ОТБОР И ПРИГОТОВЛЕНИЕ АСФАЛЬТОБЕТОННОЙ СМЕСИ. ИЗГОТОВЛЕНИЕ АСФАЛЬТОБЕТОННЫХ ОБРАЗЦОВ. Производство асфальтобетонной смеси
Производство асфальтобетона, оборудование и технология приготовления асфальтобетона в заводских условиях

Ирина
Специалист отдела продаж ответит на все ваши вопросы!
+7 (800) 700-97-90
Одним из перспективных направлений деятельности в РФ является производство асфальтобетона, который используют для обустройства покрытия автомобильных дорог различного назначения. Асфальтобетон представляет собой строительный материал, который получают вследствие затвердевания смеси минеральных веществ с битумом. Технология получения асфальтобетона включает большой набор обязательных компонентов:
- Песок. Обеспечивает создание мелкозернистой основы, которая выполняет функции наполнителя мелких полостей и способствует распределению механического давления от поверхности дороги к грунту.
- Щебень. Создает требуемый уровень механической прочности, что является одной из главных характеристик асфальтобетонной смеси.
- Минеральные наполнители. В качестве этих компонентов используют измельченную горную породу (известняк, мел, песчаник). Эти наполнители позволяют асфальтобетонной смеси заполнять остаточные пустоты и значительно снижают себестоимость её производства.
- Битум. Является жидким связующим, которое склеивает все компоненты в единую монолитную смесь.
- Резина. Этот компонент вводится в виде измельченной крошки и предназначен для придания готовому асфальту высокой степени упругости, стойкости к воздействию влаги. Стоимость резины значительно увеличивает стоимость асфальта, поэтому её используют только для самых ответственных участков дороги с повышенной механической нагрузкой.
Правильное пропорциональное распределение всех этих компонентов позволяет получить асфальт, который будет обладать всеми необходимыми эксплуатационными параметрами.
Особенности производства асфальтобетона
Процесс производства асфальтобетона может выполняться при различных температурных режимах, что служит критерием для классификации асфальтной смеси на три различных категории:
- Холодные. Асфальтобетонный материал этого типа изготавливают с добавлением жидкого битума. Допускается длительное хранение и использование этой смеси при температуре не ниже +50С.
- Теплые. Асфальт этого типа изготавливают из жидкого битума и вязких связующих, поэтому температура их хранения должна составлять не менее 1000С.
- Горячие. Асфальтобетонная смесь изготавливается и укладывается при температуре не ниже 1200С.
В зависимости от фракции, используемых для изготовления асфальта компонентов, он подразделяется на три основных вида:
- Крупнозернистый. Данный материал отменно подходит для выполнения дорожного покрытия в нижних его слоях. Одним из основных компонентов этой смеси является щебень крупной и мелкой фракции.
- Мелкозернистый. Асфальтобетон этого типа применяют для обустройства верхнего покрытия у дорог общего пользования. В его состав входит щебень мелкой фракции, который может достигать величины 15 мм.
- Песчаный. Этот тип асфальта применяют для обустройства пешеходных дорожек и тротуаров. В состав этой асфальтной смеси вводят большое количество песка, битума и щебня с фракцией до 5,0 мм.
Технология изготовления смеси
Технология производства асфальтобетона состоит из нескольких основных этапов, которые включают все необходимые операции и работы:
- Входной контроль исходного сырья: минеральные добавки, битум, щебень, песок.
- Обработка инертных материалов: просеивание песка, разделение щебня по фракциям, разогрев битума.
- Доведение всех компонентов до требуемого уровня влажности и температуры нагрева.
- Перемешивание между собой всех составных компонентов асфальтобетонной смеси, что обеспечивает сцепление битума с песком, зернами щебня и минеральным наполнителем.
- Хранение готового асфальта в специальном бункере, где происходит поддержание требуемого температурного режима.
Забор готового продукта происходит непосредственно из бункера хранения, после чего его доставляют до места укладки с соблюдением всех технологических требований. Подобная технология изготовления асфальтобетона используется практически на всех отечественных заводах. Некоторые производители вводят в состав асфальта каучуковую крошку или латекс, что направлено на получение смеси с высокой степенью упругости.
Типы оборудования для производства
Оборудование для производства асфальтобетона в зависимости от технологических особенностей подразделяют на заводы непрерывного и циклического действия:
- Технологическая схема производства асфальтобетона на оборудовании непрерывного действия характеризуется отсутствием башни и грохота, которые необходимы для качественной сортировки исходного сырья. Все ингредиенты непрерывно подают в приемные бункеры, после чего они доводятся до требуемого состояния готовности к перемешиванию. Отсутствие грохота делает возможным случаи попадания в готовую асфальтобетонную смесь щебня некондиционных размеров или посторонних включения. Основное преимущество подобных заводов – компактные размеры и высокая степень мобильности.
- Технология приготовления асфальтобетона на оборудовании циклического действия характеризуется наличием грохота и приемных башен. Благодаря этому вспомогательному оборудованию обеспечивается высокая степень подготовки исходного сырья еще до подачи в бункер для перемешивания. Асфальтный завод циклического действия располагают вблизи крупных городов, где регулярно есть потребность в небольшом объеме асфальтобетонной смеси. Главное преимущество подобных технологических схем: изменение рецептуры до нескольких раз в день, без ухудшения качества готового продукта, возможность готовить асфальт небольшими порциями, высокое качество подготовки сырья. Главный недостаток подобных заводов – низкий уровень мобильности.
Приготовление асфальтобетона в заводских условиях требует наличия персонала соответствующего уровня квалификации, который будет уметь правильно снимать показания аппаратуры, знать все технологические особенности производства и быстро реагировать на отклонения от заданного технологического режима работы.
sdm-sam.ru
Производство асфальтобетонных смесей - страница 11
Исходя из категории дорожно-климатической зоны и категории автомобильной дороги данной смеси соответствуют следующие марки битума: СГ 70/130 СГ 130/200, МГ 70/130, МГ 130/200, МГО 70/130, МГО 130/200
Содержание минерального порошка.
МП=(a/b)*100%
Где а – требуемое среднее содержание минеральной части асфальтобетона, частиц мельче 0,071 мм в %. Оно составляет 12-17% по массе.
b – содержание частиц мельче 0,071 мм в исходном минеральном порошке в % от минеральной части (по заданию). Оно составляет 93%.
МП1=(12/93)*100=12,9% МП2=(17/93)*100=18,2% МП=12,9-18,2%
4.Технология приготовления асфальтобетонных смесей
4.1 Последовательность приготовления смеси
Приготовление асфальтобетонной смеси состоит из следующих операций: подготовки минеральных материалов, подготовки битума, дозирования составляющих, перемешивания минеральных материалов с битумом и выгрузки готовой смеси в кузова автосамосвалов или накопительные бункеры.
Подготовка минеральных материалов включает подачу их к сушильным агрегатам, а при необходимости сортировку по фракциям или обогащение добавками другого материала и активацию. Сюда относится сушка материала и нагрев до требуемой температуры. Щебень, гравий и песок должны быть полностью просушены и иметь до поступления в мешалку температуру на 5 – 10 оС больше, чем битум. Температура их падает на 5 – 7 оС при перемещении горячим элеватором от сушильного барабана к дозаторам. Поэтому температура минеральных материалов должна составлять 180 – 200 оС для горячего асфальтобетона. Минеральный порошок, как правило, подается без подогрева.
Производительность асфальтобетонных заводов в значительной мере зависит от работы сушильных агрегатов. Сушильный агрегат включает сушильный барабан с топкой и форсунками, а также расходную емкость топлива. Сушка и нагрев материала осуществляются непрерывно горячими газами от сжигания топлива, идущими навстречу направлению движения щебня и песка. Скорость сушки материала, а следовательно и производительность сушильного барабана, зависят от влажности песка и щебня.
До поступления в сушильный агрегат щебень и песок дозируют агрегатами питания, окончательное их дозирование осуществляют по массе отдельных фракций перед подачей в мешалку. Точность дозирования для щебня, песка и минерального порошка должна быть не менее ±3%, а для битума ±1,5%. В асфальтосмесительных установках непрерывного действия составляющие материалы дозируются объемными дозаторами непрерывного действия. После сушки и нагрева все материалы подают в смесительный агрегат, который имеет грохот, многофракционный дозатор для щебня, песка, минерального порошка и вяжущего, а также смеситель и другие механизмы и бункеры.
Материалы взвешиваются на суммирующем весовом устройстве и загружаются в двухвальную лопастную мешалку, в которую из дозирующего устройства подают битум. Битум подают распылением под давлением до 2 МПа. В этом случае происходит равномерное распределение и обволакивание поверхности минеральных частиц пленкой битума, к тому же такая подача сокращает продолжительность перемешивания.
Продолжительность перемешивания смеси массой около 700 кг составляет для крупнозернистой 20...30 с, средне и мелкозернистой — 45...60 с и песчаной — 60...75 с. Время перемешивания сокращается на 15...20% при применении поверхностно-активных веществ или активированных минеральных порошков. При небольшом содержании битума или повышенном содержании минерального порошка продолжительность перемешивания увеличивается. Смесь должна быть хорошо перемешанной и однородной по массе. На качество готовой смеси оказывает влияние и порядок смешивания составляющих. По традиционной технологии одновременно смешиваются все компоненты.
Температура готовой асфальтобетонной смеси, используемой в горячем состоянии, должна быть в пределах 140...170°С, а при применении ПАВ — 120...140°С. Масса одного замеса — 600... 700 кг. Для загрузки большегрузного автосамосвала требуется до 15 мин. Поэтому в цели сокращения простоя автомобиля под погрузкой около смесителей устраивают накопительные бункеры, в которые смесь поступает прямо из смесителей, а оттуда выгружается в кузов автосамосвала. Для загрузки машины требуется 2... 3 мин.
Доставка асфальтобетонной смеси на трассу производится автомобилями-самосвалами, кузова которых перед загрузкой смеси должны быть тщательно очищены и смазаны тонким слоем нефти, масла или мыльного раствора. В весенне-осенний период кузова автомобилей укрываются специальными щитами или матами во избежание остывания смеси. На каждый отправляемый автомобиль с асфальтобетонной смесью выдается сопроводительный паспорт, в котором указываются масса, температура смеси и время отправки с завода.
Асфальтобетонная смесь укладывается в покрытие асфальтоукладчиками при сухой и теплой погоде. По действующей инструкции горячие асфальтобетонные смеси должны укладываться весной при температуре воздуха не ниже -f5°C, а осенью — не ниже
+ 10°С, причем поверхность нижележащего слоя основания или покрытия должна быть чистой и сухой. В противном случае не будет обеспечено требуемое сцепление между слоями.
Для обеспечения надлежащего сцепления между конструктивными слоями поверхность нижележащего обрабатывают битумами или битумными эмульсиями и суспензиями. Расход вяжущего составляет 0,4...0,6 л/м^. По подготовленному таким образом участку дороги должно быть прекращено движение.
