смазка для металлических форм. Смазка для форм
Силиконовые смазки для форм - Справочник химика 21
Для смазки применяют водные растворы мыла, слабые растворы гипосульфита натрия (3—4%-ные), а также силиконовые смазки в виде 1—2%-иых водных эмульсий. Смазку поверхности формы производят кистью или путем разбрызгивания сжатым воздухом. Иногда производят смазку или опудривание заготовок и смазку форм. Закладывание изделий в форму следует производить только после полного высыхания смазки. [c.360]
В настоящее время осваивают применение силиконовых смазок в виде эмульсии или раствора для промазки вулканизационных форм вместо смазки покрышек. Силиконовая смазка образует на поверхности формы тонкую пленку, стойкую к действию те Л-пературы вулканизации. Пленка способствует растеканию протекторной резиновой смеси в процессе вулканизации и предотвращает приваривание покрышки к форме - . [c.455]
Более эффективно, чем описанные выше, работают колонны с насадкой, представляющей собой по возможности мелкозернистый материал, свободно насыпанный в колонну. Насадка может быть изготовлена из стекла, фарфора или металла (бронза, медь, сталь). Стеклянные кольца Рашига не так эффективны, как кольца из проволочной сетки. Применение последних ведет, однако, из-за их большой поверхности, по которой растекается пленка жидкости, к сильному увеличению объема удерживаемой жидкости в колонне. Кроме того, широкое применение в качестве насадки нашли фарфоровые бусинки седловидной формы, разнообразные металлические спирали и др. Очень важно обеспечить идеальное смачивание поверхности колонны и насадки, которое иногда нарушается за счет проникновения в колонну силиконовой смазки из шлифов. При необходимости колонну ополаскивают смачивающим составом или сильно разбавленным раствором плавиковой кислоты, а шлифы смазывают порошком сульфида молибдена. [c.129]
Вулканизация. При подготовке восстанавливаемой покрышки к вулканизации в нее закладывают варочную камеру и на поверхность покрышки наносят саже-тальковую смазку, улучшающую распределение резины в пресс-форме. Рабочую поверхность пресс-формы обдувают воздухом и опрыскивают противопригарной силиконовой смазкой или мыльным раствором. [c.260]
При длительном процессе спекания (и особенно в случае применения силиконовой смазки для стенок формы) на поверхностях гранул, соприкасающихся со стенками, образуются плотные пленки толщиной 20—25 мк. [c.303]
Если отливка после отверждения должна быть извлечена из формы, стенки формы, соприкасающиеся со смолой, следует предварительно покрыть тонким слоем разделительного состава, например силиконовой смазки. [c.191]
Подлежащие металлизации поверхности не должны быть загрязнены силиконовым маслом (поэтому его нельзя применять для смазки форм). Обезжиривание чаще всего проводят при помощи щелочей, применяемых в гальванотехнике для обезжиривания металлических деталей. Применение органических растворителей менее [c.99]
Проверить условия транспортировки и складирования заготовок смазать форму силиконовой смазкой увеличить угол наклона боковых стенок [c.172]
Повторное никелирование при износе пресс-форм можно осуществлять без снятия покрытия. Пресс-формы, покрытые химическим никелем, служащие для прессования резин, обрабатываются силиконовой смазкой или натираются графитовым карандашом во избежание прилипания резин, В качестве примера защиты деталей от коррозии можно назвать химическое никелирование деталей часовых механизмов колонок, анкерных вилок, рычагов, фиксаторов, регуляторов, крепежных деталей и др. Применение N1—Р-покрытия на часовых заводах позволило практически исключить случаи коррозионных поражений часовых деталей в процессе нх сборки и эксплуатации. [c.32]
Съем получаемых заготовок с перфорированных форм облегчается при покрытии поверхности форм силиконовой смазкой. Диаметр ячейки перфорации обычно составляет 3 мм, общая площадь поверхности перфорации — 40%. Толщина получаемых заготовок обычно в 2—3 раза превышает толщину будущего изделия. Рекомендуется формовать заготовки толщиной 6— 10 мм. Толстостенные изделия целесообразно получать из нескольких заготовок, вложенных одна в другую. [c.354]
Формование БК не вызывает затруднений. Из смесей на его основе могут быть изготовлены массивные и полые детали. Благодаря высокой текучести БК при повышенной температуре легко происходит заполнение форм в начальный период вулканизации. Принципы составления рецептуры на основе БК для формовых изделий не отличаются от принципов составления рецептур для аналогичных изделий на основе других каучуков. Низкая когезионная прочность вулканизатов БК при повышенной температуре несколько осложняет съем готовых изделий с горячих форм, но применение силиконовой смазки значительно облегчает съем изделий. [c.172]
Перед заливом пены формы предварительно опрыскивают силиконовой смазкой. Допускается опрыскивать формы 10% раствором хозяйственного мыла. Температура форм 45—80 С. Формы, залитые пеной, плавным опусканием крышки закрываются и прижимаются зажимами. Тележки передвигаются из свободной зоны в зону желатинирования, где температура поддерживается 100—110 °С. Из зоны желатинирования тележка с формами переходит в зону вулканизации, где температура 137—142 °С, и далее в зону охлаждения. После охлаждения открывают зажимы форм и с поверхности крышек форм снимают вулканизованные изделия. Вулканизация длится 85— [c.270]
