Производитель пеноблоков: область применения, габариты и свойства материала. Изготовление пеноблока
Технология производства пеноблоков
На сегодняшний день производство пенобетонных блоков самое популярное среди выпуска легких ячеистых бетонов, этот успех объясняет не только простая технология изготовления пеноблоков, но и выход качественного и в каком-то смысле уникального продукта. Только такие изделия заключают в себе положительные эксплуатационные характеристики всех традиционных материалов, используемых на протяжении столетий в частном и гражданском строительстве, так как же все-таки можно создать такой универсальный строительный материал?
Технологии производства

Пенобетонные блоки могут изготовляться посредством двух технологий: литьевой и резательной, также он бывает как автоклавного твердения, так и естественной выдержки. При автоклавном твердении, пенобетонная смесь выдерживается в специальных сушилках – камерах при установленной влажности и температуре, итак, обо всем по порядку.
Литье
Отличительные черты данной технологии производства – готовая смесь заливается в заранее подготовленные формы, размеры таких форм могут быть разнообразны. Выдерживать пеноблоки при таком виде их изготовления можно как с помощью пропарочной камеры, так и на естественной сушке. Более качественный считается пеноблок автоклавного твердения, но если создать оптимальные условия в месте выдержки, то получатся не менее качественный продукт.
Оборудование
Бетономешалка, но не обычная, а специальная, секрет ее в наклонно расположенных лопастях, которые предотвращают разбиение пены во время перемешивания. Шланг для подачи смеси или же специальная емкость, объемом равным одному замесу, но для ее передвижения по цеху понадобится кран-балка, пропарочная камера или место их вдержки, полиэтиленовая пленка. Лучший вариант – это приобретение специального мини–завода целиком, оно позволит избежать большого количества брака. Как правило, к такому заводу идет подробная инструкция, и подбор состава пенобетонной смеси различных плотностей, на некоторых предприятиях, продающих такое оборудование, к нему прилагаются выездные специалисты, которые налаживают процесс. В будущем, производство блоков посредством таких заводиков минимизирует процент брака за счет 80% автоматизации производственного процесса.
Сырье
Портландцемент
Самый хороший вариант, сочетающий в себе принцип «цена — качество» — это цемент М 400 Д 20, только при условии, если он полностью подтверждает по качеству свою марку, в противном случае – не прочный пеноблок.
Песок
Модуль крупности 0,02, без мусора и инородных тел, важно, чтобы он обладал влажностью не более 5%. Если же показатель выше, то прежде чем пускать его в стройку, нужно хорошенько просушить. Дело в том, что при перемешивании песок отдает эту влагу в смесь, соответственно увеличивается водоцементное отношение, и о качественной смеси при таких обстоятельствах не может быть и речи.
Пенообразователь
Какой именно более подходит к вашему производству – зависит от типа оборудования.
Вода – обычна вводопроводная
Фиброволокно
Армирующий элемент, позволит избежать трещинообразования.
Оптимальный подбор состава смеси выявляется опытным путем, для выявления качественной смеси, нужно чтобы она обладала следующими данными:
Процесс производства
- Сборка и смазка форм, для этих целей можно использовать обычное отработанное машинное масло. Смазывать лучше пульверизатором, так слой смазки получится максимально тонким.
- Приготовление начинается со смешивания воды и фиброволокна, если его добавить уже в бетонную смесь, то фибра полностью не растворится, и эффект армирования будет слабый.
- Далее в мешалку добавляется сначала цемент, после песок.
- Пока идет перемешивание, готовим концентрат, для этого в готовый пенообразователь добавляем необходимое количество воды, перемешиваем и выливаем в специальную емкость пеногенератора.
- После однородного перемешивания цемента с песком, генерируем пену, важно следить, чтобы во время подачи она была однородная и стойкая.
- Все перемешивается не более 3 минут, главное за это время добиться однородности смеси.
Заливка форм
Можно использовать шнековую подачу смеси посредством шланга, а можно с помощью бадьи, в первом случае, лопасти шнека разбивают пену и происходят потери не только в объеме готовой смеси, но и в качестве блоков.
Выдерживание
При автоклавном производстве — не более суток, а вот при естественной сушке, чтобы пенобетон получился более надежный, рекомендуется укутывать формы утеплителем и накрывать полиэтиленовой пленкой. В среднем выдержка – сутки.
Распалубка изделий и складирования в месте выдержки
После 2 недельной просушки, блоки укладываются на поддоны и отправляются в продажу. Многие пренебрегают этим этапом, а зря, если свежие пеноблоки сразу пустить в стройку, то под нагружением они могут дать ошеломительную усадку или же частично разрушиться.
Резательная технология
Она отличается от предыдущей способом заливки смеси. Готовый пенобетон укладывается в одну большую опалубку, где и набирает свою первоначальную прочность, после чего, этот монолит освобождают от этой формы и разрезают на блоки специальным станком. Во всех остальных этапах производства обе технологии идентичны.
Изготовление пеноблока, видео
Вывод
Главный принцип производства пенобетонных блоков – соблюдение всех правил технологии и стандартов качества. Отступы от них чреваты низкокачественной продукцией и высоким процентом брака.
