Ядерная лава способна расплавить почти любой материал. Температура плавления бетона
» Ядерная лава способна расплавить почти любой материал
Результаты эксперимента с кориумной лавой
Самое интересное в научных исследованиях – это сделать открытие совсем не в той сфере, в которой работал. Таким открытием является радиоактивная лава, опасность которой обнаружилась при исследовании аварий на Чернобыльской АЭС и на Фукусиме.Казалось бы, какая вообще может быть связь между лавой и ядерной энергетикой? Тем не менее, эта связь есть. Не с искусственной лавой, которую люди производят, преимущественно, ради искусства, а с той радиоактивной субстанцией, при встрече с которой можно смело прощаться с жизнью. Происхождение такой лавы преимущественно случайно и последствия её появления исключительно трагические.
Чтобы понять, о чём идёт речь, необходимо вернуться к атомным электростанциям. Объектом нашего внимания является ни что иное как расплавление ядерных топливных элементов реактора. Это происходит, когда реакции расщепления ядра, происходящей в реакторе, становится невозможно обеспечить должное охлаждение и начинает нагреваться всё, включая урановый стержень и бетонный пол самого здания АЭС. Во время катастрофы, такой, как в Чернобыле или на Фукусиме, становится невозможным охлаждение урановых стержней, и жар начинает с высокой скоростью распространяться по станции. Два наиболее важных первичных изотопа, которые используются в реакции расщепления ядра, это уран-235 и плутоний-239. Расщепление становится возможным с помощью поглощения нейтроном изотопов с ещё более коротким периодом полураспада (таких как цезий и стронций), и, собственно, является источником тепла и самой сущностью работы ядерного реактора. Цепная реакция расщепления, разложения и поглощения разъединённых альфа-частиц другими атомами может продолжаться бесконечно; нагрев будет происходить до точки, на которой урановые стержни (сделаны оны преимущественно из обогащённого урана) начнут деформироваться, а если температура поднимется ещё выше — плавиться. Обычно ядерный реактор охлаждается водой, но в непредвиденных обстоятельствах стержни расплавятся полностью, превратившись в лаву.
Разумеется, такая искусственная лава отличается по составу от природной вулканической субстанции. Урановые стержни состоят из циркониевого корпуса и ядерного топлива — диоксида урана — внутри. В случае аварии на АЭС, когда температура превышает максимальный допустимый лимит в 700 градусов, стержень начинает деформироваться. Когда же температура достигает отметки в 1200 градусов, урановые стержни плавятся, превращаясь в субстанцию, состоящую из урана и циркония.
Для того, чтобы сделать ядерный реактор безопаснее, необходимо изучить, как ведёт себя кориум, то есть, смесь, состоящая из ядерного топлива и расплавленных соседствующих материалов. Исследователи из Аргоннской Национальной лаборатории воссоздали кориум для более детального его изучения. В Интернете можно найти великолепные видеоролики, выложенные в сеть именно этой лабораторией. На этих видео можно заметить, что кориум обладает ещё более низкой вязкостью, что неудивительно, ведь температура этой радиоактивной жижи – свыше 2000 градусов, в то время как вулканический расплавленный базальт нагрет в лучшем случае до 1100-1200 градусов. Лаборатория использовала больше тонны лавы из диоксида урана в некоторых своих экспериментах, чтобы узнать, как быстро кориум прорвётся через такую преграду, как бетонные пол и стены ядерного реактора. Оказалось, очень быстро: кориум проплавляет себе путь сквозь бетон со скоростью около 30 см в час. Кроме того, экспериментальным путём исследователи убедились, что охлаждения водой может быть недостаточно: кориум, уничтожая все на своё пути, вырвется наружу в считанные часы.
Обе катастрофы на ядерных электростанциях достигли стадии образования кориума. И Чернобыль, и Фукусима столкнулись с этим явлением. В то время как японцы утверждают, что лава не вышла за пределы здания АЭС (этот факт, кстати, не доказан), на советской электростанции, несомненно, контроль над ситуацией был потерян полностью. Существуют фотографии из Чернобыля, на которых видны трёхметровые потёки застывшего кориума. К счастью, температура плавления бетона, состоящего в основном из известняка, выше температуры плавления урановых стержней, в итоге сам процесс плавления бетона и смешивания его с лавой, охлаждает кориум. Поэтому так много внимания уделяется поиску оптимального состава бетона для постройки ядерных реакторов.
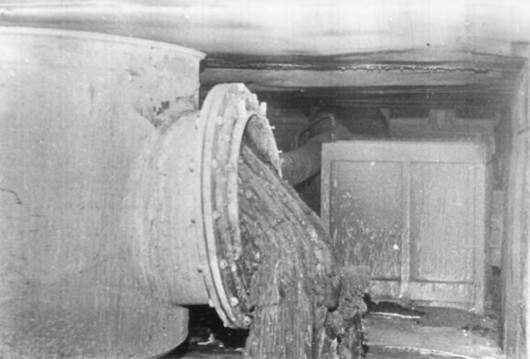
Почему же тогда кориум так опасен? Ведь дальше трех метров за пределы реактора лава продвинуться не в состоянии? Не следует забывать о составе этой субстанции. Даже когда кориум совершенно застынет, он будет очень и очень радиоактивен еще многие столетия.
Измерения радиоактивности и газов, выделяющихся из охлаждённого реактора Фукусимы, показали, что кориум во время катастрофы продвинулся более чем на полметра через заграждающие бетонные стены.
На самом деле стадия образования кориума – явление очень редкое, оно возникает только при условии цепной реакции чрезмерного количества высокоактивных изотопов. Впрочем, существуют теории, что в далеком прошлом на нашей планете имелись естественные ядерные реакторы, которые нагревали Землю за счет расщепления урана, тория и калия.
