Чем высокопрочный бетон отличается от обычного? Особенности материала и сфера применения. Сверхпрочный бетон
Чем высокопрочный бетон отличается от обычного? Особенности материала и сфера применения
Искусственный камень давно стал одним из самых распространенных материалов в строительстве. Несмотря на многообразие видов бетона, развитие и совершенствование композита происходит постоянно. Еще пару десятилетий назад высокопрочным считался бетон с классом В30, но в наши дни этот материал уже относится к рядовым. Современный высокопрочный бетон сочетает широкий спектр свойств, существенно отличающих его от классического искусственного камня.
Параметры такого материала уникальны и не описываются лишь высокими значениями прочности. Фактически подобный композит призван решать сразу несколько сложнейших технологических задач, именно поэтому понятие высокопрочного бетона объединяет несколько видов материалов и целый ряд характеристик.
Особенности композита
Получение высоких классов по прочности давно уже не считается сложной задачей. В номенклатуре многих советских заводов по производству железобетонных изделий и конструкций существовали подборы составов для классов В40, В45, В50 и даже В60. Такие бетоны использовались для производства конструкций, испытывающих существенные динамические нагрузки, например, шпал или мостовых пролетов. Но главной особенностью и свойством подобных материалов являлась низкая технологичность на этапе работы со смесью, ведь ее удобоукладываемость характеризовалась жесткостью на уровне Ж3 и выше.
Сверхпрочный бетон нового поколения представляет собой не просто материал с высокой стойкостью к различным механическим нагрузкам, но и высокотехнологичную смесь. Укладка такого материала в конструкцию любой геометрии не только не усложняется, но и позволяет сократить количество задействованных рабочих.
Высокая подвижность и плотная структура смеси обеспечивают способность самоуплотнения, что позволяет работать с материалом без применения вибраторов.
Способность к самостоятельному уплотнению
Именно свойства бетонной смеси существенно отличают камень высокой прочности, востребованный в строительной отрасли в настоящее время. За счет способности к самостоятельному заполнению формы и уплотнению он получил название самоуплотняющегося или СУБ.
Подобные свойства достигаются за счет создания уникальной структуры, предполагающей непрерывную гранулометрию всех компонентов. Фактически размер частиц в теле бетона изменяется от 5 мкм до 20 мм без разрывов, что позволяет получить так называемую реологически активную матрицу, способную течь и уплотняться под собственным весом. Благодаря сочетанию вяжущего, активных и инертных минеральных добавок, мелкого заполнителя различной крупности, система остается стабильной. Но подбор состава высокопрочного искусственного камня сложен, ведь создать сбалансированную систему из такого количества компонентов непросто.
Сферы применения
Подобный материал обладает весьма высокой себестоимостью, что существенно ограничивает область его использования. Кроме того, потенциал столь прочного бетона мало востребован в рядовых проектах и массовом строительстве.
Основной сферой применения сверхпрочного композита являются сложные по геометрии проекты или высотные здания. Раньше считалось, что бетон не способен выдерживать нагрузки при возведении сооружений в сотни этажей. Классический искусственный камень в основании здания и на первых его этажах разрушался из-за слишком большой нагрузки. Именно поэтому небоскребы возводили из металла и стекла.
Но современные сверхпрочные композиты способны не только выдержать такую нагрузку, но и позволяют сократить толщину всех несущих конструкций, что уменьшает общий вес здания. Именно поэтому высокопрочный бетон широко применяется при возведении современных высотных зданий. Его часто используют при заливке конструкций сложной геометрии, которые раньше собирались из нескольких элементов. Такой бетон часто применяют для изготовления мостовых пролетов большой длины.
Фактически подобный композит направлен на решение сложных архитектурных или инженерных задач и редко используется в массовом строительстве.
Основные характеристики
Сверхпрочный бетон нового поколения отличается широким набором свойств, поэтому чаще всего их делят на два блока.
Показатели бетонной смеси
К первому относят параметры бетонной смеси, среди которых основными считаются:
- подвижность с расплывом конуса на уровне 65 – 70 см;
- коэффициент уплотнения 1,0 – 1,4;
- время сохранения реологических свойств не менее 3 – 4 часов;
- минимальная расслаиваемость;
- воздухосодержание не более 1%.
Способность смеси сохранять свои свойства во времени крайне важна, ведь транспортировка материала от завода до объекта может занять пару часов. Не менее важно обеспечить однородность смеси, ведь расслоение приведет к полной потере свойств затвердевшего бетона.
Параметры готового камня
Ко второму блоку относят характеристики уже затвердевшего композита. К основным среди них можно отнести:
- прочность на сжатие в диапазоне 50 – 100 МПа и на растяжение при изгибе не менее 4 МПа;
- плотность и поровую структуру;
- низкую истираемость;
- морозостойкость от F400 и водонепроницаемость от W10;
- водополгощение не более 1%;
С учетом способности смеси такого бетона к образованию максимально плотного тела возникает опасность возникновения микротрещин из-за чрезмерных напряжений во время гидратации. Процесс твердения бетона сопровождается выделением большого количества тепла, а в материале столь плотной структуры этот избыток энергии просто некуда деть. Именно поэтому важно обеспечить адекватную поровую структуру, которая будет работать буфером для избытка энергии и напряжений.
Производство композита
Изготовление высокопрочного бетона по сравнению с обычным тяжелым раствором отличается большей сложностью. Во-первых, для обеспечения качественного смешения компонентов необходимо использовать современные двухвалковые скоростные смесители, способные фактически перетирать смесь сырьевых компонентов.
Во-вторых, чтобы обеспечить все свойства материала требуется соблюдать точное дозирование компонентов и очередность их загрузки. В результате вместо классических 3 – 4 бункеров требуется 6 – 8, что увеличивает стоимость установки. Любое колебание во влажности материалов приводит к выпуску брака, поэтому линии подачи песка и щебня оборудуются специальными датчиками влажности для постоянной корректировки расхода воды.
При изготовлении смеси сначала смешиваются материалы малых фракций, например, цемент, минеральная добавка и микронаполнитель. Затем добавляется песок, вода с химическими модификаторами и крупный заполнитель. Время перемешивания увеличивается в 2 – 3 раза и составляет не менее 1,5 – 2 минут.