Бутилкаучук при сушке имеет склонность прилипать к металлическим поверхностям (пластинам конвейера). Эта трудность преодолевается тем, что непосредственно перед тем местом, где на конвейер подается высушиваемый продукт, установлены распылители жидкой силиконовой смазки. Пластины конвейера опрыскиваются силиконовой смазкой с обеих сторон. Сушка завершается в шприц-машине или на вальцах, где полимеру одновременно придается форма ленты. Лента полимера после воздушного охлаждения режется автоматическим ножом и упаковывается. [c.426]
Литье под давлением является методом прецизионной отливки легкоплавких сплавов и металлов. Этим методом пользуются для отливок из цинка, алюминия и бронзы, причем для цинка температура может достигать 430 °С, для алюминия 540 °С и для бронзы 930 °С. Силиконы оказались эффективными смазками при литье цинка и в некоторых случаях—алюминия. Силиконовую жидкость наносят в виде 1%-ной эмульсии пульверизацией. В зависимости от сложности формы и температуры без возобновления смазки можно получить от 1 до 6 изделий. К преимуществам силиконовой смазки относятся ее негорючесть, уменьшение выделения дыма и паров масла в литейных цехах, а также уменьшение так называемой спайки или прилипания металла к форме. [c.206]
При хорошей вентиляции форм, обеспечивающей достаточно полное удаление из них воздуха, и при тщательной смазке форм силиконовыми составами можно отказаться от наружной смазки покрышек без снижения качества выпускаемой продукции. [c.341]
Силиконовые смазки распыливают на поверхность формы пульверизатором, что позволяет получить тончащий слой и экономно расходовать ее. [c.303]
Использовать для смазки формы силиконовую эмульсию, содержащую ингибитор коррозии. [c.88]
Проверить условия транспортировки и складирования заготовок смазать форму силиконовой смазкой увеличить угол наклона боковых стенок Уменьшить диаметр вакуумных каналов или давление формования [c.75]
В случае необходимости нагрева изделия для отверждения связующего, в форму могут быть помещены трубчатые электронагреватели, либо в ней проделаны каналы для теплоносителя, либо саму форму с изделием можно поместить в термокамеру. Для облегчения извлечения изделия из формы между ними наносят разделительный антиадгезионный слой (поливиниловый спирт, силиконовую смазку, целлофан и др.). [c.765]
Исходный диаллилфталат полимеризуют в присутствии 2—5% перекиси [401]. Процесс начинают при 65—66°. При литье необходимо пользоваться предварительно полимеризованным продуктом, иначе усадка отливок достигает 18%. Полимеризованный диаллилфталат применяют для изготовления слоистых пластиков. Пропитанный материал подвергают нагреванию и незначительному давлению. Длительность цикла отверждения для мономера достигает 5—144 часа, а для предварительно полимери-зованного продукта 0,5—4 часа. Через полчаса поднимают температуру с 75—80 до 115—125°. Процесс литья можно проводить в стеклянных, металлических, резиновых, деревянных, гипсовых или восковых формах, смазанных силиконовой смазкой. [c.356]
Прн изготовлении литсм тых (]юрм в виде скорлуп (оболочек ) смесь песка и фенольной смолы (а и настоящее время — песок, зерна которого покрыты тонким слоем смолы) загружают с помощью опрокидывающегося бункера нлн пескодувной машины в горячую форму, в которой находится нагретая (250—280°С) металлическая модель для литья. Предварительно внутреннюю поверхность формы обрызгивают разделительной силиконовой смазкой. После закрытия формы фенольная смола плавится и обволакивает зерна песка, скрепляя их друг с другом. В результате образуется твердая скорлупа, толщина которой зависит от продолжительности контакта формовочной массы с моделью, температуры формы и скорости отверждения смолы. Как только толщина оболочки достигнет 4—7 мм (обычно через 20—30 с), избыток неотвержденной массы удаляют и направляют на повторное использование. Поскольку скорлупа отверждена только с одной стороны, ее затем отверждают с обратной стороны, применяя ИК-излученне илн туннельную нечь. Прн этом получают одну половину формы. Конечная форма состоит из двух таких скорлуп, соединенных вместе механическим зажимным устройством или склеенных термореак-тивными смолами (продолжительность соединения 20—30 с). В зависимости от объема заливки и давления металла такие формы могут быть отформованы в плоских изложницах без применения других онор. [c.214]
Методом литья изготовляют изделия из отверждающихся компаундов на основе мономеров, олигомеров, смол, полимер-мономерных композиций или расплавов полимеров, имеющих консистенцию вязкой жидкости. Компаунд при нормальной или повыш. т-ре заливают в технол. оснастку (форму), в к-рой происходит его отверждение шш затвердевание. Для обеспечения извлечения изделия из формы стенки формы покрывают слоем антиадгезива, напр, отверждающейся силиконовой смазкой. Литьем изготовляют листы, плиты, блоки, разл. рода машиностроит. детали (шестерни, шкивы, кулачки, шаблоны), технол. оснастку для штамповки, литья под давлением и др. методов формования. [c.9]