Удачной стройки!
oblokax.ru
литьевая и резательная. Оборудование для производства пеноблоков :: BusinessMan.ru
Практичность при выполнении монтажных операций и оптимизация расходов – первостепенные условия, к которым стремятся участники строительной отрасли. Достигаются они разными путями и способами, но в итоге облегчают рабочий процесс и позволяют обеспечивать качественный результат. Переход от традиционных стройматериалов на более современные и даже инновационные часто выступает именно как средство оптимизации и повышения качественных характеристик сооружения.
В этом смысле интересна технология изготовления пеноблоков, которая базируется на классическом способе приготовления строительного раствора, но при этом отличается доступностью. Использовать ее может и домашний мастер, но для этого придется в деталях ознакомиться с нюансами создания такого рода блочных стройматериалов.
Из чего делают пеноблоки?
В качестве основы применяется портландцемент, причем самой высокой марки – например, подходит М 400. Цемент должен отвечать свойствам данной марки, иначе он не сможет выполнять свои функции после изготовления. Отличительной чертой пеноблока является пористая структура, благодаря которой он входит в группу ячеистых бетонов. Поэтому процесс его изготовления не обойдется и без пенообразователя. Это может быть органический или синтетический компонент, в перечень задач которого будет входить как раз образование неплотной, пористой структуры. На практике она обеспечит стенам немало эксплуатационных преимуществ.
Также в основу иногда добавляют глину, золу и некоторые разновидности промышленных отходов. С точки зрения повышения технико-физических свойств в такой разбавке особого смысла нет – добавление второсортного сырья обычно ставит целью удешевление состава путем вымещения дорогостоящего портландцемента. Также в обязательном порядке в состав вводится песок и вода.
Своего рода функциональный сегмент компонентов формируется клеем и фиброй. Что касается клеевого раствора, то он потребуется и для состава, и для кладки. Это может быть один и тот же продукт – главное, чтобы он соответствовал требованиям для использования в конкретных условиях. С точки зрения приготовления раствора важны будут такие свойства, как вязкость, сцепление, хваткость и химическая безвредность. В качестве средства формирования кладки клей для пеноблоков в чистом вид используется редко, но в любом случае он должен быть морозостойким, терпимым к влажности, прочным и огнеупорным. Фиброволокно, в свою очередь, выполняет задачу армирования. Тоже в некотором роде функция сцепки, но в более выраженном механическом варианте. Волокна позволяют минимизировать риск образования трещин, усиливают конструкции стен и перекрытий, а также снижают нагрузки на смежные конструкции.
Характеристики пеноблока
Эксплуатационные характеристики отражаются уже в самой маркировке пеноблока. Например, для акцента на теплоизоляции стоит выбирать марки от D150 до D400. Данный материал благодаря высокой плотности (числовое значение указывает на соотношение кг/м3) обеспечивает достаточное утепление для домов, расположенных в средних широтах. В плане прочности это не самый выгодный вариант на фоне традиционного кирпича, например. В среднем прочностный предел составляет 9 кг на 1 см3. Другое дело, что даже производство пеноблоков в домашних условиях допускает внесение пластификаторов и наполнителей, способных повышать отдельные свойства, в том числе прочность и морозоустойчивость.
В заводских условиях технические качества улучшаются и за счет базового состава. Марки D500-D900 считаются конструкционно-теплоизоляционными, то есть пригодными и для обеспечения тепла в северных регионах, и для поддержания надежности в плане физических нагрузок. К слову, наиболее крепкие блоки способны выдерживать до 90 кг на 1 м2 – это марка D1200. Типоразмеры могут быть разными, но существует стандартизированный формат выпуска материала, который считается оптимальным. Это пеноблок 200х300х600 мм, который в зависимости от состава обеспечивает плотность стены от 300 до 1200 кг/м3. При этом водопоглощение стабильно составляет 14 %.
Технология изготовления литьем
На первом этапе выполняется подготовка самого раствора, которую можно производить в обычном строительном бункере с функцией автоматического замеса. Далее созданная смесь выливается в кассетные формы, где масса пенобетона принимает заданные физические параметры. Традиционные литьевые технологии предусматривают возможность дальнейшей вибрации и трамбования в формах, что улучшит качества блока. Однако в упрощенных кассетных формах данная функция отсутствует из-за недостатка электропривода, который мог бы обеспечить вибрационный эффект.
Более современные матрицы с опалубкой позволяют менять конфигурацию ячеек. То есть пользователь сам может настраивать толщину и длину блока в соответствии со своими запросами. Это также дает возможность создавать пеноблок с индивидуальными параметрами в единичных экземплярах – например, для кладки в сложных местах. Период полимеризации, то есть застывания, варьируется в среднем от 10 до 20 час. Это во многом зависит от того, какой использовался клей для пеноблоков – водостойкий, на силиконовой или полимерной основе. После базового укрепления структуры можно освобождать блоки от стен опалубки.
Оборудование для литья
Реализовать литьевой метод позволят три категории оборудования. В первую очередь это установки для создания пенобетонной смеси. Они отличаются от обычных бункеров тем, что имеют устройство для генерации пены. Средняя производительность такого агрегата составляет 20-30 м3 в сутки, опять же, она зависит от конкретного состава. На следующем этапе может использоваться мобильное оборудование для пеноблоков, которое облегчит задачу транспортировки смеси к формам. Это могут быть и самоходные машины с бункерами, и прямые стационарные каналы подачи раствора целенаправленно к матрице.
