Обработка отверстий: виды операций и используемый инструмент. Сверление отверстия
Сверление отверстий. Художественная обработка металла. Охрана труда
Сверление отверстий
Глухие отверстия на заданную глубину сверлят по втулочному упору на сверле или измерительной линейке, которая закреплена на станке.
Упор представляет собой втулку, имеющую отверстие с резьбой, в которое ввинчен винт, фиксирующийся в канавке сверла.
Для измерения сверло подводят до соприкосновения с поверхностью детали, сверлят на глубину конуса сверла и отмечают по стрелке начальное положение на линейке. Затем к этому показателю прибавляют заданную глубину сверления и получают цифру, до которой надо проводить сверление.
Некоторые сверлильные станки на измерительной линейке имеют упор, нижнюю грань которого устанавливают на цифре, до которой нужно сверлить. Упор который фиксирую винтом.
Осуществляя сверление глухих отверстий нужно время от времени доставать сверло из отверстия и очищать отверстие от стружки и, если необходимо, измерять глубину глубиномером штангенциркуля.
При сверлении неполных отверстий, в случаях, когда отверстие расположено у края, сверление можно производить попарно или изделие и прокладку.
Пластины-прокладки должны быть из того же материала, что и деталь. Обе детали или деталь и прокладку зажимают в тисках и сверлят полное отверстие.
Если необходимо просверлить сквозное отверстие в уголке, необходимо закрепить его в тисках на деревянной прокладке.
Чтобы просверлить отверстия с уступами, нужно сначала просверлить отверстие по наименьшему диаметру, затем его рассверлить на один или два больших диаметра в пределах глубины каждой ступени.
Сверла меняют по количеству ступеней, последовательно увеличивая их диаметр. Другой способ сверления отверстий с уступами состоит в том, что сначала сверлят сверлом наибольшего диаметра, а затем сверлом меньшего диаметра по числу ступеней.
При первом способе сверло не уводит в сторону, оно хорошо центрируется. Измерить глубину сверления легче при втором способе, так как глубиномер тогда упирается в дно отверстия.
При сверлении отверстий в плоскостях, расположенных под углом, чтобы сверло не отклонялось в стороны и не ломалось, сначала готовят площадку перпендикулярно оси просверливаемого отверстия (фрезеруют или зенкуют), между плоскостями вставляют деревянные вкладыши или подкладки, затем сверлят отверстие обычным способом.
На цилиндрической поверхности отверстия сверлят следующим образом. Сначала перпендикулярно оси сверления на цилиндрической поверхности делают площадку, накернивают центр, затем сверлят отверстие обычным способом. При сверлении полых деталей полость забивают деревянной пробкой.
Для сверления отверстий в тонком листовом металле выбирают перовые сверла, так как обычным сверлом просверлить очень трудно из-за того, что глубина сверления меньше длины заборного конуса: режущие кромки сверла будут цепляться за обрабатываемый материал и рвать его.
Глубоким сверлением называют сверление отверстий на глубину, превышающую диаметр сверла в 5 и более раз.
Сверление может быть кольцевым и сплошным. При сверлении спиральным сверлом отверстия надсверливают коротким сверлом с последующим сверлением нормальным сверлом на полную глубину. Просверливая глубокое отверстие, сверло из него периодически выводят, не останавливая станок, и удаляют из канавок накопившуюся стружку. Длина сверла должна соответствовать глубине сверления. Не рекомендуют сверлить отверстия большой глубины с двух сторон.
При сверлении легких сплавов нужно быть особенно внимательным. Сложно сверлить алюминиевые и магниевые сплавы.
При сверлении магниевых сплавов на передней поверхности сверла делают фаску с передним углом 5 градусов шириной 0,2 – 0,6 мм в зависимости от диаметра. В этом случае, чем больше диаметр сверла, тем шире фаска. При обработке магниевых сплавов не рекомендуется большие скорости, так как эти сплавы могут воспламеняться.
При обработке магниевых магниевых сплавов применяют сверла с большими передними углами, малыми углами при вершине (24 – 90 градусов) и большими задними углами (15 градусов).
Для обработки алюминиевых сплавов изготовляют сверла с большими углами при вершине (65 – 70 градусов) и углами наклона винтовых канавок (35 – 45 градусов), чем у сверл для обработки черных металлов. Задний угол равен 8 – 10 градусам.
Причинами брака при сверлении могут быть неисправность станка, инструмента, приспособления, неправильная установка и крепление детали. Причиной брака может быть поломка сверла, которое может сломаться в случае, если металл некачественный, с пустотами или твердыми включениями – сверло отклоняется в сторону и ломается. Затупление и поломка сверла часто происходит при сверлении сквозных отверстий. Чтобы этого не случилось, нужно уменьшить подачу в момент выхода сверла в два раза.
Происходят поломки, если сверло неправильно заточено или тупое. Работать нужно только исправным инструментом, надежно и плотно закрепив сверло в патроне.
Неплотность и игра сверла приводят либо его к поломке, либо к неточному отверстию. Поломка может произойти из-за слишком большой скорости резания или из-за чрезмерно большой подачи. При глубине сверления больше режущей части сверла, канавки забиваются стружкой, что вызывает сильный нагрев сверла, сверло притупляется и может сломаться.
Сверлильные работы требуют внимательности и осторожности. При помехе в работе или необычайном звуке сверление прекращают до выяснения причин неисправности и их устранений.
В работе над скульптурой малых форм можно ограничиться небольшим набором инструментов и сравнительно несложными техническими приемами обработки металлов. При изготовлении садовой скульптуры крупных форм понадобятся знания слесарных и кузнечных работ художников и мастеров.
Следующая глава >
diy.wikireading.ru
Сверление отверстия в металле, в дереве. Сверление больших отверстий в стене
В список основных операций механической обработки материалов входит сверление. С помощью специального оборудования мастер формирует отверстия с определенными параметрами, которые в дальнейшем могут выполнять разные функции. Причем мероприятия такого рода выполняются и над отдельными элементами стройматериалов, и над готовыми конструкциями. В частности, сверление отверстия в перегородке может производиться с целью прокладки коммуникационных трасс. В зависимости от характеристик обрабатываемого материала применяется соответствующее оборудование.
