Морозостойкость и факторы, влияющие на морозостойкость. Морозостойкость формула
Морозостойкость и факторы, влияющие на морозостойкость. — МегаЛекции
Классификация свойств стройматериалов.
Свойства-это характеристика материала или изделия, к-рая проявляется в процессе преработки, применении эксплуатации. Способность материалов определенным способом реагировать отдельно или в совокупности с другими факторами ( внешними и внутренними). Свойства : простые и сложные. Простые нельзя разделить. Свойства зависят от структуры материала.
Свойства: Функциональные ( эксплуатационно-технические и технологические), Эстетические( АРх- художественные(форма, размер, блеск, цвет, текстура)), Технико-Экономические.
Эксплуатационно-технические: *физичексие(структурные(истинная плотность, средняя плотность, пористость, насыпная плотность, пустотность,водопоглащение,водостойкость, влагостойкость, влажность, влагоотдача, гигроскопичность, проницаемость, морозостойкость, огнестойкость, аккустика), гидрофизичекские и теплофизические), *механические(прочность, твердость, истираемость и т.д.), *химические(характеризуют способность материала сопротивляться агрессивным средам(бензостойкость, маслостойкость, кислотостойкость, щелочестойкость), *биологические (свойство материала сопротивляться разрушению от отдельных видов растений и др.видов живых организмов ЗАВИСЯТ: от влажности. Пористости, структуры и плотности), *технологические(способность подвергаться обработке(распиловка, дробимость, полируемость, укрывистость, гвоздимость, удобоукладываемость. ВЛИЯНИЕ: на качество и стоимость материала), *комплексные(ДОЛГОВЕЧНОСТЬ(способность сопротивляться действию атмосферных и др. факторов, СОВМЕСТИМОСТЬ: способность образовывать прочную конструкцию и способность долго сохранять свои функции, НАДЕЖНОСТЬ: выполнение своих функций )
Структурные свойства материалов: истинная средняя плотность.
Средняя плотность – это масса единицы объема материала в естественном состоянии(с пустотами и порами). Зависит от структуры и влажности.
Истинная плотность – это масса единицы объема материала в абсолютно плотном состоянии, т.е. без пор и пустот, и трещин…
Структурные свойства материалов: пористость и пустотность.
Пористость материала-это степень заполнения его объема порами. Эта характеристика влияет на эксплуатационные свойства(теплопроводность, морозостойкость, водопоглощение, водонепроницаемость, прочность, звукопроводность).
Пористость зависит от технологии получения материала.
Пористость метериала-это отношение объема его пор на его объем в естественном состоянии. Пустоты – это поры объем которых более 2 мм.
Пустотность – это масса сыпучего материала вместе с его пустотами.
Гидрофизические свойства - водопоглощение.
Водопоглощение – это способность материала впитывать в себя воду и удерживать ее при непосредственном соприкосновении с ней. Водопоглощение оценивают количеством воды, поглощенной образцом из материла при выдерживании его в воде в течении заданного времени, выраженным в процентах в %. Водопоглощение по массе – это поглощенное количество воды на, отнесенное к его(материала) массе. Водопоглощение по объему - … отнесенное к его объему.
Соотношение между водопоглощением по массе и по объему это и есть средняя плотность материала в сухом состоянии.
ВОдопоглощение зависит от пористости, продолжительности насыщения, скорости погружения в воду, от размера пор. Применяют медленное погружение при кипячении для ускорения.
Влияет на плотность, теплопроводность, прочность.
ВОдопоглощение по массе = 0…180%
Водопоглощение по объему всегда меньше 100%!!!
Гидрофизические свойства – влажность и влагоотдача.
Влажность – это содержание влаги в материале в естественно влажном состоянии, отнесенное к массе материала в сухом состоянии, выраженное в процентах.
Влажность всегда меньше водопоглощения.
Влагоотдача – свойство материала отдавать влагу окружающей среде или - это выделение влаги из материала при определенных условиях (температура, давление, движение воздуха). Зависит от структуры материала.
