетонного раствора будет меньше, а значит, себестоимость также уменьшится. Как правило повышенную НГЦТ имеют цементы, содержащие пуццолановые добавки, но применение таких цементов имеет и положительную роль — снижается водоотделение бетонного раствора и повышается коррозиеустойчивость бетонов.
ВОДООТДЕЛЕНИЕ ЦЕМЕНТА.
Под влиянием силы тяжести в бетонном растворе начинается процесс седиментации (самопроизвольного осаждения твердых частиц). Раствор уплотняется, и на его поверхности образуется пленка воды — водоотделение. При послойной укладке бетонного раствора вода, выступая, мешает сцеплению между слоями и компонентами смеси — данный процесс называется расслоением. Нормальный процент водоотделения цементов составляет до 10–15% с единицы объема теста через 3–5 часов, но зачастую данный показатель значительно больше. С целью снижения водоотделения необходимо стремиться не добавлять излишней воды при затворении цемента, что достигается путем введения ПАВ при производстве бетонных растворов. Экономически целесообразным является применение цементов с низкой водопотребностью, т.к. в данном случае уменьшается водоотделение и снижается потребность в ПАВ, удорожающих себестоимость бетонных смесей. Однако следует учитывать, что низкое водоотделение характерно для цементов с высокой удельной поверхностью, в основном присущей для цементов, производимых из низкоактивных клинкеров (для таких цементов нарастание прочности, как правило, в основном идёт в первый месяц, на протяжении которого нормируется прочность). Таким образом, цементы с низкой удельной поверхностью, но с такой же прочностью на 28 сутки как и цементы из низкоактивных тонкомолотых клинкеров, имеют преимущество, т.к. нарастание прочности идёт более равномерно и конечная прочность через несколько месяцев значительно выше. Данный фактор позволяет снижать расход цемента на м3 бетонной смеси. Следовательно, потребитель должен находить наиболее оптимальное решение при применении цемента — уменьшение водопотребности с увеличением качества и прочности бетона или уменьшение себестоимости в ущерб качеству бетона!
ТОНКОСТЬ ПОМОЛА ЦЕМЕНТА.
Все цементы представляют собой тонкомолотые порошки, тонкость помола которых характеризуется остатком на сите (или проходом через сито) с сеткой № 008 (80 мкм), удельной поверхностью или грансоставом. Из-за получения некорректных данных по удельной поверхности для цементов содержащих добавки осадочного происхождения (пуццолановые добавки — трепел, опока, глиеж, диатомит и др.) тонкость помола для них определяется только по остатку на сите № 008. К цементам, выпускаемым по ГОСТ 31108-2003, требований по тонкости помола, не предъявляется. Однако это не означает, что контроль за данными параметрами не ведётся — все основные параметры цемента регламентируются технологическими регламентами (ТР — для каждого завода свой ТР) и картами контроля на производство цемента. Средние показатели цементов по тонкости помола составляют 6–10% по остатку на сите № 008 (к первоначальной массе просеиваемой пробы) и удельной поверхностью 280-330 м2 /кг (по Блейну).
Увеличение тонкости помола (с сохранением вещественного состава) приводит к повышению прочности цемента, но при этом увеличиваются затраты на его производство (из-за снижения производительности цементных мельниц и, как следствие, уменьшения общего выпуска цемента).
Проконсультироваться по поводу выбора марки цемента, рассчитать количество и доставку, и сделать заказ на цемент навалом (ж/д и авто) и цемента в мешках, а также щебень (гранитный и гравийный) вы можете в СКМ ТЕХГРУПП.
slavcem.ru
Сроки схватывания цемента - это... Что такое Сроки схватывания цемента?
Сроки схватывания цемента – время начала и конца схватывания цементного теста, определяемое в нормированных условиях.