Описание механической обработки сверлением
Чаще всего данная операция представляет собой резку материала, в результате которой формируется отверстие цилиндрической формы. Но бывают и другие сечения – это зависит от применяемого инструмента. В определении параметров получаемого отверстия учитывается две основные характеристики – глубина и диаметр. В соответствии с требуемыми показателями подбирается и оборудование с режущей головкой подходящего типоразмера. Что касается самого инструмента, с помощью которого можно выполнить сверление отверстия, то он представлен широким диапазоном устройств и агрегатов с разными характеристиками. Наибольшей популярностью пользуются электродрели, которые можно использовать и в работе с твердотельными материалами. Главное – подобрать соответствующую насадку. Для мягких стройматериалов достаточно применения и ручных механических дрелей.
Сверление отверстий в металле
Для обработки металлических деталей обычно используют электрические аппараты, которые снабжаются сверлами из углеродистой стали. Перед работой очень важно правильно выполнить разметку будущих отверстий. Обычно это делается керном. Это приспособление даже на твердых поверхностях позволяет образовать коническое углубление, которое станет основой для «бурения». Чтобы не испортить заготовку, сверление отверстий в металле желательно выполнять только головками, у которых есть режущие кромки. Наличие последних зависит от качества выполнения заточки сверла. Дело в том, что угол конуса может быть разным и определяется твердостью материала, для которого он предназначен. Чем тверже марка металла, тем больше должен быть этот угол, например, для стали обычно выполняется заточка на 120 градусов.
Сверление древесины
Дерево является одним из самых податливых в обработке материалов, что и обусловило широкое разнообразие инструментов, позволяющих выполнить такого рода сверление. Простейшим способом реализации такой процедуры является применение буравчика, но он подходит только для формирования отверстий небольшого диаметра. В основном же используется дрель. Достаточно применять механическое приспособление, в котором крепится сверло. Несмотря на мягкую структуру материала, сверление отверстий в дереве требует большой аккуратности. Необходимо строго выдерживать вертикальность рабочего элемента и в то же время оказывать умеренный нажим. Качество выполнения таких операций во многом зависит от положения мастера. В процессе радиального сверления цилиндрических деревянных изделий сверло может «уводить». Предотвратить подобные явления можно при помощи кондуктора, который обеспечит необходимый баланс положения функционального элемента.
Сверление отверстий в стене
Эта задача является наиболее сложной, поскольку материалы сооружения стен отличаются твердостью и жесткостью. Наиболее эффективным инструментом для таких задач является перфоратор с алмазной коронкой, но в некоторых случаях можно обойтись и электродрелью. Самое главное – правильно подобрать устройство по рабочим характеристикам. Мощность аппарата должна составлять не меньше 600 Вт, а частота – до 2500 об/мин. Наибольшие сложности может вызвать сверление больших отверстий для прокладки вентиляционных трасс. Диаметр такого канала может составлять 18-20 см. Создать такое отверстие поможет твердосплавное сверло, диаметр которого составляет не менее 12 мм. То есть формирование нужного по размеру отверстия придется выполнять целой серией подходов. Для начала следует обозначить контуры будущего канала, после чего с небольшими отступами делать по ним отверстия. На финальном этапе можно будет аккуратно высадить ненужный фрагмент.
Технические нюансы в процессе сверления
Механические операции влекут за собой сильные перегревы рабочих элементов. Негативные последствия таких процессов могут отразиться и в виде порчи обрабатываемого материала, и в деформации сверла. Для предотвращения перегрева следует использовать охлаждающие жидкости и смазки. Для механического инструмента будет достаточно обычной воды, а если планируется сверление отверстия с помощью мощного электрического аппарата, то следует подготовить специальную эмульсию. Кроме того, работа со стенами может сопровождаться обильным образованием бетонной пыли. Чтобы исключить загрязнение всей площадки, будет не лишним изначально предусмотреть возможность снабжения электроинструмента специальным пылесосом, который в ходе выполнения операции будет собирать мусор.
Заключение
Технологическое развитие строительного инструмента позволяет сегодня качественно выполнять широкий спектр мероприятий по механической обработке, в том числе и сверление. Причем совершенствуется не только оборудование, но и режущие элементы. Улучшение высокопрочных твердосплавных насадок позволяет справляться и с металлом, и с кирпичом. Причем выполнять сверление отверстия такого типа можно без подключения специалистов. Правда, основы эксплуатации электроинструмента и в целом особенности технологического процесса знать все же необходимо. Со своей стороны, производители сверлильного оборудования также стремятся идти навстречу обычному потребителю. В результате наряду с повышением технико-эксплуатационных параметров такой инструмент обретает эргономичные рукоятки, системы безопасности и защиты от тех же перегревов.
fb.ru
Обработка отверстий (сверление, цекование, развертывание и др.) и инструмент
Обработка отверстий – это целый ряд технологических операций, целью которых является доведение геометрических параметров, а также степени шероховатости внутренней поверхности предварительно выполненных отверстий до требуемых значений. Отверстия, которые обрабатываются при помощи таких технологических операций, могут быть предварительно получены в сплошном материале не только при помощи сверления, но также методом литья, продавливания и другими способами.
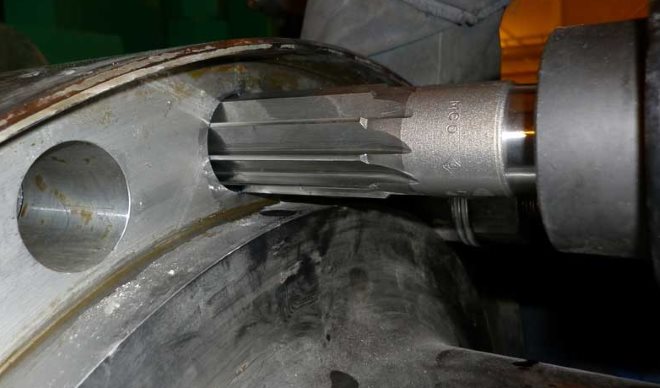
Обработка высверленного отверстия цилиндрическим зенкером
Конкретный способ и инструмент для обработки отверстий выбираются в соответствии с характеристиками необходимого результата. Различают три способа обработки отверстий – сверление, развертывание и зенкерование. В свою очередь эти методы подразделяются на дополнительные технологические операции, к которым относятся рассверливание, цекование и зенкование.
