Современные способы вакуумирования. Метод вакуумирования
Вакуумный метод
Этот метод является, по существу, разновидностью пневматического метода контроля с обмазкой пенообразующим веществом. Его применяют для контроля герметичности открытых изделий при одностороннем доступе к контролируемой поверхности.
При испытании на исследуемый участок изделия 6 накладывают переносные вакуумные камеры, состоящие из рамки 4 с резиновыми уплотнителями 5. На контролируемое изделие наносят пенообразующее вещество. Вакуумную камеру устанавливают на изделие и с помощью вакуумного насоса создают в ее полости разрежение (обычно 0,02...0,09 МПа). В результате разрежения воздух через неплотности в изделии поступает в полость камеры. Наблюдение за появлением пузырьков в пенообразующем веществе 7 ведут через прозрачное смотровое окно камеры 3.
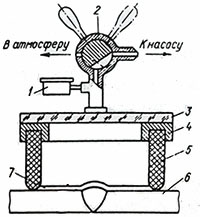
Давление в камере контролируют вакуумметром 1. При испытаниях применяют форвакуумные механические насосы. По окончании контроля трехходовым краном 2 в полость камеры напускают атмосферный воздух и перемещают ее на следующий контролируемый участок.
Широкое распространение вакуумный метод получил при контроле сварных соединений. В зависимости от конфигурации сварных изделии и видов сварных соединений применяют плоские, угловые и кольцевые вакуумные камеры. Чувствительность такого метода контроля достигает 10-2 мм3 · МПа/с.
Иногда контроль изделий осуществляют способом бароаквариума с использованием накладных вакуумных камер. Камеру устанавливают на изделии и вакуумным насосом создают в ней требуемое разрежение, после чего в ее внутреннюю полость подают контрольную жидкость (воду). Пузырьки газа в местах течей наблюдают через смотровое окно. Такой способ контроля по сравнению с обычными вакуумными испытаниями обеспечивает большую стабильность регистрации течей, поскольку пузырьки воздуха наблюдаются устойчиво в течение длительного времени.
Пузырьковые методы контроля герметичности имеют широкое распространение благодаря простоте, наглядности, возможности осмотра одновременно всей поверхности объекта, малой стоимости материалов и оснастки. К их недостаткам относятся субъективность оценки, большая трудоемкость и длительность испытания, а также сравнительно низкая чувствительность.
ndt-testing.ru
Технология вакуумирования
Понятие вакуум с латинского переводится – пустота. Глобальное направление в кулинарии, которое я затрону поверхностно. Образно под вакуумом следует понимать некую среду содержащую газ, а в нём может содержаться продукт, при давлениях значительно ниже атмосферного. Существуют различные вакуум машины, называемые ещё вакуум насосы.
Диффузионные насосы, геттерные, ионизационные насосы. Французы называют технологию приготовления пищи в вакууме «sous vide». Считается, что метод приготовления пищи в вакууме пошёл как раз из Франции в 1974 году. Эта технология имеет массу преимуществ. Удобство готовить продукт на низких температурах, что позволяет делать продукт более сочным и нежным. Пастеризация бульонов помещённых в вакуум пакеты позволяет избавиться от вредоносных бактерий и увеличить сроки реализации. Сохранение эфирных масел, аромата и концентрации танинов в продукте в результате приготовления в вакууме. Так же можно отметить наименьшую потерю влаги при заморозке заготовок, продукт не вымораживается, а тесто не высыхает. Таким образом технология вакуумирования позволяет делать заготовки впрок. Происходит в меньшей степени окисления. Продукты, имеющие большое количество влаги, к примеру, арбуз, дыня меняют свою структуру. При выборе вакуум машины стоит обратить внимание на мощность помпы. От этого параметра зависит конечный результат технологии. В некоторых моделях существует функция закачки инертного газа в вакуум пакет. Эта технология позволяет значительно увеличить сроки хранения продукта, при этом, не деформируя его при сжатии. Сам вакуум пакет имеет большую плотность и выдерживает температуру 115 градусом по Цельсию. Это позволяет свободно варить продукт, не вынимая его из пакета. Возвращусь к технологии пастеризации в вакууме. Эту технологию открыл Луи Пастер ещё в девятнадцатом веке. Чаще пастеризуют жидкости и здесь важны температурные режимы и время. Обычно пастеризация проходит при температуре 60 С* в течении часа в зависимости от объёма. Существуют так же другие температурные режимы, к примеру, 80 С* в течении 25 мин. Опять же не стоит забывать величину объёма и свойства самого продукта. При такой технологии погибают вегетативные формы микроорганизмов, но споры остаются. Эффективность пастеризации зависит от того, какие виды микроорганизмов преобладают в продукте. Таким образом, при благоприятных условиях они начинают развиваться. Поэтому когда пастеризуют бульоны, их, как правила вакуумируют и хранят в холодильнике. В этом случае срок хранения увеличивается в разы, при этом не теряются органолептические свойства продукта, и что важно, сохраняются витамины, тонины и ферменты.
