Пропорции раствора для шлакоблока: цемент, шлак, песок и вода, технология изготовления. Пропорции шлакобетон
Состав шлакобетона.
Изготовление шлакоблоков производится из шлакобетона, который относится к разряду легких бетонов. В качестве заполнителя в подобном бетоне используют металлургические шлаки или топливные шлаки, которые раздробили, рассеяли и очистили от вредных примесей. Из шлакоблоков изготавливают прочные, несгораемые, дешевые стены с низкой теплопроводностью. Шлакоблоки выгодно отличаются от пескоблоков более легким весом, и от пеноблоков – большей прочностью.
Шлакобетон, входящий в состав шлакоблоков, обладает гранулометрическим составом, в котором имеется особое соотношение частиц шлакового заполнителя: крупных (5-40 мм) и мелких (0,2-5 мм). Дело в том, что если будет использованы только мелкие частицы шлакового наполнителя, бетон получится относительно теплопроводным и очень плотным, а при использовании крупных частиц, бетон будет легким, но непрочным. Соотношение мелкого и крупного шлака при возведении наружных стен из шлакоблока должно быть следующим: от 3:7 до 4:6. При возведении внутренних несущих стен, для которых требуется большая прочность, шлакоблоки изготавливают с большим добавлением мелкого шлака. В состав шлакобетона не добавляют кусковой шлак, величина которого превышает 10 миллиметров.
Самыми прочными считаются блоки из металлургического и топливного шлака, в которые добавлено 10-20% песка. В данном сырье не должно быть примесей глины, золы, мусора или несгоревшего угля. Шлак в течение года держат в отвалах на открытом воздухе, чтобы уменьшить количество необожженных частиц глины и вредных солей в его составе. Цемент используют в качестве связующего материала в производстве смеси. А присадки из глины или извести служат для придания шлакобетону большей пластичности.
Шлакобетон изготавливают по следующей технологии. Отсортировывают шлак путем просеивания его через специальное сито. Затем, приготавливают шлаковую смесь, соединяя отсортированный крупный (с зернами 40 мм) и мелкий (с зернами от1 до5 мм) шлак в соотношении два к одному. В качестве вяжущего материала могут быть использованы цемент, гипс, известь или глина. Если вяжущим материалом является цемент, то смесь готовят в соответствии со следующими пропорциями: 1 часть цемента, 3 части шлака и 4 части извести. Смесь пригодна для использования в течение одного часа.Если вяжущим материалом является гипс, то приготовление смеси производится небольшими порциями, так как ее нужно приготовить и использовать в течение 6 минут. В подобной смеси используют следующие пропорции: 1 часть гипса, 3 части шлаковой смеси. Их перемешивают с добавлением воды и тут же используют. Чтобы повысить прочность шлакоблоков, шлак предварительно увлажняют. Количество воды, необходимой для приготовления 1 м3 шлакобетона, варьируется в пределах от 250 до 350 литров.
Шлакоблоки могут иметь не только привычные серый цвет, но и яркие цвета. Их можно получить, если добавить в смесь краситель, которым может быть цветной мел или порошок от размола красных кирпичей. В состав шлакобетона может входить каолин, представляющий собой белый порошок. Иногда вместо него добавляют молотый кирпич. Подобная технология позволяет получать шлакоблоки с высокими прочностными характеристиками, а также изготавливать блоки с наполнителями: керамзитом, опилками, шлаком и др.Блоки могут иметь самые разные формы и размеры и изготавливать их можно, как на месте строительства, так и в домашних условиях. Чтобы изготовить форму для шлакоблоков, обычно используют дерево, хотя возможно применение и других материалов. Внутренняя поверхность формы, перед наполнением ее смесью, должна быть увлажнена.