ПОХОЖИЕ ЗАПИСИ
© Gearmix 2013 Права на опубликованный перевод принадлежат владельцам вебсайта gearmix.ru Все графические изображения, использованные при оформлении статьи принадлежат их владельцам. Знак охраны авторского права распространяется только на текст статьи. Использование материалов сайта без активной индексируемой ссылки на источник запрещено.
gearmix.ru
особенности проведения работ в экстремальных внешних условиях
Для того чтобы отлитый бетонный монолит приобрел прочность, соответствующую его марке, необходимо точно соблюдать технологию заливки, в том числе процедуру гидратации бетона. Наилучшими условиями для этого процесса является среда со средней влажностью воздуха и температурой + 20 оС.
Но что делать, если необходимо проводить строительные работы в холодный сезон? Что гласит строительная инструкция по бетонированию о работе при слишком жаркой погоде? Рассмотрим эти вопросы более подробно.
Заливка бетона зимой требует соблюдения особых температурных условий
Оптимальные условия для бетонирования
Согласно ГОСТ на температуру бетонной смеси, этот показатель должен составлять + 30 оС. Но такого удается достичь лишь только в том случае, когда столбик термометра находится около отметки в + 20 оС.
Совершенно другая ситуация возникает поздней осенью и зимой, когда ртуть в термометре опускается до показателей от + 5 оС до — 3 оС.
В этом случае температура бетонной смеси на выходе из бетоносмесителя может составлять:
- при объеме цемента в бетонной смеси более 240 кг/куб. метр (марка бетона М200 и выше) – не менее + 5 оС;
- во всех остальных случаях – не менее + 10 оС.
Температура подаваемой после транспортировки смеси должна соответствовать СНИП
В наиболее экстремальных условиях, когда воздух охлаждается до отметки -3 оС допускается проведение работ только в том случае, когда свежеприготовленный бетонный раствор вызревал не менее 3 суток при внутренней температуре не менее + 10 оС. Иначе отлитая бетонная конструкция не будет соответствовать требованиям СНИП по прочности.
Совет!Если вы проводите строительство частного дома или иного сооружения своими руками, воздержитесь от бетонирования при температуре ниже -3 оС.Этот процесс требует применения специального оборудования и четкого соблюдения технологии, чего тяжело достичь в домашних условиях.
Бетонные работы в экстремальных условиях
Низкие температуры
Особенность работы в таких условиях состоит в том, что бетон при низких температурах схватывается медленнее. Для набора прочности, указанной в нормативной документации, монолиту необходимо больше времени.
Например:
- При показаниях термометра в течение суток около + 5 оС готовая конструкция застывает в два раза больше, чем в обычных условиях.
- Когда воздух на стройплощадке остывает до 0 оС, процесс затвердевания и набора прочности практически прекращается.
- Если только что уложенная бетонная смесь замерзает (что происходит при несоблюдении технологии ее изготовления или перевозки), монолит может полностью разрушиться.
Разрушение бетона вследствие замерзания в нем воды
Содержащаяся в растворе вода при отрицательных температурах кристаллизуется, вследствие чего в бетоне образуются пустоты и поры, снижающие прочность бетонного изделия. Кроме того, лед оказывает повышенное давление на стенки бетонной конструкции.
В готовом монолите могут образоваться трещины и расколы. Кроме того, замерзшая вода разрывает связи между цементом и заполнителем бетона (щебнем, гравием и так далее).
Созревание бетона при низких температурах должно завершиться до момента замерзания.
В противном случае появляется сразу два негативных момента:
- готовая конструкция не сможет набрать прочность, предусмотренную маркой бетонной смеси;
- после оттаивания затвердевание будет происходить неправильно, существует возможность разрушения.
Для того чтобы продолжать работы в холодное время года, необходимо пользоваться специальными марками бетона и соответствующими добавками. Они не только улучшат качество монолита, но и позволяет сократить время застывания.
Рассмотрим таблицу, составленную согласно СНИП 3.03.01-87, которая показывает время затвердевания различных марок бетона в зависимости от температуры окружающего воздуха.
Марка Прочность Кол-во дней при температуре +5 оС Кол-во дней при температуре +10 оС Бетон с добавками 20 4 3 М400 30 6 4 M150 –М350 40 9 6 М100 50 14 10 Бетон в водонасыщенном состоянии 70 25 20Повысить качество бетона в холодный сезон можно следующими способами:
- при производстве бетона использовать цемент, способствующий быстрому набору прочности готовым монолитом;
- повышать процентное содержание цемента в готовой строительной смеси;
- снижать количество воды, добавляемой в раствор;
- производить предварительный подогрев сырья (до +35 оС) и воды (до +70 оС) – это требование регламентировано СНиП 3.03.01-87;
- использовать противоморозные добавки для бетона (их цена невелика, потому не слишком увеличивает сметную стоимость строительства).
Фото затвердевающего бетона в фундаменте после заливки
Высокие температуры
После окончания укладки бетона на строительной площадке, вследствие воздействия воды на цементный порошок, начинается затвердевание раствора. Жаркая погода ускоряет этот процесс. Однако если этот показатель поднимается выше отметки в +25оС (температура высыхания бетона), происходит расширение строительной смеси, которое фиксируется после окончания процесса затвердевания.
Позже, после остывания, бетонный монолит начинает сжиматься, чему препятствует возникшая твердая структура. Как результат – появление усадочных трещин и деформация. Этот процесс может продолжаться вплоть до 12-16 часов, что крайне отрицательно сказывается на прочности.
Полиэтилен препятствует преждевременному испарению влаги из бетона
Если прогноз погоды в месте проведения строительных работ указывает на повышение температуры воздуха выше +25 оС в течение нескольких последующих дней, необходимо немного изменить состав бетонирующей смеси.
Для этого необходимо:
- использовать быстротвердеющий цемент, марка которого в 1,5-2 раза превышает рекомендованную;
- добавлять в готовый раствор пластифицирующие добавки или вещества, замедляющие процесс твердения;
- работать в утреннее, вечернее и ночное время, когда температура воздуха не поднимается выше + 20 оС.
Совет!При проведении работ в жаркое время, целесообразно защищать свежий бетон от воздействия ветра и прямых солнечных лучей.Кроме того, рекомендуется увлажнять поверхность, способствуя правильной гидратации.