Ещё один плюс можно отметить при заморозке продукта в вакууме. Это значительно сокращает переход внутриклеточной жидкости в лёд и позволяет кристалликам льда иметь меньший размер, не разрушая мембраны клеток замороженного продукта. Важным критерием дефростации является скорость заморозки продукта. Шоковая заморозка является наиболее эффективным методом, который позволяет уменьшить потерю веса, товарный вид, качество продукта. Такой метод делает однородные кристаллы в клеточных тканях, не изменяя структуры растительных волокон при этом оставляя эфиры в продукте.
Метод циркуляционного вакуумирования RH(OB)
Наиболее распространенная циркуляционная установка вакуумной дегазации RH в последние годы претерпела ряд конструктивных изменений за счет дополнительного применения кислородной фурмы, инжектора для вдувания порошков и модернизации наружной патрубковой системы RH(OB) (рис.12.9). Кислородная фурма размещается в верхней части отсасывающих патрубков. Кислород также может подаваться в вакуумируемый металл (рис.12.10), обеспечивая параллельно с вакуумированием подачу кислорода в обновляемый столб жидкой стали. Использование кислородной фурмы при вакуумировании позволяет выпускать сталь из ДСП с более высоким содержанием углерода и при более низких температурах. Компенсация падения температуры при вакуумировании обеспечивается протеканием экзотермической реакции окисления углерода стали кислородом продувки по реакции:
[C] + ½{O2} = {CO}, ΔН0 = 110352 КДж/моль.
Рис.1. Установка циркуляционного вакуумирования RH(OB) (разрез):
1 – теплоизоляционный экран; 2 – рабочий слой футеровки; 3 – компенсационный слой футеровки; 4 – изоляционный слой футеровки; 5 – графитовый электрод нагревателя; 6 – патрубок к вакуумному насосу; 7 – отверстие для кислородной фурмы; 8 – смотровое окно для TV; 9 – крышка кожуха камеры; 10 – средняя часть кожуха камеры; 11 – отверстие для подачи легирующих; 12 — нижняя часть кожуха камеры; 13 – контроль температуры; 14 – линия подачи аргона; 15 – футерованные патрубки
Скорость реакции обезуглероживания в вакуумкамере значительно выше, чем в ДСП. Кроме того, в последних разработках применена автономная вакуумкамера, замена которой требует значительно меньшего времени.
Дополнительно система RH(OB) оборудована фурмой для подачи инертного газа в расплав. Сочетание вакуума и продувки инертным газом ускоряет процесс обезуглероживания и обеспечивает интенсивное перемешивание металла, за счет повторной циркуляции.
Использование кислородного обезуглероживания в сочетании с подогревом по методу сопротивления и вакуумированием позволяет получать особо низкоуглеродистые стали с содержанием углерода до 0,002 % . Применение дополнительного подогрева обеспечивает остаточную температуру стали порядка 1570-15800С, что вполне достаточно для ее разливки. Порционное вакуумирование не требует большого свободного объема ковша. Высота свободного объема составляет 200 мм. Установки RH(OB) используют в настоящее время для производства ультранизкоуглеродистых сталей, содержащих до 0,002% С. Вакуумированию при этом подвергаются стали с исходным содержанием до 0,045% С. Использование кислородной фурмы в процессе RH(OB) и добавка на поверхность алюминиевокремниевых сплавов позволяет даже повысить температуру металла на 25 градусов за период обработки.
Современная технология плавки в ДСП позволяет при использовании чистой шихты и работе на вспененных шлаках получать металл перед внепечной обработкой с низким содержанием азота (до 0,0030%), который с большим трудом удаляется даже при вакуумировании.