Чтобы понять особенности каждого из вышеперечисленных способов, стоит рассмотреть их подробнее.
Сверление
Чтобы обрабатывать отверстия, их необходимо предварительно получить, для чего можно использовать различные технологии. Наиболее распространенной из таких технологий является сверление, выполняемое с использованием режущего инструмента, который называется сверлом.
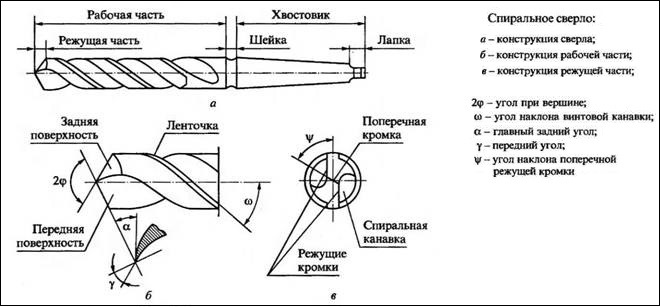
Основные части спирального сверла
При помощи сверл, устанавливаемых в специальных приспособлениях или оборудовании, в сплошном материале можно получать как сквозные, так и глухие отверстия. В зависимости от используемых приспособлений и оборудования сверление может быть:
- ручным, выполняемым посредством механических сверлильных устройств или электро- и пневмодрелей;
- станочным, осуществляемым на специализированном сверлильном оборудовании.

Физика сверления отверстий
Использование ручных сверлильных устройств является целесообразным в тех случаях, когда отверстия, диаметр которых не превышает 12 мм, необходимо получить в заготовках из материалов небольшой и средней твердости. К таким материалам, в частности, относятся:
- конструкционные стали;
- цветные металлы и сплавы;
- сплавы из полимерных материалов.
Если в обрабатываемой детали необходимо выполнить отверстие большего диаметра, а также добиться высокой производительности данного процесса, лучше всего использовать специальные сверлильные станки, которые могут быть настольными и стационарными. Последние в свою очередь подразделяются на вертикально- и радиально-сверлильные.
Рассверливание – тип сверлильной операции – выполняется для того, чтобы увеличить диаметр отверстия, сделанного в обрабатываемой детали ранее. Рассверливание также выполняется при помощи сверл, диаметр которых соответствует требуемым характеристикам готового отверстия.
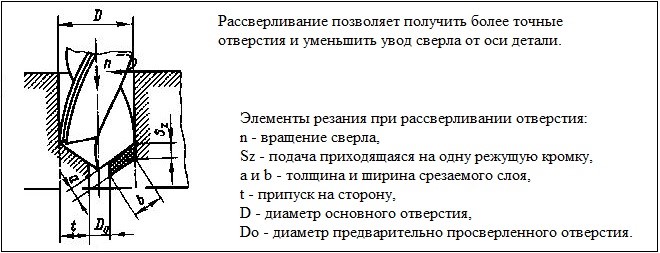
Физика рассверливания отверстий
Такой способ обработки отверстий нежелательно применять для тех из них, которые были созданы методом литья или посредством пластической деформации материала. Связано это с тем, что участки их внутренней поверхности характеризуются различной твердостью, что является причиной неравномерного распределения нагрузок на ось сверла и, соответственно, приводит к его смещению. Формирование слоя окалины на внутренней поверхности отверстия, созданного с помощью литья, а также концентрация внутренних напряжений в структуре детали, изготовленной методом ковки или штамповки, может стать причиной того, что при рассверливании таких заготовок сверло не только сместится с требуемой траектории, но и сломается.
При выполнении сверления и рассверливания можно получить поверхности, шероховатость которых будет доходить до показателя Rz 80, при этом точность параметров формируемого отверстия будет соответствовать десятому квалитету.Зенкерование
При помощи зенкерования, выполняемого с использованием специального режущего инструмента, решаются следующие задачи, связанные с обработкой отверстий, полученных методом литья, штамповки, ковки или посредством других технологических операций:
- приведение формы и геометрических параметров имеющегося отверстия в соответствие с требуемыми значениями;
- повышение точности параметров предварительно просверленного отверстия вплоть до восьмого квалитета;
- обработка цилиндрических отверстий для уменьшения степени шероховатости их внутренней поверхности, которая при использовании такой технологической операции может доходить до значения Ra 1,25.

При зенкеровании прикладывается меньшая сила реза, чем при сверлении, и отверстие получается более точное по форме и размерам
Если такой обработке необходимо подвергнуть отверстие небольшого диаметра, то ее можно выполнить на настольных сверлильных станках. Зенкерование отверстий большого диаметра, а также обработка глубоких отверстий выполняются на стационарном оборудовании, устанавливаемом на специальном фундаменте.
Ручное сверлильное оборудование для зенкерования не используется, так как его технические характеристики не позволяют обеспечить требуемую точность и шероховатость поверхности обрабатываемого отверстия. Разновидностями зенкерования являются такие технологические операции, как цекование и зенкование, при выполнении которых используются различные инструменты для обработки отверстий.