[ГОСТ 30515-2013]
Сроки схватывания – это начало и конец схватывания цемента. За начало схватывания принимается начало потери подвижности (пластичности) цементным тестом, а конец схватывания характеризуется некоторым его затвердением. Начало схватывания портландцемента должно наступать не ранее 45 минут, а конец – не позднее 12 часов. Для строителей необходимо знать сроки схватывания цемента, так как применять свежеприготовленные бетоны и растворы можно только до начала схватывания. При несоблюдении этого условия прочность растворов и бетонов будет низкой, так как схватившееся цементное тесто утратит клеящую способность. С повышением температуры окружающей среды сроки схватывания ускоряются, а с понижением замедляются. На сроки схватывания оказывает влияние тонкость помола: с повышением тонкости помола сроки схватывания уменьшаются. Портландцемент делится на 6 марок, которые обозначаются по пределу прочности на сжатие: 200,250,300,450,500 и 600.
[Портик А. А. Все о пенобетоне. – СПб.: 2003. – 224 с.]
Рубрика термина: Свойства цемента
Рубрики энциклопедии: Абразивное оборудование, Абразивы, Автодороги, Автотехника, Автотранспорт, Акустические материалы, Акустические свойства, Арки, Арматура, Арматурное оборудование, Архитектура, Асбест, Аспирация, Асфальт, Балки, Без рубрики, Бетон, Бетонные и железобетонные, Блоки, Блоки оконные и дверные, Бревно, Брус, Ванты, Вентиляция, Весовое оборудование, Виброзащита, Вибротехника, Виды арматуры, Виды бетона, Виды вибрации, Виды испарений, Виды испытаний, Виды камней, Виды кирпича, Виды кладки, Виды контроля, Виды коррозии, Виды нагрузок на материалы, Виды полов, Виды стекла, Виды цемента, Водонапорное оборудование, Водоснабжение, вода, Вяжущие вещества, Герметики, Гидроизоляционное оборудование, Гидроизоляционные материалы, Гипс, Горное оборудование, Горные породы, Горючесть материалов, Гравий, Грузоподъемные механизмы, Грунтовки, ДВП, Деревообрабатывающее оборудование, Деревообработка, ДЕФЕКТЫ, Дефекты керамики, Дефекты краски, Дефекты стекла, Дефекты структуры бетона, Дефекты, деревообработка, Деформации материалов, Добавки, Добавки в бетон, Добавки к цементу, Дозаторы, Древесина, ДСП, ЖД транспорт, Заводы, Заводы, производства, цеха, Замазки, Заполнители для бетона, Защита бетона, Защита древесины, Защита от коррозии, Звукопоглащающий материал, Золы, Известь, Изделия деревянные, Изделия из стекла, Инструменты, Инструменты геодезия, Испытания бетона, Испытательное оборудование, Качество цемента, Качество, контроль, Керамика, Керамика и огнеупоры, Клеи, Клинкер, Колодцы, Колонны, Компрессорное оборудование, Конвеера, Конструкции ЖБИ, Конструкции металлические, Конструкции прочие, Коррозия материалов, Крановое оборудование, Краски, Лаки, Легкие бетоны, Легкие наполнители для бетона, Лестницы, Лотки, Мастики, Мельницы, Минералы, Монтажное оборудование, Мосты, Напыления, Обжиговое оборудование, Обои, Оборудование, Оборудование для производства бетона, Оборудование для производства вяжущие, Оборудование для производства керамики, Оборудование для производства стекла, Оборудование для производства цемента, Общие, Общие термины, Общие термины, бетон, Общие термины, деревообработка, Общие термины, оборудование, Общие, заводы, Общие, заполнители, Общие, качество, Общие, коррозия, Общие, краски, Общие, стекло, Огнезащита материалов, Огнеупоры, Опалубка, Освещение, Отделочные материалы, Отклонения при испытаниях, Отходы, Отходы производства, Панели, Паркет, Перемычки, Песок, Пигменты, Пиломатериал, Питатели, Пластификаторы для бетона, Пластифицирующие добавки, Плиты, Покрытия, Полимерное оборудование, Полимеры, Половое покрытие, Полы, Прессовое оборудование, Приборы, Приспособления, Прогоны, Проектирование, Производства, Противоморозные добавки, Противопожарное