www.omsb.ru
Для постоянного проживания в сельской местности хочу построить одноэтажный каменный дом общей площадью 60м2, стены которого планирую залить по опалубке шлакобетонным составом. Какие должны быть пропорции цемента и шлака? Какая толщина стен должна быть для наших климатических условий? Надо ли утеплять стены такого дома? :: Вопрос
Легкие бетоны на основе котельных шлаков еще недавно широко употреблялись для строительства, как садовых домиков, так и жилых домов, особенно в районах бедных лесными ресурсами. Даже сейчас, когда в моду вошли постройки из ячеистого бетона, шлакобетон не сдает своих позиций. Наличие в большом количестве почти бесплатного сырья и простота приготовления смеси – вот те составляющие, которые обуславливают его применение в широком диапазоне построек всех типов. Перед использованием шлака его очищают от земли, золы, особенно несгоревшего угля, а также других посторонних включений. Затем шлак просеивают на сите с ячейками 40х40мм, а затем – 5х5 мм. То, что не прошло через сито 5х5мм, считается крупным шлаком. Прошедший же через это сито шлак просеивают на сите с ячейками 1х1 мм. Образуются как бы две фракции шлака – крупная, не прошедшая через сито с ячейками 5х5мм и мелкая, не прошедшая через сито 1х1 мм. 60÷70% крупного и 30÷40% мелкого шлака смешивают с одним или двумя вяжущими. Прочность шлакобетона и его теплопроводность во многом зависят от его гранулометрического состава, то есть от соотношения мелких до 5 мм и крупных более 5 мм частей шлакового заполнителя. Так при более крупных фракциях шлака бетон получается более легким, но менее прочным и, наоборот, при мелких частицах, более теплопроводным, но более прочным. Наилучшее соотношение мелких и крупных частей шлака для наружных стен составляет от 5:5 до 3:7. Шлак более мелких фракций в большем количестве используют для возведения внутренних несущих стен, где нет таких жестких требований к конструктивным элементам зданий по энергосбережению. Поэтому для возведения перегородок фракции более 10 мм в состав шлакобетонной массы вообще не включают. В качестве связующего бетонной смеси используют портландцемент. Для придания смеси повышенной пластичности и удобства при укладке применяют добавки извести или глины. Кроме того, с целью повышения прочности бетона, примерно 30% шлака заменяют песком. Технология приготовления шлакобетона несложна. Отмеривают крупный и мелкий шлак, смесь перелопачивают, добавляют цемент, еще раз все хорошо перелопачивают, смачивают водой и опять перелопачивают до получения однородной массы. Шлакобетон используют в течение 1 часа. Ориентировочные составы для приготовления шлакобетонной смеси представлены в следующей таблице:
Марка шлакобетона |
Материалы для получения 1 м3 шлакобетона |
Соотношение мелкого и крупного шлака |
Плотность шлакобетона, кг/м3 |
|||
цемент марки «400» |
известь или глина |
песок |
шлак |
|||
М10 |
50/45 |
50/35 |
100/60 |
700/1000 |
2:8 |
900 |
М25 |
100/90 |
50/35 |
200/125 |
700/900 |
3:7 |
1050 |
М35 |
|
50/35 |
300/190 |
700/800 |
4:6 |
1200 |
М50 |
200/180 |
50/35 |
400/250 |
700/700 |
5:5 |
1350 |
Примечания. 1. В числителе даны компоненты смеси в кг, а в знаменателе те же компоненты в объемных единицах (л). Например, если указано, что для шлакобетона марки М10 необходимо количество цемента марки «400» – 50/45, то это значит, что цемента по весу надо взять 50 кг, что соответствует 45 л объема. 2. Для повышения прочности за несколько часов до приготовления бетонной смеси надо увлажнить шлак. На приготовление 1 м3 шлакобетона расходуется 250÷350 л воды. 3. Готовя шлакобетон определенной марки, следует учитывать не только количество материалов, взятых по объему, но и марку цемента. Толщина шлакобетонных стен зависит от климатических условий места проживания. Минимальная толщина стен зависит от конструктивных особенностей постройки. Обычно толщину стен выполняют в пределах 300 ÷ 600мм. В соответствии с требованиями СНиП 23-02-2003 «Тепловая защита зданий» стены дома необходимо утеплить. Расчетная толщина теплоизоляционного материала, например, «Rockwool ЛАИТ БАТТС» (1000x600x50)м3 при условии: город – Москва; температура воздуха внутри помещения – 18оС; материал слоев существующей конструкции – легкие бетоны (менее 1200 кг/ м3) – составила при толщине стеновых конструкций равной:
- 300мм – 79мм;
- 600мм – 47мм.