Сразу же после раскладки асфальтобетонную смесь уплотняют легкими катками, а затем тяжелыми. В результате уплотнения смеси повышается ее плотность, ее слой приобретает водостойкость, а при остывании и прочность. Недоуплотненные асфальтобетонные покрытия могут стать причиной преждевременного разрушения. Таким образом, от степени уплотнения зависят долговечность и важнейшие свойства асфальтобетонных покрытий. Повышенной уплотняемостью обладают смеси с активированными минеральными порошками или ПАВ, поэтому наибольшая уплотняющая нагрузка для таких смесей значительно ниже, чем для асфальтобетонов с неактивированными минеральными порошками. Весьма хорошие результаты уплотнения дают пневморезиновые и вибрационные катки. Необходимо, чтобы во время строительства покры-' тие было полностью уплотнено. О степени уплотнения судят по соотношению плотности асфальтобетона, уплотненного катками и прессом под давлением 40 МПа. Это отношение, названное коэффициентом уплотнения, должно быть 0,98...0,99.
При производстве асфальтобетонных смесей на всех этапах обеспечивается систематический контроль качества. На первых этапах тщательно проверяется качество исходных материалов и устанавливается соответствие их показателей требованиям действующих ГОСТов. Работниками заводской лаборатории ведется контроль за точностью дозирования и за сохранением качества материалов.
4.2 Описание оборудования для приготовления асфальтобетонных смесей
Асфальтобетонные смеси готовят на специальных заводах (АБЗ), которые могут быть стационарными и временными. Обычно стационарные асфальтобетонные заводы устраивают для обеспечения нужд городского дорожного строительства, а для строительства загородных дорог общего пользования сооружают временные заводы, действующие 1...5 лет. Асфальтобетонные заводы, как правило, размещают вблизи железнодорожных путей или около строящейся дороги, чтобы сократить объем погрузочно-разгрузочных и транспортных работ. С одного АБЗ обслуживают строящиеся дороги в радиусе 60...70 км.
В последние годы как в СССР, так и за рубежом созданы высокопроизводительные передвижные и легкоперебазируемые АБЗ с радиусом действия 5... 10 км. Установки представляют собой комплекты агрегатов, которые принимают из транспортных средств материалы, дозируют их, производят сушку и нагрев, готовят и выдают смесь в транспортные средства. Все агрегаты смонтированы на прицепах на пневмоходу и переводятся из транспортного положения в рабочее благодаря наличию грузоподъемных средств. Как правило, склады и битумохранилище перебазируются при значительном удалении передвижного АБЗ.
Асфальтобетонные заводы оснащены оборудованием, которое позволяет механизировать и автоматизировать все технологические процессы приготовления асфальтобетонных смесей. В дорожном строительстве применяются АБЗ с оборудованием производительностью 25...200 т/ч. В ближайшие годы намечается выпуск асфальтосмесительных машин ДС-129-5 производительностью до 400 т/ч.
Основными агрегатами на АБЗ являются асфальтосмесители, которые подразделяются на три группы: смесители периодического действия со свободным перемешиванием типа Д-138 и Г-1м; смесители периодического действия с принудительным перемешиванием; смесители непрерывного действия.
Смесители первой группы широко использовались 10...15 лет назад. Они просты по конструкции и обслуживанию. В настоящее время их используют в основном для приготовления крупнозернистых смесей. Производительность их невысокая — 10...15 т/ч, масса одного замеса — З...3,5 т.
В настоящее время для приготовления асфальтобетонных смесей используют смесители периодического действия с принудительным перемешиванием: Д-508-2А производительностью 25 т/ч, ДС-117-2Е —25 т/ч, Д-617-2—50 т/ч, Д-645-2—100 т/ч, дС-84-2—200 т/ч.
К смесителям непрерывного действия относится Д-645-3 с мешалкой Д-647 производительностью 100 т/ч. Б состав асфальтобетонного завода входят: склады каменных материалов с оборудованием для их дополнительной переработки; склад минерального порошка; цех по приготовлению минерального порошка; битумное хозяйство, включающее битумохранилище, битумные расходные котлы, битумопроводы и битумные насосы; оборудование и механизмы перемещения и подачи каменных материалов; оборудование для сушки и нагрева до требуемой температуры минеральных материалов; оборудование для дозирования и перемешивания всех компонентов. Кроме того, в состав АБЗ входят: оборудование для энерго-, водо-, воздухо- и пароснабжения, а также лаборатория контроля качества используемых материалов и готовой смеси, склад мелких деталей и инструмента, служебные и бытовые помещения.
Щебень, гравий, песок и другие каменные материалы хранят в штабелях высотой 8...10 м на открытых площадках. При этом следят за тем, чтобы эти материалы не смешивались.
Каменные материалы желательно хранить под навесами во избежание излишнего их увлажнения.
К сушильным установкам каменные материалы в зависимости от принятой технологии приготовления асфальтобетонной смеси подаются ленточными транспортерами, механическими погрузчиками и т. д.
Минеральный порошок па заводы поступает в готовом виде, а также может готовиться на АБЗ. Просушенный известняк или доломит размалывают в шаровых или трубных мельницах до требуемой тонкости. В процессе помола можно вводить активирующие добавки и получать активированные минеральные порошки хранят минеральный порошок в закрытых помещениях или силосах, исключающих попадание влаги. В дозаторы и смесители минеральный порошок подают ленточными или шнековыми транспортерами, а также пневматическим транспортом.
Битумохранилище обычно располагают у железнодорожных подъездных путей, а при наличии водного пути — у пристани. Битумоплавильные котлы стараются разместить ближе к битумохранилищу, но в этом случае они могут оказаться далеко от смесителей, что приводит к необходимости установки отдельных расходных котлов у смесительных агрегатов. Разогрев битума может осуществляться: паровыми змеевиками, жаровыми трубами и электронагревательными элементами. Электронагрев наиболее гигиеничен и прогрессивен, так как дает возможность автоматически регулировать и поддерживать заданную температуру. Подача битума к смесителям осуществляется битумными насосами по обогреваемым трубопроводам.
продолжениеwww.coolreferat.com
ОТБОР И ПРИГОТОВЛЕНИЕ АСФАЛЬТОБЕТОННОЙ СМЕСИ. ИЗГОТОВЛЕНИЕ АСФАЛЬТОБЕТОННЫХ ОБРАЗЦОВ
⇐ ПредыдущаяСтр 3 из 6Следующая ⇒
2.1. Отбор проб и приготовление смесей в лаборатории
Отбор проб при приготовлении смесей в производственных смесительных установках начинают не ранее чем через 30 мин после начала выпуска смеси. Для испытаний необходимо отобрать объединенную пробу, составленную из трех-четырех тщательно перемешанных между собой точечных проб.
Отбор точечных проб смесей производят в зависимости от производительности смесителя с интервалом от 15 до 30 мин. Точечные пробы отбирают непосредственно после выгрузки смеси из смесителя или накопительного бункера.
При проведении потребителем контрольных испытаний отбор проб производят из кузовов автомобилей, при этом из одного или нескольких автомобилей в зависимости от объема поставляемой партии отбирают три-четыре точечные пробы для одной объединенной пробы.
Масса объединенной пробы смесей в зависимости от размера зерен минерального материала должна быть не менее указанной в табл. 2.1.
Таблица 2.1
Наибольшая крупность минерального материала, мм | Масса объединенной пробы, кг | |
Для приемосдаточных испытаний | Для периодических испытаний | |
В а/б смеси: 10, 15, 20 | 2,5 6,5 6,0 – для пористых и высокопористых смесей 17,0 – для плотных смесей | 3,5 10,0 6,0 - для пористых и высокопористых смесей 28,0 – для плотных смесей |
Для отбора проб из конструктивных слоев дорожных одежд выбирают участок покрытия на расстоянии не менее 0,5 м от края покрытия или оси дороги и размером не более 0,5х0,5 м. Отбор проб производят в виде вырубки прямоугольной формы или высверленных цилиндрических кернов. Цилиндрические керны высверливают на всю толщину покрытия (верхний и нижний слой вместе) с помощью буровой установки и разделяют слои в лаборатории.
Размеры вырубки и количество высверливаемых кернов с одного места устанавливают по максимальному размеру зерен и исходя из требуемого для испытаний количества образцов. При этом масса вырубки или кернов, отобранных с одного места, должна быть не менее, кг:
1 - для песчаных смесей;
2 - для мелкозернистых смесей;
6 - для крупнозернистых смесей.
Диаметр кернов должен быть не менее, мм:
50 - для проб из песчаного асфальтобетона;
70 - для проб из мелкозернистого асфальтобетона;
100 - для проб из крупнозернистого асфальтобетона.
При требовании заказчика определять пределы прочности при сжатии переформованных образцов массу вырубки или кернов следует увеличивать.
Из вырубки выпиливают или вырубают три образца с ненарушенной структурой для определения средней плотности, водонасыщения, набухания и коэффициента уплотнения смесей в конструктивных слоях дорожных одежд.
Образцы должны иметь форму, приближающуюся к кубу или прямоугольному параллелепипеду со сторонами от 5 до 10 см. Наличие трещин в образцах не допускается. Образцы-керны испытывают целиком. Допускается при необходимости керны распиливать или разрубать на части.
При приготовлении смесей в лаборатории по горячей технологии минеральные материалы (щебень, песок, минеральный порошок) предварительно высушивают, а битум обезвоживают.
Минеральные материалы в количествах, заданных по составу, отвешивают в емкость, нагревают, периодически помешивая, до температуры, указанной в таблице 2.2, и добавляют требуемое количество не нагретого минерального порошка и нагретого в отдельной емкости вяжущего.
Смеси минеральных материалов окончательно перемешивают в лабораторном смесителе до полного и равномерного объединения всех компонентов. Время, необходимое для перемешивания, устанавливают опытным путем для каждого вида смесей. Перемешивание считают законченным, если все минеральные зерна равномерно покрыты вяжущим и в готовой смеси нет его отдельных сгустков.
Допускается смешивание вручную, при этом необходимо поддерживать в процессе приготовления горячих смесей температуру в соответствии с требованием табл. 2.2.
Таблица 2.2
Наименование материалов | Температура нагрева, °С, в зависимости от показателей вяжущего | ||||||
Глубина проникания иглы при 25 °С, 0,1 мм | Условная вязкость по вискозиметру с отверстием 5 мм, с | ||||||
40-60 | 61-90 | 91-130 | 131-200 | 201-300 | 70-130 | 131-200 | |
Минеральные материалы | 170-180 | 165-175 | 160-170 | 150-160 | 140-150 | 100-120 | 120-140 |
Вяжущее | 150-160 | 140-150 | 130-140 | 110-120 | 100-110 | 80-90 | 90-100 |
Смесь | 150-160 | 145-155 | 140-150 | 130-140 | 120-130 | 80-100 | 100-120 |
Примечание - При применении поверхностно-активных веществ или активированных минеральных порошков для приготовления смесей с вязкими вяжущими температуру нагрева минеральных материалов, вяжущего и смесей снижают на 10-20 °С. |
Температура щебеночно-мастичных смесей в зависимости от применяемого битумного вяжущего при изготовлении образцов должна соответствовать значениям, указанным в табл. 2.3.