Вакуумирование позволяет уменьшить концентрацию азота до 0,0015-0,0020% (на МНЛЗ содержание азота при разливке с защитой металла вновь возрастает в среднем на 0,0010%). Активное вакуумуглеродное раскисление металла снижает концентрацию кислорода с 0,0160 до 0,0010%, после науглероживания содержание кислорода уменьшается. Удаление водорода в среднем с 5 до 2 см3/100 г происходит, в основном, в период активного раскисления металла углеродом, немного увеличиваясь после значительного науглероживания. Вакуумирование полученного в ДСП стандартного малоуглеродистого полупродукта с последующим кардинальным (присадки до 6,5-7,0 кг/т) науглероживанием на установке циркуляционного типа способствует росту производительности комплекса, достижению повышенного качества металлопродукции, обеспечивает требования техники безопасности и экологические требования, а также организационную гибкость производственного процесса.
Широкому распространению вакуумных установок RH(OB) во многом способствовало совершенствование вспомогательных систем, обеспечивающих технологический цикл. В настоящее время погружение патрубков в расплав осуществляется по трем принципиально различающимся вариантам: 1 – путем вертикального перемещения сталеразливочного ковша совместно со сталевозом; 2 – путем вертикального перемещения только сталеразливочного ковша; 3 – путем вертикального перемещения вакуумкамеры. Перемещение ковша со сталевозом осуществляется с помощью специальной платформы, опирающейся на пуансоны гидроподъемников. Механизм гидроподъемников расположен непосредственно под вакуумкамерой в подвальном помещении. Для реализации процесса сталевоз с ковшом подъезжает под вакууматор, стопорится на платформе гидроподъемника, поднимается до погружения патрубков вакууматора на определенный уровень, контролируемый концевыми выключателями, и стопорится на время цикла обработки в таком положении. После окончания цикла обработки сталевоз с ковшом опускается на нулевой уровень площадки, освобождая патрубки вакууматора, и транспортирует сталь на МНЛЗ. Предложенная система значительно упрощает вакуумное уплотнение на камере, уменьшает высоту отделения. Однако, требует применения высокомощных гидроподъемников и, самое главное, связана с опасностью попадания металла на гидроподъемники в случает аварии.
В целях повышения безопасности системы при аварийных ситуациях разработан механизм тросового вертикального перемещения ковша для обеспечения процесса вакуумирования. Тросовая подвеска для поднятия ковша обеспечивает более надежную работу механизма. Однако, требует более высокого отделения, усложняет и утяжеляет конструкцию расположенную сверху вакуумкамеры, т.к. необходимо осуществлять подъем ковша с металлом, усложняет работу других агрегатов, обеспечивающих технологический процесс.
metallurgy.zp.ua
Современные способы вакуумирования — Студопедия.Нет
⇐ ПредыдущаяСтр 75 из 95Следующая ⇒Рис. 10.1. Различные способы внепечного вакуумирования.
Схема обработки жидкой стали вакуумом была предложена еще Г.Бессемером. Практическое использование метода внепечного рафинирования для повышения качества металла относится к началу 50-х годов. В СССР работы по исследованию влияния понижения давления на процессы газовыделения были начаты в конце 30-х годов, а первая промышленная установка обработки металла вакуумом в ковше опробована на Енакиевском металлургическом заводе по инициативе ученых ИМет АН СССР А.Самарина и Л.Новика в 1952-1954 гг. Ковш с металлом опускали в камеру, которую затем плотно закрывали крышкой и из закрытой таким образом камеры откачивали воздух.
В настоящее время в промышленно развитых странах успешно работают сотни установок внепечного вакуумирования различной конструкции. Схемы наиболее распространенных конструкций представлены на (рис. 10.1). Самым простым способом является способ вакуумирования в ковше (рис. 10.1).
Недостатком вакуумирования в ковше является невысокая эффективность метода при вакуумировании относительно больших масс металла (> 50 т) и неравномерность состава металла в ковше после ввода раскислителей и легирующих вследствие слабого перемешивания всей массы металла. Этого можно избежать в том случае, когда предусматривается продувка металла в ковше интертным газом или электромагнитное перемешивание.
Рис. 10.2. Установка вакуумирования стали в ковше:
1-вакуум-крышка; 2-теплозащитный экран; 3-сталеразливочный ковш; вакуум камера.
При продувке металла инертным газом к обычным потерям тепла при выпуске и выдержке в ковше добавляются потери тепла на нагрев газа, продуваемого через металл. При электромагнитном перемешивании этот недостаток ликвидируется, однако электромагнитное перемешивание требует более сложного и дорогостоящего оборудования.
В настоящее время наиболее распространены следующие способы обработки металла вакуумом в ковше:
1. Ковш с металлом помещают в вакуумную камеру, организуют перемешивание металла инертным газом, раскислители вводят в ковш из бункера, также находящегося в вакуумной камере. Этот метод часто называют ковшевым вакуумированием (рис. 10.2).