Влажность и водопоглощение влияют на прочность, теплопроводность и плотность.
Гидрофизические свойства – водостойкость и влагостойкость.
Водостойкость – способность материала сохранять плотность при увлажнении. Характеризуется коэффициентом размягчения.
Влагостойкость – способность материала длительно сопротивляться разрушающему действию влаги при периодичном увлажнении и высыхании.
Гигроскопичность и паропроницаемость.
Гигроскопичность – это способность материала поглощать влагу из окружающей среды. Материалы которые притягивают своей поверхностью влагу называются гидрофильными, а которые отталкивают – гидрофобными.
Мелкопорные материалы – большая гигроскопичность (сахар, цемент, соль)
Влияет на теплопроводность материала.
Паропроницаемость – свойство материала пропускать сквозь себя жидкости, воздух, газ.(флюиды). И выражаются в общем виде: количеством флюида, проходящего за единицу времени через единицу поверхности материала заданной толщины при перепаде давления.
Зависит от пористости(размера, количества, характера) от поверхности и ее толщи.
Морозостойкость и факторы, влияющие на морозостойкость.
Морозостойкость – сложное свойство, характеризующее способность материала, поглощенного водой, выдерживать многократное замораживание и оттаивание без признаков разрушения и снижения прочности. F35, 50… 500. (марка)
Зависит от пористости, формы и размера пор и степени насыщения их водой.
Чтобы увеличить морозостойкость надо уменьшить пористость и увеличить прочность.
megalektsii.ru
Свойства строительных материалов — Материалы и свойства
Удельный вес — вес единицы объема материала в абсолютно плотном состоянии (без пор и пустот)
где G — вес материала в сухом состоянии в г,
V — объем материала в см3.
Объемный вес — вес единицы объема материала в естественном (вместе с порами) состоянии. Для сыпучих материалов (песок, щебень и т. д.), кроме того, определяют насыпной объемный вес — вес единицы объема вместе с пустотами между зернами материала. Объемный вес можно определять в сухом состоянии или при определенной влажности
где G — вес материала,
V — объем мерной посуды (материала).
Плотность — степень заполнения объема материала твердым веществом — выражается обычно в процентах:
Пористость — степень заполнения объема материала порами:
Пустотность (межзерновая) рыхлых материалов (песок, щебень) определяется по той же формуле, но вместо ?y берут объемный вес «в куске», a ?0 — насыпной объемный вес.
Водопоглощение — степень заполнения объема материала водой:
объемное водопоглощение
весовое водопоглощение
где G1 — вес материала в сухом состоянии,
G2- вес материала в насыщенном водой состоянии,
V — объем материала.
Водопоглощение определяют постепенным погружением в воду высушенного до постоянного веса и охлажденного образца. Полное водопоглощение определяют кипячением.
Отношение прочности материала, насыщенного водой, к прочности сухого материала называется коэффициентом размягчения:
Сорбционная влажность — влажность за счет поглощения материалом водяных паров из воздуха. Сорбционную влажность определяют увлажнением высушенных образцов в эксикаторах с определенной влажностью, поддерживаемой раствором серной кислоты. Для получения влажности в 40—60—80—97% при t = 20°C применяется серная кислота концентрации соответственно в 45, 37, 24 и 5%. Гигроскопичность (частный случай сорбционной влажности) — увлажнение материала после пребывания в течение 10 суток в воздушной среде с 100-процентной относительной влажностью при t = 18—20°.
Морозостойкость — способность насыщенного водой материала выдерживать многократное замораживание при t = 17—20° и оттаивание при t= 15—25°
Морозостойкость материала характеризуется числом циклов попеременного замораживания и оттаивания водонасыщенных образцов, которое они выдерживают до снижения прочности до 25% и потери веса до 5% (для крупного заполнителя бетона допустима потеря в весе до 10%)
В зависимости от назначения и климатических условий каменные материалы должны выдерживать 10—15—25 и более (до 300) циклов замораживания и оттаивания.