оборудование, Прочие, Прочие, бетон, Прочие, замазки, Прочие, краски, Прочие, оборудование, Разновидности древесины, Разрушения материалов, Раствор, Ригеля, Сваи, Сваизабивное оборудование, Сварка, Сварочное оборудование, Свойства, Свойства бетона, Свойства вяжущих веществ, Свойства горной породы, Свойства камней, Свойства материалов, Свойства цемента, Сейсмика, Склады, Скобяные изделия, Смеси сухие, Смолы, Стекло, Строительная химия, Строительные материалы, Суперпластификаторы, Сушильное оборудование, Сушка, Сушка, деревообработка, Сырье, Теория и расчет конструкций, Тепловое оборудование, Тепловые свойства материалов, Теплоизоляционные материалы, Теплоизоляционные свойства материалов, Термовлажносная обработка бетона, Техника безопасности, Технологии, Технологии бетонирования, Технологии керамики, Трубы, Фанера, Фермы, Фибра, Фундаменты, Фурнитура, Цемент, Цеха, Шлаки, Шлифовальное оборудование, Шпаклевки, Шпон, Штукатурное оборудование, Шум, Щебень, Экономика, Эмали, Эмульсии, Энергетическое оборудование
Источник: Энциклопедия терминов, определений и пояснений строительных материалов
Энциклопедия терминов, определений и пояснений строительных материалов. - Калининград. Под редакцией Ложкина В.П.. 2015-2016.
construction_materials.academic.ru
Как сделать цементный раствор

Цемент — один из самых важных строительных материалов, без которого невозможно сделать цементный раствор для кладки кирпичей, бетон, фундамент и другие железобетонные конструкции. Цементом называются вяжущие строительные смеси, которые отличаются друг от друга составом. При этом все они соответствуют определенным характеристикам. Этот термин также используется при определении всех видов портландцемента, шлакопортландцемента, глиноземистого цемента и многих других строительных смесей.

Таблица, показывающая составляющие и их пропорции в различных марках цементного раствора.
Марки цемента
Все виды цемента имеет свою прочность, показатель которой для каждого из них индивидуален. По этому параметру данный материал делится на марки, которые регламентируются строительными правилами и нормами ГОСТа и СНиП.
Самыми популярными считаются марки — 200, 300, 400, 500, 600. Высокая марка обладает большой вязкостью, что повышает эффективность использования цемента при изготовлении бетона.

Маркировка цемента поможет вам рассказать о качестве и его особенностях.
Из всех распространенных видов наиболее важен портландцемент. Однако он не способен удовлетворить абсолютно все требования, так как бывают случаи, когда такая смесь не подходит. Именно по этой причине производятся разновидности такого цемента:
- сульфатостойкий;
- гидрофобный;
- быстрозастывающий;
- пластифицированный.
Это самые часто используемые смеси, но существуют другие узкоспециализированные виды.
Разновидности цементного раствора
Жирный цементный раствор представляет собой смесь, состоящую из большого количества вяжущих элементов. Он быстро застывает, но после полного высыхания может дать трещины. Именно поэтому он не долговечен.
Нормальный раствор изготовляется соблюдением всех необходимых пропорций. За счет этого стынет немного дольше, чем первый, зато в нем не образуются трещины. Его отличие заключается в долговечности и прочности.
Тощий раствор содержит в себе недостаточное количество связующих компонентов. Поэтому он скорее всего не возьмется.
Приготовление смеси

Все компоненты нужно смешать до однородной массы и тщательно перемешать, чтобы получить качественный раствор.
Цемент — материал, обладающий порошкообразной формой. Он широко используется на строительных площадках. Отличие материала состоит в определенной степени вязкости и в наличии гидравлических свойств.
Благодаря этим характеристикам, при смешивании порошка с водой создается раствор, имеющий пластичную массу, которая впоследствии затвердевает, образуя камнеподобный прочный и жесткий материал.
