Алмазная резка швов - швонарезчик или шовнарезчик. Резка технических отверстий
Алмазная резка канатом больших отверстий
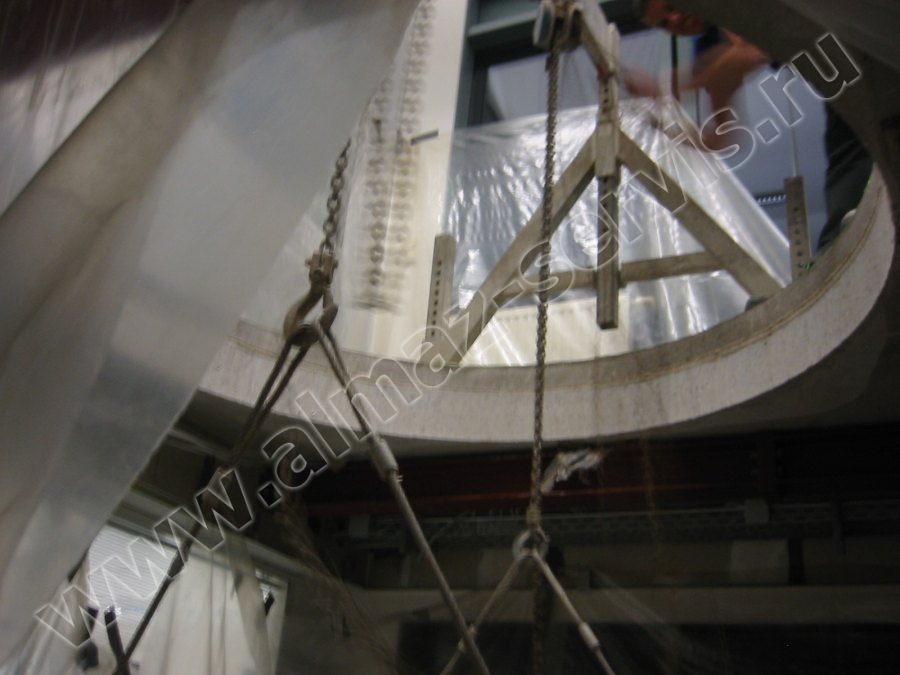
Область применения алмазной циркульной системы
Особенности и преимущества кругообразной канатной резки
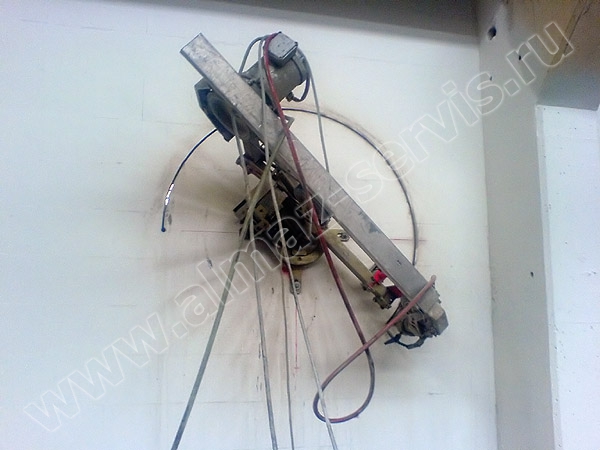
Используется для резки круглых отверстий от Ø1 м до Ø3,5 м в диаметре.
"РЕЖЕМ ЖЕЛЕЗОБЕТОН КАК МАСЛО!" - Не только в Новосибирске, но и от Урала до Камчатки!
Наш адрес:
г. Новосибирск ул. Инженерная, 4а, 5 этаж, офис 530 Индекс 630118 Отдел по алмазной циркульной резке: тел./факс: +7 383 332–05–34, Отдел по алмазному бурению: тел./факс: +7 383 335–68–03,Электронная почта: [email protected] Офис: с 9:00 до 18:00 , суббота, воскресение выходные. Работы возможно производить круглосуточно, в выходные и праздничные дни.
Алмазная циркульная резка![]() |
Круглый проём Ø1700 мм. готов, просто!![]() |
Резка круглых окон![]() |
Появились вопросы?! Пожалуйста, посетите наш форум. Мы постараемся на них ответить.
www.almaz-servis.ru
3.2. Техника резки
Техника ручной кислородной резки листов
Подготовка поверхности разрезаемого металла
Перед резкой поверхность разрезаемого металла по линии реза должна быть очищена от окалины, ржавчины, краски и грязи. Очистку можно производить щетками, пламенем резака, пескоструйной обработкой. При резке должен быть обеспечен свободный выход струи искр и шлака. С этой целью свободное пространство под разрезаемой деталью должно составлять не менее половины толщины металла плюс 100 мм. Отсутствие свободного пространства может привести к прерыванию процесса резки и обратному удару.