Таблица 2.3
Глубина проникания иглы, 0,1 мм, при температуре 25 °С | Температура, °С не менее |
От 40 до 60 включительно | 150-155 |
Св. 60 до 90 включительно | 145-150 |
Св. 90 до 130 включительно | 140-145 |
Св. 130 до 200 | 135-140 |
Температура литой смеси при изготовлении образцов указана в табл. 2.4.
Таблица 2.4
Тип смеси | Температура смеси, ºС |
I II, III IV V | 220-240 200-220 165-180 180-200 |
Контрольные образцы смесей асфальтобетона
Формы и размеры образцов.
Физико-механические свойства смесей, асфальтобетонов определяют на образцах, полученных уплотнением смесей в стальных формах.
Формы для изготовления цилиндрических образцов представляют собой стальные полые цилиндры, которые могут изготовляться в виде кассеты с тремя взаимосвязанными цилиндрическими формами диаметром 101,0мм, 71,4мм, 50,5 мм или одиночных обычных (рис.2.1). Размеры в зависимости от наибольшей крупности минеральных зерен приведены в табл. 2.5.
Таблица 2.5
Наибольшая крупность минеральных зерен | Размеры форм, мм | Площадь образца, см2 | |||||||||||
d | d1 | H | h2 | h3 | h4 | h5 | d | d1 | d2 | d3 | d4 | ||
Форма одиночная обычная | |||||||||||||
50,5 | - | - | - | - | - | - | - | ||||||
10; 15; 20 | 71,4 | - | - | - | - | - | - | - | |||||
101,0 | - | - | - | - | - | - | - |
![]() |
Рис. 2.1. - Форма одиночная обычная |
Читайте также:
lektsia.com
Современные тенденции развития заводов по производству асфальтобетонных смесей
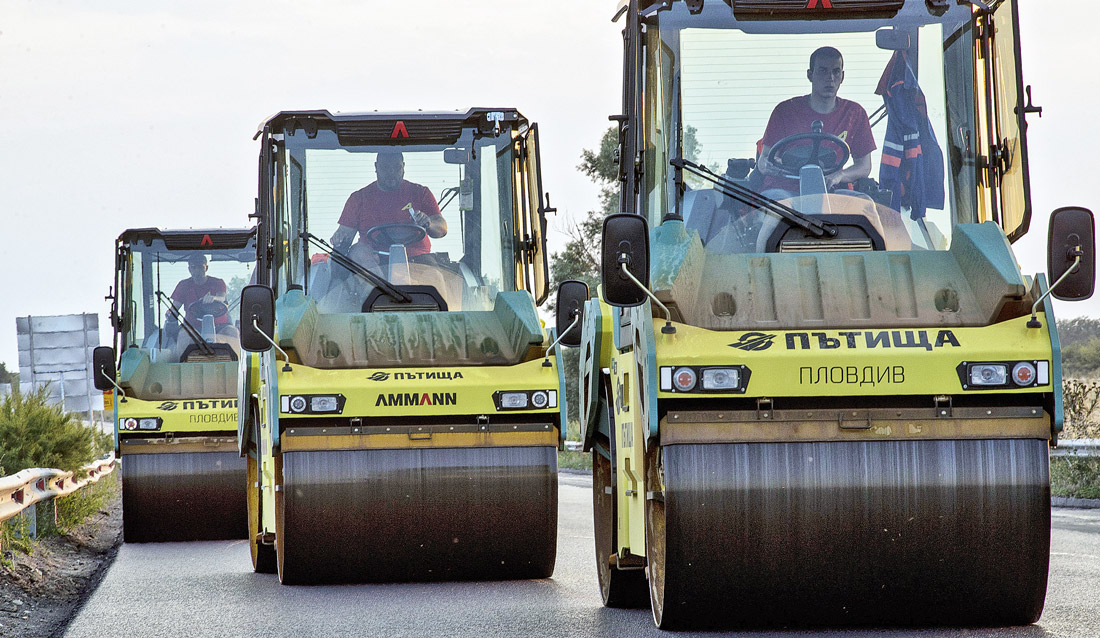
О любви и внимании
Известно, что дороги, как и люди, нуждаются во внимании и даже любви. Чтобы дороги служили долго, их нужно покрывать и ремонтировать высококачественным асфальтобетоном. В этой статье мы рассмотрим некоторые современные тенденции развития заводов по производству асфальтобетонных смесей (АБЗ).
Увеличение использования регенерированного асфальтобетона
Важной современной тенденцией является расширение вторичного использования регенерированного асфальтобетона в производстве новых асфальтобетонных смесей. Интерес к использованию регенерированного старого асфальтобетона зародился прежде всего в США, так как объемы производства и использования там асфальтобетона были значительно выше, чем в Европе. В настоящее время в США дорожники используют в асфальтовых смесях до 30–40% регенерированного асфальтобетона. Однако в настоящее время сэкономить за счет вторичного использования снятого старого асфальтобетона стараются дорожники по всему миру.
Регенерация материала старого покрытия на АБЗ позволяет экономить энергию и материальные ресурсы (по опыту дорожного строительства в США стоимость ремонта дорог уменьшается на 20–30%). Зарубежный опыт показывает, что экономия новых материалов при строительстве и ремонте дорог может составлять до 50%.
Преобладающим направлением регенерации в настоящее время на АБЗ является добавление старого асфальтобетона к новой смеси в количестве не менее 30–50% по массе.
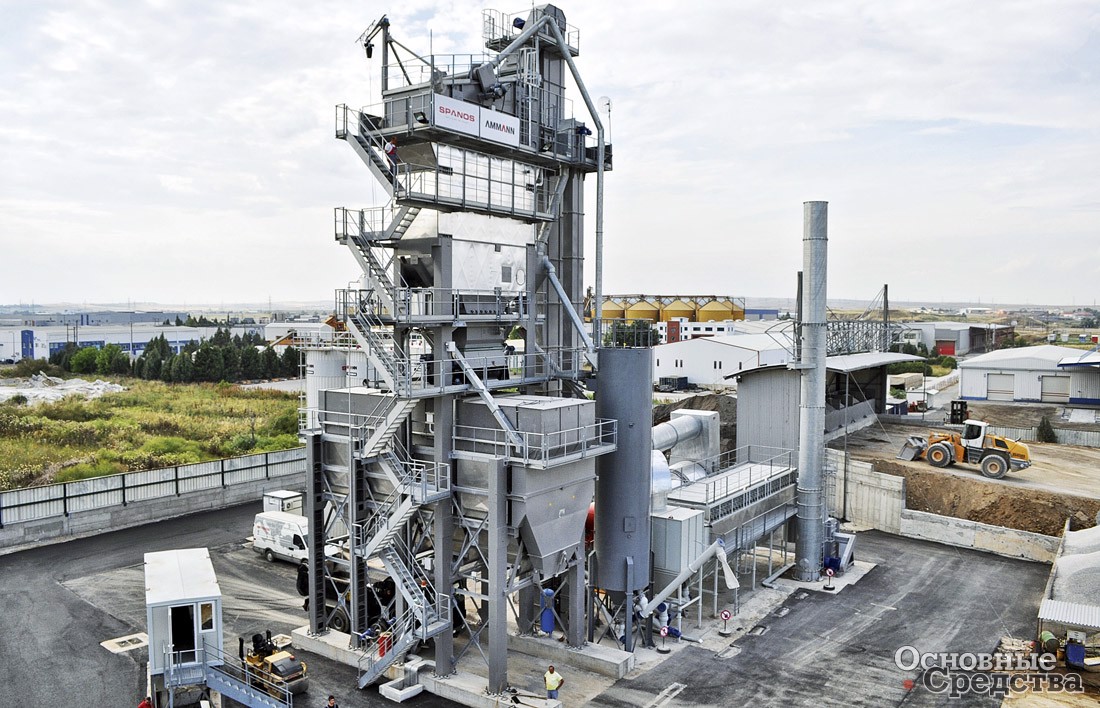
Компания Ammann представила на выставке CONEXPO-CON/AGG 2017 оригинальный асфальтовый завод ABA UniBatch, который вызвал большой интерес посетителей. Производительность завода в зависимости от комплектации может быть от 80 до 340 т/ч. Установка имеет модульную конструкцию, что позволяет удовлетворить фактически любые пожелания клиента. На заводе возможно применение до 100% вторично используемого асфальтобетона. Вторично используемый асфальт может подаваться различными технологическими способами. Объем вторичного асфальта зависит от комплектации завода и пожеланий заказчика. ABA UniBatch может работать на различных видах топлива: природный или сжиженный газ, дизельное топливо и мазут, угольная пыль и древесные опилки. Предлагается множество опций, с помощью которых любой клиент сможет подобрать наиболее подходящую для своих задач комплектацию АБЗ. Представители компании Ammann уверены, что в связи с расширяющимся применением в мире вторичного асфальта у АБЗ линейки ABA UniBatch большое будущее.