Поведение бетона при воздействии открытого огня
Рассматриваемый строительный материал является чрезвычайно огнеупорным, что стало одним из многих факторов, способствующих его популярности. Температура плавления бетона, например, составляет около + 1200 оС (в зависимости от марки и заполнителя).
Кроме того, внешний вид бетонных конструкций при пожаре помогает определить температуру пламени и выбрать подходящий способ тушения пожара:
- Температура около + 300 оС – искусственный камень приобретает розоватый оттенок, происходит оседание на поверхность значительного слоя сажи и продуктов горения.
- Температура от +400 оС до + 600 оС – бетон приобретает красный оттенок, сажа выгорает с поверхности монолита.
- Более высокая температура – конструкция становится бледно-серой.
Разрушение бетона при горении носит, как правило, спокойный характер. Коэффициент расширения входящих в него наполнителей находится в широком диапазоне, вследствие чего сцепление щебня или гравия с цементным порошком разрушается постепенно, начиная с отметки в +300 оС.
Бетон – очень огнестойкий материал
Если нагрев продолжается, в структуре монолита возникают трещины, которые постепенно расширяются вплоть до потери конструкцией целостности.
Вывод
В качестве итога следует отметить, что застывание бетонной строительной смеси при отрицательной либо слишком высокой температуре воздуха должно проходить под строгим контролем. Необходимо постоянно снимать температурные показатели поверхности монолита и корректировать их с помощью описанных выше способов.
Более подробно о процессах, связанных с заливкой и затвердеванием бетона можно узнать, ознакомившись с видео в этой статье.
rusbetonplus.ru
Виды термической резки бетона и железобетона

Категория:
Термическая резка

Бетон и железобетон режутся кислородным, прутково-кислород-ым, порошково-кислородным копьем, газопорошковой реактивной ггруей, порошково-кислородным резаком, плазменной струей и дугой косвенного действия.
Наиболее освоенной и широко применяемой в СССР является кзка железобетона кислородным копьем (рис. 1).
Копье представляет собой стальную трубку с наружным диаметром 10—60 мм и длиной 3—6 м с различным поперечным сечением, расто употребляются водогазопроводные трубы (ГОСТ 3262—75) F наружным диаметром 10,2 мм и более. Согласно стандарту водогазопроводные трубы подразделяются на легкие, обыкновенные и усиленные.
Для прожигания отверстий в бетоне целесообразно пользоваться усиленными трубами с увеличенной толщиной стенки. Для копья можно использовать трубки некруглых сечений: плоскоовальные (ГОСТ 8644—68), прямоугольные (ГОСТ 8645—68), звездообразные, крестообразные, каплевидные, ромбические и др. Возможно также применение трубки с заложенными внутрь прутками или обмотанной снаружи проволокой из низкоуглеродистой стали. Такое копье называют прутковым.
Рис. 1. Резка железобетона прутковым копьем: а — процесс резки, б — копье с сердечником из прутков, б — копье с тремя прихваченными наружными прутками, г — копье с проволочной навивкой; д — копье с сердечником из прутков и с проволочной наьивкой; 1 — трубка, 2 — пруток, 3 — проволочная навивка
Для зажигания копья в трубку подается кислород под давлением 0,5 кгс/см2. При этом рабочий торец копья нагревается сварочной дугой или газокислородным пламенем до температуры горения стали; время нагрева—5—10 с. Нагретый металл начинает окисляться (гореть), давление подаваемого кислорода повышается до рабочего, металл на конце трубы интенсивно горит, развивая температуру до 2000 °С.
Следует различать горение копья в свободном состоянии и горение копья в процессе прожигания или резки. Расход кислорода при свободном горении копья значительно меньше, чем при резке, поэтому и подача его соответственно должна меняться.
Ориентировочно для сгорания 1 кг низкоуглеродистой стали требуется 300 дм3 кислорода. Фактический расход кислорода при свободном горении копья составляет до 600 дм3 в зависимости от диаметра и толщины стенки трубки, диаметров стержней и их количества. Чем полнее обтекает кислородная струя торец копья, тем меньше затрачивается кислорода при свободном горении.
При прожигании бетона или железобетона копье с пламенем направляется в изделие с определенной силой. Под действием высокой температуры пламени копья и продольной силы, создаваемой резчиком, бетон плавится и разрушается.
При резке или прожигании железобетона копьем кислород расходуется не только на горение стали, но и на выдувание из области реза продуктов горения копья и плавления бетона.
При давлении кислорода в момент зажигания копья более 0,5 ат нагреваемый металл будет охлаждаться из-за сильного перепада давления, что затруднит зажигание копья. Только после воспламенения копья и достаточного углубления его в бетон давление кислорода повышают до рабочего.
В процессе прожигания копье прижимают горящим концом к бетону с достаточно большим усилием; углубляясь в бетон, оно образует приблизительно круглое отверстие. Вследствие испарения воды, а также из-за разности температурных деформаций цементного камня и зерен заполнителя бетон становится непрочным, в нем возникают трещины, рыхлость, выкрашивание частиц, что облегчает плавление и отрыв нерасплавленных частиц. Расплавленные и оторвавшиеся частицы бетона, продукты горения стали выдуваются наружу кислородом и парами, образуемыми при нагреве бетона, через зазор между копьем и стенками прожигаемого отверстия. Для лучшего удаления расплавленной и рыхлой массы из области реза необходимо периодически совершать копьем возвратно-поступательные и возвратно-вращательные движения. Величина продольного усилия должна быть максимально возможной для резчика. В то же время чрезмерное усилие, в особенности при большой толщине железобетона, когда нагретое докрасна копье на 1—2 м и более углублено в железобетон, может вызвать искривление копья и изменить направление образуемого отверстия. Ориентировочно величина усилия прижатия копья должна составлять от 5 до 10 кгс, а при прожигании глубоких отверстий, когда необходимо преодолевать сопротивление застывающих шлаков, усилие прижатия должно достигать 10—50 кгс.
Данные по прожиганию отверстий в железобетоне в горизонтальном положении, полученные в МИСИ, приведены в табл. 30 и 31.
