ПРОИЗВОДСТВО КЕРАМЗИТОБЕТОННЫХ БЛОКОВ МОСКОВСКАЯ ОБЛАСТЬ. Производство керамзитобетонных блоков
Производство керамзитобетонных блоков
Продукция изготавливается на автоматической линии для производства мелкошнучных изделий, обеспечивающую получение бетонной продукции самого высокого качества.
Керамзитобетонные блоки используются:
1. Для строительства жилых домов: дачных, коттеджей, танхаусы, многоквартирные дома, производственных зданий и зданий культурного назначения. Блоки используются для возведения стен, перегородок и фундаментов.
2. Для дорожного строительства: лотки, бордюрные камни, плиты для укрепления откосов, камни подпорных стен.
3. Для благоустройства дачных, парковых и городских территорий: плитка тротуарная большой гаммы форм и расцветок.
Характеристики: производство керамзитобетонных блоков
Вибропресс обеспечивает высокое уплотнение бетонной смеси за кротчайший промежуток времени и требуемые прочностные характеристики изделий при оптимальном возможном содержании инертных материалов: цемента, керамзита, песка.
В зависимости от типа изделий: керамзитобетонные блоки и тротуарная плитка - цикл формования может составлять от 15 секунд. Управление всеми процессами осуществляется на программируемом контролере, с выводом всех данных на пульт управления.
Номенклатура изделий постоянно пополняется новыми образцами, при этом желания потребителя ограничиваются практически только площадью зоны формования 1000х500мм. и высотой изделий 50…250 мм.
Исходным материалом для приготовления смеси служат заполнитель, вяжущее и вода. В качестве заполнителя могут использоваться песок, отсевы щебеночного производства, керамзит, шлаки, золы, опилки и любые другие сыпучие материалы, способные после смешивания с вяжущим приобретать и сохранять заданную форму. В качестве вяжущего применяется цемент.
Специальная конструкция и высокая точность изготовления матриц обеспечивают высокую геометрическую точность и красивый внешний вид изделий, получаемых на предприятии “Комбинат керамзитобетонных блоков”. Благодаря этому при возведении зданий из стеновых камней, удается ускорить процесс кладки при одновременной экономии строительного раствора и получать ровные стены с тонкими швами, а при использовании в строительстве других получаемых на комплексе изделий - красиво благоустраивать территорию. В камере пропаривания и сушки, с помощью парогенераторов - происходит терм о-влажная обработка изделий с сушкой и вентиляцией.
Преимущества блоков:
1. Экономичность
2. Скорость постройки
3. Экологическая безопасность
4. Морозоустойчивость
5. Стойкость к грибка и плесени
6. Низкая теплопроводность
7. Высокие звукоизоляционные свойства
8. Пожаробезопасность
9. Легкость продукции
Виды изготавливаемой продукции:
Керамзитные и керамзитобетонные блоки:
1. 8-ми щелевые блоки
2. 4-х щелевые блоки
3. перегородочные блоки
4. полнотелые керамзитобетонные блоки
5. фундаментные блоки ФБС
6. стеновые блоки
7. кирпичи стеновые
8. 2-х пустотные блоки
Камни и бордюры:
1. Камень бордюрный разных размеров
2. Камень бордюрный садовый
Элементы благоустройства:
1. Травница - решетка газонная
2. Желоб водосточный
3. Камень столбовой
4. Проступь
Тротуарная плитка:
1. Плитка тротуарная "Шестигранник"
2. Плитка тротуарная "Катушка"
3. Плитка тротуарная "Толстушка"
4. Плитка тротуарная "Ромб"
5. Плитка тротуарная "Волна"
6. Плитка тротуарная "Прямоугольная"
7. Плитка тротуарная "Старый город"
8. Плитка тротуарная "Квадрат 250"
9. Плитка тротуарная "Квадрат 100"
10. Плитка тротуарная "Квадрат 500"
11. Плитка тротуарная "Квадрат 200"
Станок для изготовления керамзитобетонных блоков
Содержание статьи:
Использование керамзитобетонных блоков в строительстве имеет ряд преимуществ. Несмотря на свою небольшую удельную массу, они обладают должной механической прочностью, имеют низкий коэффициент теплопроводности. Но главным преимуществом является относительно несложная технология изготовления, для этого необходимо правильно подобрать станки.
Технология изготовления керамзитобетонных блоков
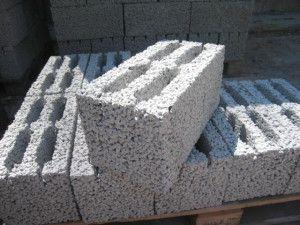
Внешний вид керамзитобетонного блока
В качестве основного материала используется керамзит небольшой фракции. Для связки компонентов между собой в смесь добавляют цемент, затем полученная масса проходит стадию обработки для получения строительных керамзитных блоков.