Только строгое соблюдение производственной дисциплины позволяет получить композит заданных свойств и параметров.
tehno-beton.ru
Что такое высокопрочный бетон
Что такое высокопрочный бетон
Что такое высокопрочный бетон сказать сложно, так как отечественных стандартов, которые бы делили бетоны по терминам – прочный, высокопрочный и пр. не существует. Тем не менее, отдельные марки бетона принято называть подобными терминами, («сверхпрочный»), но иногда под ними понимаются совершенно разные вещи.Европейская классификация бетона.
Для начала рассмотрим метод классификации прочности бетона в Европе.Класс прочности в европейском стандарте обозначается:
- для обычных составов, например, так: С40/50,
- для легких бетонов, например, так: LC40/45.
Теперь, указанные Европейские классы бетона, нужно привязать к нашей классификации. Зависимость класса бетона по прочности на сжатие (В) и марки бетона по отечественной классификации (кгс/см кв.) от европейского стандарта выглядит следующим образом.
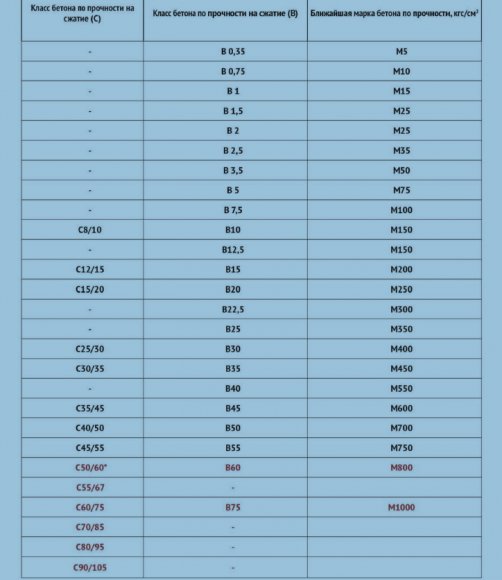
Как добиваются высоких прочностей
Высокий предел прочности у бетонов достигается путем применения особомелкофракционных заполнителей, а также особых марок цемента. В бетонах высокой прочности применяются:- микрокремнезем – тонкодисперсная минеральная добавка, ее основной компонент – диоксид кремния аморфной модификации с размером частиц не более 1 мкм. Эта добавка отлично сцепляется с цементом;
- армировка смеси. Применяются волокна, например стальная фибра.
- особые пластификаторы. Они выгоняют воду, увеличивая прочность. Достигается соотношения воды к цементу значительно ниже 0,4. Как известно для «обычных» бетонов это соотношение в пределах 0,7 – 0,3.
Где применяется высокая прочность
Применять высокопрочный бетон становится выгодным или необходимым, там, где есть потребность в значительном уменьшении массы и габаритов строительной конструкции, при сохранении или достижении высоких (выдающихся) прочностных характеристик.- Это, прежде всего, строительство высотных зданий и сооружений
- Строительство мостов и других транспортных конструкций.
- Хранилища радиоактивных отходов.
- Напольные покрытия в промышленных объектах большой площади.
- Другие специальные объекты.
Сверхэффективный бетон
Для возведения отдельных особых конструкций применялся особый бетон, который в русском языке обрел термин «сверхэффективный». Его прочность на сжатие составляет 150 – 250 МПа.Не смотря на сложность приготовления смеси и сложную технологию строительства из такого материала, в отдельных случаях применение его оказывается выгодным.
Вот пример состава бетона, который использовался для строительства мостовых балок. При этом применялась стальная фибра с длиной волокон 13 мм, а диаметром до 0,2 мм. Соотношение вода/цемент в смеси – 0,15. Все это и другие хитрости дали очень высокую прочность, и бетон стал «сверхэффективным».
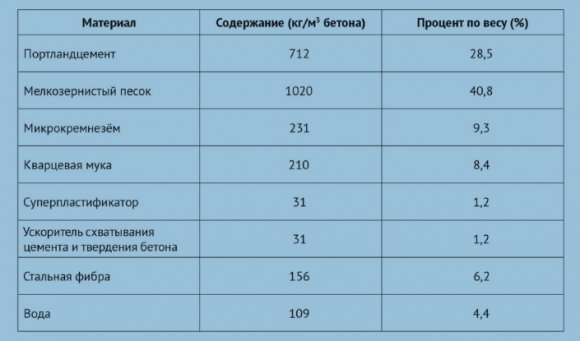
Возможности применения особых прочных марок
Подобные бетоны используются для особого строительства в западных странах и в Японии. Понятно, что широкое применение таких материалов на сегодняшний день не возможно. Как в силу экономической целесообразности, так и (в основном) из-за сложностей технологии приготовления и применения, для чего требуется, по крайней мере, очень квалифицированный специально-обученный персонал. Достаточно сказать, что отдельная технология требует двухсуточный прогрев бетонной конструкции водяным паром с температурой 88 град. спустя сутки после укладки смеси. Так что даже пока в Европе применять подобный строительный материал рекомендуют в виде готовых блоков заводского происхождения, но не как способ монолитного строительства.Высокопрочный бетон / сверхпрочный бетон
1. Уровень развития и нормативные документы
Основной тенденцией в строительстве является использование бетона с высоким пределом прочности при сжатии. В настоящее время высокопрочным считается бетон, предел прочности при сжатии которого находится выше общепринятого уровня и составляет более 60 Н/мм2. При применении обычных исходных веществ и способов укладки создаются строительные конструкции с пределом прочности при сжатии до 150 Н/мм . В наши дни ведется разработка строительных растворов и бетонов с пределом прочности до 800 Н/мм2.
