Железобетонная шпала. Железобетонная шпала
ЖЕЛЕЗОБЕТОННАЯ ШПАЛА
Изобретение относится к конструкции рельсовых опор и может быть применено для изготовления шпал, в основном железобетонных, применяемых в верхнем строении железнодорожного пути, преимущественно бесстыкового.
Общеизвестна конструкция цельнобрусковой, предварительно напряженной, струнобетонной железобетонной шпалы, в которой нижняя постель плоская или в ее средней части она имеет выемку. Шпалу подбивают выправочными органами путевых машин так, чтобы она опиралась на балласт призмы железнодорожного пути только в своей подрельсовой части (см. «Общий курс железных дорог», стр.56, под ред. Ю.И.Ефименко.- М.,2005 г.; «Железобетонные шпалы для рельсового пути», под ред. Золотарского А.Ф.- М.: Транспорт, 1980 г.). Это позволяет значительно уменьшить растягивающие напряжения в верхней средней части рельсовой опоры, являющейся ее самым ненадежным участком, и исключить появление трещин, которые являются основным дефектом всей конструкции. Опирание шпалы на балласт средней своей частью недопустимо, так как приводит к излому и выходу из строя рельсовой опоры.
Общим недостатком железобетонных шпал является низкий коэффициент сцепления µж с балластом железнодорожного пути. Он составляет µж =1,2 и меньше, чем у деревянных в 3,3…4,2 раза (см. «Новые путевые машины», под ред. Ю.П.Сырейщикова.- М.: Транспорт, 1984 г., стр.192).
Это приводит к слабой устойчивости железнодорожного пути, опирающегося на бетонные шпалы. Поэтому возможны выбросы рельсов в боковом направлении и возникновение нештатных и аварийных ситуаций, сходов поездов с рельсов железнодорожного пути.
Известна также конструкция железобетонной шпалы по патенту RU 2433218 С2, в которой в средней ее части нижней постели для повышения трещиноустойчивости и некоторого увеличения усилия сдвига имеется выступ на длине, равной зоне сжимающих кромочных напряжений. Недостатком этой конструкции является необходимость организации выемки в средней верхней части балластной призмы с обеспечением размеров, идентичных соответствующим размерам выступа шпалы. Выполнить это условие в реальных условиях при выполнении верхнего строения железнодорожного пути крайне сложно.
Кроме того, эффективность данного технического решения по повышению усилия сдвига прямопропорциональна увеличению площади боковой поверхности шпалы. Но известно, что основное сопротивление по перемещению рельсовой опоры в балласте принадлежит подошве шпалы, а влияние боковой ее части составляет лишь 15-25%. Очевидно, что высота выступа конструкции по патенту RU 2433218 составляет примерно 15-50 мм, а длина - ориентировочно 500-700 мм. Поэтому увеличение боковой поверхности стандартной рельсовой опоры по ГОСТ 10629-2006, имеющей боковую площадь около 5000 см2, составит не более 7%, что крайне незначительно для обеспечения существенного положительного эффекта.
Принимаем техническое решение по патенту RU 2433218 за прототип.
Целью предлагаемого изобретения является значительное увеличение силы сопротивления смещения в балласте шпалы в продольном и поперечном направлении и повышение прочности и трещиноустойчивости рельсовой опоры, а также продление срока службы старогодных шпал с приданием им новой способности - высокой устойчивости в балластной призме железнодорожного пути.
Указанная цель достигается тем, что подошва шпалы содержит зубцы, причем в средней части ее постели на длине, равной зоне действия сжимающих кромочных напряжений, зубцы имеют уменьшенную высоту 10-50 мм, подрельсовая зона постели не содержит зубцов, а со стороны торцов и на части подошвы средней части опоры пути, где растягивающие напряжения отсутствуют или их величина незначительна, имеют увеличенную высоту 30-100 мм.
Техническое решение позволяет эффективное его использование не только при изготовлении новых изделий, получаемых, например, вбетонированием зерен щебня в подошву или получением зубцов, шипов, формированием их из материала самой шпалы в углублениях днища или боковой поверхности прессформы путем их затвердевания, но, и это особенно ценно, для модернизации шпал, бывших в употреблении. При этом возможно самозалечивание неопасных мелких трещин в теле старогодной шпалы при заливке ее нижней постели высокопрочным бетоном для получении создаваемых выступов.
Известно, что срок службы железобетонных рельсовых опор составляет 40-50 лет. Капитальный ремонт шпальной решетки (со сменой рельсов) производят через 18-25 лет. При этом одновременно с заменой рельсов приходиться заменять и рельсовые опоры, которые выработали свой ресурс всего на 50%. Изобретение позволяет модернизировать демонтированные при капитальном ремонте пути шпалы с целью придания им повышенной устойчивости за счет увеличения усилия сдвига в балласте в 3-5 раз и «залечивания» имеющихся дефектов в виде мелких трещин. Доработка заключается или вбетонированием в подошву зерен щебня, или получением зубцов на ней с применением дополнительной прессформы, имеющей на своей рабочей поверхности соответствующие углубления.