Дополнительно необходимо применять специальные добавки для производства. Для увеличения показателя морозостойкости добавляют омыленную древесную смолу. После этого смесь определенное время настаивают в течение 40-50 мин. Это необходимо для лучшей адгезии керамзита, цемента, песка и воды. Только после этого можно приступать к процессу производства.
Стадии изготовления керамзитоблоков.
- Засыпка состава в формы. Их количество может варьироваться от одной до 16 шт.
- Установка форм на вибростол или вибромашину. Это необходимо для формирования однородной плотности вещества по всему объему;
- Прессование. Для выполнения этого этапа применяются гидравлические или механические устройства. На верхнюю часть формы воздействует пресс, в результате чего происходит уплотнение блоков.
- Излечение заготовок для дальнейшей просушки. После формирования строительные заготовки еще не имеют достаточной механической прочности. Поэтому на этапе изучения и транспортировки в зону окончательной просушки необходимо соблюдать меры безопасности.
Зачастую эти операции осуществляются на одном производственном оборудовании. Для этого рекомендуется использовать специальный станок, в конструкции которого предусмотрены механизмы для полного цикла. В качестве дополнительного оборудования потребуется бетономешалка.
Форма емкостей определит назначение строительных блоков. Они могут применяться для возведения несущих стен или межкомнатных перегородок.
Параметры выбора станка для производства керамзитобетонных блоков
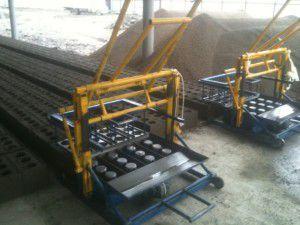
Установки по производству керамзитовых блоков
Для комплектации производственной линии можно использовать несколько видов оборудования. Их выбор зависит от требуемой производительности, общей площади цеха, а также бюджета на закупку.
Еще одним показателем является степень автоматизации. Но при этом должны соблюдаться принятые нормы качества для строительных материалов.
Условно станки для производства керамзитобетонных блоков можно разделить на следующие виды:
- ручные. Основная область применения — мелкосерийное изготовление в домашних условиях. Для уплотнения смеси вибратор крепится к корпусу станка. Но так как механический прижим не обеспечит должную плотность материала, при формировании смеси необходимо увеличить содержание цемента;
- передвижные линии. Являются оптимальным вариантом для комплектации производства с большой площадью цехов. После заполнения формы и формирования блоков они опускаются на землю. Конструкция переводится на другое место, таким образом, снижаются затраты для перемещения заготовок зоны просушки;
- вибростол. Характеризуется небольшим объемом выпускаемой продукции. Максимально этот показатель составляет 6 блоков за один цикл;
- вибропресс. Относится к разряду профессиональных линий. Объединяет в себе все операции. Для транспортировки готовых изделий присутствует конвейерная лента.
В комплектацию последней линии может входить блок для замешивания исходной смеси. Это позволяет добиться максимальной автоматизации, оптимизировать текущие затраты. Но в большинстве случаев для работы подобного оборудования необходимо выполнить ряд условий. Одним из них является подвод электролиний 380 В. Некоторые модели имеют пневматические узлы, для их функционирования может потребоваться компрессор.
В видеоматериале можно ознакомиться с примером работы передвижной линии:
stanokgid.ru
Организация производства керамзитобетонных блоков на вибропрессе Рифей-Удар
Рифей-Удар с высоким уровнем механизации производства блоков
Вибропресс Рифей-Удар успешно используется при изготовлении крупных объемов бетонных камней, в том числе, керамзитобетонных блоков, высокого качества. Производительность станка по пустотелому керамзитному камню 390х190х188 мм – 290 штук в час. Высокая эффективность вибропресса достигнута, благодаря современному уровню механизации и разумной организации производства.
Для того, чтобы минимизировать издержки из-за простоя оборудования и использовать станок Рифей-Удар для производства керамзитобетонных блоков эффективно, ознакомьтесь со следующими документами:
Требования к размещению оборудования
- Станок успешно функционирует только в закрытых помещениях или под навесом, оптимальная температура – от +5 до +45 градусов.
- Для размещения станка, склада сырья и продукции необходимо помещение площадью, как минимум, 160 м2, и высотой от 4 метров.
- Монтаж вибропресса требует обязательного бетонирования фундамента.
- В перечень работ по подготовке вибропресса Рифей-Удар входят подключение воды и электроэнергии напряжением 380 вольт. Максимальная мощность оборудования – 18,5 кВт/час.
