Технология приготовления бетонной смеси. Приготовление бетонной смеси
Технология приготовления бетонной смеси
Технологический процесс бетонирования конструкций включает приготовление бетонной смеси и транспортирования ее на строящийся объект, подачу, распределение, укладку и уплотнение ее в конструкции, уход за бетоном в процессе твердения.
Бетонную смесь нельзя заготовить заранее и перевозить на большие расстояния. После приготовления она должна быть доставлена и уложена в блоки сооружения до начала схватывания (обычно 1–3 ч). Поэтому бетонную смесь необходимо приготавливать вблизи мест ее укладки так, чтобы время нахождения ее в пути в летнее время не превышало 1 ч.
Бетонную смесь приготовляют на механизированном или автоматизированном бетонном заводе, в готовом виде доставляют на объект строительства или приготавливают на приобъектных инвентарных (передвижных) бетоносмесительных установках.
Приготовление бетонной смеси включает: прием и складирование составляющих материалов (цемента, заполнителей), взвешивание (дозирование) и перемешивание их с водой, выдачу готовой бетонной смеси на транспортные средства. В зимних условиях в данный технологический процесс включают дополнительные операции.
Бетонную смесь приготавливают по законченной или расчлененной технологии:
– при законченной технологии получают готовую бетонную смесь;
– при расчлененной технологии получают отдозированные составляющие или сухую бетонную смесь, представляющую собой смесь вяжущего, заполнителей, добавок, пигментов, отдозированных и перемешанных на заводе, и затворяемых водой перед употреблением. Точное дозирование компонентов позволяет получать более высокие технические характеристики готовой продукции по сравнению со смесями, приготовляемыми на строительной площадке. Важным достоинством сухих смесей является возможность добавления в них химических добавок и микронаполнителей как улучшающих их структуру, так и подготовленных для применения в холодное время года.
Основными техническими средствами для выпуска бетонной смеси являются расходные бункера с распределительными устройствами, дозаторы, бетоносмесители, системы внутренних транспортных средств и коммуникаций, раздаточный бункер.
Технологическое оборудование стационарного типа для приготовления бетонной смеси может быть решено по одноступенчатой и двухступенчатой схемам (рис. 2.17).
Одноступенчатая (вертикальная) схема (рис. 2.17, а) характеризуется тем, что составляющие материалы бетонной смеси (вяжущие, заполнители, вода) поднимаются в верхнюю точку технологического процесса один раз и далее перемещаются вниз под действием собственной силы тяжести по ходу технологического процесса. Достоинства: компактны, экономичны, а недостатки – сложность монтажа (из-за значительной высоты, до 35 м).
При двухступенчатой (партерной) схеме (рис. 2.17, б) подъем составляющих материалов бетонной смеси происходит дважды: составляющие бетонной смеси сначала поднимают в расходные бункера, затем они опускаются самотеком, проходя через собственные дозаторы, попадают в общую приемную воронку и снова поднимаются вверх для загрузки в бетоносмеситель. Достоинством данной схемы является меньшая стоимость монтажа, а недостатком – большая площадь застройки.
![]() |
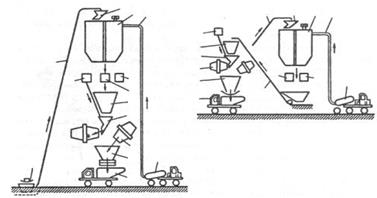
Рис. 2.17. Схемы компоновки бетоносмесительных заводов и установок:
а – одноступенчатая; б – двухступенчатая; 1 – конвейер склада заполнителей в
расходные бункера; 3, 9, 10 – поворотная направляющая и распределительная;
4 – расходные бункера; 5 – трубопровод подачи цемента; 6, 7, 8 – дозаторы
соответственно цемента, заполнителей и воды; 11 – бетоносмесители;
12 – раздаточный бункер; 13 – автобетоновоз; 14 – автоцементовоз;
2, 15 – скиповый подъемник
При потребности в бетонной смеси не более 20 м3/ч обычно применяют передвижные мобильные бетономешалки со смесителями гравитационного типа.
Конструкция бетоносмесительных установок позволяет переводить из рабочего в транспортное положение в течение одной рабочей смены и транспортировать их на прицепе на очередной объект. Использование таких установок целесообразно на крупных рассредоточенных объектах, расположенных от стационарных бетонных заводов на расстояниях, превышающих технологически допустимые.
В качестве оборудования для приготовления обычной бетонной смеси применяют смесители цикличного и непрерывного действия.
Бетоносмесители цикличного действия различаются по объему готовой смеси, выдаваемой за один замес.
Производительность цикличного бетоносмесителя
, (2.82)
где q – объем готовой бетонной смеси за один замес, л;
n – число замесов в один час;
kв – коэффициент использования бетоносмесителя по времени
(0,85–0,93).
Загрузку бетоносмесителя цикличного действия производят в следующей последовательности. Сначала в смеситель подают 20–30 % требуемого на замес количества воды, затем одновременно начинают загружать цемент и заполнители, не прекращая подачи воды до необходимого количества. Цемент поступает в смеситель между порциями заполнителя, благодаря чему устраняется его распыление. Продолжительность перемешивания бетонной смеси зависит от вместимости барабана смесителя и необходимой подвижности бетонной смеси и составляет от 45 до 240 с.
Бетоносмесители непрерывного действия выпускаются производительностью 5, 15, 30 и 60 м3/ч, а машины гравитационного типа с барабанным смесителем – производительностью 120 м3/ч. Продолжительность перемешивания в этих бетоносмесителях указывают в паспортах машин.
При приготовлении бетонной смеси по раздельной технологии необходимо соблюдать следующий порядок: в смеситель дозируется вода, часть песка, тонкомолотый минеральный наполнитель (в случае его применения) и цемент. Все эти составляющие тщательно перемешиваются, полученную смесь подают в бетоносмеситель, предварительно загруженный оставшейся частью песка и воды, крупным заполнителем, и еще раз вся эта смесь перемешивается.
Для получения бетона высокого качества необходимо применять высококачественные материалы, также бетонная смесь должна обладать определенными свойствами, соответствующими выбранной технологии. Одним из этих свойств является удобоукладываемость – способность ее заполнять форму с наименьшими затратами труда и энергии, обеспечивая при этом максимальную плотность, прочность и долговечность бетона. Она зависит от зернового состава смеси, количества воды, степени армирования, способов транспортирования и уплотнения смеси. Кроме того, бетонная смесь должна сохранять однородность (при транспортировании, перегрузке и укладке в опалубку), которая обеспечивается связностью (нерасслаиваемостью) и водоудерживающей способностью. Все это достигается правильным подбором состава смеси, точностью дозировки составляющих и тщательным перемешиванием всех компонентов.