Применение шлакоблоков и шлакобетона в современном строительстве
В последнее время все чаще при строительстве малоэтажных зданий прибегают к легким бетонам, которые превосходят полнотелый кирпич и монолитный бетон по своим теплосберегающим показателям минимум в 1.5 раза, а скорость строительства при применении бетона с различными наполнителями значительно выше. Еще одним плюсом легких бетонов является их стоимость, которая намного ниже стоимости тяжелых бетонов.
Приготовление легкого бетона происходит путем смешивания составляющих: песка, цемента, воды и наполнителей, которые бывают пористые (керамзит, шлак, перлит), легкие органические (полистерол, арболит) и ячеистые (газобетон и пенобетон).
Интересные статьи:
Преимущества керамзитобетонных блоков
Строим дом из газобетона
Пескобетон: состав и применение
Как резать кирпич
Инъецирование трещин в кирпичной кладке
Применение легких бетонов
Наиболее доступными является бетон со шлаковым наполнителем. Как известно, шлаки - это побочный продукт, который образуется при производстве металла и при сжигании каменного угля, а так же антрацита. В зависимости от назначения бетона, прибегают к добавлению шлаков различного происхождения. Так, например, для несущих стен применяют металлургические шлаки, которые увеличивают их прочность, а для внутренних стен используются топливные шлаки, улучшающие теплоизоляцию. Так же для улучшения свойств шлакобетона необходимо достичь оптимального гранулометрического состава, для чего шлак просеивается через специальные сита, сначала крупные, с размером ячеек 40X40мм, а потом мелкие 5X5мм. Соотношение крупных и мелких частиц в бетоне на прямую влияют на его прочностные и тпелоизоляционные характеристики - так при применении крупного шлака, бетон получается легкий с хорошей теплоизоляцией, но менее прочным, а при применении мелкого шлака наоборот - более прочным, но с меньшей теплоизоляцией. Для возведения несущих стен соотношение мелкого шлака к крупному должно составлять не менее 3:7. Так же для увеличения прочности стен добавляется 20% песка от общей массы шлака, а для пластичности- 3- 5% глиняного или известкового теста. В монолитных стенах из шлакобетона при заливке можно создавать пустоты и вводить вкладыши из менее плотных материалов дерево, пенопласт, полиуретан, бумага, которые улучшают теплозащитные свойства стен, сокращают расход бетона, но снижают прочностные их характеристики.
Шлакобетон маркируется цифрами, которые характеризуют его прочность. Так марка 10 рассчитана на нагрузку 10 кг/см2 и изготавливается в следующих пропорциях:
- цемент марки 200 – 1 часть,
- шлак- 15 частей, из которого мелкого-5,крупного-10 и применяется исключительно как утеплитель.
Марка 25, с расчетной нагрузкой 25 кг/см2, имеет следующие пропорции:
- на 1 часть цемента марки 200 приходится 8 частей шлака ( мелкого-3, крупного-5) и применяется для возведения внутренних стен.
Самая прочная марка 50 необходима для несущих стен, которая изготовляется исходя из пропорций:
- 1 часть цемента марки 400 и 8 частей шлака, притом в равных пропорциях крупного и мелкого по 4 части и способна выдерживать нагрузку соответственно 50 кг/см2.
При возведении стен из легких бетонов применяется опалубка, изготовленная из досок, обработанных водоотталкивающими составами и оббитых изнутри металлом, рубероидом или синтетической пленкой. По мере заливки стен бетоном опалубка переставляется выше, и крепится с помощью стальных шпилек с резьбой под гайки длинной 50-70 мм. с каждой стороны или же к неподвижным стойкам, установленным через 1,5 метра вдоль заливаемых бетоном стен. По истечению 3 дней после заливки, бетон набирает прочность, и опалубку снимают или переставляют выше.
