Бетон из шлака: как приготовить своими руками. Шлаковый бетон
Бетон из шлака | Новости в строительстве
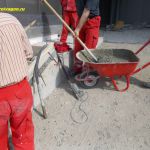
Укладка бетона в опалубку
В производстве бетонов широкое использование находят шлаки, золы и золошлаковые смеси. Они с успехом заменяют традиционные заполнители природного происхождения,такие как песок, щебень или гравий, легкие и пористые заполнители искусственного происхождения (аглопорит, керамзит и другие), природного происхождения (туф,пемза, а также и другие виды) или в сочетании с ними.
Содержание статьи:
1. Использование золы и шлаков в производстве бетонов.
2. Виды , прочностные марки и основные эксплуатационные характеристики бетонов на основе золы, шлака и золошлаковой смеси.
3.Производство и использование бетонов на основе золы и шлака в строительстве.
А также легкие и пористые заполнители искусственного происхождения (аглопорит, керамзит и другие), природного происхождения (туф,пемза, а также и другие виды) или в сочетании с ними.
Использование шлаков, золы и золошлаковых смесей в сочетании с цементным вяжущим дает возможность получить в конечном итоге бетоны высоких марок :
1. По прочности – М50… М500.
2. По водонепроницаемости W2…W12 .
3. По морозостойкости F50…F300, а также бетонов следующих видов :
а) Легкий или тяжелый с добавлением золы взамен определенной части цемента, а также части заполнителей и части цемента.
б) Мелкозернистый бетон, приготовленный на золошлаковой смеси, имеющий плотность от 1800 до 2200 кг/м³.Золошлаковая смесь применяется взамен природного мелкого песка.
в) Тяжелый бетон с комбинированными заполнителями, состоящие из плотного шлака в сочетании с заполнителями природного происхождения или золошлаковой смеси .
г) Легкий бетон с комбинированными заполнителями состоящие из золошлаковой смеси, золы или пористого шлака совместно с природными или искусственными пористыми заполнителями.
д) Жаростойкий бетон состоящий из с комбинированных заполнителей: например, из золошлаковой смеси или плотного шлака в сочетании с заполнителями природного происхождения.
е) Ячеистый бетон.
Если ввести в состав бетонов оптимальное количество золошлаковой смеси или золы,то это позволит улучшить ряд очень значимых эксплуатационных свойств.Такие как- улучшенную удобоукладываемость бетона, высокую морозостойкость, высокую прочность а также позволит снизить усадку и водопроницаемость.
Использование золы в состав бетона не сказывается отрицательно на деформации ползучести, на модуль упругости бетона обычного состава и усадки. Наличие золы в состав бетона повышает значительно сульфатостойкость бетона и коррозионную стойкость железобетона. Бетон из шлака и золы а также на основе золошлаковой смеси принято называть золошлаковые бетоны и используются широко в разных областях строительства.
Производство и использование бетонов из шлака в строительстве
Золошлаковые бетоны не используются для покрытия верхнего слоя покрытий в строительстве автомобильных дорог,оболочек градирен и отводов вытяжных труб,пролетных строений мостов ,гидротехнических сооружений в тех частях где наиболее сильно подвергаются попеременному замораживанию и оттаиванию.Во время приготовления тяжелых бетонов на основе плотных заполнителях, золу добавляют в оптимальном количестве в следующих усредненных количествах:
1. На 1 м³ пропариваемого бетона -150 кг.
2.На 1 м³ бетона который твердеет без тепловой обработки (в естественных условиях) -100 кг.
Экономия цемента при этом может достичь до 50-70 кг на 1 м³ пропариваемого бетона и до 30-40 кг, для бетона твердеющего без тепловой обработки.Золу при этом вводят в бетонную массу одновременно, взамен части цемента, части песка и щебня,без изменения принятого между ними соотношения.Природный щебень заменяют на шлак в предельных соотношениях от 20 до 50 %, при этом зерна шлакового щебня выбираются крупнее 3 мм.
Когда определяется расход воды в бетонах на основе шлака и золы (золошлаковые бетоны),учитывают степень водопоглощения используемых заполнителей.Рисунок № 1. Расход золошлаковой смеси в зависимости от расхода цемента и содержания золы в золошлаковой смеси
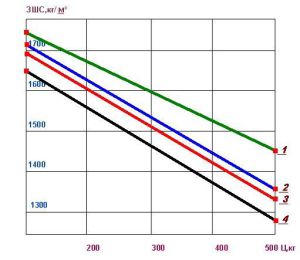
Расход золошлаковой смеси
Цифрой 1 обозначается расход цемента при содержании золы 16% ,2-24 %, 3- 30 % и 4-35 %.
Рисунок № 2. Зависимость прочности золошлакобетона от В/Ц бетонной смеси при марки цемента 300; 400 ; и 500.
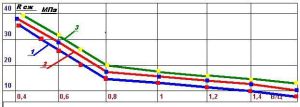
Зависимость прочности золошлакового бетона от В/Ц и марки цемента
На рисунке №2 приводится зависимость прочности золошлаковых бетонов от В/Ц и расхода цемента, где 1-марка цемента М 300; 2-400 и 3-500.Тепловую обработку изделий проводят при максимальной температуре (80…95 °С) при пропаривании бетона и 140…150 °С при сухом прогреве. При таких температурах гидравлические свойства золошлаковых материалов, наиболее максимально проявляются.
Продолжительность изотермического прогрева должна составлять не менее 9 часов.Общая длительность -не менее 14 часов включая и время необходимое для подъема температуры и охлаждения- не менее 14 часов. Благодаря разработанной технологии изготовления панелей перекрытий и стен на основе золошлаковых бетонов можно достичь высокое качество поверхности изделий, а также существенно уменьшить время уплотнения смеси (до 2-3 сек).
Это в свою очередь позволяет отказаться от шпаклевки поверхностей изделий под окраску,снизить стоимость изделий до 4 % и улучшить условия труда в цехе.Экономия достигается в основном за счет уменьшения расхода цемента и за счет исключения затрат связанные с отделкой поверхностей. Легкобетонные смеси, которые содержат золошлаковые материалы, имеют пониженную расслаиваемость и повышенную воздухоудерживающую способность. Легкобетонные смеси менее чувствительны к воздействию перегрузок и при транспортировании посредством ленточного конвеера.
Рисунок № 3. Зависимость прочности золошлакобетона от расхода цемента марки : 1-300; 2-400 и 3- 500.
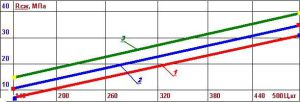
Зависимость прочности золошлакобетона от расхода цемента
При введении золы в состав легкобетонной смеси повышается ее вязкость в статическом состоянии,но это не влияет во время вибрации на условия ее тиксотропного разжижения.Бетонные смеси с добавкой золы имеют хорошую удобоукладываемость,заполняют легко формы и уплотняются под воздействием вибрации.Зола и золошлаковая смесь ТЭС используется при изготовлении керамзитобетона,в целях снижения расхода цемента и для экономии дорогих искусственных пористых заполнителей.Также используется для уменьшения средней плотности легких бетонов, для полной замены или уменьшения расхода плотного песка.
Таблица №1. Характеристика керамзитобетона с золой в качестве мелкого заполнителя
По сравнению с керамзитобетоном приготовленного на дробленном керамзитовом песке, средняя плотность конструкционно -теплоизоляционного керамзитобетона на золе снижается на 50 кг/м³. При этом расход керамзита уменьшается на 0,4…0,6 м³ (с учетом потребностей на дробление).
Таблица №2. Состав жаростойких бетонов с добавкой золы
Зола и золошлаковые смеси широко используются как заполнители и для приготовления жаростойкого бетона на портландцементе с температурой выдержки до 1000 °С.
Просмотров: 495
РЕКОМЕНДУЕМ выполнить перепост статьи в соцсетях!
Бетон из шлака
Бетон из шлака
Укладка бетона в опалубку
В производстве бетонов широкое использование находят шлаки, золы и золошлаковые смеси. Они с успехом заменяют традиционные заполнители природного происхождения,такие как песок, щебень или гравий, легкие и пористые заполнители искусственного происхождения (аглопорит, керамзит и другие), природного происхождения (туф,пемза, а также и другие виды) или в сочетании с ними.
Содержание статьи:
1. Использование золы и шлаков в производстве бетонов.
2. Виды , прочностные марки и основные эксплуатационные характеристики бетонов на основе золы, шлака и золошлаковой смеси.
3.Производство и использование бетонов на основе золы и шлака в строительстве.
А также легкие и пористые заполнители искусственного происхождения (аглопорит, керамзит и другие), природного происхождения (туф,пемза, а также и другие виды) или в сочетании с ними.
Использование шлаков, золы и золошлаковых смесей в сочетании с цементным вяжущим дает возможность получить в конечном итоге бетоны высоких марок :
1. По прочности – М50… М500.
2. По водонепроницаемости W2…W12 .
3. По морозостойкости F50…F300, а также бетонов следующих видов :
а) Легкий или тяжелый с добавлением золы взамен определенной части цемента, а также части заполнителей и части цемента.
б) Мелкозернистый бетон, приготовленный на золошлаковой смеси, имеющий плотность от 1800 до 2200 кг/м³.Золошлаковая смесь применяется взамен природного мелкого песка.
в) Тяжелый бетон с комбинированными заполнителями, состоящие из плотного шлака в сочетании с заполнителями природного происхождения или золошлаковой смеси .
г) Легкий бетон с комбинированными заполнителями состоящие из золошлаковой смеси, золы или пористого шлака совместно с природными или искусственными пористыми заполнителями.
д) Жаростойкий бетон состоящий из с комбинированных заполнителей: например, из золошлаковой смеси или плотного шлака в сочетании с заполнителями природного происхождения.
е) Ячеистый бетон.
Если ввести в состав бетонов оптимальное количество золошлаковой смеси или золы,то это позволит улучшить ряд очень значимых эксплуатационных свойств.Такие как- улучшенную удобоукладываемость бетона, высокую морозостойкость, высокую прочность а также позволит снизить усадку и водопроницаемость.
Использование золы в состав бетона не сказывается отрицательно на деформации ползучести, на модуль упругости бетона обычного состава и усадки. Наличие золы в состав бетона повышает значительно сульфатостойкость бетона и коррозионную стойкость железобетона. Бетон из шлака и золы а также на основе золошлаковой смеси принято называть золошлаковые бетоны и используются широко в разных областях строительства.
Производство и использование бетонов из шлака в строительстве
Золошлаковые бетоны не используются для покрытия верхнего слоя покрытий в строительстве автомобильных дорог,оболочек градирен и отводов вытяжных труб,пролетных строений мостов ,гидротехнических сооружений в тех частях где наиболее сильно подвергаются попеременному замораживанию и оттаиванию.Во время приготовления тяжелых бетонов на основе плотных заполнителях, золу добавляют в оптимальном количестве в следующих усредненных количествах:
1. На 1 м³ пропариваемого бетона -150 кг.
2.На 1 м³ бетона который твердеет без тепловой обработки (в естественных условиях) -100 кг.
Экономия цемента при этом может достичь до 50-70 кг на 1 м³ пропариваемого бетона и до 30-40 кг, для бетона твердеющего без тепловой обработки.Золу при этом вводят в бетонную массу одновременно, взамен части цемента, части песка и щебня,без изменения принятого между ними соотношения.Природный щебень заменяют на шлак в предельных соотношениях от 20 до 50 %, при этом зерна шлакового щебня выбираются крупнее 3 мм.
Когда определяется расход воды в бетонах на основе шлака и золы (золошлаковые бетоны),учитывают степень водопоглощения используемых заполнителей. Рисунок № 1. Расход золошлаковой смеси в зависимости от расхода цемента и содержания золы в золошлаковой смеси
Расход золошлаковой смеси
Цифрой 1 обозначается расход цемента при содержании золы 16% ,2-24 %, 3- 30 % и 4-35 %.
Рисунок № 2. Зависимость прочности золошлакобетона от В/Ц бетонной смеси при марки цемента 300; 400 ; и 500.