На Фиг.1 и 2 показана модернизированная старогодная шпала, содержащая зубцы, сформированные с помощью специальной накладной прессформы и заливки ее высокопрочным твердеющем с течением времени цементным раствором с гранитным щебнем фракции 3-7 мм. Часть уменьшенных по высоте зубцов предпочтительно должны быть расположена в зоне сжимающих напряжений. То есть эти зубцы должны быть размещены в средней части шпалы, в зоне сжимающих сил. Длина этой зоны ориентировочно составляет 600-700 мм. Высота шипов должна быть уменьшена по сравнению с высотой шипов, расположенных в зонах нулевых или незначительных по величине растягивающих напряжениях. В этом случае вновь добавленный бетон и зубья будут работать на сжатие и увеличат прочность самой шпалы. Зубцы в зоне проекции головки рельса на подошву рельсовой опоры, то есть в подрельсовой зоне нижней постели, отсутствуют. Их введение может увеличить вероятность развития трещин. Зубцы в зоне торцов и прилегающей к подрельсовой зоне части середины рельсовой опоры, где растягивающие напряжения отсутствуют или малы, имеют более высокие зубья, чем те, которые расположены в зоне сжимающих кромочных напряжений.
Можно сделать оценочный подсчет увеличения усилия сдвига в балласте модернизированной старогодной шпалы. Известно, что несущая способность уплотненного действием поездной нагрузки щебня верхнего слоя балластной призмы составляет приблизительно 15 кг/см2. Площадь поперечных сечений зубьев шпалы, изображенной на Фиг.1 и 2, составляет около 800 см2. Усилие фиксации тела рельсовой опоры в уплотненном балласте увеличится на F=15×800=12000 кгс и превысит аналогичный показатель стандартной шпалы в 10-15 раз.
Такое значительное повышение сопротивления перемещению шпалы в верхнем слое балластной призмы объясняется тем, что вновь сформированные шипы выполняют ту же функцию, что и зубья у бороны или корни у дерева.
Применение нового технического решения позволяет значительно, на порядок, увеличить силы фиксации шпал в щебне, оказывать эффективное противодействие сжимающим температурным силам, исключить возможность выброса и угона пути, организовать безаварийное движение поездов на высокоскоростных магистралях, повторно использовать старогодные шпалы не только на малодеятельных, но и на главных железнодорожных путях.