2. Металл вакуумируют при переливе из ковша в ковш или из ковша в изложницу, т.е. обработке вакуумом подвергается струя металла (метод называют струйным вакуумированием или вакуумированием струи).
3. Металл под воздействием ферростатического давления засасывается примерно на 1,48 м (рис. 10.3) в вакуумную камеру, которую через определенные промежутки времени поднимают, но так, чтобы конец патрубка все время оставался опущенным в металл в ковше. Металл из камеры сливается по патрубку в ковш, затем камеру опускают и под действием разрежения в нее засасывается очередная порция металла (метод называют порционным вакуумированием). В некоторых случаях поднимают и опускают не вакуумную камеру, а ковш с металлом, а камера остается неподвижной.
Этот способ часто называют также способом DH — по первым буквам предприятия Dortmufld-Horder, ФРГ, где он был осуществлен впервые (рис. 10.3).
Рис.10.3. Схема процесса порционного вакуумирования(DH-процесс)
4. Два патрубка вакуумной камеры погружают в металл; при вакуумировании порция металла засасывается в вакуумную камеру (рис. 10.4).
Рис.10. 4. Схема процесса циркуляционного вакуумирования(RH-процесс)
В один из патрубков начинают подавать инертный газ, в результате чего металл в этом патрубке направляется вверх, в вакуум-камеру, а по другому - стекает вниз, в ковш. Происходит циркуляция металла через вакуум-камеру. Способ этот называют циркуляционным вакуумированием (или RH-процессом — по первым буквам предприятия Ruhrstahl-Heraeus, ФРГ, где процесс был осуществлен впервые). Заслуживает особого упоминания метод непрерывного (поточного) вакуумирования при разливке, разработанный в Липецком политехническом институте под руководством проф. Г.А.Соколова и внедренный на НЛМК.
Рис.10.5. Схема установки поточного вакуумирования:
1-сталеразливочный ковш; 2-вакуумная камера; 3-промежуточный ковш; 4-кристализатор.
Рис.10.6. Метод пульсационного перемешивания металла в ковше (РМ-процесс)
В основу метода положен принцип вакуумной дегазации струи и слоя металла в проточной камере, расположенной между сталеразливочным и промежуточным ковшами (рис.10.5). Рафинированная сталь поступает в промежуточный ковш по металлопроводу, погруженному под уровень металла.
Достоинствами метода является одновременное решение проблем:
1) вакуумирования в потоке;
2) защиты струи от вторичного взаимодействия с атмосферой;
3) повышение эффективности вакуумирования в результате движения струи через вакуумированное пространство, при котором происходит ее раскрытие и раздробление на капли, а также увеличение поверхности контакта металл—газовая фаза (вакуум).
Методы вакуумной обработки стали непрерывно совершенствуются, предлагаются новые решения, позволяющие получать металл высокого качества с использованием более простых методов. Примером может служить разработанный на одном из японских заводов метод, названный методом РМ (Pulsation Mixing — пульсирующее перемешивание), схема которого показана на рис. 10.6. На установке такого типа обрабатывают 100-т плавки конвертерного металла. Сущность метода заключается в переменном включении и выключении подачи аргона и вакуумного насоса, вследствие чего металл в цилиндре (и в ковше) интенсивно пульсирует, что обеспечивает высокую степень его рафинирования. Достоинство установки — возможность высокоэффективной работы без глубокого вакуума.