Термин «сверхпрочный бетон» указывает на то, что при различном использовании критерии долговечности имеют первостепенное значение и, соответственно, представляют интерес для определения прочности, смотри таблицу 1. Так как сопротивление бетона внешним воздействиям в значительной степени определяется особо плотной структурой, то с точки зрения бетонной технологии, как правило, нет различия между высокопрочным и сверхпрочным бетоном. Иногда понятие «сверхпрочный бетон» используется в отношении других бетонов, состав и свойствам которых не соответствуют общепринятым стандартам, например, самоуплотняющийся бетон. Эти виды бетона в спецификации не рассматриваются. Во внимание принимается обычный высокопрочный бетон с классами прочности от C 55/67 до C 100/115, а также легкий высокопрочный бетон с классами прочности от LC 55/60 до LC 80/88. В рамках стандарта высокопрочный бетон может использоваться для производства неармированного бетона, железобетона и предварительно напряженного бетона. Для использования бетона классов
Таблица 1: Определение высокопрочного и сверхпрочного бетона
|
Обозначение |
|
высокопрочный бетон |
сверхпрочный бетон |
|
определение |
предел прочности при сжатии > 60 Н/мм2 |
бетоны, разработанные в соответствии со специальными высокими требованиями к использованию, например непроницаемость, сопротивление физическому или химическому воздействию прочность |
преимущественные области применения |
несущая способность |
долговечность |
высокая прочность |
||
плотная структура |
прочности C 90/105, C 100/115, LC 70/77 и LC 80/88 требуются общие допуски строительного надзора, а в отдельных случаях разрешения. Новое поколение норм пришло на смену директиве по высокопрочному бетону, которая дополнила стандарт DIN 1045:1988 для обычного бетона классами прочности с B 65 по B 115. Для переходного периода до конца 2004 года, определенного строительным надзором, могут использоваться на выбор как старые, так и новые поколения норм и стандартов.
2.Основные положения по выбору исходных веществ
2.1 Водоцементное отношениеПри производстве высокопрочного бетона учитывается коэффициент водоцементного отношения < 0,35. Нижний предел водоцементного отношения определяется в настоящее время степенью достижения достаточной удобоукладываемости бетонной смеси и равен 0,20.
2.2 ЦементПри производстве высокопрочного бетона может использоваться стандартный цемент. До этого времени в Германии применялись, например, портландцементы CEM I 42,5 R, CEM I 52,5 R и CEM I 52,5 N, а также цементы, содержащие гранулированный доменный шлак (CEM II-S, CEM III). Для обеспечения достаточной удобоукладываемости бетонной смеси целесообразно соблюдать низкое водопотребление. Как правило, содержание цемента в бетонной смеси составляет от 350 кг/м3 до 500 кг/м3.
2.3 Зернистый заполнительДля высокопрочного бетона характерно уменьшение разницы между прочностью зернистого заполнителя и цементного камня, поэтому в нем по сравнению с обычным бетоном повышается влияние зернистых заполнителей на прочностные характеристики и деформацию. Для получения предела прочности на сжатие, превышающего 100 Н/мм2, необходимо использовать дробленый зернистый заполнитель. Имеется положительный опыт применения базальта, диабаза и мелафира. Кривая гранулометрического состава должна проходить в зоне кривых A и B, причем для фракции зернового состава < 2 мм - ближе к кривой B, а для фракции зернового состава > 2 мм - ближе к кривой A. При этом содержание мелкодисперсной взвеси в зернистом заполнителе должно быть низким. По причине отсутствия продолжительного опыта в стандарте [2] определено использование зернистого заполнителя в отношении щелочных реакций.
2.4 Тонкомолотые добавки
Типичным отличием высокопрочного бетона от бетона обычной прочности наряду с низким водоцементным отношением является добавление силикатной пыли s (называемой также кремнеземная пыль и микросилика). Однако бетон с классом прочности C 55/67 и C 60/77 может производиться и без добавления кремнеземной пыли. Кремнеземная пыль, средний размер частиц которой соответствует одной десятой среднего размера частиц цемента, представляет собой побочный продукт, образующийся в процессе очистки отработанных газов при производстве кремния и феррокремния. Использование кремнезема в бетоне регулируется общими допусками, выданными органами строительного надзора, или европейскими техническими допусками. В рамках Европейской стандартизации допуск заменяется стандартом DIN EN 13263. Действие кремнеземной пыли в бетоне основывается на трех эффектах: заполнение объема пор между частицами цемента, цементный камень приобретает более плотную структуру, - пуццолановая реакция с гидроксидом кальция, повышающая прочность цемента, - улучшение связи между зернистым заполнителем и цементным камнем.
Таблица 2: Общие правила использования кремнеземной пыли s и летучей золы f
Марка цемента |
s/z [весовая доля] |
f/z [весовая доля] |
CEM I |
≤ 0,11
|
≤ 3 (0,22 - s/z) |
CEM II-S CEM II-T CEM II/A-LL CEM III/A |
≤ 3 (0,15 - s/z) |
|
цемент с кремнеземной пылью в качестве основного компонента все другие марки цемента |
не допустимо использование кремнеземной пыли в качестве тонкомолотой добавки |
≤ 0,15 для CEM II/A-D |
не допустимо общее использование летучей золы и кремнеземной пыли |
Максимальное количество добавляемой кремнеземной пыли, необходимое для обеспечения долговечности бетона (антикоррозионная защита арматуры), составляет 11 % от массы цемента. При производстве бетона возможно одновременное использование кремнеземной пыли и летучей золы, однако при этом ограничено их количество, см. таблицу 2. Кремнеземная пыль используется в виде порошка (спрессованная, непрессованная) и в виде суспензии. По причине легкости и удобства в использовании применяется, как правило, суспензия кремнеземной пыли, например, в пропорции 50 % твердого вещества и 50 % воды. Бетон, в состав которого входит кремнеземная пыль, имеет темный цвет. Светлый высокопрочный бетон производится при добавлении кремнеземной кислоты (наносилика) или метакаолина. Кремнеземная кислота может использоваться в качестве добавки в бетон (стабилизатор).
2.5 ДобавкиУкладка бетона с очень низкой теплотой гидратации не возможна без добавления пластификаторов или разжижителей. Надежная укладка бетонной смеси на строительной площадке предполагает мягкую, в лучшем случае текучую консистенцию (например, F4, F5). При снижающемся водоцементном отношении повышается количество добавляемых веществ. Имеется положительный опыт использования разжижителей на основе поликарбоксилата или на основе комбинации смол из нафталина и меламина. Для обеспечения достаточного времени укладки в бетонную смесь целесообразно добавлять замедлитель. Количество добавляемых добавок необходимо ограничивать - до 70 г/кг, соответственно до 70 мл/кг цемента при дозировании разжижителя и - до 80 г/кг, соответственно до 80 мл/кг цемента при дозировке нескольких видов добавок.
