Ультрабетон – характеристики и производство. Технология ультрабетон
Ультрабетон – характеристики и производство
Существует множество видов бетонов, среди которых есть тяжелые и легкие типы. В данной статье речь пойдет о плотном материале, который производится в виде окатышей. Мы рассмотрим ниже, как изготавливать ультрабетон своими руками способом вибролитья в формы.
На фото – декоративный забор, изготовленный по новой технологии
Общие сведения
Возможно, вы встречали и такие его названия, как кевларобетон или гранилит, но производят их по той же технологии, суть которой одна – создается окатыш бетона, который выглядит в виде шарика.
Этому способствует использование модифицированного бетоносмесителя. Фактически, технология ультрабетона, хотя и имеет разные названия, использует один и тот же метод приготовления материала, рецептуру и сырье.
Тротуарная плитка с фотолюминофорными добавками
Сводится процесс к тому, что из бетонной смеси, которую приготовили по специальному рецепту, начинают удалять воздух. Для этого используют гравитационный бетоносмеситель, в котором и получаются окатыши с пониженным соотношением воды и цемента, что увеличивает их плотность.
Вы можете изготавливать различные малые архитектурные формы
Такой метод дает возможность получить имитацию природных материалов, таких как:
- гранит;
- малахит;
- янтарь;
- мрамор,
а также цветные переливы.
Это очень прочный, современный и новый тип бетона, который применяется для изготовления:
- тротуарной плитки;
- бордюров;
- заборов;
- фасадного камня;
- каминов и других МАФов.
Красота и необычность материала
Использование материала
Ультрабетон основан на принципиально других решениях, принятых в области изготовления декоративного архитектурного цветного бетона способом гравитационного катышеобразования. В этом случае удается получить изделие с высокими физико-механическими параметрами.
Поверхность отливки имеет совершенную плотность и высокий глянец. При этом удается получить цветовую гамму различной сложности, независимо от площади отливаемого элемента и его габаритных размеров. Тем самым создается эффект природного или искусственного материала в диапазоне от пластика и до малахита.
В производстве стройматериалов для архитектурно-ландшафтных работ используют эффективные схемы, с помощью которых удается получать новые виды бетонов.
Для раскрытия диапазона их применения применяют различные:
- сырьевые материалы;
- вяжущие;
- заполнители;
- пластификаторы;
- эксперименты с методами и этапами добавления химических модификаторов, а также минеральных активных добавок;
- оптимизационные работы с составом многокомпонентного бетона;
- способы управления технологией.
Для создания изделий применяют практически любые формообразующие оснастки и формы. При этом продукция обладает высокими физико-механическими свойствами, которые сочетают в себе высокие показатели прочности на сжатие — В 40-90. Это сродни бетонам марок М600-1200 и выше.
Производственный процесс
Ниже предлагается инструкция, которая поможет разобраться в этом вопросе:
Совет: обязательно нужно проводить контроль влажности минеральных заполнителей.
Совет: нужно контролировать температуру воды, которая используется для затворения пластификатора.
Процесс изготовления
Ультрабетон – окатыш в разрезе
Совет: накройте формы или всю паллету п/э пленкой.
Применяйте цемент без добавок
Сырье
Состав ультрабетона выглядит таким образом:
Портландцемент | Марка М400 и М500 Д0, т.е. без добавок. В противном случае он имеет повышенную реакционной способностью к СО2, который есть в воздухе. Из-за этого образуются первичные высолы и снижаются декоративные качества продукции, а также медленнее твердеет состав. |
Песок | Используйте карьерный или речной, фракция 1,8-2,5. Цена вполне доступна. |
Гранитный отсев | Применяется фракция материала 0-5 мм. Просев в данной технологии не используется. |
Пластификатор | Подходит суперпластификатор С-3 или СП-1, но без воздухововлекающих добавок. Его использование позволит быстрее сформироваться монолиту и поднять производительность работ. Составы должны быть только порошкообразными. |
Для материала можно применять различные формы
Совет: если вы хотите окрасить ультрабетон в определенный цвет, используйте красители и пигменты для окрашивания бетона.