Зависимость прочности золошлакового бетона от В/Ц и марки цемента
На рисунке №2 приводится зависимость прочности золошлаковых бетонов от В/Ц и расхода цемента, где 1-марка цемента М 300; 2-400 и 3-500.Тепловую обработку изделий проводят при максимальной температуре (80…95 °С) при пропаривании бетона и 140…150 °С при сухом прогреве. При таких температурах гидравлические свойства золошлаковых материалов, наиболее максимально проявляются.
Продолжительность изотермического прогрева должна составлять не менее 9 часов.Общая длительность -не менее 14 часов включая и время необходимое для подъема температуры и охлаждения- не менее 14 часов. Благодаря разработанной технологии изготовления панелей перекрытий и стен на основе золошлаковых бетонов можно достичь высокое качество поверхности изделий, а также существенно уменьшить время уплотнения смеси (до 2-3 сек).
Это в свою очередь позволяет отказаться от шпаклевки поверхностей изделий под окраску,снизить стоимость изделий до 4 % и улучшить условия труда в цехе.Экономия достигается в основном за счет уменьшения расхода цемента и за счет исключения затрат связанные с отделкой поверхностей. Легкобетонные смеси, которые содержат золошлаковые материалы, имеют пониженную расслаиваемость и повышенную воздухоудерживающую способность. Легкобетонные смеси менее чувствительны к воздействию перегрузок и при транспортировании посредством ленточного конвеера.
Рисунок № 3. Зависимость прочности золошлакобетона от расхода цемента марки : 1-300; 2-400 и 3- 500.
Зависимость прочности золошлакобетона от расхода цемента
При введении золы в состав легкобетонной смеси повышается ее вязкость в статическом состоянии,но это не влияет во время вибрации на условия ее тиксотропного разжижения.Бетонные смеси с добавкой золы имеют хорошую удобоукладываемость,заполняют легко формы и уплотняются под воздействием вибрации.Зола и золошлаковая смесь ТЭС используется при изготовлении керамзитобетона,в целях снижения расхода цемента и для экономии дорогих искусственных пористых заполнителей.Также используется для уменьшения средней плотности легких бетонов, для полной замены или уменьшения расхода плотного песка.
Таблица №1. Характеристика керамзитобетона с золой в качестве мелкого заполнителя
По сравнению с керамзитобетоном приготовленного на дробленном керамзитовом песке, средняя плотность конструкционно -теплоизоляционного керамзитобетона на золе снижается на 50 кг/м³. При этом расход керамзита уменьшается на 0,4…0,6 м³ (с учетом потребностей на дробление).
Таблица №2. Состав жаростойких бетонов с добавкой золы
Зола и золошлаковые смеси широко используются как заполнители и для приготовления жаростойкого бетона на портландцементе с температурой выдержки до 1000 °С.
stroivagon.ru
Шлакобетон: виды, самостоятельное приготовление раствора
Шлакобетон широко используется в частной застройке из-за целого ряда достоинств и простоте работы с материалом. Благодаря тому, что материал намного легче обычного бетона, его использование позволяет снизить нагрузку на конструкции дома при том, что теплоизолирующие свойства сохраняются на достаточно высоком уровне. Рассмотрим основные виды данной группы изделий, их преимущества и особенности использования.
Шлакобетонные блоки обладают высокими эксплуатационными свойствами
Обзор основных особенностей материала
Чтобы принять решение о целесообразности использования подобных изделий, необходимо знать всю информацию о них, чтобы сравнить с другими вариантами и сделать правильные выводы (читайте также статью «Бетонирование дорожек на даче – особенности проведения работ»).
Виды изделий
В зависимости от используемого наполнителя и особенностей приготовления состава можно выделить несколько основных групп:
- Шлакобетон изготавливается на основе шлаков металлургического производства. Лучше всего подходит шлак антрацита, но и другие варианты также обладают достаточно высокими характеристиками. Главное условие, о котором не стоит забывать: материал должен быть чистым, без примесей чернозема, остатков растений и других загрязнений.
- Шлакопемзобетон изготавливается на основе шлаковой пемзы, представляющей собой вспученный доменный шлак в виде щебня диаметром 2-3 сантиметра. Еще одно название материала – термозит, из-за чего готовый материал имеет еще одно название – термозитобетон, но это то же самое.
- Еще один интересный вариант – шлакощелочной пенобетон. Добавление щелочи в шлаки придает материалу высокие свойства морозостойкости, а также устойчивости изделий к влаге и перепадам температур. Такие конструкции отлично подходят даже для сложных условий эксплуатации, в качестве щелочной добавки может использоваться известь, кальцинированная или каустическая сода, а также жидкое стекло.
Добавление щелочи добавляет изделиям прочность и стойкость к неблагоприятным воздействиям
Достоинства и недостатки данной группы изделий
Чтобы понять все плюсы и минусы шлакобетонного дома, нужно знать все особенности материала (см.также статью «Методы склеивания таких материалов, как пенополистирол и бетон, с целью создания качественного утепления»).
В первую очередь рассмотрим преимущества:
- Технические характеристики шлакобетона достаточно высоки, благодаря чему его можно использовать для малоэтажной застройки любого назначения. Универсальность использования позволяет применять его практически для любых целей.
- Отличные теплосберегающие свойства позволяют сэкономить значительные средства на обогрев в дальнейшем. Это очень полезно как в регионах с холодными зимами, так и в теплых поясах: в таких строениях постоянно будет поддерживаться микроклимат, приближенный к оптимальному.
- Все знают, что резка железобетона алмазными кругами – процесс трудоемкий и сложный, но резать изделия на основе шлаков в разы легче, это упрощает самостоятельную работу и позволяет провести работы за меньшее время. Это касается и прокладки коммуникаций: если алмазное бурение отверстий в бетоне требует наличия специального оборудования, то рассматриваемый нами материал можно просверлить и самостоятельно.
- В зависимости от особенностей применения можно выбрать как полнотелые блоки, так и варианты с пустотами, которые гораздо легче. При этом и конфигурация пустот может очень сильно различаться, но согласно строительным нормам пустотность не должна превышать 40%.
Пустоты облегчают изделия, но снижаются и показатели прочности
- Еще одно очень важное свойство, которым обладает шлакобетон – стойкость к огню. Материал не поддерживает горение, что значительно повышает уровень безопасности возводимых объектов.
- Изделия устойчивы к поражению плесенью и грибком, что также немаловажно в случаях, когда на конструкции постоянно воздействует избыточная влажность, губительная для большинства аналогов.
- Хорошая паропроницаемость конструкций делает помещение комфортным для проживания. Свойства рассматриваемого материала приближены к характеристикам древесины – идеального варианта для использования в жилых комнатах.
- Еще одно несомненное достоинство – низкая цена бетонных изделий на основе шлака, благодаря чему данный вариант относится к одним из самых доступных.
- Возможность возведения строений, как с применением шлакоблоков, так и методом монолитных конструкций. Это позволяет добиться высокой прочности и долговечности там, где это особенно необходимо.
На фото: при возведении стен монолитным способом важно провести качественное армирование
- Еще одно большое преимущество – возможность изготовления изделий своими руками. При этом характеристики шлакобетонных блоков зависят от пропорций компонентов. Специальные формы позволяют создать идеально ровные блоки и упрощают рабочий процесс.
Специальные формы позволяют сделать блоки прямо на стройплощадке
Конечно, нельзя не затронуть и недостатки, их немного:
- Одна из главных проблем, это очень длительный период набора прочностных характеристик. Через 4 недели блок набирает только 50% прочности, а полное затвердевание происходит примерно в течение года.
- При самостоятельном изготовлении очень важно периодически увлажнять материал, иначе он потрескается.
- Из-за большой усадки отделку помещений желательно начинать не ранее, чем через год после возведения сооружения.
Совет! Если вы приобретаете готовые изделия, то следует уделить особое внимание качеству материала. Маленькие полукустарные производства не имеют надежной системы контроля качества, поэтому велика вероятность брака. Лучше выбирать проверенных изготовителей.
Особенности самостоятельного приготовления раствора
Как отмечалось выше, состав шлакобетона достаточно прост, и его можно приготовить своими руками.
Инструкция по приготовлению раствора несложная, но все же имеет целый ряд особенностей:
- Вначале нужно подготовить шлак, для этого его необходимо просеять для получения двух фракций: вначале через сетку 40*40 мм, а затем через сетку 5*5 мм. Оптимальное соотношение крупной и мелкой фракций при изготовлении изделий для стен 3:7.
Слишком большие гранулы шлака снижают прочность конструкций, поэтому и нужно просеивание
Совет! Чтобы добиться наивысшей прочности готовых изделий, шлак желательно замочить в воде за несколько часов до применения, это позволит снизить забивание пор цементом и увеличить свойства вяжущего компонента.
- Далее следует смешать две фракции шлака так, как указано выше, должна получиться равномерная масса.
- Для снижения стоимости и повышения влагостойкости требуется добавление щелочи. Самый популярный вариант раствора следующий: цемент марки М500 1 часть, известь пушонка гашеная 0,8 части, песок 3 части и смешанный шлак 12 частей. Такие пропорции шлакобетона позволяют добиться оптимального соотношения высоких теплоизоляционных свойств и прочности изделий.
Важно! Применение извести позволяет не только повысить прочность, но сделать раствор гораздо пластичнее, что повышает удобство работы с ним.
Известь стоит немного, но благодаря ей значительно улучшаются свойства раствора
- Все компоненты тщательнейшим образом перемешиваются. Чем лучше это сделано, тем выше будет прочность конструкций. Если вы не используете бетономешалку, то лучше всего использовать обыкновенные металлические грабли.
- В последнюю очередь добавляется вода, и состав опять же размешивается до однородной массы.
- Использовать готовый раствор желательно в течение 60-80 минут.
Как отмечалось выше, при высыхании важно проводить периодическое увлажнение поверхности, чтобы избежать появления трещин на поверхности.
Многие выбирают данный вариант в качестве основного материала для возведения дома
Вывод
Как видите, можно сделать шлакобетон своими руками, а можно приобрести и готовые изделия. Стоит помнить, что при всех достоинствах прочность данного варианта все-таки ниже, чем у обычного бетона, поэтому обращаться с ним стоит бережнее (см.также статью «Железнение бетона: способы, материалы, последующая обработка»).
Видео в этой статье подробнее расскажет некоторые факты касательно рассматриваемой в данном обзоре темы.
rusbetonplus.ru
Шлакобетон и шлакощелочной бетон: сырьё и способы их производства
При строительстве малоэтажных сооружений невысокие нагрузки на стены позволяют существенно расширить ассортимент материалов, из которых можно возводить стеновые и другие строительные конструкции. Это относится и к шлакобетону, который хоть и принадлежит к категории тяжёлых бетонов, но имеет гораздо меньший вес, чем аналоги на традиционных заполнителях – гравии и щебне природного происхождения. Из молотого шлака может быть изготовлен и полноценный вяжущий компонент – шлакощелочной цемент, способный качественно заменить традиционный портландцемент.
Требования к шлаку
Шлак – это сопутствующий продукт, представляющий собой сплав различного рода оксидов, образующийся при высокотемпературной обработке сырья. В зависимости от состава сырьевых материалов шлак может быть основным или кислым.
Для производства шлакобетона подходит не любое сырьё. Основным требованием к шлаку является отсутствие в сплаве оксидов химических соединений, отрицательно воздействующих на характеристики получаемого строительного материала. Особые требования предъявляются и к чистоте шлака. Он должен быть свободен от земли, глины, золы и иного мусора.
Для производства шлакобетона применяют шлаки металлургической и топливной промышленности.
Применение металлургического шлака даёт возможность получать более прочный бетон. Из шлаков топливной промышленности наиболее подходящим сырьём являются продукты горения антрацитных пород. Непригодны для производства бетона продукты сгорания бурых углей, так как они содержат примеси, присоединенные к шлаку на основе неустойчивых связей.
Желательно, чтобы при хранении шлак около трёх раз перемещали с места на место. Такая мера позволяет достигнуть высокой степени очистки материала от примесей извести и серы.
Предназначенный для производства бетона шлак не менее полугода должен храниться на открытом воздухе. За этот период материал приобретает необходимые свойства, а под воздействием атмосферных осадков он освобождается от вредных компонентов.
