SMOOTH-ON Полиуретан для форм VytaFlex 40 для бетонных изделий (упаковка 0,45+0,45кг). Смазка для форм полиуретановых форм
Изготовление полиуретановых форм своими руками
Недавно я писал статью про изготовление формы для искусственного декоративного камня из силикона, сегодня же хочу рассказать, как изготовить полиуретановую форму своими руками, т.к. процесс немного отличается. У меня при заливке форм из силикона, всегда получалось все гладко — формы получались без пузырей. С полиуретаном же все наоборот и прежде, чем начали получаться качественные формы я «закосячил» около 10 форм.
Высококачественные формы для камня
Форма «Леон»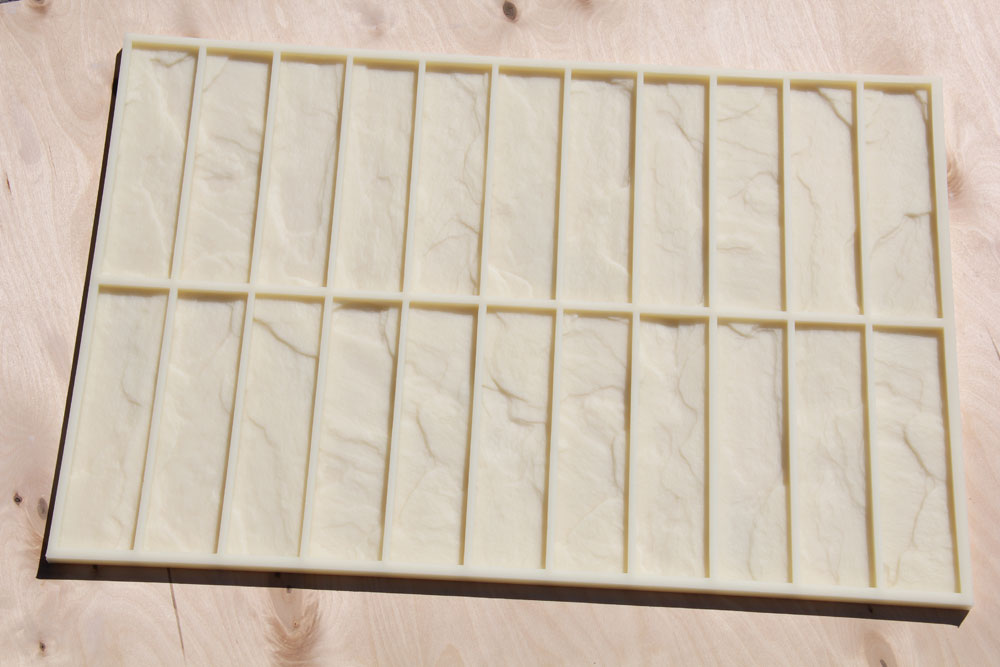
Форма Леон, 0, 25 м2
Дворцовый камень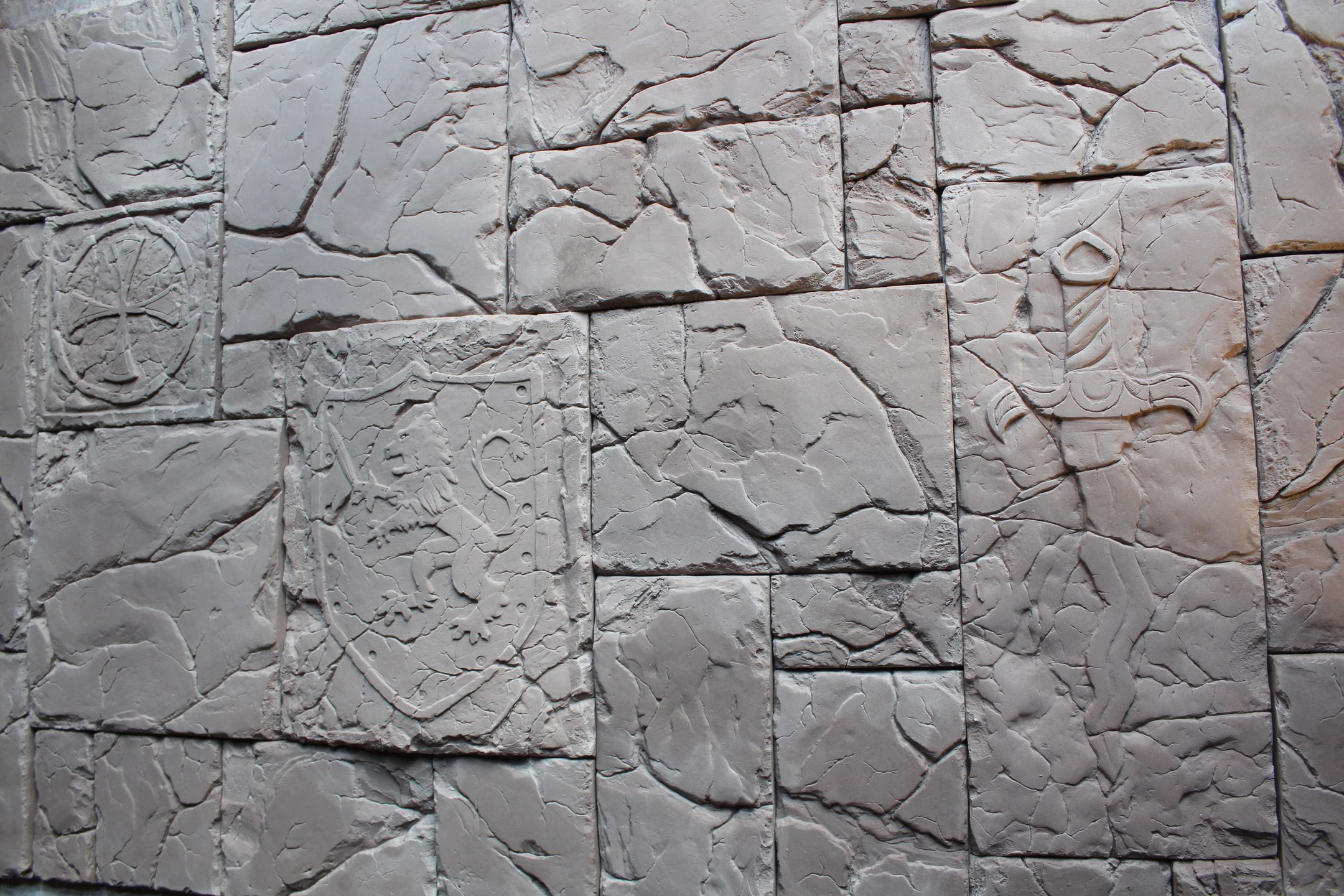
Дворцовый камень
Форма «Американо»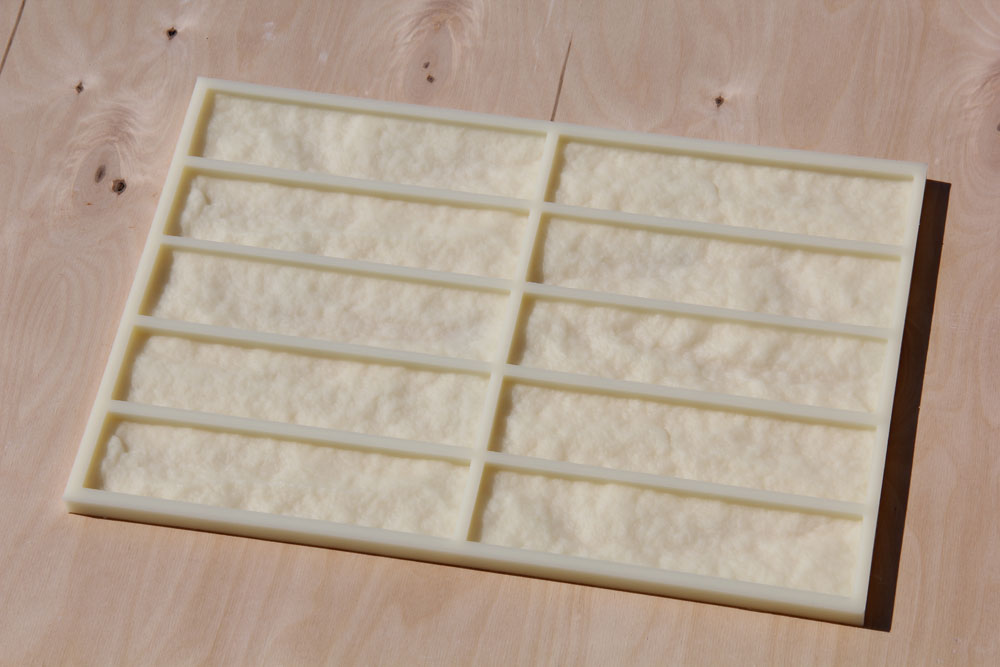
Форма кирпич Американо 0,1 м2
Лев Геральдический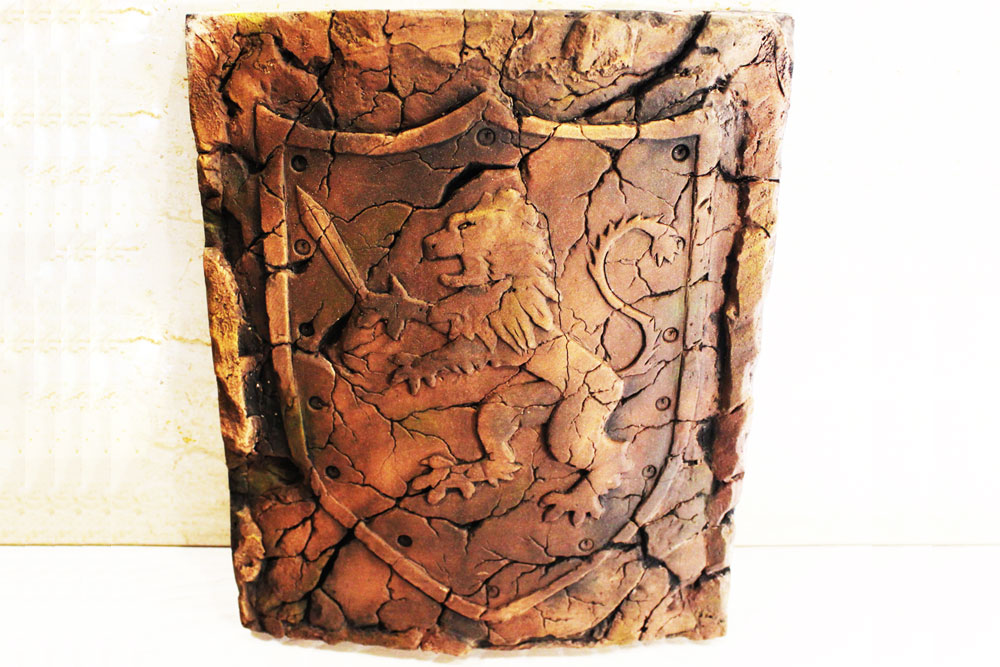
Форма льва (панно)
Немецкий кирпич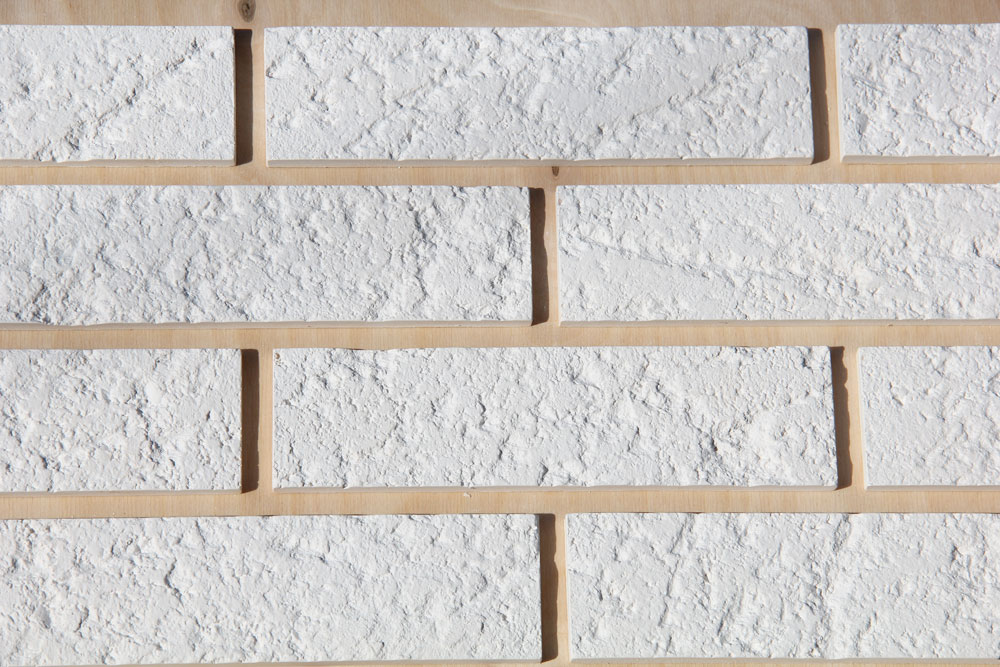
Форма немецкмй кирпич
Крест Тамплиеров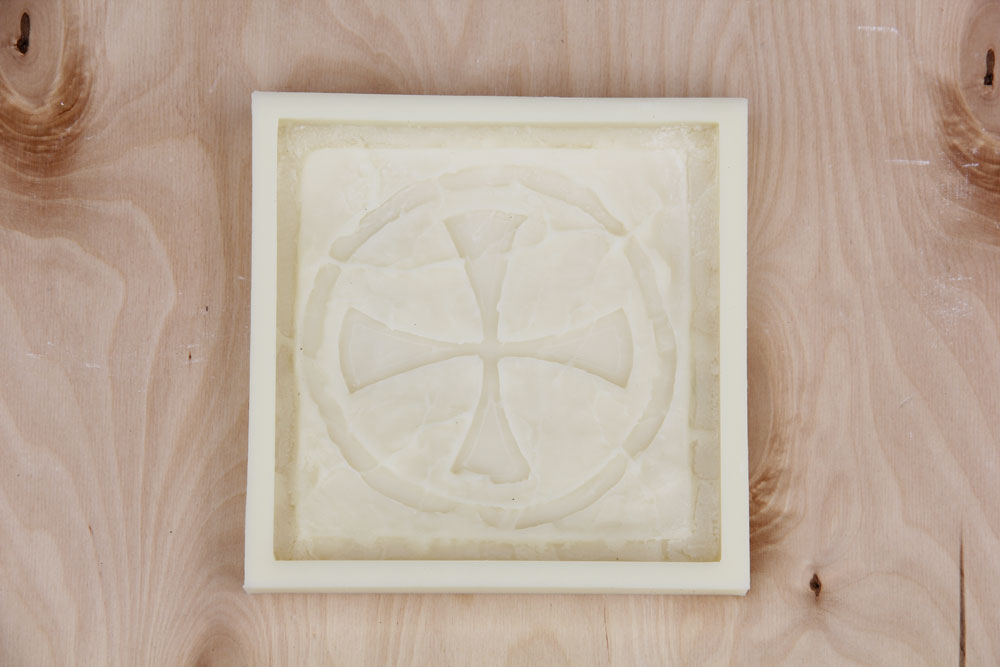
Форма Крест Тамплиеров
Меч Фламберг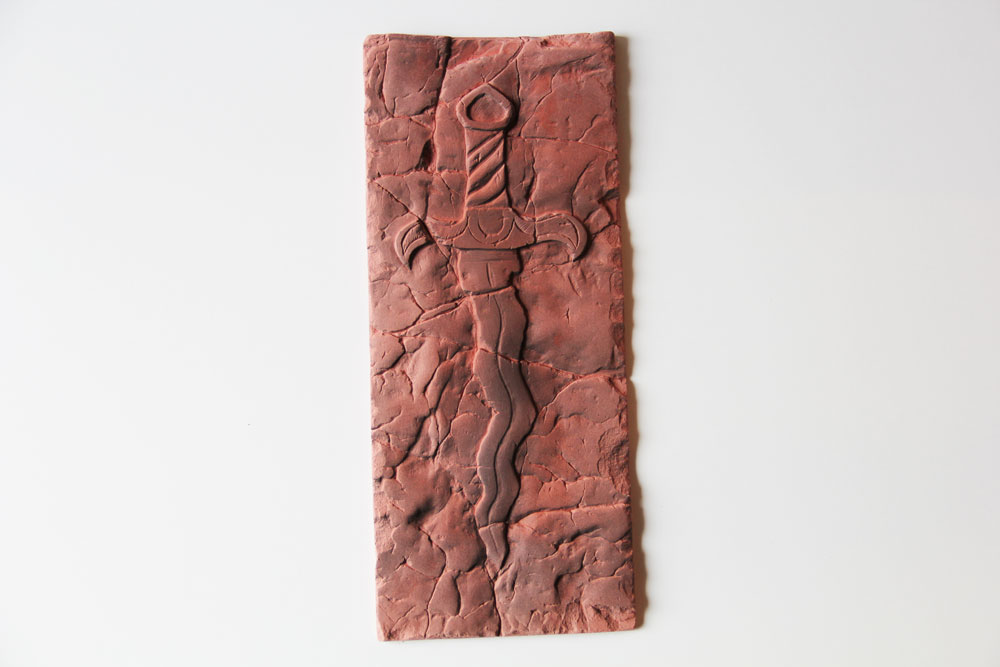
Форма Меч Фламберг
Древесный кирпич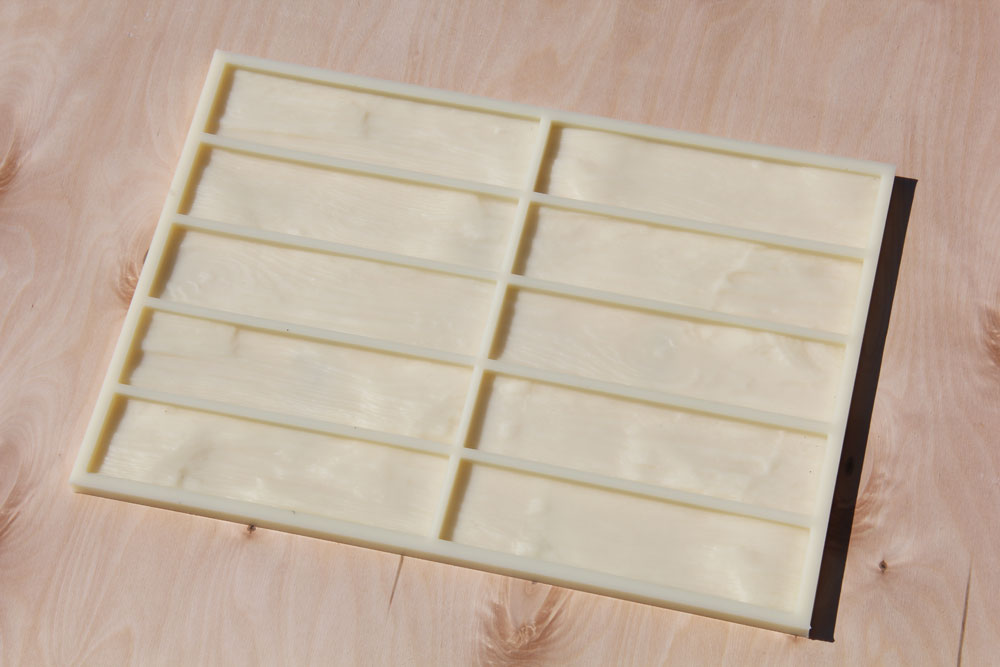
Форма Древесный кирпич
ПОСМОТРЕТЬ ВЕСЬ КАТАЛОГ
Что нужно для изготовления формы
Чтобы форма из полиуретана получилась качественной нужно сделать хорошую матрицу. Как собрать матрицу можно почитать тут. Также вам понадобится сам полиуретан для заливки форм, ведерко, палочка для замешивания (или шуруповерт с миксером), пластиковый шпатель (я его сделал из крышки пластикового ведерка), весы и смазка. В качестве смазки я использую восковую разделительную смазку ВС-М. Можно также взять мыльный раствор, растрясти его, чтобы получилась пенка и ею обработать матрицу, но лично мне, ВС-М мне нравится больше.