Вывод
Ультрабетон — совершенно новая и современная технология производства. Она дает возможность создать материал, обладающий уникальными характеристиками. Для производства необходимо иметь специальное оборудование.
Видео в этой статье поможет найти вам дополнительную информацию по этой тематике.
rusbetonplus.ru
Как сделать ультрабетон своими руками?
Есть очень много видов бетонов, посреди каких имеется тяжкие и легкие разновидности. В предоставленной статье речь пойдет о плотном материале, который делается в виде окатышей. Мы осмотрим ниже, как изготавливать ультрабетон собственными руками способом вибролитья в формы.Может быть, вы встречали и эти его названия, как кевларобетон либо гранилит, однако создают их сообразно той же технологии, сущность которой 1 – формируется окатыш бетона, который смотрится в виде шарика.
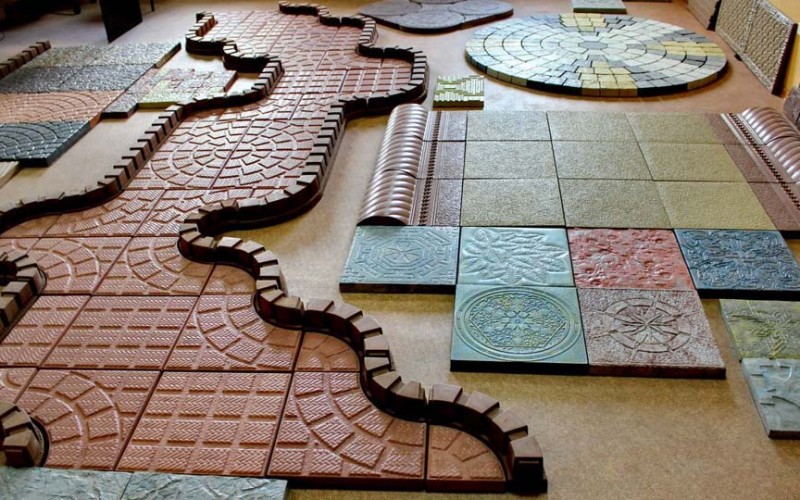
rusbetonplus.ru
Ультрабетон - Производство ультрабетона - Состав
В составе Ультрабетона (УБ) следующие компоненты: портландцемент, минеральный заполнитель, суперпластификатор С3, пигменты, вода.
Состав и Основная рецептура Ультрабетона
Все массы ингредиентов зависят от запланированной массы УБ, т.е от количества изделий, которые Вы можете изготовить в течение 20 мин (жизнеспособность смеси УБ).Портландцемент (ПЦ) М 500 Д0, цвет серый. Содержание ПЦ в УБ рассчитывается по следующей формуле: Мб х 0,287=Мпц, где Мб – запланированная масса УБ, 0,287 – не изменяемый коэффициент, Мпц – расчетная масса портландцемента.
Минеральный заполнитель
Это песок модуль крупности 2 – 2,5 и гранитный отсев фракция 0 – 5 мм.В тяжелом бетоне минеральный заполнитель будет состоять из 70% гранитного отсева и 30% песка.В легком бетон минеральный заполнитель будет состоять из 40% гранитного отсева и 60% песка.Содержание минерального заполнителя в УБ рассчитывается по следующей формуле:Мпц х 2,3 = ∑Ммз для тяжелого бетона = Мп х 0,3 + Мго х 0,7 , илиМпц х 2,3 = ∑Ммз для легкого бетона = Мп х 0,6 + Мго х 0,4, где Мпц – расчетная масса портландцемента, 2,3 – не изменяемый коэффициент, Мп – масса песка, Мго – масса гранитного отсева, ∑Ммз – расчетная суммарная масса минерального заполнителя.
Суперпластификатор С3
Содержание С3 в УБ рассчитывается по формуле: Мпц х 0,01 = М С3, где Мпц – расчетная масса портландцемента, 0,01 – не изменяемый коэффициент, М С3 – расчетная масса С3.
Пигменты
При колеровке УБ лучше применять железоокисные пигменты. Их количество рассчитывается по формуле: Мпц х 0,03 = ∑п, где Мпц – расчетная масса портландцемента, 0,02 – не изменяемый коэффициент, ∑п – расчетная суммарная масса пигментов.При составлении колеровочных рецептур нужно помнить несколько правил: мелирование позволяет получить яркие тона, время на прокрашивание должно быть затрачено не менее 5 сек и не более 15 сек, суммарная масса пигментов, желательно, не должна превышать коэффициента 0,03.