Железобетонная шпала, цельнобрусковая, предварительно напряженная, струнобетонная, отличающаяся тем, что подошва шпалы содержит зубцы, причем в средней части ее постели на длине, равной зоне действия сжимающих кромочных напряжений, зубцы имеют уменьшенную высоту 10-50 мм, подрельсовая зона постели не содержит зубцов, а со стороны торцев и на части подошвы средней части опоры пути, где растягивающие напряжения отсутствуют или их величина незначительна, имеют увеличенную высоту 30-100 мм.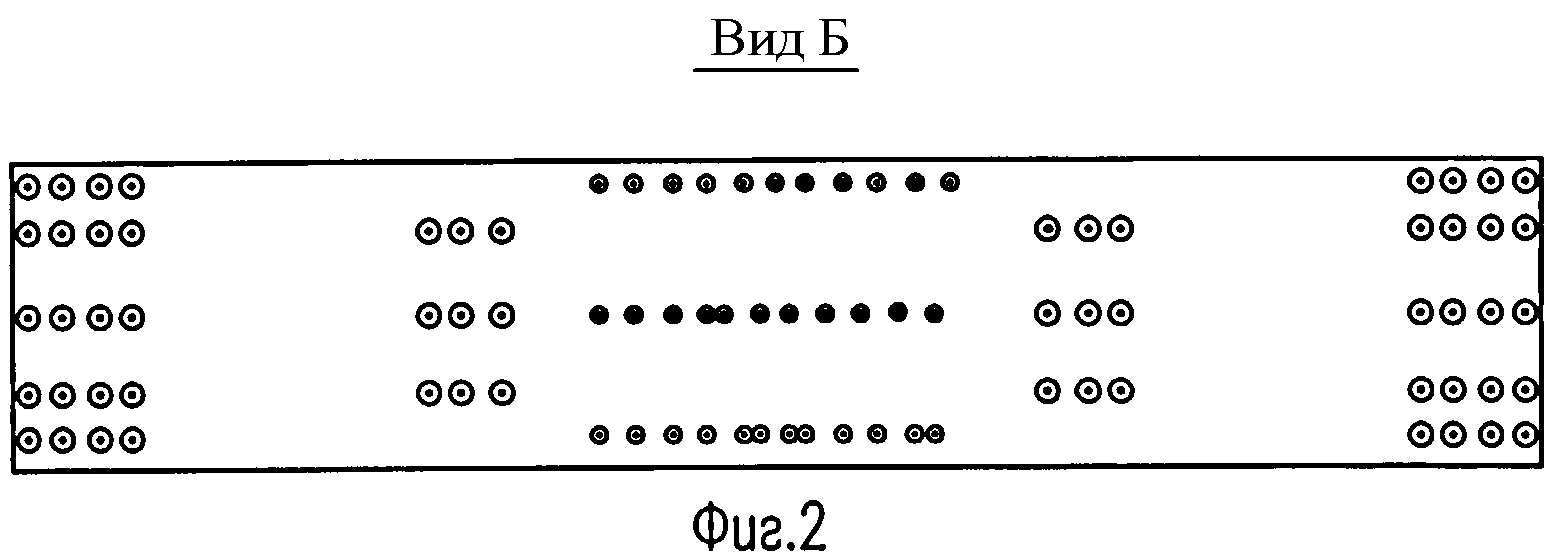
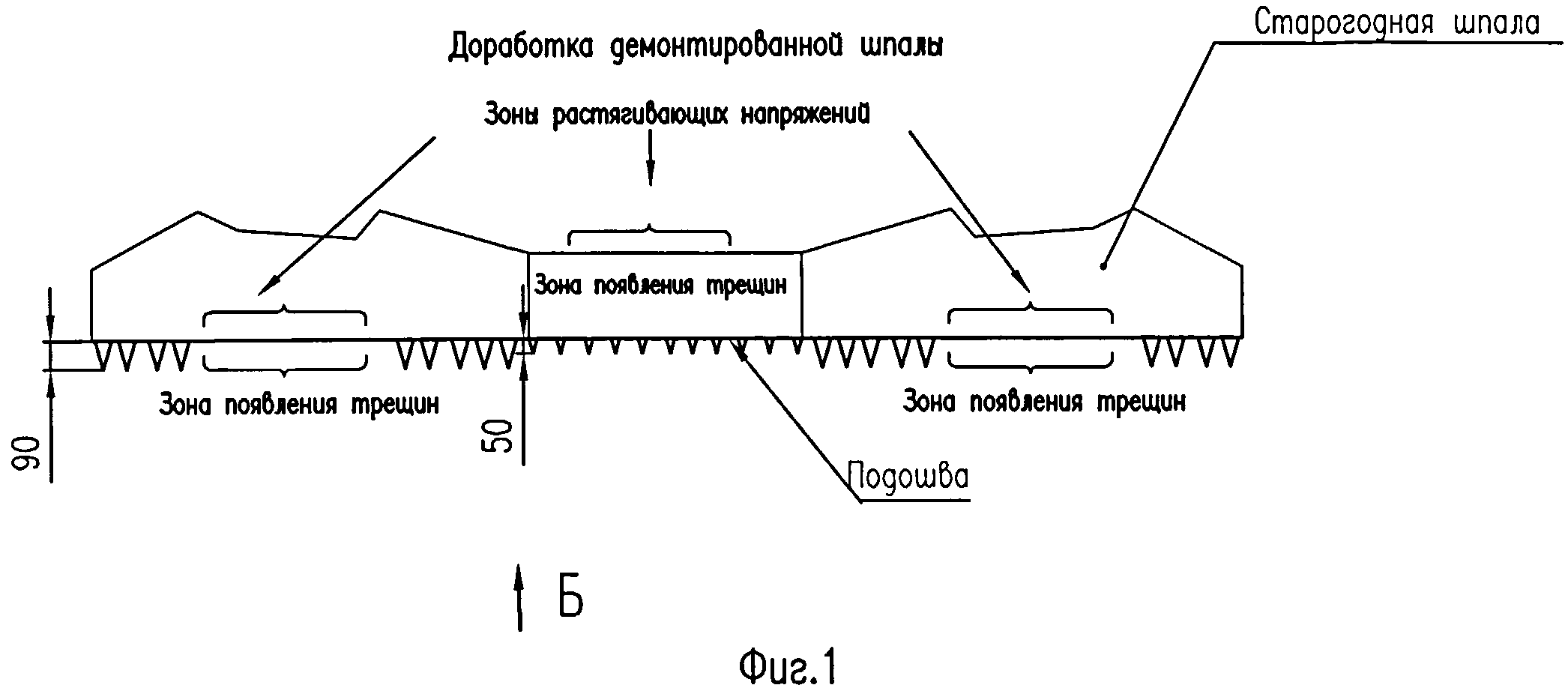
edrid.ru
Железобетонная шпала
Изобретение относится к верхнему строению железнодорожного пути и может быть использовано в конструкции шпал, в основном железобетонных и используемых преимущественно в бесстыковом пути. Подошва шпалы содержит зубцы. В средней части ее постели на длине, равной зоне действия сжимающих кромочных напряжений, зубцы имеют уменьшенную высоту 10-50 мм. Подрельсовая зона постели не содержит зубцов. Со стороны торцов и на части подошвы средней части опоры пути, где растягивающие напряжения отсутствуют или их величина незначительна, зубцы имеют увеличенную высоту 30-100 мм. В результате расчетное увеличение усилия сдвига рельсовой опоры ориентировочно составляет 10-15 раз. 2 ил.
Изобретение относится к конструкции рельсовых опор и может быть применено для изготовления шпал, в основном железобетонных, применяемых в верхнем строении железнодорожного пути, преимущественно бесстыкового.
Общеизвестна конструкция цельнобрусковой, предварительно напряженной, струнобетонной железобетонной шпалы, в которой нижняя постель плоская или в ее средней части она имеет выемку. Шпалу подбивают выправочными органами путевых машин так, чтобы она опиралась на балласт призмы железнодорожного пути только в своей подрельсовой части (см. «Общий курс железных дорог», стр.56, под ред. Ю.И.Ефименко.- М.,2005 г.; «Железобетонные шпалы для рельсового пути», под ред. Золотарского А.Ф.- М.: Транспорт, 1980 г.). Это позволяет значительно уменьшить растягивающие напряжения в верхней средней части рельсовой опоры, являющейся ее самым ненадежным участком, и исключить появление трещин, которые являются основным дефектом всей конструкции. Опирание шпалы на балласт средней своей частью недопустимо, так как приводит к излому и выходу из строя рельсовой опоры.