Крышка калориметрического стакана подгоняется весьма плотно при помощи резиновой прокладки, сжимаемой винтами и болтами в последней модели калориметра (в Эк-зетерском университете) используется резиновая прокладка в форме тора. Калориметрический стакан подвешен внутри вакуумной рубашки при помощи стеклянной трубки, приклеенной к крышке стакана резиновая трубка соединяет стержень и трубку. Пробка вакуумной рубашки выполнена в виде конического сочленения, а силиконовая смазка обеспечивает надежное вакуумное уплотнение. В новейшей модели крышка плоская и прижимается кольцевой прокладкой. [c.393]
Последнее время метилсиликоновые масла благодаря их несовместимости с большинством органических полимеров нашли дальнейшее широкое распространение их применяют в качестве смазывающих срёдств [Т5, Т81] при прессовании, шприцевании и литье под давлением пластмасс, поскольку они обладают многочисленными преимуществами перед чисто органическими и неорганическими смазками [794]. Раньше из смазок органического происхождения применяли главным образом масла, вазелины, парафин, воска и мыла их основным недостатком является малая стойкость к повышенным температурам. Из неорганических веществ применялись слюда, тальк и графит. Однако эти вещества неприятно пылят и загрязняют прессованные изделия. У силиконовых продуктов выгодно сочетаются термостойкость, несмешиваемость с высокомолекулярными соединениями, очень низкая летучесть даже при максимальных рабочих температурах и совершенная химическая инертность к конструктивным материалам формы [Т82]. Силиконовые смазки образуют между пластмассой и металлической формой очень тонкий слой, который позволяет легко извлекать прессованную или отлитую вещь из формы. [c.335]
Производство резиновых изделий, пластмасс, фанеры. Благодаря перечисленным свойствам силиконовые смазки для форм весьма эффективны и экономичны в любых операциях формования. Эти смазки применяются в виде масел и э.Л ульсий в различных отраслях промышленности, но главным образом они используются как смазка форм для вулканизации шин. Для этой цели применяют метилполисилоксаны с вязкостью 300 сст, которые после разбавления наносят на формующие детали и резиновые мешки автоматических машин для изготовления шин. Эмульсию метнлполисилоксана применяют также с целью облегчить отделение протектора шины от формы. Облегченное отделение в результате применения силиконов [c.202]
В последние годы налажен промышленный выпуск ИП на основе феноло-формальдегидных олигомеров (ФФО) и многослойных изделий на их основе [68—72]. Технология изготовления этих материалов в принципе не отличается от технологии получения ИП на основе других полимеризационноспособных олигомеров, например уретановых. Однако для широкого производства ИП на основе ФФО существует ряд ограничений коррозия оборудования, а также высокая адгезия исходных композиций и готовых изделий к металлическим поверхностям оборудования. Последняя трудность преодолима, хотя значительно удлиняет цикл формования в частности, стенки форм покрывают воском и силиконовыми смазками. [c.140]
Для предотвращения прилипания резины к металлу пресс-формы на рабочую поверхность дважды, с интервалом в 1-2 ч, наносят кисточкой тонкий слой 10 %-ного раствора силиконовой смазки МПС-200А (МРТУ-6-02-260-631) в бензине. После сушки второго слоя пресс-формы выдерживают 2—3 ч в термошкафу при 270—280°С. [c.85]
Эксперименты показывают, что разрушение поверхности происходит в начале заполнения формы и возникает обычно в области впускного литникового канала. Так, при литье образцов из сополимера тетрафторэтилена и гексафторпропилена при скорости сдвига 55—70 с разрушений на поверхности не возникает, а при 110— 150с- уже происходит разрушение поверхности образца, которое выражается в отстаивании поверхностных слоев В случае изотермического течения этого сополимера при температуре литья критическая скорость сдвига, при которой наблюдается нестабильность течения, составляет около 200 с" . Если при литье полистирола, например, поверхность формы покрыть силиконовой смазкой, то вследствие изменения коэффициента трения полимера о стенки формы можно наблюдать разрушение поверхности изделия [c.211]
Силиконовые масла особенно пригодны для смазки форм. Вследствие нх низкого поверхностного натяжения они легко распределяются тонкой пленкой по всей поверхностп прессформы будучи теплосто11Кимн, они не разлагаются, форма не загрязняется н срок службы ее увеличивается плохая совместимость с большинством органических полимеров обеспечивает легкость выемки изделия из формы. [c.202]
Силиконовые смазки быстро вытесняют минеральные масла. При применении этих смазок уменьшается опас-1юсть пожара, образование дыма, сажи и грязи, неизбежное при использовании горючих и воспламеняющихся масел. Изделия получаются чище и без черных пятен углерода, а прессованные изделия могут быть изготовлены с меньшими допусками. Сокрашается продолжительность рабочего цикла и реже требуется чистка формы. Поскольку расход силиконового масла значительно меньше, чем минерального, достигается даже снижение себестоимости в одном типичном случае себестоимость снизилась на треть. [c.204]
Полидиметилсилоксаны используются также в лаках, в качестве диэлектрических жидкостей, масел для диффузионных насосов, Б виде водных эмульсий для смазки форм, как антивспе-ниваюш,ие агенты, в качестве водоотталкиваюш,его агента и аппрета в текстильной промышленности. Линейные полидиметилсилоксановые каучуки с молекулярным весом 500 ООО используются при производстве силиконовых резин. [c.354]