Пример колеровочной рецептуры для Мрамора классического:1. Белый – 0,013 – 10 секунд.2. Черный – 0,007 – 7 секунд.По готовности катышного замеса УБ, в бетоносмеситель в «активную» зону (см. гл. «Последовательность действий») вводится масса пигмента из расчета: Мпц х 0,013. После введения работник считает до десяти и вводит черный пигмент, масса которого рассчитывается как, Мпц х 0,007. После введения черного пигмента (также в активную зону), через семь секунд начинается загрузка замеса в опалубку (в формы).
Вода
Температура воды должна быть от +20 до +40 градусов по Цельсию. Замечено, если температура воды около +40 градусов, то риск возникновения первичных высолов гораздо ниже.
Содержание воды в УБ
Содержание воды в УБ рассчитывается по следующей формуле: Мпц х 0,17 = Мв, где Мпц – расчетная масса портландцемента, 0,17 – не изменяемый коэффициент (Данное значение может меняться от 0,14 до 0,22 в зависимости от влажности минерального заполнителя и жесткости цемента, величина изменения рассчитывается в каждом частном случае), Мв – расчетная масса воды.
formbeton.org
Технология ультрабетон
Ультрабетон является новым современным, очень прочным материалом, который используется для производства таких архитектурных форм, как заборы, бордюры, вазоны, фасадный камень, тротуарная плитка и т.д.
Особенностью технологии изготовления ультрабетона является то, что её цель – высокое качество, ультрасовремнные физико-механические характеристики в сочетании с декоративно-эстетическими качествами.
Для производства ультрабетона используется самое качественное сырьё, из которого можно получить материал, имитирующий мрамор, природный камень и обладающий такой же прочностью, как гранит.
Компания БИОП использует принципиально новые технологии в производстве архитектурного бетона, основанные на методе гравитационного катышеобразования. Продукция из ультрабетона имеет приятный глянцевый вид и характеризуется прочностью и плотностью.
Особенностью производства ультрабетона является то, что ему доступны элементы любой сложности, получение продукции разнообразных цветов, имеющей сходство, как с искусственными, так и природными материалами.
Технология ультрабетон заключается в том, что из бетонной смеси, изготовленной по специальному рецепту, удаляется воздух. После этого замес уже в твёрдом виде попадает на резонатор. Высокочастотный резонатор равномерно распределяет замес по формообразующему устройству, где он приобретает ещё большую плотность.
Благодаря новым технологиям и использованию химических и минеральных добавок, налажено производство новых видов бетона, прочность которых соответствует маркам М-600 – М-1200. такой бетон очень ценится в архитектурном строительстве. В нём применяются разные варианты рецептов приготовления замесов с использованием вяжущих и других модифицированных материалов, а также технологических схем.
Технология производства ультрабетона отличается темпами твердения, прогрессивными методами стоительно-технического управления производственными процессами и современным строительным оборудованием.
biopp.ru
Технология — ULTRABETON
Почему стоит обратить внимание на искусственный камень — Ультрабетон?
Ультрабетон очень прочный материал. Прочность на сжатие — больше 550 кгс/кв.см. Проще говоря, груженый «Камаз» его раздавить не сможет!
Морозостойкость. Ультрабетона не менее F300 — это значит, что он выдерживает не менее 300 циклов замерзания-оттаивания в солевом растворе без потери массы и прочности! Это особенно важный показатель в наших краях, где каждую весну асфальт на дорогах сходит вместе со снегом как раз из-за недостаточной морозостойкости.
Ультрабетон достаточно точно повторяет рисунок натурального камня, будь то мрамор, гранит или любой другой минерал. При этом он абсолютно равнодушен к атмосферным воздействиям, не выцветет и не выгорит даже под нашим жарким южным солнцем.
Приемлимая цена. Стоимость Ультрабетона сравнима с обычной тротуарной плиткой, а не с натуральным камнем, как может показаться после прочтения обо всех его свойствах.