Относительно самих форм уже отмечалось, что они представляют собой матричные кассетные ячейки, в которые заливается смесь. В домашних условиях аналог такого приспособления можно изготовить из обычных металлических листов. Конструируется своего рода обрешетка, причем для нее не обязательно наличие дна – в процессе работы даже заводские конструкции часто ставятся на ровную поверхность, и этого хватает, чтобы получить геометрически правильный материал кладки. Другое дело, что технология изготовления пеноблоков литьевым способом также предусматривает возможность легкого и быстрого демонтажа формы после застывания раствора.
Технология изготовления резкой
Этот способ создания пеноблоков тоже предусматривает отдельные этапы приготовления и доставки смеси к непосредственному месту конечного формирования материала. Но в отличие от предыдущего метода предполагает другой подход к самой подготовке блоков. Они формируются не в ячейках матрицы, а путем механического разделения общего массива. То есть изначально также производится заливка, но не по отдельным матричным формам, а в общий поддон. Затем осуществляется раскрой вылитого раствора по секторам. Как именно будет выполняться эта операция – зависит от того, в каких условиях применяется резательная технология. Пеноблоки заводского типа на крупных предприятиях режутся лазерами и термическими головками. На малых и средних комбинатах это делается посредством пил, нитей и других механических резчиков, которые заслуживают отдельного внимания.
Оборудование для резки блоков
Профессиональное изготовление пеноблока не обходится без специальных линий резки, которые работают с монолитным бетоном. В плане режущего инструмента это очень разнообразное оборудование – могут использоваться ленточные резчики, струны, циркулярные пилы, металлические тросы и т. д. Базируется такое оборудование для пеноблоков на платформе или станине, предназначенной также и для размещения целевого материала. В процессе работы резчики проходят по монолиту, оставляя за собой полосы разделенных сегментов. Поперечное прохождение завершает операцию резки, оставляя уже готовые блоки.
У данного метода есть несколько преимуществ перед литьевым. В первую очередь обеспечивается точность формирования граней и сторон. Благодаря этому повышается и качество будущей укладки. К тому же, если формовка требует в некоторых случаях нанесения специальной смазки на края металлических ячеек, из-за чего страдает адгезия поверхностей блоков, то резка сохраняет шероховатость граней и тем самым улучшает их сцепку с другими инородными поверхностями. Кроме того, остается полная свобода в регуляции параметров, с которыми выпускаются пеноблоки. Размеры и вес изделий могут разниться: их выполняют и в стандартном формате 200х300х600 со средней массой 500 кг на 1 м2, и с индивидуальными характеристиками.
Технология выполнения распалубки
Этот способ по сути напоминает литьевой, но с большей долей автоматизации. Классическая формовка может полностью выполняться вручную с применением самодельных металлических ячеек. Автоматическая распалубка требует участия оператора только в процессе регуляции заливки в изначальные формы. Далее машина самостоятельно забирает формы на поддон и удерживает их в своем бункере (иногда с тепловым воздействием) до момента полного застывания. Такое производство пеноблоков в домашних условиях организовать затруднительно, поскольку оборудование может требовать подключения к сети в 380 В, но при наличии трехфазной линии – вполне возможно. Тем более что смесь также готовится сторонним образом без подключения специальных агрегатов. После застывания установка автоматически открывает бункер, выносит на поддоне форму с блоками и убирает опалубку.
Сушка блоков из пенобетона
В условиях поточного производства, когда нет времени на многочасовые и даже суточные ожидания полимеризации блоков, используют дополнительный технологический этап – термическую сушку. Для этого применяется специальная камера, в которую загружают пеноблоки. Строительные технологии по изготовлению кирпича в обязательном порядке предусматривают использование печей как средства обжига и укрепления. Пенобетон - менее плотный материал, поэтому без термического воздействия часто обходятся – но для экономии времени и укрепления структуры данный этап лишним не будет. По расчетам специалистов, печная пропарка за пару часов позволяет блоку набрать еще порядка 70 % от базовой прочности. Организационно данная технология изготовления пеноблоков возможна только на автоматизированных линиях. Машина должна автоматически управлять загрузочно-разгрузочными процессами, связанными с перемещением кассетных форм в печь.
Мини-заводы для создания пеноблоков
На небольших производствах в целях оптимизации часто используют небольшие линии изготовления, в которых компактно концентрируются функциональные площадки. Концепция мини-завода для пеноблока строится на тех же принципах. Оператору не нужно искусственно заполнять бреши между технологическими этапами – от начала до конца производство контролируется автоматикой. Начинается линия с бункера, в котором размешивается смесь для пенобетона. Оператор вносит в нее все необходимые компоненты с добавками и устанавливает программу приготовления строительной смеси. Далее раствор подается в емкость, которая сформирует прямоугольный монолит.
Типовой мини-завод по производству пеноблоков работает по методу нарезки блоков, так как изначально ориентируется на получение элементов с точными геометрическими размерами. После естественного или печного застывания монолит отправляется на этап автоматической резки, откуда уже в виде готовых блоков переправляется на пункт приема.
Заключение
Изготовление пенобетонного стройматериала гораздо проще, чем кирпича или панельных плит. Но так ли оправдывает себя этот материал на практике эксплуатации? Такие блоки отличаются небольшой массой, поэтому и прочность изначально будет несравнима с обычным кирпичом. Но есть и положительные свойства у ячеистого бетона. Даже упрощенная технология изготовления пеноблоков без специальных добавок позволяет добиваться высоких теплоизоляционных качеств. Поэтому даже при скромной массе и плотности такой блок может гарантировать оптимальный микроклимат. С точки зрения экологической безопасности это тоже неплохой вариант для строительства дома. Опять же, если обойтись без специальных модификаторов, то конструкция будет химически безопасна для жильцов.