Дата добавления: 2018-04-05; просмотров: 7; ЗАКАЗАТЬ РАБОТУ
studopedia.net
Вакуумный метод - Большая Энциклопедия Нефти и Газа, статья, страница 1
Вакуумный метод
Cтраница 1
Вакуумный метод широко известен в производстве клееных металлических деталей сложной конфигурации. [1]
Вакуумный метод разработан английской фирмой Авро Ризерч и используется для выявления дефектов клеевого соединения между обшивкой и заполнителем в сотовых панелях. [2]
Вакуумный метод основан на регистрации падения вакуума в замкнутом объеме контролируемого изделия или на фиксации молекул пробного газа, появившихся в этом объеме. Большое распространение получил вакуумный метод для контроля швов конструкций, имеющих незамкнутую форму объема, а также конструкций, доступ к которым возможен только с одной стороны. Контроль осуществляется следующим образом. Одну сторону участка сварного соединения обильно смачивают раствором пенного индикатора. На это место устанавливают вакуум-камеру, из которой откачивают воздух. [3]
Вакуумный метод основан на регистрации параметров индикаторной жидкости и газов, проходящих через сквозные неплотности при отрицательном перепаде давления или на регистрации изменения вакуума. [4]
Вакуумный метод во многих случаях является более дешевым. При использовании двусторонних форм обе стороны изделия имеют гладкую поверхность. В отличие от контактного вакуумный метод не всегда пригоден для изготовления изделий, имеющих форму, близкую к сферической, так как во многих случаях усилия формования, создаваемого атмосферным давлением, недостаточно, чтобы полностью закрыть матрицы. [5]
Вакуумный метод широко известен в производстве клееных металлических деталей сложной конфигурации. [6]
Вакуумный метод позволяет отбирать пробу в очень короткий промежуток времени ( доли секунды), что очень важно при определении концентрации токсических газов, выделяющихся с резкими колебаниями их количества во времени. Для отбора проб вакуумным методом используются газовые пипетки или баллоны. [7]
Вакуумный метод заключается в нанесении смывки и удалении продуктов очистки с помощью вакуума. [9]
Вакуумный метод приемлем для контроля непроницаемости стыковых, нахлесточных, тавровых и трехгранных соединений во всех положениях в пространстве. [11]
Вакуумный метод состоит в том, что колонка с сорбентом предварительно вакуумируется. Затем в нее вводят определенный объем анализируемого газа. При движении вдоль слоя сорбента легкие компоненты опережают другие, лучше сорбирующиеся вещества и собираются на выходе из колонки в специальных ловушках, из которых вымываются газом-носителем для анализа проявительным методом в аналитическую колонку. [12]
Вакуумный метод широко известен в производстве клееных металлических деталей сложной конфигурации. [13]
Вакуумный метод - разновидность пневматического метода контроля с обмазкой пенообразующим веществом применяют для контроля герметичности в основном открытых изделий при одностороннем подходе к контролируемым сварным и другим соединениям. Метод заключается в использовании переносных вакуумных камер-присосок, накладываемых на участок контролируемого соединения. [15]
Страницы: 1 2 3 4
www.ngpedia.ru
Метод вакуумирования стимулирования водоотбора
Вакуумирование — весьма распространенный метод интенсификации водоотбора, широко применяемый при эксплуатации водопонижающих скважин и различных дренажных устройств в районах горнорудных разработок и в строительном водопонижении — для осуществления пород (грунтов) с низкими фильтрационными свойствами. Сущность метода заключается в повышении энергии фильтрационного потока созданием пониженного давления (вакуума) в стволе скважины, изолированном от проникновения атмосферного воздуха.
Для создания достаточно глубокого и устойчивого вакуума применяются вакуумные насосы с различной подачей, отсасывающие воздух из герметично закрытого пространства между водоподъемной трубой и эксплуатационной колонной. Чаще всего для вакуумирования скважин используют вакуумные водокольцевые насосы типа КВН или ВВН, обеспечивающие разрежение до 0,08—0,09 МПа.
Эксплуатация скважин, оборудованных вакуум-насосами, сводится к поддержанию внутри ствола необходимого разрежения периодическим включением насоса.
Эффект вакуумирования может быть достигнут также с помощью водонепроницаемой перемычки, устанавливаемой в пространстве между водоподъемными трубами и эксплуатационной колонной над погружным насосом. С этой целью обычно используют специальную чашеобразную манжету из эластичной резины, которую крепят на водоподъемных трубах при монтаже насоса. После включения насоса манжета прижимается к эксплуатационной колонне, отделяя расположенный над ней столб воды, и изолируя водоприемную часть скважины, в которой создается пониженное давление.
Вакуумирование скважин, приводящее к возрастанию скоростей фильтрации в прифильтровой зоне и увеличению водопритока, в определенной мере способствует также и очистке фильтрующих каналов от тонкодисперсного кольматанта различного происхождения (остатков промывочной жидкости, хемо - генных рыхлых осадков и пр.), т. е. позволяет поддерживать проницаемость прифильтровых зон на относительно более высоком уровне по сравнению со скважинами, эксплуатируемыми без наложения вакуума.
