Содержание
Состав газобетона на 1 м3, пропорции, изготовление в домашних условиях
Газобетонные блоки относятся к востребованным изделиям, успешно сочетающим теплоизоляционные и конструкционные свойства. При соблюдении пропорций и простых правил замеса они без проблем изготавливаются дома, при наличии подходящего оборудования и проведения автоклавной обработки выпуск продукции организовывается в промышленных масштабах. Итоговые характеристики зависят от качества сырья, тщательности его подготовки и последовательности соединений при замесе, правильный материал имеет однородную закрыто-ячеистую структуру.
В зависимости от вида и соотношений используемого вяжущего выделяют следующие разновидности:
- Цементные, с долей ПЦ с маркой прочности от М300 и выше, достигающей 50 % от общей массы.
- Известковые, на основе негашеной помолотой кипелки (до 50 %), гипса, шлака, цемента или их смесей (до 15 %).
- Шлаковые, полученные путем вспенивания молотых отходов металлургии с другими видами вяжущего.
- Зольные, содержащие до 50 % продуктов уноса.
- Смешанные, получаемые путем соединения всех вышеперечисленных видов вяжущего, с долей ПЦ от 15 % и выше.
В качестве инертного заполнителя применяется кварцевый и другие виды песка и вторичные отходы металлургии и теплоэнергетики: зола уноса и гидроудаления, ферросплавные шлаки, продукты обогащения рудных материалов. Все они вводятся после тщательного размола, доля в общем составе варьируется от 20 до 40 %. Поризация обычного и автоклавного газобетона достигается за счет ввода алюминиевой пудры и хлорида кальция, для затворения смеси используется вода с минимальным содержанием солей. К улучшающим свойства добавкам относят упрочнители, полиамидные пластмассы и аналогичные вещества, снижающие усадку, их соотношение в общей массе очень низкое.
Ориентировочные пропорции сырья для газобетона без автоклавной обработки:
Наименование | Доля в общей массе, % | ||
Портландцемент | 15-50 | 51-71 | 35,3-49,4 |
Наполнитель | Кварцевый песок: 31-42 | Молотый микрокремнезем: 0,6-3,5 | Молотый известняк до удельной поверхности 300-700 м2/кг: 12,4-26,5 |
Алюминиевая пудра | 0,1-1 | 0,01-0,15 | 0,06-0,1 |
Известь | — | 0,04-0,7 | 2,6-2,65 |
Полуводный гипс | — | 0,1-0,4 | — |
Другие добавки | Каустическая сода: 0,05-0,45 | Хлористый кальций: 0,5-3 | Хлорид кальция: 0,18-0,25 |
Вода для затворения | Все остальное |
Приведенные пропорции также подходят для автоклавного производства газобетона, в перерасчете на вес на приготовление 1 м3 смеси с плотностью 600 кг/м3 уходит 90 кг ПЦ, 375 – чистого кварцевого песка тонкого помола, 35 – известняка, 0,5 – порообразователя и около 300 л чистой воды комнатной температуры. Компоненты растворов могут меняться, а соотношения вяжущих при их комбинировании варьироваться от 1:0 до 1:5 (отмеряется по доле цемента). Требуемая марка прочности последнего зависит от целевого назначения, для изготовления теплоизоляционных марок используется ПЦ М300, конструкционно-теплоизоляционных – М400, плотных конструкционных – М500. В отличие от обычных товарных бетонов в данном случае лучшие результаты наблюдаются при вводе составов с примесями пуццолана и шлака (имеющим маркировку Д20, а не Д0).
Особые требования выдвигаются к порообразователю: для достижения равномерной ячеистой структуры материала применяется алюминиевая сухая пудра с долей активного металла в пределах 90-95 % или суспензии – до 93. Их ввод требует осторожности: при снижении доли менее 0,06 % блоки не достигают заданной пористости, при засыпке более 0,1 – выделяется избыток водорода, приводящий к образованию чересчур крупных ячеек, вырыванию из них газа и усадке изделий.