Ориентировочные данные по морозостойкости глиняного кирпича и некоторых других материалов можно получить по методу определения коэффициентов морозостойкости:
где Bx —водопоглощение материала при комнатной температуре,
Bk — водопоглощение при кипячении в течение 4 часов.
Материал считается морозостойким, если К < 0,85.
Ускоренные испытания морозостойкости каменных материалов можно производить погружением образцов в насыщенный раствор сернокислого натрия на 20 часов и высушиванием при t=105—110°
Насыщение и высушивание производят 4—5 раз, что соответствует 15—25 циклам замораживания и оттаивания.
Морозостойкость материала можно определить без разрушения по снижению динамического модуля упругости. К ускоренным методам испытаний на морозостойкость относится замораживание в жидкой среде.
Таблица 43
Удельный и объемный веса и коэффициент теплопроводности основных строительных материалов
Наименование материалов | Удельный вес г/см3 | Объемный вес в сухом состоянии в кг/м3 | Коэффициент теплопроводности в ккал/мчасград |
Артикский туф | 2,8 | 800-1400 | 0,16-0,28 |
Асбестоцементные плитки | 2,5 | 1600-1900 (м2-11кг) | 0,30 |
Асфальтобетон | 2.6 | 2000-2200 | 0,75 |
Базальт | 3,3 | 2700-3200 | 1,6-3 |
Бетон на гравии или шебне | 2,6 | 2000 — 2250 | 0,85-1,4 |
Бетон на кирпичном щебне | 2,6 | 1800-2000 | 0,6-1 |
Бетон на шлаке | 2,6 | 1400—1600 | 0,30-0,70 |
Бетон ячеистый (пенобетон, пеносиликат) | 2,8 | 400- 1200 | |
Береза | 1,6 | 500-600 | 0,15 |
Бут-известняк (обмер в штабелях) | 2,6 | 1300-1400 | 1,1 |
Битумно-опилочпые плиты . | — | 30)-400 | 0,10 |
Войлок в кипах | 1,7 | 200—300 | 0,05 |
Газогипс | 2,7 | 500 | 0,12 |
Гипс в изделиях | 2,7 | 700-1300 | 0,2-0,38 |
Гипсобетон | 2,6 | 1000—1300 | 0,30 |
Гипсовая сухая штукатурка | — | 1000 | 0,25 |
Глина | 2,7 | 1600 — 1800 | 0,50 |
Гравий | 1000-1800 | 0,40 | |
Граниты | 3,0 | 2500-2900 | 3,0 |
Древесно-волокнистые плиты | 1,7 | 150-60J | 0,05-0,11 |
Дуб | 1,65 | 700- 900 | 0,1 -0,20 |
Железобетон | 2,9 | 2400—2500 | 1-1,40 |
Земля сухая (растительная) | 1200-1400 | 0,35 | |
Зола | 700-900 | 0,17 | |
Известняки тяжелые . | 2,6 | 1600 -2100 | 0,45—0,86 |
Известь- кипелка | 2.6 | 600- 1400 | — |
Известняки-ракушечники | 2,6 | 1100 — 1600 | 0,25-0,4 |
Известь-пушонка | 2,6 | 450-550 | _ |
Известковое тесто | 1000-1400 | — | |
Камни шлакобетонные пустотелые (обмер в штабелях) | — | 1200-1300 | 0,50-0,70 |
Камышит | — | 250 400 | 0,10 |
Картон | 1,6 | 250-500 | 0,09 |
Керамзит (гравий) | 2,6 | 300 — 900 | 0,13-0,35 |
Керамзитобетон | 2,6 | 800-1400 | 0,25-0,45 |
Керамические блоки . | 2,7 | 1900 — 2200 | 0,5 -1 |
Кирпич глиняный обыкновенный | 2,7 | 1600—1900 | 0,4 -0,58 |