Начало резки
Резку металла обычно начинают с края детали. Подогревающее пламя направляют на край детали и нагревают его до температуры горения, после чего подается режущий кислород. При резке листовой стали резак в начальной точке резки устанавливают практически вертикально к поверхности листа. Для ускорения прогрева металла большой толщины рекомендуется делать зарубку зубилом в начальной точке реза. В ряде случаев при резке листов необходимо начинать резку не с края листа, а внутри контура листа. В этом случае необходимо производить операцию пробивки отверстия. С помощью ручной кислородной резки можно выполнять пробивку отверстий в листах толщиной до 100 мм. При большей толщине для пробивки отверстий применяются другие методы. При небольшой толщине (менее 20 мм) пробивку отверстия можно производить неподвижным резаком. С этой целью после подогрева металла до температуры горения плавно производят пуск режущего кислорода и немного поднимают резак для предотвращения попадания брызг на резак до момента окончания пробивки. При большей толщине после нагрева места пробивки плавно включают режущий кислород и одновременно начинают перемещение резака. В этом случае кислородная струя постепенно углубляется в металл.
Расстояние от режущего наконечника до металла
Для обеспечения качества реза и стабильности процесса резки расстояние от наконечника до металла необходимо поддерживать постоянным. При ручной резке этого можно добиться использованием специальных тележек, прикрепляемых к головке резака и другими способами. При резке листов менее 100 мм расстояние от наконечника до поверхности металла должно быть на расстоянии 2 – 3 мм от конца ядра. При большей толщине металла для избежания перегрева резака расстояние необходимо увеличить на 30 – 40%.
Рис. 31. Схема перемещения резака в процессе резки:
1. В начале реза; 2. В процессе резки; 3. В конце резки (3)
При резки со скосом кромки поверхности реза получаются не одинаковые по качеству. Поверхность б всегда лучше, чем поверхность а. Острый угол на поверхности а оплавляется сильнее, так как на нем концентрируется большая часть подогревающего пламени. Тупой угол поверхности а (нижняя кромка) омывается жидким шлаком кислородной струей, вследствие чего также оплавляется. Поэтому лучше, если позволяет характер реза, располагать резак таким образом, чтобы была использована отрезанная часть с поверхностью б.
Рис. 32. Вид поверхностей при резке под углом (3)
www.e-ope.ee
Обрезка концов рельсов, вырезка дефектов, мерная резка и сверление отверстий (Технологическая карта)
УТВЕРЖДАЮ
Начальник РСП-21
__________В.П.Челноков
« 12 » 02 2004 г.
ТЕХНОЛОГИЧЕСКАЯ КАРТА
Операция : ОБРЕЗКА КОНЦОВ РЕЛЬСОВ , ВЫРЕЗКА ДЕФЕКТОВ, МЕРНАЯ РЕЗКА И СВЕРЛЕНИЕ ОТВЕРСТИЙ..
Исполнитель : резчик-станочник на станках 3-го разряда-1 чел.
Оборудование : рельсорезно-сверлильные станки модели МП6-1515 , МП6-1185,, абразивныя шаровая головка, электротельфер-2 шт.,клещи-2 шт.,траверса-2 шт., оттяжки-2 шт.
Инструмент : дисковая пила Ø 630 ÷ 710 мм . .
Вспомогательный инструмент материалы : угольник , набор щупов ,штангенциркуль , щетка, ветошь ..
Индивидуальные средства защиты, защитные очки . рукавицы .
№№ п/п | Наименование операции | Технические требования |
1. | Произвести осмотр станка с записью в журнале т.осмотров и обслуживания . Выявленные недостатки или неисправности устранить. | 1..У рельсов, направляемых на профильную обработку, отрезают концевые участки на расстоянии не менее 10см от края последнего болтового отверстия, включая отверстия под штепсельные соединители и дроссельные перемычки . 2. У рельсов, полученных от разрезки бесстыковых плетей перед подачей их на фрезерование, предварительно обрезается по 20 см от места разрезки плети газопламенным способом для удаления зоны термического влияния . Длина кусков при этом должна быть не менее 6 м. Расстояние до ранее сваренного контактным способом (старого) сварного шва должно быть не менее 3 м. 3. Торцы рельсов после обрезки должны быть перпендикулярны к продольной оси. Перекос не должен превышать 1 мм при измерении в любом направлении . 4.Болтовые отверстия в рельсах бесстыкового пути и рельсах длинной 25 м должны быть просверлены по схеме , соответствующей данному типу рельсов. Диаметр отверстий и расстояние их от торца рельсов должны соответствовать размерам указанным в таблице 3.4 Технических условий на ремонт, сварку и использование старогодных рельсов № цпт-80/350 РЕЛЬСЫ ЖЕЛЕЗНОДОРОЖНЫЕ СТАРОГОДНЫЕ Поверхность болтовых отверстий должна быть гладкой без следов надрывов на кромках ,Отклонение по диаметру отверстий не должно превышать 1мм ; отклонение по расстоянию от торца рельса до центров болтовых отверстий не должно превышать 1,0 мм. На кромках болтовых отверстий и в торцах по всему сечению рельса должна быть снята фаска размером 15÷2 мм под углом 45º |
2.
3.
5.