Метод вакуумирования применяется для стимулирования водоотбора из скважин, эксплуатирующих как напорные, так и безнапорные водоносные горизонты, при различных глубинах залегання и составе водовмещающих пород. Особенно эффективна вакуумирование при осушении рыхлых обводненных пород со слабой водоотдачей и низкой водопроницаемостью, в частности, мелко - и тонкозернистых глинистых песков с коэффициентом фильтрации менее 1 м/сут. На рудниках КМА этот метод успешно применили, в частности, для интенсификации водопритока к восстающим скважинам, пробуренным для осушения рудной толщи с коэффициентом фильтрации менее 0,1 — 0,2 м/сут.
Вакуумирование водопонижающих скважин получило распространение в Подмосковном и Днепровском угольных бассейнах, Никопольском марганцевом бассейне и некоторых других горнорудных районах. Опыт практического применения метода в горнорудной промышленности показал, что помимо существенного (в среднем 2—3-кратного) увеличения водоотбора, вакуумирование позволяет существенно ускорить снятие остаточных напоров водоносных горизонтов при освоении обводненных месторождений и значительно сокращает продолжительность осушения пород со слабой водоотдачей в условиях неустановившейся фильтрации.
Включение вакуумирования в группу методов интенсификации водопритока в некоторой мере условно, так как усиленный водоотбор из вакуумированных скважин достигается лишь в период создания вакуума. Поэтому вакуумирование правильнее рассматривать как интенсифицированный метод эксплуатации водопонижающих и водозаборных устройств в сложных условиях водоотбора.
kolodci.com.ua
Вакуумирование стали
Идея использования вакуума при выплавке стали была высказана еще Г. Бессемером в XIX в., но в промышленных масштабах начали широко применять его только с начала 50-х годов XX в. после создания пароэжекторных вакуумных насосов, имеющих высокую производительность и обеспечивающих глубокий вакуум.
В современной сталеплавильной практике диапазон применения вакуумирования весьма широк. Во-первых, оно является обязательным элементом технологии ковшевой обработки металла, которая широко применяется при производстве качественных сталей массового назначения. Во-вторых, при производстве в небольших объемах сталей специального (особо ответственного) назначения под вакуумом проводят как выплавку, так и разливку стали.
При выплавке сталей массового назначения вакуумированием решают следующие основные задачи:
- Удаление из металла водорода до остаточного содержания его не более 1,5-2 мл/100 г, при котором исключается образование внутренних трещин (флокенов) в твердой стали.
- Вакуумно-углеродное раскисление стали.
- Глубокое обезуглероживание металла, когда углерод является вредной примесью (получение остаточного содержания углерода менее 0,01%, в пределе не более 0,001-0,002%).
Из многочисленных способов, предложенных в разных странах, наибольшее промышленное применение имеют два — порционный и циркуляционный способы, разработанные в Германии, а также практическое применение имеет струйное вакуумирование, впервые промышленно освоенное в СССР при отливке крупных слитков, имеющих массу до 100 т и более.
Порционный способ вакуумирования стали
Порционный способ вакуумирования стали был разработан и промышленно освоен в 1956 г. западно-германской фирмой “Дартмунд Хердер Хюттенюнион”. Обычно его называют способом ДН. Принципиальная схема конструкции установки и ее работа показаны на рис. 112а.
Металл засасывается в вакуумную камеру порциями через огнеупорный патрубок, нижний конец которого постоянно находится в металле. Засасывание металла происходит благодаря разности давлений на расплав в открытой части ковша и в вакуумной камере. Из физики известно, что при полном вакууме и внешнем давлении в 1 ат ртуть, имеющую плотность 13,6 г/см3, можно поднять на 760 мм (ртутный барометр), а воду, имеющую плотность 1 г/см3, на 10 м. Жидкое железо имеет плотность около 7 г/см3, следовательно, его можно поднять на 1,43 м. Полного вакуума в вакуумной камере не бывает, поэтому можно считать, что жидкое железо с помощью вакуума можно максимально поднять на 1,4 м.
Эту величину учитывают при установлении параметров конструкции вакуумной камеры, которая должна обеспечивать засасывание в один прием 10-12% метала от общей массы его вковше.
Слив металла обратно в ковш осуществляется увеличением расстояния между ковшом и вакуумной камерой, для чего или поднимают вверх вакуумную камеру, или опускают вниз ковш. Обычно вариант перемещения ковша принимают при его вместимости менее 100 т. Если же масса металла в ковше больше, то перемещают вакуумную камеру. Последний вариант является более распространенным.