Но главное достоинство пеноблока заключается в финансовой экономии. И технология изготовления, и логистика при строительстве и транспортировке требуют минимальных вложений по сравнению с альтернативными кладочными и панельными стройматериалами.
businessman.ru
Производство пеноблоков в домашних условиях
Рассматривается производство пеноблоков в домашних условиях обычно в тех случаях, когда приобретение готового строительного материала является нерентабельным. Самостоятельное производство – это значительная экономия финансовых средств и достижение своей заветной мечты – постройка собственного дома.
Быстро построить надежный и функциональный дом возможно с помощью пеноблоков, которые являются удобным для использования и выгодным по стоимости строительным материалом.
Процесс производства пеноблоков
Стандартные размеры пеноблока 60×60×25 сантиметров, а его вес примерно составляет 18 килограмм. Получается, что при таких приличных габаритах, пеноблок имеет небольшой вес и не оказывает серьезного давления в структуре стены на фундамент.
Но если вы планируете изготавливать пенобетонные блоки самостоятельно, тогда рассматриваются варианты с любыми габаритными размерами. Все будет зависеть от того, какую форму сделать для производства пенобетонных блоков.
Основные этапы производства пенобетонных блоков сразу следует выделить, потому что производителю предстоит:
- Приготовить цементную смесь,
- Приготовить раствор пенообразователя,
- Разлить пенобетонную смесь по формам,
- Дождаться полного застывания смеси.
Чтобы приготовить смесь цемента с песком, требуется использование бетономешалки, иначе процесс получится слишком трудоемким и невыгодным. Еще потребуется изготовление формы с такими габаритами, которые вам требуются для строительства дома.
Также нужно иметь в наличии пеногенератор с достаточными для обеспечения нужного количества пенной смеси техническими параметрами. Еще требуется наличие пенообразователя, отвердителя и места, где будет происходить процесс застывания. Кроме того, производство пеноблоков в домашних условиях будет успешным, если вам удастся правильно приготовить цементную смесь.
Оптимальное соотношение один к одному песка и цемента, также потребуется добавка в виде пенообразователя в количестве 4 грамма на 1 кг цемента.
Смесь для пенобетона
Для получения качественного пенобетонного блока лучше пользоваться портландцементом, и с песком тоже надо быть внимательнее, чтобы он был самой мелкой фракции. Даже к воде должны предъявляться особые требования, и в ней не должно быть повышенной концентрации солей.
Пенообразователем обычно пользуются синтетическим, который имеется в продаже, но если вы решили приготовить его самостоятельно, то необходимо воспользоваться:
- 1 кг канифоли,
- 60 граммами столярного клея,
- 150 граммами едкого натра.
Нужно измельчить смесь и подогреть ее при постоянном помешивании, чтобы получилось однородное вещество. Когда раствор готов, производство пеноблоков в домашних условиях можно продолжить и воспользоваться специальными формами.
Как производятся пенобетонные блоки
Для форм допускается использовать металлические листы или фанеру, но при этом нужно следить за размерами и прочностью, чтобы во время заливки форма не деформировалась и пенобетонные блоки не теряли свою геометрию.
Надо засыпать качественный цемент, чистый песок, добавить воду, и все это смешать с пенообразователем. Когда смесь будет готова, добавляется отвердитель, при этом процесс смешивания должен постоянно продолжаться.
Цемент с песком используется 1 к 3, пенообразователь добавляется в количестве 400 грамм, а объем отвердителя составит 200 грамм.
Формы перед заливкой готовой смеси необходимо тщательно смазать, чтобы затем было проще извлекать пенобетонные блоки. Если формы сделаны из фанеры, внутри необходимо использовать полиэтилен, чтобы фанерные листы не утратили свои свойства под воздействием влаги.
Когда форма высыхает, пенобетонный блок извлекается, и процедура подготовки формы и заливки повторяется. Чтобы готовые блоки не повредились, для них нужно определить удобное место – это может быть деревянный поддон.
Тем более что в дальнейшем пенобетонные блоки нужно будет транспортировать на строительную площадку.
Допускается использование цементного раствора с пенообразователем для монолитного строительства, для этого нужно изготовить опалубку из деревянных досок или из листового металла и выполнить заливку смеси.
Ускорить процессы высыхания пенобетонных блоков допускается с помощью хлористого кальция. Если нужно получить гладкую поверхность пенобетонных блоков, для смазки формы необходимо выбирать специальные вещества без содержания жира. Тогда конечный продукт достаточно обработать тонким финишным слоем или просто покрасить.
dom-data.ru
видео-инструкция по монтажу своими руками, фото
Рынок современных строительных технологий предполагает использование и современных материалов, и мы к одному из таких прогрессивных изделий можем с точностью отнести пеноблок, который прочно занял достойную позицию в области возведения малоэтажных строений.