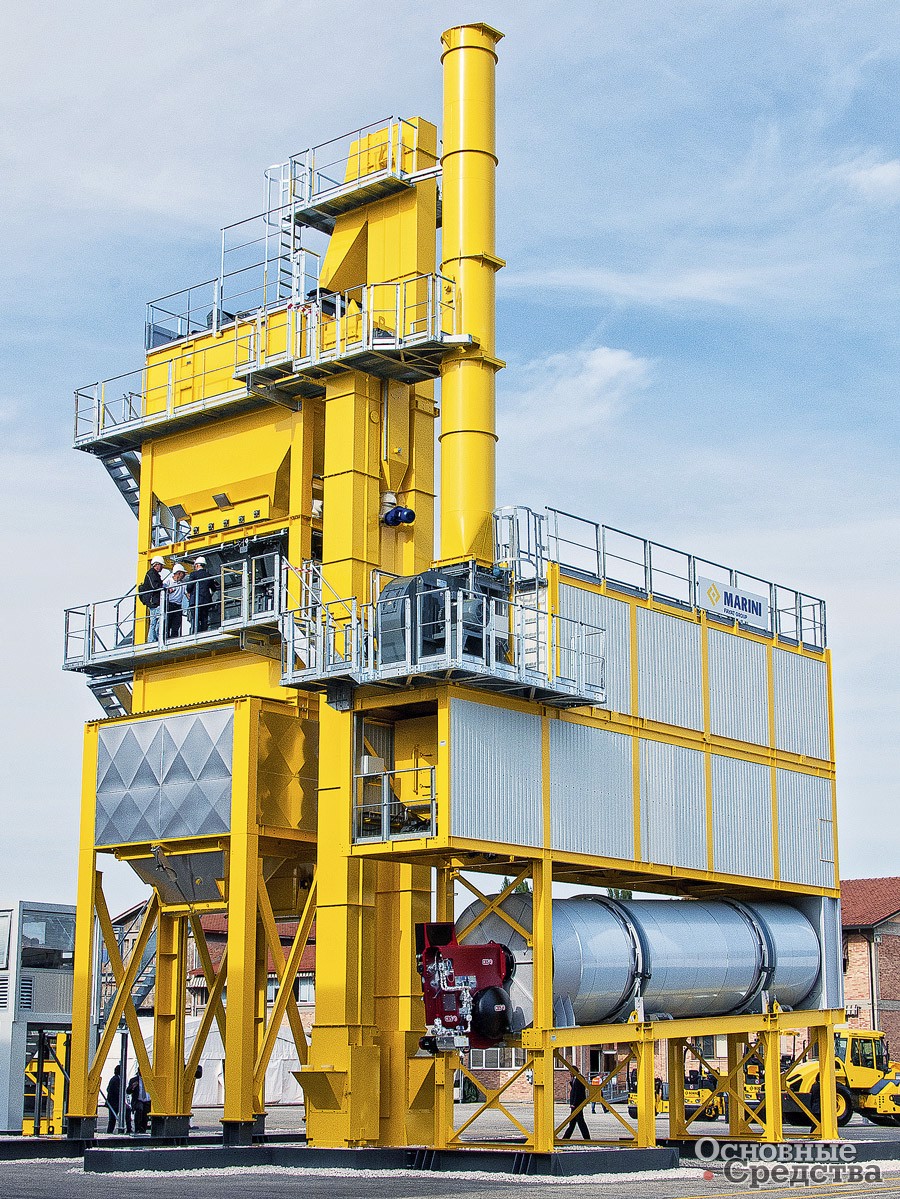
Итальянская компания MARINI (входит в группу компаний FAYAT) уже долгое время является экспертом в области переработки рециклинга. В портфеле предложений компании имеются все различные схемы использования вторичного асфальта, однако изначально компания специализировалась на подаче материала в рециклинговое кольцо сушильного барабана. Следует отметить, что в этом направлении компания достигла впечатляющих результатов, конструктивно такой способ продуман до мелочей, начиная от внутренней части сушильного барабана и заканчивая управлением блоком подачи рециклинга. Для того чтобы у заказчика была возможность быстро и недорого подключить данную опцию в будущем, все барабаны, производящиеся компанией MARINI, в базовой комплектации имеют предварительно встроенное в барабан кольцо рециклинга. Для подачи до 60% материала без его нагрева в параллельном сушильном барабане компания предлагает дуплексную систему ввода материала в кольцо барабана и в смеситель в одном цикле. Для обеспечения рекордной производительности заводов серии TOP TOWER компания MARINI разработала и внедрила смеситель объемом 6000 кг. Решение позволяет при подаче рециклинга в смеситель должным образом выдерживать время контакта «RAP-щебень» до введения битума, что препятствует возникновению испарения с высоким уровнем летучих органических веществ. В этом случае качество вводимого битума не теряется, так как отсутствует окисление при его попадании на чрезмерно разогретый щебень, а производительность растет, так как увеличение время контакта «RAP-щебень» компенсируется дополнительным объемом материала в смесителе. Для заказчиков, выбирающих гипермобильный асфальтобетонный завод MARINI XPRESS 2500 производительностью 200 т/ч, имеется возможность подачи асфальтовой крошки даже в смеситель, что уникально для мобильных заводов в принципе. Само конструктивное решение завода необычно и прогрессивно с точки зрения монтажа: не требуется использования кранов и устройства бетонных фундаментов. Грохот устанавливается в рабочее положение по направляющим рельсам-лонжеронам с криволинейным профилем с помощью лебедки за считаные минуты. Сама мобильная смесительная башня поднимается на штатных гидродомкратах. Горячий элеватор перевозится на шасси смесительной башни и устанавливается в рабочее положение на поворотном шкворне. На борту завода XPRESS 2500 новая система управления Cybertronic Plus с модулями контроля за электропотреблением и управлением рециклингом, реализованная по принципу Smart Wiring. Электропроводка выполнена на штекерных разъемах, что существенно сокращает время монтажа/ демонтажа.
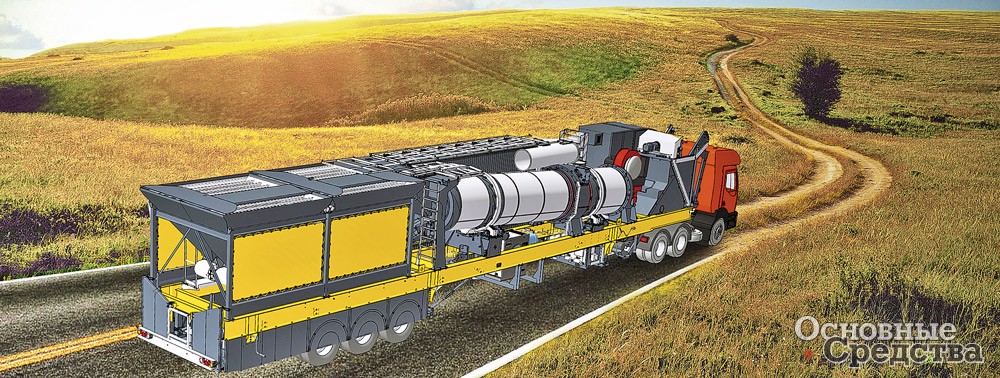
Французская компания MARINI-ERMONT (из той же группы FAYAT) в 2016 г. представила новую мод. RM120 ALLROAD из серии компактных АБЗ ROADMASTER. У RM120 ALLROAD в зависимости от комплектации производительность составляет от 50 до 120 т/ч. Завод способен использовать до 40% регенерированного асфальтобетона. Эта модель даже имеет собственный девиз: «Любой асфальт где угодно», так как благодаря самой совершенной системе дозирования может производить смеси любого состава.
Заметим, однако, что некоторые компании в США также предлагают АБЗ, способные использовать в смесях регенерированный асфальтобетон в больших процентных соотношениях.
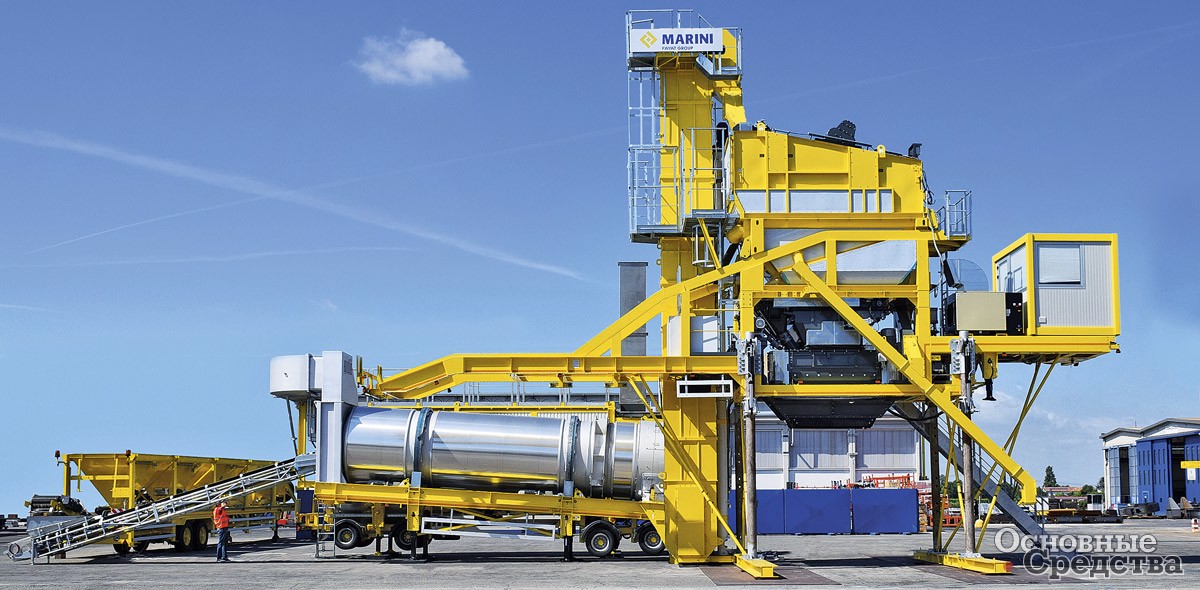
Американская компания Asphalt Drum Mixers Inc. предлагает асфальтобетонный завод EX120в качестве решения для строителей, которым нужен компактный АБЗ непрерывного действия, способный использовать в смеси большую долю регенерированого асфальта. Завод работает по противоточной технологии с отдельными зонами высушивания и перемешивания с одним барабаном. Это позволяет EX120 достигать максимальной теплопередачи и топливной эффективности. Данная технология обеспечивает минимальный уровень вредных выбросов сажи, которые являются широко распространенной проблемой АБЗ барабанного типа предыдущих поколений. Кроме того, компании ADM удалось еще больше снизить вредные выбросы за счет оригинальной конструкции противотока, в которой газы повторно подаются в зону сгорания барабана.
Производительность EX120 составляет 120 т/ч. Как утверждает компания, завод соответствует всем экологическим стандартам США. Это легко адаптируемый к любым нуждам потребителя асфальтовый завод, который можно перевезти в любое место, который производит материал с низкими затратами на тонну готовой продукции и высоким экономическим эффектом.
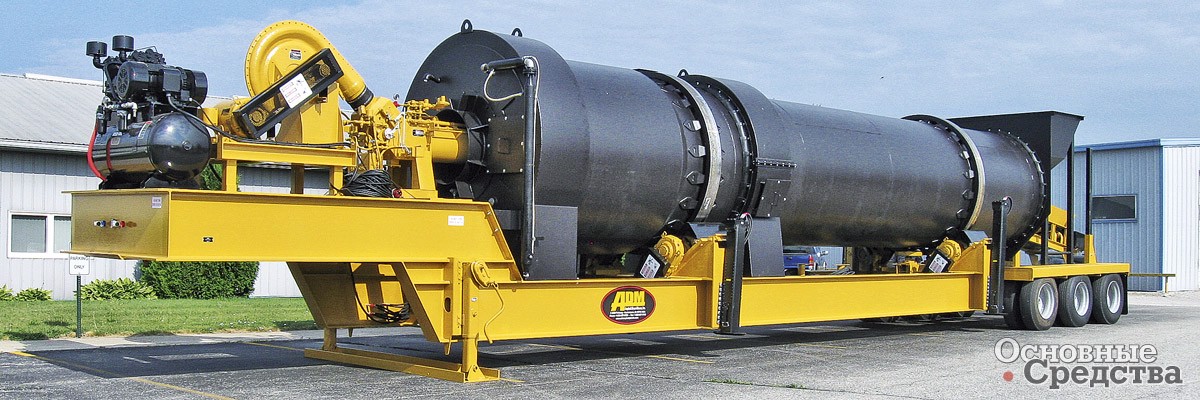
EX120 отличается самым длительным в своем классе временем высушивания инертных материалов и перемешивания, в результате этого затраты на тонну готовой продукции получаются очень низкими. Установка выдает непрерывный поток высококачественной асфальтовой смеси, появление некондиционного продукта исключено. Кроме того, АБЗ способен перерабатывать до 50% регенерированного асфальтобетона в составе исходного материала. АБЗ ADM серии EX имеют относительно небольшую производительность и оптимальную мобильность. Весь завод EX120 размещается на одном шасси, это упрощает его транспортировку, в том числе в отдаленные и труднодоступные места по всему миру. К тому же компактные размеры АБЗ и хорошая маневренность упрощают получение разрешения на работу по сравнению со стационарными заводами, поскольку предполагается, что мобильный завод будет работать лишь ограниченное время, а стационарный возводится надолго.