В качестве смазочных составов применяют различные мыльные или масляные эмульсии. В последнее время широкое применение нашли кремнийорганические (силиконовые) эмульсии, образующие пленки, препятствующие прилипанию резины к форме. Обычно для смазки форм применяют 1%-ную силиконовую эмульсию, которую получают путем разбавления дистиллированной водой концентрированной эмульсии, содержащей 40% жидкого силокса-на, 40% эмульгирующего вещества и 20% воды. [c.389]
Несмотря на большие преимущества перед другими смазками, силиконовая еще не получила широкого распространения и не вытеснила остальные по неизвестным причинам. Она успешно применяется на Днепропетровском и Московском шинных заводах на протяжении длительного времени, но на остальных заводах применение ее ограничивается экспериментами. Некоторые заводы не применяют силиконовые смазки только по той причине, что считают нерациональным способ нанесения их на прессформы, так как при этом нельзя создать отдельного централизованного участка смазки, как это делается при смазке покрышек сажевыми или мыльными смазками. Те преимущества, которыми обладают силиконовые смазки, настолько значительны, что даже при отсутствии специального пункта нанесения смазки они должны внедряться на шинных заводах. Хорошая распыляемость и способность создавать тончайшую пленку позволяют применять автоматически действующие форсунки для нанесения силиконовых смазок на формы у формат оров-вул-канизаторов и индивидуальных вулканизаторов, что исключает надобность в организации специального пункта смазки. Такие устройства получили распространение в Англии и применяются на Днепропетровском шинном заводе. [c.303]
При получении глубоких изделий формовщику часто трудно удалить готовое изделие из формующего инструмента. При позитивном формовании эти затруднения связаны с усадкой изделия, при негативном — с наличием в форме поднутрений, знаков и т. п. Чтобы облегчить съем таких изделий, рекомендуется через 3—4 формовки сл1азывать формующий инструмент тонким слоем силиконовой смазки. [c.83]
chem21.info
Смазка для форм и листов
Союз Советских
Социалистических
Республик
Qn NCAHNIE
ИЗОБРЕТЕН ИЯ
К АВТОРСКОМУ СВИДЕТЕЛЬСТВУ
„„7ЗЗБО2 (6! ) Дополнительное к авт. свил-ву— (22) Заявлено 12.04.77 (21) 2477259/18-13 с присоединением заявки ¹â€” (23) Приоритет
Опубликовано 15.05.80. Бюллетень ¹ 18
Дата опубликования описания 15.05.80 (51)М. Кл.
А 21Э 8/08.Всудерстееиный комитет пв делам изобретений и открытий (53) УДК 621,,89 (0 88. 8) Р, Я, Лейтес, О, А. Клокачева, Л. Ф. Шеголева, А, А. Шмидт, А. Е. Лехтер, Б, С. Шейнтова, 3. И. Шмелева, В. М, Баринский и 10. К. Подкопаев
;", Д 1 .) 0"
Московский филиал Всесоюзного научно-исследовательского института жиров и Кондитерско-булочный комбинат Черемушки
1 -.
1 (72) Авторы изобретения (7I) Заявители
li
::4 .. 4 ° (54) СМАЗКА ДЛЯ ФОРМ И ЛИСТОВ
Изобретение относится к смазкам для форм и листов, используемым в пищевой промышленности, например, при производстве мучных кондитерских изделий.
Широко известны составы смазок для форм и листов, применяемых для выпечки мучных изделий, в частности хлеба, представляющие собой жироводньте эмульсии или силоксановые полимеры. Но и те и другие имеют ряд недостатков.
Так, жироводные эмульсии неустойчи10 вы во времени, содержат до 90-95% воды, неэкономичны пои,применении, транспортировании и хранении и, кроме того, в зимнее время могут замерзать.
15 формы покрытые силоксановыми полимет рами, требуют дополнительной термической обработки для отверждения полимера и поэтому для выпечки рыхлых мучных кондитерский изделий силоксановые покрытия не пригодны.
Из известных смазок наиболее близкой по составу к предлагаемой является смазка для форм и противней, включающая растительное масло, саломас пищевой, ацетопроизводные моноглицериды, фосфорсодержашую добавку, в качестве которой взят лецитин, причем компоненты взяты в следующем соотношении, вес, 4:
С ое вый лецити н. 30-60
Растительное масло 30-39
Ацетопроизводн ые мо ноглицерид ы 5-25
Силиконовое ьласло 2 — 2 Ц, Основной составной частью известной смазки является дорогостоящий и дефицитный лецитин, а также дорогостоящее силиконовое масло, введенное якобы для усиления смазываюшей способности лецитина. Силиконовое масло обладает антипенным,действием и отрицательно влияет на структуру и объем готового изделия, особенно рыхлых пенообразных мучных кондитерских продуктов.
Кроме того, составляющий до 60% общей массы фосфорсодержащий продукт— соевый лецитин- дорогостоящий и дефио питный уже при 150 С начинает разла1
733602 смесью моно- и диглицеридов или их ацетспроизводными и смеси растительного масла и пищевого саломаса обеспечивает высокую эффективность смазываюгдего действия и универсальность применения, Растительное масло (например, под-солнечное, хлопковое) и саломас пищевой должны быть рафинированными, дезодори10 рованными. В качестве фосфорсодержащей о- добавки используют фосфатидный концентрат, предпочтительно соевый или подсоли- нечн ый.
Предлагаемая смазка — полужидкий
15 продукт светло-коричневого цвета со слабым жировым запахом, имеет температуру о каплепадения 26-30 С и вязкость при
40 С 3845 сП.
Пример 1.
20 Масло подсолнечное 37
Саломас соевый пищевой . 44
Ацетилированные моноо) глицерид ы фосфатидный концентрат соевый пищевой 7
t о
Температура каплепадения продукта с- 28 С, вязкость при 40 С 43,7 сП.
