Производство керамзитобетонных блоков. Завод по производству керамзитобетонных блоков
Оборудование + Технология для 2018
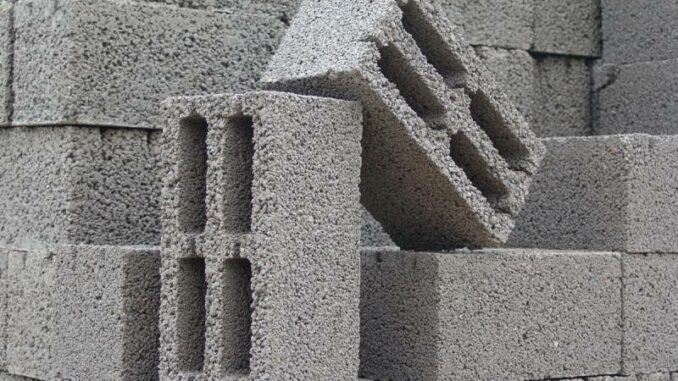
Сегодня керамзитобетонные блоки стали достаточно популярными, поскольку обладают значительными преимуществами по сравнению с кирпичом или камнем. В Америке и Европе из данного материала возводят примерно 40 процентов жилых помещений. Такой блок легче кирпичной кладки вдвое, что снижает в два раза давление на фундамент, а стало быть, вы получаете экономию на заливании фундамента. При использовании керамзитобетонных блоков, на 40 процентов сокращаются расходы на строительство малоэтажных домов. Данный стройматериал способен на 20% увеличить площадь при возведении перегородок между квартирами и комнатами. Керамзитобетонный блок это надежный, выгодный, экологичный и весьма удобный строительный материал, который имеет большой потенциал.
Технология и оборудование для производства керамзитобетонных блоков
В основе производства лежит керамзит. С греческого слово переводится как «обожженная глина». Внешний вид керамзита всем известен — легкие пористые гранулы овальной формы, которые получаются путем обжига легкоплавкой глины. Внутри гравий пористый, снаружи данный материал обладает прочной и герметичной оболочкой. Приготовление керамзита происходит по следующему сценарию: приготовленную глину необходимо за 30 минут нагреть до температуры в 1200 градусов, после чего масса закипит, и образуются овальные частицы с порами внутри.
Функциональные возможности керамзита очень широки: он не тонет и не горит, кроме того, имеет высокую износоустойчивость. Наверное, наиболее важной отличительной чертой материала является его высокие способности утеплять, ведь данный материал снижает теплопотерю на 45-50%.
Керамзитобетонный блок – это строительный материал из легкого бетона с крупным заполнителем из керамзита. Для производства применяют керамзитовый гравий фракциями 5-10 мм. Обычно плотность керамзита составляет 350-1800 кг/кубометр. Вяжущим элементом, как правило, выступает цемент, реже используется гипс или известь. При изготовлении керамзита используют песок в качестве мелкого заполнителя. Для многих сегодня важна экологичность производства. Так вот, производство, как и сам материал, — абсолютно экологически чисты. Готовые блоки не содержат ни частицы синтетических веществ, ни капли химии и производятся на современном оборудовании согласно ГОСТам. Процесс производства строительных блоков прост: готовые смеси в специальных формах подвергаются полусухому вибропрессованию, а потом сушатся и обжигаются в производственных печах. В зависимости от состава смеси, соотношения наполнителей этим же способом получаются не только керамзитобетонные, но и пескоцементные блоки, пеноблоки.
Видео как делают:
В хозяйственных постройках раньше первенство принадлежало шлакоблокам. Шлакоблоки в качестве наполнителя содержат в себе золу, доменные шлаки, отходы керамического производства. Разница в ценах практически незаметна, однако, блок обладает гораздо более высокими эксплуатационными качествами, нежели шлакоблок. Словом, преимущества значительны. В домашнем строительстве кирпич уже давно начал уступать керамзитобетону по части экономичности, звуко- и теплоизоляции.