Шлаки остаются пригодными для производства шлакобетона до тех пор, пока сохраняется их кристаллическая структура и не проявляются признаки распада, которые возникают при переходе одних соединений материала в другие под влиянием влаги и газов, находящихся в воздухе. Новые соединения имеют больший объём, чем первоначальные, поэтому такой переход сопровождается растрескиванием и разрушением кусков шлака.
Особенности изготовления шлакобетона
В зависимости от размеров зерен шлак для шлакобетона разделяют на щебень, имеющий фракцию 5-40 мм, и песок с гранулами до 5 мм. Применение шлакового песка повышает такие показатели бетона, как прочность и плотность. Благодаря использованию шлакового щебня получают более лёгкий бетон с высокими теплоизоляционными свойствами, но более низкими прочностными характеристиками.
Для приготовления шлакобетона используют два вида сит: с крупными (40 х 40 мм) и мелкими (5 х 5 мм) ячейками.
- Для изготовления наружных стен для бетона берут 7 частей крупного и 3 части мелкого шлака.
- Для внутренних стен пропорция фракций будет несколько иной: 6 частей крупных зёрен и 4 части мелких.
Увеличить прочность шлакобетона можно заменой пятой части самой мелкой фракции на обычный песок и исключением из состава смеси наиболее крупных зёрен шлака.
Для снижения стоимости сооружения из шлакобетона возможно использование в его составе сочетания двух вяжущих компонентов: цемента и глины, цемента и извести. Оптимальные пропорции компонентов вяжущего в шлакобетоне: цемент – не менее 2/3 от объёма вяжущего, известь – не более 1/3.
Добавки глины и извести не только удешевляют строительство, но и делают стены более сухими и тёплыми. Известковый шлакобетон, вяжущее которого состоит из 1/3 извести и 2/3 глины, твердеет гораздо дольше цементного, но в дальнейшем он имеет более высокие прочностные характеристики.
Перед установкой перекрытий со времени сооружения стен из известкового шлакобетона должно пройти не менее трёх месяцев. Такие стены необходимо начинать возводить в начале тёплого периода года, чтобы успеть закончить работы до наступления морозов.
Известь можно не добавлять, но в этом случае смесь не будет обладать достаточной пластичностью и её невозможно будет перемешать до образования однородного цвета массы.
Качество перемешивания оказывает существенное влияние на несущую способность строительных конструкций из шлакобетона.
Последовательность приготовления шлакобетона своими руками аналогична производству традиционного строительного материала:
- в сухом состоянии смешивают песок, цемент и шлак, который предварительно увлажняют;
- добавляют глиняное или известковое тесто, этот компонент способствует повышению пластичности смеси;
- заливают воду.
Использование шлакобетона при возведении различных строительных конструкций
Шлакобетон на сегодняшний день является одним из наиболее дешевых строительных материалов. Из шлакобетона изготавливают не только стены, но и армированные плиты перекрытия. Если весь дом сооружается из облегченных материалов, то для устройства фундамента и пола также возможно использование шлакобетона.
Для возведения стен может быть применена монолитная технология с переставной опалубкой. Но всё большую популярность приобретают готовые стеновые и фундаментные блоки из шлакобетона.
Шлакобетон классифицируется по маркам. Марка 10 применяется в основном для теплоизоляции. Из шлакобетона марок 25 и 35 возводят не несущие конструкции, марка 50 применяется для изготовления армированных перемычек, внутренних и наружных несущих стен.
Главным преимуществом шлакобетона является его меньший удельный вес по сравнению с керамическим или силикатным кирпичом. Это свойство позволяет снизить нагрузку на фундамент и прочие несущие конструкции строения. Большие размерные параметры блоков способствуют сокращению временных и материальных затрат на их укладку. Шлакобетонные блоки удобны для транспортировки.
К недостаткам блоков из шлакобетона можно отнести их медленное твердение. Через месяц после изготовления этот материал приобретает всего половину своей марочной прочности.
Полное соответствие всем заложенным в данной марке характеристикам у шлакобетонных блоков наступает примерно через год после их изготовления.
Стены из шлакобетона гигроскопичны, легко впитывают воду, поэтому у такого сооружения крыша должна иметь свесы не менее 500 мм. Предохранять шлакобетонные элементы от воздействия влаги необходимо уже через 2-3 дня после их производства.
Наиболее высокой теплопроводностью обладает шлакобетон марки 10. Если вы хотите сами приготовить материал с повышенной теплоизоляцией, добавьте в вяжущее вещество известь или гипс.
Особенности шлакощелочного бетона
Высокие цены на портландцемент привели к поискам более дешевых типов вяжущего компонента. Одной из наиболее интересных находок можно назвать шлакощелочной цемент. История его использования началась в Германии ещё в начале девятнадцатого века, а в современных условиях он применяется на строительных площадках во всём мире. Создание таких цементов стало возможным благодаря установлению вяжущих способностей у соединений щелочных металлов, к которым относятся литий, натрий, калий, рубидий, цезий.
Шлакощелочной цемент – вяжущее высокой прочности, состоящее из молотого шлака и любой щёлочи – жидкого стекла, соды и других.
На базе шлакощелочного цемента получают железобетонные элементы с повышенной устойчивостью к химически агрессивным веществам. При их изготовлении могут быть использованы загрязненные глинистыми включениями наполнители.
Шлакощелочной бетон является незаменимым при возведении массивных объектов. Это связано с тем, что при изготовлении крупных элементов из бетона на портландцементе происходит выделение значительного количества тепла, при этом температура конструкции может достигать 80°С. Если охлаждение бетонного объекта произойдет слишком быстро, то могут образоваться деформационные трещины. Применение шлакощелочного бетона даёт возможность избежать возникновения этой проблемы.
Наиболее широкое применение получил шлакощелочной цемент на базе молотого металлургического шлака и соединений щелочных металлов, у которых преобладающими являются гидросиликаты кальция, а вспомогательными – гидроалюмосиликаты.
Достоинства бетона на основе шлакощелочного цемента
- Применение бетона на шлакощелочном цементе позволяет получать конструкции с меньшим количеством капиллярных пор, чем при использовании обычного бетона на портландцементе. Это свойство существенно снижает водопоглощение и повышает морозоустойчивость бетона, что способствует росту эксплуатационных качеств строительной конструкции.
- Коррозия арматуры в шлакощелочном бетоне протекает значительно медленнее, чем в традиционном материале.
- Прочность бетона на шлакощелочном вяжущем достигает 130 МПа.
- Бетонная смесь прекрасно укладывается, а изготовленные элементы хорошо обрабатываются.
- В первые сутки материал набирает около 30% прочности.
- Такие бетоны устойчивы к воздействию морской воды и некоторых других агрессивных сред – кислот, хлоридов, сульфатов.
Благодаря возможности управлять свойствами шлакощелочного цемента на разных стадиях структурообразования стало возможным получение вяжущих со специальными свойствами: жаро- и морозостойких, с повышенной коррозионной устойчивостью, безусадочных, с высокой скоростью твердения, тампонажных.
Состав возможных смесей шлакобетона
Марка шлакобетона | Объемный состав (в частях) | Объемный вес | ||||
Цемент 400 | Известь или глина | Песок | Мелкий шлак | Крупный шлак | ||
10 | 0,9 | 2 | 1 | 5 | 12 | 700 |
10 | 0,9 | 0,7 | 1 | 3 | 8 | 1100 |
25 | 1 | 1 | 2 | 6 | 12 | 900 |
25 | 0,9 | 0,5 | 2 | 3 | 5 | 1300 |
35 | 1 | 0,8 | 3 | 6 | 8 | 1100 |
35 | 0,9 | 0,3 | 2 | 3 | 3 | 1500 |
50 | 1 | 0,6 | 3 | 6 | 5 | 1300 |
www.navigator-beton.ru
Бетон из шлака: как приготовить своими руками
Шлакобетонные смеси пользуются заслуженной популярностью не только в промышленном, но и в частном малоэтажном строительстве. Это обусловлено характеристиками данного материала. Шлаки, добавляемые в состав бетона, получают в качестве вторичного материала в металлургической промышленности.
Длительное время гранулированный материал считался просто отходами, но мировая практика доказала его целесообразность для применения в строительстве. Шлаковый бетон более легкий, нежели песчано-гравийный, отличается своей долговечностью, устойчивостью к колебаниям температуры, звукоизолирующими свойствами.
Наибольшей прочностью обладает именно металлургический материал в смеси с цементом. Также в качестве вяжущего агента могут выступать известь, гипс или даже глина. Активно используются две разновидности гранулированного шлака:
- с мелкими зернами (0,5-1,5 мм) – получается довольно тяжелый бетон высокой прочности с хорошей теплопроводностью;
- с крупными зернами (20-30 мм) – бетон более легкий, обеспечивает хорошую теплоизоляцию, но чуть менее долговечен.
Использовать разновидности крупнее 6 мм не рекомендуется, поскольку долговечность такого бетона будет неудовлетворительной. Более мелкие фракции предпочтительно заменить песком. Шлак для строительства должен быть максимально чистым, без примесей глины, почвы, органических элементов.
Учитывая свойства бетона с разной фракцией, для создания наружных стен часто смешивают крупные и мелкие зерна в пропорции 7:3 соответственно. Для внутренних перегородок можно взять на единицу больше мелкого шлака. Если вы хотите получить максимально прочную после застывания смесь, желательно полностью убрать фракцию 12 мм, а 20% самого мелкого шлака заменить песком.
Как приготовить шлакобетон
До начала приготовления смеси (примерно за несколько часов) необходимо увлажнить шлак водой, чтобы улучшить долговечность будущего бетона. Далее необходимо смешать компоненты в одной из указанных выше пропорций, хорошо перемешать. После добавления воды раствор следует вымесить до однородного состояния. Для получения средней марки бетона, можно использовать 4-5 частей шлака (фракционной смеси), 2 части цемента и 2 части песка.
Готовую массу желательно использовать в течение часа, максимальное время обработки – 1,5 часа. Более дешевым раствор можно сделать, смешав цемент с известью в соотношении 3:1. Стены дома могут быть возведены набивным методом (монолитная конструкция) или из приготовленных шлакобетонных блоков.
postroika.com.ua
vest-beton.ru
Бетон из шлака: как приготовить своими руками
Шлакобетонные смеси пользуются заслуженной популярностью не только в промышленном, но и в частном малоэтажном строительстве. Это обусловлено характеристиками данного материала. Шлаки, добавляемые в состав бетона, получают в качестве вторичного материала в металлургической промышленности.
Длительное время гранулированный материал считался просто отходами, но мировая практика доказала его целесообразность для применения в строительстве. Шлаковый бетон более легкий, нежели песчано-гравийный, отличается своей долговечностью, устойчивостью к колебаниям температуры, звукоизолирующими свойствами.
Наибольшей прочностью обладает именно металлургический материал в смеси с цементом. Также в качестве вяжущего агента могут выступать известь, гипс или даже глина. Активно используются две разновидности гранулированного шлака:
- с мелкими зернами (0,5-1,5 мм) – получается довольно тяжелый бетон высокой прочности с хорошей теплопроводностью;
- с крупными зернами (20-30 мм) – бетон более легкий, обеспечивает хорошую теплоизоляцию, но чуть менее долговечен.
Использовать разновидности крупнее 6 мм не рекомендуется, поскольку долговечность такого бетона будет неудовлетворительной. Более мелкие фракции предпочтительно заменить песком. Шлак для строительства должен быть максимально чистым, без примесей глины, почвы, органических элементов.
Учитывая свойства бетона с разной фракцией, для создания наружных стен часто смешивают крупные и мелкие зерна в пропорции 7:3 соответственно. Для внутренних перегородок можно взять на единицу больше мелкого шлака. Если вы хотите получить максимально прочную после застывания смесь, желательно полностью убрать фракцию 12 мм, а 20% самого мелкого шлака заменить песком.
Как приготовить шлакобетон
До начала приготовления смеси (примерно за несколько часов) необходимо увлажнить шлак водой, чтобы улучшить долговечность будущего бетона. Далее необходимо смешать компоненты в одной из указанных выше пропорций, хорошо перемешать. После добавления воды раствор следует вымесить до однородного состояния. Для получения средней марки бетона, можно использовать 4-5 частей шлака (фракционной смеси), 2 части цемента и 2 части песка.