Шлакоблоки: технология производства, состав
Для ускорения процесса возведения зданий применяется шлакоблок, который изготавливается из предварительно приготовленного шлакобетонного раствора, путем естественной усадки или вибропрессованием в формах. Разборные формы изготавливаются за ранее из дерева в виде ящиков без дна. Их стенки оббиваются металлом или же пластиком, с целью предотвращения впитывания влаги деревом. Смесь из цемента, шлака и воды загружается в бетоносмеситель и раствор тщательно перемешивается до однородной массы, после чего загружается в формы с пустотообразователями или без них. После загрузки, раствор уплотняется с помощью прижима и вибрации. Стандартный размер шлакоблока регламентирован ГОСТ и составляет 188x199x399мм., однако самостоятельно можно производить блоки любых размеров, зависящие от толщины стен, способов укладки и переноски. Отформованные блоки необходимо выдерживать 2-3 недели, при этом избегать попадания на них прямых солнечных лучей, а при сухой и ветреной погоде периодически обильно их смачивать.
Шлакоблоки могут быть монолитными и пустотными. Монолитный блок изготовлен без полостей. Достоинством таких блоков является повышенная прочность, а из недостатков можно выделить большую массу и плохую теплоизоляцию. К пустотным - относятся блоки с полостями, которые могут варьироваться от 30 до 40 % от общего их объема. В отличие от монолитных, они обладают хорошей теплоизоляцией и малым весом, но применять их для несущих конструкций не рекомендуется, из-за сниженных прочностных характеристик. Так же в шлакоблок, как и шлакобетон можно вводить вкладыши из различных менее плотных материалов. Хорошим заполнителем является опила или древесная стружка, которая значительно облегчает строительный материал и улучшает его теплоизоляцию.
Итак, шлакоблок и шлакобетон это современные облегченные материалы, предназначенные для строительства небольших зданий, с помощью которых возможна относительно высокая скорость возведения стен. Невысокая стоимость, по сравнению с аналогами, делает применение данного материала экономически выгодным. Однако существует ряд недостатков шлакоблока и шлакобетона, к которым можно отнести относительно невысокую прочность (запрещается строительство многоэтажных зданий из данного материала) и плохую морозостойкость. Так же из-за возможной токсичности шлака не рекомендуется применять его при возведении жилых домов, однако шлакобетон и шлакоблок идеально подходит для производственных зданий.
- < Назад
- Вперёд >
zembr.ru
Бетон из граншлака: состав и пропорции
Особенности и области применения
Гранулированный шлак повсеместно применяется в строительных целях. Доменные граншлаки в составе смеси используются в качестве заменителя (иногда частично) песка. Также гранулированный шлак – это эффективный заменитель натуральных материалов из камня, которые используются для ремонта и строительства автомобильных магистралей.
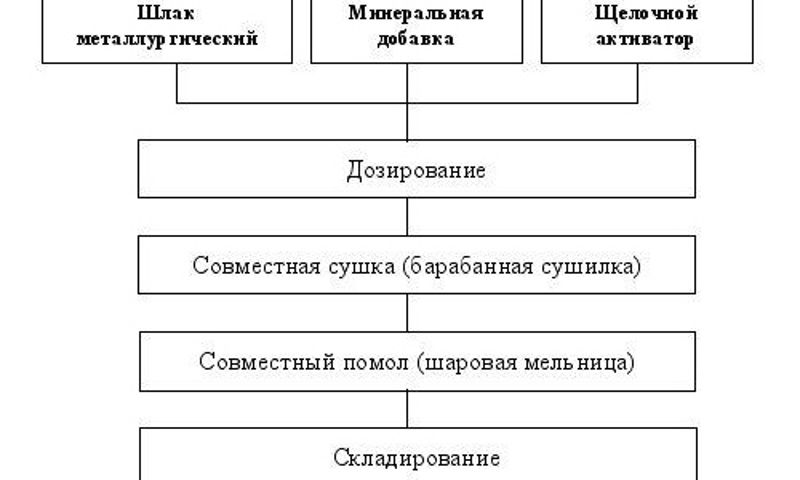
Схема производства бесклинкерных цементов.