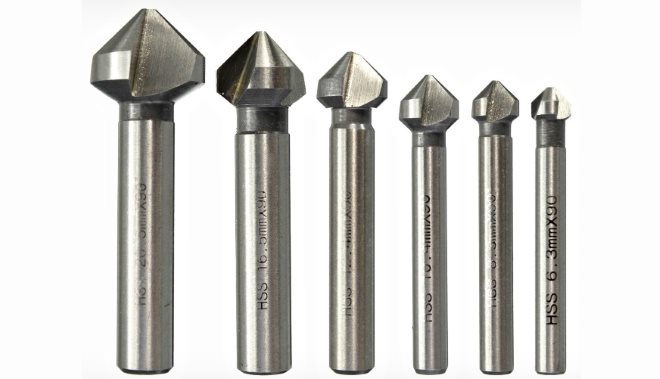
Зенкеры конусные по металлу
Специалисты дают следующие рекомендации для тех, кто планирует выполнить зенкерование.
- Зенкерование следует проводить в процессе той же установки детали на станке, при которой осуществлялось сверление отверстия, при этом из параметров обработки меняется только тип используемого инструмента.
- В тех случаях, когда зенкерованию подвергается необработанное отверстие в деталях корпусного типа, необходимо контролировать надежность их фиксации на рабочем столе станка.
- Выбирая величину припуска на зенкерование, надо ориентироваться на специальные таблицы.
- Режимы, на которых выполняется зенкерование, должны быть такими же, как и при осуществлении сверления.
- При зенкеровании должны соблюдаться те же правила охраны труда и техники безопасности, как и при сверлении на слесарно-сверлильном оборудовании.
Зенкование и цекование
При выполнении зенкования используется специальный инструмент – зенковка. При этом обработке подвергается только верхняя часть отверстия. Применяют такую технологическую операцию в тех случаях, когда в данной части отверстия необходимо сформировать углубление для головок крепежных элементов или просто снять с нее фаску.
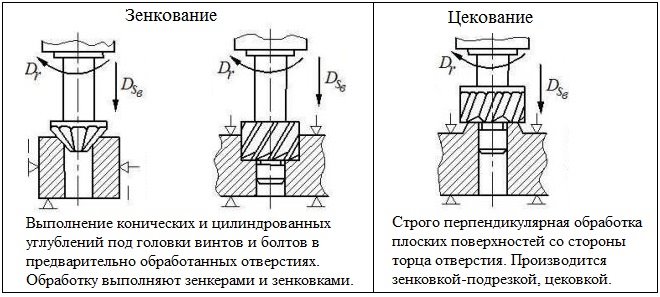
Чем различаются зенкование и цекование
При выполнении зенкования также придерживаются определенных правил.
- Выполняют такую операцию только после того, как отверстие в детали будет полностью просверлено.
- Сверление и зенкование выполняются за одну установку детали на станке.
- Для зенкования устанавливают небольшие обороты шпинделя (не больше 100 оборотов в минуту) и применяют ручную подачу инструмента.
- В тех случаях, когда зенкование осуществляется цилиндрическим инструментом, диаметр цапфы которого больше диаметра обрабатываемого отверстия, работу выполняют в следующей последовательности: сначала сверлится отверстие, диаметр которого равен диаметру цапфы, выполняется зенкование, затем основное отверстие рассверливается на заданный размер.
Целью такого вида обработки, как цекование, является зачистка поверхностей детали, которые будут соприкасаться с гайками, головками болтов, шайбами и стопорными кольцами. Выполняется данная операция также на станках и при помощи цековки, для установки которой на оборудование применяются оправки.
Развертывание
Процедуре развертывания подвергаются отверстия, которые предварительно были получены в детали при помощи сверления. Обработанный с использованием такой технологической операции элемент может иметь точность, степень которой доходит до шестого квалитета, а также невысокую шероховатость – до Ra 0,63. Развертки делятся на черновые и чистовые, также они могут быть ручными или машинными.
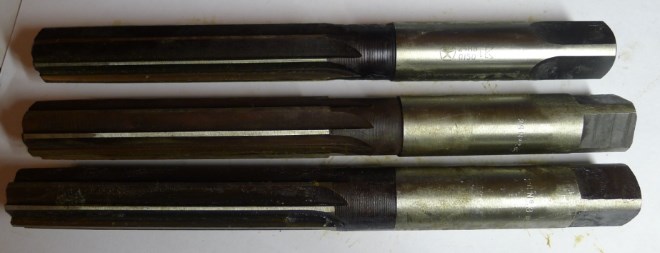
Цилиндрические ручные развертки 24Н8 0150
Рекомендации, которых следует придерживаться при выполнении данного вида обработки, заключаются в следующем.
- Припуски в диаметре обрабатываемого отверстия выбираются по специальным таблицам.
- При использовании ручного инструмента, который вращают только по часовой стрелке, сначала выполняют черновое, а потом чистовое развертывание.
- Обработку стальных деталей выполняют с обязательным использованием СОЖ, чугунных – всухую.
- Машинное развертывание проводят сразу после сверления на станке – с одной установки детали.
- Для контроля качества результата используют специальные калибры.
Оценка статьи:

Поделиться с друзьями:
met-all.org
Сверление отверстий на сверлильном станке

Категория:
Сверление металла

Сверление по разметке. Перед началом работы на сверлильном станке подготовляют рабочее место. Инструмент должен быть установлен в шпинделе надежно и правильно, а изделие — неподвижно закреплено на столе станка. Нельзя допускать биения сверла, которое обычно происходит из-за неправильной его установки. Рукоятки (рычаги) управления скоростями станка переводят в положение, соответствующее выбранному режиму резания.
Приступая к сверлению, нужно пустить станок и подвести сверло к изделию плавно, без ударов: оно установится вершиной точно в накерненном углублении. Сверление по разметке выполняют в два приема: сначала производят пробное сверление, а затем окончательное. При пробном сверлении надсверливают при ручной подаче небольшое углубление размером около lU диаметра отверстия, потом сверло поднимают, удаляют стружку и проверяют совпадение засверленного углубления с центром размеченной окружности. Если такое совпадение есть, можно
продолжить сверление и довести его до конца. Если же надсверленное углубление отошло от центра, то его исправляют, для чего прорубают от центра в ту сторону углубления, куда нужно сместить сверло, две-три канавки. Сделав еще одно надсверливание и убедившись в его правильности, доводят сверление до конца.