Готовую массу желательно использовать в течение часа, максимальное время обработки – 1,5 часа. Более дешевым раствор можно сделать, смешав цемент с известью в соотношении 3:1. Стены дома могут быть возведены набивным методом (монолитная конструкция) или из приготовленных шлакобетонных блоков.
postroika.com.ua
Цемент со шлаком пропорции для бетона
Применение смеси цемента со шлаком
Комментариев:
Рейтинг: 70
Оглавление: [скрыть]
- Особенности смесей в рамках бытового применения
- Использование в более серьезных целях
В настоящее время распространенной строительной смесью является цемент со шлаком, применение которой себя оправдало. Ведь именно эти составляющие в комплексе способны придать прочности любому раствору и подобному составу для отделки.
Схемы производства цемента разными способами.
Особенности смесей в рамках бытового применения
Есть множество вариантов применения шлака с цементом в ремонтных и строительных работах.
Но для начала будет целесообразным рассмотреть особенности такого бетона, которые наиболее уместны для отдельно взятых случаев его применения.
Таблица сроков схватывания цемента с разным типом шлака.
- Как правило, отличаются особенности изготавливаемой смеси для наружных и внутренних отделок. Если вы собираетесь сделать раствор на основе шлака и цемента, которым будете отделывать внутренние поверхности, то следует отдать предпочтение крупнозернистому шлаку, которого нужно взять примерно 6 частей. Остальные 4 части — мелкозернистый гранулированный шлак. Цемент для бетона может быть использован любой. Для отделки наружного фасада здания принято использовать такие пропорции: примерно 3 части мелкозернистого шлака и 7 частей крупнозернистого. Цемент нужно брать более качественный, чтобы он обладал достаточной устойчивостью к внешним атмосферным воздействиям.
- Если вам нужно сделать качественную заливку, и времени в запасе есть достаточно, то следует отдать свое предпочтение негранулированному шлаку. Эта смесь будет заметно медленнее застывать, но в результате покрытие будет намного качественнее. Ведь на нем долго не будут образовываться трещины, появление которых наблюдается уже через 1-2 года на залитом цементном полу.
- Для отделки наружной части выступающего фундамента (цоколя) специалисты рекомендуют использовать цемент со шлаком гранулированным. При этом, чем больше отделываемая поверхность, тем больше гранулы в шлаке могут быть использованы. И наоборот.
Строительство стены из шлакоблока.
Итак, это были основные особенности использования шлака и цемента в обычном бытовом строительстве. Соблюдая такие несложные правила, вы сможете добиться качественной отделки и ни о чем не жалеть в последующем.
При этом у вас появляется отличная возможность произвести хоть незначительную, но все же экономию денежных средств за счет четкого выбора конкретных пропорций.
Вернуться к оглавлению
Но есть еще и немного другие, более серьезные сферы применения цемента со шлаком. В основном применяется шлаковый портландцемент, который считается одним из наиболее прочных и надежных строительных материалов. Чтобы предвидеть хороший результат от смеси цемента со шлаком, применение материала должно быть правильно продумано.
Схема формирования стен из шлакобетона.
- Шлаковый портландцемент все чаще применяется для изготовления плит перекрытия при строительстве многоэтажных домов. Это связано с тем, что высокий уровень надежности материала обеспечивает долговечную службу перекрытий, что так важно для безопасности жилых домов.
- Смесь цемента и шлака применяется для устройства фундаментов зданий. Это очень актуально, в особенности если стены в доме планируется делать из облегченных строительных материалов. Именно фундамент здесь будет служить основательной опорной конструкцией.
- Из шлакобетона, изготовляемого на основе смеси самого качественного вида цемента со шлаком, изготавливаются армированные пояса. Они также распространены в проектах многоэтажного строительства, а еще для армирования отдельных инженерных конструкций.
- Смесь высококачественных шлака и цемента очень востребована в строительстве подводных и околоводных сооружений, в том числе и инженерных. Ведь такие конструкции сильно подвержены воздействию пресной воды, которая со временем имеет свойство разрушать несоответствующие такому строительству конструкции.
- Также данная смесь нашла свое применение и в отдельных видах теплоизоляции помещений. Особенно качественно все получается в комплексе со стандартными утеплителями. Это придает помещению максимальную степень защищенности от проникновения холода. Это наиболее хорошо проявляется в использовании функциональной штукатурки, которая и дефекты заделывает, и вид стене придает более ухоженный.
Но и это еще не все. Классов шлакового портландцемента на сегодняшний день так много, что специалисты успели выделить из них самые распространенные и хорошие, которые наиболее целесообразно применять для тех или иных задач в строительно-ремонтных работах.
Класс типа 50 используется для армирования, а еще для изготовления разных несущих стен. А 35 класс применяется для строительства ненесущих элементов здания. Класс под номером 25 также используется для неосновных мелких конструкций. А вот 10-й класс нашел активное свое применение в теплоизоляционных работах.
tolkobeton.ru
Цемент со шлаком: применение смеси
Портландцемент представляет собой вяжущее гидравлическое вещество, получаемое методом измельчения цементного клинкера, гипса и гранулированного шлака.
Цемент со шлаком применяют с 1824 года. Это соединение справедливо может быть названо наиболее популярным видом цемента, нашедшим свое применение во всех сферах строительства.
Смесь цемента со шлаком используют уже почти 2 столетия, за это время данный материал нашел применение во всех сферах строительства.
Технология производства
Такой материал производят с использованием доменного шлака, который представляет собой вторичный продукт металлургического производства. Класс данного материала определяется качеством исходных материалов клинкера и доменных шлаков. Клинкер исполняет роль активизатора шлаков в составе шлакоцемента.
В основе технологии производства лежит принцип высушивания шлака в сушилках до получения показателей влажности не более 1%. Затем клинкер, шлак и гипс загружается в бункер цементной мельницы, и измельчается до гомогенного тонкодисперсного порошка.
Класс шлакоцемента зависит и от используемого вида шлака: это могут быть основные, кислые, гранулированные и негранулированные шлаки. Особое значение в определении прочности имеет не физическая структура, а химический состав. На данной закономерности основывается правило выбора сырья. С экономической стороны предпочтение стоит отдать гранулированным видам, в связи с тем, что использование негранулированных масс усложняет производственный процесс. Цемент со шлаком, который получается в результате, затвердевает медленнее обычного, потому что содержание шлака в нем варьируется в пределах 20-80% общей массы.
При изготовлении портландцемента используют сито с крупными (40х40 мм) и мелкими (5х5 мм) ячейками.
Шлаковый портландцемент изготавливают, используя два вида сит: с мелкими (5х5 мм) и крупными (40х40 мм) ячейками.
- При использовании материала для наружных стен соединяют крупный и мелкий шлак в соотношении 7:3.
- Для внутренних стен в пропорции 4 части мелких зерен и 6 частей крупных.
- Для увеличения прочности материала заменяют пятую части самой мелкой фракции обычным песком и исключают из состава наиболее крупные зерна шлака.
- Благодаря использованию сочетаний 2-х вяжущих компонентов (цемента и извести, цемента и глины) удается существенно снизить стоимость материала. Наиболее оптимальной являются пропорция: известь – не более 1/3 и цемент – не менее 2/3 общего объема.
Глина и известь способны не только снизить стоимость, но и делают стены более теплыми и сухими. Известковый портландцемент на основе шлака, в состав вяжущего которого входит 2/3 глины и 1/3 извести, твердеет дольше цементного, однако в дальнейшем показывает более высокие показатели прочности.
Состав возможных смесей шлакобетона
Класс шлакобетона | Объемный состав (в частях) | Объемный вес | ||||
Цемент 400 | Песок | Известь или глина | Крупный шлак | Мелкий шлак | ||
50 | 1 | 3 | 0,6 | 5 | 6 | 1300 |
35 | 0,9 | 2 | 0,3 | 3 | 3 | 1500 |
35 | 1 | 3 | 0,8 | 8 | 6 | 1100 |
25 | 0,9 | 2 | 0,5 | 5 | 3 | 1300 |
25 | 1 | 2 | 1 | 12 | 6 | 900 |
10 | 0,9 | 1 | 0,7 | 8 | 3 | 1100 |
10 | 0,9 | 1 | 2 | 12 | 5 | 700 |
Технические характеристики
Портландцемент характеризуется медленным твердением, а достаточная прочность достигается за 6-12 месяцев.
Портландцемент в сравнении с обычным цементом обладает более низкой стоимостью, а также выделяет меньше теплоты в процессе затвердения, что в свою очередь дает возможность использовать его в возведении массивных бетонных сооружений. Помимо прочности, материал обладает меньшей степенью объемной деформации, противостоит негативному влиянию сульфатных и пресных вод, жаростоек. Ему присуща меньшая, в сравнении с обычным цементом, морозостойкость. Данный показатель важен при эксплуатации в условиях колебания температур, которые провоцируют переменное замораживание и оттаивание.
Для цемента со шлаком характерно медленное нарастание прочности при начальных стадиях твердения. Для достижения необходимых показателей прочности обычному цементу необходимо 6-12 месяцев.
Замедление процессов схватывания и твердения провоцируется пониженными температурами. В случае с цементом со шлаком ускорение процесса достигается благодаря использованию клинкера с высоким содержанием силиката и алюмината, а также шлаков с высоким содержанием глинозема.
Выбор сырья и особенности хранения
Портландцемент на основе шлака следует на протяжении длительного времени выдерживать во влажной среде, поскольку преждевременное высыхание плохо влияет на его твердение. При достаточных показателях влажности и повышенных температурах ускоряется твердение, поэтому обработка портландцемент в автоклавах и камерах весьма эффективна.
Прочность строительного материала достигается выполнением мельчайшего помола. Благодаря таким действиям цемент быстрее твердеет и становится более прочным. Тонкость помола отвечает за такой показатель, как активность. С целью получения вяжущего высокого качества специалисты рекомендуют применять двухступенчатый или сепараторный помол.
В производстве шлакобетона может использоваться не любое сырье. Главным требованием в отношении шлака выступает отсутствие оксидов химических соединений, которые способны отрицательно влиять на характеристики получаемого строительного материала. С особым вниманием относятся и к чистоте шлака, он должен быть лишен глины, земли, золы и иного мусора. В производстве шлакобетона используют шлаки топливной и металлургической промышленности.
Прочность портландцемента достигается мельчайшим помолом (двухступенчатым или сепараторным).
Благодаря металлургическому шлаку получают максимально прочный бетон. Из всего разнообразия шлаков топливной промышленности наиболее подходящий класс – антрацитные породы. Непригодными для данных целей считаются продукты сгорания бурых углей, поскольку они содержат примеси, которые присоединены к шлаку на основе неустойчивых связей.
Не последние место в достижении чистоты, а как результат и прочности принадлежит правильному хранению, в процессе которого шлак перемещают не менее 3-х раз с места на место, тем самым позволяя избавиться от примесей извести и серы.
Шлаки пригодны для производства до тех пор, пока сохраняют кристаллическую структуру и не проявляют признаков распада, возникающих при переходе одних соединений в другие под действием влаги и газов, которые находятся в воздухе. Образующиеся соединения обладают большим объемом, поэтому переход сопровождается разрушением кусков шлака и растрескиванием.
Класс шлакобетона зависит от размеров зерен шлака, которые могут варьироваться в пределах 5-40 мм. Песок для получения смеси используют с размером гранул не более 5 мм. Благодаря наличию шлакового песка повышается ряд показателей бетона, среди которых плотность и прочность. Шлаковый щебень позволяет получить более легкий бетон, обладающий высокими теплоизоляционными свойствами, однако его прочностные характеристики будут иметь более низкий уровень.