6. | Включить станок . Проверить работу станка на холостом ходу . Продвинуть тельфер нажатием кнопок пульта управления до штабеля с рельсами. Расположить тельфер и соответственно крюк с клещами над головкой рельса. Захватить клещами головку рельса Поднять рельс тельфером на высоту 200-300 мм, убедиться в правильной его центровке . Перемещать рельс эл.тельфером ,поднимая на высоту не менее 0,5 м над всеми встречающимися препятствиями без «забега» одного конца относительно другого в горизонтальном и вертикальном направлениях , до рольганговой линии . Аккуратно уложить рельс на рольганговую линию. Убедиться в правильном (устойчивом)положении рельса на рольганговой линии . | |
7.
8 | ||
9. | Ослабить и снять клещи. | |
10. | Подать рельс по рольганговой линии к станку и установить в станок | |
11. | Зажать рельс в станке , включить станок . | |
12 | Произвести резку рельса по метке. | |
13. | Отжать зажим. | |
14. | Убрать отрезанный кусок на определенное место складирования . | |
15. | Проверить торец рельса по угольнику | |
16 | Рельс установить по шаблону , зажать . | |
17. | Просверлить отверстия .. | |
18.. | Выгнать рельс , снять фаски с отверстий .и по всему периметру . | |
19. | Продвинуть рельс за пределы станка . | |
20. | Снять рельс с рольганговой линии, уложить в штабель согласно схеме складирования. | |
21. | Повторить операции с 4-й по 10-ю . | |
22. | В конце смены убрать свое рабочее место и станок . |
Техника безопасности :
1.Проход по территории контактно-сварочного цеха и прилегающих к нему складов рельсов разрешается только по технологическим проходам, вдоль потоков, переход через которые осуществляется по переходным мостикам.
2. Запрещается :
-находиться под поднятым и перемещаемым грузом ;
-переходить через рольганговые линии ,пролезать под ними и перетаскивать инструмент в не установленных местах ;
-наступать на электрические провода и кабели.;
--прикасаться к оторванным проводам и другим легкодоступным токоведущим частям ;
-облокачиваться на потоки и браться руками или поправлять рельс во время движения .
3. Резчик должен содержать в исправном состоянии и чистоте рабочее место , станок , инструмент и приспособления всю смену.
4.Перед началом работ требуется убедиться в исправном состоянии станка ,наличии и исправности всех видов ограничителей, правильности работы блокировочных устройств ,работоспособности и наличии манометров ,
наличии и исправности ограждений приводных ремней ,устройств для фиксации рельса, надежности закрепления кожуха отрезного диска.
5. Запрещается приступать к работе при :
-отсутствии кожухов ,щитков и других защитных приспособлений ;
-неисправности заземляющих устройств ;
-отсутствии смазки ;
- затупленной пиле или сверлах ;
-наличии утечек масла из гидросистеиы ;
-неисправности зажимных и транспортных уст-в .
6.Запрещается производить работы на станке при неисправности блокировки ,контрольно-сигнальных и регулирующих устройств, вращающихся частях станка .
7.Запрещается :
-выполнять любые виды ремонтных работ гидросистемы ,находящихся под давлением и электросхемы, находящейся под напряжением ;
-работать на станке при замыкании на землю цепей управления ;
-оставлять отсоединенными и не заглушенными отверстия после завершения ремонтных работ в системе гидропривода ;
-отвлекаться во время работы на посторонние разговоры ;
-присутствие посторонних лиц на рабочем месте станочника .
При выполнении обязанностей стропальщика :
1.Во время работы стропальщик должен находиться в защитной каске и иметь при себе удостоверение .
2.При работе на электротельфере или электротали запрещается :
-работать лицам, не имеющим удостоверения стропальщика ;
-работать на неисправном или не отремонтированном механизме ;
-поднимать и перемещать при помощи электротельфера людей ;
-работать при неисправности ограничителя подъема или его отсутствии ;
-постоянно пользоваться ограничителем подъема для остановки крюка.
3 Запрещается производить погрузочно-разгрузочные работы без рукавиц.
4..Перед началом работ обязан :
-произвести осмотр и подготовку площадки складирования
-проверить работу концевого выключателя;
-всех кнопок пульта управления ;
-работу тормозов;
-проверить исправность грузозахватных приспособлений (они должны быть испытаны и замаркированы ).
-осмотреть грузоподъемные механизмы;
-проверить правильность навивки каната на барабан ;
-проверить освещенность места производства работ,
-проверить служебные проходы (в зимнее время очистить их от снега, при необходимости посыпать песком).
-проверить исправность гибкого кабеля пульта управления .
5.При перемещении или подъемке рельсов не допускать их раскачку. Для предотвращения самостоятельного разворота длинномерных и громоздких грузов во время их подъема или перемещения применять специальные оттяжки.
6.При производстве работ запрещается :
-подъем и перемещение груза над людьми ;
-отрывать и перемещать грузы уложенные в «залив» ;
-оставлять на продолжительное время груз в подвешенном состоянии ;
-подтягивать рельсы с земли при косом натяжении троса ;
-передавать управление тельфером постороннему лицу ;
-производить подъемку и перемещение рельсов при несогласованности действий со вторым стропальщиком ;
-производить самостоятельный ремонт электрического и механического оборудования.