При сверлении необходимо быть очень внимательным. Надо изредка выводить сверло из отверстия и освобождать его канавки от стружки. Вводить обратно сверло в отверстие нужно осторожно, так как его легко сломать. Если производится сверление сквозного отверстия, то в момент выхода из него сверла надо выключить автоматическую подачу и перейти на ручную, ослабив нажим на сверло.
При диаметрах свыше 30 мм отверстия сверлят в два приема: сначала сверлом меньшего диаметра, а затем сверлом в окончательный размер.
Если требуется повышенная чистота поверхности отверстия, то рассверливание производят зенкером или, для еще большей чистоты, развертками, иногда в несколько переходов.
Рассмотрим несколько примеров сверления отверстий на сверлильных станках.
Сверление в чугунном бруске сквозного отверстия диаметром 20 мм. При выполнении этой работы следует придерживаться такой последовательности действий:1) получить заготовку и сверло;2) подготовить рабочее место;3) разметить брусок, нанеся на его широкую плоскость по диагоналям (с угла на угол) две риски, накернить центр отверстия; очертить циркулем контрольную окружность диаметром 20,5 мм и накернить ее;4) поставить на стол сверлильного станка машинные тиски и зажать в них брусок, предварительно очистив стол станка, тиски и брусок от стружек;5) определить наиболее производительный режим сверления;6) настроить станок на выбранное число оборотов шпинделя и выбранную подачу;7) установить сверло в шпинделе станка;8) пустить станок в ход и проверить, не бьет ли сверло;9) подвести сверло к намеченному кернером центру и засверлить пробное углубление, отвести сверло от бруска;10) проверить совпадение надсверленного углубления с центром контрольной окружности; если обнаружится увод в сторону, устранить его;11) исправив надсверленное углубление, окончательно просверлить отверстие;12) остановить станок, снять брусок, вынуть из шпинделя сверло и очистить станок от стружек.
Рис. 1. Прорубание канавок при уводе надсверленного углубления в сторону
Рис. 2. Чертеж чугунного бруска
Рис. 3. Сверление отверстия в угольнике: а — с зажимом детали в тисках; б — с зажимом детали в приспособлении; 1 — сверло, 2 — угольник (обрабатываемая деталь), 3 — подкладка, 4 — тиски или приспособление, 5 — стол станка
Сверление в угольнике сквозных отверстий диаметром 8 мм. Материал — мягкая сталь.
Работу над каждым отверстием нужно выполнять так:1) зажать угольник в тисках или в специальном приспособлении;2) выбрать режим обработки;3) настроить станок на выбранное число оборотов шпинделя и выбранную подачу;4) вставить сверлильный патрон или переходные втулки в шпиндель станка;5) закрепить сверло и проверить его на биение;6) подвести сверло к намеченному углублению;7) пустить станок;8) засверлить пробное углубление и проверить его по контрольным окружностям; остановить станок и исправить увод углубления, если он имеется;9) пустить станок, вновь засверлить небольшое углубление, проверить, устранен ли увод;10) окончательно просверлить отверстие;11) переставить угольник в тисках для сверления отверстия на другой его полке;12) повторить операции, указанные в пп. 8—11;13) остановить станок;14) снять с тисков угольник, вынуть сверло, очистить станок.
Рис. 4. Сверление несквозного отверстия: а—чертеж детали; б —установка детали для сверления; 1 — приспособление, 2 — прижимная планка, 3 — призмы
Сверление в валике несквозного отверстия. Центр отверстия размечен.
Эту работу выполняют следующим образом:1) приготовляют инструмент и приспособления;2) устанавливают и закрепляют валик на столе станка;3) определяют требуемое число оборотов шпинделя;4) настраивают станок на установленное число оборотов шпинделя и на заданную глубину сверления;5) закрепляют сверло в патроне и проверяют его на биение;6) засверливают пробное углубление и проверяют его совпадение с контрольной риской;7) окончательно просверливают отверстие;8) останавливают станок, вынимают сверло и патрон, снимают со стола станка валик, очищают станок от стружек.
На рис. 5 показаны другие случаи сверления отверстий.
Сверление по кондуктору.
Рис. 5. Примеры сверления
Рис. 6. Сверление в приспособлениях: а и б — типы кондукторов
Кондуктор накладывают на ту часть поверхности изделия, где нужно просверлить отверстия. Крепят кондуктор на изделии боковыми винтами или прижимами различных конструкций.
Коробчатый кондуктор имеет форму коробки с откидной крышкой. Обрабатываемое изделие закладывают внутрь коробки и крепят крышкой. Для сверления сверло вводят в соответствующую направляющую втулку кондуктора и просверливают в изделии отверстие. Пользование кондуктором сокращает время на установку и выверку изделий; кроме того, отпадает надобность в разметке и пробном надсверливании.
Сверление глухих отверстий. Глухие отверстия свер. лят на требуемую глубину, пользуясь упорным приспособлением, имеющимся на сверлильном станке, или же (если такого приспособления нет) упорной втулкой, закрепленной на сверле. Глубину сверления отмечают на сверле мелом или карандашом. В случаях пользования упором станка сверло, закрепленное в шпинделе, опускают на изделие, а упорный стержень устанавливают и закрепляют на высоте, соответствующей глубине отверстия. Когда сверло опустится на установленную глубину, упорный стержень, дойдя до ограничителя, остановится. В результате этого при ручной подаче сверло не сможет продвинуться дальше в металл, а при автоматической подаче движение сверла прекратится.
Сверление неполных отверстий. Для получения неполных отверстий (полуотверстий) закрепляют в тисках по две детали так, чтобы поверхности их, на которых должны быть просверлены неполные отверстия, совпали. Размечают на линии стыка закрепленных деталей центры отверстий и производят сверление обычным способом.