Классификация портландцемента со шлаком
Портландцемент класс 300 по ГОСТ 10178-85
Характеристика | Показатель | |
1 | Вещественный состав цемента, %:- гранулированный доменный шлак- портландцементный клинкер- гипсовый камень | 50-6040-501,5-3,5 |
2 | Предел прочности (3 суток твердения)- при изгибе, МПа- при сжатии, МПа | 3,0-3,512,0-13,0 |
3 | Массовая доля:- свободного оксида кальция, %- оксид магния в клинкере, % | менее 0,5менее 1,6 |
4 | Активность при пропаривании- при изгибе, МПа- при сжатии, МПа | 3,8-4,222,0-23,5 |
5 | Предел прочности (28 суток твердения)- при изгибе, МПа- при сжатии, МПа | 5,2-5,533,5-34,0 |
6 | Начало схватывания не ранее, час/мин | 3-10 |
7 | Тонкость помола (через сито 008), % | 90,0 |
8 | Конец схватывания не ранее, час/мин | 4-40 |
http://youtu.be/NzxlwmWevlg
Портландцемент класс 400
Характеристика | Показатель | |
1 | Вещественный состав цемента, %:- гранулированный доменный шлак- портландцементный клинкер- гипсовый камень | 38-4058-621,5-3,5 |
2 | Предел прочности (3 суток твердения)- при изгибе, МПа- при сжатии, МПа | 3,0-3,512,0-13,0 |
3 | Массовая доля:- свободного оксида кальция, %- оксид магния в клинкере, % | менее 0,5менее 1,6 |
4 | Активность при пропаривании- при изгибе, МПа- при сжатии, МПа | 4,1-4,325,0-26,0 |
5 | Предел прочности (28 суток твердения)- при изгибе, МПа- при сжатии, МПа | 5,8-6,041,4-42,5 |
6 | Начало схватывания не ранее, час/мин | 3-00 |
7 | Тонкость помола (через сито 008), % | 90,0 |
8 | Конец схватывания не ранее, час/мин | 4-20 |
Портландцемент класс 500
Характеристика | Показатель | |
1 | Вещественный состав цемента, %:- гипсовый камень- портландцементный клинкер | 2,0-2,5100 |
2 | Предел прочности (3 суток твердения)- при изгибе, МПа- при сжатии, МПа | 4,5-4,825,0-27,0 |
3 | Массовая доля:- свободного оксида кальция, %- оксид магния в клинкере, % | менее 0,5менее 1,5 |
4 | Активность при пропаривании- при изгибе, МПа- при сжатии, МПа | 4,3-4,631,0-34,0 |
5 | Предел прочности (28 суток твердения)- при изгибе, МПа- при сжатии, МПа | 6,3-6,550,5-52,0 |
6 | Начало схватывания не ранее, час/мин | 2-32 |
7 | Тонкость помола (через сито 008), % | 90,0 |
8 | Конец схватывания не ранее, час/мин | 3-43 |
Сферы применения
Портландцемент отличается высокой прочностью, поэтому его используют в приготовлении бетонных смесей и строительных растворов.
Шлаковый портландцемент нашел свое активное применение при строительстве бетонных и железобетонных подводных, наземных и подземных сооружений, подверженных воздействию минерализованных и пресных вод. Благодаря высоким показателям прочности он используется при производстве бетонных смесей, стеновых блоков, сухих смесей и строительных растворов. Такой цемент не менее популярен, нежели классический цемент марки М500.
Строительный материал на данном этапе развития строительной промышленности является одни из наиболее доступных и экономически привлекательных. На его основе изготавливаются как стены, так и армированные плиты перекрытия. В большинстве случаев при сооружении зданий из облегченных материалов для фундамента отдают предпочтение шлакобетону.
При возведении стен используется как монолитная технология с переставной опалубкой, так и готовые фундаментные и стеновые блоки из шлакобетона.
Шлаковый портландцемент распределяют по классам, каждый из которых является наиболее подходящим для выполнения тех или иных задач. Класс 10 получил свое применение при теплоизоляции. Классы 25 и 35 используют при возведении ненесущих конструкций, класс 50 применяется при изготовлении армированных перемычек, наружных и внутренних несущих стен.
Масштабное применение шлакобетона определяется рядом преимуществ, среди которых малый удельный вес в сравнении с силикатным и керамическим кирпичом. Благодаря этому свойству снижаются нагрузки на фундамент и несущие конструкции строения.
Возможность создания блоков больших параметров способствует материальных и временных затрат в процессе укладки. Кроме того, такие блоки максимально удобны при транспортировке.
Особенности шлакощелочного бетона
Шлакощелочной портландцемент получают благодаря использованию щелочных металлов. Высоких показателей прочности удалось достичь добавлением различных щелочей: соды, стекла и ряда других.
Шлакощелочной портландцемент нашел свое применение при производстве железобетонных элементов с высоким показателем устойчивости к химически агрессивным веществам. Класс таких бетонов является незаменимым при строительстве массивных конструкций. Это связано с тем, что при производстве крупных бетонных элементов, в основе которых лежит портландцемент, происходит выделение большого количества тепла, и температура конструкции может достигать отметки в 80°С. При слишком быстром охлаждении объекта могут образовываться деформационные трещины. Использование шлакощелочного бетона позволяет избежать возникновения данной проблемы.
http://youtu.be/4Z7cFsEyPvc
Наиболее популярным является класс шлакощелочного цемента на основе соединений щелочных металлов с преобладанием гидросиликатов кальция и гидроалюмосиликатов и молотого металлургического шлака.
Шлакощелочной цемент позволяет производить конструкции с меньшим количеством капиллярных пор. Данное свойство способно снизить водопоглощение и повысить морозоустойчивость бетона, способствуя росту эксплуатационных качеств строительной конструкции. За первые сутки материал набирает 30% прочности, которая в дальнейшем способна достичь отметки в МПа.
Данный класс бетона устойчив к воздействию агрессивных сред: сульфатов, кислот, хлоридов и морской воды. Возможность управлять свойствами цемента на различных стадиях структурообразования позволила получать вяжущие со специальными свойствами: морозо- и жаростойкие, безусадочные, с повышенной коррозионной устойчивостью, с высокой скоростью твердения, тампонажные.
Page 2
- Армирование
- Виды
- Изготовление
- Инструменты
- Монтаж
- Расчёт
- Ремонт
1pobetonu.ru
Цемент со шлаком: применение смеси
Портландцемент представляет собой вяжущее гидравлическое вещество, получаемое методом измельчения цементного клинкера, гипса и гранулированного шлака.
Цемент со шлаком применяют с 1824 года. Это соединение справедливо может быть названо наиболее популярным видом цемента, нашедшим свое применение во всех сферах строительства.
Смесь цемента со шлаком используют уже почти 2 столетия, за это время данный материал нашел применение во всех сферах строительства.
Технология производства
Такой материал производят с использованием доменного шлака, который представляет собой вторичный продукт металлургического производства. Класс данного материала определяется качеством исходных материалов клинкера и доменных шлаков. Клинкер исполняет роль активизатора шлаков в составе шлакоцемента.
В основе технологии производства лежит принцип высушивания шлака в сушилках до получения показателей влажности не более 1%. Затем клинкер, шлак и гипс загружается в бункер цементной мельницы, и измельчается до гомогенного тонкодисперсного порошка.
Класс шлакоцемента зависит и от используемого вида шлака: это могут быть основные, кислые, гранулированные и негранулированные шлаки. Особое значение в определении прочности имеет не физическая структура, а химический состав. На данной закономерности основывается правило выбора сырья. С экономической стороны предпочтение стоит отдать гранулированным видам, в связи с тем, что использование негранулированных масс усложняет производственный процесс. Цемент со шлаком, который получается в результате, затвердевает медленнее обычного, потому что содержание шлака в нем варьируется в пределах 20-80% общей массы.
При изготовлении портландцемента используют сито с крупными (40х40 мм) и мелкими (5х5 мм) ячейками.
Шлаковый портландцемент изготавливают, используя два вида сит: с мелкими (5х5 мм) и крупными (40х40 мм) ячейками.
- При использовании материала для наружных стен соединяют крупный и мелкий шлак в соотношении 7:3.
- Для внутренних стен в пропорции 4 части мелких зерен и 6 частей крупных.
- Для увеличения прочности материала заменяют пятую части самой мелкой фракции обычным песком и исключают из состава наиболее крупные зерна шлака.
- Благодаря использованию сочетаний 2-х вяжущих компонентов (цемента и извести, цемента и глины) удается существенно снизить стоимость материала. Наиболее оптимальной являются пропорция: известь – не более 1/3 и цемент – не менее 2/3 общего объема.
Глина и известь способны не только снизить стоимость, но и делают стены более теплыми и сухими. Известковый портландцемент на основе шлака, в состав вяжущего которого входит 2/3 глины и 1/3 извести, твердеет дольше цементного, однако в дальнейшем показывает более высокие показатели прочности.
Состав возможных смесей шлакобетона
Класс шлакобетона | Объемный состав (в частях) | Объемный вес | ||||
Цемент 400 | Песок | Известь или глина | Крупный шлак | Мелкий шлак | ||
50 | 1 | 3 | 0,6 | 5 | 6 | 1300 |
35 | 0,9 | 2 | 0,3 | 3 | 3 | 1500 |
35 | 1 | 3 | 0,8 | 8 | 6 | 1100 |
25 | 0,9 | 2 | 0,5 | 5 | 3 | 1300 |
25 | 1 | 2 | 1 | 12 | 6 | 900 |
10 | 0,9 | 1 | 0,7 | 8 | 3 | 1100 |
10 | 0,9 | 1 | 2 | 12 | 5 | 700 |
Технические характеристики
Портландцемент характеризуется медленным твердением, а достаточная прочность достигается за 6-12 месяцев.
Портландцемент в сравнении с обычным цементом обладает более низкой стоимостью, а также выделяет меньше теплоты в процессе затвердения, что в свою очередь дает возможность использовать его в возведении массивных бетонных сооружений. Помимо прочности, материал обладает меньшей степенью объемной деформации, противостоит негативному влиянию сульфатных и пресных вод, жаростоек. Ему присуща меньшая, в сравнении с обычным цементом, морозостойкость. Данный показатель важен при эксплуатации в условиях колебания температур, которые провоцируют переменное замораживание и оттаивание.
Для цемента со шлаком характерно медленное нарастание прочности при начальных стадиях твердения. Для достижения необходимых показателей прочности обычному цементу необходимо 6-12 месяцев.
Замедление процессов схватывания и твердения провоцируется пониженными температурами. В случае с цементом со шлаком ускорение процесса достигается благодаря использованию клинкера с высоким содержанием силиката и алюмината, а также шлаков с высоким содержанием глинозема.
Выбор сырья и особенности хранения
Портландцемент на основе шлака следует на протяжении длительного времени выдерживать во влажной среде, поскольку преждевременное высыхание плохо влияет на его твердение. При достаточных показателях влажности и повышенных температурах ускоряется твердение, поэтому обработка портландцемент в автоклавах и камерах весьма эффективна.
Прочность строительного материала достигается выполнением мельчайшего помола. Благодаря таким действиям цемент быстрее твердеет и становится более прочным. Тонкость помола отвечает за такой показатель, как активность. С целью получения вяжущего высокого качества специалисты рекомендуют применять двухступенчатый или сепараторный помол.
В производстве шлакобетона может использоваться не любое сырье. Главным требованием в отношении шлака выступает отсутствие оксидов химических соединений, которые способны отрицательно влиять на характеристики получаемого строительного материала. С особым вниманием относятся и к чистоте шлака, он должен быть лишен глины, земли, золы и иного мусора. В производстве шлакобетона используют шлаки топливной и металлургической промышленности.
Прочность портландцемента достигается мельчайшим помолом (двухступенчатым или сепараторным).
Благодаря металлургическому шлаку получают максимально прочный бетон. Из всего разнообразия шлаков топливной промышленности наиболее подходящий класс – антрацитные породы. Непригодными для данных целей считаются продукты сгорания бурых углей, поскольку они содержат примеси, которые присоединены к шлаку на основе неустойчивых связей.
Не последние место в достижении чистоты, а как результат и прочности принадлежит правильному хранению, в процессе которого шлак перемещают не менее 3-х раз с места на место, тем самым позволяя избавиться от примесей извести и серы.
Шлаки пригодны для производства до тех пор, пока сохраняют кристаллическую структуру и не проявляют признаков распада, возникающих при переходе одних соединений в другие под действием влаги и газов, которые находятся в воздухе. Образующиеся соединения обладают большим объемом, поэтому переход сопровождается разрушением кусков шлака и растрескиванием.