Читайте также:
lektsia.com
37 Приготовление и транспортирование бетонной смеси
37 Приготовление и транспортирование бетонной смеси.
Приготовление бетонной смеси
Дозированные по объёму или массе компоненты бетона перемешивают. Это один из важнейших этапов приготовления бетонной смеси, когда составляющие в процессе перемешивания необходимо превратить в однородную гомогенную массу.
Недостаточно тщательное перемешивание — одна из причин недобора бетоном требуемой прочности. Следствием неравномерного перемешивания может явиться снижение прочности бетона, а также ухудшение других его свойств.
Наиболее частой ошибкой при приготовлении бетонной смеси вручную является добавление воды без перемешивания сухой смеси. В этом случае нельзя обеспечить гомогенность смеси.
Для первого мокрого перемешивания треть необходимого количества воды заливается в сухую смесь, оставшаяся вода добавляется при втором мокром перемешивании.
Для каждой бетономешалки существует оптимальное время перемешивания, то истечение которого получают гомогенную бетонную смесь. Недопустимо не только сокращение времени перемешивания, но и увеличение его сверх необходимого, т.к. при длительном перемешивании смесь расслаивается, т.е. хорошо перемешанные частицы вновь распадаются и бетонная смесь делится на составляющие. Оптимальное время перемешивания 2–3 мин (в зависимости от объёма и типа бетономешалки).
При приготовлении бетонной смеси холодное время года частой ошибкой является неправильный порядок загрузки компонентов. Используя для затворения нагретую до 60–70°C воду, следует смешивать её с незамороженным щебнем. Температура смеси при этом составит 20–22°C; в неё можно будет подмешивать цемент.
При приготовлении бетонной смеси необходимо принимать меры, обеспечивающие сохранение требуемой консистенции к моменту ее укладки в опалубку. Это может быть достигнуто за счет увеличения расхода воды, что, однако, связано с увеличением расхода цемента.
Консервация консистенции бетонной смеси может быть достигнута и путем введения в бетонную смеси при ее приготовлении поверхностно-активных добавок (0,4...0,5% массы цемента). Они не только уменьшают обезвоживание смеси, но и пластифицируют ее, снижая водопотребность.
Транспортирование бетонной смеси
Приготовленную бетонную смесь доставляют к месту укладки на носилках или тачках. Неправильно выбранное средство транспортировки может снизить качество бетонной смеси, поскольку от тряски она расслаивается. Применять такой бетон опасно, т.к. дефекты в конструкциях могут проявиться неожиданно через некоторый промежуток времени.
Нередко для подачи бетонной смеси применяют транспортёры. Если подавать транспортёром пластичную смесь, то теряя часть воды она будет расслаиваться, утрачивая свои свойства. Бетонную смесь нельзя сбрасывать с высоты более 1,5 м. Расслаивание можно предотвратить, устроив у выгрузочного конца транспортёра приёмный бункер и отводную трубу; обычного фартука здесь недостаточно.
При транспортировке бетонных смесей в условиях сухого жаркого климата кузова бетоновозов или автобетоносмесителей должны иметь термоизоляцию. Однако и в этом случае во избежание интенсивного обезвоживания дальность перевозки не должна превышать 10..15 км.
В условиях сухого жаркого климата должно быть примерно в 1,5 раза увеличено время перемешивания смеси, обеспечена перевозка в закрытой таре, ограничено время перевозки и сведены к минимуму перегрузки.
studfiles.net
Приготовление и укладка бетонной смеси
Особенности приготовления
Наполнители
Существуют различные способы, используемые для изготовления растворов, отличные по соотношению компонентов, марок цемента, добавок и фракций наполнителя.
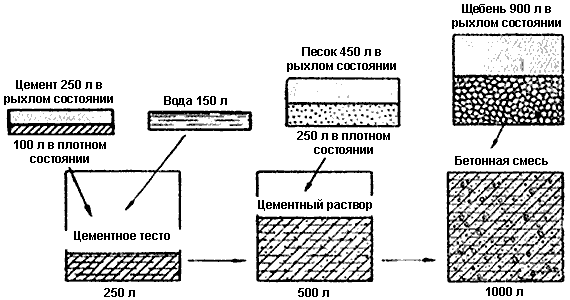
Приготовление смеси: схема.
В состав смеси входят следующие элементы:
- Вода.
- Цемент.
- Наполнитель.
Цемент является гидравлическим вяжущим веществом, которое по истечении определенного срока становится нерастворимым в водной среде материалом в результате перемешивания с водой, твердения его под водой или на воздухе.
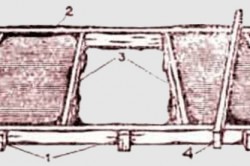
Схема укладки: 1 — колышки; 2 — доски опалубки 50×150 мм; 3 — разделительные доски 25 х 150 мм; 4 — рейка для разравнивания.
Наполнителем являются песок и щебень, имеющие различные фракции. Уложенной в форму смеси придается соответствующая форма в процессе твердения. Возможен замес бетонного раствора вручную. Зачастую для создания специальных форм смесь изготавливают в заводских условиях, но можно воспользоваться и бетономешалкой. Раствор, изготовленный на заводе, имеет высокие показатели качества, чего нельзя сказать о смеси, приготовленной самостоятельно. Отсюда можно сделать вывод, что соблюдение технологии изготовления смеси при строительстве индивидуальных домов отсутствует.
Качество готовой смеси зависит от правильного хранения заполнителей, которые не должны загрязняться, что может повлиять на прочность. Следует помнить, что если наполнитель не имеет двойную прочность, то и бетон необходимой прочности из него изготовить нельзя. Поэтому любые засорения, например, глинистый грунт, будут оказывать отрицательное влияние на показатели прочности. Укладка, который загрязнен органическими веществами, такими как битый кирпич, стружка, лед или снег, способна привести к образованию коррозии арматурного каркаса.
Фактор загрязненности может оказывать влияние не только на прочность, но и на следующие качества:
- Теплоизоляция.
- Морозостойкость.
- Износостойкость.
- Водонепроницаемость.
Чтобы в заполнитель не попали засоряющие вещества, перед началом работ площадку для складирования следует вычистить и выровнять. Ее необходимо размещать так, чтобы дождевая вода могла свободно стекать из-под слоя гравия.
Согласно техническим требованиям, содержание засоряющих веществ в виде глинистых частиц должно составлять до 3% от всего объема заполнителя. Прочность будет снижена на 50%, если наличие примесей глины будет составлять 16%. При содержании глинистых веществ в составе 6% от объема заполнителя качество снизится на 10%.