Копьем размером 10X8 мм с сердечником из 8 прутков диаметром 2 мм можно прожигать отверстия в бетоне со скоростью 5 м/ч на глубину до 200 мм. С повышением толщины прожигаемого бетона диаметры трубы и прутков необходимо увеличивать.
При прожигании отверстий кислородным копьем изменение свойств и снижение прочности бетона от нагрева происходят в радиусе 30—200 мм пропорционально толщине прожигаемого бетона.
Скорость прожигания отверстий прутковым копьем в потолочном положении достигает 10 м/ч.
По сравнению с пневмоинструментом копье прожигает отверстие более чем в 4 раза быстрее, стоимость работ при этом значительно ниже.
Порошковое копье отличается от пруткового тем, что на место реза подается железный порошок или смесь его с каким-либо другим (например, алюминиевым), при сгорании порошка выделяется дополнительное тепло. Подача порошка (флюса) выполняется автоматизированным устройством, как в установках для кислородно-флюсовой резки. Это усложняет оборудование для резки порошковым копьем.
Резак для кислородно-флюсовой резки сталей может быть использован и для резки неметаллов. Однако пользоваться им удобно лишь при разделительной резке бетона толщиной до 400 мм.
Разделительную резку можно также осуществлять прутковым и порошковым копьями последовательным образованием ряда отверстий с последующим разрушением перемычек механическим способом.
Резка реактивной газовой струей находит применение для прожигания отверстий в горных породах и железобетоне.
В настоящее время созданы специальные горелки, в которых жидкое горючее (преимущественно керосин) в смеси с кислородом сжигается в топке; пламя выбрасывается через узкое отверстие со сверхзвуковой скоростью до 2000 м/с; температура пламени — 2500—2750° С. Эта струя нагревает поверхность обрабатываемого тела, а при подаче воды оно разрушается и частицы выносятся газами из зоны реза. Разделительная резка этим способом бетонных плит толщиной 100—150 мм происходит со скоростью 8—10 м/ч. Хороших результатов достигают при прожигании отверстий реактивной струей.
Прожигание отверстий диаметром до 100 мм в железобетонных плитах успешно осуществляется угольной дугой косвенного действия. Для этого применяют угольные электроды диаметром 50—100 мм и силу тока 500—1000 А. Необходимость пользоваться светофильтром для глаз снижает эффективность резки угольной дугой.
Применение термической резки бетона и железобетона необходимо для образования проемов в стенах и перекрытиях, круглых небольшого диаметра сквозных отверстий, срезки старых фундаментов для постройки новых под более мощное оборудование и в других случаях — вместо трудоемкой и дорогостоящей механичен ской резки, сопровождающейся вибрациями, разрушениями и сильным шумом.
Резка копьем по сравнению с другими видами является наиболее универсальной, позволяющей резать бетон и железобетон толщиной до 4 м в различных пространственных положениях как при ремонтных работах, так и в новом строительстве. При этом оборудование для резки относительно несложно.
Читать далее:
Краткие сведения о сталях
Статьи по теме:
pereosnastka.ru
При какой температуре заливают бетон, оптимальная температура твердения бетона
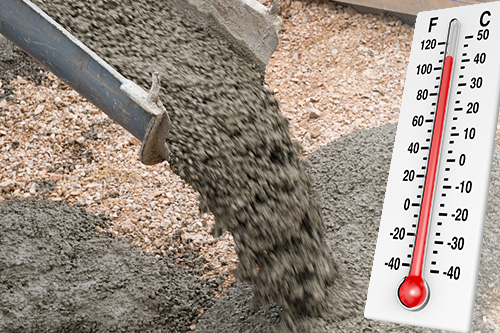
Одним из важных критериев набора бетоном требуемой прочности (прочность на сжатие) является температура его твердения. Несоблюдения температурного режима на строительной площадке может вылиться в значительное увеличение сроков сдачи объекта или, что значительно хуже, в изъяны будущей конструкции.
Именно поэтому еще на этапе планирования монолитных работ необходимо четко уяснить, при какой температуре заливают бетон. За эталонные условия, при которых бетон набирает максимальную (марочную) прочность за 28 суток принято считать +20°C. Этот показатель обозначается R28 и принимается равным единице при данных условиях. В других ситуациях прочность принимает дробное значение. Так 0,3 R28 означает 30% проектной прочности.
Зависимость прочности бетона от температуры и времени выдерживания представлена в таблице:
Прочность бетона от температуры и времени
-3°C | 0°C | 5°C | 10°C | 20°C | 30°C | |
1 | 0,03 | 0,05 | 0,12 | 0,21 | 0,34 | 0,37 |
2 | 0,06 | 0,12 | 0,19 | 0,32 | 0,5 | 0,52 |
3 | 0,08 | 0,18 | 0,23 | 0,38 | 0,6 | 0,6 |
7 | 0,15 | 0,28 | 0,31 | 0,51 | 0,78 | 0,75 |
14 | 0,2 | 0,3 | 0,37 | 0,6 | 0,9 | 0,85 |
28 | 0,25 | 0,36 | 0,43 | 0,7 | 1,0 | 0,93 |
56 | 0,3 | 0,4 | 0,49 | 0,79 | 1,08 | 1,0 |
Данные в таблице приведены для лабораторных условий и марок цементов, имеющих нормальную скорость твердения. В реальных же условиях и температура меняется в значительных диапазонах, и раствор может иметь разные характеристики. Поэтому рекомендуется немного увеличивать сроки выдерживания.
Заливка бетона при низких и высоких температурах
Основной совет, который можно дать людям, которые строят что-то своими руками, не прибегая к профессиональной помощи и технике, это заливать бетон летом при температурах выше 10°C (в крайнем случае – выше 5°C). Тогда бетон затвердеет в нужной степени за достаточно короткий срок.