7.Укладка рельсов на складе производиться в соответствии с требованиями штабелевания.
8.При длине рельсов 12,5 м и более производить захват их необходимо не менее чем в двух местах.
9.Подача рельсов в одно лицо запрещена.
9.При укладке рельса на роликовый путь перед тем , как освободить его от клещей следует убедиться в том , что рельс лежит на роликах.
Исполнитель технолог Ромахина М.Ю.
И.о.главного инженера С.Н.Белышев
vunivere.ru
18. Резка отверстий в металле
Компания Hypertherm, один из мировых лидеров по производству источников тока для плазменной резки запатентовала технологию TRUE HOLE, призванную решить проблему качественной вырезки отверстий под болтовое соединение.
Какие проблемы в обработке отверстий необходимо было решить:
- Перегиб или задир внутри отверстия:
Рис. 48. Задир внутри отверстия (17)
- Сужение нижнего диаметра отверстия по отношению к верхнему:
Рис. 49. Отверстие. Красная линия – желаемая форма, синяя – реальная форма (17)
Какие параметры резки необходимо исправить для получения отверстия желаемой формы:1. Использовать в качестве плазмообразующего и защитного газов чистый технический кислород (Чистый 99,5%, сухой, обезжиренный, давление 793 кПа, расход 4250 л/час). Использование кислорода обуславливается тем, что этот газ лучше горит, чем воздух.
2. Необходима пониженная подача защитного газа во время резки отверстия.3. Для получения идеальной формы отверстия необходимо осуществлять пробивку строго посередине желаемой формы отверстия, для этого необходимо отключение компенсации движения дуги на величину радиуса дуги.
4. Вход на рабочую траекторию необходимо осуществлять строго по касательной к контуру.5. На конечном участке траектории необходимо уменьшение скорости резки, силы тока (20% от рабочего тока) и выключение движения самого станка из-за инерционности движения головки.
Данная технология имеет следующие ограничения: только сталь, толщина от 3 до 25 мм.
Рис. 50. Сравнение качества вырезания отверстий без использования и с использовнием технологии True Hole (16)
1. Отверстие 12 мм вырезанное с помощью плазменной системы HPRXD без использования технологии True Hole.
2. Отверстие 12 мм вырезанное с помощью плазменной системы HPRXD при использовании технологии True Hole.
При этом все выполняется автоматически без участия оператора, в результате чего достигается небывалое качество отверстия.
www.e-ope.ee
Алмазная резка швов - швонарезчик или шовнарезчик
Компания «LOMBETON» предлагает комплексный спектр услуг по алмазной резке швов. Мы квалифицированно выполняем данный вид работ на любой горизонтальной поверхности. Сотрудничество с нами станет для Вас по-настоящему качественным, так как к любому заказу наша компания подходит индивидуально и ответственно.
Алмазная резка швов - это из самых экономичных и при этом эффективных способов выполнения определенного ряда специальных работ. В большинстве случаев такая резка требуется тогда, когда в горизонтальных бетонных конструкциях необходимо организовать углубления или ниши, лотки. Также алмазная резка швов с успехом применяется при строительстве новых и ремонте старых тротуаров, мостов и дорог. Вместе с тем без данного вида работ не обойтись при снятии локальных участков защитного покрытия дороги, прокладке и ремонте подземных коммуникаций. Кроме того, алмазная резка швов востребована в нестандартном строительстве.
Швонарезчик — это специальная дисковая установка для алмазной резки швов. Внешне такое оборудование представляет собой станину (основную неподвижную часть машины). Эта станина оснащена электрическим или гидравлическим двигателем и алмазным диском. Также шовнарезчик имеет систему, в том числе автоматическую с приводом, подведения алмазного диска, а также водяного охлаждения режущего диска.
В распоряжении компании «LOMBETON» находятся различные швонарезчики. Так, у нас имеются шовнарезчики, которые отличаются небольшим весом и компактными габаритами, что соответственно делает их удобными в использовании в квартирах, частных домах, помещениях с низкими потолками и так далее. Помимо удобных мобильных швонарезчиков, в арсенале компании «LOMBETON» имеются мощные дизельные и электрические нарезчики швов, которые идеально подходят для алмазной резки толстых перекрытий и полов толщиной до 500 мм, покрытий автомагистралей, стоянок и паркингов, причальных комплексов, взлетно-посадочных полос и др.
Разнообразие шовнарезчиков с высокими техническими характеристиками позволяет выполнить работы по алмазной резке швов малочисленными бригадами, быстро, качественно, рационально при невысокой стоимости работ.
В каждом случае наши специалисты учитывают необходимую глубину реза и характеристики материала, с которым предстоит работать. Ввиду этого они подбирают наиболее подходящий тип швонарезчика, а потому легко справляются с поставленными задачами.
Чтобы узнать более подробную информацию об услуге алмазной резки швов, Вам следует связаться по телефону с нашими менеджерами. Они смогут подробно ответить на все интересующие Вас вопросы.