Класс шлакобетона зависит от размеров зерен шлака, которые могут варьироваться в пределах 5-40 мм. Песок для получения смеси используют с размером гранул не более 5 мм. Благодаря наличию шлакового песка повышается ряд показателей бетона, среди которых плотность и прочность. Шлаковый щебень позволяет получить более легкий бетон, обладающий высокими теплоизоляционными свойствами, однако его прочностные характеристики будут иметь более низкий уровень.
Классификация портландцемента со шлаком
Портландцемент класс 300 по ГОСТ 10178-85
Характеристика | Показатель | |
1 | Вещественный состав цемента, %:- гранулированный доменный шлак- портландцементный клинкер- гипсовый камень | 50-6040-501,5-3,5 |
2 | Предел прочности (3 суток твердения)- при изгибе, МПа- при сжатии, МПа | 3,0-3,512,0-13,0 |
3 | Массовая доля:- свободного оксида кальция, %- оксид магния в клинкере, % | менее 0,5менее 1,6 |
4 | Активность при пропаривании- при изгибе, МПа- при сжатии, МПа | 3,8-4,222,0-23,5 |
5 | Предел прочности (28 суток твердения)- при изгибе, МПа- при сжатии, МПа | 5,2-5,533,5-34,0 |
6 | Начало схватывания не ранее, час/мин | 3-10 |
7 | Тонкость помола (через сито 008), % | 90,0 |
8 | Конец схватывания не ранее, час/мин | 4-40 |
Портландцемент класс 400
Характеристика | Показатель | |
1 | Вещественный состав цемента, %:- гранулированный доменный шлак- портландцементный клинкер- гипсовый камень | 38-4058-621,5-3,5 |
2 | Предел прочности (3 суток твердения)- при изгибе, МПа- при сжатии, МПа | 3,0-3,512,0-13,0 |
3 | Массовая доля:- свободного оксида кальция, %- оксид магния в клинкере, % | менее 0,5менее 1,6 |
4 | Активность при пропаривании- при изгибе, МПа- при сжатии, МПа | 4,1-4,325,0-26,0 |
5 | Предел прочности (28 суток твердения)- при изгибе, МПа- при сжатии, МПа | 5,8-6,041,4-42,5 |
6 | Начало схватывания не ранее, час/мин | 3-00 |
7 | Тонкость помола (через сито 008), % | 90,0 |
8 | Конец схватывания не ранее, час/мин | 4-20 |
Портландцемент класс 500
Характеристика | Показатель | |
1 | Вещественный состав цемента, %:- гипсовый камень- портландцементный клинкер | 2,0-2,5100 |
2 | Предел прочности (3 суток твердения)- при изгибе, МПа- при сжатии, МПа | 4,5-4,825,0-27,0 |
3 | Массовая доля:- свободного оксида кальция, %- оксид магния в клинкере, % | менее 0,5менее 1,5 |
4 | Активность при пропаривании- при изгибе, МПа- при сжатии, МПа | 4,3-4,631,0-34,0 |
5 | Предел прочности (28 суток твердения)- при изгибе, МПа- при сжатии, МПа | 6,3-6,550,5-52,0 |
6 | Начало схватывания не ранее, час/мин | 2-32 |
7 | Тонкость помола (через сито 008), % | 90,0 |
8 | Конец схватывания не ранее, час/мин | 3-43 |
Сферы применения
Портландцемент отличается высокой прочностью, поэтому его используют в приготовлении бетонных смесей и строительных растворов.
Шлаковый портландцемент нашел свое активное применение при строительстве бетонных и железобетонных подводных, наземных и подземных сооружений, подверженных воздействию минерализованных и пресных вод. Благодаря высоким показателям прочности он используется при производстве бетонных смесей, стеновых блоков, сухих смесей и строительных растворов. Такой цемент не менее популярен, нежели классический цемент марки М500.
Строительный материал на данном этапе развития строительной промышленности является одни из наиболее доступных и экономически привлекательных. На его основе изготавливаются как стены, так и армированные плиты перекрытия. В большинстве случаев при сооружении зданий из облегченных материалов для фундамента отдают предпочтение шлакобетону.
При возведении стен используется как монолитная технология с переставной опалубкой, так и готовые фундаментные и стеновые блоки из шлакобетона.
Шлаковый портландцемент распределяют по классам, каждый из которых является наиболее подходящим для выполнения тех или иных задач. Класс 10 получил свое применение при теплоизоляции. Классы 25 и 35 используют при возведении ненесущих конструкций, класс 50 применяется при изготовлении армированных перемычек, наружных и внутренних несущих стен.
Масштабное применение шлакобетона определяется рядом преимуществ, среди которых малый удельный вес в сравнении с силикатным и керамическим кирпичом. Благодаря этому свойству снижаются нагрузки на фундамент и несущие конструкции строения.
Возможность создания блоков больших параметров способствует материальных и временных затрат в процессе укладки. Кроме того, такие блоки максимально удобны при транспортировке.
Особенности шлакощелочного бетона
Шлакощелочной портландцемент получают благодаря использованию щелочных металлов. Высоких показателей прочности удалось достичь добавлением различных щелочей: соды, стекла и ряда других.
Шлакощелочной портландцемент нашел свое применение при производстве железобетонных элементов с высоким показателем устойчивости к химически агрессивным веществам. Класс таких бетонов является незаменимым при строительстве массивных конструкций. Это связано с тем, что при производстве крупных бетонных элементов, в основе которых лежит портландцемент, происходит выделение большого количества тепла, и температура конструкции может достигать отметки в 80°С. При слишком быстром охлаждении объекта могут образовываться деформационные трещины. Использование шлакощелочного бетона позволяет избежать возникновения данной проблемы.
Наиболее популярным является класс шлакощелочного цемента на основе соединений щелочных металлов с преобладанием гидросиликатов кальция и гидроалюмосиликатов и молотого металлургического шлака.
Шлакощелочной цемент позволяет производить конструкции с меньшим количеством капиллярных пор. Данное свойство способно снизить водопоглощение и повысить морозоустойчивость бетона, способствуя росту эксплуатационных качеств строительной конструкции. За первые сутки материал набирает 30% прочности, которая в дальнейшем способна достичь отметки в МПа.
Данный класс бетона устойчив к воздействию агрессивных сред: сульфатов, кислот, хлоридов и морской воды. Возможность управлять свойствами цемента на различных стадиях структурообразования позволила получать вяжущие со специальными свойствами: морозо- и жаростойкие, безусадочные, с повышенной коррозионной устойчивостью, с высокой скоростью твердения, тампонажные.
o-cemente.info
Шлакоцемент: определение понятия, главные особенности, правильные пропорции
Очень часто в строительстве используется цемент со шлаком, что это за материал, не нужно объяснять опытным мастерам. А вот новичкам в строительном деле будет полезно узнать, что шлакоцемент — это гидравлическая вяжущая субстанция, образованная посредством измельчения клинкера, гипса, а также доменного шлака — вторичного металлургического продукта. Химический состав шлаков играет важнейшую роль в определении класса прочности шлакоцемента. В цемент могут идти гранулированные и негранулированные, кислые, основные шлаки.
Особенности стройматериала
- Наиболее выгодным с экономической точки зрения считается гранулированный шлакоцемент, также уменьшить расходы поможет добавление извести и глины в цементную смесь. Эти вяжущие элементы дают отличный результат: теплые и сухие стены по низкой цене. Известь не должна превышать одну треть всей смеси, количество цемента — не меньше 2/3 общего объема.
- Мелкий и крупный шлак сортируется путем просеивания через сито с маленькими ячейками (5х5мм) и большими (40х40мм). Крупный и мелкий шлак для работы с наружными стенами соотносится как 7:3. Для внутренних стен пропорция крупных и мелких шлаков — 6 к 4.
- Чтобы стройматериал был прочнее, следует заменить 1⁄5 часть наиболее мелкой фракции песком, а также убрать самые крупные частицы шлака.
- Негранулированный шлак используется для высококачественной заливки в том случае, если есть возможность дождаться длительного застывания смеси. Зато заливка будет надежной, на ней гарантированно не появятся трещины.
- Практика показала, что цемент со шлаком — это один из самых надежных, долговечных и прочных материалов, в связи с чем он получил широкое распространение в сфере многоэтажного строительства. Фундаменты, плиты перекрытия, армированные пояса, подводные и околоводные инженерные сооружения, теплоизоляция помещений — со шлакоцементом можно добиться качественного выполнения любых строительных целей.
Подытожим вышесказанное. Цемент со шлаком — что это?
Это экономически оправданный, высокоэффективный по прочности состав, который нашел самое широкое распространение в строительстве. В зависимости от ваших потребностей вы можете изменять пропорции материалов в цементной смеси для достижения наилучших результатов.