2.6 Состав бетонной смесиВо время производства высокопрочного бетона необходимо проводить контроль предусмотренных исходных веществ (вид, производитель, место добычи). При этом следует учитывать добавление разжижителей на строительной площадке. В большинстве случаев проектирование высокопрочного бетона осуществляется на основании уже созданных бетонных смесей. В таблице 3 представлены составы бетонных смесей с различными классами прочности, дающими представление об исходных данных для предварительных исследований или первичных испытаний. В зависимости от исходных веществ в значительной степени меняется состав бетонной смеси.
Рис. 1: Взаимосвязь предела прочности на сжатие и эквивалентного водоцементного отношения в высокопрочном бетоне |
Таблица 3: Исходные данные по составу бетонной смеси
Прочность бетона
|
|
C |
C |
C |
C |
C |
C |
C |
|
|
55/67 |
60/75 |
60/75 |
70/85 |
70/85 |
80/95 |
100/115 |
||
Содержание цемента при |
CEM I 42,5 R |
кг/м3 |
420 |
340 |
- |
420 |
- |
- |
- |
CEM I 52,5 R |
кг/м3 |
- |
- |
- |
- |
- |
450 |
450 |
|
CEM III/A42,5 R |
кг/м3 |
- |
- |
380 |
- |
450 |
- |
- |
|
Содержание кремнеземной пыли (твердое вещество) s Содержание летучей смолы f Содержание воды Разжижитель |
кг/м3 |
- |
30 |
30 |
40 |
40 |
45 |
45 |
|
кг/м3 |
- |
80 |
- |
- |
- |
- |
100 |
||
кг/м3 |
125 |
123 |
125 |
135 |
112 |
126 |
119 |
||
л/м3 |
от 4 л/м3 до 10 л/м3 поликарбоксилат, от 10 л/м3 до |
||||||||
|
20 л/м3 разжижитель на основе меламина и нафталина |
||||||||
Замедлитель |
кг/м3 |
- |
- |
- |
- |
- |
да |
да |
|
Содержание зернистого заполнителя |
0/2 (песок) |
кг/м3 |
650 |
640 |
630 |
630 |
620 |
660 |
830 |
2/8 (гравий) |
кг/м3 |
420 |
410 |
410 |
405 |
400 |
355 |
- |
|
8/16 (гравий) |
кг/м3 |
790 |
880 |
770 |
765 |
725 |
- |
- |
|
2/8 (щебень) |
кг/м3 |
- |
- |
- |
- |
- |
- |
480 |
|
8/16 (щебень) |
кг/м3 |
- |
- |
- |
- |
- |
760 |
770 |
|
Эквивалентное водоцементное отношение (w/z)eq согласно уравнению (1) |
|
032 |
0,35 |
0,32 |
0,32 |
0,27 |
0,28 |
0,26 |
|
Растекаемость (добавление разжижителя через 45 |
a10 |
см |
45.55 |
~ 45 |
|||||
a45. FM |
см |
45...55 55...65 45...55 |
~ 55 |
||||||
a90 |
см |
45.55 |
~ 45 |
||||||
минут после изготовления смеси) |
|
|
|
|
|||||
Плотность свежеприготовленной бетонной смеси |
кг/дм3 |
2,41 |
2,39 |
2,40 |
2,41 |
2,40 |
2,41 |
2,48 |
|
Предел прочности при сжатии (кубик с длиной ребра 150 мм, выдерживание в воде) |
1 d |
Н/мм2 |
30 |
35 |
35 |
40 |
35 |
60 |
65 |
7 d |
Н/мм2 |
60 |
75 |
70 |
80 |
75 |
100 |
115 |
|
28 d |
Н/мм2 |
80 |
90 |
90 |
100 |
100 |
125 |
135 |
|
56 |
Н/мм2 |
85 |
95 |
100 |
110 |
115 |
130 |
140 |
Для определения необходимого эквивалентного водоцементного отношения можно использовать рис. 1, при этом учитывается влияние добавок на прочностные характеристики:
Высокое содержание мелкодисперсной взвеси ведет к образованию клейких бетонов, плохо подвергаемых укладке, и оказывает отрицательное влияние на характеристики бетона при деформации. Поэтому в высокопрочных бетонах ограничено максимально допустимое содержание мелкодисперсной взвеси и мелкого песка, таблица 4.
Таблица 4: Максимально допустимое содержание мелкодисперсной взвеси в высокопрочном и легком бетоне
Содержание цемента 1) [кг/м2] |
Максимально допустимое содержание мелкодисперсной взвеси [кг/м2] при максимальном размере зерна зернистого заполнителя |
|
16 - 63 мм |
8 мм |
|
≤ 400 |
500 |
500 |
450 |
550 |
550 |
≥ 500 |
600 |
600 |
3. Производство и укладка бетона
3.1 Дозировка и смешиваниеДополнительный процесс дозирования заключается в добавлении суспензии кремнеземной пыли. Она поставляется, например, в контейнере объемом 1 м3 и должна храниться в условиях, защищающих ее от замерзания. При хранении свыше 7 дней может потребоваться гомогенизация. Вязкая, клейкая консистенция свежеприготовленной бетонной смеси требует повышенной интенсивности смешивания. В зависимости от состава бетонной смеси и вида смесителя время смешивания после добавления всех исходных веществ составляет от 60 (для легкого бетона от 90) до 180 с. Для оптимальной гомогенизации мелких веществ наиболее благоприятной оказывается следующая последовательность дозирования: зернистый заполнитель, вода, а затем летучая зола и суспензия кремнеземной пыли. Для получения оптимального эффекта от добавок их необходимо добавлять после воды и кремнеземной пыли. Последовательность и время смешивания определены в соответствующей инструкции.
При производстве высокопрочного бетона из-за клейкой консистенции смеси может потребоваться дополнительная очистка смесителя. Смешивание с подачей пара не допустимо. В товарный бетон и бетон, транспортировка которого осуществляется на дальние расстояния, для достижения мягкой или текучей консистенции, удобной для укладки, разжижитель часто добавляют на строительной площадке. Разжижитель должен равномерно распределяться в барабане бетоносмесителя, например, с помощью распылительной трубки. Минимальное время смешивания составляет 1 мин/м3 бетона, но не менее 5 мин. Перед наполнением бетоносмеситель необходимо освободить от оставшейся промывочной воды. О времени бетонирования завод товарного бетона необходимо проинформировать как минимум за два дня до начала работ, чтобы приготовить исходные вещества, приборы и оборудование.