Срок службы Ультрабетона установлен в 25 лет. Технология существует 25 лет и до настоящего времени ни один объект не пришлось ремонтировать! Вероятно, что в ваш облицовочный камень из Ультрабетона прослужит намного дольше.
УЛУЧШЕННЫЙ ВИД УЛЬТРАБЕТОНА
Для всех изделий из Ультрабетона, а это: тротуарные плиты и брусчатка, облицовочный камень, еврозабороры, ступени, скамьи и барельефы, мы предлагаем ряд дополнительных эффектов, призванных улучшить внешний вид изделий
ЭФФЕКТ ЛОТОСА
Вода на обработанной поверхности собирается в шарики, как на листе лотоса, и скатывается вниз. Грязь не прилипает, а пыль не въедается. Результат — поверхность всегда чистая и глянцевая. Любое загрязнение смывается простой водой без давления и оттирания.
ЭФФЕКТ МОКРОГО КАМНЯ
Такое покрытие применяется для тротуарных плит и ступеней, придает цветам еще большую насыщенность, дополнительный глянец поверхности, она выглядит так, будто только прошел дождь и вода еще не высохла. В некоторых случаях возможно применение эффекта и к обычной плитке
КОМУ ВЫГОДНО РАБОТАТЬ С НАМИ ?
Мы стремимся максимально учесть пожелания заказчиков и сократить время поиска необходимых материалов и услуг, поэтому для комплексного подхода к объектам клиентов предлагаем взаимовыгодное сотрудничество организациям и частным лицам:
дизайнерам;
архитекторам;
проектировщикам;
студиям дизайна;
производителям мебели;
рекламным компаниям;
строительным организациям;
управляющим компаниям и другим.
На всю бетонную продукцию документально предоставляем гарантию!!!!
ultrabeton24rus.ru
Технология Ультрабетон . Статьи компании «Компания Ультралит»
Технология Ультрабетон - это особый оригинальный способ изготовления бетонной смеси, отличающийся от привычных методов применяемых в такой сфере производства строительных материалов, как вибролитье.
Главными приципами данной технологии является то, что бетонная смесь на основе портландцемента, представляет собой плотно сжатые окатыши сферической формы, диаметр которых, как правило, варьируется от 2 до 5 сантиметров.
Способ получения окатышей Ультрабетона был заимствован из области черной металлургии, где применяются схожие принципы окатышного гранулирования при окомкование шихты.
Окатыши Ультрабетона формируются в барабане модифицированного гравитационного смесителя. Окомкование бетонной смеси в гравитационном смесителе позволяет получить окатыши высокой плотности с полным исключением воздуха из смеси. А На ощупь созревший окатыш напоминает жесткую резину.
Сам окатыш представляет собой шар, состоящий из плотного конгломерата строительного песка и зерен различной фракции гранитного (или аналогичного материала) отсева, сцепленных между собой портландцементом. А в центре такого сферического образования находится ядро,состоящее из одного или нескольких крупных зерен (4-5мм) отсева.
В качестве колера в основном используются обычные светостойкие железооксидные и фталоцианиновые пигменты для бетона.
Но данные пигменты расходуются в два-три раза меньше в сравнении с принятыми нормами. Здесь пигменты не прокрашивают все тело бетона, что в принципе и не нужно, а подаются небольшими, подобранными по рецептуре, дозами на поверхность созревших окатышей.
В этом случае каждый шар Ультрабетона окрашивается неповторимо по своему и при дальнейшем формовании монолита дает свою линию неповториую(«жилку») оттенка в поверхности изделия.
В результате продукция из Ультрабетона имитирует натуральные камни со сложным природным рисунком под мрамор, гранит, янтарин и прочее.
vazon22.ru
Ультрабетон - технология изготовления
Рассмотрим подробно технологию приготовления ультрабетона - от приготовления компонентов смеси до заливки форм и выдержки распалубочной прочности
1. Приготовление вторичных компонентов
Отвесьте расчетную массу воды. Согласно выбранной рецептуре отвесьте расчетную массу пигментов. Отвесьте расчетную массу Суперпластификатора С3. Растворите расчетную массу С3 в расчетной массе воды.