Кирпич глиняный пористый | 2,7 | 600-1400 | 0,14-0,32 |
Кирпич силикатный | 2,6 | 1800- 2000 | 0,75 |
Кирпич трепальный . | 2,7 | 700-1300 | 0,19-0,29 |
Кирпичная кладка | — | 1400-1900 | 0,50-0,75 |
Ксилолит | 2,4 | 900— 1800 | 0,25-0,6 |
Лес хвойный полусухой | 1,6 | 650-700 | 0,16-0,23 |
Мипора | — | 15-20 | 0,03 |
Минераловатные плиты жесткие | 2,8 | 300-500 | 0,08—0,12 |
Мрамор | 2,9 | 2600- 2800 | 3,0 |
Мусор строительный . | — | 1200-1400 | 0,35 |
Опилки древесные | 1,6 | 200-300 | 0,04-0,06 |
Опока | 2,6 | 1300-1800 | 0,30-0,80 |
Пенопласт | 1,4 | 70-190 | 0,04-0,045 |
Пенокералит | 2,7 | 350-500 | 0,07-0,17 |
Пеностекло (газостекло) . | 2,6 | 300-500 | 0,1 -0,14 |
Песчаник | 2,6 | 1800 — 2400 | 0,7 -1,40 |
Песок речной | 2,6 | 1500-1700 | 0,40-0,50 |
Растворы известково-песча- ные | 2,8 | 1600—1809 | 0,46-0,60 |
Растворы легкие (шлаковые) | 2,6 | 1200-1400 | 0,30-0,40 |
Стекло | 2,6 | 2500 | 0,65 |
Стеклянная вата | 2,7 | 150-200 | 0,04 |
Соломит | 1,4 | 150—250 | 0,06 |
Сосна | 1,6 | 500—600 | 0,15 |
Трепел (диатомит) | 2,7 | 600 | 0,15 |
Торфоплиты | 1,5 | 150-250 | 0,065 |
Фанера | 1,6 | 575-650 | 0,15 |
Фибролит на цементе . | 350-850 | 0,06-0,15 | |
Цемент | 3,1 | 1000- 1400 | |
Шлак гранулированный | 3,3 | 300-700 | 0,08-0,12 |
Шлак котельный | 2,7 | 700-1300 | 0,16-0,30 |
Шлаковая вата | 3,3 | 200 400 | 0,04-0,06 |
Щебень из плотных пород | 2,6 | 1600-1800 | _ |
Щебень известняковый . | 2,6 | 1300-15?0 | — |
arxipedia.ru
Испытание на морозостойкость — Материалы и свойства
Учитывая, что морозостойкость играет решающую роль, в длительности службы природных каменных материалов, при оценке долговечности, камня обычно пользуются показателями морозостойкости. Согласно ГОСТ 9479-84 на морозостойкость должны испытываться все породы, предназначенные для использования в наружных облицовках.
Определение морозостойкости камня производят на образцах кубической формы с ребром 40 – 50 мм или цилиндрах диаметром и высотой 40—50 мм. Вначале образцы в течение 48 ч выдерживают в воде при температуре 20 °С, затем помещают в холодильную камеру, доводя в ней температуру до минус 17 ‑25 °C (длительность выдержки 4 ч). После этого промороженные образцы помещают в воду с температурой 20 °С и выдерживают при этой температуре до полного оттаивания, но не менее 2 ч. Далее цикл повторяется. После 15, 25 и 50 циклов замораживания и оттаивания по 5 образцов испытывают на сжатие.
Потерю прочности Δ,(%) образцов вычисляют по формуле
∆ = (Rсж – R»сж) / Rсж 100,
где Rсж и R»сж – средние арифметические значения предела прочности при сжатии пяти образцов соответственно в насыщенном водой состоянии и после испытания их на морозостойкость, МПа.