Правильно будет отметить, что цемент относится к неорганическим материалам с повышенной вязкостью. Все, что строителями добавляются в такой материал (раствор, вода, добавки минерального типа), предназначено для повышения его качеств, а также для изменения его состояния.
Этапы производства цементного раствора
Подготовка
Данный этап является одним из самых главных, так как от него зависит возможность качественного материала. Во время него заготавливается необходимый материал и инструмент, который понадобится во время работы. Сюда входят:
- цемент выбранной марки;
- вода;
- песок;
- емкость;
- строительный миксер;
- строительное сито;
- лопата.
Важно! Объем емкости должен соответствовать объему раствора, который планируется приготовить.
Если емкость окажется меньше, готовый раствор начнет из нее выливаться, и его придется собирать с земли. Если же тара будет больше, невозможно будет получить равномерную массу, необходимую для создания качественной будущей постройки. Стоит отметить, что тара должна быть обязательно устойчивой. Идеальным решением вопроса с тарой для приготовления раствора в домашних условиях является использование старой чугунной ванны.
Инструмент должен быть легким и прочным. Это способствует более удобному созданию раствора. Если нет возможности использовать специальный миксер, можно для этих целей использовать дрель с насадками.
Прежде чем начать делать раствор правильно будет тщательно просеять порошок, что позволит избежать образования комков и попадание мусора в уже готовую смесь.
Приготовление
Прежде чем сделать раствор нужно правильно продумать последовательность всех необходимых действий. В первую очередь требуется разместить все расходные материалы и инструменты вблизи себя, чтобы не бегать за недостающими элементами во время работы.
Правильно начинать работу с просеивания песка и цемента с целью очищения смеси от мусора, который способен ухудшить вяжущие свойства цемента.
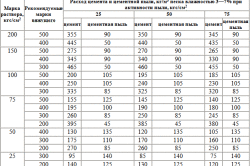
Схема расхода цемента.
Далее определяется соотношение каждого элемента, который будет входить в будущий раствор. На этом этапе важно помнить, что, используя высокую марку цемента, примесь строительного песка может быть незначительной. Также правильно использовать классическое соотношение, используемое строителями уже довольно длительный период времени. В этом случае одна часть цементного порошка смешивается с тремя частями песка.
Вода или любая другая жидкость добавляется в смесь только после того, как были тщательно перемешаны все компоненты. В емкость сначала насыпается песок и уже поверх него высыпается цемент.
Важно! Только при тщательном и грамотном подходе к смешиванию компонентов можно получить надежный и качественный раствор.
При создании раствора необходимо правильно влить жидкость, соблюдая при этом аккуратность и постепенность. В противном случае невозможно будет получить на выходе требуемую консистенцию.
Использование готового раствора
Только что приготовленный цементная смесь является таким строительным материалом, который не подлежит долгому хранению. Это связано с тем, что он обладает высоким показателем вязкости, за счет чего он моментально застывает. Если он не был вовремя применен, затвердевший цемент разбавлять водой заново ни в коем случае нельзя. Состав, который был правильно смешан, можно использовать только в течение часа.
Возможные исключения

При кладке кирпича однородная масса раствора не должна растекаться.
Иногда может случиться так, что цемент нужно сделать не по классическому рецепту, а по особой технологии, выбор которой полностью зависит от определенных целей.
Чтобы сделать нестандартную смесь, в нее добавляют всевозможные примеси, которые способны изменить свойства раствора. Это может быть изменение скорости застывания, улучшение показателей вязкости полученного вещества для придания пластичности смеси, необходимой при работе на более сложных участках. В качестве таких смесей чаще всего применяется известь.
Применяя дополнительные примеси нужно учитывать, что их пропорции зависят исключительно от качества исходного материала.
Проверка качества
Надежность и долговечность готовой конструкции, возведение которой требовало обязательно использование цемента, зависит от качества применяемого цементного раствора.