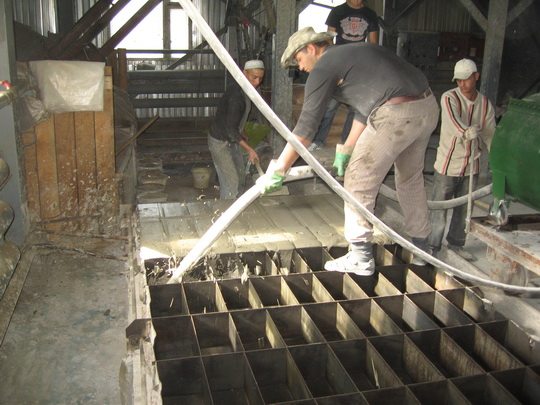
Фото изготовления пеноблоков
Реклама
Пеноблок для разных работ в строительстве
Понятно, что для того, чтобы составить конкуренцию таким материалам, как кирпич или древесина, пеноблочный стеновой камень должен предоставить такие свойства, которые не будут отставать от характеристик обозначенных конкурентов, а в некоторых случаях и преобладать.
Это сказано к тому, что производители пеноблоков именно так ориентируются в производстве и разработки своего изделия.
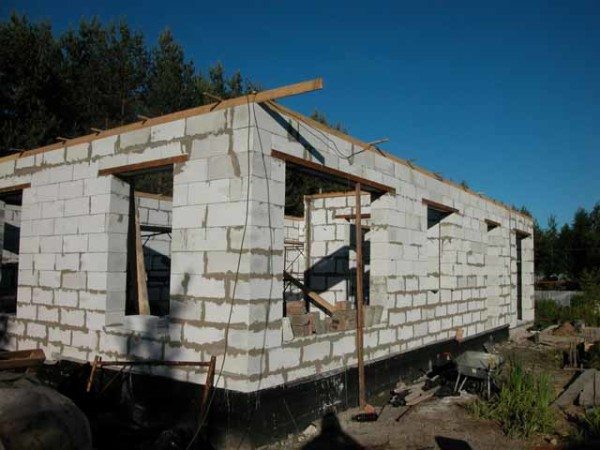
Несущие конструкции из пенобетона
Итак, что нам может предложить это изделие?
Пеноблок, что это
Среди многих определений выберем наиболее точное и простое, и определим, что наш материал — это разновидность ячеистого бетона, а точнее пенобетона.
В производстве принимает участие:
- Любой тип песка.
- Вода.
- Цемент, в зависимости от необходимой прочности изделия, разных марок.
- И специальный пенообразователь.
Важно!Кстати, именно пенообразователь оказывает влияние на образование мелких пор в материале, что и делает его столь особенным!
Область применения
Как мы уже успели сказать, применяется данный материал преимущественно в малоэтажном строительстве. Пенобетон, при всех плюсах, не обладает высокими показателями прочности и плотности, а поэтому строить из него можно максимум частный дом в три этажа.
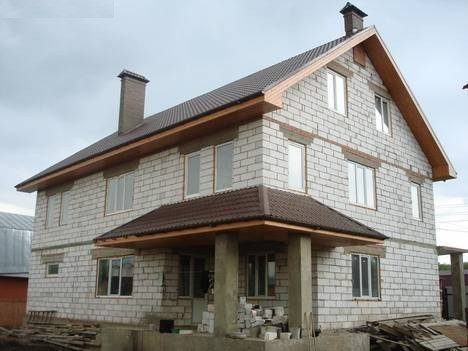
Пеноблочный дом
Тем не менее, мы можем применять изделие в следующих конструкциях и работах:
- В возведении несущих стен в жилом доме, высотой до трех этажей.
- В строительстве межкомнатных перегородок.
- В строительстве нежилых построек, гаражей из пеноблока, бань, сараев.
- В устройстве чернового пола, в качестве утеплителя.
- В строительстве заборов.
Как видим, сферы использования масштабные и в малоэтажном строительстве наш стеновой камень можно найти везде. Соответственно, можно начинать разговор и о его свойствах.
Габариты
Здесь мы остановимся более подробно, так как пеноблоки от производителя обладают действительно большим количеством положительных качеств и минимальным количеством минусов.
Сначала о характеристиках и габаритах. Стандартные или, правильнее будет сказать, наиболее распространенные размеры — 200х300х600 мм. С такими габаритами легко и удобно работать и кладка получается идеальной.
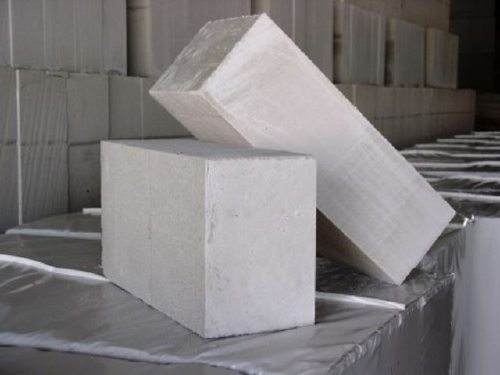
Идеальные габариты
Есть и другие габариты, они не так часто используются, но, к примеру, для простенков могут применяться 100х300х600 мм или 80х300х600 мм. Этого вполне хватает для межкомнатной перегородки.
Важно!В межкомнатных перегородках большое внимание всегда уделяется звукоизоляции, а благодаря высокому количеству пор, и воздуха в них, пеноблочное изделие способно достаточно хорошо «гасить» звук.
Помимо выше обозначенных габаритов, пеноблок от производителя может встречаться в размере 200х400х600 мм, однако и этот более «укрупненный» вариант позволяет быстрее вести кладку и даже сокращает расход клея для пеноблоков.
Свойства
Мы начинали наш разговор с того, что определили конкурентную борьбу с кирпичом и древесиной, а это полностью натуральные компоненты и, чтобы с ними конкурировать пенобетон также должен быть экологически безопасным.