Если среднее значение величины потери прочности пяти образцов при сжатии после попеременного их замораживания и оттаивания не превышает 20 % при установленном количестве циклов (табл. 3 ГОСТ 9479—84), то горная порода отвечает соответствующей марке по морозостойкости. При величине потери прочности свыше 20 % испытываемый камень не отвечает соответствующей марке по морозостойкости.
Методика испытания материалов на морозостойкость
Методика испытания материалов на морозостойкость впервые предложена в 1886 г. русским ученым Н. А. Белелюбским, основавшим первую в России лабораторию строительных материалов.
Для используемого в наружных облицовках камня действующим стандартом установлена следующая минимальная морозостойкость: граниты и аналогичные изверженные породы, а также кварциты и гнейсы – 50 циклов; мраморы, мраморизован- ные известняки, пористые базальты, песчаники, плотные доломиты, травертины, пористые известняки и туфы вулканические – 25 циклов; туфы фельзитовые и известняки- ракушечники – 15 циклов.
Пригодность камня изверженных пород для производства облицовочных материалов, применяемых в конструкциях, которые соприкасаются с грунтом (цоколи, парапеты и т. п.), в соответствии с упомянутым выше стандартом оценивается путем испытания образцов в растворе сернокислого натрия. Высушенные до постоянной массы образцы помещают в раствор сернокислого натрия и выдерживают в нем в течение 20 ч при комнатной температуре, затем их переносят на 4 ч в сушильный шкаф, где поддерживается температура 105—110 °С. После этого образцы охлаждают до комнатной температуры, вновь заливают раствором сернокислого натрия, выдерживают в течение 4 ч и снова помещают в сушильный электрошкаф на 4 ч. В указанной последовательности операцию повторяют требуемое число раз. После 5 и 10 циклов попеременного выдерживания в растворе и высушивания в электрошкафу образцы промывают горячей водой для удаления сернокислого натрия, высушивают до постоянной массы и определяют их массу взвешиванием на гирных или циферблатных весах.
Потери образцов в массе Am (%) вычисляют по формуле
∆m = (m1 – m2) / m1 100,
где m1 и m2 – массы образца соответственно до испытания и высушенного до постоянной массы после испытания, кг.
Потеря образцов в массе не должна превышать 5 % после 10 циклов испытаний.
arxipedia.ru
Морозостойкость - Определения структурных характеристик
Навигация:Главная → Все категории → Определения структурных характеристик


Многие строительные конструкции (стены и фундаменты зданий, устои мостов, покрытия дорог) подвергаются совместному действию влаги и знакопеременных температур, которые постепенно приводят их к разрушению. Причина разрушения — расширение (примерно на 9%) воды при замерзании.
Морозостойкость — способность материала в насыщенном водой состоянии выдерживать многократное попеременное замораживание и оттаивание без видимых признаков разрушения. Испытание строительных материалов на морозостойкость заключается в цикличном попеременном замораживании и оттаивании в насыщенном водой состоянии и определении потери материалом массы и прочности. Замораживание и последующее оттаивание образца составляет один цикл; продолжительность цикла не должна превышать 24 ч. Количество циклов испытания принимают в соответствии с ГОСТом на материал. Так, бетон, применяемый для сооружения стен зданий, должен выдерживать 35…50 циклов, а бетон для гидротехнических сооружений – 300 циклов и более.
Выдержавшими испытание на морозостойкость считаются те материалы, которые после установленного для них ГОСТом числа циклов замораживания — оттаивания не имеют видимых признаков разрушения (не крошатся, не растрескиваются, не расслаиваются). Кроме того, потери прочности и массы образцов не должны превышать значений, установленных ГОСТом на данный материал. Например, для бетона потеря прочности при испытании на морозостойкость не более 5%, для кирпича и строительных растворов не более 25%; потеря массы при испытании кирпича не должна превышать 5%.
Испытывают материалы на морозостойкость на установках с холодильными машинами, создающими низкие температуры за счет испарения сконденсированных (сжатых и переведенных в жидкое состояние) газов: аммиака, фреона и т. п.