Существует четкая связь между качеством используемого наполнителя и прочностными характеристиками: чем тоньше будет его помол, тем лучше. Водоцементное соотношение подбирают опытным путем, доля затворяемой жидкости достигает 45-75% от общего веса сухих составляющих и в идеале сводится к минимуму.
Лучшие результаты при изготовлении неавтоклавного газобетона наблюдаются при В/Ц=0,4, повышение этого показателя приводит к снижению прочности материала.
Технология получения газоблоков в домашних условиях
Для кладочных изделий помимо сырья и емкостей для замеса потребуются формы – заводские металлические или самоделки из фанеры и дерева. Их размеры зависят от назначения блоков: чем больше будет ячеек, тем быстрее пойдет процесс выпуска. Внутренние стороны форм выполняются из ламинированной фанеры или других влагостойких материалов, принимаются меры по исключения протеканию воды, с целью упрощения выемки стенки смазывают составами на основе воды и технического масла в соотношении 3:1, эту процедуру повторяют каждый раз перед заполнением.
Этап замеса считается самым сложным в домашнем производстве, без дозаторов и оборудования для подготовки компонентов пропорции подбираются только опытным путем. Любое изменение степени активности вяжущего, температурных условий или чистоты воды оказывает прямое влияние на процесс поризации и итоговое качество. Важную роль играет последовательность соединения ингредиентов: вяжущее, песок или другие сухие заполнители перемешиваются и затворяются водой порционно, вплоть до получения однородной консистенции (но не более 5 мин, в противном случае цемент начнет схватываться), далее в нее вводят хлористый кальций или каустическую соду (при наличии их в выбранном составе), и в последнюю очередь – алюминиевую пудру или суспензию. После засыпки порообразователя смесь перемешивается со всей возможной тщательностью не более, чем 1 минуту и заливается в предварительно подготовленные формы.
При изготовлении газобетонных блоков в домашних условиях раствором заполняется только половина ячейки. Реагирование ингредиентов начинается незамедлительно, объем массы нарастает в течение первых 5-10 минут, после чего она слегка усаживается. Полученную «горбушку» срезают струной, формы оставляют в теплом помещении на сутки. Элементы вынимают с максимальной аккуратностью и размещают на стеллажах или поддонах до окончательного набора прочности.
Для получения автоклавных изделий они проходят обработку горячим паром под избыточным давление в специальных камерах, в домашних условиях этот этап пропускается. Это вместе с отсутствием возможности строгого контроля за составом и геометрической точностью форм объясняет уступку качества кустарных элементов заводским. С целью его улучшения принимается ряд мер:
- Площадка или помещение защищаются от сквозняков и холодной температуры. В идеале работы проводятся в теплое время года.
- Формы слегка прогревают перед смазыванием. После выемки изделий оценивается состояние стенок и проводится их тщательная чистка.
- Сухие компоненты перед затворением водой просеиваются сквозь сито и вводятся малыми порциями.
Состав газобетона: компоненты и технология производства
Газобетон является пористым материалом и относится к ячеистым бетонам, делится на автоклавный и неавтоклавный. Различия в плане состава между ними незначительны, но в процессе производства разница существенна.
Компоненты газобетона:
- Портландцемент высокой марки (35%).
- Песок очень мелкой фракции (35%).
- Измельченная известь (1%).
- Алюминиевая пудра (0.05%).
- Вода (28%).
Чем лучше измельчены все компоненты, тем прочнее получается газобетон.
Сама технология изготовления газобетона заключается в смешивании наполнителей (цемента и песка) с газообразующими добавками (известь и алюминиевая пудра). После их перемешивания, между алюминиевой пудрой и известью начинается химическая реакция с выделением газа – водорода. Именно этот газ и создает в газобетоне поры, которые обеспечивают хорошую теплоизоляцию и легкий вес.
Меняя количество газообразующих добавок, можно добиться различной плотности газобетона, то есть, чем больше газа в бетоне, тем он легче, соответственно, меньше его плотность и прочность. На рынке стройматериалов можно найти газобетон плотностью от D150 до D700.