Поэтому вынесем это его свойство на первое место, и продолжим:
- Прочность. Даже, если учесть, что мы говорим о низкой прочности, ее показатели могут быть и на уровне М 150, а это вполне подходит под прочность стандартного красного кирпича. Так что можно не переживать, стены из пеноблочного камня не подведут!
- Гигроскопичность. Это свойство особенно интересно для поддержания здоровой атмосферы в помещениях, ведь связано оно с поглощением водяного пара и выведением его наружу. Соответственно, пеноблочный дом всегда будет обладать свежим воздухом.
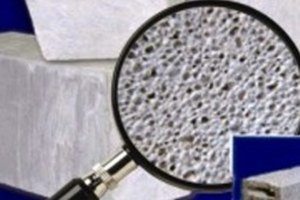
Структура пенобетона
- Низкая плотность. Если сравнивать с древесиной, то пенобетон не сильно плотнее дерева, а это позволяет нам с легкостью работать с ним.
- Теплоизоляционные показатели. Здесь очень все интересно, пенобетон в разы превосходит стандартный глиняный кирпич, и практически ничем не уступает дереву. Соответственно, это полностью изменяет подход к утеплению дома из пеноблоков и к разработке и внедрению системы отопления.
- Влагостойкость. Инструкция по использованию изделия утверждает, что цельный пенобетонный камень не имеет практически ни одной открытой поры, а соответственно у него очень высокое сопротивление воде.
- Морозостойкость. И здесь также вся «соль» в порах. Мелкие проходы в теле пенобетона оставляют воде, которая в нем скапливается из водяного пара, место для маневра при замерзании. Таким образом, не происходит расширение материала.
- Пожаробезопасность. Раз уж мы иногда сравниваем стеновой камень с древесиной, то здесь мы просто победители, пенобетон не горит, не плавится при температуре и не выделяет вредных, ядовитых соединений!
- Однородность. В силу того, что в нем нет пустот, мы можем спокойно проводить различные работы, связанные со сверлением или штроблением.
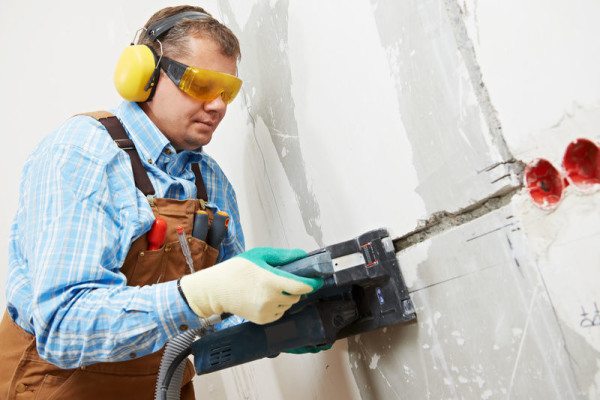
Штробление пеноблочной стены
Получается, что это идеальный материал, с которым мы работаем своими руками, к слову говоря, и практически не видим минусов! Так и есть, ведь за исключением низкой плотности, минусов-то и не отыскать.
Важно!Отношение к плотности как к некому минусу — достаточно относительное, ведь это заставляет нас просто использовать другие типы креплений, и проблема решена.На основные направления в малоэтажном строительстве плотность не влияет.
Вывод
Достаточно привлекательная цена изделия, простота в работе, вариативность и просто огромная область использования – все это делает пеноблок действительно привлекательным строительным продуктом.
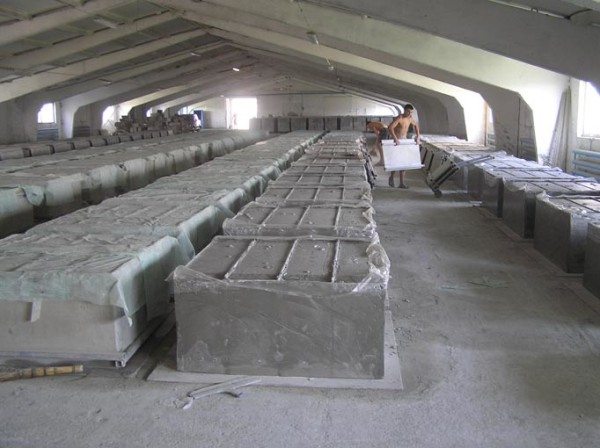
Этот продукт позволяет говорить о достаточно высоком качестве строительства с его использованием
Соответственно, многие выбирают именно пеноблочный камень, потому как это рационально и удобно, финансово привлекательно и отвечает всем требованиям современного малоэтажного строительства.
А главное, с пенобетоном любой строитель справится самостоятельно. И в представленном видео в этой статье вы найдете дополнительную информацию по данной теме.
openoblokah.ru
Изготовление пеноблоков своими руками
Изготовление пеноблоков, спрос на которые неизменно высок, на сегодняшний день имеет рентабельность 300% и выше. Организация производства пеноблоков не требует огромных материальных затрат
Изготовление пеноблоков своими руками
Минимальный комплект необходимого оборудования, которое потребуется на начальном этапе для изготовления пеноблоков своими руками, включает в себя формы для производства пеноблоков или разъемную опалубку, пеногенератор, компрессор, растворомешалку емкостью 80-100 литров. При подобном оснащении два работника за смену смогут изготавливать 2-3 кубометра пенобетона.