Ну и конечно же нужно помещение с пониженной влажностью и комнатной температурой. Хотя, честно признаюсь, я формы заливал всего при +5 градусов. Полиуретан не такой текучий при такой температуре, но других условий у меня не было.
Как сделать полиуретановую форму. Инструкция
В первую очередь матрицу нужно просушить, т.к. на ней может оставаться влага (которая никак не ощущается) и именно из-за этой влаги у меня было куча пузырей на тыльной стороне формы. Я беру фен строительный и в течении 3-5 минут просушиваю. Но нужно сушить так, чтобы камень слишком не нагревался, т.к. может нагреваться силикон на который он приклеен. После сушки, примерно через 5 минут, как камень примет комнатную температуру, можно наносить разделительную смазку. Я делаю в 2 слоя с интервалом в несколько минут. Беру ВС-М и на расстоянии 20-30 см распрыскиваю его во все участки матрицы, под разными углами. Одного баллончика мне хватает на 2 формы, площадью ~0,2 кв. метра. Далее нужно развести компаунд, но для начала определяем его количество.
Как узнать сколько нужно полиуретана?
Возьмите готовую матрицу с прикрученными брусками (желательно до обработки разделительной смазкой) и насыпьте в нее что-нибудь сыпучее. Я видел на ютубе как парень засыпает пшеницу и таким образом определяет объем компаунда. Я бы рекомендовал использовать, что-то более мелкое, например, рис, гречку или пшено. И он еще там говорит, что дно формы должно быть толщиной 1-1,5 см — это я считаю лишнее. Достаточно всего 5 мм, чтобы получилось нормальное изделие, а для своих форм я вообще делаю 3 мм — и этого вполне хватает.
Итак, находим самый высокий камень в матрице, замеряем его максимальную толщину (высоту), прибавляем 5 мм и делаем отметку сбоку на одном из брусков. Затем засыпаем пшено ровно по этой отметке и разравниваем. Затем пересыпаем все в какую нибудь тару и замеряем объем, именно объем, а не вес, т.к, например, у гречки и пшена вес будет разный. Для подсчета можно использовать мерные стаканчики или стеклянные банки по 0,5 литра. Допустим у вас получилось 2,5 литра — это и будет объем компаунда. У меня на форму 0,2 квадратных метра с толщиной камня около 1 см как раз получается 2,5 килограмма. Не забываем, что это примерный расчет и лучше перестраховаться, добавив 300-500 грамм полиуретана.
Также хочу сказать про расстояние между плитками в матрице. В идеале это 1 см, но в целях экономии можно делать меньше. Для тонких кирпичей я делаю по 6 мм между плитками и по 8 мм по периметру. Для более толстых 8 и 1 см соответственно.
Приступаем к заливке
Вначале медленно (что бы не было пузырьков воздуха) размешиваем оба компонента палочкой в течении 2-3-х минут. Затем берем чистое ведерко, отмеряем компонент А и наливаем нужное количество. В зависимости от марки полиуретана кол-во двух компонентов может быть разное, у некоторых делается 2 к 1, у других 1 к 1. Я использую Силагерм 5045 он разводится 2 к 1. Беру 2 части компонента А — 1666 грамм и 1 часть компонента Б — 833 грамма, итого 2500 грамм или 2,5 кг.
Затем добавляю компонент Б и начинаю замешивать до однородной массы в течении 2-3х- минут. Замешивать можно палочкой или дрелью с насадкой на небольших оборотах. Полиуретан нужно хорошо размешать, тщательно проходя по дну и стенкам.
Матрица должна стоять по уровню и после этого можно заливать нашу смесь. Заливку лучше производить в одну точку по центру, тонкой струйкой. Если температура компаунда и помещения 20-25 градусов, то компаунд сам растечется, если меньше, то можно помочь ему шпателем, как делаю я. Если полиуретан плохо растекается, то он скорее всего холодный. Компоненты можно предварительно разогреть, но только по отдельности. В смешанном состоянии этого делать категорически нельзя, т.к. высокая температура влияет на скорость отверждения.
Спроси у камнедела!Если у вас есть какие-нибудь вопросы про гипс, формы или декоративный камень, то можете мне задать вопрос в комментариях.Задать вопрос
После того, как смесь выровнялась по матрице, а это примерно через 1-2 минуты, берем фен, включаем на максимум и на расстоянии 2-3 см от залитого компаунда проходим сверху всю поверхность — так мы максимально выгоним воздух. Жидкий полиуретан от фена будет «плыть» и будет выходить воздух.Напоследок
На этом можно было и завершить написание инструкции, но бывает так, что в 1-2-х местах постоянно выходит воздух, шарик лопается, но снова надувается. Это может происходить из-за того, что либо под камнем, есть небольшая щель, либо в самом камне есть «раковинка». В таком случае, я беру обычную иглу, вставляю в то место откуда идет воздух и резко выдергиваю. При необходимости можно сделать несколько раз. Бывает помогает, бывает нет.