3.2 УкладкаПри укладке высокопрочный бетон проявляет нетипичные свойства. Поэтому на стройке - укладкой смеси должны руководить работники (начальник строительного участка, бригадир), имевшие опыт работы по укладке бетона марки > C 30/37 и - перед каждым этапом бетонирования необходимо проводить инструктаж работников строительного участка (данные необходимо документировать). Целесообразной, и, как правило, необходимой, является проверка на практике свойств бетона в отношении пригодности к перекачке и удобоукладываемости, проводимая персоналом строительной площадки на предусмотренном для этого оборудовании. В частности, необходимо согласовать обработку поверхности плоских строительных деталей (затирка поверхности, создание уклона, профилирование и т.д.). Подача высокопрочного бетона может осуществляться как с помощью бадьи, так и с помощью насоса, если использование того или иного способа было определено при проведении испытаний по укладке. Если в бетонную смесь не добавлялся замедлитель, то следует рассчитывать на более быстрое схватывание высокопрочного бетона по сравнению с бетоном обычной прочности. Укладка высокопрочного бетона в скользящую или подъемно-передвижную опалубку возможна в том случае, если свежеприготовленная бетонная смесь имеет низкую вязкость. При снижении водоцементного отношения и повышении содержания кремнеземной пыли увеличивается энергия уплотнения, необходимая для удаления воздуха из бетона. Расстояния между местами погружения внутреннего вибратора должны быть равны пятикратному диаметру булавы и составлять от 30 до 50 см.
3.3 Выдерживание бетонаИспользование минимального времени выдерживания бетона согласно 1045-3:2001 означает, что во многих случаях уже после первого дня данный этап в процессе бетонирования может быть закончен. Вследствие короткого времени выдерживания высокопрочный бетон в зоне поверхности не достигает полной эффективности. Рекомендуемое время выдерживания внутренних строительных элементов составляет как минимум 2 дня, а наружных - 3 дня. Благоприятно на качестве бетона сказывается выдерживание с подводом воды, результате низкого водоцементного отношения, что может привести к образованию микротрещин. Мероприятия по выдерживанию бетона необходимо начинать проводить сразу же после его уплотнения.
3.4 Обеспечение качестваПри производстве высокопрочного бетона стандартами DIN EN 206-1:2001 и DIN 1045-2:2001 [1, 2] устанавливаются высокие требования к контролю продукции. Для непрерывного обеспечения качества продукции необходимо составить план обеспечения качества, который будет включать в себя следующую информацию: • поставка исходных веществ, • производство и транспортировка бетона, • обработка бетона на строительной площадке или на заводе готовых конструкций, • действия при отклонении от заданного плана, • определение предельных значений наконец, секции бетонирования и личную ответственность. позволяющее избежать его высыхания в
Таблица 5: Классы прочности высокопрочного бетона (Образцы: цилиндр (0 150 мм, высота 300 мм) или кубик (длина ребра 150 мм, выдерживание в соответствии с EN 12390-2))
Класс прочности бетона |
Характеристическая прочность цилиндра на сжатие fck [Н/мм2] |
Характеристическая прочность кубика на сжатие fck, cube [Н/мм2] |
Средний показатель прочности цилиндра на сжатие fck [Н/мм2] |
Средний показатель прочности кубика на сжатие fck, cube [Н/мм2] |
C 55/67 C 60/75 C 70/85 C 80/95 C 90/105 C 100/115
|
55 60 70 80 90 100
|
67 75 85 95 105 115
|
63 68 78 88 98 108 fcm = fck + 8 |
4,2 4,4 4,6 4,8 5,0 5,2 fctm = 2.12 In (1 + fcm/10) |
Таблица 6: Частота отбора проб для оценки соответствия высокопрочного бетона
Производство
|
Частота отбора проб | |
первые 50 м3 продукции |
после первых 50 м3 |
|
Первичное производство (до получения как минимум 35 результатов) |
3 пробы |
продукции 1) 1/100 м2 или 1/день производства |
Непрерывное производство 2) (когда получено минимум 35 результатов) |
|
1/200 м2 или 1/день производства
|
1) Отбор проб должен осуществляться на протяжении всего процесса, на каждые 25 м3 должно быть отобрано не более одной пробы 2) Если стандартное отклонение последних результатов превышает 1,37 а, то частоту отбора проб на следующие 35 результатов испытания следует увеличить на количество, необходимое для первичного производства.
Таблица 7: Критерии соответствия прочности высокопрочного бетона на сжатие
Производство |
Количеств о n результато в |
Критерий 1 |
Критерий 1 |
Среднее значение n результато в fcm [Н/мм2] |
Каждый отдельный результат испытания fci [Н/мм2] |
||
Первичное производство |
3 |
≥ fck + 5 |
≥ fck - 5 |
Непрерывное производство |
15 |
≥ fck + 1,48 δ, δ≥ 5 [ Н/мм2] |
≥ 0,9 fck |
Таблица 8: Частота проведения испытаний и критерии приемки для результатов испытаний на прочность высокопрочного бетона при сжатии и использовании товарного бетона (должны быть выполнены оба критерия)
Количество отдельных значений
|
Критерий 1 Среднее значение fcm для n отдельных значений [Н/мм ] |
Критерий 1 Каждое отдельное значение fci [Н/мм2] |
Частота проведения испытаний
|
от 3 до 4 |
≥ fck + 1 |
≥ fck - 4 ≥ fck- 4 требование отсутствует |
для каждой партии бетона минимум 3 образца для испытаний - каждые 50 м3 - каждый день бетонирования |
от 5 до 6 |
≥ fck + 2 |
||
> 6 |
Проверка определяющих свойств свежеприготовленной бетонной смеси и жесткого бетона в процессе бетонирования высокопрочного бетона осуществляется в соответствии с классом контроля 3.
brusshatka.ru
Высокопрочный бетон
Высокопрочный бетон
Высокопрочный бетон - тяжелый или мелкозернистый бетон классов по прочности на сжатие В60 и выше, приготовленный с применением вяжущего на основе портландцемента. Строительство из высокопрочных бетонов позволяет как заказчику, так и строителю не ограничивать себя сложностью архитектурных решений. В сочетании с прочной арматурой он занимает немаловажную роль в современном строительстве, особенно в предварительно напряженных железобетонных конструкциях.