Подобная смазка может быть приготовлена с ацетилированными моно- и диглицеридами.
П ример 2.
Масло подсолнечное 39
Саломас подсолнечный пищевой 42
Ацетилированные моноглицериды фосфатидный концентрат соевый или подсолнечный пишевой 8
40 о
Температупа каплепадения, 26 С, вязкость при 40 С 38,0 сП, Пример3, Масло хлопковое 41 р Сал омас п од сол не чн ый
45 пищевой 40
Ацетилированные моног лице рид ы 10 фосфатидный концентрат вый пищевой 9
50 гаться с образованием триметила мина, обладающего рыбным запахом. Поэтому применение смазки с таким высоким содержанием лецитина в производстве пищевых продуктов, особенно мучньгх кондитерских изделий, нежелательно.
1гелью изобретения является повышение качества смазки и ее удешевление.
Указанная цель достигается путем введения в смесь растительного масла, саломаса пищевого, ацетопроизводных м ноглицеридов в качестве фосфорсодержашей добавки фосфатидного концентрата и щевого, при этом компоненты взяты в следующем. соотношении, вес,%:
Масло растительное 37-41
Саломас пищевой 40-44
Аце топ роиз вод н ые моног лицеридов 10-12 фосфатидный концентрат 7-9 фосфатидный концентрат, введенный в смазку в небольшом количестве (7-9/ является дешевым побочным продуктом процесса рафинации растительных масел.
Он содержит фосфатидов только 55-60% причем в их состав входит целый ряд фо форсодержащих веществ, таких как кефалины, фосфатидилсерины, фосфатидилинознты, фосфатидные кислоты, а также лецитин, остальные 40-45% составляет растительное масло. Смазывающий эффект данной смазки обеспечивается за счет наличия в ней фосфатидного концентрата, ггредставляюшего собой целый комплекс указанных фосфорсодержащих веществ, а также растительного масла, причем лецитина в этом комплексе фосфбрсодержащих веществ в 20-40 раз меньше, чем в известной смазке. Резкое снижение ко личества лецитина в смазке устраняет опасность образования в процессе выпечки триметиламина. Содержащийся в фосфатидном концентрате комплекс фосфо содержащих веществ в совокупности с моноглицеризами или смесью моно- и дигли церидов или их ацетопроизводными обеспечивает отличное смазывающее действие смазки при исключении силиконового масла.
Предлагаемая смазка отличается принципиально другой основой, в качестве которой используют доступные отечественные растительные масла и саломас. Смазка благодаря применению фосфатидного
55, концентрата, содержащего комплекс фосфорсодержащих производных глицеридов, в совокуггности с моноглггцеризами или о
Температура каплепадения 26 С, вязкость при 40 С 40, 1 сП.
Способ приготовления смазки черезвычайно прост и сводится к следующему.
Компоненты в соответствующих рецептуре количествах загружают в снабженную ме.цалкой, обогревом и охлаждением емкость, нагревают при перемешивании до
733602
10-1 2
7-9
Составитель М. Осипова
Редактор Е. ХоринаТехредж. КастейевичКорректор M. Пожо
Заказ 1929/4 Тираж 41.8 Подписное
11НИИПИ Государственного комитета СССР по делам изобретений и открытий
113035, Москва, Ж-35, Раушская наб., д. 4/5 филиал ППП Патент, г. Ужгород, ул. Проектная, 4 и
45-50 С. Перемешивание продолжают до получения однородной смеси. Затем смесь при перемешивании охлаждают до 30-32 С о и выгружают.
Предлагаемая смазка готова к приме- 5 нению. формы, покрытые ею, не требуют дополнительной обработки. Наличие поверхностно-активных веществ в составе смазки обеспечивает отличное смазывающее действие. Образующаяся при выпечке тонкая высокоэффективная пленка предохраняет изделие от прилипания и обеспе« чивает легкое и полное (без повреждений) отделение его от формы.. При этом нижняя корка изделия гладкая, с блеском. Отсутствие в рецептуре силиконового масла позволяет использовать смазку и в производстве пенообразных мучных кондитерских изделий без ухудшения их структуры и снижения объема.
Согласно результатам производственных испытаний смазка технологически и экономически эффективна. Она может быть успешно использована при выпечке бис25 квита, в том числе и на поточно-механизированной линии по производству бисквитных тортов длительного хранения, взамен применяемой смазки на импортном дефицитном и дорогостоящем сырье. формула изобретения
Смазка для форм и листов, включающая растительное масло, саломас пищевой ацетопроизводные моноглицеридов и фосфорсодержащую добавку, о т л и ч а ющ а я с я тем, что, с целью повышения качества смазки и ее удешевления, в качестве фосфорсодержащей добавки используют фосфатидный концентрат пищевой, при этом компоненты взяты в следующем соотношении, весЯ,:
Масло растительное 37 4 1
Саломас пищевой 40-44
Ацетопроизводные моноглицеридов фосфатидный концентрат
Источники информации, принятые во внимание при экспертизе
1. Патент фРГ ¹ 1 22 1 16 1, кл. 2 с, 5, опублик. 1967 (прототип).