ДРУГИЕ СТАТЬИ РАЗДЕЛА
lombeton.ru
Технология резки - Газовая резка
Технология резки
Ручная разделительная резка. Подлежащий резке лист укладывают на подкладки, выверяют и при необходимости закрепляют. Затем места предполагаемого реза очищают от окалины, ржавчины, грязи, неблагоприятно влияющих на качество реза. Лист размечают мелом или чертилками таким образом, чтобы металл был максимально использован. После подбора номера наружного и внутреннего мандштуков в зависимости от толщины разрезаемого металла, зажигают смесь и проверяют, устойчиво ли горит пламя резака. Обычно резку начинают с кромки листа.
Если резку надо начать не с середины листа, а отступив на некоторое расстояние от его кромки (при вырезке фланцев), то прожигают кислородом отверстие, от кромки которого начинают резку. В месте начала реза нагревают металл, затем открывают вентиль режущего кислорода и перемещают резак по разметке.
Время начального подогрева ацетилено-кислородным пламенем при резке с кромки металла толщиной 5—200 мм составляет 3—10 сек. При пробивке отверстия кислородом данное время увеличивается в 3—4,5 раза.
Основным показателем режима резки являются давление режущего кислорода, чистота его и скорость резки. Давление режущего кислорода зависит от конструкции резака и мундштуков.
Скорость резки зависит толщины металла, метода резки (ручная или машинная), линии реза (по прямолинейному или фасонному контуру) и ее вида, т. е. разделочной, заготовительной с соответствующим припуском на обработку, под сварку. Минимальными скоростями пользуются при чистовой резке деталей криволинейного контура (фланцы и т. д.).
При резке металла на малой скорости происходит оплавление кромок реза, а при большой скорости — значительное отставание кислородной струи. В этом случае появляются не дорезанные до конца участки.
Скорость резки прямо пропорциональна чистоте режущего кислорода. При понижении чистоты скорость резки значительно уменьшается, а расход кислорода резко возрастает.
В среднем при снижении чистоты кислорода на 1% время резки 1 м стали увеличивается на 10—15%, а расход кислорода — на 25—35%. В значительной степени ухудшается чистота реза с понижением чистоты кислорода.
Если в кислороде содержится примеси (азот, аргон и др.) более 2%, то такой кислород применять нельзя, так как в этом случае поверхность реза получается не чистой, с глубокими рисками и трудноотделяемым шламом.
При ручной резке надо пользоваться опорной тележкой для резака, циркулем, направляющими линейками и т. д.
При массовом изготовлении однотипных деталей малой толщины применяют так называемую пакетную резку, при которой набирают максимальное количество листов, какое может разрезать резак, собирают их в пакет и плотно сжимают струбцинами. Вместо струбцин набранный пакет можно скрепить вертикальными швами по его кромкам дуговой электросваркой. Лучшие результаты резки получаются, когда пакет набран из листов толщиной 2—5 мм. Резку пакета начинают с нижней кромки, поднимая резак по торцу пакета. При достижении верхней кромки резак ведут по разметке, следя за тем, чтобы прорезался весь пакет. С применением резаков низкого давления пакетная резка протекает эффективнее. При резке кислородом низкого давления (1,5 кгс/см2) можно разрезать пакет толщиной 80—120 мм с ростом производительности резки в 1,5—2 раза.
При резке стали большой толщины с применением кислорода низкого давления металл располагают так, чтобы зазор между нижней плоскостью металла и опорой составлял 300—500 мм. Данный зазор обеспечивает свободное стекание шлака в процессе резки и не создает противодавления кислородной струе. На процесс резки существенное влияние оказывает характер подогревающего пламени.
В процессе резки металла большой толщины (рис. 49) пламя должно быть с избытком ацетилена, что позволяет увеличить его длину с равномерным выделением тепла по всей длине факела, это способствует про-резанию металла по всей его толщине.
Торец металла, особенно в нижней части, надо хорошо подогреть пламенем резака, для чего в начале резки мундштук выдвигают примерно на [/з диаметра пламени вперед от верхней кромки реза.
При открывании вентиля режущего кислорода мундштук несколько отклоняют в направлении резки. Данный технологический прием в процессе резки способствует «врезанию» струи кислорода в металл и предупреждает образование «порога», ниже которого сталь гореть не может. Для пуска режущей струи кислорода вентиль открывают медленно, по мере врезания в металл.
Поверхностную стружку металла производят при наклоне режущей струи кислорода к поверхности металла под углом 15—40°. Ширину реза при этом определяют диаметром режущей струи кислорода. Скорость поверхностной резки 1—6 м/мин.
Рис. 49. Положение мундштука при резке стали больших толщин
Рис. 50. Положение мундштука при скоростной резке1 — струя режущего кислорода; 2 — защищающие боковые струи; 3 — подогревающее пламя
Если чистоту кислорода увеличить на 1%, скорость резки увеличится на 15%.
При большой скорости истечения горючей смеси применяют многосопловые мундштуки с диаметром каждого сопла 1,8—3 мм, учитывая при этом расход смеси.