Возможности завода усовершенствованы, а система управления проста в использовании. Работу EX120 могут обеспечить один оператор установки и один оператор погрузчика. Компания заявляет, что завод рассчитан на надежную работу и простое техобслуживание. Большим преимуществом является широкая доступность запчастей. Покупатели могут самостоятельно комплектовать завод из широкого ассортимента компонентов, чтобы приспособить к своим конкретным задачам. ADM предлагает холодные дозаторы, барабаны с нефтяными горелками для подогрева асфальтобетона (горизонтальные и вертикальные), горизонтальные барабаны для подогрева смеси открытым пламенем, рукавные фильтры, системы подачи минеральных материалов, системы вторичной переработки асфальтобетона, самовозводящиеся и стационарные силосы; взвешивающие и скребковые конвейеры, бункеры-дозаторы и дополнительные баки для топлива.
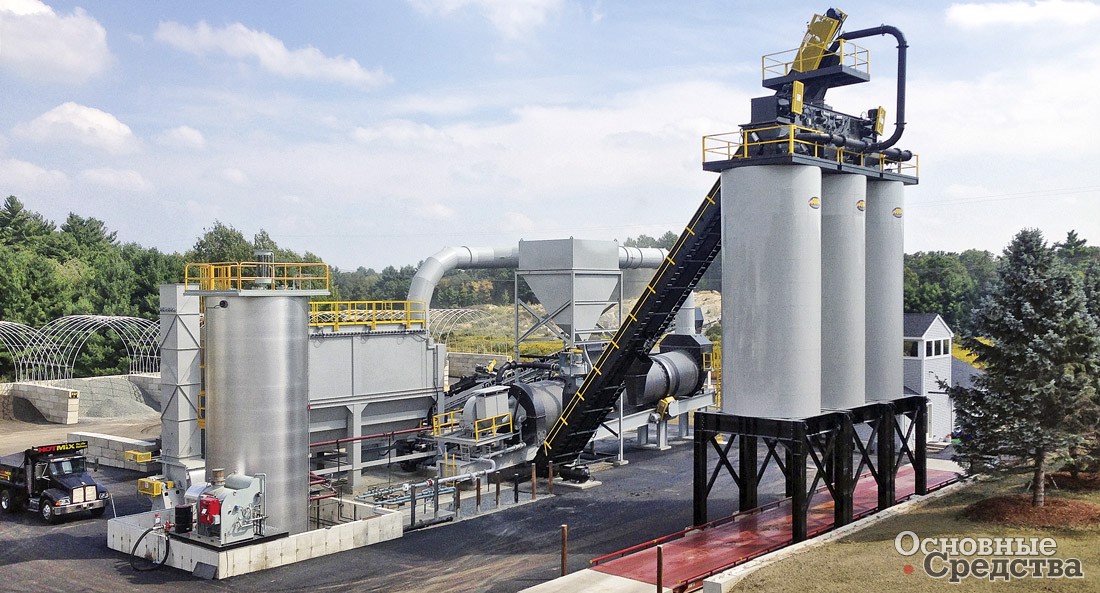
Повышение эффективности использования энергии
Строители-дорожники заинтересованы в экономии за счет улучшения энергоэффективности производства асфальтобетонных смесей. Один из способов сокращения энергозатрат на АБЗ – применение теплых асфальтобетонных смесей. Американская компания Astec Inc. разработала компактную высокоэффективную систему Double Barrel Green, которой может быть укомплектован любой новый или уже работающий смеситель противоточного действия Astec Double Barrel. Система служит для производства вспененного битума, применяемого вместо дорогостоящих компонентов при изготовлении теплого асфальтобетона. Double Barrel обеспечивает однородность смеси. Процесс происходит без доступа кислорода, за счет чего битум дольше сохраняется. Пары углеводорода из зоны смешивания подаются в зону пламени горелки. Установка предлагается в стационарном, полумобильном или мобильном исполнении. На вспененном битуме можно также производить и укладывать щебеночно-мастичный асфальтобетон (ЩМА) с температурой на 15–30 °С ниже обычной.
Компания Lintec GmbH & Co. KG выпускает АБЗ линейки CSD с сортировочно-сушильным барабаном. Эта запатентованная технология обеспечивает высокую энергоэффективность процесса. Сортировка выполняется в одном барабане одновременно с высушиванием и нагревом инертных материалов. Благодаря этому исключаются потери тепла при транспортировке минералов, тепло передается от оболочки барабана во время сортировки. К тому же уменьшается уровень шума. Производительность АБЗ линейки Lintec CSD составляет 80–240 т/ч в зависимости от модели.
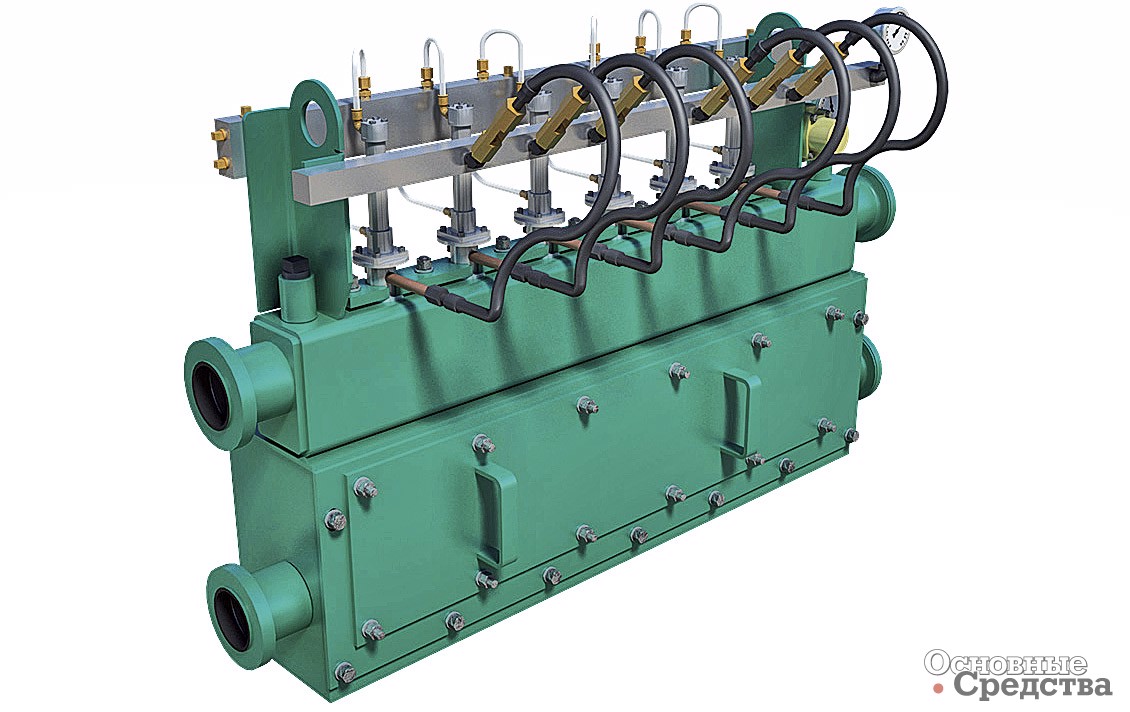
Выпуск асфальтобетонных смесей с усовершенствованными характеристиками
Работа по усовершенствованию свойств асфальтобетона никогда не прекращается. Разрабатываются все новые добавки для улучшения характеристик дорожного покрытия. В конструкции современных АБЗ предусматриваются возможности введения в смесь различных веществ на разных этапах производства.
Так, мало известная в России бразильская компания Ciber Equipamentos Rodoviarios (входит в Wirtgen Group), выпускает АБЗ под брендом Ciber по технологиям и лицензии Wirtgen, которые способны производить специальные асфальтобетонные смеси, а также работать с материалами разного качества, поступающими из разных источников.
Качество битума, поступающего от разных поставщиков, тоже может сильно отличаться, иногда требуется улучшить характеристики инертных добавок, которые должны соответствовать более жестким требованиям современных спецификаций, особенно для сортов асфальтобетона, предназначенных для эксплуатации в тяжелых климатических условиях или в условиях напряженного дорожного движения. Для решения проблем разносортности битумов в них могут вводиться полимеры и резиновая крошка, однако использование этих добавок может стать причиной осложнений в процессе производства. Технологи завода должны хорошо знать свойства различных сортов материалов и как на них влияют разные добавки, чтобы составлять высококачественные асфальтобетонные смеси, соответствующие заданным спецификациям.
На заводах Ciber имеются возможности перенастройки процесса и использования различных технологий, обеспечивающих успешное введение разных добавок в асфальтобетонные смеси: можно изменять скорость и время перемешивания, чтобы вяжущее успело распределиться и покрыть все частицы инертного материала, использовать принудительную рециркуляцию битума по системе, чтобы продукт оставался гомогенным и т. д. Для некоторых смесей может также потребоваться выполнить сначала сухое перемешивание. Кроме того, перемешивание и рециркуляция способствуют выравниванию температуры асфальтовой смеси в бункере, ускорению разогрева вяжущего и уменьшению расхода топлива при прогреве.