Проверить уровень содержания глины в заполнителе доступно любому. Для этого необходима литровая стеклянная банка, заполненная песчаным гравием. Ее на ? объема требуется заполнить водой. Затем банку необходимо интенсивно взбалтывать в течение часа. После этого на поверхности должен образоваться слой, включающий илистые и глинистые частицы. Для определения процента содержания засоряющих веществ измеряют толщину полученного слоя загрязнений, затем соотносят ее с общим объемом гравия в банке. Способов очистки заполнителей существует несколько. Одним из них является промывка.
Вяжущие вещества

Схема укладки дорожки: 1 — Грунт, 2 — Выравнивающий слой, 3 — Опалубка, 4 — Бетон.
Цемент представляет собой важный компонент смеси. Он применяется в качестве вяжущего вещества. Чтобы бетон получился качественным, при его изготовлении соблюдают все необходимые инструкции, а также рецепты приготовления смеси, изложенные в справочной литературе.
Ошибочно полагать, что добавление цемента в раствор позволит увеличить его прочность. Вместо желаемого результата можно получить отрицательный, то есть снижение прочности. Цементное тесто должно быть приготовлено в достаточном количестве. Тогда будет обеспечена необходимая максимальная прочность.
Свободно плавающий в цементном тесте заполнитель способен нарушить структуру арматурного каркаса, который обеспечивает несущую способность. Впоследствии бетон подвергается чрезмерной усадке и появлению большого числа трещин. Вместе с тем на использовании вяжущего вещества экономить не следует, поскольку оно не будет обволакивать частицы заполнителя полностью, при этом они будут соединяться друг с другом, а не с цементом. Такой раствор не является водонепроницаемым, поэтому каркас в нем теряет защиту от коррозии. В результате вся железобетонная конструкция может быть разрушена.
Использование залежалого цемента является большой ошибкой. Такой цемент становится комковатым, поэтому продается по низким ценам. Расходы в данном случае на устранение образованных дефектов превзойдут все вложенные средства.
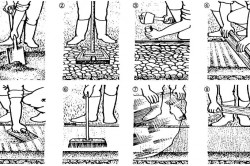
Схема укладки дорожки из декоративного бетона.
Качество цемента снижается не только по причине его залежалости, но и в результате отсутствия необходимых условий для хранения вяжущего вещества. Помещение для складирования должно быть сухим, защищенным от ветра и излишней влажности воздуха. Для укладки мешков с цементом используют настил из дерева, отстоящий от пола более чем на 30 сантиметров. Цемент нельзя хранить больше трех месяцев даже при сухой погоде.
Чтобы перекрыть поступление влажного воздуха, цемент укрывают настилом из брезента. Насыщение цемента воздухом может привести к гидратации или схватыванию, образованию комков. Поэтому всегда перед тем, как начать замешивать цемент, следует убедиться, что он новый, то есть с момента его изготовления не должно пройти 90 суток. Если мешок с цементом открыт, то его хранят не более одной недели при сухой погоде, а при сырой – не больше суток. Норма подачи цемента в бетономешалку равна объему, необходимому на один день строительства.
Вода и добавки
Смесь должна включать воду и содержать необходимые добавки.
Без этого химический процесс схватывания происходить не будет. Чтобы смесь могла твердеть качественно, поверхность следует увлажнить. Без этого смесь не сможет достичь полной прочности – только частичной.
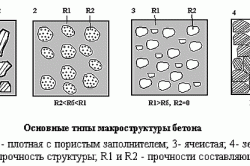
Схема макроструктур.
Воду необходимо использовать только чистую, например, питьевая вода из водопровода может применяться без проведения дополнительных исследований. Воду, поступающую не из водопровода, подвергают лабораторным исследованиям в обязательном порядке. Если питьевая вода содержит примесь солей, являясь при этом термальной, минеральной или лечебной, то ее не применяют для изготовления.
Если состав воды неизвестен, то ее использование может привести к серьезным последствиям. Например, наличие в воде растворенных сульфатов способно разрушить бетон, а наличие серной кислоты в воде представляет наибольшую опасность для изготовления.
Добавки к смеси способствуют улучшению некоторых полезных свойств. Для применения добавок в условиях индивидуального строительства необходимо иметь профессиональные навыки. Чаще всего в таких условиях применяются добавки, позволяющие ускорить процесс твердения и схватывания. Одним из активных компонентов, входящих в состав добавок, является хлористый кальций, используемый в качестве противоморозной добавки и ускорителя твердения.
Применение добавок в больших количествах, приводящее к их передозировке, может стать причиной возникновения электрохимической коррозии. Поэтому наряду с катализаторами, то есть ускорителями процесса твердения и других реакций, в раствор с добавками необходимо включать ингибиторы – вещества, способствующие замедлению реакций. Тогда наличие противоморозных добавок не приведет к образованию коррозии. Иначе все дефекты, вызванные отсутствием ингибитора в растворе, невозможно будет устранить.
Приготовление и заливка
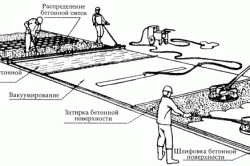
Схема заливки и затирки смеси.
Бетонная смесь готовится из дозированных по массе или объему необходимых компонентов, которые перемешивают между собой вручную или в бетономешалке. В итоге получается однородная гомогенная масса. Поскольку в сухом материале, используемом для приготовления раствора, содержится достаточный объем воздуха, который начинает вытесняться при перемешивании, то его место заполняется более мелкими частицами заполнителя и цемента, имеющими вид пленки. При этом происходит процесс гидратации или схватывания.
Если наблюдается недобор расчетной мощности раствором, то это является результатом недостаточного перемешивания, которое производилось неравномерно. Это стало причиной ухудшения свойств. Поэтому раствор должен быть не только хорошо перемешан, но и качественно уложен. Способ укладки должен обеспечивать монолитность бетона и его однородность, качественное сцепление с закладными деталями и арматурой.
Перед укладкой устанавливают опалубку и проверяют ее техническое состояние. После этого укладывают арматурный каркас в опалубке, производя его вязку с помощью вязальной проволоки и крючка своими руками. Если в опалубке есть щели, то их следует законопатить. Борта опалубки и ее основание требуется обильно смочить водой.
Бетонная смесь должна укладываться в опалубку с высоты не более 2 метров. Слои укладывают горизонтально высотой не более 50 см. Следует соблюдать при укладке одинаковое направление и одну и ту же высоту. Необходимо соблюдать и процесс непрерывной укладки. Каждый последующий слой нужно укладывать до того, как начнет схватываться предыдущий.
o-cemente.info
Технология приготовления бетонной смеси
В настоящее время самым распространенным материалом для возведения фундаментов жилых домов и всякого рода надворных построек является бетон. Все чаще товарный бетон стали заказывать в организациях, его производящих, но если требуется его относительно немного − например, для заливки столбчатых фундаментов − можно приготовить бетонную смесь непосредственно на строительной площадке. Единственное условие в этом случае — необходимость соблюдать технологию и учитывать пропорции при смешивании исходных компонентов, а именно цемента, щебня, песка и воды. Рассмотрим коротко, какими свойствами должны обладать исходные материалы.