Лучше конечно при заливке использовать вакуумную камеру, чтобы избежать брака, но это дорогое удовольствие. И подходит только тем, кто делает формы на продажу. Ну и хочу дать один совет: если вы собираетесь сделать себе декоративный камень и встал вопрос с формами, покупать или сделать самому, то я бы рекомендовал купить, т.к. при изготовлении без вакуумной камеры высока вероятность брака. Если планируется производство и нужно много форм, то можно сделать самому, но я вас уверяю, брак будет 100%.
Читайте дальше: как сделать сушилку для декоративного камня
kamnedeloff.ru
SMOOTH-ON Полиуретан для форм VytaFlex 40 очень прочный для бетонных изделий
SMOOTH-ON Полиуретан для форм VytaFlex 40
Описание и применение. Полиуретан для форм VytaFlex от производителя полиуретановых резин № 1 в мире компании Smooth-on (USA, год основания 1895) обеспечивает превосходные физические и эксплуатационные свойства форм для литья бетона. Универсальная твердость по Шору 40A. Удобное соотношение при смешивании - один к одному по объему.
ВАЖНО! Работать только со смазкой для полиуретановых форм, так как полиуретан ко всему прилипает!
Особенно эффективны полиуретаны VytaFlex для литья пигментного/цветного бетона. Формы, изготовленные из полиуретана VytaFlex 40, позволят получать точные и однородные цветные отливки.
Внешний вид: часть Б – кремовая, часть А - прозрачно-желтоватая, средней вязкости, при смешивании становится кремовым - отличная индикация тщательности смешивания.
Расфасовка: ПЭ канистры (наш репак из заводской тары) - 0,45 кг + 0,45 кг = 0,9 кг.
Соотношение смешивания по объему | 1А: 1В |
Соотношение смешивания по весу | 1А: 1В |
Плотность, г/см3 | 1,03 |
Цвет | Кремовый |
Твердость по Шору А | 40 |
Предел прочности | 522 фунтов на квадратный дюйм |
Удлинение при разрыве, % | 660 |
Жизнеспособность, мин. (при 23°С) | 30 |
Время отверждения (при 23°С), часов | 16 - 24 |
Усадка, % | менее 0,3 |
Предел прочности на разрыв, МПа C | 3,60 |
Вязкость после смешивания, cps | 2000 |
Технология работы с полиуретановым компаундом VytaFlex 40
Хранить и использовать при комнатной температуре 23 °C. Этот продукт имеет ограниченный срок хранения и должен использоваться как можно скорее. Используйте в условиях низкой влажности (ниже 50% относительной влажности). Контейнеры для смешивания должны иметь прямые стороны и плоское дно. Смешивающие палочки должны быть плоскими и жесткими для очистки сторон и нижней части контейнера для смешивания.
Пористые поверхности (например, натуральные камни, гипсовые штукатурки, бетон, дерево, камень, глина, полистирол и т. д.) должны быть «запечатаны» перед нанесением разделительного агента. Все полиуретаны являются по своей сути клеями. Чтобы предотвратить адгезию между поверхностью резины и модели, модели должны быть «запечатаны» капсулятором (закрытие пор) SuperSeal ™ (он также есть у нас в продаже). Это быстросохнущий герметик, подходящий для герметизации пористых поверхностей, не портящий детализацию поверхности. Следует нанести герметик и оставить его полностью высохнуть перед нанесением разделительного агента.
Непористые поверхности. Металл, стекло, твердые пластмассы, требуют только разделительного агента.
Разделительная смазка обязательно необходима для демонтажа при литье, иначе неизбежно прилипание. Используйте разделительный агент, специально предназначенный для изготовления полиуретановых форм Universal Mold Release от Smooth-On (он также есть у нас в продаже). На все поверхности, которые будут контактировать с полиуретаном, должен быть нанесен защитный слой этого разделительного агента. Он на основе силикона, и его можно использовать только с полиуретановыми формами, с силиконовыми нельзя!
ВАЖНО: чтобы обеспечить полное покрытие, нанесите смазку мягкой щеткой на все поверхности модели. Дайте смазке высохнуть в течение 30 минут. Поскольку каждое применение всегда отличается друг от друга, рекомендуется всегда делать пробные отливки для определения пригодности для вашего проекта.
________________________________________
Дозирование и смешивание. Жидкие полиуретаны очень чувствительны к влаге и поглощают атмосферную влагу. Смесительные инструменты и контейнеры должны быть чистыми, сухими и изготовлены из металла или пластика. Материалы следует хранить и использовать в теплой среде (не ниже 23 °C).
ВАЖНО: тщательно перемешать часть Б (кремовую) перед дозированием. После дозирования равных количеств частей А и Б в емкость для смешивания тщательно перемешайте в течение как минимум 3 минут, убедившись, что вы несколько раз очищаете боковые стенки и днище смесительного контейнера.
Если смешиваете большие количества (от 1 кг или более) за один раз, используйте механический смеситель в течение 3 минут с последующим тщательным перемешиванием вручную в течение одной минуты.
Затем вылейте все количество в новый, чистый контейнер для смешивания и перемешайте снова и снова (техника двойного перемешивания).
Хотя этот продукт разработан для минимизации пузырьков воздуха в вашей отвержденной полиуретановой форме, вакуумная дегазация резины еще больше уменьшит захваченный воздух.
________________________________________
Заливка, отверждение, ресурс формы, хранение. Для достижения наилучших результатов, вылейте свою смесь в одном месте в самой нижней точке. Равномерный низкий поток поможет свести к минимуму захваченный воздух. Жидкая резина должна выровняться по крайней мере на 1,3 см над самой высокой точкой поверхности модели.
Отверждение происходит как минимум 24 часа при комнатной температуре (23 °C) перед извлечением из опалубки. Не отверждайте полиуретан при температуре ниже 18 °C.
Постотверждение необязательно, но после 16-24 ч. отверждения нагрев резины до 65 °C в течение 4-8 часов увеличит физические свойства и рабочие характеристики формы.
Ресурс и хранение. Полностью отвержденный полиуретан - прочный, долговечный и будет работать при правильном использовании и хранении. Физическая жизнь резины зависит от того, как вы ее используете. Храните в ровном нескрученном положении.
При тиражировании бетонных изделий для облегчения выемки и сохранности формы можно использовать густой мыльный раствор (нанести и просушить).