Общим недостатком железобетонных шпал является низкий коэффициент сцепления µж с балластом железнодорожного пути. Он составляет µж =1,2 и меньше, чем у деревянных в 3,3…4,2 раза (см. «Новые путевые машины», под ред. Ю.П.Сырейщикова.- М.: Транспорт, 1984 г., стр.192).
Это приводит к слабой устойчивости железнодорожного пути, опирающегося на бетонные шпалы. Поэтому возможны выбросы рельсов в боковом направлении и возникновение нештатных и аварийных ситуаций, сходов поездов с рельсов железнодорожного пути.
Известна также конструкция железобетонной шпалы по патенту RU 2433218 С2, в которой в средней ее части нижней постели для повышения трещиноустойчивости и некоторого увеличения усилия сдвига имеется выступ на длине, равной зоне сжимающих кромочных напряжений. Недостатком этой конструкции является необходимость организации выемки в средней верхней части балластной призмы с обеспечением размеров, идентичных соответствующим размерам выступа шпалы. Выполнить это условие в реальных условиях при выполнении верхнего строения железнодорожного пути крайне сложно.
Кроме того, эффективность данного технического решения по повышению усилия сдвига прямопропорциональна увеличению площади боковой поверхности шпалы. Но известно, что основное сопротивление по перемещению рельсовой опоры в балласте принадлежит подошве шпалы, а влияние боковой ее части составляет лишь 15-25%. Очевидно, что высота выступа конструкции по патенту RU 2433218 составляет примерно 15-50 мм, а длина - ориентировочно 500-700 мм. Поэтому увеличение боковой поверхности стандартной рельсовой опоры по ГОСТ 10629-2006, имеющей боковую площадь около 5000 см2, составит не более 7%, что крайне незначительно для обеспечения существенного положительного эффекта.
Принимаем техническое решение по патенту RU 2433218 за прототип.
Целью предлагаемого изобретения является значительное увеличение силы сопротивления смещения в балласте шпалы в продольном и поперечном направлении и повышение прочности и трещиноустойчивости рельсовой опоры, а также продление срока службы старогодных шпал с приданием им новой способности - высокой устойчивости в балластной призме железнодорожного пути.
Указанная цель достигается тем, что подошва шпалы содержит зубцы, причем в средней части ее постели на длине, равной зоне действия сжимающих кромочных напряжений, зубцы имеют уменьшенную высоту 10-50 мм, подрельсовая зона постели не содержит зубцов, а со стороны торцов и на части подошвы средней части опоры пути, где растягивающие напряжения отсутствуют или их величина незначительна, имеют увеличенную высоту 30-100 мм.
Техническое решение позволяет эффективное его использование не только при изготовлении новых изделий, получаемых, например, вбетонированием зерен щебня в подошву или получением зубцов, шипов, формированием их из материала самой шпалы в углублениях днища или боковой поверхности прессформы путем их затвердевания, но, и это особенно ценно, для модернизации шпал, бывших в употреблении. При этом возможно самозалечивание неопасных мелких трещин в теле старогодной шпалы при заливке ее нижней постели высокопрочным бетоном для получении создаваемых выступов.
Известно, что срок службы железобетонных рельсовых опор составляет 40-50 лет. Капитальный ремонт шпальной решетки (со сменой рельсов) производят через 18-25 лет. При этом одновременно с заменой рельсов приходиться заменять и рельсовые опоры, которые выработали свой ресурс всего на 50%. Изобретение позволяет модернизировать демонтированные при капитальном ремонте пути шпалы с целью придания им повышенной устойчивости за счет увеличения усилия сдвига в балласте в 3-5 раз и «залечивания» имеющихся дефектов в виде мелких трещин. Доработка заключается или вбетонированием в подошву зерен щебня, или получением зубцов на ней с применением дополнительной прессформы, имеющей на своей рабочей поверхности соответствующие углубления.
На Фиг.1 и 2 показана модернизированная старогодная шпала, содержащая зубцы, сформированные с помощью специальной накладной прессформы и заливки ее высокопрочным твердеющем с течением времени цементным раствором с гранитным щебнем фракции 3-7 мм. Часть уменьшенных по высоте зубцов предпочтительно должны быть расположена в зоне сжимающих напряжений. То есть эти зубцы должны быть размещены в средней части шпалы, в зоне сжимающих сил. Длина этой зоны ориентировочно составляет 600-700 мм. Высота шипов должна быть уменьшена по сравнению с высотой шипов, расположенных в зонах нулевых или незначительных по величине растягивающих напряжениях. В этом случае вновь добавленный бетон и зубья будут работать на сжатие и увеличат прочность самой шпалы. Зубцы в зоне проекции головки рельса на подошву рельсовой опоры, то есть в подрельсовой зоне нижней постели, отсутствуют. Их введение может увеличить вероятность развития трещин. Зубцы в зоне торцов и прилегающей к подрельсовой зоне части середины рельсовой опоры, где растягивающие напряжения отсутствуют или малы, имеют более высокие зубья, чем те, которые расположены в зоне сжимающих кромочных напряжений.