Свойства материалов для изготовления бетонной смеси.
Песок, используемый в строительстве, если не вдаваться в подробности, подразделяется на речной и карьерный. Карьерный песок наиболее распространен в природе, потому находит более широкое применение. Он дешевле речного, но обладает большим количеством примесей - глины, пыли и различных частиц осадочных пород. В речном песке, который добывается из русла рек, посторонних включений гораздо меньше. Поэтому, для приготовления бетонной смеси он наиболее пригоден. Возможно применение и карьерного песка, но предварительно промытого и просеянного. Не старайтесь выбирать слишком мелкий песок. Для приготовления бетонной смеси используют песок фракции 1,2 ÷ 3,5 мм.
Щебень, применяемый для самостоятельного изготовления бетонной смеси, желательно брать фракцией 1 ÷ 2 см. Компоненты, с такой фракцией щебня, намного легче перемешиваются, а при укладке с большей вероятностью заполнит воздушные полости возводимой конструкции. Возрастет плотность укладки, а в результате прочность и долговечность всего сооружения. При работе следует следить за отсутствием мусора в щебне и других посторонних включений.
Вода также должна быть относительно чистой, без масляных разводов, не заиленной и плавающего мусора. В жаркую погоду смесь можно затворять холодной водой, для замедления процесса гидратации, а осенью или весной, при температуре окружающего воздуха, близкой к нулевой, воду, при изготовлении бетонной смеси, необходимо подогревать.
<p
Цемент для приготовления бетонной смеси должен обладать рядом свойств, в зависимости от условий эксплуатации возведенных из него бетонных конструкций. При этом расход цемента зависит от его марки, величины наполнителя и водоцементного (В/Ц) отношения. Для частного строительства применяется, как правило, самый распространенный портландцемент марки 400 (М400), но в некоторых случаях можно использовать и шлакопортландцемент, исключая устройство фундаментов, так как он отличается пониженной морозостойкостью. В зависимости от использования той или иной марки цемента, получают различные марки бетонной смеси. Так, например, используя цемент марки М400, при соблюдении технологии изготовления, получают бетон марки М250.
Технология приготовления бетонной смеси.
Как уже было сказано выше — бетонная смесь включает в себя четыре основных компонента: песок, цемент, вода и щебень. для получения качественной бетонной смеси, все эти компоненты должны находятся в строго определенных пропорциях, при нарушении которых снижается прочность бетона и, как следствие, долговечность конструкции и сооружения в целом. Вариантов состава бетонной смеси может быть достаточно много. При изготовлении бетонной смеси непосредственно на строительной площадке чаще всего используется следующее долевое соотношение компонентов: цемент составляет 1 часть, вода составляет 1/2 части, щебень составляет 4 части и песок − 2 части. Но, здесь следует отметить, что это, конечно же, приблизительные пропорции для получения бетона заявленной марки. Необходимо также учитывать и марку цемента, который применяется при изготовлении бетонной смеси (для получения бетона М250, используется цемент не ниже М400), свойства песка и щебня, а также применение каких-либо добавок. Важную роль играет соотношение воды и цемента, которые являются главными компонентами бетона. Они отвечают за связь всех компонентов и образование единой монолитной смеси - цементного камня. Водоцементное (В/Ц) отношение также сильно влияет на морозостойкость получаемого бетона а, учитывая суровые зимы на большей части территории нашей страны, желательно, чтобы В/Ц было не более 0,5.
Перемешивать компоненты при изготовлении бетонной смеси желательно в бетономешалке малой емкости. В индивидуальном строительстве для этого, как правило, используют бытовые бетоносмесители гравитационного действия объемом до 300 л. Они выпускаются нашей промышленностью в достаточном ассортименте. Но можно приспособить для этих целей и обычное корыто с относительно высокими бортами, чтобы бетонная смесь при перемешивании не выплескивалась через край. Для облегчения процесса перемешивания, в первую очередь перемешайте цемент с песком, затем добавьте воду и в последнюю очередь крупный заполнитель. Перемешивать необходимо до получения однородной массы.
Еще почитать:
Применение и приготовление строительных растворов.
stroiazbuka.ru
Приготовление бетонной смеси
Подготовка объектов бетонирования
До начала бетонирования необходимо проверить правильность установки арматуры и закладных частей, наличие бетонных подкладок для соблюдения защитного слоя. Если арматура, анкерные болты, опорные плиты и т. п. были установлены задолго до укладки бетонной смеси и коррозировали, они должны быть очищены от ржавчины, которая снижает сцепление бетона с металлом и отрицательно влияет на качество конструкции. Качество и положение арматуры и закладных частей фиксируется актом.
Работы по бетонированию массивных конструкций должны быть организованы на основе типовых технологических карт, составленных с учетом опыта передовых строек и в каждом отдельном случае уточненных и привязанных к местным условиям строительства данного объекта.
Технологические карты, разработанные по определенной методике, содержат в своем составе следующие разделы: область применения; основные указания по выполнению комплексного процесса бетонирования; суточный график выполнения работ; схема организации работ; потребность в материально-технических ресурсах; технико-экономические показатели. К технологической карте должна быть приложена производственная калькуляция трудовых затрат, которая служит для составления наряда на производство работ.
Приготовление бетонной смеси
Бетонная смесь должна обладать свойствами, обеспечивающими заданную прочность бетона. Бетонная смесь должна удовлетворять следующим требованиям: сохранять при транспортировании, перегрузке и укладке в опалубку свою однородность, достигнутую при перемешивании; обладать соответствующей консистенцией, способностью хорошо формоваться и уплотняться; обладать удобоукладываемостью для быстрого и плотного заполнения опалубки, всех промежутков между арматурными стержнями.
Различают подвижные (пластичные) смеси, способные укладываться в опалубку и уплотняться под действием собственного веса, и жесткие, требующие для своего уплотнения приложение внешних сил (вибрирование, виброштампование, вибропрокат). Жесткие смеси содержат ограниченное количество воды; смесь при этом отличается большой насыщенностью крупного заполнителя (щебнем или гравием). Применение жестких бетонных смесей способствует повышению прочности бетона, более экономному расходованию цемента и ускорению оборачиваемости опалубки. В процессе приготовления жестких смесей требуется точная дозировка воды, так как даже незначительные отклонения содержание ее в смеси резко изменяют ее свойства.
При осуществлении бетонных и железобетонных работ широкие применение нашли малоподвижные смеси, которые по структуре и повышенному содержанию цементного теста приближаются к пластичным смесям, а из-за уменьшенного содержания воды обладают положительными свойствами жесткой бетонной смеси.