Обзор материала:
Такой блок используют во всех видах строительства. Керамзитобетон выпускается в различных видах и фракциях, что позволит выбрать именно то, что необходимо для конкретной постройки. Если сравнивать с кирпичом, то возведение наружных и внутренних стен из данного материала позволит сэкономить порядка 40 процентов денежных средств. Использование керамзитобетона для возведения перегородок в доме или квартире сможет, кроме того, повысить и звукоизоляцию и увеличить используемое пространство на 15 процентов. Приятным моментом является то, что в такие стены можно смело вбивать гвозди. Напрашивается вывод, что это прогрессивный материал, идеально подходящий для строительства: он прочный, морозоустойчивый, долговечный, экономный и экологически чистый. Для разных конструкций используются блоки соответствующего назначения: щелевые, перегородки и другие.
Читайте также
moybiznes.org
Керамзитобетонный блок-Производство-Оборудование-Станки
Оборудование, станки для производства керамзитобетонных блоков
Керамзитобетонные блоки – строительный стеновой материал, производится в виде блоков и полублоков. Обладает рядом преимуществ по сравнению с другими стеновыми материалами. Прежде всего, благодаря своему составу, который включает:
- керамзит (конгломерат обожженной глины)
- вяжущее вещество (цемент)
- вода
Благодаря своему составу керамзитобетонный блок имеет высокую прочность при небольшой массе, не гниет и не выделяет вредных веществ, обладает высокими теплоизоляционными свойствами и является экологически чистым материалом.
Технология производства керамзитобетонных блоков включает в себя несколько этапов:
- Подготовка керамзитной смеси ( загрузка всех компонентов в бетоносмеситель и перемешивание).
- Подача готовой смеси в оборудование для производства (вибропресс).
- Укладка бетонной смеси и ее прессование с получением готовых керамзитовых блоков.
- Сушка и складирование готовых изделий.
Для изготовления керамзитобетонных блоков применяют комплексное производственное оборудование, которое включает в себя систему дозирования и перемешивания исходных материалов (бетоносмеситель с дозаторами), транспортировку керамзитобетонной смеси (транспортер) и формования готовой смеси (вибропресс).
Предлагаем Вашему вниманию линии-станки для производства керамзитобетонных блоков:
Рифей-Буран | ||
Стоимость линии | 3 250 000 руб | |
Керамзитовые блоки | 500 шт/час | |
Плитка тротуарная | 56 кв м/час | |
Мощность | 41 кВт | |
Масса | 12,5 тонн | |
Рифей-Полюс | ||
Стоимость линии | 2 685 000 руб | |
Керамзитобетонные блоки | 420 шт/час | |
Плитка тротуарная | 45 кв м/час | |
Мощность | 33 кВт | |
Масса | 9 тонн | |
| Рифей-Удар | |
Стоимость линии | 1 545 000 руб | |
Керамзитоблоки | 330 шт/час | |
Плитка тротуарная | 28 кв м/час | |
Мощность | 22 кВт | |
Масса | 4,4 тонн | |
Рифей-РАМ | ||
Стоимость станка | 895 000 руб | |
Керамзитоблоки | 200 шт/час | |
Плитка тротуарная | 10 кв м/час | |
Мощность | 16 кВт | |
масса | 3 тонны | |
Рифей-04ТС | ||
Стоимость линии | 613 000руб | |
Керамзитоблоки | 150 шт/час | |
Плитка тротуарная | Не производит | |
Мощность | 15 кВт | |
Масса | 2,7 тонн | |
Кондор | ||
Стоимость станка | от 220 000 руб | |
Керамзитовые блоки | 100 шт/час | |
Плитка тротуарная | 7 кв м/час | |
Мощность | 7 кВт | |
Масса | от 650 кг |
Следует отметить, что производство керамзитобетонных блоков своими руками практически невозможно, так как для стабильного качества выпускаемых блоков необходимы специальные станки или линии по производству керамзитобетонных блоков, которые в своем составе имеют специальный бетоносмеситель с дозаторами, транспортер, пресс и другие необходимые устройства.