Если же температура за время выдерживания может опуститься ниже 5°C, то следует подумать о технологиях прогрева бетона или сохранения выделяемого им тепла. Особенно это актуально в первые дни, когда происходит схватывание. Если в это время вода в растворе кристализуется, то лед попросту разорвет образовавшиеся связи цемента с наполнителем и конечное изделие получится крайне хрупким.
С другой стороны при температурах выше 30°C возникает проблема чрезмерного испарения влаги из тела бетона, что также негативно сказывается на его качестве. В этом случае залитый бетон необходимо накрывать защитной пленкой и периодически поливать его поверхность водой.
Для измерения температуры можно использовать бесконтактный термометр (пирометр), например, такой, как на видео:
Прочность бетона при распалубке и его нагрузка
Распалубку бетона можно проводить при достижении прочности в районе 50%, то есть на третий день при температуре воздуха 20°C. При достижении им 60-70% допускается производить частичную нагрузку конструкции.
betonprogrev.ru
Строительный бетон
Создание защиты железобетонных конструкций от воздействия агрессивных сред способствует увеличению их долговечности и является одним из путей повышения экономической эффективности строительства. Наряду с известными способами облицовки фасадов керамической и каменной плиткой, известны процессы декоративной отделки строительных изделий путем поверхностного оплавления. В качестве источников энергии для оплавления применяют газовые горелки, электрическую дугу, плазму. В результате плазменного оплавления на поверхности бетона образуется декоративный слой, одновременно являющийся защитным слоем от агрессивного воздействия окружающей среды. Создавать такие покрытия можно даже с помощью ручных плазмотронов или в некоторых случаях ацетиленовых горелок, что расширяет зону применения отделки. Плазменное оплавление поверхности бетона целесообразно применять в условиях, когда другие виды отделки менее доступны и в условиях повышенной агрессивности окружающей среды, что характерно для зданий агропромышленного комплекса. При отделке бетона плазмой в его толще будут создаваться температурные поля, зная распределение которых можно управлять технологическим процессом отделки и корректировать качественные показатели получаемых бетонных изделий. В процессе термообработки строительных материалов происходит взаимосвязанный тепломассоперенос. Быстрый темп изменения температуры и массосодержания в поверхностных слоях материала приводит к возникновению градиентов потенциалов переноса, которые способствуют образованию потоков субстанции, направленных из толщи к поверхности и в обратном направлении. В данной работе исследовалось влияние температуры на свойства бетона при его высокотемпературной отделке. В качестве модельной рассматривалась задача прогрева полуограниченного тела.
За основу была взята задача теплопереноса в виде
при начальном условии Т(h,0)=T0(h) и граничном условии на бесконечности
В начальный момент времени (?=0) открытая поверхность тела имела температуру, которая поддерживалась постоянной при протекании всего процесса нагревания.
Для получения распределения температурных полей по толщине бетонного камня была
создана компьютерная программа “Глазурь” на языке Pascal для работы в среде indows.
При расчете использовался численный метод неявной классической разностной схемы. Весь процесс разделялся на следующие фазы:
1. нагрев внешней поверхности до температуры плавления покрытия;
2. плавление покрытия;
3. кристаллизация покрытия.
Продолжительность фазы зависит от параметров нагревателя и свойств образца и может колебаться от нескольких секунд до нескольких минут. На каждом временном шаге рассчитывалась плотность теплового потока между нагревателем и образцом.
Наглядно распределение температур внутри оплавляемого изделия, вычисленных и построенных с помощью программы, приведены на рис. 1.
Рис.1. Распределение температурных полей в толще бетона в зависимости от температуры нагрева и вида покрытия поверхности
1 – нагрев бетона до температуры плавления стекловидного покрытия; 2 – нагрев бетона без покрытия за тот же интервал времени; 3 – завершение плавления покрытия на бетоне; 4 – нагрев бетона без покрытия через интервал времени, равный длительности плавления покрытия. Из приведенных графиков видно, что нагрев бетона до температуры плавления как с нанесенным покрытием, так и без него не дает распределение температурных полей по толще бетона более 1-1,5 см. При завершающей фазе термической обработки на глубине 4 см бетон прогревается на температуру меньше, чем температура удаления физически связанной воды. Таким образом, изменение физико-механических свойств бетона в результате высокотемпературной отделки может происходить только в поверхностных слоях, не затрагивая всю конструкцию.
strbeton.narod.ru
Температурное расширение бетон - Справочник химика 21
Коэффициент линейного температурного расширения для жаростойких бетонов на глиноземистом цементе и заполнителе из хромита в интервале температур от 20 до 900° С равен [c.43]Так как коэффициенты температурного расширения бетона и стали по величине очень близки, то температурные напряжения не нарушают монолитности железобетона. [c.28]
Температурный коэффициент линейного расширения бетонов [c.188]
Коэффициент температурного расширения бетона составляет 0,00001. Коэффициент усадки принимается 0,00015 таким образом, на 1 м длины бетонного сооружения усадка составляет 0,15 мм. Необходимо отметить, что быстротвердеющий, белитовый и пуццолановый портландцементы обычно дают большую усадку бетона усадка бетона большая происходит также при использовании мелкозернистых и пористых заполнителей. [c.370]Обмуровка трубчатых печей. Обмуровка печи включает слой из фасонного огнеупорно-изоляционного кирпича толщиной до 250 мм и наружный слой тепловой изоляции. Для придания прочности и защиты от атмосферных воздействий обмуровку снаружи закрывают стальным кожухом. Применяют также печи с монолитной обмуровкой из жаропрочного бетона. Обмуровку крепят на специальных подвесках и кронштейнах, которые соединены с каркасом печи (рис. Х1-6). Боковые поверхности кирпича иногда выполняют волнистыми для обеспечения большей герметичности печи. Для возможности теплового расширения кладки устраивают температурные швы, заполненные мягкой, легко деформируемой тепловой изоляцией (например, асбестом). [c.194]