Во фреоновой компрессорной холодильной установке (рис. 3.5) жидкий фреон под давлением 0,5…0,8 МПа из ресивера через дроссель поступает в испаритель. Сечение труб испарителя значительно больше, чем сечение дросселя, в результате давление фреона в испарителе резко падает (до 0,05…0,1 МПа) и фреон, испаряясь, переходит в газообразное состояние. Этот процесс происходит с поглощением теплоты, поэтому в холодильной камере, где помещен испаритель, температура понижается до -16…-20°С. Из испарителя пары фреона поступают в компрессор, где они вновь сжимаются до 0,5…0,8 МПа, при этом температура фреона повышается. Затем в конденсаторе фреон охлаждается окружающим воздухом или водой, конденсируется и в жидком виде поступает в ресивер.
Морозостойкость различных материалов определяют как на целых изделиях, так и на образцах, специально изготовленных или высверленных из изделий. Форма и размеры образцов различных материалов определяются ГОСТами на эти материалы.
Образцы измеряют и взвешивают в состоянии, которое предусматривается стандартом, и укладывают в ванну для насыщения водой. Насыщенные водой образцы слегка обтирают тканью, повторно взвешивают и помещают в холодильную камеру при температуре не выше -16 °С. В камере образцы укладывают на металлический поддон с интервалами между ними для лучшего охлаждения. Если образцы размещают в несколько рядов по высоте, то их укладывают на подкладках толщиной не менее 20 мм. Общий объем загруженных в камеру образцов должен составлять не более 50% объема камеры.
Замороженные образцы вынимают из камеры и укладывают для оттаивания в ванну с водой при температуре 18…20°С. После полного оттаивания образцы вынимают из ванны, обтирают мягкой тканью, осматривают и вновь помещают в холодильную камеру. Через установленное стандартом для данного материала число циклов образцы после очередного оттаивания в воде взвешивают и испытывают на прочность.
Морозостойкость материала может быть определена ускоренными методами, заключающимися, например, в насыщении образцов материала в растворе сульфата натрия (п. 10.6) или путем глубокого (до -60 °С) их замораживания (п. 12, 13).
Похожие статьи:Структурные характеристики и свойства строительных материалов
Навигация:Главная → Все категории → Определения структурных характеристик
Статьи по теме:
Главная → Справочник → Статьи → Блог → Форум
stroy-spravka.ru
Морозостойкость
Морозостойкость – способность материала после насыщения его водой выдерживать определенное количество циклов замораживания – оттаивания без ухудшения свойств ниже установленного предела. *** Морозостойкость строительных материалов.Морозостойкость Frost resistance
Морозостойкость строительных материалов - способность насыщенного водой материала выдерживать многократное попеременное замораживание и оттаивание без видимых признаков разрушения и без значительного снижения прочности. Морозостойкость измеряется количеством циклов замораживания и оттаивания, проводимых в лабораторных условиях.
МОРОЗОСТОЙКОСТЬ КИРПИЧА
В условиях нашего изменчивого климата это одна из важнейших характеристик для кирпича. Морозостойкость кирпичей измеряется количеством циклов попеременного замораживания и оттаивания водонасыщенного изделия: чем больше циклов оно способно преодолеть, не изменив своих потребительских свойств, тем дольше прослужит. Почему речь идет о водонасыщенном изделии? Потому что морозостойкость во многом зависит от степени водопоглощения материала: ведь влага, замерзая и оттаивая при перепадах температур, разрушает его структуру. А значит, чем меньше влаги находится в порах керамики, тем лучше. По нормам водопоглощение кирпича должно быть не менее 6 и не более 16%.
В технической документации морозостойкость обозначается буквой «F», а следующая за ней цифра говорит о количестве циклов, которые кирпич может выдержать. В Центральном регионе рекомендуется применять строительный кирпич с морозостойкостью не ниже 15 - 25 циклов, лицевой – не ниже 50 циклов.