Скоростная резка осуществляется путем наклона струи режущего кислорода под углом а к поверхности разрезаемого металла, который равен 30—60° в зависимости от толщины разрезаемого металла. При таком наклоне более полно используется кислород режущей струн, позволяющей прорезать большой участок по длине (рис. 50) и значительно повысить скорость резки. В процессе резки подогревающее пламя направляется на кромку верхней поверхности разрезаемого металла и подогревает его до температуры сгорания. Данным способом режут сталь толщиной 3—50 мм при скоростях в 1,5—3 раза выше обычных. Скоростную резку производят на обычных переносных резательных машинах или используют для этих целей тележки, применяемые при машинной плазменно-дуговой резке с пределом регулирования скорости перемещения от 118 до 8000 мм/мин.
При машинной резке листы укладывают на передвижные или стационарные столы из швеллеров, на которых в качестве опор для разрезаемого листа установлены штыри. Столы снабжены специальными поддонами, в которые попадает выдуваемый при резке шлак. Для вырезки деталей с точными размерами лист перед резкой правят. Плоскость копира и поверхность разрезаемого листа должны быть расположены строго горизонтально.
Рис. 51. Возможные деформации и способы их уменьшения при вырезке деталей замкнутого контураа — деформация отрезанной части листа; б—начало резания по зигзагообразной линии; в — закрепление детали клиньями после прохождения резака; г — последовательность резки листа на полосы одним резаком; д — машинная резка листа на полосы двумя резаками
Расстояние от поверхности пола или поддона должно быть не менее 0,555+100 (где S — толщина разрезаемо» го листа в мм).
При меньшем расстоянии вытекающая струя и шлаки, отражаясь от поверхности пола или поддона, испортят поверхность реза.
При машинной резке отверстия пробивают ручным резаком во избежание забивки брызгами жидкого металла или шлака каналов машинного мундштука.
Деформация при резке. В результате местного нагрева при кислородной резке возникает значительное коробление листа, из которого вырезают деталь. Во время резки возможно коробление самой детали. При отрезке полосы от края листа деформации приведут к выгибу листа и самой полосы. Когда вторую полосу отрезают с противоположной стороны, то прогиб листа будет меньше. Порядок резки нескольким полос небольшой ширины из длинных листов показан на рис. 51.
На рис. 51, а показано деформирование отрезанной части; чтобы обрезанная часть не могла свободно деформироваться, оставляют «замок» (рис. 51,6) или перемычки перерезают после того, как лист остынет полностью. Перемычки длиной 6—10 мм оставляют через каждые 500—800 мм длины реза. После разрезки перемычек в местах их расположения у вырезанных деталей остаются выхваты металла, которые при автоматической сварке могут быть очагом прожога.
При вырезке детали (особенно при машинной резке) в замкнутом контуре после прохождения резака ее закрепляют клиньями в точках, обозначенных цифрами на рис. 51,6.
Читать далее:Эксплуатация газосварочной и газорезательной аппаратуры и оборудованияЭксплуатация переносных ацетиленовых генераторовКачество сварных соединенийМеханизированная резкаРучная резкаCварочные деформации и напряженияCварка чугунаCварка цветных металлов и сплавовСварка низкоуглеродистой сталиТехника наложения сварных швов
stroy-server.ru
Технология разделительной кислородной резки
Подробности Подробности Опубликовано 27.05.2012 13:09 Просмотров: 11366При выполнении разделительной кислородной резки необходимо учитывать, какие требования предъявляются к точности резки и качеству поверхности вырезаемой детали. Чем ниже эти требования, тем меньше расходуется кислорода и горючего и тем большей может быть скорость резки.
Например, при разделочной резке (резка в лом) качество поверхности и точность резки не имеют значения. Поэтому резка ведется вручную при наибольшей возможной скорости.
При заготовительной резке (вырезается заготовка, из которой механической обработкой изготавливается деталь) качество реза также не имеет значения, но должен быть выдержан определенный размер заготовки при наименьших припусках на механическую обработку. Резка производится вручную. При этом часто применяются простейшие приспособления (опорные ролики, циркуль, направляющие тележки и т. п.), с помощью которых легче выдержать задаваемые припуски.
Резка под сварку должна осуществляться так, чтобы была чистая поверхность реза и были соблюдены заданные размеры детали. Требования повышаются, когда детали подготавливаются под автоматическую сварку. В этом случае применяется обычно механизированная резка.
Чистовая вырезка круглых и фасонных деталей, которые будут использованы без последующей механической обработки, производится только автоматами.
Таким образом, в зависимости от вида кислородной разделительной резки необходимо добиваться определенного качества реза.
Качество реза определяется следующими показателями.
Отклонением линии реза от намеченной (не получается прямолинейный рез, вместо окружности получился эллипс и т. д.). Это отклонение вызывается смещением резака или разрезаемого листа, деформацией листа в процессе резки.
Отклонением от заданного угла реза, которое наблюдается при изменении угла наклона резака, при изменении формы струи режущего кислорода или при неправильно выбранной скорости резки.
Степенью оплавления верхней кромки, которое происходит при излишней мощности подогревающего пламени или заниженной скорости резки.