Смесь считается качественной, если она не растекается, то есть обладает средним или высоким уровнем вязкости. При этом она не должна быть сухой, так как это может привести к утере крепящих качеств цементного раствора, из-за чего кладка получится некачественной, а это уже ставит под угрозу разрушение строения.
Температура жидкости не должна быть высокой или слишком низкой. Вода должна иметь среднюю температуру, такую же, как и в окружающей среде на момент создания раствора.
При размешивании всех компонентов необходимо правильно проявить интенсивность движений. Если не приложить к процессу усилий, невозможно будет получить качественный и надежный раствор, с помощью которого можно будет построить прочную конструкцию, способную прослужить длительное время.
1pokirpichy.ru
4. Определение сроков схватывания цементного теста
Скорость схватывания – важное свойство портландцемента, определяющее жизнеспособность бетонной смеси. Быстрое и медленное схватывание – это существенный недостаток цемента. Если цемент схватывается быстро, то он превращается в камень, прежде чем его успевают использовать. Применение же медленно схватывающихся цементов замедляет темпы строительства.
Согласно ГОСТ 10178-85 начало схватывания должно наступить не ранее чем через 45 мин., а конец – не позднее чем через 10 ч. от начала затворения.
Тонкоизмельченный клинкер характеризуется короткими сроками схватывания (3 ... 5 мин), поэтому в чистом виде он непригоден. Для получения нормальных сроков схватывания при помоле клинкера вводят добавку двуводного гипса в количестве 3 ... 5%.
Начало схватывания характеризуется промежутком времени, прошедшим от начала затворения водой до того момента, когда игла при опускании не будет доходить до пластинки на 1 – 2 мм.
Концом схватывания характеризуется промежутком времени, прошедшим от начала затворения до момента, когда игла погружается в гипсовое тесто не более чем на 1,0 мм.
Примечание. В начальный момент опыта игла погружается до дна металлической формы.
Ход выполнения работы |
1. Ознакомиться с устройством прибора Вика. 2.Подготовить прибор Вика к выполнению лабораторной работы. Вставить в нижнюю часть стержня 2 иглу – (3). Проверить, свободно ли опускается стержень прибора, а также проверить нулевое показание прибора, приводя иглу в соприкосновение с пластинкой, на которой расположено кольцо. В случае отклонения от нуля, шкала прибора соответствующим образом передвигается. 3. Приготовить цементный раствор. Отвесить 200 г цемента, высыпать в чашку. Добавить для ускорения затвердевания цемента 15 г. алебастра. Сделать в смеси углубление, в которое влить в него в один прием 100 мл воды. 4. Быстро отвинтить закрепляющий винт, освободить стержень и предоставить игле свободно погружаться в тесто. Повторять опускание иглы каждые 3 мин, каждый раз, меняя место соприкосновения иглы с раствором и тщательно вытирая ее. Фиксировать грубину погружения иглы. |
В начале испытания иглу рекомендуется при погружении слегка задерживать, чтобы она не погнулась и не сломалась. Результаты опыта занести в таблицу 6.2. |
Таблица 6.2 - Глубина погружений иглы прибора Вика в цементное тесто
Время | 0 мин | 1 мин | 2 мин | 3 мин | 4 мин | 5 мин | 8 мин | 10 мин | 12 мин | 14 мин | и т.д. |
Глубина погружения иглы (мм) | ... мм | ... мм | ... мм | ... мм | .. мм | .. мм | .. мм | .. мм | .. мм | .. мм | .. мм |
5. Построить график схватывания цементного теста, и методом интерполяции, определить время конца схватывания. По горизонтальной оси надо откладывать время, по вертикальной оси – глубину погружения иглы. Построить график по точкам пересечения и затем плавно продолжить его до пересечения с горизонтальной осью. Это будет являться временем конца схватывания.
6. Определить по графику начало, конец и интервал схватывания цементного теста.
Заполнить строки 2, 3 и 4 итоговой таблицы 6.3.
Рисунок 6.2 – График схватывания цементного теста
studfiles.net