Рис. 7. Сверление несквозных от< верстий по втулочному упору на сверле: 1 — быстродействующее зажимное приспособление, 2 — изделие, 3 — упорная втулка
Сверление «пакетом». При сверлении тонких деталей для ускорения работы обычно собирают несколько штук деталей в «пакет», сжимают его струбцинами, зажимают в тисках и производят сверление собранных таким образом деталей одновременно.
Читать далее:
Ручное сверление металла
Статьи по теме:
pereosnastka.ru
Сверление отверстий
Сверление отверстий
Подробности Категория: Тонколистовой металлПробивание и сверление отверстий.
Отверстия в тонколистовом металле можно получить пробиванием или сверлением.
Для пробивания отверстий диаметром до 8 мм применяют пробойник (бородок) — стальной стержень с плоской рабочей поверхностью (см.рис. справа а).Лист жести кладут на торец деревянного бруска, пробойник устанавливают в нужной точке и ударами слесарного молотка по бойку пробивают отверстие(см.рис. справа б). Края полученного отверстия с нижней стороны листа выравнивают ударами киянки или молотка.
На заводах для получения отверстий в листовом металле вместо пробойника применяют специальный инструмент — пуансон. Пробивают отверстия на штамповочном прессе (см.рис. слева). Лист или несколько листов кладут на матрицу с одним или несколькими отверстиями. Пуансон или несколько пуансонов под давлением входят в матрицу и пробивают отверстия, выталкивая отходы — кружки диаметром, равным диаметру отверстий.
При пробивании отверстий работать исправным молотком.Не держать пальцы около рабочей части пробойника.
Более точные отверстия в металле можно получить сверлением.Сверлением называется технологическая операция по обработке материалов резанием с помощью сверла.
При этом выполняют те же приемы и правила безопасной работы, что и при сверлении отверстий в древесине. Место расположения отверстия намечают кернером, чтобы сверло не скользило по заготовке (см.рис. справа).
Существуют различные виды сверл. Наиболее распространенные из них — спиральные (см.рис. слева). Во время сверления режущая часть сверла врезается в материал изделия и снимает стружку, которая затем отводится через винтовые канавки, расположенные на направляющей части. Ленточка позволяет уменьшить трение сверла о стенки отверстия. Хвостовик с лапкой служит для закрепления сверла во время сверления.
При сверлении изделие закрепляется неподвижно, а сверлу сообщается одновременно два движения: движение резания — вращательное вокруг оси и движение подачи — поступательное вдоль оси сверла.
Инструменты и приспособления для сверления.
При сверлении часто возникает необходимость расширить верхнюю часть отверстия, чтобы углубить в нее головку болта, винта, шурупа и т. д. Для этого используют сверло большего диаметра или специальный инструмент — зенковку (см.рис. справа).
Операцию по обработке верхней части отверстия зенковкой называют зенкованием.
Для закрепления заготовки во время сверления обычно используют машинные тиски (см.рис. справа). На их основании закреплена неподвижная губка, а по направляющей с помощью винта с рукояткой может перемещаться подвижная губка.Изделие устанавливают между губками и вращением винта рукояткой передвигают подвижную губку и прочно закрепляют изделие в тисках.Если сверление производится на сверлильном станке, то сами тиски можно закрепить на столе станка. Для этого в основании тисков сделаны выемки, а на столе станка имеются специальные пазы. Установив в пазы стола и выемки основания тисков болты с гайкой, тиски закрепляют на столе сверлильного станка.
Перед установкой машинных тисков тщательно протрите опорные плоскости стола и основания тисков и слегка смажьте их машинным маслом.При сверлении отверстий малого диаметра тиски закреплять необязательно.
Устройство сверлильного станка и приемы работы.
Сверлильный станок, как и любая технологическая машина, состоит из следующих составных частей: двигателя, передаточного механизма, рабочего органа, органов управления. Передаточный механизм служит для передачи движения от электродвигателя к рабочему органу, которым является сверло. Оно крепится в патроне, насаженном на вращающийся вал — шпиндель.
Вращение от электродвигателя к шпинделю передается с помощью ременной передачи. Поворотом рукоятки подачи патрон со сверлом можно поднимать или опускать с помощью реечной передачи.На передней панели станка расположены кнопки включения и выключения электродвигателя. Включают станок нажатием на одну из крайних кнопок в зависимости от необходимого направления вращения шпинделя. Выключают станок нажатием на среднюю кнопку красного цвета.К основанию станка неподвижно прикреплен вертикальный винт-колонна. Поворотом рукоятки можно перемещать шпиндельную бабку вниз и вверх вдоль винта-колонны, а рукояткой фиксировать ее в необходимом положении.Для контроля глубины глухих отверстий предусмотрена шкала.В зависимости от материала заготовки требуется различная скорость сверления. Для этого устанавливают необходимую частоту вращения шпинделя, перебрасывая ремень ременной передачи на шкивы разных диаметров.
Перед сверлением убирают с рабочего стола станка все лишние предметы. Заготовку с накерненными центрами отверстий закрепляют в тисках. Сверло необходимого диаметра вставляют в патрон и закрепляют специальным ключом. Для проверки правильности установки сверла кратковременно включают станок (с разрешения учителя). Если сверло установлено в патроне правильно, его острие при вращении не описывает окружность. Если сверло установлено с перекосом и наблюдается его биение, то станок выключают и закрепляют сверло правильно. Затем, поворачивая рукоятку подачи, опускают сверло и устанавливают тиски с заготовкой так, чтобы керн совпал с острием сверла.
Включают станок и сверлят отверстие, плавно нажимая на рукоятку подачи без рывков и больших усилий. При сверлении сквозных отверстий заготовку устанавливают на деревянный брусок, чтобы не сломать сверло и не испортить стол станка(см.рис. справа). При сверлении глубоких отверстий необходимо время от времени выводить сверло из отверстия и охлаждать его, окуная в емкость с охлаждающей жидкостью. В конце сверления силу нажима на рукоятку подачи необходимо уменьшить. Просверлив отверстие, нужно, плавно поворачивая штурвал подачи, поднять шпиндель в крайнее верхнее положение и выключить станок.