Делаем бетонную раковину в полиуретановой форме из VYTAFLEX 40
Смотрите видео о полиуретане VYTAFLEX 40 на сайте производителя SMOOTH-ON
VytaFlex™ 40 Product Information | Smooth-On, Inc.
elastoform24.ru
Технология литья форм из заливочного полиуретана — Artsil
Мы предоставляем Вам технологию по изготовлению литьевых полиуретановых форм для самостоятельного производства искусственного камня. Технология будет расписана по этапам, к каждому этапу прилогаются ссылки на видео приложения!
1. Подготовка мастер-модели. Тщательно очистите и просушите мастер-модель (наличие влаги не допустимо). Далее следует обработать вашу модель и внутреннюю поверхность заливочной опалубки разделительной смазкой. Нанесите смазку равномерно на всю поверхность мастер-модели и заливочной опалубки. Не наносите слишком толстый слой, чтобы ни скрыть фактуру камня под слоем разделительного агента. После нанесения дайте слою просохнуть в течение примерно 10 минут.
2. Строительным феном греем модель, это делается для того чтобы разделительный агент(основа парафин)при воздействие на него феном начинает плавиться тем самым заполняя микропоры а излишки стекают, так образуется на фактуре камня тонкий слой парафина что гарантирует в дальнейшем четкую копию рисунка, без искажений.
3. Далее производим сборку модели (прикручиваем борта) и выставляем по уровню. Также следует герметизировать модель по периметру для предотвращения вытекания формовочного материала, заливочная опалубка должна быть тщательно герметизирована.
4. Взвешивание (полиола часть А) и (изоционата часть В). Перед тем, как смешивать компоненты, убедитесь, что полиуретановый компаунд имеют комнатную температуру. Имейте в виду, что при хранении (или перевозке) материала на открытом воздухе в холодную погоду, может понадобиться до 24 часов для того, чтобы компоненты достигли комнатной температуры. Оптимальная температура помещения при формовании должна быть 20-25°C и влажностью не более 50%.
Для смешивания компонентов используйте чистые, сухие пластиковые ведра (стаканы) равного объема. Отвесьте в ведра равные количества (по весу или по объему) полиола (часть А) и изоционата(часть В). Смешивание компонентов обычно занимает 2-4 мин(в зависимости от вязкости материала)можно обычной дрелью на средних оборотах ,лопатка должна вращаться против часовой стрелки что бы не вовлекать в смесь излишние пузырьки воздуха.
5. Процесс заливки полиуретанового компаунда на мастер-модель. После того как Вы тщательно перемешали оба компонента до однородного состояния включается процесс жизни (время жизни компаунда ,это переход с жидкого состояния в гелеобразное 10-15 мин)в этот короткий период времени нужно успеть залить полиуретановую массу на мастер-модель.
Заливать лучше с одного угла, в этом случае материал будет покрывать мастер-модель медленно, как поток лавы.
6. Распалубка производится после полной полимеризации материала 16-24 часа, процесс извлечение полиуретановой формы нужно проводить очень аккуратно. В течение 3-х суток форма ещё будет набирать прочность, после чего её можно будет эксплуатировать.
artsil.ru
Разделительная смазка Universal Mold Release от Smooth-On для полиуретановых форм (70 г) под кисть
Universal Mold Release - разделительный состав для полиуретановых форм
Описание и применение. Universal Mold Release - разделительный состав в виде жидкости, разработанный специально для формовочных и литейных работ и применяемый как для облегчения снятия только что изготовленной формы с прототипа изделия, так и при тиражировании изделий, для облегчения выемки последних из эластичных полиуретановых форм.
Хорошо работает с большинством жидких резин (таких как полиуретаны и полисульфиды), жидких пластмасс, а также является отличным разделительным составом для эпоксидных и полиэфирных смол при формовке последних в эластичные полиуретановые формы. Universal Mold Release эффективен в широком температурном диапазоне от 21 °С до 260 °С.
ВАЖНО! Перед применением смазки может потребоваться герметизация пористых моделей (дерева, гипса, бетона) или некоторых модельных глин (содержащих воду или серу) с помощью Smooth-On SuperSeal.
Особенности
- Нельзя использовать Universal Mold Release с силиконовыми формами
- Universal Mold Release улучшает эффективность формования и продлевает срок службы вашей полиуретановой форме.
Применение смазки Universal Mold Release:
-
Хорошо взболтать перед использованием.
-
Этот продукт имеет ограниченный срок хранения и должен использоваться как можно скорее.
-
Используя мягкую щетку, нанесите смазку на все поверхности, где будет соприкосновение с полиуретановой формой.
-
Дать смазке высохнуть 5 минут.
-
Для ускорения высыхания можно использовать фен.
-
Повторите применение и дайте высохнуть (до 20 минут).
-
Теперь можно лить полиуретан для форм или делать отливки в отвержденную резиновую форму.
-
Поскольку каждое применение всегда отличается друг от друга, рекомендуется всегда делать пробные отливки для определения пригодности для вашего проекта.
elastoform24.ru
Обмазочный полиуретановый формовочный компаунд Силагерм 5240
У каждого мастера часто возникает потребность изготовить форму с вертикальной поверхности, потолка или любой другой поверхности, декоративного элемента и тогда идеальным материалом для этой задачи служит полиуретан для форм Силагерм 5240.
Это двухкомпонентный материал пастообразной консистенции,смешивается в пропорции 100/80 и имеющий время жизни 30-50 минут(время в течении которого с материалом можно работать до момента схватывания и превращению в резину). в зависимости от температуры окружающей среды.
Чем температура выше, тем время жизни компаунда меньше, при уменьшении температуры до +10 С время жизни может увеличиться до 60-70 минут.
Перед нанесением материала на копируемую модель, саму модель и прилегающие поверхности, которые будут соприкасаться с формовочным материалом, необходимо обработать восковой разделительной смазкой Вс-М. Через 10-20 минут после нанесения смазки, приступают к процессу изготовления формы.
Перед тем как отмерить необходимое количество гр/кг, компонент А (бежевого цвета) обязательно хорошо перемешайте в таре поставке, т.к. допускается расслоение и только после этого отмеряйте необходимое кол-во. Компонент В перемешивать не надо.
Смешанные компоненты перемешиваются до однородности в течении 3- 7 минут в зависимости от количества и далее наносятся на обработанную разделительной смазкой поверхность с помощью жесткой кисти.
Рекомендует смешивать небольшими порциями и изготавливать форму 3-4мя подходами (3-4- слоя), тогда форма получится без пузырей и расход материала будет небольшой, и форма по всей своей поверхности будет иметь одинаковую толщину.