Можно сделать оценочный подсчет увеличения усилия сдвига в балласте модернизированной старогодной шпалы. Известно, что несущая способность уплотненного действием поездной нагрузки щебня верхнего слоя балластной призмы составляет приблизительно 15 кг/см2. Площадь поперечных сечений зубьев шпалы, изображенной на Фиг.1 и 2, составляет около 800 см2. Усилие фиксации тела рельсовой опоры в уплотненном балласте увеличится на F=15×800=12000 кгс и превысит аналогичный показатель стандартной шпалы в 10-15 раз.
Такое значительное повышение сопротивления перемещению шпалы в верхнем слое балластной призмы объясняется тем, что вновь сформированные шипы выполняют ту же функцию, что и зубья у бороны или корни у дерева.
Применение нового технического решения позволяет значительно, на порядок, увеличить силы фиксации шпал в щебне, оказывать эффективное противодействие сжимающим температурным силам, исключить возможность выброса и угона пути, организовать безаварийное движение поездов на высокоскоростных магистралях, повторно использовать старогодные шпалы не только на малодеятельных, но и на главных железнодорожных путях.
Железобетонная шпала, цельнобрусковая, предварительно напряженная, струнобетонная, отличающаяся тем, что подошва шпалы содержит зубцы, причем в средней части ее постели на длине, равной зоне действия сжимающих кромочных напряжений, зубцы имеют уменьшенную высоту 10-50 мм, подрельсовая зона постели не содержит зубцов, а со стороны торцев и на части подошвы средней части опоры пути, где растягивающие напряжения отсутствуют или их величина незначительна, имеют увеличенную высоту 30-100 мм.
www.findpatent.ru
Железобетонная шпала
Изобретение относится к конструкциям железнодорожных шпал. Шпала включает в себя арматуру (1) и устройство для увеличения ее сопротивления перемещениям поперек и вдоль пути. Устройство расположено на концевых участках шпалы. Устройство представляет собой в плане Т-образные элементы (3), которые прикреплены с возможностью замены вертикальными полками к пластинам. Пластины выполнены за одно целое со шпалой и расположены с обеих боковых сторон шпалы. Нижняя часть горизонтальной полки каждого Т-образного элемента (3) расположена ниже нижней поверхности шпалы. Изобретение направлено на увеличение сопротивления сдвигу шпалы вдоль и поперек пути. 1 з.п. ф-лы, 3 ил.
Изобретение относится к конструкциям железобетонных шпал, укладываемых на железнодорожном пути.
Известна железобетонная шпала (Шахунянц Г.М. "Железнодорожный путь. М. "Транспорт". 1987 г., с. 196-197). При укладке в путь таких шпал не обеспечивается необходимое сопротивление перемещениям их вдоль и поперек пути в особо сложных условиях, что ведет к расстройству пути. Известна также железобетонная шпала, включающая в себя устройство увеличения сопротивления ее перемещениям поперек и вдоль пути, расположенное на концевых участках шпалы (патент Германии 839363. E 01 В 3/28, 1952 г.). При укладке в путь таких шпал также не обеспечивается необходимое сопротивление перемещениям их вдоль и поперек пути в особо сложных условиях, а также изменение величины сопротивления сдвигу. Техническим результатом изобретения является увеличение сопротивления сдвигу шпалы вдоль и поперек пути, изменение величины сопротивления сдвигу. Для достижения этого технического результата в железобетонной шпале, включающей в себя устройство увеличения сопротивления ее перемещениям поперек и вдоль пути, расположенное на концевых участках шпалы, это устройство представляет собой Т-образные в плане элементы, прикрепленные с возможностью замены вертикальными полками к пластинам, выполненным за одно целое со шпалой и расположенным с обеих боковых сторон шпалы. Кроме этого, нижняя часть Т-образного элемента расположена ниже нижней поверхности шпалы. На фиг. 1 изображена железобетонная шпала, вид сбоку с частичным разрезом. На фиг.2 - то же, вид сверху. На фиг.3 - разрез А-А фиг.2. Железобетонная шпала включает в себя арматуру 1 и выполнена с устройством для увеличения сопротивления перемещениям шпалы поперек и вдоль пути. Это устройство представляет собой Т-образные в плане элементы 3, прикрепленные с возможностью замены вертикальными полками к пластинам 2. Пластины 2 размещены на концевых участках шпалы и закладываются в тело шпалы при ее изготовлении, т. е. в готовом виде шпала имеет пластины 2, выполненные за одно целое со шпалой. Пластины 2 должны выступать с обеих боковых сторон шпалы на расстояние, достаточное для крепления элемента 3, и могут иметь, например, П-образную форму (фиг.3). К выступающим частям пластин 2 крепятся с возможностью замены вертикальные полки элементов 3. Нижняя часть горизонтальной полки каждого элемента 3 может быть расположена ниже нижней