Сырье для производства керамзитобетонных блоков
Основные исходные материалы для изготовления блоков – это заполнитель, вяжущий компонент и вода, которые преобразуются в жесткую бетонную смесь. В качестве заполнителя выступает песок, керамзит, мраморная крошка, отсевы производства щебня и другие материалы. Вяжущим всегда является цемент.
Примерные составы бетонных смесей для производства керамзитобетонных блоков описаны в разделе «Составы бетонов».
Необходимые процедуры
После формования сырые изделия подвергаются:
- либо вылеживанию в течение 1 суток при температуре от +15 до +45 градусов или в течение 2 суток при температуре от +5 до +10 градусов;
- либо 6-8-часовой термовлажностной обработке при температуре от + 50...75 градусов и влажности от 90%.
После прохождения одной из указанных процедур бетонные блоки приобретают прочность, позволяющую транспортировать и складировать их.
Полная прочность после вылеживания появляется у изделий через 28 суток хранения при температуре 20 градусов.
После вылеживания в пропарочной камере блоки сразу приобретают 60-80% конечной прочности.
Дополнительное оборудование
- Емкость для хранения цемента.
- Шнековый транспортер, необходимый для перемещения цемента в смеситель.
- Бункеры с ленточным транспортером для подачи заполнителя в смеситель.
- Поддоны, которые требуются для размещения отформованных бетонных изделий при их вылеживании и хранении. Поддоны должны быть сделаны из фанеры марки ФСФ, с толщиной 30 миллиметров. Для нормального функционирования вибропресса требуются поддоны в количестве от 240 до 500. Необходимое количество поддонов снижается при наличии пропарочной камеры.
Поддоны располагаются на металлическом стеллаже. Металлический стеллаж – это сварная конструкция, на которой можно разместить 6 поддонов. Производство керамзитобетонных блоков требует от 40 до 85 стеллажей.
Для хранения и подачи пустых поддонов необходимы кассеты в количестве 3-5 штук.
Базовый комплект поставки для производства и изготовления блоков включает в себя 1 стеллаж, 1 кассету и 8 поддонов. Это дополнительное оборудование требуется для пробного пуска станка и изготовления опытной партии блоков. Остальные кассеты, поддоны и стеллажи покупатель должен заказать или изготовить самостоятельно. Чертежи Вы найдете в разделе сайта «Справочная информация».
- Грузоподъемное оборудование, обеспечивающее высокую производительность: кран-укосина, кран-балка, погрузчик, таль. Двухскоростная кран-балка помогает избежать повреждения отформованных изделий при транспортировке.
Как работает станок для производства блоков керамзитобетонных
- Приготовление бетонной смеси. Заполнитель, вода и цемент подаются в дозатор бетоносмесителя, в количестве, определяемом оператором. Подача заполнителя и вяжущего может осуществляться как вручную, так и с помощью бункеров и другого оборудования. Уровень воды поддерживается автоматически, посредством поплавкового механизма.
- Из дозатора компоненты подаются в бетоносмеситель вручную – оператор поворачивает рукоятки, открывающие дно затвора.
- После смешивания компонентов смеси открывается люк на дне бетоносмесителя, и смесь попадает на транспортер, доставляющий ее в вибропресс. Подготовка смеси производится столько раз, сколько это необходимо для обеспечения бесперебойной работы вибропресса. Электродвигатели транспортера и бетоносмесителя включаются дистанционно, с помощью пульта управления.
- Смесь поступает из бункера в загрузочный ящик, а затем транспортируется в матрицу и загружается в нее с помощью вибростола.
- После полной загрузки матрицы происходит уплотнение смеси движениями вибростола и пуансона.
- Приготовленные блоки выдавливаются на поддон и перемещаются к накопителю тележкой пресса, а затем поддоны загружаются на стеллаж, установленный на накопителе. После загрузки стеллаж снимается с накопителя, а на его место устанавливается следующий пустой стеллаж. Из кассеты вибропресса поступают новые поддоны, и цикл повторяется нужное количество раз.
- После заполнения стеллажи с керамзитобетонными блоками собираются в штабель (друг на друга по 7 штук) с помощью тали, крана-укосины, или других грузоподъемных средств. Полученные штабели переносятся в пропарочную камеру или на место для вылеживания с помощью кран-балки или вилочного погрузчика.
- После отвердевания блоков штабели стеллажей перемещаются в зону распалубки, в которой блоки перекладываются на товарные поддоны. На этом этапе изделия готовы к транспортировке к потребителю или на склад. Пустые и очищенные поддоны собираются в кассеты и используются при производстве многократно.
press-rifey.ru