Сборные конструкции из предварительно напряженного железобетона изготовляют преимущественно из тяжелых бетонов марок 400 — 500. Использование бетонов более высоких марок позволяет снизить собственный вес конструкций, уменьшить площадь их сечения, создать более рациональные конструктивные формы элементов.
Высокопрочный бетон, обладающий повышенной скоростью твердения, набирает прочность в сравнительно короткие сроки. По этой причине можно сократить продолжительность пропаривания изделий из таких бетонов при заводском изготовлении, а в некоторых случаях отказаться от тепловлажностной обработки. Пониженная деформативность высокопрочного бетона под кратковременной и длительной нагрузками улучшает жесткость элементов конструкции и позволяет уменьшить потери предварительного натяжения от ползучести бетона. Усадка высокопрочного бетона, как правило, не превышает в сопоставимых условиях аналогичных деформаций бетона обычной прочности.
Состав высокопрочного бетона
К материалам, используемым для производства высокопрочного бетона, предъявляются повышенные требования, обеспечивающие получение бетоном нужных свойств при минимальных затратах сырья. Подбор состава бетона может корректироваться химическими добавками (наиболее эффективны пластификаторы).
Вяжущее высокопрочного бетона
В качестве вяжущего применяют пластифицированный, гидрофобный или обычный портландцементы, которые должны иметь наибольшую возможную активность и наименьшую нормальную густоту. Рекомендуются цементы, у которых нормальная густота цементного теста не более 25 — 26% и активность не ниже 500 — 600.
Высокопрочные бетоны наиболее целесообразно приготовлять на высокоактивных портландцементах (ВПЦ), которые выпускаются в настоящее время отечественной цементной промышленностью. Достаточно быстрое нарастание прочности в раннем возрасте позволяет сократить до минимума использование различного рода ускорителей твердения бетона.
Песок в высокопрочном бетоне
В производстве высокопрочного бетона используются природные, искусственные (или их смеси) фракционированные кварц-полевошпатовые пески, поставляемые в виде двух фракций — крупной (размерами зерен от 1,25 до 5 мм) и мелкой (размерами зерен от 0,14 до 0,63 мм). Зерновой состав крупного и мелкого заполнителей после фракционирования должен отвечать требованиям ГОСТ.
В крупной фракции наличие зерен более 5 мм, а в мелкой менее 0,14 мм не допускается, при этом содержание отмучиваемых примесей в песке не должно превышать 1% по весу.
Исходя из условий получения бетонной смеси с наилучшей удобоукладываемостью соотношение крупной и мелкой фракций песка выбирают в пределах: крупной - 20 — 50% и мелкой - 80 — 50% по весу.
Для приготовления высокопрочных бетонов марок до 800 включительно можно применять чистые крупно- или среднезернистые пески природной гранулометрии (без фракционирования) при условии, если кривая просеивания находится в пределах области, рекомендуемой ГОСТ. В случаях, когда вязкость применяемого цементного теста велика (нормальная густота Кнг > 26%, а В/Ц < 0,33) кривая просеивания должна находиться у верхней границы области, рекомендуемой ГОСТ. Такой песок следует фракционировать, отделяя частицы мельче 0,3 мм. Применять пески, зерновой состав которых не отвечает указанным требованиям, допускается только при соответствующем технико-экономическом обосновании.
Крупный заполнитель
В качестве крупного заполнителя в высокопрочных бетонах применяют щебень, получаемый дроблением прочных плотных горных пород. Прочность щебня при сжатии в насыщенном водой состоянии должна превышать прочность бетона не менее чем в полтора раза.
Допускается применять щебень пониженной прочности, но не ниже прочности бетона. В этом случае его следует испытывать в бетоне и использовать после соответствующего технико-экономического обоснования.
Щебень должен быть чистым, не содержащим отмучиваемых частиц и фракционированным. Размеры фракций принимаются 5 — 10, 10 — 20 и 20 — 40 мм.
Наибольшую крупность щебня выбирают в зависимости от размеров поперечного сечения элемента конструкции и особенностей её армирования. Для изготовления слабоармированных, толстостенных конструкций можно применять щебень с крупностью до 70 мм.
Заполнители, используемые для приготовления высокопрочного бетона, должны быть сухими и соответствовать требованиям ГОСТа.
Вы смотрели: Высокопрочный бетон
Поделиться ссылкой в социальных сетях
Оставить отзыв или комментарий
stroykaa.ru
Высокопрочный бетон: свойства, сверхпрочный материал нового поколения, состав и применение
Чем высокопрочный бетон отличается от обычного? Особенности материала и сфера применения
Искусственный камень давно стал одним из самых распространенных материалов в строительстве. Несмотря на многообразие видов бетона, развитие и совершенствование композита происходит постоянно. Еще пару десятилетий назад высокопрочным считался бетон с классом В30, но в наши дни этот материал уже относится к рядовым. Современный высокопрочный бетон сочетает широкий спектр свойств, существенно отличающих его от классического искусственного камня.
Параметры такого материала уникальны и не описываются лишь высокими значениями прочности. Фактически подобный композит призван решать сразу несколько сложнейших технологических задач, именно поэтому понятие высокопрочного бетона объединяет несколько видов материалов и целый ряд характеристик.
Особенности композита
Получение высоких классов по прочности давно уже не считается сложной задачей. В номенклатуре многих советских заводов по производству железобетонных изделий и конструкций существовали подборы составов для классов В40, В45, В50 и даже В60. Такие бетоны использовались для производства конструкций, испытывающих существенные динамические нагрузки, например, шпал или мостовых пролетов. Но главной особенностью и свойством подобных материалов являлась низкая технологичность на этапе работы со смесью, ведь ее удобоукладываемость характеризовалась жесткостью на уровне Ж3 и выше.
Сверхпрочный бетон нового поколения представляет собой не просто материал с высокой стойкостью к различным механическим нагрузкам, но и высокотехнологичную смесь. Укладка такого материала в конструкцию любой геометрии не только не усложняется, но и позволяет сократить количество задействованных рабочих.
Высокая подвижность и плотная структура смеси обеспечивают способность самоуплотнения, что позволяет работать с материалом без применения вибраторов.
Способность к самостоятельному уплотнению
Именно свойства бетонной смеси существенно отличают камень высокой прочности, востребованный в строительной отрасли в настоящее время. За счет способности к самостоятельному заполнению формы и уплотнению он получил название самоуплотняющегося или СУБ.