Глубиной и искривлением бороздок на поверхности реза. Эти бороздки обычно имеют криволинейное очертание, что объясняется отставанием режущей струи кислорода. Отставание становится особенно заметным при слишком высокой скорости резки или при слишком низком давлении кислорода.
Глубина бороздок также зависит от скорости перемещения резака и давления кислорода. Образованию бороздок способствует неравномерная скорость передвижения резака и колебания его, а также засорение отверстия режущего мундштука.
Техника резки. Перед началом резки лист нужно уложить на подкладки, чтобы беспрепятственно удалялись шлаки из места реза. Зазор между полом и, нижней плоскостью листа должен быть не менее 100— 150 мм. Затем лист по предполагаемой линии реза необходимо очистить от окалины, ржавчины, краски и других загрязнений. При кислородной резке металла с загрязненной поверхностью резко ухудшается качество резки и уменьшается производительность.
Зачистка поверхности производится стальной щеткой. Для удаления окалины, краски и масла следует медленно провести по линии реза пламенем резака или горелки. Под действием тепла окалина отделится от поверхности металла, краска и масло сгорят. После этого поверхность зачищают стальной щеткой.
Разметка листа производится с помощью чертилки или мела. Перед началом резки газорезчик подбирает и устанавливает на резаке нужные для заданной толщины разрезаемого металла номера мундштуков, проверяет редукторы, водяной затвор, шланги, резак, вентили баллонов, присоединяет шланги и надежно их закрепляет на резаке и источнике газов.
Установив необходимое давление газов, производят зажигание резака и регулировку пламени. Состав, свойства и строение подогревательного пламени такие же, как и у сварочного.
Роль подогревательного пламени при разделительной кислородной резке различна в зависимости от толщины разрезаемой стали, условий резки и требований, предъявляемых к поверхности реза.
При резке стали толщиной до 80 мм на скорость резки главным образом влияет мощность подогревательного пламени: чем мощнее пламя, тем больше скорость. Количество тепла, выделяемое подогревательным пламенем, больше или равно количеству тепла, получаемого при сжигании металла во время резки. Однако увеличивать в значительной степени подогревательное пламя нельзя, так как начинают заметно оплавляться верхние кромки реза. Поэтому в данном случае выгоднее брать подогревающее пламя с избытком кислорода, при котором получается высокая концентрация тепла на поверхности нагреваемого листа.
При резке стали толщиной 80—300 мм наилучшее состояние поверхности обеспечивается при нормальном подогревательном пламени.
При резке стали толщиной свыше 300 мм количество тепла, выделяемое подогревательным пламенем, значительно меньше количества тепла, получаемого при сгорании металла в месте реза. В этом случае следует брать подогревательное пламя с избытком ацетилена.
При резке литья, покрытого окисленной коркой и песком, а также при резке проката с окалиной и ржавчиной на поверхности необходимо более мощное пламя с избытком кислорода для быстрого удаления (оплавления) поверхностного слоя и доведения чистого металла до температуры воспламенения, чем при резке проката с чистой поверхностью.
Окончательную регулировку пламени необходимо вести при открытом вентиле режущего кислорода. В противном случае вследствие того, что режущий и подогревательный кислород поступает в резак по одному шлангу, при пуске режущего кислорода во время резки пламя будет обедняться кислородом.
При пуске режущей струи кислорода подогревательное пламя не должно гаснуть или изменяться по форме и размерам.
Мощность подогревательного пламени выбирают в зависимости от толщины разрезаемого металла, скорости резки и состава стали. Требуемая для подогрева мощность увеличивается при увеличении содержания в стали углерода и специальных примесей.
Практически при резке листовой стали ядро пламени отстоит от поверхности металла на 1,5—2,5 мм. Расстояние от мундштука до металла в процессе резки следует поддерживать постоянным.
Давление режущего кислорода также имеет большое значение при резке. При слишком большом давлении увеличивается расход, кислорода и разрез получается менее чистым. При недостаточном давлении шлаки не будут выдуваться и резка будет происходить не на всю толщину металла.
Процесс резки начинается с нагревания участка металла, расположенного в начале намечаемой линии разреза, до температуры, близкой к температуре плавления металла. Затем на нагретое место пускают струю режущего кислорода и начинают перемещать резак вдоль линии реза.
В некоторых случаях резку приходится начинать не с края поверхности. В этом случае необходимо в точке начала реза проделать отверстие диаметром, равным примерно ширине предполагаемого реза. При толщине металла до 50 мм это отверстие может быть вырезано ручным резаком. В этом случае поверхность листа подогревают при вертикальном положении горелки резака. После подогрева головку резака наклоняют и одновременно подают режущий кислород. В наклонном положении головка удерживается в течение времени, какое нужно для получения сквозного отверстия. Этот наклон головки резака необходим для того, чтобы предупредить засорение отверстия сопла подогревающего пламени шлаком. Признаком засорения являются, хлопки. С получением сквозного отверстия головке резака придают нормальное положение, и отверстие разделывается до нужных размеров.
При толщине металла 50—100 мм отверстие просверливается сверлом. При больших толщинах первоначальное отверстие в металле может прожигаться кислородным копьем.