www.findpatent.ru
Разделитель-смазка для гипсовых форм - Илена Ельина
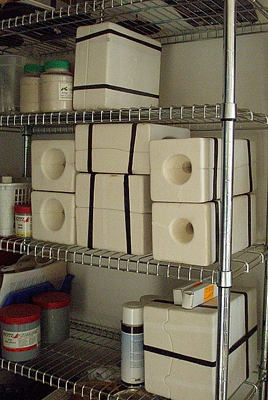
Столь популярный разделитель готовится из кускового мыла и солярки. Мыло нужно брать самое дешевое, без ароматизаторов, лосьонов и увлажнителей. В России это "Детское" и светлое "Хозяйственное". Темное "Хозяйственное" не подойдет, оно щелочное.
Мыло надо настругать на терке, на стороне с круглыми дырочками с рваными краями. Это довольно утомительно, но если стругать на крупные кусочки, трудно будет распустить его в солярке без комков. Наструганное мыло заливаем стаканом солярки и ставим на водяную баню, постоянно размешиваем. Важно: не пользуйтесь при этом газовой плитой, пары солярки могут воспламениться!Солярку время от времени подливаем. Куски мыла бывают разного размера, и сколько потребуется солярки не известно. Нам нужно получить консистенцию гуще, чем зубная паста, но мягче, чем гуталин - примерно что-то среднее между ними. Если после долгого перемешивания на водяной бане однородной консистенции добиться не удается, можно разбить комочки блендером.
На 1 кусок мыла уйдет приблизительно пол литра солярки. Но берите солярку с двойным запасом. Во-первых может уйти больше 1/2 литра, во-вторых долго хранящаяся смазка начинает подсыхать сверху, образуя мешающиеся корочки, т.к. солярка очень летучая.
Я часть смазки откладываю во вторую банку и заливаю слоем оставшейся солярки для хранения.
Полученный разделитель наносится щетинной кистью тонким слоем - просто намазали кисточкой, как будто покрасили. Через пару минут - второй слой.
Смывка.
Готовую форму надо не откладывая промыть. Промываем поролоновой губкой горячей водой с жидким мылом. Мне "Ариэль-гель" в этом применении нравится больше, чем жидкое мыло для посуды. Мылом для рук промывать не следует, оно содержит смягчающие масла. Затем ополаскиваем проточной водой и замачиваем в теплом растворе соды. Не надо делать слишком концентрированный раствор, его будет трудно полностью вымыть из формы, и форма поростет содовыми "сталагмитами". Что в принципе не страшно, их достаточно просто смести кисточкой.Можно обойтись без соды, но раз на раз не приходится, а переделывать всю работу по формовке - адский труд. Если черепок плохо насасывается, то одна из причин - забитые плохо смытой смазкой поры. Это касается любой смазки, и крема, и вазелина. И если маленькие формы можно как следует вымыть без соды, то большие так легко не промоешь.
И заодно скажу, чем удобнее всего обкладывать модель.
Если вы собираетесь снять форму с головы Давида в натуральную величину, то лучше традиционной глины ничего не придумаешь. Нам можно обойтись и без глины, она развозит жуткую грязь, даже больше, чем гипс.Обычный модельный пластилин для художников содержит воск, который плохо вымывается. Кроме того он довольно твердый, большие модели им обкладывать тяжело.
Лучшая обкладка, на мой взгляд - детский модельный пластилин Джови в больших пачках. Он мягкий, его не надо разогревать, он легко выравнивается. И он не содержит воска, поэтому легко и просто смывается с форм. И еще один плюс Джови - он не плавится от разогревающегося гипса.
ilinadolls.livejournal.com
Смазки для форм - Справочник химика 21
Для снижения водопоглощения и набухания ДВП вводят воск ( 1% от массы сухих волокон) или парафин. Кроме того, могут быть добавлены антипирены, фунгициды и инсектициды, смазки для форм и др. [c.139]Смазка для форм Сушильная установка Температура, °С, не выше Свойства препрега Содержание смолы, /о Текучесть смолы, % [c.187]
В результате утилизации верхнего слоя можно получать смазку для форм по производству железобетонных изделий — дорожное, вяжущее, а также сжигать его в смеси с мазутом при производстве цемента. [c.349]
Антиадгезионные Обработка форм Смазки для форм [c.422]Смазки для форм. . Резиновая, стекольная, [c.139]
Д о в ж и к О. И., Ратинов В. Б., Эффективные смазки для форм в производстве сборного железобетона, Стройиздат, 1966. [c.167]
И отвердителя. 13 качестве смазки для форм пригодны кремнийорганические масла и растворы кремнийорганических смол. [c.663]
Смазки для форм в производстве железобетонных изделий [c.203]
Ароматичес1с1[е соединения верхнего слоя используют для получения смазки для форм по производству железобетопны.х и делий, дорожного вяжущего или сжигают в смеси с мазутом ]фи производстве цемента. Средний водный слой нейтрализуют с помощ ) о известковых материалов, одновременно происходит его очистка от органических соединений. Нижний слой нейтрализуют, переводят в твердое состояггпе и хранят в условиях, исключающих размывание атмосферными осадками. [c.138]
Смазочные вещества и смазки для форм. В большинстве случаев при получении формовочных материалов приходится применять смесь нескольких смазочных веществ. В рецептуры вводят до ] % таких веществ. Для снижения адгезии материала к металлам применяют наружные смазки, которые улучшают загрузочные свойства пластифицированных материалов и действуют в качестве смазки для форм. Введение внутренней смазки влияет на текучесть расплава, снижая вязкость, давление впрыска и улучшая гомогенность расплава. Положительный эффект от введения внутренней смазки возрастает по мере увеличения ее полярности и растворимости в фенольных смолах. В качестве смазок могут использоваться спирты жирного ряда, сложные эфиры жирных кислот или амиды жирных кислот. Соли жирных кислот подобно стеаратам кальция или магния занимают промежуточное положение. Нарулфенольных смолах. К. ним относятся парафиновые углеводороды и воски. [c.154]