*** Морозостойкость цемента - способность цементного камня противостоять многократному попеременному замораживанию и оттаиванию. *** Способность материала после насыщения его водой выдерживать определенное количество циклов замораживания - оттаивания без ухудшения свойств ниже установленного предела. Например, кирпич и раствор для дымовых труб должны иметь свою определенную морозостойкость. *** Морозостойкость организмов Морозостойкость - способность организмов (растений) длительное время выносить температуры ниже 0 град.С. Морозостойкость также предполагает способность противостоять очень сильным (более 4О град.С) морозам. Усилению морозостойкости растений способствует накопление к началу зимы возможно большего количества запасных питательных веществ, особенно сахара и жиров.proseptic.ru
Коэффициент - морозостойкость - Большая Энциклопедия Нефти и Газа, статья, страница 1
Коэффициент - морозостойкость
Cтраница 1
Коэффициент морозостойкости при 15 циклах равен 0 89 и при 30 циклах - 0 75, что является вполне приемлемой величиной. Таким образом, исследованный закрепленный грунт является вполне морозоустойчивым, а метод закрепления мочевиноформальдегидной смолой можно считать вполне надежным. [1]
Коэффициент морозостойкости после пяти циклов при закреплении ВМТ-3 для суглинка составил 0 33 при сухом и 0 565 при влажном режимах хранения, для супеси тяжелой мелкой - 0 45 при сухом и 0 33 при влажном режимах хранения. [3]
Коэффициент морозостойкости при этом рассчитывают как отношение изгибающего усилия, необходимого для изгиба образца на этот угол при нормальной температуре, к изгибающему усилию, затрачиваемому при пониженной температуре. [4]
Коэффициент морозостойкости по ГОСТ 10672 - 63 - определяют при статическом и динамическом гармоническом сжатии как отношение деформации при заданных нагрузке и пониженной температуре - к деформации при той же нагрузке и температуре 20 5 С на приборе УПКМ. [5]
Коэффициент морозостойкости при этом рассчитывают как отношение изгибающего усилия, необходимого для изгиба образца на этот угол при нормальной температуре к изгибающему усилию, затрачиваемому при пониженной температуре. [7]
Коэффициент морозостойкости / См определяется различными методами [ 221, с. Он представляет собой отношение определяемой характеристики резины при низкой температуре к той же характеристике при комнатной температуре. [8]
Коэффициент морозостойкости измеряется при постоянной нагрузке. [9]
Коэффициент морозостойкости резин при сжатии определяют измерением деформации образцов при статическом и динамическом сжатии под воздействием одной и той же нагрузки в нормальных температурных режимах и при пониженной температуре. Этот метод характеризует потерю эластичности резин при охлаждении. Испытание проводят на приборе УПКМ-4. Образцы для испытания имеют форму цилиндра высотой 10 0 2 мм. [10]
Определение коэффициента морозостойкости при растяжении и по эластическому восстановлению при сжатии сопровождается относительно большой деформацией образцов - до 100 % при растяжении и до 20 % при сжатии. [12]
Полученные значения коэффициентов морозостойкости не могут характеризовать поведение резин, работающих в условиях ударных нагрузок или при периодической деформации. В таких случаях рекомендуется определять Тс полимера при разных частотах воздействия нагрузки. [14]
По значениям коэффициента морозостойкости, износо - и водостойкости резины из БНЭФ уступают резинам из СКН-26М. Эти недостатки ликвидируются при замене серной вулканизующей системы диметилглиоксимом. [15]
Страницы: 1 2 3 4
www.ngpedia.ru
Способ определения морозостойкости цементных материалов
Использование: в процессе контроля показателей качества строительных пористых материалов, изготавливаемых на основе применения цементобетонов, растворов, цементного камня и асбестоцемента. Сущность изобретения: изготавливают контрольные и основные образцы, насыщают их водой при сжатии контрольных образцов после насыщения водой, а основных после одноразового замораживания. Затем определяют капиллярную пористость испытуемого материала и показатель повышения прочности при замораживании для данной капиллярной пористости, находят максимальную и минимальную морозостойкость и максимальный и минимальный показатель повышения прочности материала при замораживании для капиллярной пористости испытуемого материала по статистически установленной зависимости морозостойкости от их капиллярной пористости. Морозостойкость цементных материалов рассчитывают по формуле. 1 ил.