Степень подвижности пластичных бетонных смесей оценивают при помощи стандартного конуса, в который укладывают бетонную смесь. После снятия формы бетон под собственным весом оседает; величина осадки в мм характеризует подвижность бетонной смеси.
Бетонная смесь, как правило, приготовляется на бетонных заводах и доставляется на строительство специализированными автомашинами. В необходимых случаях приготовление бетона может быть организовано в бетонорастворных узлах непосредственно на строительной площадке. Бетонные заводы или бетонные узлы на строительной площадке состоят из складов цемента, песка и гравия (или щебня), дозировочных устройств, бетоносмесительных машин и бункеров для готового бетона. Бетонные заводы и установки оборудуются водоснабжением и средствами автоматизации производства и механизации подъемно-транспортных работ.
Дозирование составляющих материалов при приготовлении бетонной смеси механизированным способом производится по весу.
Дозирование воды не по весу, а по объему допускается только на бетонных заводах непрерывного действия.
Бетонная смесь, доставляемая к месту укладки, должна быть однородной и удобоукладываемой. Расслоившуюся при перевозке бетонную смесь, потерявшую прочность перед укладкой, необходимо вновь хорошо перемешать до полного восстановления однородности.
Укладка бетонной смеси производится слоями с тщательным их уплотнением, от качества уплотнения зависят плотность, прочность и долговечность бетона. Для уплотнения бетона применяются электромеханические, электромагнитные и пневматические вибраторы.
Уплотнение бетона и ускорение его твердения возможно при помощи вакуумирования, то есть искусственное удаление лишней влаги, которая замедляет процесс схватывания и не позволяет достичь более полного уплотнения.
Зимой же укладку бетонной смеси следует производить после отогрева промороженного основания. Допускается укладывать смесь на не отогретое не пучинистое основание или старый бетон при выдержании бетона в конструкции способом термоса, при предварительном разогреве бетонной смеси, а также при применении бетона с противоморозными добавками.
Похожие статьи:
poznayka.org
Приготовление бетонной смеси
Строительные машины и оборудование, справочник

Категория:
Технология и организация железобетонных конструкций

Завод применяет быстротвердеющее портландцемент марки БТЦ и 500, поставляемый Николаевским цементным заводом. Этот цемент является эффективным для производства железобетонных изделий без тепловой обработки или с сокращенным циклом про-паривания. О высоком качестве цемента этих марок свидетельствует график зависимости прочности бетона от Ц1В (рис. 20). Для этого цемента характерно интенсивное нарастание прочности в возрасте 1 — 3 суток благодаря содержанию СзА и C3S в сумме не менее 60-65% (из них C3S в пределах 50-60% и С3А — 8-12 %), повышенной добавке гипса и тонкому помолу цемента (удельная поверхность по Това-Рову 4000-5000 см21г).
Завод получает с Академического карьера Калининской области гранитный гравий с объемным весом 1,5 -1,6 т/м3 и удельным весом 2,6 г/см3.
Загрязненность илисто-глинистыми примесями составляет 0,5- 1,5%, водопоглощаемость 1,1 — 1,3%. Гравий выдерживает 25-кратное замораживание.
Щебень гранитный завод получает также с Академического карьера. Объемный вес щебня 1,4-1,5 т/м3 и удельный вес 2,6 г/см3. Загрязненность глинистыми примесями от 1 до 2%, водопоглощаемость 1,1-1,3%; щебень выдерживает 25-кратное замораживание.
Песок завод получает из Тучковского карьера. Объемный вес песка при естественной влажности 1,2-1,3 т/м3 и удельный вес 2,6 г/см3.
Загрязненность песка илисто-глинистыми примесями составляет от 1 до 3%.
Рис. 1. График зависимости прочности бетона от ЩВ 1 — БТЦ; 2 — цемент марки 500 Николаевского завода; 3 — пластифицированный цемент марки 500 Белгородского завода
Гранулометрический состав песка приведен ниже.
Стоимость 1 м3 заполнителей, получаемых заводом (франко-за-вод): песка — 2 р. 39 к.; щебня — 5 р. 85 к. и гравия — 4 р. 53 к.
Исходными данными при подборе состава бетона являются:– марка цемента по предварительному паспорту;– отпускная прочность бетона в конструкции или изделии и проектная марка бетона;– условия твердения бетона; требуемая подвижность или удобоукладываемость бетонной смеси;– наибольшая крупность зерен гравия или щебня;– условная водопоглощаемость крупного заполнителя; – объемный вес крупного заполнителя; удельный вес и модуль крупности песка.
Оптимальный режим пропаривания изделий выбирается исходя из условия обеспечения 70% прочности бетона от проектной в течение наименьшего срока пропаривания с соблюдением установленных производственных норм расхода цемента.
При подборе состава бетона учитывается, что не вся вода, вводимая в замес, участвует в образовании цементного камня, так как часть воды поглощается крупным заполнителем и поэтому при определении В/Ц, а также абсолютного объема бетона она исключи ется из общего количества воды, вводимой в замес. Для упрощения количество воды, которое поглощается щебнем или гравием в 1 мъ бетона, принимается равным 1,15 л/м3 на каждую 0,1% условной водопоглощаемости.
После определения расходов материалов на 1 м3 бетона рассчи гывают их количество на пробный замес. При пробном замесе корректируют окончательный расход воды на 1 м3 бетона, который соответствует заданной подвижности бетонной смеси. Воду добавляют порциями по 2-3% от заданного количества, а песок и ще беив (гравий) — по 3-5% от их веса.
Прочность бетона определяют испытанием на сжатие трех контрольных кубов сразу после пропаривания. По результатам пробных замесов вносят соответствующие изменения в первоначальный состав бетона.
Дозировку составляющих бетона рассчитывают на замес и не редают в бетоносмесительный цех. Данные о дозировках (под номерами) хранятся у оператора дозировочного отделения, который выдает бетон. Лаборатория два раза в смену отбирает пробы бетона с каждого конвейера, определяет удобоукладываемость бетонной смеси по упрощенному методу (в форме 20X20X20 см) и изготовляет контрольные кубы (за смену 27 кубов размером 10XI0X XI0 см). Пробы отбирают в начале и в середине смены. Контрольные кубы испытывают сразу после выхода из пропарочной камеры и результаты испытаний сообщают в ОТК.
Работниками завода совместно с молодыми специалистами АН СССР были начаты эксперименты по сокращению расхода цемента ы сроков тепловлажностной обработки железобетонных изделий.