Газобетон хорош тем, что поры в его составе распределены очень равномерно, что обеспечивает одинаковую прочность и теплопроводность по всей толщине блоков.
После процесса газообразования и первичного схватывания смеси, общий массив разрезается струной на отдельные блоки нужной толщины. Далее газоблоки набирают прочность.
Что такое автоклавирование газобетона
Если мы говорим про автоклавный газобетон, то он обязательно проходит процесс автоклавирования. Автоклавами называют большие емкости, в которых создается высокая температура (160-180 С) и давление насыщенного водяного пара.
Процесс автоклавирования длится около 12 часов, и его задача заключается в быстром наборе прочности газобетона. Обычный тяжелый бетон набирает 70% своей марочной прочности примерно через месяц, но если увеличить температуру до 180 градусов, то прочность наберется в 100 раз быстрее.
Это решает сразу несколько проблем: усадка блоков отсутствует, не требуется время для набора прочности газобетона. Далее газобетон упаковывают в защитную пленку и развозят заказчикам.
Свежий автоклавный газобетон является очень влажным, воды в нем около 30-40%. Из-за влаги, его плотность значительно выше заявленной. По этому, перед отделочными работами, выложенная газобетонная стена должна просохнуть хотя бы два сезона.
Автоклавный газобетон имеет более высокую прочность, в отличии от неавтоклавного.
В научной терминологии, автоклавный газобетон называют тоберморитом – искусственным пористым камнем. Так как камни являются минералами, то они абсолютно экологичны. Газобетон не выделяет никаких вредных веществ, и не является радиоактивным.
Отличия газобетона и пенобетона
В плане наполнителей эти ячеистые бетоны похожи, отличие в газообразующих добавках. Если в газобетоне пузыри образуются из-за выделяющихся пузырей газа, то в пенобетоне из-за пены, которую добавляют в смесь отдельно. Проблемой пенобетона может быть его неоднородность, то есть, в одном месте пузырей будет больше, а в другой – меньше.
Процесс изготовления пенобетона намного проще, из-за чего его производством занимаются в гаражных условиях. Доверие к качеству заводского автоклавного газобетона и его составу намного выше. Прочность и геометрия автоклавного газобетона лучше, чем у пенобетона.
Из чего состоит газобетон(видео)
Понимание газовой системы AR-15 |
Система прямого удара газа AR-15 довольно проста для понимания. Когда оружие стреляет, газ проходит по стволу позади пули. Когда он проходит через газовое отверстие, он направляется в базу мушки (ФСБ) или газовый блок в газовую трубку, по которой он попадает в ключ затворной рамы. Как только
газ достигает ключа, он сбрасывает газ в камеру, заставляя затворную раму двигаться назад.
( Элементы газовой системы )
Газирование начинается в патроннике патроном. Это означает, что выбор боеприпасов важен. Боеприпасы могут быть загружены либо по спецификации .223, либо по спецификации 5.56 NATO. Боеприпасы, произведенные с плохим контролем качества, могут повлиять на работу оружия.
Отсюда двигаемся к газовому порту. Газовый порт очень важен для общей функции винтовки. В военном мире это практически не проблема, поскольку газовые порты стандартизированы. В коммерческом/гражданском мире производитель может заправить свой ствол как угодно. Первое, что я делаю, когда собираю верх или провожу поиск и устранение неисправностей, — это измеряю размер порта. Если вы знаете правильный размер, это может избавить вас от многих проблем в процессе.
( Использование штифтового калибра для определения правильного размера порта )
Самый прочный газовый блок, который может иметь человек, — это штифтовая мушка (FSB), которая имеется почти на всех M16 / M4 в военном стиле и их вариантах. . ФСБ выступает в роли газового блока и мушки.
( MILSPEC F-Marked FSB прикреплен к стволу )
С распространением рельсовых систем возникла потребность в низкопрофильных газовых блоках (LPGB). К сожалению, эти модификации и распространение AR в коммерческой (невоенной) среде привели к проблемам. Использование некачественных компонентов в сочетании с небрежным исполнением может привести к нарушению работы газовой системы (утечке), что приведет к неисправностям.