В жаростойком железобетоне арматуру располагают в местах, где температура не превышает 350° С. При более высоких температурах температурное расширение арматуры больше, чем у бетона, [c.72]
В строительстве часто необходимо иметь цемент, отличающийся малым тепловыделением. Он предназначается для массивных бетонных конструкций, например, в гидротехнических сооружениях. При твердении цемента с большим экзотермическим эффектом возникает температурное расширение бетона, причем он сильно расширяется во внутренних частях массива и в меньшей степени в наружных частях, которые подвергаются естественному охлаждению воздухом или водой. Скорость и степень охлаждения тоже различны в разных зонах конструкции. Объемные деформации, возникающие при неравномерных расширении и сжатии бетона, вызывают образование трещин и иногда приводят к разрушению сооружений. Для получения цемента, обладающего небольшим тепловыделением, клинкер должен изготовляться с относительно невысоким содержанием трехкальциевого силиката и трехкальциевого алюмината. [c.181]
Коэффициент линейного температурного расширения бетона на периклазовом цементе при нагревании до 1450° С равен 1,47%. Термостойкость жаростойких бетонов на шамотном заполнителе— 15—25 водяных теплосмен, а на хромитовом — порядка 5. Объемная масса бетонов с хромитовым заполнителем 3200 кг/м , а с шамотным — 1800—2000 кг1м . [c.43]
В жаростойком железобетоне арматуру располагают в местах с температурой, не превышающей 350° С. При более высоких температурах температурное расширение арматуры больше, чем температурное расширение бетона, сцепление арматуры с бетоном нарушается, арматура корродирует, расширяется и разрушает бетон. [c.174]
К разрушению бетонного тела приводят и внутренние причины — высокая водопроницаемость, взаимодействие щелочей цемента с кремнеземом заполнителя, изменение объема из-за различия температурного расширения цемента и заполнителя, образование соединений с увеличением объема твердой фазы в условиях, когда структура цементного камня окончательно сформировалась (образование гидроксида кальция или. магния, гидросульфоалюминатов кальция). [c.367]
Предел прочности, МПа, при. сжатии растяжении изгибе Адгезия к бетону, МПа Коэффициент линейного температурного расширения в пределах температур 40... 100 °С, ГС [c.92]
В номинальных режимах эксплуатации АЭС рабочие параметры установки сохраняются примерно постоянными (для ВВЭР-440 с учетом данных 1 гл. 2 давление и температура на входе составляют 12,7 МПа и 265 °С, а на выходе — 12,4 МПа и 296 °С). Расход теплоносителя через реактор составляет около 43 000 м /ч, Давление в контуре, стационарные температурные смещения и напряжения от весовых нагрузок определяются с использованием общей расчетной схемы. Весовые нагрузки из-за массивности оборудования АЭУ оказьшаются весьма значительными. Суммарная масса оборудования составляет около 10% от массы бетонных сооружений, заключающих в себя установку. Эта характеристика АЭУ важна для проектирования опор, анализа отклика на сейсмические воздействия и нагрузки, обусловленные аварийными режимами эксплуатации АЭС, Опорные конструкции должны допускать температурные расширения и быть достаточно жесткими, поскольку они строго влияют на собственные колебания всей системы АЭС, даже контролируя их, что также важно для учета влияния землетрясений и аварийных нагрузок. Жесткостные свойства опор, возможные (заложенные в проекте) их особенности рассеяния (диссипации) энергии колебаний учитываются в расчетах введением соответствующих матриц жесткости и демпфирования. [c.90]
К разрушению бетонного тела приводят и внутренние причины — высокая его водопроницаемость, взаимодействие щелочей цемента с кремнеземом заполнителя, изменение объема из-за различия температурного расширения цемента и заполнителя. Поскольку эти вопросы рассмотрены в главе, посвященной свойствам бетонов, остановимся на внешних причинах коррозии цементного камня и бетона, возникающих в результате физического и химического взаимодействий материала с окружающей средой. [c.368]
Результаты испытаний образцов бетона с магнезитовым заполнителем показывают постепенное снижение прочности от 100 до 1100°. Снижение прочности в этом интервале температур можно объяснить частичным нарушением структуры образцов, происходящим в результате температурного расширения зерен периклаза (магнезита), обладающего значительным термическим коэффициентом линейного расширения (а р. = 17-10 ). [c.45]
Коэффициент температурного расширения к-бетона в пределах температур от 20 до 300° равен 0,000008, если Д/ вычислять как разность между длиной нагретого образца и длиной образца после охлаждения его вновь до 20°, и 0,000004, если Д/ относить к первоначальной длине образца. Такая разница объясняется тем, что при нагревании к-бетона до 300° происходит не только тепловое расширение материала, но и другие физико-химические процессы, вероятно связанные с дальнейшей дегидратацией геля ЗЮз и уменьшением первоначального объема материала. [c.110]
Для температур, не превышающих 500—550°, В. И. Мурашек считает возможным в качестве мелкого заполнителя применять, естественные или искусственные пески, обосновывая это тем,, что при размере зерен до 5 мм их температурное расширение и физическая анизотропность не могут существенно повлиять на снижение прочностп бетона. В. И. Мурашев не рекомендует применять пески из доломита и мергеля, а также из доломитизи-рованного и мергелистого известняков, так как температура диссоциации углекислого магния лежит в пределах 400—500°, а примесь глинистых веществ и магнезии к известняку снижает температуру его диссоциации. Для температур, превышающих 550°, применяют материалы, не содержащие большого количества кристаллического кварца и обладающие малым коэффициентом линейного расширения, достаточной огнеупорностью, термостойкостью, а также прочностью при высокой температуре. К их числу относятся базальт, диабаз, доменные шлаки, бой красного или шамотного кирпича, хродшстый железняк, магнезит и тому подобные материалы. Выбор соответствующего заполнителя зависит от величины рабочей температуры, специфических условий работы элемента конструкции и местных условий. [c.18]