При резке металла круглого сечения на поверхности в месте начала реза надо сделать насечку зубилом. В месте насечки края металла быстро нагреваются до температуры воспламенения и тем самым облегчается начало процесса резки.
В начале резки подогревательное пламя резака, направляемое на край разрезаемого металла, может составлять различные углы наклона к поверхности. При резке металла толщиной до 50 мм подогревательное пламя направляется вертикально. При резке более толстого металла подогревательное пламя резака устанавливается с наклоном к поверхности разрезаемого металла на угол 10—15° по ходу резака, что позволяет лучше прогреть кромки по всей толщине металла и облегчить начало процесса резки. Резку толстого металла часто начинают с нижней кромки, постепенно поднимая резак по торцу до верхней кромки, после чего производят резку на всю толщину.
Положение резака в процессе резки деталей малой толщины (до 5—6 мм) должно быть таким, чтобы режущая струя имела наклон в направлении, противоположном направлению резки, что искусственно увеличивает разрезаемую толщину, замедляет прогрев места реза и тем самым предупреждает оплавление кромок.
При резке деталей средней толщины (10—50 мм) резак обычно устанавливается перпендикулярно к поверхности разрезаемого металла. Однако при резке по прямой линии листовой стали толщиной до 30 мм резак следует располагать с наклоном на угол 20—30° в сторону, обратную движению. В этом случае скорость резки существенно повышается.
При резке металла большой толщины перпендикулярное направление режущей струи приводит к отставанию резки нижней кромки, и резка может прекратиться. Поэтому при резке деталей толщиной свыше 50 мм режущую струю следует направлять по ходу резки под углом 15—25° от вертикали для достижения полного срезания нижнего края листа. Наклоны резака возможны только при выполнении резки вручную или при прямолинейной резке резательными приборами. При резке по криволинейным контурам положение резака должно быть перпендикулярным к поверхности разрезаемого металла.
Движение резака должно быть равномерным. Скорость передвижения резака должна соответствовать скорости окисления металла. При движении резака с правильно установленной скоростью поток искр вылетает под прямым углом к разрезаемой поверхности, т. е. прямо вниз. При слишком большой скорости движения резака поток искр будет отставать, а при слишком медленном — опережать резак.
По окончании резки резак следует задержать на выходе и произвести разрез нижнего участка (если имеется значительное отставание).
При резке с предварительным подогревом, обычно применяющимся для сталей с повышенным содержанием углерода и специальных примесей, скорость резки увеличивается. Температура подогрева берется около 300°.
При резке профильной стали - уголка, швеллера, двутавра и других — нужно направлять струю режущего кислорода так, чтобы не повредить соседнюю полку или стенку.
При реже углового профиля лучше всего положить его на прокладку краями полок вниз, утлом вверх. Резку производить снизу без перерывов. По мере передвижения резака к вершине угла струю режущего кислорода необходимо наклонить в сторону начала реза, т. е. от второй полки, с тем чтобы ее не повредить. Такой же наклон придается головке резака , при резке швеллера,
При резке тавра или двутавра при приближении резака к средине полки его также следует наклонить струей наружу (от стенки) и в таком положении перерезать металл за средину полки. Далее, не прерывая резки, резак нужно установить перпендикулярно к полке.
При резке стальных заготовок круглого сечения положение резака в момент подогрева должно соответствовать позиции 7, а при резке — позиции 2.
Для повышения производительности и качества резки следует использовать простейшие приспособления: циркульное устройство и тележку, поставляемые заводом-изготовителем к каждому резаку, а также направляющие. Такие приспособления дают возможность избежать случайных колебаний резака относительно линии реза.
На рисунке приведены примеры вырезки кругов и отверстий при помощи циркуля и резки трубы с помощью специальной каретки.
При резке по окружности газорезчику приходится перемешаться вместе с резаком, что представляет большие неудобства.
В этих случаях лучше пользоваться циркулем с вращающейся головкой.
Циркуль имеет головку 3, внутри которой свободно вращается втулка 1. В последней крепится резак 6 винтом 2.При резке по окружности резчик остается на месте, шланги при этом не скручиваются, так как положение резака во время работы сохраняется в одном направлении, а вращается только головка циркуля вокруг центра 7.
В головке циркуля имеется гнездо с резьбой для крепления планки с опорным роликом.
Вращающаяся головка для резки по окружности позволяет укреплять резак на необходимой высоте. При резке ровных листов могут быть применены простейшие приспособления.
Однотипные фигурные детали могут вырезаться с помощью шаблона, устанавливаемого на разрезаемый лист. Постоянство расстояния между концом мундштука резака и поверхностью листа обеспечивается кольцом 2, укрепляемым на головке резака. Головка резака в процессе резки прижимается к краю шаблона.
При резке тавра или двутавра при приближении резака к средине полки его также следует наклонить струей наружу (от стенки) и в таком положении перерезать металл за средину полки. Далее, не прерывая резки, резак нужно установить перпендикулярно к полке.
Читайте также
Добавить комментарий
electrowelder.ru