Подобные свойства достигаются за счет создания уникальной структуры, предполагающей непрерывную гранулометрию всех компонентов. Фактически размер частиц в теле бетона изменяется от 5 мкм до 20 мм без разрывов, что позволяет получить так называемую реологически активную матрицу, способную течь и уплотняться под собственным весом. Благодаря сочетанию вяжущего, активных и инертных минеральных добавок, мелкого заполнителя различной крупности, система остается стабильной. Но подбор состава высокопрочного искусственного камня сложен, ведь создать сбалансированную систему из такого количества компонентов непросто.
Сферы применения
Подобный материал обладает весьма высокой себестоимостью, что существенно ограничивает область его использования. Кроме того, потенциал столь прочного бетона мало востребован в рядовых проектах и массовом строительстве.
Основной сферой применения сверхпрочного композита являются сложные по геометрии проекты или высотные здания. Раньше считалось, что бетон не способен выдерживать нагрузки при возведении сооружений в сотни этажей. Классический искусственный камень в основании здания и на первых его этажах разрушался из-за слишком большой нагрузки. Именно поэтому небоскребы возводили из металла и стекла.
Но современные сверхпрочные композиты способны не только выдержать такую нагрузку, но и позволяют сократить толщину всех несущих конструкций, что уменьшает общий вес здания. Именно поэтому высокопрочный бетон широко применяется при возведении современных высотных зданий. Его часто используют при заливке конструкций сложной геометрии, которые раньше собирались из нескольких элементов. Такой бетон часто применяют для изготовления мостовых пролетов большой длины.
Фактически подобный композит направлен на решение сложных архитектурных или инженерных задач и редко используется в массовом строительстве.
Основные характеристики
Сверхпрочный бетон нового поколения отличается широким набором свойств, поэтому чаще всего их делят на два блока.
Показатели бетонной смеси
К первому относят параметры бетонной смеси, среди которых основными считаются:
- подвижность с расплывом конуса на уровне 65 – 70 см;
- коэффициент уплотнения 1,0 – 1,4;
- время сохранения реологических свойств не менее 3 – 4 часов;
- минимальная расслаиваемость;
- воздухосодержание не более 1%.
Способность смеси сохранять свои свойства во времени крайне важна, ведь транспортировка материала от завода до объекта может занять пару часов. Не менее важно обеспечить однородность смеси, ведь расслоение приведет к полной потере свойств затвердевшего бетона.
Параметры готового камня
Ко второму блоку относят характеристики уже затвердевшего композита. К основным среди них можно отнести:
- прочность на сжатие в диапазоне 50 – 100 МПа и на растяжение при изгибе не менее 4 МПа;
- плотность и поровую структуру;
- низкую истираемость;
- морозостойкость от F400 и водонепроницаемость от W10;
- водополгощение не более 1%;
- небольшой модуль сдвига.
С учетом способности смеси такого бетона к образованию максимально плотного тела возникает опасность возникновения микротрещин из-за чрезмерных напряжений во время гидратации. Процесс твердения бетона сопровождается выделением большого количества тепла, а в материале столь плотной структуры этот избыток энергии просто некуда деть. Именно поэтому важно обеспечить адекватную поровую структуру, которая будет работать буфером для избытка энергии и напряжений.
Производство композита
Изготовление высокопрочного бетона по сравнению с обычным тяжелым раствором отличается большей сложностью. Во-первых, для обеспечения качественного смешения компонентов необходимо использовать современные двухвалковые скоростные смесители, способные фактически перетирать смесь сырьевых компонентов.
Во-вторых, чтобы обеспечить все свойства материала требуется соблюдать точное дозирование компонентов и очередность их загрузки. В результате вместо классических 3 – 4 бункеров требуется 6 – 8, что увеличивает стоимость установки. Любое колебание во влажности материалов приводит к выпуску брака, поэтому линии подачи песка и щебня оборудуются специальными датчиками влажности для постоянной корректировки расхода воды.
При изготовлении смеси сначала смешиваются материалы малых фракций, например, цемент, минеральная добавка и микронаполнитель. Затем добавляется песок, вода с химическими модификаторами и крупный заполнитель. Время перемешивания увеличивается в 2 – 3 раза и составляет не менее 1,5 – 2 минут.
Только строгое соблюдение производственной дисциплины позволяет получить композит заданных свойств и параметров.
Советуем почитать:
Рекомендуем ознакомится: http://tehno-beton.ru
fix-builder.ru
Высокопрочный легкий бетон - конструкционный легкий бетон нового поколения
Подробности Создано: 01 Июнь 2012Научно-технической целью проекта Высокопрочный легкий бетон является создание технологии высококачественных строительных материалов для повышения эффективности строительства и снижения удельной стоимости строительного объекта. Для достижения этой цель сформулирована основная задача: разработка технологии материала полифункционального назначения с универсальным набором эксплуатационных свойств.
Мировой тенденцией по повышению качества бетона, как наиболее распространенного в строительстве материала, является объединение положительных качеств легких и тяжелых его видов. То есть снижение средней плотности и повышение прочности бетона обеспечит возможность сочетание конструкционных и теплоизоляционных свойств этих материалов. Критичной областью для решения этой проблемы является средняя плотность бетона 1800 кг/м3, при снижении которой ниже этого предела материал теряет в прочности и не способен обеспечить конструкционные характеристики.
Авторами проекта разработана технология получения энергоэффективных высокопрочных легких бетонов (ВПЛБ) средней плотностью 1300...1500 кг/м3 и маркой по прочности более М600, что на 15..20 % легче и 30...40 % прочнее по сравнению с ближайшими мировыми аналогами. Наш бетон почти вдвое легче и "теплее" традиционного тяжелого бетона, сохраняя при этом высокую прочность и морозостойкость (более F300), что не достижимо для применяемых сегодня ячеистых бетонов.
Высокопрочный легкий бетон является мелкозернистым бетоном, не содержащим крупный заполнитель. Снижение средней плотности достигается за счет сферических частиц микрометрического размера представляющих собой углекислый газ в твердой непористой оболочке. В сочетании с подобранными особым способом компонентами цементно-минеральной составляющей бетона и специальными модифицирующими добавками полый наполнитель формирует одновременно плотную и прочную структуру бетона с насыщенной закрытой пористостью.