Производство керамзитобетонных блоков – Видео: На примере линии "Рифей – Удар"
Представленное оборудование рекомендовано МинСтроем РФ для изготовления бетонных изделий на территории России, а так же стран СНГ( Казахстан, Белоруссия, Украина, Узбекистан и т.п)
rifey-kondor.ru
Производство керамзитобетонных блоков на заводе компании ООО «Калита»
ООО «Калита», используя современные технологии, профессионально занимается изготовлением строительных материалов с 2000 года. В это время заработал наш завод керамзитобетонных блоков в г. Алексин Тульской области. На сегодняшний день изделия производятся на двух высокопроизводительных линиях Златоустовского производства Рифей-Универсал.
Являясь одним из лидеров по производству сертифицированных керамзитобетонных блоков в центральном регионе, предприятие выпускает широкий ассортимент продукции: более 10 видов наименований товарных единиц с объемом более 140 м3 блоков.
На данном этапе развития строительной отрасли производство керамзитобетонных блоков с точным соответствием ГОСТ 6133-99 осуществляется методом полусухого вибропрессования.
Технологические этапы производства керамзитоблоков:
- Смешивание компонентов в бетономешалке.
- Формовка изделий на вибрационно-прессовальном оборудовании.
- Сушка блоков.
- Складирование готовой продукции.
- Транспортировка блоков заказчику.
В производственный цех подается исходное сырье: песок, керамзит мелкой фракции, цемент. Все составляющие обладают регламентируемыми ГОСТ характеристиками.
Подача песка
Подача керамзита
Подача цемента
От процентного содержания того или иного компонента зависят свойства готовой продукции.
Благодаря соблюдению оптимальных пропорций получаются универсальные керамзитобетонные блоки с уникальными характеристиками: прочные, легкие, с высокими звуко- и теплоизоляционными качествами.
Бетоносмеситель
Далее происходит смешивание компонентов бетонной смеси.
Замес керамзитобетона
Последовательность поступления в бетоносмесительную установку исходных компонентов такова: первой в емкость поступает вода, затем идет засыпка керамзитового гравия, далее – цемента, и только в последнюю очередь – песка. Автоматическая поддержка уровня воды обеспечивается поплавковым механизмом.
Выход блоков
Приготовленная растворная смесь отправляется на формовку. На этом этапе происходит наполнение рабочей смесью формообразующей оснастки.
Непосредственно изготовление керамзитобетонных блоков начинается на специальном оборудовании – вибрационно-прессовальном станке. Форму конечного продукта создают стальные пластины-матрицы, в которые и засыпают приготовленную керамзитобетонную смесь. Процесс вибропрессования исключает возможность образования пространства в стенках изделий, обеспечивая плотную укладку керамзито-бетонной смеси в форму. Давление в гидросистеме пресса создается насосной установкой.
От того, какие матрицы были использованы, керамзитобетонные блоки могут быть различных размеров и видов: полнотелые или пустотелые.
В зону распалубки блоки из керамзитобетона перемещаются после отвердевания.
Камера сушки
После завершения этапа формовки вместе со стальной пластиной блоки перемещают в сушильную камеру. Для окончательного затвердевания готовых изделий требуется определенное время.
Цех
Готовая продукция
После завершения процесса сушки готовые изделия укладывают на специальные товарные поддоны, на которых они хранятся и транспортируются заказчику
Складирование готовой продукции
Заводские условия позволяют нам работать в течение всего года. Стабильное качество сертифицированной продукции обеспечивается за счет комплексного оборудования и точного соблюдения всех звеньев технологического процесса.
Площадка складирования
Мы гордимся не только эффективной технологией производства керамзитоблоков – отправка продукции осуществляется собственным большегрузным автотранспортом. Оперативно, точно в оговоренный срок керамзитовые блоки доставляются на объект заказчика. Автопарк состоит из техники не старше пяти лет. Также для вашего удобства компания предоставляет услугу доставки грузов манипулятором.
Отправка блоков заказчику
ООО «Калита» имеет собственную лабораторию, контроль качества выпускаемой продукции ежедневно проводится на каждом производственном этапе. Независимые специалисты ОАО «Гурово-Бетон» контролируют качество блоков еженедельно. Блоки из керамзитобетона производства «Калита» рекомендованы для применения во всех областях строительства без ограничения, о чем свидетельствует сертификат Тульской областной СЭС.
Результат нашей работы
www.kalitablok.ru