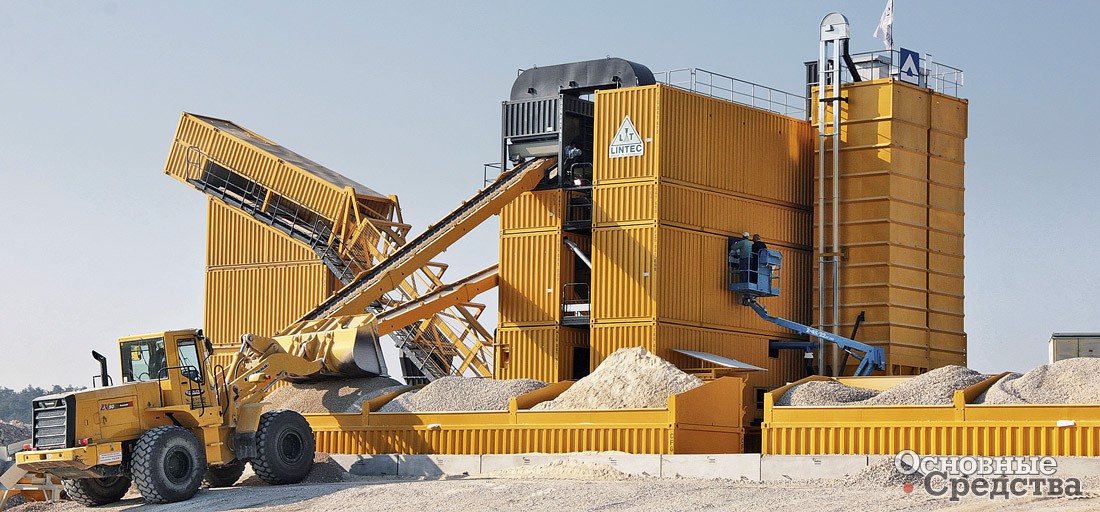
Модернизация АБЗ предыдущих поколений
Производство асфальта – давно устоявшийся рынок, на котором имеют шанс выйти в лидеры компании, способные раньше других понять новые запросы потребителей и откликнуться на них.
Так, в эксплуатации находится множество АБЗ прежних лет выпуска. Модернизация таких производств, приведение в соответствие с современными запросами клиентов – одна из тенденций сегодняшнего дня.
Уже упоминавшаяся компания Marini, идя навстречу пожеланиям клиентов, предусмотрела возможности модернизации находящихся в эксплуатации асфальтовых заводов путем оборудования новыми системами. Модернизация позволит увеличить производительность и качество изготавливаемых заводом материалов, а также выпускать новые сорта асфальтобетонных смесей. К тому же в результате модернизации можно улучшить экологичность завода и повысить безопасность труда на предприятии. Модернизация поможет также выполнить такие требования клиентов, как снижение температур асфальтобетонных смесей, использование вспененных и модифицированных битумов, а также добавок, например целлюлозного волокна, и внедрить другие новинки современных технологий в производстве асфальтобетонных смесей.
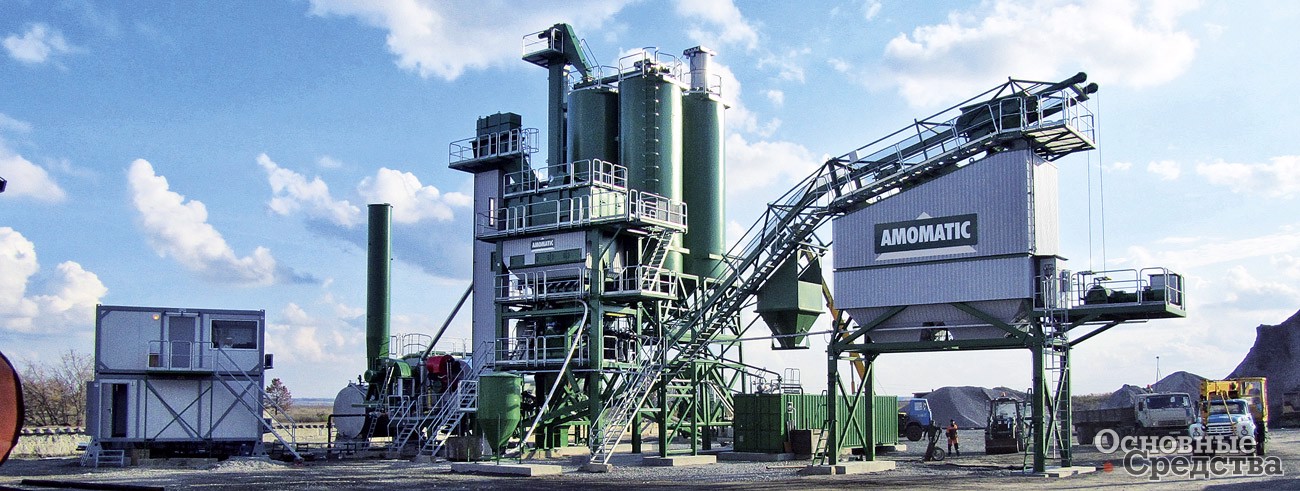
Одним из наиболее ярких примеров является успешная модернизация АБЗ MAP 260 в Италии, выполненная компанией Marini. Завод был построен в 1997 г. и позже неоднократно модернизировался, чтобы отвечать новым требованиям рынка. В 2004 г. площадь поверхности грохота была увеличена с 783 до 1096 м2, чтобы усовершенствовать процесс сортировки материалов, фильтрации и вторичного использования мелких частиц и пыли и улучшить контроль температуры на входе в фильтр. В 2007 г. количество холодных дозаторов было увеличено с 7 до 10, чтобы повысить возможности завода по приготовлению асфальтобетонных смесей нового состава. При заводе была оборудована специальная площадка для складирования материалов. Площадка имела водонепроницаемую поверхность, вода из атмосферных осадков собиралась с площадки и подавалась на завод (предварительно от нее отделялся песок и нефтепродукты).
В 2016 г. была установлена новейшая версия программного обеспечения Cybertronic 500 электронной системы управления заводом, которая позволяет более точно дозировать составляющие смеси. Благодаря внедрению нового программного обеспечения завод Marini MAP 260 стал выпускать смеси более точного состава по сравнению с другими асфальтосмесительными установками тех же лет выпуска и теперь может поставлять смеси такого же качества, что и АБЗ новейшего поколения. Это программное обеспечение также дало возможность провести модернизацию завода, и теперь он может применять при изготовлении смесей новейшие добавки в битум, точно дозировать составляющие с помощью гравиметрической системы взвешивания и подавать их непосредственно в момент загрузки битума. Теперь на АБЗ есть две отдельные линии дозирования, что также расширяет возможности его производства.
Асфальтобетонные заводы Teltomat во времена СССР были широко распространены в нашей стране и пользовались заслуженным признанием за хорошее качество работы. Некоторые из этих АБЗ работают до сих пор. Нынешний владелец бренда Teltomat – компания GP Gunter Papenburg AG. Некоторые российские компании предлагают провести модернизацию старых АБЗ Teltomat с внедрением электронного компьютерного управления и установкой новых контроллеров управления взвешиванием и смешиванием; фильтром очистки пыли; предварительным дозированием инертного материала; разгрузкой асфальта; горелкой и сушильными механизмами и т. д.
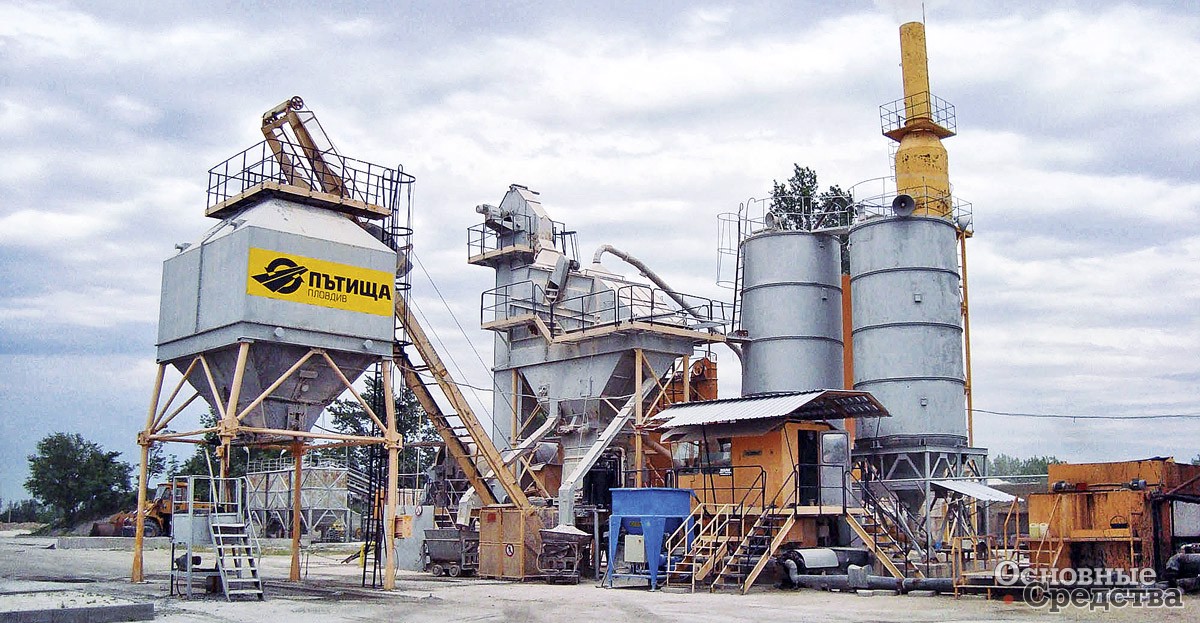
Повышение удобства перевозок и сокращение затрат на транспортировку
Специалисты утверждают, что за счет расположения модулей АБЗ в стандартных контейнерах можно сэкономить на затратах на перевозку до 75% средств. Перевозка АБЗ в контейнерах – это очень удобно и выгодно, если компании в ходе осуществления строительного проекта необходимо быстро перемещать АБЗ с одних объектов на другие, расположенные достаточно далеко.
Так, в 2017 г. финская компания Amomatic Oy представила мобильные приспособленные для перевозки в контейнерах АБЗ модульной конструкции серии СМ (Container Model) циклического действия, комплектации которых клиент может подбирать в зависимости от своих конкретных задач. Компоненты АБЗ размещаются в контейнерах стандарта ISO 1496-1, отвечающих требованиям норм безопасности CSC.