Если сравнивать основание из гранитного щебня и из шлака, то второе имеет ряд преимуществ. Благодаря тому что шероховатость поверхности зерен щебня из шлаков больше, он лучше и легче укатывается.
Щебень из доменного шлака повышает качество технологических характеристик бетона, являясь эффективным заполнителем. На 70-80% его прочность выше, чем те же параметры у бетонной смеси с добавлением гранита, что не может не сказываться на качестве готовых изделий.

Схема процесса сухой грануляции доменного шлака.
Мелкозернистый бетон, используемый в армоцементных и железобетонных конструкциях, содержит в своем составе гранулированные шлаки. В целом состав мелкозернистого бетона выглядит следующим образом: в роли вяжущего компонента применяют шлакопортландцемент и бесклинкерные шлаковые вяжущие, дробленый отвальной/литой шлак в качестве заполнителя, вода и ПАВ.
Для достижения полноты химико-физических процессов, которые происходят при тепловлажностной обработке, и высокой удобоукладываемости важно подобрать при выборе сочетания мелкозернистого шлакового бетона необходимое содержание воды.
Количественное соотношение материалов
Ниже представлена таблица, в которой показано, сколько граншлака нужно взять, чтобы приготовить один куб раствора.
Расход каждого компонента зависит от марки смеси, какую вы хотите получить
Марка | Цемент (кг) | Щебень (м3) | Песок (м3) |
100 | 220 | 0,8 | 0,6 |
200 | 280 | 0,8 | 0,5 |
250 | 330 | 0,8 | 0,5 |
300 | 380 | 0,8 | 0,4 |
Количество раствора, необходимого для приготовления и применения на площади конкретных размеров, рассчитывается по следующей формуле: длину нужно умножить на ширину и на глубину обрабатываемой поверхности. Полученная цифра и будет тем количеством, которое вам потребуется для заливки требуемого пространства.
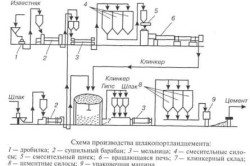
Схема производства шлакопортландцемента.
На качество раствора влияет назначение и ответственность будущей конструкции. Для состава М100 расходуют цемента меньше, чем для М400 (500). В силу того что бетон М400 (500) способен выдерживать большие нагрузки, чем М100, то и соотношение входящих в них материалов будет разным.
Товарный бетон – это М400 (500). Помимо основных составляющих, в них вносят различные добавки (в том числе и морозостойкие). Ниже приведены данные по изготовлению раствора классом М100-450 из цемента М400 (500).
Пропорции бетонной смеси из цемента М400
Марка | Объем раствора из 10 л цемента, в л | Массовый состав (кг) Ц/П/Щ | Массовый состав (л) на 10 л цемента П/Щ |
100 | 78 | 1/ 4,6/ 7 | 41/61 |
150 | 64 | 1/ 3,5/ 5,7 | 32/50 |
200 | 54 | 1/ 2,8/ 4,8 | 25/42 |
250 | 43 | 1/ 2,1/ 3,9 | 19/34 |
300 | 41 | 1/ 1,9/ 3,7 | 17/32 |
400 | 31 | 1/ 1,2/ 2,7 | 11/24 |
450 | 29 | 1/ 1,1/ 2,5 | 10/22 |
Пропорции бетонной смеси из цемента М450
Марка | Объем раствора из 10 л цемента, в л | Массовый состав (кг) Ц/П/Щ | Массовый состав (л) на 10 л цемента П/Щ |
100 | 90 | 1/ 45,8/ 8,1 | 53/71 |
150 | 73 | 1/ 4,6/ 6,6 | 40/58 |
200 | 62 | 1/ 3,5/ 5,6 | 32/49 |
250 | 50 | 1/ 2,6/ 4,5 | 24/39 |
300 | 47 | 1/ 2,4/ 4,3 | 22/37 |
400 | 36 | 1/ 1,6/ 3,2 | 14/28 |
450 | 32 | 1/ 1,4/ 2,9 | 12/25 |
Технология изготовления
(средняя плотность – 1800-2300 кг/м3, прочность – 30-100 МПа)
- оптимизация зернового состава заполнителя;
- подбор рационального состава цементно-шлаковой смеси;
- интенсивное перемешивание цементно-шлаковой смеси в смесителях;
- применение эффективных способов пропаривания (t = 90-100°C) и уплотнения.