Новолачная смола с температурой плавления 70—75°С должна иметь низкую вязкость расплава, что обеспечивает быстрое получение равномерного покрытия. Водный раствор ГМТА следует вводить лишь после того, как смесь охладится водой примерно до 100 °С это предотвращает излишнее проникновение смолы в поры между зернами песка. В том случае, когда в формовочной массе образуются комки, которые распадаются ири охлаждении смеси, то следует добавить в массу смазку для форм, затем всыпать песок ири 60—65 °С, просеять его, охладить до 30 °С в исевдоожнжеи-ном слое, чтобы предотвратить комкообразование, и еще раз загрузить в бункер. [c.216]
Токсическое действие. Раздражает кожу, вызывая папулезные и пузырьково-папулезные высыпи. Отчасти действию К. приписывался также дерматоз у выдувальщиков столовой стеклянной посуды и бутылок (при этом применяется смазка для форм, в состав которой входит также и К-). Описан случай тяжелой бронхиальной астмы у химика, долгое время работавшего с сильно перегреваемой К. (Лихт). [c.528]
К этой группе способов можно отнести и склеивание пластмасс растворителями. При соединении же двух разнородных полимеров целесообразнее использовать клей. На первый взгляд склеивание пластмасс менее сложный процесс, чем склеивание металлов. Однако это не совсем так. Работа с полимерными материалами практически гораздо сложнее работы с металлами. Существенно не только непостоянство молекулярно-массового распределения, но также то, что пластмассы содержат большое количество различных добавок, многие из которых препятствуют склеиванию (например, воски, добавляемые для улучшения обрабатываемости, пластификаторы, смазка для форм и т. д.). Несмотря на это, склеивание — вполне оправданный способ соединения как одинаковых, так и различных пастмасс. При этом [c.164]
Электроизоляция Слоистые пластики и пре . -макриалы Смазки для форм Защитные покрытия Водоотталкивающие покрытия [c.140]
Гидрофсбизирующие жидкости Смазки для форм Полировальные составы [c.140]
Смаз - и для форм снижают затрату усилий на отделение готовсго изделия от формы. Хорошая смазка для формы должна эффективно действовать, будучи нанесена в виде очень тонкой пленки. Она должна быть стойкой к различным воздействиям и к нагреванию и обладать минимальной совместимостью с органическими полимерами, ка основе которых готовится изделие. До появления силиконовых с лазок, для смазки прессформ обычно применяли органические вещества, которые разлагались при высоких температурах, обычных для операций прессования. Продукты разложения пригорали к поверхности формы 1 делали ее менее гладкой, что не только ухудшало внешний вид издели , но и затрудняло отделение изделия от формы. Загрязненные форлш приходилось очищать, что ие только снижало производительность труда, но и портило самую форму из-за появления царапин на полированных поверхностях. Испорченные формы при последующем использовании требовали еще большей чистки, и в конечном счете срок службы прессформ сильно снижался. [c.202]
Производство резиновых изделий, пластмасс, фанеры. Благодаря перечисленным свойствам силиконовые смазки для форм весьма эффективны и экономичны в любых операциях формования. Эти смазки применяются в виде масел и э.Л ульсий в различных отраслях промышленности, но главным образом они используются как смазка форм для вулканизации шин. Для этой цели применяют метилполисилоксаны с вязкостью 300 сст, которые после разбавления наносят на формующие детали и резиновые мешки автоматических машин для изготовления шин. Эмульсию метнлполисилоксана применяют также с целью облегчить отделение протектора шины от формы. Облегченное отделение в результате применения силиконов [c.202]
Если в качестве литьевого компаунда употребляют твердые смолы, то отливку изделий производят следующим образом смолу нагревают до ПО—120°С, добавляют отвердитель (иногда и пластификатор), тщательно перемешивают, вливают в горячем состоянии в форму и отверждают при 100—200° С в течение 1—48 ч, в зависимости от температуры и отвердителя. В качестве смазки для форм пригодны кремнийорганические масла и растворы кремнийоргаг]ических смол. [c.685]
chem21.info
Смазка для форм
Изобретение относится к технологии изготовления бетонных, железобетонных изделий и строений. Смазка содержит, мас.%: отработанное минеральное масло - 50-85, кубовый остаток производства мыла из растительных масел - 15-50. Технический результат - снижение расходных норм смазки, снижение ее стоимости и повышение качества поверхности получаемых изделий и строений, особенно крупногабаритных и сложной конфигурации. 1 табл.
Изобретение относится к технологии изготовления изделий из бетона и сборного железобетона, а именно к составам для смазки металлических форм.