zfundament.ru
vest-beton.ru
Шлак как заполнитель бетона - Справочник химика 21
При получении щебня дроблением неизбежен выход фракции менее 5 мм, которая как щебень некондиционна, но отвечает по крупности пескам (5,0-0,14 мм). В частности, при дроблении доменных шлаков образуется до 15-20% песка с насыпной плотностью 1320-1370 кг/м . Он полностью используется при изготовлении рядового бетона, гипсобетона, железобетонных труб, гипсо-шлаковых перегородок. Песок иэ сталеплавильных шлаков применяется как наполнитель асфальтобетона. В качестве мелкого заполнителя бетона утилизируется фракция 5-0 мм отвальных шлаков медной и никелевой плавок и т.д. [c.169] Утилизация шлаков в качестве крупного и мелкого заполнителей бетона также хорошо известна. [c.184]Гуревич Б.И. Гранулированный шлак медно-никелевого производства как заполнитель бетона. В сб. Химия и технология вяжущих веществ, изд. Наука , Л., 1968. [c.98]
Таким образом, коррозия арматуры в бетоне за счет серы возможна в том случае, если происходит растворение и гидролиз сульфида кальция, содержащегося в цементе или заполнителе. Очевидно, что при измельчении шлака Сульфиды переходят в раствор. В более крупных кусках шлака-заполнителя значительная часть [c.64]
Шлак как заполнитель бетона [c.591]
Из смеси цемента, воды и заполнителей (песок, гравий, щебень, шлак) после их затвердевания получают искусственный камень — бетон. Смесь этих материалов до затвердевания называется бетонной смесью. При затвердевании цементное тесто связывает зерна заполнителей. Затвердевание происходит даже в воде. Бетон со стальной арматурой (внутренним каркасом) называется железобетоном. Бетон и железобетоны в больших количествах идут на сооружение гидроэлектростанций, дорог, несущих конструкций зданий. [c.221]
Из смеси цемента, воды и заполнителей (песок, гравий, щебень, шлак) после ее затвердевания получают искусственный камень — бетон. Смесь этих материалов до затвердевания называется бетонной смесью. При затвердевании цементное тесто связывает зерна заполнителей. Затвердевание происходит даже в воде. Бетон со стальной арматурой (внутренним каркасом) назьшается железобетоном. [c.271]
Шлак — расплав (после затвердевания — стекловидная масса) в металлургических, плавильных процессах, покрывающий поверхность жидкого металла, состоит из всплывших продуктов пустой породы с флюсами. Ш. предохраняет металл от вредного воздействия газовой среды печи, удаляет примеси. Ш. применяется для изготовления стройматериалов (кирпич, черепица), как удобрение. См. Томасшлак. Шлакобетон — разновидность легкого бетона, где заполнителем служат шлаки. Шлам — продукт, содержащий обычно благородные металлы, отделяющиеся в виде осадка при электролизе меди, цинка и других металлов. [c.155]
Щебень иэ доменных и сталеплавильных шлаков является эффективным крупным заполнителем для бетонов, так как их механическая прочность на 70-80% выше чем естественных, достигая 50-100 МПа. Кроме того, более интенсивное взаимодействие на границе шлакового щебня с цементными фазами снижает расход вяжущего на 10% по сравнению с использованием природного, например гранитного, щебня. [c.184]
Для легких бетонов ЗШС (с малым содержанием шлака) применяется в качестве мелкого заполнителя и обеспечивает одновременно снижение плотности бетона и расхода цемента в тех же пределах, что и сухие золы. Для производства шлакоблоков она употребляется, как правило, без дополнительного введения обычных заполнителей. [c.198]
Горелая порода используется при засыпке междуэтажных перекрытий вместо обычного котельного шлака, как заполнитель в легких бетонах, для производства минеральной ваты (фракция 20—80 мм), в штукатурных растворах (после размола с известью) и для производства шлакоблоков. [c.180]
Мелким заполнителем или песком в технологии бетона называют материалы с размером зерен до 5 мм. Используются как естественные кварцевые, полевошпатные и другие пески, так и искусственные, полученные дроблением горных пород или из шлаков. [c.246]
В последнее время используется также керамзит, представляющий собой продукт обжига некоторых глин, легко вспучивающихся под действием высокой температуры (порядка 1000° С) и образующих по остывании пористые прочные гранулы. Керамзит в виде кусков большого размера используется также как крупный наполнитель бетона. Размер зерен крупного заполнителя от 5 до 150 мм. В качестве крупного наполнителя используются горные породы — гранит, кварцит и т. д., а также искусственные материалы — битый кирпич, крупные куски шлака и др. Для изготовления легких бетонов берут пористые разновидности наполнителей, для тяжелых — наполнитель с большим удельным весом, без пор. [c.246]
Наиболее распространенный материал для кладки нагревательных печей — шамотный кирпич. Под печей выкладывают из магнезитового или талькового кирпича, как наиболее устойчивого против воздействия окалины и шлаков. Имеется положительный опыт работы методических печей, в которых под выложен из бетонных блоков с форстеритовым заполнителем. [c.112]
Хранение сыпучих материалов. Песок, гравий, щебень, шлаки, красную глину хранят на открытых складах штабелями или в закромах. Диатомитовую крошку, андезитовый и диабазовый порошки хранят в закромах в закрытых складах. Мертели, огнеупорные порошки, огнеупорные заполнители для жаростойких бетонов хранят в бункерах (силосах), в закромах, в закрытых складах или под навесом раздельно в условиях, не допускающих их перемешивания между собой, загрязнения посторонними примесями и увлажнения осадками. Цемент и негашеная известь (кипелка) хранятся в силосах или в закрытых складах с плотным деревянным полом. При хранении негашеной извести необходимо особенно тщательно предохранять ее от попадания влаги. [c.306]
Бетоны (предварительно не просушенные) на легких заполнителях (пемзе) или топливных шлаках [c.269]
Проведенными лабораторными исследованиями показана целесообразность переработки полученных из расплавов шлаков на легкие пористые заполнители бетона типа азерит и активную минеральную добавку в высокомарочные цементы. Азерит как искусственный заполнитель выделяется из других заполнителей благодаря технологии его производства и товарным свойствам. Значительная заслуга в разработке, получении и развитии технологии получения азерита — эффективного по рыночным оценкам [c.172]
Таким образом, в результате изучения возможностей комплексного использования сырья с учетом экологической безопасности технологий установлено, что топочно-барботажный агрегат (ТБА) выгодно отличается от других и позволяет решить задачу по созданию технологии получения расплавов на основе углеотходов и использования шлаков при производстве литого щебня, шлаковой пемзы, легких пористых заполнителей бетонов типа азерит , минеральной ваты и другой товарной продукции. Сплавы метгишов в зависимости от концентрации в них цветных металлов могут быть реализованы для переработки заводом черной или цветной металлургии. [c.174]
Хорошо освоено производство силикатного бетона на основе ваграночного шлака. В частности, на Дзержинском заводе бесцементных дорожных плит (Нижегородская обл.) в качестве вяжущего использовали известково-шлаковую смесь, которую готовили совместным помолом ваграночного шлака, гашеной извести и кварцевого песка. В качестве активирующей добавки вводили гипсовый камень или гипс. Как заполнитель бетона применяли речной песок с модулем крупности [c.182]
ЗАПОЛНИТЕЛИ ПОРИСТЫЕ - природные или искусственные минеральные сыпучие материалы, применяемые для получения легких бетонов, железобетона и строительных растворов с пониженной объемной массой. К природным 3. п. относятся пемзы, туфы, черепашники, вулканические шлаки и зола. К искусственным относятся отходы промышленности (шлаки), керамзит, шлаковая пемза, гранулированный шлак и др. [c.99]
Аглопорит — пористый материал, получаемый агломерацией топливных шлаков, золы, глинистых пород. Он состоит в основном из стекловидной фазы, содержащей вкрапления кристаллов кварца, полевых шпатов, магнетита, фаялита, муллита, анортита. Используют как заполнитель легких бетонов и теплоизоляционную засыпку. [c.224]
Пластобетон представляет собой безцемептиый бетон и изготовляется на основе одного органического вяжущего (связующего). В качестве заполнителя применяется песок, щебень, шлак, керамзит и другие материалы. [c.355]
Щебень — распространенный строительный материал. Он широко испольэуется в качестве крупного заполнителя при производстве бетонов, применяется для устройства оснований и подстилающих слоев автомобильных и железных дорог. В настоящее время для его получения в равной мере привлекают каменные материалы естественного и искусственного происхождения. Добьиу первых ведуг в специальных карьерах, в качестве вторых используют ряд промышленных отходов. Среди них основное место занимают различные виды шлаков крупно-тоннажных металлургических производств. Шлаковый щебень по своим свойствам (прочность, устойчивость, морозостойкость) соответствует производимому из горных пород и заменяет его с эквивалентом, равным единице. Допустимые размеры его фракций варьируют от 5-10 до 70-120 мм. [c.165]
При получении бетона и изделий из него металлургические шлаки утилизируют в качестве основного компонента бесцементных вяжущих, а также как крупный и мелкий заполнители. [c.182]
Жаростойкие и огнеупорные бетоны (ГОСТ 19038—73 и ГОСТ 20910—75) изготовляют на высокоглиноземистом, глиноземистом и периклазовом цементах, портландцементе с тонкомолотыми добавками, жидком стекле и фосфатных связках. В качестве мелкого и крупного заполнителей применяют дробленые и рассеянные огнеупорные материалы, доменный шлак, бой обыкновенного глиняного кирпича, диабаз, базальт, андезит и другие местные материалы. Зерновой состав мелкого (песок с крупностью зерен до 5 мм) и крупного (щебень с крупностью зерен 5—40 мм) заполнителей должен соответствовать табл. 52. [c.71]
ЩЁБЕНЬ — минеральный строительный материал в виде угловатых зереи неправильной формы, получаемый дроблением и рассевом исходного продукта. Природный Щ.— рыхлые или слабо сцементированные остроугольные остатки выветривания горных пород. Исходным продуктом для получения Щ. служат естественный камень из различных горных пород, гравий п валуны, доменные литые и отвальные, сталеплавильные, ферросплавные и др. шлаки, специально поризуемые горные породы и др. Щ. используют в качестве заполнителя для бетона монолитных железобетонных и бето1П1ЫХ конструкций и изделий, материала [c.754]
При использовании доменных щлаков для литья брусчатки или в качестве заполнителя для бетона важно, чтобы шлаковый материал был абсолютно стабилен. Особенно нежелательно использовать для этого шлаки,, со- [c.927]
chem21.info
Цемент со шлаком: применение смеси
Портландцемент представляет собой вяжущее гидравлическое вещество, получаемое методом измельчения цементного клинкера, гипса и гранулированного шлака.
Цемент со шлаком применяют с 1824 года. Это соединение справедливо может быть названо наиболее популярным видом цемента, нашедшим свое применение во всех сферах строительства.
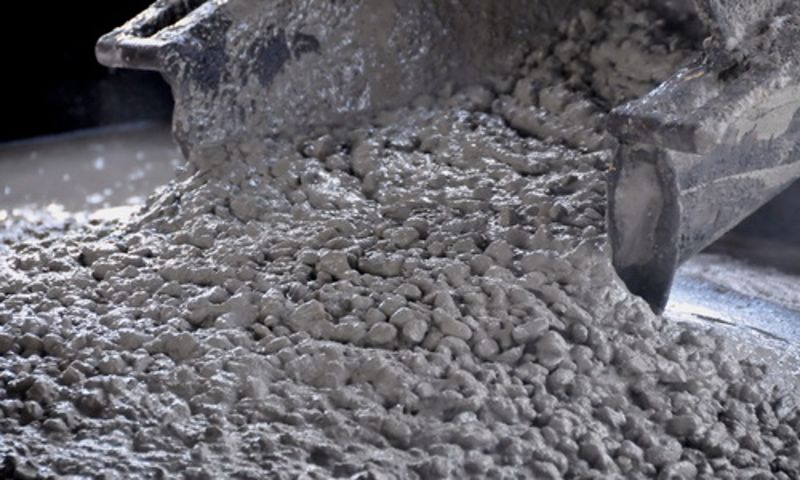
Смесь цемента со шлаком используют уже почти 2 столетия, за это время данный материал нашел применение во всех сферах строительства.
Технология производства
Такой материал производят с использованием доменного шлака, который представляет собой вторичный продукт металлургического производства. Класс данного материала определяется качеством исходных материалов клинкера и доменных шлаков. Клинкер исполняет роль активизатора шлаков в составе шлакоцемента.
В основе технологии производства лежит принцип высушивания шлака в сушилках до получения показателей влажности не более 1%. Затем клинкер, шлак и гипс загружается в бункер цементной мельницы, и измельчается до гомогенного тонкодисперсного порошка.
Класс шлакоцемента зависит и от используемого вида шлака: это могут быть основные, кислые, гранулированные и негранулированные шлаки. Особое значение в определении прочности имеет не физическая структура, а химический состав. На данной закономерности основывается правило выбора сырья. С экономической стороны предпочтение стоит отдать гранулированным видам, в связи с тем, что использование негранулированных масс усложняет производственный процесс. Цемент со шлаком, который получается в результате, затвердевает медленнее обычного, потому что содержание шлака в нем варьируется в пределах 20-80% общей массы.

При изготовлении портландцемента используют сито с крупными (40х40 мм) и мелкими (5х5 мм) ячейками.
Шлаковый портландцемент изготавливают, используя два вида сит: с мелкими (5х5 мм) и крупными (40х40 мм) ячейками.
- При использовании материала для наружных стен соединяют крупный и мелкий шлак в соотношении 7:3.
- Для внутренних стен в пропорции 4 части мелких зерен и 6 частей крупных.
- Для увеличения прочности материала заменяют пятую части самой мелкой фракции обычным песком и исключают из состава наиболее крупные зерна шлака.
- Благодаря использованию сочетаний 2-х вяжущих компонентов (цемента и извести, цемента и глины) удается существенно снизить стоимость материала. Наиболее оптимальной являются пропорция: известь – не более 1/3 и цемент – не менее 2/3 общего объема.
Глина и известь способны не только снизить стоимость, но и делают стены более теплыми и сухими. Известковый портландцемент на основе шлака, в состав вяжущего которого входит 2/3 глины и 1/3 извести, твердеет дольше цементного, однако в дальнейшем показывает более высокие показатели прочности.
Состав возможных смесей шлакобетона
Класс шлакобетона | Объемный состав (в частях) | Объемный вес | ||||
Цемент 400 | Песок | Известь или глина | Крупный шлак | Мелкий шлак | ||
50 | 1 | 3 | 0,6 | 5 | 6 | 1300 |
35 | 0,9 | 2 | 0,3 | 3 | 3 | 1500 |
35 | 1 | 3 | 0,8 | 8 | 6 | 1100 |
25 | 0,9 | 2 | 0,5 | 5 | 3 | 1300 |
25 | 1 | 2 | 1 | 12 | 6 | 900 |
10 | 0,9 | 1 | 0,7 | 8 | 3 | 1100 |
10 | 0,9 | 1 | 2 | 12 | 5 | 700 |
Технические характеристики

Портландцемент характеризуется медленным твердением, а достаточная прочность достигается за 6-12 месяцев.
Портландцемент в сравнении с обычным цементом обладает более низкой стоимостью, а также выделяет меньше теплоты в процессе затвердения, что в свою очередь дает возможность использовать его в возведении массивных бетонных сооружений. Помимо прочности, материал обладает меньшей степенью объемной деформации, противостоит негативному влиянию сульфатных и пресных вод, жаростоек. Ему присуща меньшая, в сравнении с обычным цементом, морозостойкость. Данный показатель важен при эксплуатации в условиях колебания температур, которые провоцируют переменное замораживание и оттаивание.