2. Приготовление замеса
2.2. Отвесьте расчетную массу песка. Песок высыпьте в грушу бетоносмесителя. Угол наклона груши – загрузочный. Бетоносмеситель отключен.2.3. Отвесьте расчетную массу гранитного отсева. Отсев высыпьте в грушу бетоносмесителя. Угол наклона груши – загрузочный. Бетоносмеситель отключен.2.4. Переведите грушу бетоносмесителя в рабочее положение. Включите бетоносмеситель. Период перемешивания – 1 минута. После перемешивания отключите бетоносмеситель и переведите угол наклона груши в загрузочное положение.2.5. Отвесьте расчетную массу портландцемента М500 Д0. Цемент высыпьте в грушу бетоносмесителя. Угол наклона груши – загрузочный. Бетоносмеситель отключен.2.6. Переведите грушу бетоносмесителя в рабочее положение. Включите бетоносмеситель. Период перемешивания – 1 – 2 минуты. 2.7. После окончания перемешивания цемента с минеральным заполнителем груша бетоносмесителя остается в рабочем положении. Бетоносмеситель работает. В замес вводится расчетная масса вода с затворенным С3. Здесь следует соблюдать следующие рекомендации: вода вводится несколькими порциями, в 4-5 заходов; временной промежуток между заходами – 10 – 15 секунд; вода вводится в «мертвую» зону груши бетоносмесителя.2.8. На третьем, четвертом заходе начинают формироваться катыши. Через 1-1,5 минуты осуществляется контроль качества катышей.
3. Контроль качества катышей
3.1. Общий объем катышей должен занимать от 80% до 90% всего объема замеса в груше бетоносмесителя. Нормальные катыши имеют форму шаров с диаметром от 3 до 6 см, занимают «активную» и «рабочую» зоны груши бетоносмесителя.3.2. Катыши в замесе не должны иметь пылевую поверхность, на ощупь катыш должен представлять собой плотную субстанцию. 3.3. Допускается повышенная мягкость катыша, особенно при получении замеса для легкого бетона.3.4. Допускается увеличение объема псевдо катышей до 30% при применении гранитного просева диаметром 5-10 мм. Но данное явление не желательно, особенно при производстве изделий с толщиной более 50 мм.
4. Колеровка катышного замеса
4.1. После того как оператор убедился в готовности катышей, им производится колеровка замеса согласно установленной рецептуре. ВНИМАНИЕ! Контроль качества замеса, а также корректировки влажности катышей не должны занимать по времени более 20 минут. «Живучесть» катышного замеса ограничена. Это связано с «жизнеспособностью» суперпластификатора С3, а также с тем, что длительное уплотнение катышей в работающем гравитационном бетоносмесителе резко снижает текучесть этих катышей на поверхности вибростола. 4.2. Согласно рецептуре вводится первая расчетная масса пигмента. По истечении заданного промежутка вводятся следующие расчетные массы пигментов. Все пигменты вводятся в «активную» зону. Допускается захват «рабочей зоны» но не более 20%. Желательно пигменты вводить не в одну точку, а в течение 2-3 секунд рассеивать над крутящейся массой катышей.
5. Заливка форм
5.1. Отколерованные катыши выбираются сначала из «активной» зоны, затем из «рабочей» зоны и равномерно распределяются по формам. 5.2. После того, как объем форм будет заполнен на 80%, оператор начинает выгружать псевдо катыши из «мертвой» зоны. Массой смеси нормальных катышей из «рабочей» зоны и псевдо катышей из «мертвой» зоны окончательно заполняются формы.5.3. После того как емкости форм полностью заполнены, вибростол выключается, и формы переносятся на стеллажи для набора распалубочной прочности.
6. Выдерживание периода набора распалубочной прочности
6.1. Формы, заполненные замесом, накрываются парниковой полиэтиленовой пленкой. Пленка должна плотно прилегать к поверхности бетона, залитого в формы. Все формы должны быть закрыты пленкой полностью. Не допускаются воздушные пузыри и складки.6.2. Температура в помещении, где проходит период набора распалубочной прочности, должна быть не менее +18 и не более +35 оС. Период набора распалубочной прочности составляет от 20 до 24 часов.
formbeton.org