Предварительно дробят гранулированный шлак. Способ дробления во многом определяет форму зерен и величину их поверхности. Полученный состав шлакового заполнителя в виде зерен должен по минимуму обеспечивать потребность смеси в воде. При производстве гранулированного шлака нужно использовать смесь дробленого и недробленого гранулированного шлака, обеспечивающую оптимальный состав заполнителя.
Население с давних времен использует для целей строительства шлаки. Легкий и прочный материал шлакобетон получается путем смешения вяжущего и металлургического шлака. Его стоимость в 1,5 раза дешевле полнотелого кирпича, а эффективность теплозащитных свойств примерно во столько же раз выше. При хорошей защищенности от влаги и гидроизолированном фундаменте срок службы стен из данного материала обладает долговечностью и составляет около 50 лет.
o-cemente.info
Пропорции раствора для шлакоблока: цемент, шлак, песок и вода, технология изготовления
Пропорции компонентов раствора для изготовления шлакоблока
При возведении небольших зданий, хозяйственных пристроек, гаражей используются недорогие стройматериалы. Для стен оптимальным вариантом является шлакоблок. Это настолько дешевый и простой в производстве искусственный камень, что его вполне можно изготовить своими руками. Главное – соблюсти верные пропорции раствора.
Особенности и область применения
Шлакоблок представляет собой искусственный камень, который состоит из смеси воды, цемента и наполнителя. В качестве последнего используется шлак – измельченные отходы, образовавшиеся в результате:
- производства металла в доменных, мартеновских печах;
- некоторых химических процессов;
- сжигания разных видов твердого топлива (каменный уголь, торф, горючие сланцы и другие).
Шлакобетон относится к легким видам бетонов плотностью до 1800 кг/м 3. так как гранулированный шлак отличается уровнем пустотности – до 60 %. Однако при этом обладает высокой степенью тепло- и звукоизоляции, относительно небольшим весом и, в отличие от газо- и пенобетона, достаточной прочностью для удерживания любых метизов в теле.
В заводских условиях пропорции раствора соблюдаются очень точно, ведь от этого зависит качество шлакоблока. Готовая смесь заливается в формы и отправляется на вибропрессование, реже – автоклавирование (пропаривание и прессовка). Благодаря данной технологии срок производства сокращается до нескольких дней. Стандартные габариты: 39х19х18,8 см.
Если шлакоблок изготавливается своими руками, то акцент делается на правильную рецептуру и естественные условия вызревания так называемых цементных минералов:
- Срок сушки – не менее 28 дней.
- Влажность – минимум 60 %.
- Температура – от +15 до +25 °С.
Нередко для шлакоблока, изготовленного самостоятельно, используются дешевые и доступные для конкретного региона заменители шлака: гранитный щебень, отсев, кирпичный бой, бетонный скол и многое другое. Несмотря на разную рецептуру, полученные изделия условно называют одним и тем же термином – «шлакобетонные блоки».
Сферы применения: при возведении складских зданий, времянок, гаражей, помещений хозяйственного назначения (сарай, котельная), подвалов, беседок и тому подобное. Материал отличается высоким уровнем гигроскопичности, поэтому строение нуждается в полноценной гидроизоляции.