Разработанный бетон классифицируется как материал конструкционного назначения с высоким эксплуатационными свойствами, который может быть использован в жилищном и общественном строительстве, для возведения многоэтажных и высотных зданий и сооружений, при строительстве железнодорожных и автомобильных мостов, эстакад, развязок, а также при изготовлении большепролетных изделий из железобетона (фермы, балки, ригели и т.д.) и устройстве сложных строительных объектов. Кроме того, такой бетон значительно расширяет архитектурные возможности строительства.
Применение высокопрочного легкого бетона в строительстве позволяет:
Подробнее...
www.vplb.ru
Бетон своими руками: технология и пропорции
Невзирая на все достоинства применения готового покупного бетона, очень часто строителям приходится замешивать цементный раствор или бетон своими руками непосредственно на месте строительства объекта. Актуальным применение бетона, замешенного своими руками, бывает в том случае, когда требуется залить небольшую железобетонную конструкцию, сделать локальную стяжку на пол, дорожку во дворе, а также ступеньки для лестницы.
Когда лучше все сделать своими руками?
Как правило, применить и приготовить бетон своими руками бывает нужно в следующих случаях:
- Когда требуется замесить небольшой объем раствора, например, для пола в гараже. Минимальная доставка заводской смеси равна объему от 5 м3. В этом случае заказать готовую смесь будет нерационально или даже невозможно.
- Когда строительные работы по заливке бетоном ведутся с промежутками, постепенно. Это тот случай, когда произвести одномоментное заливание требуемых объемов бетонным раствором проблематично. К примеру, при заливке сложных многоярусных железобетонных строений, единичных ригелей или свайно-ригельных оснований для домов.
- Когда затруднена транспортная доставка к объекту на автобетоносмесителе или бетононасосе. Причиной этому может послужить дорожное полотно, непригодное для проезда грузовой техники, или в случае, когда строительство ведется на старой застройке.
- Когда строительство располагается достаточно далеко от бетонного завода и доставка его с учетом транспортировки будет существенно дороже, тем самым будет выгоднее изготовить бетон своими руками и в необходимом объеме.
Виды бетонов по назначению
Согласно своему предназначению, бетоны делятся на следующие виды:
- Конструктивные. Стандартный состав бетонной смеси, который применяется для железобетонных и бетонных несущих конструкций, таких как плиты, панели перекрытия, колонны, фундаменты.
- Специальные. Это химически стойкие, теплоизоляционные, декоративные и жаростойкие составы бетона. Огнеупорный бетон устойчив к перепадам температур и не теряет свои жароупорные качества при нагревании. Качественный жаропрочный бетон, как правило, применяется при возведении каминов, дымовых труб печей, как в жилищном строительстве, так и в промышленном. Жароупорный бетон, приготовленный по всем требованиям, обеспечит надежную защиту и высокую степень безопасности при весьма высоких температурах.
- Напрягающие или бетонополимеры. Этот сверхпрочный бетон применяется при строительстве мостов, военных бункеров, стен метро или многоэтажных строений.
Необходимые компоненты и инструменты
Цемент — главный компонент бетона, его обычно используют под маркой 500 или 400. Существуют марки от 100 и до 600, с шагом по 100. Данная цифра означает прочность цемента, которая колеблется в диапазоне от 10 до 60 МПа. То есть цемент через 28 дней, на момент окончательного затвердевания, будет иметь прочность сжатия, указанную на упаковке, в МПа. Этот компонент лучше применять свежий, так как при долгом хранении он теряет свои качества.
Максимальный срок хранения цемента составляет до одного года, затем его необходимо будет утилизировать.
Для того чтобы приготовить бетон своими руками, например для фундамента, потребуются также следующие компоненты: песок, щебень и вода. Песок рекомендуется использовать карьерный. Его обязательно надо будет просеять от всевозможного мусора. А щебень нужен будет в качестве заполнителя бетона. Для легких бетонов подойдет керамзит, шлак и других пористые заполнители. Для «тощего» бетона, который применяют в качестве стяжки для пола в гараже, заполнители не используются. Можно, в зависимости от условий и технологических требований, применить по желанию добавки или присадки. Вода добавляется до необходимой густоты согласно пропорции.
Таким образом, основные компоненты бетона при замешивании имеют такие пропорции — 1/3/5. То есть на одну часть цемента берутся 3 части песка и 5 частей щебня.
Рассчитать объем бетона можно будет по следующей формуле:
Длина конструкции умножить на ширину конструкции, затем умножить на высоту покрытия. В результате получаем объем бетона. При высоте покрытия в 0,1 м с длиной конструкции в 10 м и шириной в 1 м потребуется 1м3 бетона.
При этом объем воды будет равен весу цемента, поделенного пополам, то есть, например, на 50 кг цемента потребуется 25 л воды. Воду следует добавлять постепенно, соблюдая пропорции.
Из инструментов понадобится следующий комплект:
- Ёмкость для размешивания раствора — корыто.
- Тара для воды, других сыпучих компонентов и самого раствора для переноски его на объект, например, ведро.
- Совковая лопата и сито для песка.
- Молоток, чтоб отбивать от стенок корыта застывший раствор и для дробления слежавшегося цемента.
- Весы, если раствор будет приготовляться не по объему, а по весу.
Приготовление строительного раствора
Ручной замес строительной смеси или бетонного раствора состоит из следующих этапов:
- На чистые полы или в специальную емкость для строительной смеси насыпается горка песка, а в случае для бетона — песок и гравий.
- Соблюдая требуемые пропорции, в песок добавляется цемент, который затем с помощью лопаты тщательно перемешивается в однородную массу.
- Сделав горку из получившейся массы, сверху делаем углубление для воды, ее необходимо добавлять в состав небольшим объемом, соблюдая пропорции. Затем сухие края подсыпаются в центр к воде и перемешиваются до однородной массы.
Использование электрической бетономешалки позволит произвести эту процедуру гораздо быстрее, а также приготовить наиболее однородный раствор.
При помощи бетономешалки можно выполнить намного больше работ по замесу бетонного раствора.
Установлено, что качественный бетон возможен только при соблюдении точных пропорций. Безусловно, его марка зависит от качества используемых компонентов. Удачи!
tvoygarazh.ru