Были проведены многочисленные опыты по выбору соответствующих добавок п определению их оптимального количества, в результате которых в качестве добавки была выбрана окись кальция, взятая в количестве 1% от веса цемента. Опыты проводились на бетонных образцах размерами 10X10X10 см; бетон марки 200, режим тепловлажностной обработки 4 + 8 + 4 = 16 ч, расход цемента для контрольных замесов — 280 кг/м3, а для замесов с добавкой СаО — 230 кг/м3, т.е. на 17% меньше. Было проделано более 100 опытов. При введении СаО наблюдалось быстрое загустевание бетонной смеси и резкое снижение ее удобоукладываемости. Для устранения подобных явлений применили добавку сульфитно-спиртовой барды. Определено оптимальное количество добавки с.с.б. — 0,03% от веса цемента. Введением в бетонную смесь 1% СаО и 0,03% сульфитно-спиртовой барды было достигнуто повышение прочности бетона на 15-17%.
Серия контрольных испытаний, проведенных в лаборатории на бетонных кубах в течение длительного времени (июль 1959 г. — апрель 1961 г.), подтвердила предложенный рецепт: прочность бетонных кубов, изготовленных из смеси с сокращенным расходом цемента, 1% СаО и 0,03% с.с.б., была в среднем на 10% выше прочности кубов из серийного бетона. После 28-суточной выдержки прочность опытного бетона также составила 105-110% от прочности бетона без добавок.
Положительные результаты лабораторных опытов позволили перейти к испытанию в производственных условиях при изготовлении плит топа НУ-59-20. Песок, цемент, щебень и гравий для замеса отвешивались обычным образом и поступали в бетономешал ку принудительного действия. Чтобы не нарушать технологический процесс производства плит, добавки после тщательного перемешивания вводили вместе с водой из промежуточной емкости. Водоцементное отношение, время перемешивания, так же как и остальные технологические параметры, были те же, что и для серийных плит. Для каждой плиты определяли удобоукладываемость бетонной смеси и прочность бетона. Прочность трех кубов измеряли в день выхода их из пропарочной камеры (одновременно с плитами), остальных — в день испытания плит. Кубы испытывали по общепринятой методике, а плиты — на специальном стенде, где давление передавалось равномерно на всю поверхность изделия с помощью сжатого воздуха. Нагрузку увеличивали постепенно, ступенями по 100 кГ/м2, с интервалом в 5 мин. Под нагрузкой 500 кГ/м2 каждую плиту выдерживали 20 мин. При давлении от 570 до 650 кГ/м2 на плитах появлялись поперечные волосные трещины. При давлении 960-1000 кГ/м2 (по существующим нормам- это максимальная нагрузка разрушения для плит данного типа) плиту выдерживали 9-10 мин. Дальнейшее увеличение нагрузки вплоть до разрушения плиты производилось ступенями по 100 кГ/м2 с интервалом в 3 мин. Стрелу прогиба фиксировали индикаторы в средней точке с каждой стороны плиты. Для сравнения аналогично испытывали и серийные плиты. Разрушающая нагрузка для опытных плпт всегда превосходила разрушающую нагрузку для серийных плпт (или была равна ей) и минимум в 1,4 раза превышала допустимую. Прочность опытных бетонных кубов оказалась на 10-15% выше прочности кубов из серийного бетона; укладываемость опытного бетона — в пределах нормы. По истечении 25 суток относительные величины прочности кубов и плит из опытного и серийного бетонов не изменились.
Производственные испытания показали, что введение в бетон СаО позволяет уменьшить количество цемента в смеси, при этом прочность бетона не снижается, однако возрастает жесткость смеси и несколько ухудшается удобоукладываемость. Добавление с.с.б. и бетонную смесь повышает ее пластичность и улучшает удобоукла
дываемость. Оптимальными величинами доба вок, позволяющими сократить расход цемента на 17%, являются для СаО-1%, а для с.с.б. — 0,03%.
Силами работников завода была сконструирована, изготовлена л смонтирована специальная опытно-промышлен ная установка для дозирования окиси кальция и сульфптно-спиртовов барды и введения их в бетонную смесь.
Производительность установки — 150 л смеси за 3-4 мин, что обеспечивает подачу добавок на 3 замеса. Объем бака для окиси кальция -1 м3, вместимость — 500-600 кг окиси кальция. Объем нижнего смесительного бака — 225 л, верхнего расходного — 460 л. Бак для с.с.б. вмещает 50 л. Дозатор окиси кальция может подавать за один раз от 1 до 5,5 кг СаО, дозатор с.с.б. — от 100 до 1000 см3 с.с.б.
Схема установки показана на рис. 2. Установка состоит из бункера окиси кальция, дозатора окиси кальция, бачка супь фитно-спиртовой барды, дозатора с.с.б., нижнего смесительного бачка, клапана наполнения нижнего бачка водой, запорного клапана нижнего бачка, насоса с электродвигателем верхнего смесительного бачка и крана подачи смеси на весы.
Верхний и нижний смесительные бачки оборудованы мешалками. Привод мешалок — от электродвигателей.
Верхний и нижний бачки соединены с поплавковыми камерами. Положение поплавков в камерах определяет в соответствии с автоматикой управления перекачку смеси из нижнего бачка и верхний или наполнение нижнего бачка водой. Привод всех клапанов осуществляется пневмоцилиндрами, питаемыми от воздуш ной магистрали завода.
Рис. 2. Установка для дозирования окиси кальция и сульфитно-спиртовой барды
При установке рукоятки управления на положение «автоматика» срабатывает электропневматический клапан, воздух поступает в соответствующий пневмоцилиндр и открывается клапан наполнения нижнего бака водой. Наполнение бака продолжается до тех нор, пока поплавок не дойдет до верхнего уровня, и груз, связанный тросом с поплавком, не замкнет контакты концевого выключателя. После этого клапан закрывается. Затем включаются дозаторы окиси кальция и с.с.б. Если запас смеси в верхнем бачке достаточен, то в обоих бачках работают мешалки, которые включаются и отключаются периодически на 2-3 сек с интервалами в 5 — 7 сек. Когда поплавок верхней поплавковой камеры опустится ниже определенного уровня, включаются контакты кла пана, а также электродвигателя насоса, и приготовленная смесь из нижнего бачка перекачивается в верхний. Выключение электродвигателя и клапана происходит в момент, когда поплавок нижнего бачка доходит до нижнего уровня. Одновременно включается клапан, и цикл повторяется.
Внедрение в производство указанного выше метода изготовления бетона с добавками СаО и с.с.б. позволит заводу экономить до 7000-7500 т цемента в год.
Бетоносмесительный узел на заводе представляет собой шестиэтажное здание, расположенное в центре главного корпуса симметрично по отношению к формовочным цехам.
Инертные материалы со склада заполнителя подаются к расходным бункерам надбункерното отделения 15-ю транспортерами общей протяженностью 533 м.
Цемент из силосов подается в расходные бункера по труба-м 0 200 мм с помощью пневмовинтового насоса Павшинского завода производительностью 50 т цемента в час.
В надбункерном отделении установлено шесть расходных бун коров для конвейерного производства, из которых два бункера емкостью 30 т каждый предназначены для цемента, один бункер — для гравия, один — для щебня и два — для песка.