Раствор для производства шлакоблока готовится из следующих составляющих:
1. цемент марки не ниже М350. Иначе изделие получится недостаточно прочным и быстро начнет разрушаться;
3. песок либо отсев – применяется для увеличения плотности шлакоблока;
4. пластификаторы (УПД) или модифицирующие добавки – улучшают некоторые свойства бетона либо ускоряют процессы цементации. Смешиваются с водой в пропорции, указанной в инструкции;
5. вода техническая.
Рецептура шлакобетона различается в зависимости от состава и размера зерен шлака и силиката. Раствор в усредненном варианте «цемент-шлак-вода» имеет соотношение 1:7:0,7. Более точные пропорции приведены в таблице ниже.
Процесс изготовления включает три этапа:
1. Замес раствора в бетоносмесителе.
2. Загрузка в форму, вибропрессование.
3. Выгрузка готовых, но еще сырых изделий, штабелирование на 1-3 недели для просушки.
Как делать шлакоблок в домашних условиях? Практически так же, с той разницей, что вместо бетоносмесителя можно воспользоваться обычной лопатой, а уплотнение производится ручным способом.
Виброустановка, удаляющая пузырьки воздуха и уплотняющая раствор, не обязательна, хотя многие умельцы собирают агрегат самостоятельно из запчастей для автомобилей. Но для получения блоков приемлемого качества нужно оставить их в форме не менее, чем на 24 часа, периодически смачивать и переворачивать. После выгрузки нужно разложить на поддоне и через 4-5 суток можно штабелировать для окончательной просушки в течение 25-30 дней.
http://hardstones.ru
legkoe-delo.ru
Тайны производства шлакобетона
Не всякий шлак берут в производство шлакобетона – только антрацитовый от топливной и шлаки от металлургической промышленности. Но еще сортируют его согласно «габаритам» шлаковых зерен, по-разному их называя. Например, 5-40 мм зерна именуют щебнем, а до 5-мм – песком. Шлаковый песок дает бетон плотный и прочный, а щебень – облегченный с хорошими свойствами теплоизоляции, но с прочностью меньшей.
Приготовление шлакобетона начинается, понятно, с приготовления определенной фракции зерен шлака, для чего необходимы два сита, имеющие ячейки 40х40 и 5х5 мм. «Рецепты» же следующие:
1. Изготовление стен наружных – требуется крупного щлака – 7 частей, а мелкого – 3.2. Стены внутренние – шлак крупный – 6 частей, мелкий – 4.3. Секрет прочности: 1/5 самой мелкой шлаковой фракции заменяем песком обычным, а крупные зерна их смеси исключаем.
Стоимость сооружаемых шлакобетонных строений можно снизить, применив следующие сочетания вяжущих компонентов – цемента с глиной либо известью. Цемент здесь от объема вяжущего должен составить 2/3, известь же – не более 1/3, таковы правильные пропорции. Помимо удешевления, с помощью глины можно добиваться более теплых и сухих стен. А известковый шлакобетон. У которого вяжущее из извести с глиной – соотношения тут 1/3, соответственно, и 2/3 Шлакобетон будет твердеть дольше бетона обычного – зато прочность потом превысит его. Кстати. Повысить теплопроводность можно путем добавления в вяжущее вещество гипса.
Без извести шлакобетон тоже неплох, только вот пластичности серьезно поубавится, от чего однородной массы путем перемешивания достичь невозможно в принципе, а качество перемешивания, как знаем, бетонной смеси придает более повышенные характеристики.Самостоятельное приготовление качественного шлакобетона возможно, но тут качество гарантируете вы сами, последовательность же аналогична заводской:
- Песок с цементом загодя увлажненный шлак смешивают.
- Добавляют пластификатор – глиняное тесто либо известковое.
- Заливают все водой, а потом мешают.
Шлакобетонные стены выстаиваются не меньше 3 месяцев – только потом за монтаж перекрытий можно браться. Соответственно. строительство стен начинают, когда нчинается лето (ли весной, когда грунт оттает и от снегов просохнет), иначе до морозов стройку не завершить.
Учитывая то, что в настоящее время на рынке присутствует большое количество производителей технической химии, советуем Вам правильно отнестись к выбору производителя.
10x15.by