Одним из таких некачественных компонентов является алюминиевый газовый блок. Многие производители нижнего уровня будут использовать их, потому что они очень дешевы. Алюминиевый газовый блок страдает от двух основных проблем. Первое — это тепловое расширение, а второе — эрозия газоблока от горячих газов.
( Эрозия алюминиевого газового блока )
Эти две проблемы создают утечки в газовой системе, что приводит к неисправности, известной как «короткий ход». Чаще всего, когда эти газовые блоки устанавливаются на ствол, производитель также не делает углубление на стволе, что приводит к смещению газового блока. Это также приведет к неисправности в какой-то момент.
Переходя к правильно изготовленным газоблокам стального типа, мы видим, что есть и отличия. Не только общей длиной и конструкцией блока, но и расстоянием между отверстиями для установочных винтов. Это важно знать, и это одна из причин, по которой большинство производителей, использующих такие блоки, делают углубление на стволе только ниже отверстия для установочного винта ниже газового порта.
( L-R: неизвестный блок, блок BCM, Geissele SGB, Centurion Arms MK12 блок )
Это в свою очередь приводит к еще одной проблеме с использованием газоблоков низкопрофильного типа и это правильная установка. Первостепенное значение имеет то, что при установке газового блока он не загораживает газовый порт. Большинство всех должным образом изготовленных стволов имеют газовое отверстие размером прибл. 0,295 дюйма от плеча до центра газового порта. Здесь всегда будет небольшой допустимый допуск из-за размера отверстия газового порта. В общем, нам нужна максимально плотная посадка между стволом и газовым блоком.
( Расположение газового порта )
Что касается отверстия газового порта, я обычно видел, что размер порта обычно составляет около 0,154-0,160 дюймов в диаметре у самых разных производителей. Это означает, что во многих случаях отверстие газового порта примерно в 2-2,5 раза больше самого газового порта.
( Centurion Arms MK12 размер отверстия 0,158 дюйма )
Теперь, когда мы закрыли газовый порт, FSB и газовые блоки, давайте перейдем к газовой трубе. Обычно, когда мы устанавливаем газовую трубку в ФСБ или газовый блок, нам нужна хорошая плотная посадка. Нестандартные трубки или небрежная посадка могут привести к утечке газа. Важно отметить, что почти всегда имеется небольшая утечка газа. Обычно небольшой утечки недостаточно, чтобы остановить цикл. Но если мы соединим утечку газа в блоке с нестандартным газовым портом и некоторыми другими проблемами (например, плохими газовыми кольцами), то у нас есть рецепт катастрофы.
( Пример типичной утечки газа )
Следующей проблемной областью газовой трубки является место, где газовая трубка соединяется со шпонкой затворной рамы. Правильно изготовленная газовая трубка будет иметь фланец в верхней части, где она соединяется со шпонкой и обеспечивает уплотнение. Если эта область изнашивается, газ будет выходить. Причиной чрезмерного износа является несоосность газовой трубки со шпонкой водила. Это также напрямую связано с правильной установкой, включая выравнивание газоблока.
(Офис новой газовой трубки и болта. Carrier Group или BCG. Эта тема не лишена споров. Есть лишь несколько компаний/производителей, которые понимают это правильно. За 30 лет работы с оружием семейства AR-15 я повидал столько неудачных работ по ставкам, что это не смешно.
Итак, давайте обсудим несколько фактов. Ставки изменились за эти годы. Оригинальные держатели, которые были покрыты твердым хромом, имели другую раскладку, которая выполнялась с помощью центрального пуансона в верхней части держателя. Позже это изменилось на (2) опорные точки на каждом винте. Кроме того, как указано в старой печати, Permatex #3D был нанесен в области под ключом держателя. Я не видел, чтобы это делалось несколько лет, и я не могу быть уверен, что это все еще требуется.