поверхности шпалы, например, на 5-10 см. Размеры полок элементов 3 для различных условий эксплуатации шпалы могут быть различными. Например, увеличение размеров полок элементов 3 до 15 см дает возможность увеличить сопротивление перемещениям шпалы вдоль и поперек пути, а вследствие этого сократить количество укладываемых шпал в криволинейных участках пути, например, вместо 2000 шп/км можно уложить 1840 шп/км. Таким образом, железобетонная шпала с Т-образными заменяемыми элементами 3 на обеих боковых сторонах концевых участков шпалы дает возможность увеличить сопротивление сдвигу шпалы вдоль и поперек пути, а также изменять величины сопротивления сдвигу шпалы в зависимости от конкретных условий эксплуатации железнодорожного пути за счет возможности замены Т-образных элементов на Т-образные элементы, имеющие большую или меньшую площадь полок. Вследствие этого обеспечивается изменение эпюры шпал в сторону уменьшения количества шпал, укладываемых на километр пути. Расположение пластин 2 с обеих боковых сторон шпалы дает возможность прикрепить Т-образные элементы с обеих боковых сторон шпалы, что обеспечивает равномерное распределение усилий и исключает возможность кантования (поворота) шпалы в вертикальной плоскости.Формула изобретения
1. Железобетонная шпала, включающая в себя устройство для увеличения сопротивления ее перемещениям поперек и вдоль пути, расположенное на концевых участках шпалы, отличающаяся тем, что устройство для увеличения сопротивления перемещениям шпалы поперек и вдоль пути представляет собой Т-образные в плане элементы, прикрепленные с возможностью замены вертикальными полками к пластинам, выполненным за одно целое со шпалой и расположенным с обеих боковых сторон шпалы. 2. Шпала по п.1, отличающаяся тем, что нижняя часть горизонтальной полки каждого Т-образного элемента расположена ниже нижней поверхности шпалы.РИСУНКИ
Рисунок 1, Рисунок 2, Рисунок 3Похожие патенты:
Изобретение относится к верхнему строению железнодорожного пути, преимущественно для карьерного железнодорожного транспорта
Изобретение относится к области верхнего строения железнодорожного пути, а именно к устройствам для крепления рельсов к железобетонным шпалам
Изобретение относится к верхнему строению железнодорожного пути, а именно к устройствам для крепления рельсов к железобетонным шпалам с пустотами под путейские болты
Изобретение относится к промышленному железнодорожному транспорту, способам и устройствам для изготовления железобетонных шпал
Изобретение относится к конструкциям верхнего строения рельсовых путей, в частности к армированным шпалам
Изобретение относится к железнодорожному транспорту и может быть использовано в железнодорожном пути
Изобретение относится к конструкциям верхнего строения рельсовых путей, в частности к армированным шпалам
Изобретение относится к конструкции верхнего строения пути и предназначено для восприятия нагрузки от подвижного состава
Изобретение относится к шпалам для пути без применения балластного слоя или в туннеле/виадуке, где опорой для шпал служит подошва/плита
Изобретение относится к верхнему строению железнодорожного пути и предназначено для обеспечения скоростного движения пассажирских и грузовых поездов. Железобетонная шпала выполнена в виде армированного бруса с переменным подлине поперечным сечением. Шпала имеет концевые участки (1), участки (2) для крепления рельсов и участки (3) сопряжения со средним участком (4), имеющим ширину меньше ширины других участков. Средний участок (4) в поперечном сечении выполнен в виде трапеции, а участки (2) для крепления рельсов выполнены с сопряженными между собой наклоненными к горизонтали гранями (5) и (6). Гранями (5) образованы грани соответствующих концевых участков (1), а участки (3) сопряжения со средним участком (4) выполнены с наклоненными к горизонтали гранями (7) и (8). Грани (7) участков (3) сопряжены с гранями (6) участков (2) для крепления рельсов. Достигается снижение материалоемкости железобетонной шпалы и повышение ее эксплуатационных характеристик. 5 з.п. ф-лы, 15 ил.
Изобретение относится к конструкциям железнодорожных шпал
www.findpatent.ru
Способ изготовления железобетонной шпалы
Использование: изобретение относится к способам формования бетонной массы железнодорожных шпал и позволяет создать железобетонную шпалу высокой эксплуатационной стойкости. Сущность изобретения: производят заполнение формы бетонной смесью и арматурой, уплотнение бетонной смеси с последующим нагревом в печах. При этом уплотнение бетонной смеси производят приложением ультразвуковых колебаний с частотой 18 - 21 кГц. 1 ил.
Изобретение относится к области производства железобетонных изделий, а именно к способу формования бетонной массы железнодорожных шпал.