По консистенции компаунд мягкий, как вазелин, легко наносится. немного оплывает, но не стекает с поверхности. Чтобы разбить пузырьки, которые могут остаться в мелком и глубоком рельефе, наносить компаунд надо постукивающими движениями . После нанесения первого слоя, не спешите и подготовьте вторую порцию смеси к моменту когда первый слой схватится (т.е. перестанет мазаться и течь и будет липкой резиной). Таким же образом наносят все 3-4 слоя. Для увеличения прочности на раздир между 3-м и 4-м слоем рекомендуется наносить армирующий слой (марля. серпятка, капрон и т.п.).
Через 3-6 часов после нанесения последнего слоя, материал по виду и ощущениям выглядит как полностью готовый, но это обманчиво.
ВАЖНО: ВСЕ полиуретаны холодного отверждения по своим химическим свойствам отверждаются 5 суток (т.е. через 5 суток заканчиваются все химические процессы в материале), но уже через сутки- трое - форму можно аккуратно снимать,т.к.50-80% реакции уже будут закончены, но т.к. процессы все ещё идут, форму надо положить на ровную поверхность и дать время до завершения всех процессов. Только тогда форма прослужит долго и её геометрия не будет нарушена.
В качестве жесткой подложки можно использовать гипс или гипсовые бинты.
После завершения процесса изготовления формы, у вас должна получиться форма состоящая из гибкого вкладыша с точной копией и жесткого кожуха для поддержания этого гибкого вкладыша.
Если у Вас остались вопросы по процессу изготовления формы из обмазочного компаунда силагерм 5240, звоните нам по телефону (495)221-87-50, мы обязательно ответим на них.
Силагерм 5240 является аналогом американского компаунда brush on 40 (брошен 40).
Ниже приведены характеристики на отвержденный компаунд Силагерм 5240 после 5 суток.
Марка | Твердость по Шору A | Соотношение (по весу) | Цвет | Время жизни, мин | Время отверждения, час | Плотность г/см3 |
Вязкость основной пасты Pa*s | Вязкость отвердителя Pa*s | Удлинение при разрыве, % | Предел прочности на разрыв, МПа | Усадка, % |
Силагерм 5240 | 40±3 | 100 А : 80 В | бежевый | 30-100 | 24 |
1,05-1,15 |
паста |
30-40 | Не менее 300 | Не менее 2,5 | 0,1 |
В готовую форму из полиуретана можно заливать бетон, гипс и другие материалы которые при отверждении разогреваются не выше + 110С.
Для полиэфирных смол, легкоплавкий металлов и других материалов которые разогреваются до + 250С необходимо использовать силикон для форм Силагерм 7140 или Силагерм 8040.
silagerm.ru
Полиуретан для форм в разрезной форме. Инструкция по изготовлению
Разрезная полиуретановая форма – универсальное средство для прототипирования и отливки сложных объёмных изделий с фактурой, рисунком и неровностями по всей площади поверхности. Как правило, разрезные формы применяют для литья в них смол, жидкого пластика, либо подобных материалов. Для изготовления такой формы применяют жидкий полиуретан для форм или жидкий силикон. Разрезной такая форма называется, потому, что, как правило, при её производстве, жидкий компаунд заливает мастер модель полностью, оставляя лишь литьевое отверстие, а после затвердения материала делается продольный разрез, из которого достаётся мастер модель, и в будущем будут доставаться прототипированные изделия.
Чтобы облегчить понимание процесса производства такой формы, необходимо следовать ряду несложных инструкций, представленных ниже.
Инструкция по производству разрезной полиуретановой формы
1. Закрепляем нашу мастер модель на небольшой подставке. Важно обеспечить полное соприкосновение мастер модели с подставкой, чтобы во время литья компаунда, последний не попал между ними. Важно это, потому, что в готовой форме, углубление от подставки будет служить нам литьевым отверстием для отливки будущих изделий. Закреплять мастер модель на подставке эффективнее всего с помощью супер клея.
2. На втором этапе необходимо тщательно обработать мастер модель смазкой. Также, обработке подлежит любая поверхность, которая при заливке формы будет контактировать с жидким полиуретаном, это: подставка мастер модели и стенки опалубки. Смазку необходимо наносить аккуратным очень тонким слоем, важно не ошибиться: оставите какой-то элемент мастер модели не смазанным – материал прилипнет, и форма будет испорчена, смажете слишком обильно – рискуете забить фактуру, впадины и неровности мастер модели, как следствие – этот рельеф не отпечатается на готовой форме. В качестве смазки может служить любой материал, обладающий антиадгезионными свойствами (масло, жир, вазелин), однако мы настоятельно рекомендуем использовать специализированный восковой или силиконовый разделитель.
3. Размещаем нашу подставку с мастер-моделью в опалубке и закрепляем её там. Необходимо, чтобы мастер модель и подставка твёрдо и уверенно стояли в опалубке, дабы избежать смещений и наклона во время литья компаунда. Также важно, чтобы в опалубке не было зазоров, щелей и трещин. Статью о правильном изготовлении опалубки мы выкладывали ранее.
4. На данном этапе наша мастер модель готова к заливке. Теперь необходимо подготовить жидкий полиуретан для форм или иное сырьё. Как правило, подобный материал является двухкомпонентным, поэтому важно перемешать составляющие согласно инструкции, прилагаемой к нему. После начала смешивания компонентов засекайте время: в среднем у нас есть около 30 минут, прежде чем компаунд начнёт затвердевать. После смешивания, если есть такая возможность, дегазируйте материал, разместив его на вибростоле или вакуумной камере.
5. Теперь можно заливать полиуретан для форм в опалубку с нашей мастер моделью. Лить материал нужно в одну точку и не спеша, дабы в смеси не образовались лишние пузырьки воздуха. Таким образом, необходимо полностью покрыть мастер модель, пока она не скроется под компаундом на 8 – 15 мм. После заливки оставляем будущую форму сохнуть. Точное время полной полимеризации всегда указывается в инструкции к материалу.
6. Когда смесь окончательно затвердеет, разбираем опалубку и извлекаем форму. Теперь нужно сделать из полной формы разрезную. Для этого нужно аккуратно растягивать форму от отверстия, которое у нас осталось от подставки при заливке. Растягивая форму, осторожно поддеваем её и делаем разрез вдоль формы, стараясь не задеть мастер модель. Когда разрез станет достаточно большим, чтобы достать мастер модель, извлекаем оную. Готово.