Бункера для заполнителей имеют емкость 25 м3 каждый.
Из расходных бункеров материалы для приготовления бетона подаются в автоматические весовые дозаторы типа ДЦ-300, ДИ-1200 и ДВ-300. Цикл взвешивания длится 60 сек. Погрешность дозировки не превышает 2%.
Взвешенные компоненты бетонной смеси через сборный бункер попадают в бетономешалки принудительного действия типа С-356 емкостью 1000 л (рпс. 22). Бетономешалка состоит из рамы, станин, смесительной чаши, привода, мешалок и разгрузочного устройства. Рама сварная, на ной смонтированы 4 опорных ролика, на которых установлена смесительная чаша.
Смесительная чаша изготовлена из листовой стали, в ее дне имеется отверстие для выдачи готового бетона. К смесительной чаше приварен зубчатый венец. Привод бетономешалки крепится к станинам, расположенным с обеих сторон рамы.
На крестовине мешалки, на одном из держателей закреплена длинная лопасть, которая служит для выгребания массы из-под крестовины и перемешивания бетона в центре чаши. Воздух в нижнюю полость пневмоцилиндра разгрузочного устройства подводится от сети давлением 3,5 атм, а в верхнюю полость от сети давлением 4-7 атм через электровоздушный клапан. Система кнопочных выключателей, сблокированных между собой, обеспечивает нормальное открывание и закрывание разгрузочных устройств.
Емкость такой бетономешалки 1000 л, диаметр чаши 2200 мм, число оборотов 6. 7 об/мин\ производительность по проекту 15 м3/ч, фактическая — более 19,5 м3/ч; мощность электродвигателя 15 кет, вес агрегата 4,5 т.
Рис. 3. Бетономешалка принудительного действия 1 — рама; 2 — смесительная чаша; 3 — привод; 4 — неподвижные гребни; 5 — мешалка; 6 — очистной гребок; 7 — разгрузочное устройство
Бетономешалки G356 отличаются хорошими эксплуатационными качествами. Бетонная смесь получается однородной. Как показали исследования, ее однородность повысилась с 0,6-0,65 при перемешивании в бетономешалках со свободным падением до 0,7- 0,8 при использовании бетономешалок принудительного действия.
Из 1455 образцов бетона М 200 в 28-суточном возрасте 1000 (или 68%) имела нормальную прочность, 365 (или 28%) имели повышенную прочность и 90 (или 6,3%) имели пониженную прочность.
Эксплуатация бетономешалок G356 показала, что они имеют также и конструктивные недостатки. Непрочным оказался ряд узлов, в том числе опорные катки, конические шестерни, грибкодержатели. В настоящее время завод-изготовитель на основе выявленных недостатков вносит необходимые изменения в конструкцию бетономешалок.
Приготовленная бетонная смесь поступает на транспортерные ленты шириной 650 мм и подается к посту формования. Длина транспортеров от узла выдачи до технологических бункеров 18 м. Транспортеры расположены горизонтально и под углом от 8 до 30°. Скорость движения ленты 1 -1,2 м/сек. Бетонная смесь, двигаясь по транспортерной ленте, не теряет однородности и подвижности и не расслаивается. По пути транспортирования бетонная смесь попадает в специальные бункера для взвешивания. Предел ‘взвешивания 2500 кг, точность до 2,3%. Благодаря взвешиванию бетонной смеси полностью ликвидированы потери бетона и обеспечен проектный вес конструкций.
На заводе процессы приготовления бетонной смеси и выдачи ее на конвейеры автоматизированы.
Существовавшая ранее схема имела существенные недостатки Оператор дозировал материалы в два приема — грубая отвесна и точная довеска, на что уходило много времени. Пневматический привод секторных затворов расходных бункеров заполнителей и затворов дозаторов работал по принципу противодавления, т.е. с одной стороны воздушного цилиндра подавался редуцированный воздух под давлением 3-3,5 атм. Чтобы преодолеть это давление и совершить рабочий ход цилиндра, надо было подать воздух под давлением 6,5 — 7 атм. При понижении этого давления и небольшом заедании приводного механизма пневмопривод отказывал в работе, что приводило к простою оборудования. Кроме того, часто выходили из строя ртутные конечные выключатели, установленные на секторных затворах. Существовавшая электроблокпровка схем дозировочного и смесительного отделений не обеспечивала точных показаний световой сигнализации при опорожнении бетономешалки и давала ложное разрешение на загрузку в нее материалов. Подача готовой бетонной смеси на конвейер требовала затраты дополнительного труда, так как связь дозировочного отделения с формовочным была не оперативна.
Оператор, выдающий бетон, передавал заказ по телефону в дозировочное отделение, вследствие чего оператор дозировочного отделения много времени затрачивал на телефонные переговоры по приему заказов.
Рис. 4. Весовые устройства для взвешивания бетона а — схема; б — общий вид; 1 — циферблат весов; 2 — стойка; 3 — система рычагов: 4 — бункер прямоугольный; 5 — бункер конусный; 6 — шибер; 7 — бункер бетоно укладчика; 8 — транспортер; 9 — направ ляющий лоток
Согласно заказу, оператор но выдаче бетона включал электро привод транспортерных лент, и бетон поступал в технологический бункер одного из конвейеров. Такая схема управления транспортерами готовой бетонной смеси была несовершенной. Имели место несогласованные действия оператора по дозированию с оператором по выдаче бетона.
В смесительном отделении на двух бетономешалках были заняты два моториста. Прежняя электросхема создавала неудобства в работе по обслуживанию оборудования, требовала большого количества людей, вызывала простои оборудования и снижала производительность труда.
На заводе была разработана система автоматического управления дозирования материалов, приготовления бетонной смеси и подачи ее на конвейеры. Основой автоматики является дистанционное управление, внедрение которого позволило автоматизировать пуск н остановку электроприводов транспортерных лент, бетономешалок, а также дозировать материалы. Автоматическая сигнализация точно и своевременно отражает рабочее состояние механизмов.
Предусмотрено автоматическое программное управление процессом приготовления бетонной смеси. Системы управлений дозировочного, смесительного отделений и узла выдачи бетона в технологические бункера конвейеров связаны между собой электро-блокировкой.
Дозировочное отделение имеет три схемы управления: дистанционное — по заказу конвейеров, местное автоматическое-с пульта дозировочного отделения и местное — наладочное.
Смесительное отделение имеет две схемы управления: автоматическое — дистанционное и местное.
Линии выдачи бетона на конвейеры имеют также две схемы управления — автоматическое и местное наладочное.
В настоящее время автоматическая схема внедрена заводом на всех трех конвейерах и работает безотказно. Ею предусмотрено управление работой дозировочного и смесительного отделений, загрузка материала в бетономешалку и выгрузка бетонной смеси на транспортерную ленту, а также подача бетонной смеси в технологические бункера.