Известен способ изготовления железнодорожных шпал из древесины (Лысюк В. С. Износ деревянных шпал и борьба с ним. Труды ЦНИИ МПС /Под ред.В.С.Лысюка/, вып.445, 1971, рис.3, на с.23. Эта шпала имеет невысокую жесткость, обладает хорошими демпфирующими свойствами, сравнительно легко по весу. Однако указанная шпала имеет следующие недостатки: повышенный износ, из-за гниения и механического разрушения, постоянный дефицит и острая потребность в древесине во всех отраслях. Наиболее близким к изобретению по технической сущности является способ изготовления железобетонной шпалы (Золотарский А.Ф. Балашов А.А. Исаев Н.М. и др. Железнодорожный путь на железобетонных шпалах, М. Транспорт, 1967, с. 254). Одним из основных в технологической цепи производства шпалы является процесс обработки бетонной смеси путем ее виброуплотнения, который осуществляется следующим образом. Форму со свежеуложенной бетонной смесью передвигают по рольгангу на формовочный пост, состоящий из виброплощадки и пригрузочного щита, где производится виброуплотнение бетонной смеси. Уплотнение смеси производится в форме в две стадии: стадии предварительного уплотнения и стадии окончательного уплотнения. Первая стадия уплотнения производится с частотой вибрирования до 1000 колебаний /мин (порядка 17 Гц), что приводит к ускорению заполнения фирмы бетонной смесью. Вторая стадия состоит из двух этапов. Первый этап осуществляется с частотой вибрирования до 3000 колебаний/мин (50 Гц) в течение 2 3 мин. Второй этап вибрирования ведется с такой же частотой 50 Гц продолжительностью 1 2 мин с дополнительным статическим пригрузом, создающим давление 20 30 г/см2 для создания повышенной плотности бетонной смеси. После виброобработки форму с бетонной смесью нагревают в печах. В некоторых случаях на втором этапе, по возможности, повышают частоту вибрирования смеси до 6000 9000 колебаний/мин (120 150 Гц (там же, с.224). Как выяснилось, вибрирование значительно уплотняет бетонную смесь, обеспечивает однородность бетона, шпал, позволяет увеличить его прочность. Однако известный способ имеет целый ряд недостатков: частные поломки вибраторов и узлов креплений; громоздкое и тяжелое оборудование; большой шум при работе вибраторов; плотность шпального бетона не достигает необходимого уровня, так как внутри шпал образуется огромное количество воздушных пор, раковин, различных микропустот, пузырьков; из-за большого количества пор происходит преждевременное разрушение бетона, оголение арматуры; от попадания влаги в поры и раковины бетона, из которых впоследствии от перепада температур развиваются трещины. Технический результат, на достижение которого направлено изобретение заключается в создании железобетонной шпалы высокой эксплуатационной стойкости. Сущность изобретения состоит в том, что в способе изготовления железобетонной шпалы, включающем в себя заполнение формы бетонной смесью и арматурой, уплотнение бетонной смеси с последующим нагревом в печах, согласно изобретению уплотнение бетонной смеси производят приложением ультразвуковых колебаний с частотой 18 21 кГц. От действия ультразвуковой частоты в жидком растворе бетона возникают интенсивные микроударные циклические волны, которые способствуют появлению огромного количества кавитационных пузырьков, проникающих в поры, углубления, микротрещины, что приводит к заполнению этих пустот жидкостью и вытеснению воздуха. Одновременно с этим протекает процесс омывания кавитационной жидкостью частиц цемента, щебня, окатывания их острых кромок за счет взаимного соударения и трения между ними. В процессе кавитационного взаимодействия происходит сглаживание поверхностных микронеровностей, что приводит к округлению частиц цемента, щебня приданию им сферической формы. В результате обработки ультразвуком происходит удаление воздуха из раствора, что приводит к ликвидации очагов зарождения и развития трещин. Выбор ультразвуковых частот в пределах 18 21 кГц объясняется высокой энергонесущей способностью этих частот и наличием оборудования, вырабатывающих эти частоты. На чертеже представлена схема способа производства железобетонной шпалы. Магнитострикционные преобразователи 1 жестко крепятся к металлической форме 2, выполненной по размерам перевернутой железобетонной шпалы, заполненной бетонной смесью. Способ изготовления железобетонной шпалы заключается в следующем. Форму 2 со свежеуложенной бетонной смесью передвигают по рольгангу на формовочный пост, где к форме крепят магнитострикционные преобразователи 1 марки ПМС-6М. После закрепления преобразователей 1 включают ультразвуковой генератор (например, УЗГ 10 22), вырабатывающий ультразвуковые колебания частотой 18 21 кГц, которые передаются на магнитострикционные преобразователи 1, где происходит преобразование ультразвуковых электрических колебаний в механические ультразвуковые колебания такой же частоты 18 21 кгц и амплитудой 5 10 мкм. Ультразвуковое уплотнение смеси производится в одну стадию и длится 20 30 мин без дополнительного статического пригруза. Функцию статического пригруза в условиях ультразвукового вибрирования выполняет сама бетонная смесь. В процессе ультразвукового вибрирования происходит уплотнение смеси, выход из пор воздуха. После виброобработки преобразователи 1 снимаются и форма 2 направляется далее по технологическому маршруту. Пример конкретного выполнения. Металлическая форма для бетонной шпалы 2 имеет снизу жестко закрепленные три магнитострикционных преобразователя ПМС-6М которые работают от ультразвукового генератора УЗК 10 22. Генератор УЗГ 10 22 вырабатывает ультразвуковые колебания частотой 18 кГц, которые передаются на преобразователи ПМС-6М, где происходит преобразование ультразвуковых электрических колебаний в механические колебания такой же частоты 18 кГц и амплитудой 10 мкм. Уплотнение бетонной смеси производят под действием механических ультразвуковых колебаний, действующих со стороны преобразователей ПМС-6М. Длительность ультразвукового уплотнения длится 30 мин без дополнительного статического пригруза. После 30 минутной ультразвуковой обработки преобразователи 1 снимаются с формы 2 и крепятся к следующей форме. Обработанная ультразвуком будущая бетонная шпала в форме направляется далее по технологическому маршруту. Последующие испытания прочности бетона железобетонных шпал показали следующее. Испытания прочности проводили с помощью огнестрельного метода из пневматического ружья китайского производства по методике профессора В.