Теперь у нас есть форма с литьевым отверстием и разрезом, через которое мы будет доставать отлитые изделия. Для того, чтобы жидкий пластик, гипс или другой материал, который мы будем лить в эту форму не просачивался и не вытекал через разрез перед литьём будет нужно стягивать форму, чтобы края разреза плотно примыкали друг к другу, но стараться делать это без деформации самой формы.
В данной инструкции приведена наиболее простая и распространённая модель разрезной формы. В будущих статьях мы подробно опишем, как делать более сложные вариации разрезной формы.
kremen.ru
Что применить для формовки? Формопласт, силикон или полиуретан?
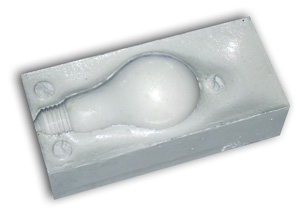
Изготавливать садовые скульптуры и элементы ландшафтного дизайна самому - заманчивая идея. Еще заманчивее научиться тиражированию собственных изделий.
Один из способов копирования скульптур - литье в снятые с изделия формы.
Как подобрать материал для изготовления эластичной формы для отливок из гипса, бетона, полимербетона, полимерных (полиэфирных и эпоксидных) смол?Рассмотрим достоинства и недостатки некоторых существующих видов компаундов.
Гибкие («резиновые») формы-матрицы, позволяют воспроизводить и тиражировать сложные фактуры и поверхности. Они применяются для изготовления искусственного камня, декоративной плитки, гипсовой лепнины, создания малых архитектурных форм, статуэток и художественных изделий, фигурных свечей, изделий из стеклопластика и т. п.
Существует четыре вида материалов для изготовления эластичных форм - ПВХ (формопласт), силиконовые, полиуретановые и тиоколовые материалы.
Формопласт
Самый дешевый, но трудный в работе - ПВХ компаунд - формопласт. Это однокомпонентный компаунд.
Формопласт расплавляется и заливается при высокой температуре (до 200 °С). Важно четко выдерживать температурный режим, так как при перегревании он будет не пригоден к дальнейшему использованию, поэтому необходимо специальное плавильное оборудование с регулировкой температуры. Кроме того, нужна вытяжка, так как при нагревании формопласт выделяет вредные вещества.
Формы из формопласта не дают повышенной точности отливок, так как есть усадка. Формопластовые матрицы используются при отливке не выше 70 °С.
Достоинства: дешевизна, прочность формы по сравнению с силиконовыми формами, не требуется никаких добавок - ни катализаторов, ни отвердителей.
Недостатки: токсичен, нужно специальное оборудование, специальные навыки в работе, есть усадка, при заливке (изготовлении формы) может сильно прилипать к модели, нетермостойкий. При низких температурах (- 10 - 15 °С) затвердевает.
Следующие три вида материалов еще называют «жидкой резиной». Они представляют собой текучие составы, переходящие при отверждении в резиноподобное состояние.
Силикон для форм.
Силиконовый компаунд бывает однокомпонентный, двухкомпонентный и многокомпонентный.
Однокомпонентные компаунды - это в основном строительные герметики для изоляции швов. Они затвердевают только при небольшой толщине слоя и не используются для форм.
Для изготовления форм предназначены двухкомпонентные материалы: силиконовый компаунд (основной состав) + катализатор.
Силикон для форм застывает при комнатной температуре при смешивании с катализатором. Этот материал легко смешивается, допускает отклонение в дозировке компонентов. При смешивании не выделяет токсических веществ. Хорошо снимается с материала модели, не дает практически усадки, не требует дополнительных смазок, допускает заливку в широком диапазоне температур.
Достоинства: отличительными особенностями силиконовых заливочных материалов являются термостойкость (до 200 °С и выше градусов), стойкость к многим агрессивным средам, простота в работе и нетоксичность (силиконы широко используются в медицине), высокая точность слепка.
Недостатком является умеренная прочность, сравнимая с прочностью формопласта, но уступающая прочности полиуретана.
Полиуретан для форм.
Самый дорогой и прочный состав - заливочный полиуретан.
Это двухкомпонентные или многокомпонентные материалы.
Полиуретаны для форм имеют довольно высокую цену, так на рынке СНГ представлены только американские и европейские полиуретановые продукты. В Украине и России еще не освоено производство полиуретановых заливочных компаундов для изготовления форм.
Также как и силиконовый компаунд, полиуретан для форм затвердевает при комнатной температуре при смешивании всех имеющихся в наборе компонентов.
Необходимо четко придерживаться инструкций по заливке при смешивании: должно соблюдаться соотношение всех компонентов при смешивании. При неправильном соотношении будет понижена прочность и долговечность, потому что непрореагировавшие компоненты вызывают разрушение формы.
При открывании определенного количества упаковки, все количество сырья необходимо использовать сразу же, то есть нельзя его делить на разные порции, так как полиуретановые компоненты начинают взаимодействовать с воздухом и влагой и портятся - изменяют свои свойства.
Сложность работы заключается еще и в том, что полиуретан сильно прилипает ко всем материалам, из которых снимается форма. Требуется большое количество смазки, нужно тщательно проводить смазывание модели.
Компоненты полиуретана ядовитые и боятся контакта с воздухом и влагой. Основные марки полиуретана не стойки к таким материалам как гипс, цемент, полимерные смолы, поэтому нужно быть внимательным к рекомендациям производителя.
Под каждый материал надо выбирать конкретную марку полиуретана. Формы из полиуретана в основном предназначены для материалов, заливаемых при температуре до 70 °С.
Достоинства: высокие прочностные характеристики, большая гибкость, малая усадка.
Недостатки: высокая цена, токсичность, сложность в работе, требуется повышенная и тщательная смазка, достаточно густой вязкий материал - сложно заливать.
Тиоколовые составы
Тиоколовые компаунды бывают двух- и многокомпонентные.
Они сходны по свойствам с силиконовыми, но имеют такую же или более низкую прочность, низкую термостойкость изготовленных из них форм.
Главное преимущество - высокая стойкость к нефтепродуктам (различным растворителям, входящим в состав полимерных смол, из которых делают некоторые отливки).
Достоинства: стойкость к растворителям, нетоксичность.
Недостатки: тиоколовые компаунды более густые, чем силиконовые - с ними сложнее работать. Производятся в ограниченных количествах. Очень специфический материал на любителя.
Евгений Зайцев, Институт Вяжущих и Адгезивов Оригинал статьи: Силикон формопласт или полиуретан?
Похожие страницыfilsadovnik.ru