Один цикл, обеспечивающий всасывание и слив, обычно продолжается 15-30 с. Общая продолжительность вакуумирования определяется количеством циклов, которое зависит от коэффициента (показателя) циркуляции, выражающего отношение суммарной массы металла, прошедшей через вакуумную камеру, к массе стали в ковше. Средняя величина коэффициента циркуляции обычно равна пяти, т.е. через вакуумную камеру необходимо пропустить металл пять раз. Обычно конкретное требуемое значение его устанавливают экспериментально применительно к конкретной вакуумной установке, определенной группе вакуумируемых марок сталей и решаемой главной технологической задаче.
Если принять, что каждый цикл обеспечивает всасывание 10% металла, находящегося в ковше, то для одного пропуска его через вакуумную камеру необходимо 10 циклов. При коэффициенте циркуляции пять общее число циклов потребуется 50. Следовательно, продолжительность вакуумирования составит до 25 мин. В случае глубокого обезуглероживания может возникнуть необходимость довести коэффициент циркуляции до 10 и более, поэтому продолжительность вакуумирования может составить до 40-50 мин. Но это может привести к чрезмерному охлаждению металла.
Эффективность вакуумирования стали любым способом в большой степени зависит от разрежения в камере, т. е. от остаточного давления газов в ней, которое зависит от типа и производительности вакуумных насосов, а также от времени вакуумирования. В начале процесса, когда газовыделение из металла энергичное, остаточное давление относительно высокое, а в конце процесса оно минимально и обычно составляет 0,5 мм рт.ст. (0,067 кН/м2). Лучшие вакуумные насосы обеспечивают конечное давление 0,1-0,2 мм рт. ст.
Циркуляционный способ вакуумирования
Циркуляционный способ вакуумирования был опробован в производственных условиях в 1959 г. фирмой “Руршталь Гереус”, часто его сокращенно называют способом RH. Этот способ по конструкции устройства и гидродинамическим условиям взаимодействия металлической и газовой фаз является более совершенным, чем порционный способ, поэтому он имеет большее распространение.
Принципиальная схема работы установки циркуляционного вакуумирования показана на рис. 112б. Вакуумная камера имеет два патрубка — всасывающий (подъемный) и сливной. В рабочем положении нижние концы обоих патрубков погружаются в металл, а камера остается неподвижной. Донная часть ее должна находиться на таком расстоянии от уровня металла в ковше, чтобы было обеспечено затопление этой части металлом при создании разряжения в камере. Циркуляция металла ковш-камера-ковш обеспечивается благодаря подаче в подъемный патрубок аргона, пузыри которого, разрыхляя металл, снижают его плотность в патрубке, вызывая тем самым всасывание дополнительного количества металла, вызывающего повышение его уровня в камере. По достижении определенного уровня (несколько более 1,4 м над уровнем в ковше) плотный металл вытекает по сливному патрубку в ковш, поскольку имеет большую плотность.
Скорость циркуляции металла зависит от создаваемого в камере разряжения, диаметра всасывающего патрубка и расхода аргона. Обычно эти параметры выбирают так, чтобы через вакуумную камеру можно было пропустить весь металл один раз за 3-5 мин. Следовательно, при коэффициенте циркуляции пять продолжительность вакуумирования будет составлять 15-25 мин.
Из практики известно, что при циркуляционном вакуумировании продолжительность обработки металла в ковше можно уменьшить по сравнению с порционным вакуумированием, не ухудшая, даже улучшая конечные показатели. Этому в немалой степени способствует обработка металла аргоном во всасывающем патрубке. Циркуляционное вакуумирование — это по существу комбинированная вакуумно-аргоновая обработка стали в ковше.
Следует особо подчеркнуть, что в способах порционного и циркуляционного вакуумирования в классических вариантах, описанных выше, кинетические условия взаимодействия металлической и газовой фаз являются явно недостаточными для реализации термодинамических возможностей. Об этом свидетельствует сопоставление данных, полученных термодинамическими расчетами, с фактическими данными, наблюдаемыми в производственных условиях по обезуглероживанию металла.
Равновесные соотношения содержаний углерода и кислорода в металле для температуры 1600°С несколько упрощенно могут быть описаны простым уравнением [C] · [O]=0,0025PCO, где PCO — парциальное давление CO в газовой фазе, которое в случае вакуумирования можно принять равным остаточному давлению в вакуумной камере (ат). Указанное уравнение графически представлено на рис. 113.
Как указывалось выше, современные вакуумные установки обеспечивают остаточное давление 0,5 мм рт. ст., т. е. менее 0,001 ат. Следовательно, можно принять, что PCO ≤0,001 ат.