Г. Скрамаева (Новгородский М.А. Испытания материалов, изделий и конструкций, М. Высшая школа, 1977, с.185). Выстрел свинцовой пулей производили с расстояния 100 мм в ранее отмеченную на образце точку. После выстрела замеряли глубину и средний диаметр воронки и определяли объем воронки. Выстрелы производили в пять отмеченных точек, расположенных друг от друга и от края образца на расстоянии 50 мм. Испытания показали, что предел прочности бетона, полученного обычным методом, составляет 300 кг/см2, а предел прочности бетона, полученного при ультразвуковой обработке, составляет 400 кг/см2.Формула изобретения
Способ изготовления железобетонной шпалы, включающий заполнение формы бетонной смесью и арматурой, уплотнение бетонной смеси с последующим нагревом в печах, отличающийся тем, что уплотнение бетонной смеси производят приложением ультразвуковых колебаний с частотой 18 21 кГц.РИСУНКИ
Рисунок 1Похожие патенты:
Изобретение относится к верхнему строению пути и может быть использовано для железнодорожных, трамвайных и подкрановых путей в качестве подрельсовых опор на сплошном упругом основании
Изобретение относится к элементам верхнего строения пути
Изобретение относится к бетонной шпале для рельсовых путей на грузонапряженных, высокоскоростных и городских участках железной дороги
Изобретение относится к конструкции железобетонных шпал
Изобретение относится к дорожному строительству, например плитам покрытий колейных автомобильных дорог и аэродромов, а также балкам, например шпалам железнодорожных, лесовозных и трамвайных путей
Изобретение относится к конструкциям и способам изготовления удлиненных конструктивных элементов, используемых как морская свая, или телефонная опора, или рельсовая шпала
Изобретение относится к верхнему строению железнодорожного пути, предназначено служить опорой рельсов, является основанием для деталей рельсового скрепления, воспринимает от рельсов и скрепления эксплуатационные усилия и передает их на балластный слой и может найти применение на магистральных железнодорожных линиях, в том числе высокоскоростных, в тоннелях, метрополитенах и на подъездных железнодорожных путях промышленных предприятий
Изобретение относится к конструкциям верхнего строения рельсовых путей, в частности к армированным шпалам
Изобретение относится к области железнодорожного транспорта, в частности к железобетонным шпалам и брусьям, используемым в верхнем строении высокоскоростных железнодорожных путей, выполненных с использованием щебеночного балласта или железобетонного основания
Изобретение относится к железнодорожному транспорту и может быть использовано в железнодорожном пути
Изобретение относится к конструкциям верхнего строения рельсовых путей, в частности к армированным шпалам
Изобретение относится к верхнему строению железнодорожного пути и предназначено для обеспечения скоростного движения пассажирских и грузовых поездов. Железобетонная шпала выполнена в виде армированного бруса с переменным подлине поперечным сечением. Шпала имеет концевые участки (1), участки (2) для крепления рельсов и участки (3) сопряжения со средним участком (4), имеющим ширину меньше ширины других участков. Средний участок (4) в поперечном сечении выполнен в виде трапеции, а участки (2) для крепления рельсов выполнены с сопряженными между собой наклоненными к горизонтали гранями (5) и (6). Гранями (5) образованы грани соответствующих концевых участков (1), а участки (3) сопряжения со средним участком (4) выполнены с наклоненными к горизонтали гранями (7) и (8). Грани (7) участков (3) сопряжены с гранями (6) участков (2) для крепления рельсов. Достигается снижение материалоемкости железобетонной шпалы и повышение ее эксплуатационных характеристик. 5 з.п. ф-лы, 15 ил.
Изобретение относится к области железнодорожного транспорта, в частности к конструкции шпал из бетона с арматурой. Железобетонная шпала включает брус (1) с арматурой (2), концы которой защищены на торцах бруса (1) пробкой (3), выполненной из полимерного материала. Шпала снабжена наконечником (4), выполненным в виде стакана из полимерного материала для размещения в нем пробки (3), связанным с концом арматуры (2) и торцом бруса (1). Верхняя часть наконечника (4) может быть выполнена ступенчатой и иметь двойное расширение. Пробка (3) может быть выполнена с наружным диаметром верхней ее части, равным диаметру других элементов пробки и равным внутреннему диаметру верхней части наконечника (4). Пробка (3) может быть выполнена с наружным диаметром верхней ее части, большим диаметра других элементов пробки и равным внутреннему диаметру первого расширения верхней части наконечника (4). Достигается повышение долговечности шпалы за счет исключения попадания влаги к концам арматуры на торцах бруса и повышении трещиностойкости при извлечении шпалы из формы. 3 з.п. ф-лы, 4 ил.
Изобретение относится к области производства железобетонных изделий, а именно к способу формования бетонной массы железнодорожных шпал
www.findpatent.ru