Смеситель должен быть снабжен поворотным механизмом, компрессор, если нет возможности трехфазного подключения, должен работать от сети 220V. Пеногенератор для производства пеноблоков разумней изготовить своими руками, поскольку фабричные пеногенераторы для начинающего предпринимателя неподъемно дороги, а пенообразующие компоненты, продающиеся в торговой сети, пены образуют в десяток раз меньше, чем пеногенератор, да и бетон для образования пены с помощью этих компонентов требуется взбивать на очень высоких оборотах.
Для изготовления пеногенератора потребуется корпус с металлической сеткой, емкость, насос, шланги и компрессор. Принцип работы следующий: пенообразователь в емкости перемешивается с водой, потом смесь, одновременно с воздухом от компрессора, поступает в корпус пеногенератора. Перемешанный с воздухом раствор, ударяясь о сетку, преобразуется в пену. Подробно об изготовлении своими руками простого и надежного пеногенератора для производства пенобетона я написал здесь.
Качество пены проверяется следующим образом: ею наполняют ведро и переворачивают вверх дном. Пена должна удержаться внутри. Оптимальной считается плотность пены, соответствующая примерно 80 граммам на 1 литр. Можно получить пену и гораздо меньшей плотности – до 10 граммов на литр, но такая пена для производства пеноблоков непригодна - она разрушится очень быстро.
Для изготовления пеноблоков применяют цемент марки не менее 400, не допускается присутствие примесей. Для бетонов с плотностью 300-500 кг/м3 (теплоизоляционных) песок не применяют. При производстве бетонов с плотностью 600 кг/м3 и выше добавляют природный или дробленый песок. При изготовлении пеноблоков своими руками предпочтительней применять отсев, поскольку активность отсева в бетоне значительно выше, а стоит он намного дешевле. На себестоимость пеноблоков существенное влияние оказывают фракции песка: при наличии крупных песчинок, для удержания раствора во вспененном состоянии потребуется дополнительно добавлять цемент.
Исходя из требований к марке бетона, компоненты загружают в смеситель. Вначале смешиваются цемент, песок и вода, а потом добавляется пена. Бетон для изготовления пеноблоков получится тем выше качеством, чем быстрее перемешаются все компоненты.
В вертикальном смесителе, предназначенном для приготовления обычного бетона, перемешивание пенобетона будет занимать порядка 20 минут в силу того, что пена будет долго держаться на поверхности. В обычной бочке с подвижными лопастями пену можно перемешать за пару минут. При помощи сжатого воздуха бетон из смесителя возможно подать на расстояние в несколько десятков метров.
Изготовление пеноблоков своими руками возможно одним из двух способов: либо бетон заливают в готовые формы для производства пеноблоков, либо заливают в опалубку, а затем, не дожидаясь полного застывания, разрезают на блоки. Форму следует изготавливать разборной – с откидными бортами и перегородками, извлекаемыми после готовности пеноблоков.
Формы разбирают не ранее, чем через сутки после заливки. Уложенные на поддоны пеноблоки перед отправкой на склад или реализацию требуют выдержки еще не менее 16 часов. Температуру в производственном помещении необходимо выдерживать не ниже +5 градусов по Цельсию.

znay-i-umey.ru
Технология производства и изготовления пеноблоков
Производство пенобетонных блоков состоит из нескольких основных стадий, таких как: затворение пенобетонной смеси, формовка, сушка, распалубка, распиловка, термообработка, упаковка, складирование и так далее. В зависимости от выбора технологии изготовления пеноблоков и имеющегося оборудования, производители используют различные комбинации и варианты перечисленных стадий. Начнем по порядку.
Производство пенобетонной смеси
Современное производство пенобетонной смеси можно поделить на два основных вида: баротехнология и получение пенобетона с помощью пеногенератора. Каждая из технологий имеет свои плюсы и минусы. Первая более проста и экономична. Вторая более затратна, но позволяет получать пенобетон более высокого качества. Более подробно об плюсах и минусах этих двух технологий Вы можете прочитать в разделе производство пенобетона.
Формовка пеноблоков
На сегодняшний момент существует две основных технологии получения готовых пенобетонных блоков: литьевая и резательная.
Литьевая технология Литьевой способ производства пеноблоков очень похож на классическое изготовление изделий из железобетона, при котором готовая бетонная смесь отливается в металлическую форм-оснастку, сушится до набора необходимой прочности и затем вынимается из форм уже в виде готового изделия.
При производстве пеноблоков по литьевой технологии используются кассетные формы, представляющие из себя металлический поддон со съемными бортами и переборками, делящими форму на несколько отдельных секций. Похожая кассетная форма для приготовления льда лежит у Вас в холодильнике. Почти такая же применяется и на производстве пенобетонных блоков, только из металла, разборная и размером побольше. Чаще всего используются кассетные формы высотой 600 мм.
Главными минусами литьевой технологии являются:
- Неудовлетворительная геометрия готовых пеноблоков. То есть, габариты пенобетонных блоков по высоте, длине и ширине "пляшут". Происходит это из-за смещения металлических переборок при заливке пенобетонной смеси в кассету. Как правило, переборки сделаны из тонкого металла и при неравномерной заливке они могут смещаться, деформироваться и т.д.
Конечно же существуют качественные блок-формы, с переборками из толстой листовой стали, отлично подогнанные по размерам. Но такие формы дороги, и многочисленные кустари используют дешевые покупные или самодельные формы. Более подробно о возможных проблемах с геометрией изделий из пенобетона читайте в разделе размеры пеноблоков.