Изобретение относится к промышленности строительных материалов, в частности к контролю качества бетонов, растворов и цементного камня.
Известен способ определения морозостойкости бетона по капиллярной пористости, согласно которому экспериментально определяют степень гидратации цемента в бетоне, вычисляют по данным о составе бетона и степени гидратации цемента капиллярную пористоть бетона и по значениям капиллярной пористости находят морозостойкость бетона на графике заранее установленной усредненной зависимости между морозостойкостью бетона и его капиллярной пористостью. Недостатком способа является неучет водоснабжения бетона конкретного состава, так как известно, что при одной и той же капиллярной пористости бетоны обладают различным водоснабжением, соответственно различной льдистостью при замораживании, а следовательно, и различной морозостойкостью. По этой причине отклонения определяемой по данному способу морозостойкости от ее фактического значения могут достигнуть 30-100% Отклонения, как правило, тем больше, чем меньше морозостойкость. Наиболее близким к предлагаемому является способ определения морозостойкости цементных материалов, включающий изготовление контрольных и основных образцов, насыщение их водой, испытание на прочность при сжатии контрольных образцов в насыщенном водой состоянии. Недостатки этого способа высокая энерго- и трудоемкость, обусловленная необходимостью изготовления значительного количества образцов и их многоцикловыми испытаниями в мощных морозильных камерах, а также его большая длительность, которая из-за многоцикловых испытаний достигает нескольких месяцев, а при испытании высокоморозостойких бетонов до одного года. Задача изобретения снижение энерго- и трудоемкости и длительности определения морозостойкости цементных материалов. Задача достигается тем, что в способе определения морозостойкости цементных материалов, включающем изготовление контрольных и основных образцов, насыщение их водой, прочность при сжатии контрольных образцов в насыщенном водой состоянии, насыщенные водой основные образцы подвергают одноразовому замораживанию и испытывают на прочность при сжатии в замороженном состоянии, определяют капиллярную пористость испытуемого материала, находят показатель повышения прочности испытуемого материала при замораживании для данной капиллярной пористости, по статически установленной зависимости морозостойкости от их капиллярной пористости находят максимальную и минимальную морозостойкость и максимальный и минимальный показатель повышения прочности материала при замораживании для капиллярной пористости испытуемого материала, а морозостойкость цементных материалов рассчитывают по формуле: Mi= Mmax+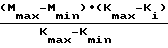










Формула изобретения
СПОСОБ ОПРЕДЕЛЕНИЯ МОРОЗОСТОЙКОСТИ ЦЕМЕНТНЫХ МАТЕРИАЛОВ, включающий изготовление контрольных и основных образцов, насыщение их водой, испытание на прочность при сжатии контрольных образцов в насыщенном водой состоянии, отличающийся тем, что насыщенные водой основные образцы подвергают одноразовому замораживанию и испытывают их на прочность при сжатии в замороженном состоянии, определяют капиллярную пористость испытуемого материала, находят показатель повышения прочности испытуемого материала при замораживании для данной капиллярной пористости, по статистически установленной зависимости морозостойкости от их капиллярной пористости находят максимальную и минимальную морозостойкость и максимальный и минимальный показатель повышения прочности материала при замораживании для капиллярной пористости испытуемого материала, а морозостойкость цементных материалов рассчитывают по формуле

РИСУНКИ
Рисунок 1, Рисунок 2www.findpatent.ru