Перевод секторных затворов расходных бункеров инертных материалов на одно давление позволил взвешивать материалы за один прием с точностью до 1% при дозировании цемента и до 1,5% при дозировании заполнителей. Вода взвешивается точно.
С внедрением новой схемы решен вопрос электроблокировки и сигнализации системы загрузки двух замесов в одну бетономешалку. Пневматический привод типа КПМ-10 секторных затворов расходных бункеров заполнителей переведен на одно давление. Ртутные конечные выключатели секторных затворов и затворов дозаторов заменены конечными выключателями ВК-211. Смонтирована и внедрена новая схема заказа бетона непосредственно с конвейеров в дозировочное отделение.
Автоматизация работы дозировочного отделения и узла выдачи бетона дала возможность высвободить 6 рабочих (трех операторов узла выдачи бетона и трех мотористов бетономешалок), ввести строгий режим перемешивания бетонной смеси, улучшила качество приготовления бетона, облегчила труд рабочих, улучшила условия их труда и снизила затраты на приготовление бетона.
Читать далее: Изготовление панелей перекрытий на конвейере
Категория: - Технология и организация железобетонных конструкций
Главная → Справочник → Статьи → Форум
stroy-technics.ru
Приготовление бетонной смеси
Приготовление бетонной смеси состоит из операций по приему и складированию составляющих материалов (цемента и заполнителей), дозирования и перемешивания их и выдачи готовой бетонной смеси на транспортные средства. Иногда в данный технологический цикл включаются дополнительные операции. Так, при бетонировании конструкций в условиях отрицательных температур необходимо подогревать заполнители и воду, при применении бетонов с добавками (противоморозными, пластифицирующими, порообразующими и др.) следует предварительно приготовить водный раствор этих добавок.
Бетонную смесь приготовляют по законченной или расчлененной технологии. При законченной технологии в качестве продукции получают готовую бетонную смесь, при расчлененной - отдозированные составляющие - сухую бетонную смесь.
Основными техническими средствами для приготовления бетонной смеси являются расходные бункера с распределительными устройствами, дозаторы, бетоносмесители, системы внутренних транспортных средств и коммуникаций, раздаточный бункер.
Технологическое оборудование компонуют по одноступенчатой (вертикальной) или двухступенчатой (партерной) схеме. Вертикальная схема характеризуется тем, что материальные элементы (цемент, заполнители) один раз поднимают на необходимую высоту, а затем под действием собственной массы они перемещаются по ходу технологического процесса. При двухступенчатой схеме составляющие бетонной смеси сначала поднимают вные бункера, затем они опускаются самотеком, проходят через дозаторы, попадают в общую приемную воронку и снова поднима ются вверх для загрузки в бетоносмеситель.
Приготовление бетонной смеси в зависимости от условий ее потребления организуют одним из следующих способов.
Районные заводы снабжают готовыми смесями строительные объекты, расположенные на расстояниях, не превышающих технологически допускаемые расстояния автомобильных перевозок. Это расстояние, называемое радиусом действия завода, зависит от технологических свойств цемента и местных дорожных условий и в первом приближении может быть определено неравенством
R < ( t1 - ( t2 + t3 + t4 ) ) v / 60,
где R - максимально допустимый радиус действия завода, км, t1 - начало схватывания цемента, мин, t2 - продолжительность загрузки и выгрузки бетонной смеси из транспортных средств, мин, t3 - продолжительность транспортирования, мин, t4 - продолжительность укладки бетонной смеси в конструкцию, мин, v - скорость транспортирования, км/ч.
Районный завод обычно обслуживает стройки, находящиеся в радиусе действия до 25... 30 км.
Районные заводы имеют годовую мощность 100...200 тыс. м3 бетонной смеси. Технологическое оборудование скомпоновано по вертикальной схеме. Завод заключает бетоносмесительный цех, состоящий из одной, двух или трех бетоносмесительных установок (секций), каждая из которых рассчитана на самостоятельную работу. Подобные установки представляют собой сооружение башенного типа с металлическим каркасом, имеющим в плане форму прямоугольника, и примыкающей к нему наклонной галереей для ленточного конвейра.
Основными сборочными единицами установки (на примере односекционной бетоносмесительной установки с двумя бетоносмесителями производительностью 20 м3/ч) являются ленточный конвейер, поворотная воронка, элеватор, комплект дозаторов (цемента, заполнителей и воды), расходные бункера, приемная воронка, бетоносмесители и раздаточные бункера.
Заполнители четырех фракций подаются на четвертый этаж башни ленточным конвейером и с помощью поворотной воронки направляются в соответствующие отсеки бункеров. Цемент подается горизонтальным винтовым конвейером и элеватором и по распределительным желобам направляется в один из двух отсеков бункера в соответствии с маркой.
Указатели уровня, предусмотренные в отсеках бункеров, сигнализируют о наполнении их материалами. На третьем этаже башни размещено дозировочное отделение, в котором установлены два дозатора заполнителей, один дозатор цемента и два дозатора воды. Отдозированные материалы попадают в приемную воронку и далее в смесительные барабаны, расположенные на втором этаже.
Управление дозаторами и смесителями ведется с пультов, расположенных соответственно на третьем и втором этажах. Готовая бетонная смесь из бетоносмесителей выгружается в раздаточные бункера.
Заводы готовят и сухие товарные смеси. В этом случае бетонные смеси в специальной таре доставляют обычными автомобилями к месту потребления и приготовляют на объекте в бетоносмесителях или в процессе транспортирования в автобетоносмесителях. Районные заводы экономически оправданы, если в районе их действия гарантировано потребление продукции в течение 10... 15 лет.
Приобъектные заводы обычно обслуживают одну крупную строительную площадку в течение 5...6 лет. Такие заводы выполняют сборно-разборными блочной конструкции, что делает возможным их перебазировку за 20... 30 сут на трейлерах грузоподъемностью 20 т.
Построечные бетоносмесительные установки обслуживают одну строительную площадку или отдельный объект при месячной потребности в бетоне до 1,5 тыс, м3. Такие установки компонуют по партерной схеме.
В качестве построечных применяют также мобильные бетоносмесительные установки, которые смонтированы на специальном полуприцепе и имеют производительность до 20 м3/ч. Конструкция установок позволяет в течение смены приводить их в транспортное положение и перевозить на буксире на очередной объект.
Использование таких установок особенно целесообразно на крупных рассредоточенных объектах, расположенных от бетонных заводов на расстояниях, превышающих технологически допустимые. Это могут быть мобильные бетонорастворные установки, что увеличивает гибкость системы централизованного обеспечения товарными смесями и повышает надежность работы установок.
stroyrubrika.ru