Остаточное содержание углерода в металле в конце окислительного рафинирования обычно составляет менее 0,05%, ввиду чего фактическое содержание кислорода более 0,10%. При вакуумировании концентрации углерода и кислорода в металле снижаются благодаря протеканию реакции [C]+[O]={CO}, но остаточное содержание кислорода всегда составляет не менее 0,02% (имеется в виду вакуумирование нераскисленной стали).
Согласно рис. 113, при [O]≈0,02% и PCO ≈0,001 ат равновесное остаточное содержание углерода в металле должно составлять примерно 0,0001%. Практически же с очень большим трудом удается получать 0,001%, т. е. на порядок меньше.
Ввиду этого предпринимались шаги по созданию способов, улучшающих кинетические условия взаимодействия металлической фазы с газовой. Результатом является разработка способов вакуумирования в струйном режиме, когда жидкий металл дробится на мелкие капли, чем обеспечивается резкое увеличение поверхности контакта металла с газовой фазой, аналогично увеличению поверхности контакта пузырей аргона с металлом при уменьшении их диаметра.
Струйное вакуумирование при отливке крупных слитков
Струйное вакуумирование при отливке крупных слитков было разработано в СССР, промышленно освоено на “Уралмашзаводе”, применяется широко при отливке крупных слитков массой до 100 т и более, обрабатываемых, как правило, ковкой. Разработка и промышленное освоение этого способа вакуумной обработки стали является принципиально новым шагом в повышении качества весьма ответственных крупных изделий, поэтому создатели его были отмечены Государственной премией.
Принципиальная схема установки показана на рис. 114. Изложница для приема металла помещается в вакуумную камеру. Металл из сталеразливочного ковша попадает в промежуточную емкость, представляющую большую воронку; через воронку металл попадает в вакуумную камеру, где разбивается на мелкие капли благодаря естественному газовыделению; капли металла, имеющие огромную удельную поверхность, взаимодействуют с газовой фазой (подвергаются воздействию вакуума) во время их падения. Кроме того, металл, находящийся в изложнице, тоже подвергается воздействию вакуума примерно так же, как при порционном вакуумировании.
Сталь для отливки крупных слитков обычно содержит углерода не менее 0,2%, нередко до 0,5% и даже выше. Поэтому при ее обработке вакуумом описываемым способом происходит не только глубокая дегазация, обеспечивающая полное устранение образования флокенов (опасного дефекта крупных слитков легированной стали), но и глубокое вакуумно-углеродное раскисление, результатом которого является весьма существенное снижение содержания оксидных неметаллических включений в слитке. В итоге наблюдается скачок в повышении качества стали и изделий из нее.
Это связано, во-первых, с тем, что улучшаются кинетические условия взаимодействия металла с газовой фазой, благодаря чему эффективность вакуумирования существенно повышается; во-вторых, весь эффект вакуумирования сохраняется (фиксируется в готовом металле). При порционном и циркуляционном вакуумировании часть эффекта этой операции теряется во время разливки стали. К сожалению, лишь малая доля (не более 5%, редко выше) производимой стали идет на отливку крупных слитков. Основная масса производимой стали разливается непрерывным способом с использованием явно малоэффективных способов порционного и циркуляционного вакуумирования. Учитывая это, в СССР в конвертерном цехе № 2 НЛМК была сделана попытка совместить струйное вакуумирование с непрерывной разливкой (А. с. 295607 СССР).
Струйное вакуумирование, совмещенное с непрерывной разливкой
Струйное вакуумирование, совмещенное с непрерывной разливкой, названное авторами поточным вакуумированием, по идее является способом, заслуживающим самого серьезного внимания. Принципиальная схема установки показана на рис. 115, которая вполне понятна без дополнительного пояснения.
Проведенные производственные эксперименты показали, что при таком способе вакуумирования обеспечивается почти полная реализация термодинамических возможностей обезуглероживания металла. Кроме того, этот способ позволяет весьма существенно сократить время нахождения металла в ковше по сравнению с обычными способами вакуумирования, благодаря чему становится возможным выпускать металл из сталеразливочного агрегата с меньшим перегревом выше температуры плавления; почти полностью исключить вторичное насыщение металла газами во время разливки, неизбежное при вакуумной обработке обычными способами.
Основным недостатком рассматриваемого способа вакуумирования является необходимость увеличения расстояния между сталеразливочным и промежуточным ковшами, а это в действующих цехах практически невозможно.
По нашему мнению этот самый перспективный способ вакуумирования стали может быть полноценно реализован при изменении принципа подвода вакуумированного металла в промежуточный ковш.
metallurgy.zp.ua