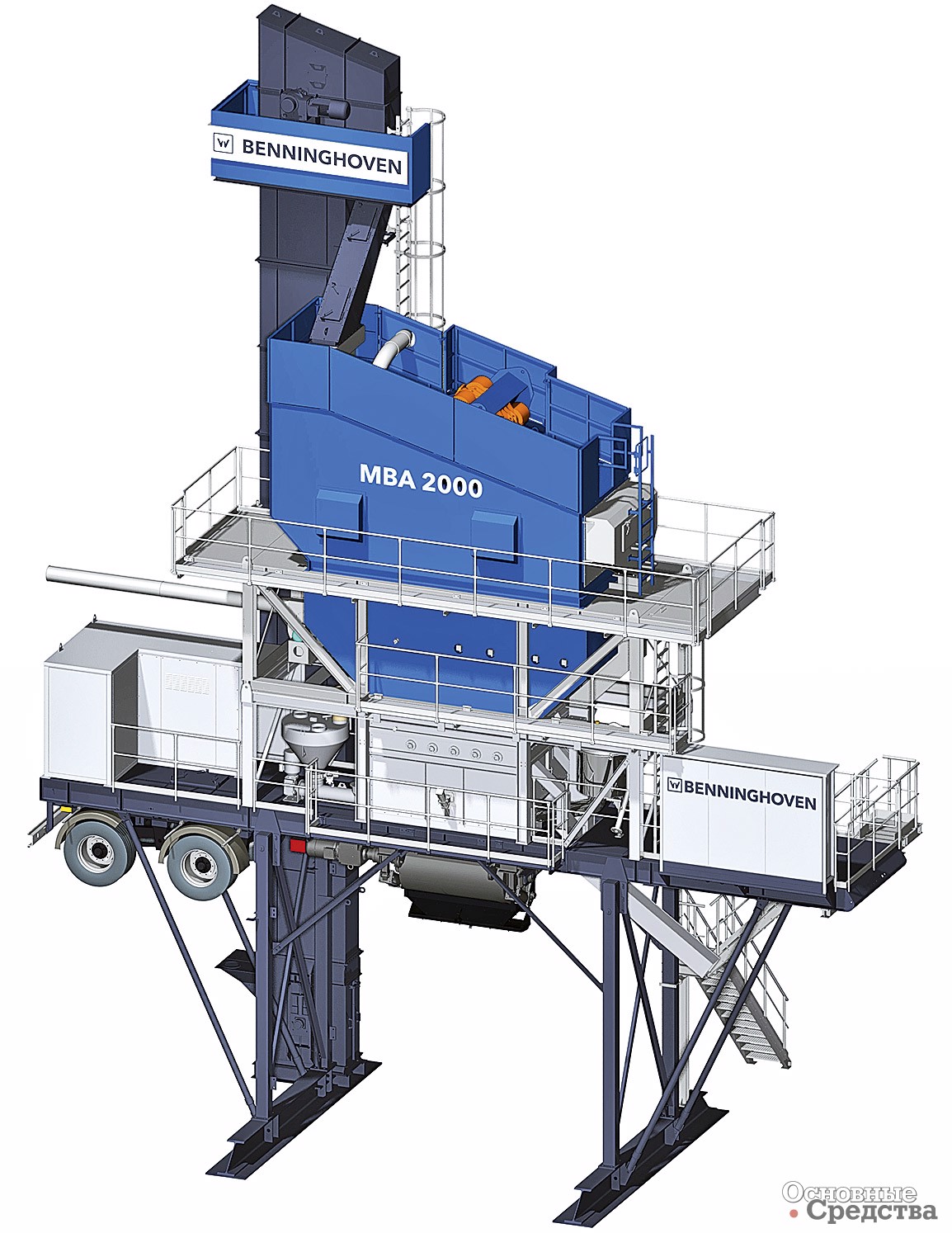
Надежность является одной из важнейших характеристик АБЗ финской компании, ведь они рассчитаны на эксплуатацию в короткие северные строительные сезоны, когда производство должно работать на полную мощность бесперебойно, без остановок на ремонт. В зависимости от комплектации производительность АБЗ составляет 120–160 т/ч. Заводы имеют электронную систему управления AmoControl с облачным хранением архивированных данных.
Конструкцией АБЗ серии СМ предусмотрена возможность использования регенерированного асфальтобетона. Инертные заполнители отделяются от битума, обе фракции сохраняются в накопителях для использования в дальнейшем при возведении дорожной насыпи и других объектов. АБЗ новой конструкции вызвали огромный интерес, поскольку они могут изменить порядок вторичного использования регенерированного асфальтобетона по всему миру.
Компания Benninghoven GmbH & Co. KG (входит в Wirtgen Group) также предлагает АБЗ типа ЕСО, рассчитанные на перевозку в стандартных 20- и 40-футовых контейнерах. Заводы оборудованы системой взвешивания на тензодатчиках, 2-вальным лопастным смесителем с теплоизолированными стенками. Производительность АБЗ серии ЕСО в зависимости от модели составляет от 100 до 320 т/ч.
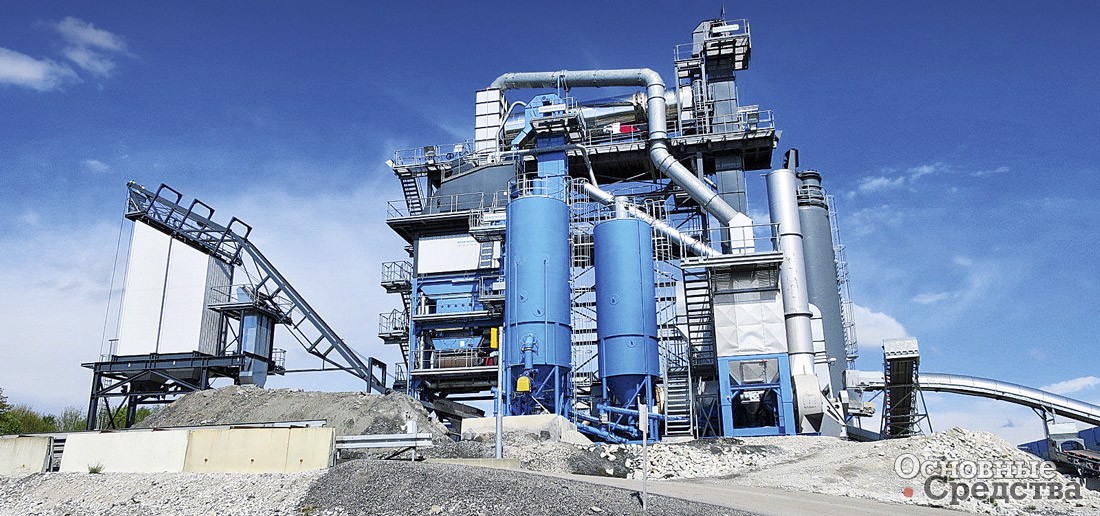
Английская компания Parker Plant Ltd производит высокотехнологичные мобильные асфальтобетонные заводы линейки Parker RoadStar производительностью 40 и 80 т/ч. Так, Parker RS500 – самый маленький мобильный асфальтный завод Parker из линейки RoadStar производительностью 40 т/ч циклического типа с замесом в 500 кг за цикл. Производит все виды асфальтобетонной смеси, в том числе ЩМА, ЩМС (щебеночно-мастичная смесь). Он смонтирован на двух мобильных шасси с пневматическим ходом. На первом шасси размещаются бункер инертных материалов, сушилка, горелка, на втором – кабина управления с большим цветным сенсорным экраном, фильтр, сортировочно-смесительная секция с элеватором горячего материала. Выгрузка готовой асфальтобетонной смеси производится прямо из-под смесителя. Все управление заводом происходит из кабины оператора. Завод полностью автоматизирован. Скорость запуска АБЗ в работу всего 4 часа после доставки на место. Требуется минимальная подготовка площадки. Каждая секция оборудована стабилизирующими аутригерами.
Итак, мы видим: для того, чтобы проявлять любовь и внимание к дорогам, промышленность дает дорожникам большие возможности. Остается только пожелать, чтобы они максимально использовали эти возможности. Ведь если ремонт выполняется с опозданием, а не своевременно в плановом порядке, стоимость его возрастает во много раз. И еще: хотелось бы, чтобы в нашей стране опять появились собственные производители АБЗ.
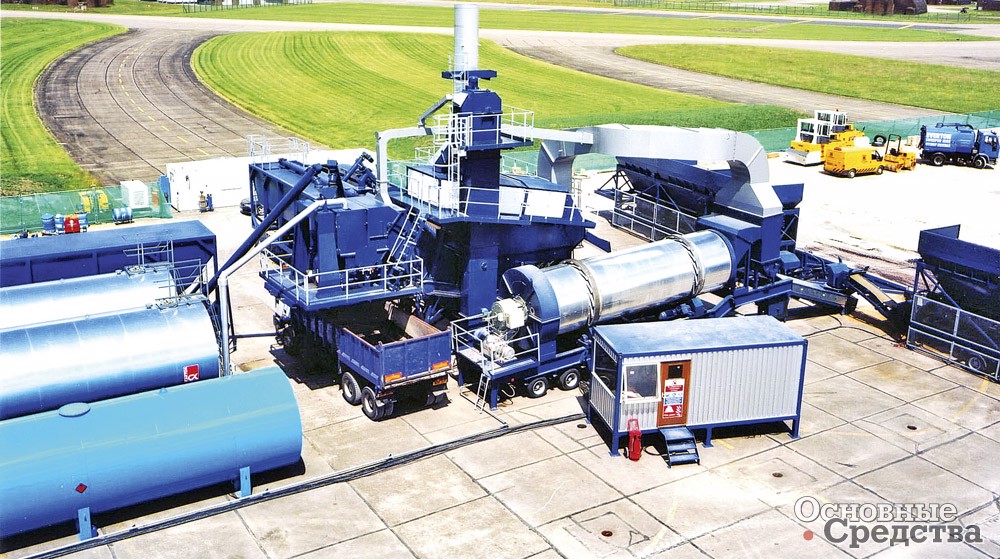
os1.ru
Использование инновационных методов производства асфальтобетонной смеси без увеличения сметной стоимости проекта Текст научной статьи по специальности «Экономика и экономические науки»
УДК 625.8+625.08
А.Н. Кузьмин
главный механик, АО «ДП Ижевское»
П.Е. Манохин
канд. техн. наук, доцент, кафедра «Промышленное и гражданское строительство», ФГБОУ ВО «Ижевский государственный технический университет имени М.Т. Калашникова»
ИСПОЛЬЗОВАНИЕ ИННОВАЦИОННЫХ МЕТОДОВ ПРОИЗВОДСТВА АСФАЛЬТОБЕТОННОЙ СМЕСИ БЕЗ УВЕЛИЧЕНИЯ СМЕТНОЙ СТОИМОСТИ ПРОЕКТА
Аннотация. Методы по улучшению выпускаемого на асфальтобетонном заводе асфальтобетона с применением различных добавок и материалов. Изучение их преимуществ и недостатков, сравнение и выбор наиболее предпочтительного для конкретного предприятия и проекта.
Ключевые слова: инновации, автомобильные дороги, асфальтобетон, полимербитум.
A.N. Kuzmin, JSC «Izhevsk DP»
P.E. Manokhin, Ph.D., Kalashnikov Izhevsk State Technical University
THE USE OF INNOVATIVE METHODS FOR THE PRODUCTION OF ASPHALT MIX WITHOUT
INCREASING THE COST OF THE PROJECT
Abstract. Methods for improving produced at asphalt plant of asphalt concrete using different admixtures and materials. Study their advantages and disadvantages, comparing and selecting the most preferred for a particular company and project.
Keywords: innovation, road, asphalt, polimerbitum.
В данной статье описываются методы улучшения физических свойств асфальтобетонной смеси в рамках заложенного бюджета проекта на примере реконструкции автодороги «Ижевск-Сарапул».