Для цемента со шлаком характерно медленное нарастание прочности при начальных стадиях твердения. Для достижения необходимых показателей прочности обычному цементу необходимо 6-12 месяцев.
Замедление процессов схватывания и твердения провоцируется пониженными температурами. В случае с цементом со шлаком ускорение процесса достигается благодаря использованию клинкера с высоким содержанием силиката и алюмината, а также шлаков с высоким содержанием глинозема.
Выбор сырья и особенности хранения
Портландцемент на основе шлака следует на протяжении длительного времени выдерживать во влажной среде, поскольку преждевременное высыхание плохо влияет на его твердение. При достаточных показателях влажности и повышенных температурах ускоряется твердение, поэтому обработка портландцемент в автоклавах и камерах весьма эффективна.
Прочность строительного материала достигается выполнением мельчайшего помола. Благодаря таким действиям цемент быстрее твердеет и становится более прочным. Тонкость помола отвечает за такой показатель, как активность. С целью получения вяжущего высокого качества специалисты рекомендуют применять двухступенчатый или сепараторный помол.
В производстве шлакобетона может использоваться не любое сырье. Главным требованием в отношении шлака выступает отсутствие оксидов химических соединений, которые способны отрицательно влиять на характеристики получаемого строительного материала. С особым вниманием относятся и к чистоте шлака, он должен быть лишен глины, земли, золы и иного мусора. В производстве шлакобетона используют шлаки топливной и металлургической промышленности.

Прочность портландцемента достигается мельчайшим помолом (двухступенчатым или сепараторным).
Благодаря металлургическому шлаку получают максимально прочный бетон. Из всего разнообразия шлаков топливной промышленности наиболее подходящий класс – антрацитные породы. Непригодными для данных целей считаются продукты сгорания бурых углей, поскольку они содержат примеси, которые присоединены к шлаку на основе неустойчивых связей.
Не последние место в достижении чистоты, а как результат и прочности принадлежит правильному хранению, в процессе которого шлак перемещают не менее 3-х раз с места на место, тем самым позволяя избавиться от примесей извести и серы.
Шлаки пригодны для производства до тех пор, пока сохраняют кристаллическую структуру и не проявляют признаков распада, возникающих при переходе одних соединений в другие под действием влаги и газов, которые находятся в воздухе. Образующиеся соединения обладают большим объемом, поэтому переход сопровождается разрушением кусков шлака и растрескиванием.
Класс шлакобетона зависит от размеров зерен шлака, которые могут варьироваться в пределах 5-40 мм. Песок для получения смеси используют с размером гранул не более 5 мм. Благодаря наличию шлакового песка повышается ряд показателей бетона, среди которых плотность и прочность. Шлаковый щебень позволяет получить более легкий бетон, обладающий высокими теплоизоляционными свойствами, однако его прочностные характеристики будут иметь более низкий уровень.
Классификация портландцемента со шлаком
Портландцемент класс 300 по ГОСТ 10178-85
Характеристика | Показатель | |
1 | Вещественный состав цемента, %:- гранулированный доменный шлак- портландцементный клинкер- гипсовый камень | 50-6040-501,5-3,5 |
2 | Предел прочности (3 суток твердения)- при изгибе, МПа- при сжатии, МПа | 3,0-3,512,0-13,0 |
3 | Массовая доля:- свободного оксида кальция, %- оксид магния в клинкере, % | менее 0,5менее 1,6 |
4 | Активность при пропаривании- при изгибе, МПа- при сжатии, МПа | 3,8-4,222,0-23,5 |
5 | Предел прочности (28 суток твердения)- при изгибе, МПа- при сжатии, МПа | 5,2-5,533,5-34,0 |
6 | Начало схватывания не ранее, час/мин | 3-10 |
7 | Тонкость помола (через сито 008), % | 90,0 |
8 | Конец схватывания не ранее, час/мин | 4-40 |
Портландцемент класс 400
Характеристика | Показатель | |
1 | Вещественный состав цемента, %:- гранулированный доменный шлак- портландцементный клинкер- гипсовый камень | 38-4058-621,5-3,5 |
2 | Предел прочности (3 суток твердения)- при изгибе, МПа- при сжатии, МПа | 3,0-3,512,0-13,0 |
3 | Массовая доля:- свободного оксида кальция, %- оксид магния в клинкере, % | менее 0,5менее 1,6 |
4 | Активность при пропаривании- при изгибе, МПа- при сжатии, МПа | 4,1-4,325,0-26,0 |
5 | Предел прочности (28 суток твердения)- при изгибе, МПа- при сжатии, МПа | 5,8-6,041,4-42,5 |
6 | Начало схватывания не ранее, час/мин | 3-00 |
7 | Тонкость помола (через сито 008), % | 90,0 |
8 | Конец схватывания не ранее, час/мин | 4-20 |
Портландцемент класс 500
Характеристика | Показатель | |
1 | Вещественный состав цемента, %:- гипсовый камень- портландцементный клинкер | 2,0-2,5100 |
2 | Предел прочности (3 суток твердения)- при изгибе, МПа- при сжатии, МПа | 4,5-4,825,0-27,0 |
3 | Массовая доля:- свободного оксида кальция, %- оксид магния в клинкере, % | менее 0,5менее 1,5 |
4 | Активность при пропаривании- при изгибе, МПа- при сжатии, МПа | 4,3-4,631,0-34,0 |
5 | Предел прочности (28 суток твердения)- при изгибе, МПа- при сжатии, МПа | 6,3-6,550,5-52,0 |
6 | Начало схватывания не ранее, час/мин | 2-32 |
7 | Тонкость помола (через сито 008), % | 90,0 |
8 | Конец схватывания не ранее, час/мин | 3-43 |
Сферы применения

Портландцемент отличается высокой прочностью, поэтому его используют в приготовлении бетонных смесей и строительных растворов.
Шлаковый портландцемент нашел свое активное применение при строительстве бетонных и железобетонных подводных, наземных и подземных сооружений, подверженных воздействию минерализованных и пресных вод. Благодаря высоким показателям прочности он используется при производстве бетонных смесей, стеновых блоков, сухих смесей и строительных растворов. Такой цемент не менее популярен, нежели классический цемент марки М500.
Строительный материал на данном этапе развития строительной промышленности является одни из наиболее доступных и экономически привлекательных. На его основе изготавливаются как стены, так и армированные плиты перекрытия. В большинстве случаев при сооружении зданий из облегченных материалов для фундамента отдают предпочтение шлакобетону.
При возведении стен используется как монолитная технология с переставной опалубкой, так и готовые фундаментные и стеновые блоки из шлакобетона.
Шлаковый портландцемент распределяют по классам, каждый из которых является наиболее подходящим для выполнения тех или иных задач. Класс 10 получил свое применение при теплоизоляции. Классы 25 и 35 используют при возведении ненесущих конструкций, класс 50 применяется при изготовлении армированных перемычек, наружных и внутренних несущих стен.
Масштабное применение шлакобетона определяется рядом преимуществ, среди которых малый удельный вес в сравнении с силикатным и керамическим кирпичом. Благодаря этому свойству снижаются нагрузки на фундамент и несущие конструкции строения.
Возможность создания блоков больших параметров способствует материальных и временных затрат в процессе укладки. Кроме того, такие блоки максимально удобны при транспортировке.
Особенности шлакощелочного бетона
Шлакощелочной портландцемент получают благодаря использованию щелочных металлов. Высоких показателей прочности удалось достичь добавлением различных щелочей: соды, стекла и ряда других.
Шлакощелочной портландцемент нашел свое применение при производстве железобетонных элементов с высоким показателем устойчивости к химически агрессивным веществам. Класс таких бетонов является незаменимым при строительстве массивных конструкций. Это связано с тем, что при производстве крупных бетонных элементов, в основе которых лежит портландцемент, происходит выделение большого количества тепла, и температура конструкции может достигать отметки в 80°С. При слишком быстром охлаждении объекта могут образовываться деформационные трещины. Использование шлакощелочного бетона позволяет избежать возникновения данной проблемы.
Наиболее популярным является класс шлакощелочного цемента на основе соединений щелочных металлов с преобладанием гидросиликатов кальция и гидроалюмосиликатов и молотого металлургического шлака.
Шлакощелочной цемент позволяет производить конструкции с меньшим количеством капиллярных пор. Данное свойство способно снизить водопоглощение и повысить морозоустойчивость бетона, способствуя росту эксплуатационных качеств строительной конструкции. За первые сутки материал набирает 30% прочности, которая в дальнейшем способна достичь отметки в МПа.
Данный класс бетона устойчив к воздействию агрессивных сред: сульфатов, кислот, хлоридов и морской воды. Возможность управлять свойствами цемента на различных стадиях структурообразования позволила получать вяжущие со специальными свойствами: морозо- и жаростойкие, безусадочные, с повышенной коррозионной устойчивостью, с высокой скоростью твердения, тампонажные.
o-cemente.info
Приготовление легкого бетона с применением шлака
Часто в строительстве не имеет смысла использовать материалы неоправданно завышенной прочности. Например, строим здание с малым количеством этажей. Конструкции там мало нагружены, поэтому на стены и перегородки нет сильной нагрузки и можно использовать материалы с прочностью пониже. Например, легкий бетон.Бетонная смесь для легкого бетона довольно проста. Основная часть «коктейля» шлак. При смешивании с цементом получается шлакобетон материал легкий, теплый и достаточно прочный. Кроме того, возведение обойдется гораздо дешевле, а при хорошей надежной влагоизоляции срок службы таких стен составляет более 50 лет. Еще одна положительная деталь - шлак, для приготовления такой смеси можно использовать самый разный. Металлургический, топливный. Самый распространенный и доступный конечно топливный, который образуется после сгорания угля. Лучше всего использовать шлак после сгорания антрацитовых углей, а вот шлак после сгорания бурого или подмосковного угля уже похуже. Первое требование к шлаку, который мы будем использовать для приготовления смеси его чистота. В нем не должно быть глины, земли и других посторонних примесей присутствие примесей, во-первых, снизит в итоге качество нашего шлакобетона, во-вторых, сложно будет угадать конечный результат при использовании «грязного» исходного сырья.
Отбирая шлак, нужно помнить, какие именно теплозащитные свойства и характеристики прочности мы хотим получить от стены из нашего шлакобетона. Если мы хотим в первую очередь легкую и теплую стену, лучше отбирать шлак крупной фракции, с гранулами 6-45 мм. Стена получится легкой и теплой. Но она будет и менее прочной.
Шлак с мелкими гранулами даст нам прочный бетон. Например, шлак с гранулами 0.3-6 мм даст нам прочную стену, но и тепловые свойства ее будут низкими. Для получения необходимого результата можно комбинировать шлак разных фракций при приготовлении смеси. Например там, где от стены требуется прочность и достаточная теплозащита, можно смешать крупную и мелкую фракции шлака. Соотношение крупная: мелкая фракции в пропорциях для приготовления смеси при этом обычно делается 7:3 или 6:4. Это даст достаточную прочность и хорошую теплозащиту для, например, несущих или наружных стен здания. Вдобавок для экономии цемента можно при этом использовать известь или глину в качестве добавок к бетонной смеси.
Приготовление самой смеси для легкого бетона ничем не отличается от приготовления обычной, разве что крупную фракцию шлака перед началом смешивания лучше увлажнить. Монолитные стены из приготовленного таким способом шлакобетона можно возводить так: заливается слой 15-20 см, после высыхания опалубка переставляется, заливается следующий слой и так до нужной высоты. Главное, при заливке слоя, нужно удалять пустоты. То есть слой нужно трамбовать и штыковать. Это достаточно хорошо препятствует образованию пустот.
Стены сохнут довольно долго, 25-30 дней. После высыхания можно приступать к дальнейшим работам отделке и пр. Хорошие результаты в плане придания внешнего вида получаются, если обкладывать полученные монолитные стены кирпичом. Или использовать другие типы отделки. Здесь много вариантов придания законченного благородного внешнего вида строению, зависит конечно от фантазии строителя и финансовых вложений.
nerudr.ru