Недостатком подобной облицовки кроме уже упомянутой относительно низкой границы температур применения и большого температурного расширения, что при сочетании с армированным бетоном очень неблагоприятно, является хрупкость этого материала при низких температурах. [c.133]
Необходимо, однако, предупредить читателя о то.м, что пленка из пластифицированного поливинилхлорида обладает большим температурным расширением при высоких температурах она размягчается, а при низких — становится хрупкой. Из-за этого, например, ее нельзя рекомендовать для форм, в которых твердение бетона ускоряют с помощью пропаривания. [c.174]
Фундамент печи, выложенный из кирпича или бетона, делают полым для. вентилирования и возможности осмотра днища кожуха. Кожух печи сваривают из обечаек, изготовленных из листового железа толщиной 12—15 мм, имеющих ребра жесткости. Изнутри кожух печи тщательно футеруют фасонным пришлифованным шамотовым кирпичом с пористостью, не превышающей 16%. Кирпич кладут на специальной замазке, состоящей, например, из тонкоразмолотого полевого шпата, замешанного на калиевом жидком стекле. Между кожухом и футеровкой укладывают асбестовые листы для теплоизоляции и амортизации усилий от температурных расширений кладки. Так как давление газов в печи доходит до 200—250 мм рт. ст., то сочленение футеровки с электродами, фурмами, леткой и другими элементами тщательно уплотняют. [c.100]
Цемент широко применяют также для изготовления самостоятельного строительного материала — бетона. Последний представляет собой смесь цементного теста с песком и каменной мелочью естественного или искусственного происхождения (гравий, щебень, обломки кирпичей и т п.). Хорошо перемешаннук> бетонную смесь укладывают в формы, где она затвердевает. Очень часто внутри этих форм предварительно устанавливают каркасы из железа, с которым бетон имеет почти одинаковый коэффициент температурного расширения и хорошо сцепляется. Такие сооружения носят название железобетонных. [c.394]
Также довольно остро стоит вопрос о восприятии температурных деформаций. Термореактивные смолы и бетоны на их основе имеют коэффициент температурного расширения (к. т. р.) значительно (в 2—3 раза) больший, чем у цементного камня и цементных бетонов [порядка (30 20) 10 против (15 10) 10 соответственно]. [c.13]
Фундаменты для компрессоров малой мощности (до 50 кВт) сооружают из бетона, для компрессоров и двигателей внутреннего сгорания большой мощности — из железобетона. Бетон — искусственный каменный материал, который получается в результате затвердения смеси цемента (вяжущего), щебня, песка (заполнителей) и воды. Железобетон — сочетание бетона и стальной арматуры, монолитно соединенных и работающих в конструкции как единое целое. Совместная работа материалов в железобетоне обеспечивается прочным сцеплением бетона с арматурой, относительной близостью значений температурных коэффициентов линейного расширения обоих материалов. [c.33]
Кроме перечисленных факторов, на работу уплотнений РВП ТКЗ первых выпусков значительное влияние оказывают температурные деформации каркаса котла, каркаса РВП, железобетонной тумбы и газовых коробов. Это связано с тем, что нижняя опора РВП не связана конструктивно с верхней, направляющей, опорой. В результате этого верхняя часть каркаса РВП, соединенная с каркасом котла, при нагревании расширяется и уводит верхнюю опору относительно нижней, установленной на железобетонной тумбе. Так как бетон и металл имеют различные коэффициенты линейного расширения, то при изменении температуры наружного воздуха ротор и корпус могут несколько смещаться относительно друг друга по высоте. На некоторых котлах ТКЗ верхняя балка РВП, в которой установлены направляющие подшипники, связывает все четыре воздухоподогревателя (котел ТПП-110). Во время работы балка нагревается (до 130—150° С) и в результате ее расширения опоры уходят от оси котла. Патрубки дымовых газов присоединены к общему коробу, который при нагревании расширяется и перекашивает корпус РВП. [c.119]
ОГНЕСТОЙКОСТЬ — способность материала сохранять физико-меха-нические свойства при воздействии огня в условиях пожара. У одних материалов (доломита, известняка, мрамора) воздействие огня вызывает хим. разложение, другие материалы (алюминий) плавятся, третьи (бетон, гранит, сталь) деформируются. Так, бетон под воздействием высокотемпературного пламени частично теряет прочность от внутренних напряжений, возникающих вследствие различия температурного коэфф. линейного расширения цементного камня и крупного заполнителя. Кроме того, при т-ре выше 500° С начинается разложение гидрата окиси кальция в структуре цементного камня. Одновременно разрыхляются зерна кварца в песке и крупном за- [c.93]
Под температурными деформациями понимают обратимые деформации, возникающие при нагреве или охлаждении материалов. Эти деформации принята оценивать температурным коэффициентом линейного расширения (ТКР). У большинства полимеров значение ТКР значительно выше [для термопластов (0,5—5) 10 1/°С], чем у бетона и стали (1-10- 1/°С). [c.21]
Примечание 1. Эмпирические формулы для вычисления температурного коэффициента линейного расширения бетонов в интервале температур от —30" до 0°С ( ) и от О до +40°С ) я з вискиости от лажностк по объему т (%) и температуры Г °С следующее [c.189]
Во избежание подсоса воздуха или потерь газа температурные швы обычно заполняются маловлажной огнеупорной массой с добавкой 25—30% асбеста по объему. При заделке в кладку пода стелюг, балок и т. п. между кладкой и. металлом оставляют температурные швы для свободного расширения металла при нагревании. При укладке жаростойких бетонов температурные швы должны быть предусмотрены проектом. Типовые температурные швы приведены на рис. 60. [c.262]
Так, например, временное сопротивление на разрыв синтетических волокон типа нейлон, капрон достигает 8000 кГ1см при объемном весе около 1 г/см . Однако низкий модуль упругости (до 50 000 кГ см ), слишком высокий коэффициент температурного расширения (удлинения) а=(8—10) 10- и сравнительно большая ползучесть под нагрузкой не позволяют использовать их в качестве арматуры для бетонных конструкций. [c.90]