Сверление можно выполнять ручной дрелью, электродрелью(см. рис. слева).
При сверлении тонколистового металла обычное спиральное сверло сминает и рвет заготовку. В этом случае применяют сверла со специальной заточкой (см.рис. справа).
Работать на сверлильном станке можно только с разрешения учителя.При работе на станке рабочий халат должен быть застегнут на все пуговицы, волосы убраны под головной убор.При сверлении пользоваться защитными очками.Устанавливать сверло в патрон и заготовку в тиски, а также убирать стружку со стола следует только после отключения станка.Нельзя тормозить руками вращающийся патрон.Не отходить от станка, не выключив его.Надежно закреплять заготовку в тисках, сверло в патроне и патрон в шпинделе.При сверлении электродрелью нельзя сильно нажимать на ручку дрели.Ось вращения сверла при работе дрелью должна быть строго перпендикулярна плоскости заготовки.
На предприятиях сверлильные станки обслуживают сверловщики. Они должны знать устройство станка, уметь его налаживать и обслуживать, выбирать правильную скорость сверления, уметь пользоваться различными приспособлениями для сверления, затачивать инструменты, разбираться в чертежах.В цехах заводов применяются более сложные станки, чем мы только что рассмотрели. Это вертикально-сверлильные, радиально-сверлильные, многошпиндельные станки и станки-автоматы, выполняющие без участия человека сверлильные операции по заданной программе.
technologys.info
Сверление отверстий. Художественная обработка металла. Охрана труда
Сверление отверстий
Глухие отверстия на заданную глубину сверлят по втулочному упору на сверле или измерительной линейке, которая закреплена на станке.
Упор представляет собой втулку, имеющую отверстие с резьбой, в которое ввинчен винт, фиксирующийся в канавке сверла.
Для измерения сверло подводят до соприкосновения с поверхностью детали, сверлят на глубину конуса сверла и отмечают по стрелке начальное положение на линейке. Затем к этому показателю прибавляют заданную глубину сверления и получают цифру, до которой надо проводить сверление.
Некоторые сверлильные станки на измерительной линейке имеют упор, нижнюю грань которого устанавливают на цифре, до которой нужно сверлить. Упор который фиксирую винтом.
Осуществляя сверление глухих отверстий нужно время от времени доставать сверло из отверстия и очищать отверстие от стружки и, если необходимо, измерять глубину глубиномером штангенциркуля.
При сверлении неполных отверстий, в случаях, когда отверстие расположено у края, сверление можно производить попарно или изделие и прокладку.
Пластины-прокладки должны быть из того же материала, что и деталь. Обе детали или деталь и прокладку зажимают в тисках и сверлят полное отверстие.
Если необходимо просверлить сквозное отверстие в уголке, необходимо закрепить его в тисках на деревянной прокладке.
Чтобы просверлить отверстия с уступами, нужно сначала просверлить отверстие по наименьшему диаметру, затем его рассверлить на один или два больших диаметра в пределах глубины каждой ступени.
Сверла меняют по количеству ступеней, последовательно увеличивая их диаметр. Другой способ сверления отверстий с уступами состоит в том, что сначала сверлят сверлом наибольшего диаметра, а затем сверлом меньшего диаметра по числу ступеней.
При первом способе сверло не уводит в сторону, оно хорошо центрируется. Измерить глубину сверления легче при втором способе, так как глубиномер тогда упирается в дно отверстия.
При сверлении отверстий в плоскостях, расположенных под углом, чтобы сверло не отклонялось в стороны и не ломалось, сначала готовят площадку перпендикулярно оси просверливаемого отверстия (фрезеруют или зенкуют), между плоскостями вставляют деревянные вкладыши или подкладки, затем сверлят отверстие обычным способом.
На цилиндрической поверхности отверстия сверлят следующим образом. Сначала перпендикулярно оси сверления на цилиндрической поверхности делают площадку, накернивают центр, затем сверлят отверстие обычным способом. При сверлении полых деталей полость забивают деревянной пробкой.
Для сверления отверстий в тонком листовом металле выбирают перовые сверла, так как обычным сверлом просверлить очень трудно из-за того, что глубина сверления меньше длины заборного конуса: режущие кромки сверла будут цепляться за обрабатываемый материал и рвать его.
Глубоким сверлением называют сверление отверстий на глубину, превышающую диаметр сверла в 5 и более раз.
Сверление может быть кольцевым и сплошным. При сверлении спиральным сверлом отверстия надсверливают коротким сверлом с последующим сверлением нормальным сверлом на полную глубину. Просверливая глубокое отверстие, сверло из него периодически выводят, не останавливая станок, и удаляют из канавок накопившуюся стружку. Длина сверла должна соответствовать глубине сверления. Не рекомендуют сверлить отверстия большой глубины с двух сторон.
При сверлении легких сплавов нужно быть особенно внимательным. Сложно сверлить алюминиевые и магниевые сплавы.
При сверлении магниевых сплавов на передней поверхности сверла делают фаску с передним углом 5 градусов шириной 0,2 – 0,6 мм в зависимости от диаметра. В этом случае, чем больше диаметр сверла, тем шире фаска. При обработке магниевых сплавов не рекомендуется большие скорости, так как эти сплавы могут воспламеняться.
При обработке магниевых магниевых сплавов применяют сверла с большими передними углами, малыми углами при вершине (24 – 90 градусов) и большими задними углами (15 градусов).
Для обработки алюминиевых сплавов изготовляют сверла с большими углами при вершине (65 – 70 градусов) и углами наклона винтовых канавок (35 – 45 градусов), чем у сверл для обработки черных металлов. Задний угол равен 8 – 10 градусам.
Причинами брака при сверлении могут быть неисправность станка, инструмента, приспособления, неправильная установка и крепление детали. Причиной брака может быть поломка сверла, которое может сломаться в случае, если металл некачественный, с пустотами или твердыми включениями – сверло отклоняется в сторону и ломается. Затупление и поломка сверла часто происходит при сверлении сквозных отверстий. Чтобы этого не случилось, нужно уменьшить подачу в момент выхода сверла в два раза.