( Оригинальная затворная рама Colt Model 601 )
Величина крутящего момента шпоночных винтов несущей конструкции очень минимальна (58 дюйм/фунт), что делает крепление еще более важным. Не менее важны правильные винты. Вот подсказка. Если вы видите YFS на головке винта, это неправильно.
( Винты MILSPEC с правильной фиксацией )
Некоторые отказываются верить, что эти винты могут и будут ослабевать со временем при использовании. Я видел это столько раз, что сбился со счета. К сожалению, многие не могут сделать это правильно. Если шпонка установлена неправильно, винты не затянуты и не закреплены должным образом, они могут ослабнуть. Это приводит к массивной утечке газа, а также к повреждению газовой трубки.
( Неправильная фиксация шпонки водила )
( Неправильные винты и шпонка )
И последнее, но не менее важное: у нас есть газовые кольца для болтов. Газовые конфорки — это, по сути, самая дешевая часть газовой системы, и, вероятно, ею чаще всего пренебрегают. Средняя цена набора газовых конфорок (их бывает по 3 штуки) меньше, чем цена латте с карамельным соусом Venti mochacchino.
( Газовые кольца )
Часто возникает вопрос: «Как узнать, что они плохие»? Используются два теста. Самый простой и распространенный заключается в следующем; с чистым затвором и затворной рамой вставьте затвор в отверстие рамы. Выдвиньте болт в открытое положение (без кулачкового штифта) и поставьте его на лицевую сторону. Если держатель рухнет на болт под собственным весом, то вам следует заменить кольца. Стандартное правило — вы заменяете все три одновременно. Еще одна небольшая заметка о газовых кольцах. Миф о том, что газовые кольца должны располагаться в шахматном порядке, чтобы предотвратить совмещение трещин и утечку газа, на самом деле таков.0006 МИФ . Для этого нет причин.
( Проверка газового кольца )
Я надеюсь, что все будущие владельцы или пользователи AR-15 при покупке или ремонте оружия найдут эту информацию полезной.
Что делает газовый блок (2022) Ваш эксклюзивный ресурс
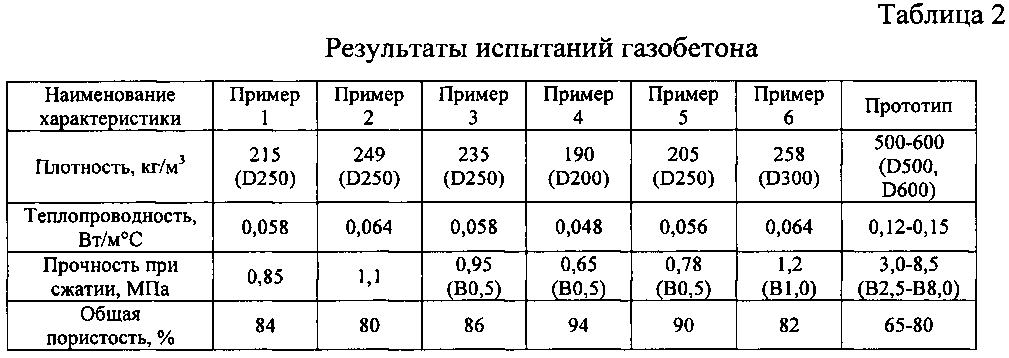
-
Альфред Мендоса -
9 июня 2022 г.
Внутренний механизм вашего оружия быстро изнашивается, а отдача слишком велика? Виновником является воздух, выходящий из газовой трубки, и в этом вам может помочь газоблок. Итак, что делает газоблок?
Ниже приведено полное руководство о том, как этот аксессуар повышает эффективность стрельбы.
Содержание
- 1 Что такое газоблок?
- 2 Что это делает?
- 3 Типы газовых блоков
- 3,1 Регулируемые
- 3,2 после прицела.
Это устройство в винтовке, которое можно установить в небольшие газовые отверстия в верхней части ствола и настроить на меньшую отдачу. Он регулирует избыток газа из взорванного патрона после нажатия на спусковой крючок. Это устройство можно встретить на газоотводном оружии.