- Наличие так называемой "горбушки". Горбушка образовывается в верхнем слое залитой кассеты. Для примера вспомните кубики льда из холодильника, верхняя часть которых имеет неровную поверхность. Аналогично образуется неровность и на поверхности застывшего пенобетона. Многие наверное помнят верхнюю часть плит перекрытий и тому подобных железобетонных изделий, у которых все стороны ровные кроме одной - верхней, которая не "обжимается" опалубкой. Горбушку на пеноблоках, изготовленных по литьевой технологии, почти всегда можно обнаружить на одном из торцов.
- Необходимость использования специализированных переборок для кассет, заточенных под конкретный размер пеноблоков. Для того, чтобы выпускать три-четыре размера пенобетонных блоков, производители должны иметь несколько видов переборок с разными размерами ячеек.
- При распалубке кассет происходит частичное повреждение углов и поверхностей готовых блоков. Происходит это из-за прилипания пенобетона к стенкам кассеты, так как к моменту распалубки пенобетон не успевает набрать достаточной прочности. Время-деньги. Нужно побыстрее вынуть едва вставшие блоки, чтобы залить очередную партию.
Отчасти повреждение готовых блоков при распалубке происходит из-за некачественной смазки блок-формы перед заливкой. По технологии полагается применять специальные смазки, которые стоят определенных денег. В условиях тотальной экономии на всем, для смазывания форм-оснастки производители зачастую используют отработку и прочую масляную дрянь, которую можно смело назвать ложкой дегтя в нашей бочке пенобетонного меда, потому как даже тяжелые бетоны имеют низкую стойкость к разрущающему действию машинных масел.
Из плюсов литьевой технологии производства пенобетонных блоков можно выделить лишь экономическую выгоду для производителя: отсутствие необходимости приобретения дорогостоящего резального оборудования и простота процесса. Впрочем, для конечного потребителя это преимущество не имеет никакого значения.
Резательная технология Подобный способ производства пеноблоков состоит из двух ступеней: отливка массива пенобетона в большую форму и его распалубка с дальнейшей резкой на блоки заданного размера. Происходит это на специальных резательных установках. В различных типах резательных установок используются разные виды режущих элементов. Это могут быть специальные струны, ленточные и цепные пилы.
Эта технология производства пенобетонных блоков обладает целым рядом преимуществ. Вот основные из них:
- Великолепная геометрия поверхностей получаемых пеноблоков, соответствующая требованиям ГОСТ 21520-89. Благодаря этому, блоки можно монтировать на клей с минимальной толщиной шва.
- На гранях и углах пеноблоков отсутствуют сколы и неровности. Этот нюанс особенно важен для сокращения расходов и трудозатрат при дальнейшей отделке стен.
- За счет отсутствия на поверхностях блоков остатков смазки (а тем более масляной обработки) которой смазываются формы-кассеты, готовые стеновые блоки обладают хорошей адгезией и привлекательным внешним видом. И если внешние данные не столь важны, то хорошая адгезия пеноблока - один из важнейших критериев успешного оштукатуривания или шпатлевания стены при проведении внешней и внутренней отделки дома.
- Возможность изготовления пеноблоков произвольных размеров. Перенастройка шага пильных струн позволяет нарезать готовые блоки по размерам заказчика.
- Благодаря обрезке массива пенобетона со всех сторон, решается и проблема с пресловутой "горбушкой" на торце блока. Она просто срезается.
Впрочем, есть у резательной технологии и свои неприятные моменты. При использовании разных видов режущих элементов должны быть четко соблюдены определенные требования к своевременности проведения резки. При резке струнами важно поймать момент, когда пенобетон уже встал, но ещё не набрал "лишней" прочности. Если этот момент прозевать, при проведении разрезки массива, струна может смещаться, уходить, что отрицательно скажется на окончательной ровности блока.
При разрезке пенобетона ленточными пилами массив наоборот должен иметь более высокую прочность, так как при резке он кантуется (переворачивается на резальном столе). И если прочность будет недостаточной, он просто будет ломаться при кантовании.
Перечисленные проблемы скорее досаждают производителям пенобетонных блоков, нежели их конечным потребителям. В любом случае, Ваша главная задача - сделать правильный выбор.
Сушка пеноблоков и набор прочности
При производстве блоков из пенобетона литьевым способом возможны две технологии первоначальной сушки изделий. Первый вариант - естественная сушка, подразумевающая 10 часовой набор прочности пенобетона в форме и его дальнейшая распалубка. Второй вариант - термическая обработка пенобетонных блоков в пропарочной камере. В отличие от естественной сушки, пропарка в камере позволяет пенобетону за несколько часов набрать 65-75% расчетной прочности.
Стоит заметить, что по подобной технологии производятся почти все железобетонные изделия. Группа BESTO поставляет пеноблоки, произведенные с применением термо-влажностной обработки в пропарочных камерах. Производство пеноблоков расположено на территории завода ЖБИ-16 в Москве.
Резательная технология производства пенобетонных блоков подразумевает естественную сушку массива в течение 4-14 часов с дальнейшей его разрезкой. Время сушки перед разрезкой зависит от использования того или иного вида режущих элементов (струны, ленточные пилы, цепи), а так же ускорителей твердения, добавляемых в пенобетонную смесь при затворении.
www.avtobeton.ru