Происходят поломки, если сверло неправильно заточено или тупое. Работать нужно только исправным инструментом, надежно и плотно закрепив сверло в патроне.
Неплотность и игра сверла приводят либо его к поломке, либо к неточному отверстию. Поломка может произойти из-за слишком большой скорости резания или из-за чрезмерно большой подачи. При глубине сверления больше режущей части сверла, канавки забиваются стружкой, что вызывает сильный нагрев сверла, сверло притупляется и может сломаться.
Сверлильные работы требуют внимательности и осторожности. При помехе в работе или необычайном звуке сверление прекращают до выяснения причин неисправности и их устранений.
В работе над скульптурой малых форм можно ограничиться небольшим набором инструментов и сравнительно несложными техническими приемами обработки металлов. При изготовлении садовой скульптуры крупных форм понадобятся знания слесарных и кузнечных работ художников и мастеров.
Поделитесь на страничкеСледующая глава >
hobby.wikireading.ru
Глубокое сверление отверстий в металле: классификация и характеристики
Сверление отверстий — разновидность обработки металлов посредством вращающихся приспособлений способом резания. Данную операцию подразделяют на глубокое сверление и обычное. При первом варианте заглубление отверстия составляет больше 10 см либо имеет размер более чем 5 имеющихся диаметров (d*5). Сверлами получается добиться выемок разного заглубления и диаметра (с несколькими гранями сечения).

Схема сверла по металлу.
Сверление отверстий в металле возможно одним из следующих способов:
- Осуществляют вращение заготовки и одновременно производят продольную подачу не вращающегося инструмента для сверления.
- Вращение заготовки не осуществляют, она принимает фиксированное положение.
- Одномоментное движение вокруг своей оси и механизма, и детали.
На практике данные технологии достаточно востребованы. Большим спросом процедура формирования глубоких отверстий пользуется в таких областях, как изготовление труб, металлургия, аэрокосмическая и нефтегазовая сфера, производство плит теплообменников и др. Глубокие отверстия чаще приходится проделывать на следующих деталях: осях, гильзах, бандажах, валах, роторах, втулках, цилиндрах, скорлупах из металла и т.д.
Сверление глубоких отверстий: классификация

Схема сверления металла.
- По типу выведения высверливаемого содержимого (стружки) выделяют: кольцевую и сплошную процедуры. Во втором способе высверливаемое содержимое выводится наподобие стружечных частиц, в первом — кольцевая плоскость частично убирается наподобие стержня, а другая часть — стружкой.
- По методу резания выделяют технологии:
Одноштанговая (STS). Данный способ оптимален для изготовления заготовок в высокопроизводительном либо массовом процессе производства. Проблема здесь заключается в том, что приходится использовать маслоприемник с разнообразными шлангами подачи при одновременном вращении детали. Данная система признана самой эффективной при формировании отверстий высокого качества.
Эжекторная. Вариант глубокой обработки с параметрами изделий среднего качества. Обработка осуществляется на токарных станках с множеством сложных функций. Система предполагает применение дополнительной мобильной или установленной насосной станции. Данный метод позволяет получать отверстия с диаметром от 2 до 6 см в глубину до 120 см, в том числе прерывистого вида.
Ружейными (трубчато-лопаточными) сверлами с подачей изнутри охладительно-смазочного средства. Данный вариант подходит для небольших предприятий, в которых условиями технологии планируется получать отверстия малого диаметра.

Таблица подбора охлаждающей жидкости при сверлении разных видов металла.
Сверла с одинарным резцом запросто встраивают в станки универсального принципа действия. Резец изготавливают из твердых сплавов и на всем протяжении стержня у него расположена V-образная канавка. Преломляющий угол последней может достигать 110-1200º. Рекомендованный диаметр для просверливания — 3,5-4,0 см, длина — d*50. Этот способ не предусматривает проведения операций развертывания и зенкерования.
Автоматическое управление процессами позволяет выделить: глубокое воздействие с автоматизированной сменой одного либо многих режимных параметров (подачи смазки, скорости вращения и др.).
Вернуться к оглавлению
Характеристики процесса глубокого просверливания
При глубокой обработке соблюдают основные принципы технологического процесса.
Изначально выполняют подбор вращательной скорости сверлильной части оборудования либо максимально возможной скорости резания (подачи сверл).
Следят за обеспечением нормального дробления стружки, выводом содержимого из углублений полностью.
Важным нюансом в момент иссечения отходов считается сохранность резца инструмента. В этой части сверло повреждений иметь не должно, равно как и заусенцев и прочих изъянов. Еще одним ключевым критерием эффективной обработки поверхностей металла является подача охладительно-смазывающей жидкости по правилам.
Поскольку детали сверлятся в сопровождении подачи охладительно-смазывающей жидкости с некоторым давлением и с заданной величиной расхода, в систему вводят работу насосных устройств — маслонасосов либо насосов для перекачивания вязких веществ.
Мощность системы подбирают, основываясь на расходовании жидкости и необходимой величине давления для подачи смазочного средства.
Подача жидкости — непременный пункт технологии:
- Выполняется правильный вывод стружки из рабочей зоны по выводным каналам.
- Понижается сила трения между соприкасающимися элементами.
- Осуществляется выведение излишков тепла, образующегося при процедуре длительного сверления, при этом обеспечивается сохранность сверла.
- Производится дополнительная обработка выемки.
Вернуться к оглавлению
Некоторые сложности процесса
С увеличением заглубления появляется больше сложностей с обработкой выемки.
При глубоком просверливании задействуют специализированный инструмент, оснащенный технически с дополнительными возможностями применения режущих и других типов приспособлений. Это необходимо по той причине, что использование стандартных приспособлений не позволяет получить высокой производительности процесса, а иногда делает его невозможным.
Для решения технологических задач нередко требуется участие нестандартных приспособлений, коими может оснащаться спецоборудование.
moiinstrumenty.ru