Что он делает?
Задерживает лишний воздух AR 15, направляя его в газовое отверстие, а затем в газовую трубку в верхней части ствола.
Он ограничивает поступление воздуха в группу затворной рамы для уменьшения образования нагара, что облегчает чистку оружия.
Уменьшает отдачу и движение прицела для более быстрой дострелки. Это также создает небольшую нагрузку на вашу винтовку, поскольку она работает не тяжелее, чем без этого инструмента. Буферная трубка также может помочь газовому отверстию нести буферный вес для более усовершенствованной газовой системы.
Типы газовых блоков
Регулируемые
Регулируемые газовые блоки — это модернизированные устройства, которые могут поднять характеристики вашей винтовки на более высокий уровень. Он позволяет регулировать количество газа с помощью регулировочного винта и не ограничивает поток, будь то слишком мало газа или слишком много газа.
Газоблок регулируемый для газа AR 15 имеет два варианта устройства; отрезать и обескровить. Он предлагается многим стрелкам, предпочитающим работу с глушителем и немедленное отключение газовой системы.
Стойка мушки
После выстрела воздух проходит по газовой трубке, проходит через основание прицела и выходит [1].
Горячий газ за болтом будет вынужден пройти через маленькое газовое отверстие и подняться в болт. Он выйдет через газовое отверстие, которое перемещает группу затворной рамы назад.
Представляет собой комбинацию мушки и воздушного устройства.
Наша команда рекомендует начинающим стрелкам использовать AR 15 с FSP из-за его простоты использования и доступного несвободно плавающего ствола для рельсовых систем.
Низкопрофильный
В наши дни низкопрофильный блок чаще всего используется в пистолетах и винтовках. Низкопрофильные газоблоки спроектированы для обеспечения высокой точности и занимают мало места.
Что нам больше всего нравится в низком профиле, так это то, что он универсален с любым свободно плавающим цевьем. Это дает лучшую точность газовым системам, так как не касается стволов. Низкопрофильный газовый блок регулирует начальное сгорание AR 15 и вместе с правильной длиной ствола помогает винтовке быстро и плавно переключаться.
Можно ли стрелять из AR без газового блока?
Да, вы можете снимать AR без этого устройства. Однако новый раунд без прямого удара и установочного винта может быть громче, поскольку воздух выходит в атмосферу. Вы также почувствуете большее давление, но не беспокойтесь о горячих газах, так как они будут идти прямо вверх.
Могут ли газоблоки влиять на точность?
Нет, этот инструмент не может повлиять на точность ваших выстрелов. Однако это может повлиять на газовые системы, потому что для полного цикла действия требуется сжатый воздух. Установочные винты, с другой стороны, могут повлиять на точность, поэтому пользователи дозвуковых боеприпасов предпочитают использовать зажимы для своих стволов.
Изнашиваются ли газоблоки?
Да, этот аксессуар со временем изнашивается. Поскольку он подвергается воздействию высоких температур, есть вероятность, что он изнашивается за годы использования. Это как-то можно предотвратить частой очисткой и точной настройкой газоблока юстировки буферной системы.
Имеет ли значение марка газоблока
Да, марка устройства имеет значение. Наша команда следит за качеством, и надежный бренд может гарантировать хорошую производительность. Газовая система является неотъемлемой частью боеприпаса, а орудие — необходимой частью газовой системы.
Понимание того, как работают газовые блоки
Существует множество способов минимизировать отдачу и улучшить работу огнестрельного оружия, но установка пневматического инструмента является отличным решением. Это наполнитель, который идеально подходит над патронником AR 15. Если быть точным, это помогает воздушной системе контролировать количество газа в газовой трубке и ресивере.
Наша команда проверила систему прямого попадания, выстрелив не один раз, а тысячами, и никаких сбоев не было. Для вашей винтовки будет полезно использовать выравнивание инструмента, поскольку это предотвращает внутренние повреждения. Кроме того, на затворной раме нет нагара из-за плавной отдачи, что экономит ваше время и энергию.