В настоящее время существует ряд методов улучшения физических свойств асфальтобетонной смеси, с помощью которых возможно увеличение срока службы покрытия. На сегодняшний день, пожалуй, наиболее действенный метод - это улучшение основания, базиса, производство его по самым передовым технологиям, что гарантирует увеличение срока службы на 20-25 лет. В условиях кризиса и жесточайшей экономии выделяемых бюджетных средств стоит задача найти методы, позволяющие поддерживать дорожное покрытие в удовлетворительном состоянии без капитальных вложений, с уменьшением затрат на содержание (ямочный ремонт, заливка трещин и т.п.). Тем самым высвободившиеся средства в дальнейшем аккумулировать в капитальное строительство автодорог.
Мы же рассмотрим методы, позволяющие провести улучшения, изменяя только состав самого асфальта, без существенных изменений технологии и способов укладки.
1. Выбор более качественного щебня и песка
Основным компонентом для приготовления асфальтобетонной смеси является щебень, т.к. от его качества зависит свойство асфальта и, как следствие, дорожного покрытия, а именно коэффициент сцепления колес, долговечность и прочность асфальта. Вместе с тем стоит отметить дефицит качественного щебня в России, который бы удовлетворял параметрам для приготовления высококачественного асфальта. Сегодня не весь щебень, производимый в нашей стране, применим при изготовлении асфальта, ввиду отсутствия необходимых характеристик, таких как прочность, адгезия с битумом, кубовидность и пр. Практика показывает, что требования, предъявляемые к щебню для приготовления асфальта, выше, чем того, который используется на общестроительных работах.
Такая ситуация является следствием того, что при открытии новых карьеров по добыче
щебня зачастую невозможно со 100% достоверностью определить, какого качества щебень будет на выходе. Такие ошибки, как правило, обнаруживаются уже в процессе промышленной добычи материала и становятся необратимыми [1].
2. Использование полимерных порошков-добавок при производстве асфальтобетона
Основное назначение поверхностно активных веществ заключается в предотвращении
уменьшения и исчезновения эффекта адгезии между материалом (щебень) и битумом. Такое происходит в процессе все более усиленной эксплуатации автодорог и атмосферных воздействий, что в конечном итоге приводит к разрушению верхнего слоя дорожной одежды в виде трещин и выкрашивания. Вышеперечисленные поверхностно-активные вещества (ПАВ) призваны улучшить адгезионные свойства асфальта, т.е. битум более плотно обволакивает щебень, что приводит к улучшению свойств асфальтобетонных смесей и, как следствие, дорожного полотна [2].
В данном случае мы также столкнемся с удорожанием проекта по причине отсутствия на рынке сколько-нибудь достойных заменителей полимеров отечественного производства. На сегодняшний день мы имеем отечественные продукты, такие как АМДОР-9, ДОРОС АП, БП-КСП, БП-3М, Азол1001, которые сильно уступают своим импортным аналогам.
3. Использование порошка и резиновой крошки
Существует также метод добавления к традиционному асфальту порошка, изготовленного на основе резиновой крошки, которую можно приготовить из старых автомобильных покрышек, шлангов и т.п. Однако расчеты показывают, что при выпуске 1500 тонн асфальта в сутки в радиусе 100 км мы не сможем найти такого количества, свободного от какого-либо посягательства резинотехнических изделий бывших в употреблении.
Еще один значительный недостаток такого метода в том, что мы не можем спрогнозировать процесс поступления необходимого количества резиновой крошки на асфальтобетонном заводе (АБЗ). При этом улучшение физических свойств асфальтобетонной смеси при использовании данной технологии дает улучшение ее свойств в целом всего на 2%, что подтверждено испытаниями экспериментальных образцов лабораторией ДП «Ижевское».
Таблица 1 - Сравнительный анализ БНД 60/90 с добавлением ВРБ УйаКиЫх-Г
№ п /п Наименование показателей ГОСТ 31015-2002 БНД 60/90 БНД 60/90 + ВРБ УйаКиЫх-Г
1 Средняя плотность, г/см3 не норм 2,46 2,46
2 Водонасыщение,% по объему от 1,0 до 4,0 2,9 2,3
3 Предел прочности при сжатии (МПа)
20°С не менее 2,2 2,6 3,0
50°С не менее 0,65 0,80 0,94
4 Сдвигоустойчивость
коэфф. внутреннего трения не менее 0,93 0,93 0,93
сцепление при сдвиге 50°С, МПа не менее 0,18 0,23 0,25
5 Трещиностойкость 0°С, МПа не менее от 2,5 до 6,0 4,3 4,17
6 Стекание вяжущего не более % 0,2 0,01 0,002
Данные, указанные в протоколе, распространяются только на пробы № 200716/1 и № 200716/2 от 20.07.16 года *
За основание составов был взят состав 21-1 без учёта изменившихся материалов. При использовании модификатора гранулированного вяжущего резинобитумного (ВРБ) УйаКиЫх-Г физико-механические свойства а/б улучшаются. По указанным показателям соответствуют требованиям ГОСТ 31015-2002. Для принятия решения о дальнейшем использовании модификатора гранулированного вяжущего резинобитумного (ВРБ) УйаКиЫх-Г рекомендуем провести тщательный подбор состава и укладку пробного участка покрытия.
Необходимо отметить и тот факт, что химический состав авторезины у производителей отличается и который никому не известен в силу объективных причин. Поэтому спрогнозировать физические параметры каждой партии асфальтобетона не представляется возможным, а тем самым нельзя гарантировать стабильность выпускаемого асфальтобетона на АБЗ.
4. Применение полимермодифицированного битума
Перейдём к битуму, который является, пожалуй, самым важным компонентом в асфальтобетонной смеси. На сегодняшний день ситуация на рынке битумов такова, что импортные образцы битума позволяют применять практически любой щебень без потери качества асфальтобетона. Это связано с тем, что европейские заводы по производству битума ориентированы на производителей асфальтобетона. В нашей стране всё с точностью до наоборот. Весь битум у нас выпускают буквально несколько нефтеперерабатывающих заводов (НПЗ), и выбор здесь невелик.
Отсюда возникает производство битума с добавлением полимеров или полимербитум-ных вяжущих (ПБВ) добавок, в которых используется трехблочный сополимер в качестве основного компонента. Концентрация этой добавки достигает до 6,5% от массы битума. С добавлением ПБВ достигается более высокая упругость, сопротивляемость деформации, снижение хрупкости при отрицательных температурах, которая присуща эластомерам. Это в итоге приводит к повышению такого важного показателя асфальтобетона, как сдвигоустойчивость, при повышении температуры окружающего воздуха [2].
Но и этот метод также ведёт к удорожанию проекта, т.к. стоимость полимермодифицированного битума на 60% выше обычного. Вместе с тем его использование в производстве асфальтобетонной смеси позволит увеличить межремонтный интервал автодороги. При улучшении физических характеристик на 5% можно достичь увеличения срока службы дорожного полотна до 2,5 раз.
5. Вывод
Все методы ведут к существенному удорожанию выпускаемой продукции от 15 до 30%. Однако, если не покупать полимермодифицированный битум, а производить его самим, с использованием соответствующих добавок в виде порошка, стоимость которых не столь критична по сравнению с готовым продуктом, то можно добиться того, что смета затрат будет вполне приемлемой. Учитывая, что это будет являться долгосрочным вложением, можно определить ряд преимуществ, которые АО «Дорожное предприятие «Ижевское» может получить в дальнейшем:
- получение полного законченного технологического цикла выпуска полимермодифицированного битума, который можно использовать на всех проектах, независимо от проектной документации;
- значительное уменьшение стоимости затрат по гарантийным обязательствам и по содержанию дорожного покрытия с использованием данного метода;
- возможность продажи готовой асфальтобетонной смеси на рынке, используя конкурентное преимущество по более высокой стоимости, нежели стандартный продукт.
Все эти аспекты помогут покрыть те разовые издержки на переход по выпуску полимермодифицированного битума и через достаточно непродолжительное время получать дивиденды от своих вложений.
Список литературы:
1. Данилов Д.Ю. Пути повышения качества асфальтобетона. Режим доступа: http: //www.newchemistry.ru/printletter.php?n_id=5422 (дата обращения: 29.11.2016).
2. Петровский В.Н. Пути повышения качества асфальтобетона. Режим доступа: http: //www.newchemistry.ru/printletter.php?n_id=5422 (дата обращения: 29.11.2016).
cyberleninka.ru
Асфальтовые заводы России - 12 предприятий
Производство асфальтобетонной смеси, как самостоятельного сегмента промышленного производства, развилось сравнительно недавно. С развитием нефтеперерабатывающей промышленности стала возможной замена природного битума (иудеской смолы) продуктами перегонки (крекинга) нефти. Производство асфальта, не смотря на кажущуюся простоту, достаточно сложный технологический процесс, требующий качественных технических решений и строгого соблюдения технологических режимов.
В основе производства смеси лежит процесс обволакивания природного камня определенной фракции (щебня) битумом. При добавлении минеральной присадки (бетона) создается асфальтобетонная смесь, из которой получается другой тип покрытия. Бетон добавляется в виде раствора или в виде измельченных отходов бетонного производства. О важности соблюдения технических условий производства говорит приведение ГОСТа 9128-2009 в соответствии с европейскими стандартами и обязательное применение его семью государствами СНГ.
Основным признаком градации асфальтобетонных заводов является производительность (объем/вес смеси в единицу времени), которая влияет на компоновку и размещение завода. Различают следующие типы заводов.
Стационарные заводы
Производительность таких заводов составляет десятки/сотни тонн в час. Они используют многобункерные системы приготовления смеси с автоматизированными системами дозирования (транспортировки) исходных и готовых материалов. Высокий уровень автоматизации процессов позволяет учитывать суточные, погодные и сезонные колебания потребностей дорожников в рабочей смеси. Выбор места размещения такого завода — серьезная технико-экономическая задача, требующая учета многих факторов: от стоимости и доступности сырья (энергии и т.п.), до решения логистических (транспортных) задач.
Передвижные заводы
Предназначены для обеспечения строительства дорожных объектов большой протяженности на достаточном удалении от крупных промышленных узлов. Это уменьшенная копия стационарного завода модульного типа, в конструкции которого предусматривается возможность демонтажа и переноса на подготовленную площадку. Степень механизации и автоматизации технологических процессов находятся на уровне стационарных, как и требования к качеству продукции. Передвижные заводы — это наиболее гибкая и эффективная модель производства, способная решать большинство задач дорожного строительства.
Мобильные заводы
Это вариант передвижного завода. Отличие заключается в оснащении модулей завода собственными колесами, которые позволяют перевозить завод тягачами без применения дополнительной техники (платформ). Применяется для решения задач локального значения.
Асфальтобетонные заводы любой модели — очень перспективные объекты для инвестирования, но требуют серьезной проработки в плане оценки перспектив развития дорожной сети в каждом конкретном случае применительно к региону.
www.wiki-prom.ru