Если пластмассовый трубопровод залит в бетон, то он окажется прочно зафиксированным в бетоне каждым соединительным устройством и каждой фасонной частью, если даже бетон не образует сцепления с пластмассовой поверхностью трубы. Трубопровод будет неподвижен в бетоне и лишен возможности расширения. Трубы же уложенные в свободный или стабилизированный цементом материал Le a не будут иметь такой жесткой фиксации и потому должны рассматриваться как свободно уложенные. В таких трубопроводах температурные расширения гасятся либо в муфтах, либо за счет смещения водоотводящих трубопроводных патрубков. [c.78]
Аппарат представляет собой кожухотрубный вертикальный одноходовой теплообменник, который имеет две трубные решетки нижнюю толщиной 15 мм и верхнюю толщиной 155 мм. В горячей камере устанавливается распределитель потока. Нижний корпус футерован жаропрочным бетоном. ЗИА соедп-нен циркуляционными трубами с барабаном-паросборником.. Удовлетворительные эксплуатационные характеристики работы и простота обслуживания способствуют широкому распространению аппаратов, несмотря на необходимость применения массивного прочного корпуса (в условиях получения пара высоких, параметров) и ряд конструктивных недостатков. Ввиду того,, что трубные решетки работают при различных температурных перепадах (нижняя 650—450 °С и верхняя 260 °С, температура испарения воды 330°С) возникают трудности в креплении концов труб за счет разницы в величине линейного расширения. Кроме того, возникают осложнения, связанные с газодинамикой потока, который, выходя из центрального штуцера с температурой 800—870 °С, должен быть равномерно распределен по всем трубам. Неравномерность потока пирогаза по охлаждающим трубкам ЗИА вызывает местное переохлаждение пирогаза и как результат — конденсацию компонентов тяжелых смол, их полимеризацию, захват ими частиц кокса и сажи, содержащихся в газе, что способствует забивке труб, расположенных преимущественно по периферии распределительной решетки. [c.122]
Теплостойкость П. на основе различных связующих следующая (в °С) фурановые смолы — 150—200, эпоксидные — 80—120, полиэфирные — 70—100, фенольные — 120—180. Температурный коэфф. линейного расширения П. в 2—6 раз превышает этот показатель для стали и обычного бетона при повышенци темп-ры от —40- до 60 °С он изменяется от 20-10 °С до 60-10 °С . Теплопроводность П. на основе мономера [c.439]
Н. А. Житкевич к числу основных причин, вызывающих снижение прочности обычного бетона при его нагревании, относит наличие кварцевого песка. Известно, что переход модификации -кварца в а-кварц при температуре 573° сопровождается значительным скачкообразным изменением объема, что нарушает структуру бетона. Неравномерное расширение кристаллов некоторых минералов по различным осям симметрии также способствует нарушению структуры бетона при нагревании. Кроме того, основными причинами, вызывающими снижение прочности бетона при его нагревании, являются возникновение внутренних напряжений и повреждение структуры вследствие разности температурных деформаций цементного камня и заполнителя. [c.15]
Температурные деформации. При нагреве до 100° затвердев-пше цементные растворы теряют небольшое количество воды. При этом увеличение объема затвердевшего раствора вследствие теплового расширения его компенсируется уменьшением объема этого раствора, вызванным испарением воды. Структура цементного камня при этом Не нарушается. При дальнейшем повышении температуры объем отвердевшего цементного раствора уменьшается, что связано с нарушением структуры цементного камня. Усадка цементного камня объясняется уплотнением его при высыхании коллоидальных веществ, образовавшихся в процессе твердения цемента. Особенно большое значение приобретают характер и величина относительных деформаций бетонных футеровок при их армировании металлической сеткой и наличие шпилек, стержней или кольцевых перегородок. Козфф1щиент линейного расширения стали Ст.З с повышением температуры от 100 до 500° увеличивается с 11,9-10 до 14,2-10" , а нержавеющей стали типа 1Х18Н9Т — с 16,6- 10 до 17,9 10 . [c.34]
chem21.info
Максимальная температура - применение - Большая Энциклопедия Нефти и Газа, статья, страница 1
Максимальная температура - применение
Cтраница 1
Максимальная температура применения, С 1ССО - 1100 Теплопроводность, ВтДм-К. Технологическая схема производства вермикулитоперлитовых изделий состоит в подготовке формовочной смеси, формовке и термообработке. [2]
Максимальная температура применения составляет 500 С. [3]
Максимальная температура применения мертелей определяется температурой применения составляющих компонентов. [5]
Максимальная температура применения плотных огнеупоров обычно несколько выше ( примерно на 50 С) температуры начала деформации под нагрузкой 0 2 МПа, регламентируемой стандартом на материал. Для легковесных изделий температура применения определяется температурой дополнительной линейной усадки материала, регламентируемой стандартом. [6]
Максимальные температуры применения рассматриваемых паст весьма высоки - 300 - 400 С. При таких температурах они, правда, могут работать не очень долго, как правило, не более нескольких часов. [7]
Максимальная температура применения синтетических солидолов не превышает 65 - 70 С. Выше этой температуры они необратимо распадаются. В связи с этим, в частности, нельзя наносить еолидолы на трущиеся или защищаемые от коррозии поверхности в расплавленном виде. В состав солидолов всегда входит вода, которая является стабилизатором их структуры. При снижении концентрации ее ниже 0 5 % еолидолы распадаются. [8]
Максимальной температурой применения огнеупорных бетонов считается температура, при которой их линейная усадка в течение 5 ч не превышает 1 % для плотных изделий и 2 % для теплоизоляционных. [9]
За максимальную температуру применения бетона принимают температуру предпоследнего испытания. Температуру первого испытания устанавливают в зависимости от состава бетона. [10]
По максимальной температуре применения огнеупорные бетоны подразделяют на группы: для умеренной - до 1100 С, средней - до 1400 С, высокой - до 1700 С и особо высокой - выше 1700 С. [11]
Температура плавления и максимальная температура применения в вакууме тугоплавких металлов соответственно: молибден - 2 600 и 1700 С, тантал - 3000 и 2 200 С, вольфрам - 3380 и 2 500 С, ниобий 2415 и 1700 С. [12]
С увеличением огнеупорности заполнителя максимальная температура применения жароупорного бетона может быть значительно повышена. [14]
Страницы: 1 2 3 4
www.ngpedia.ru