Для приготовления смазок широко используются чистые и отработанные минеральные масла с различными добавками. Известные смазки обеспечивают легкую распалубку изделий, но отличаются малой вязкостью, стекают с бортов формы, образуют пятна на готовой продукции. Известна смазка для металлических форм при изготовлении бетонных и железобетонных изделий на основе отработанного минерального масла и органической добавки - низкомолекулярного полиэтилена при следующем соотношении компонентов, мас.%: Отработанное минеральное масло - 90-96 Низкомолекулярный полиэтилен - 4-10 (а.с. СССР 268235, кл. В 28 В 7/38, 68). Эта смазка не позволяет получить высокое качество поверхности бетона, использовать ее при отрицательных температурах и предусматривает повышенный расход минерального масла. Известна смазка для форм при изготовлении бетонных изделий, включающая отработанное минеральное масло, в качестве которого используется соляровое масло, органическую добавку - синтетические жирные кислоты и солидол при следующем соотношении компонентов, мас.%: Соляровое масло - 76-77,5 Солидол - 15-18 Синтетические жирные кислоты - 6,0-7,0 (а.с. СССР 487730, кл. В 28 В 7/38, 73). Указанная смазка предназначена преимущественно для изделий автоклавного твердения и не может быть использована при отрицательных температурах. К недостаткам этой смазки также относится невысокое качество поверхности изготавливаемых бетонных изделий, особенно сложной конфигурации - масляные разводы, поры и раковины. Наиболее близкой по технической сущности к предлагаемому изобретению является смазка для форм при изготовлении бетонных и железобетонных изделий, содержащая отработанное минеральное масло 50-70% и головную фракцию C10-C23 отходов вакуумпереработки смеси высших синтетических жирных спиртов 30-50 мас.% (А.С. 1049253, кл. B 28 B 7/38, опубл. 23.10.1983). Задачей, на решение которой направлено изобретение, является снижение расходных норм, себестоимости смазки и увеличение срока ее хранения. Указанная задача решается за счет того, что смазка для форм при изготовлении бетонных и железобетонных изделий, включающая отработанное минеральное масло, содержит кубовый остаток производства мыла из растительных масел, производимый по ТУ 18 РСФСР 486-17 под названием "Жировая композиция", при следующем соотношении компонентов, мас.%: Отработанное минеральное масло - 50-85 Кубовый остаток производства мыла из растительных масел - 15-50 Кубовый остаток производства мыла из растительных масел содержит 40-60% олеиновой кислоты и остальное смесь высших нормальных кислот, углеводородов, лактона, полимеризованных продуктов, нейтральных жиров и др. Смазку готовят следующим образом: в расчетное количество разогретого до 70-90oС отработанного минерального масла при непрерывном перемешивании медленно добавляют разогретый до 60-65oС кубовый остаток производства мыла из растительных масел (жировую композицию). В зависимости от вязкости отработанного масла изменяют количество вводимой жировой композиции. Чем ниже вязкость минерального масла, тем большее количество кубового остатка производства мыла из растительных масел (жировой композиции). Смазку наносят на поверхность формы любым известным способом (кистью, щеткой, валиком или с помощью распыляющих устройств), после чего в форму заливают бетонную массу. В процессе формования смазка не расслаивается на компоненты, не образует капель и не обладает механической прочностью, поэтому распалубка крупногабаритных изделий и сложной конфигурации возможна с минимальными трудозатратами. В таблице приведены варианты состава смазки и результаты ее испытания, в сравнении с преимущественно используемым в строительстве эмульсолом ЭКС. Из примеров видно, что предлагаемая смазка обладает высокой эффективностью. Кроме того, смазка не образует на поверхности бетона пятен, снижается расходная норма, благодаря использованию отходов производства, имеет невысокую стоимость и не расслаивается при длительном хранении.Формула изобретения
Смазка для форм при изготовлении бетонных и железобетонных изделий, включающая отработанное минеральное масло, отличающаяся тем, что она дополнительно содержит кубовый остаток производства мыла из растительного масла при следующем соотношении компонентов, мас. %: Отработанное минеральное масло - 50-85 Кубовый остаток производства мыла из растительного масла - 15-50РИСУНКИ
Рисунок 1Похожие патенты:
Изобретение относится к промышленности строительных материалов, а именно к смазкам для форм при изготовлении бетонных и железобетонных изделий
Изобретение относится к промышленности строительных материалов, а именно к смазкам для форм при изготовлении бетонных и железобетонных изделий
Изобретение относится к области строительного производства, и может быть применено при изготовлении бетонных и железобетонных изделий и конструкций
Изобретение относится к области промышленности строительных материалов и может быть использовано при производстве штучных изделий (блоки, плиты, стеновые камни и т.п.) из гипса
Изобретение относится к производству строительных материалов и конструкций, в частности к производству строительных блоков, панелей, плоских и пространственных конструкций из ячеистого и монолитного /тяжелого, легкого/ бетона
Изобретение относится к производству керамических изделий, преимущественно строительного кирпича способом пластического формования
Изобретение относится к промышленности строительных материалов, а именно к смазкам для форм при изготовлении бетонных и железобетонных изделий
Изобретение относится к промышленности строительных материалов, а именно к смазкам для форм при изготовлении бетонных и железобетонных изделий
Изобретение относится к промышленности строительных материалов, а именно к смазкам для резиновых форм при изготовлении бетонных изделий
Изобретение относится к промышленности строительных материалов, а именно к смазкам для резиновых форм при изготовлении бетонных изделий
Изобретение относится к промышленности строительных материалов, а именно к смазкам для резиновых форм при изготовлении бетонных изделий и мелкозернистого бетона
Изобретение относится к смазочно-охлаждающим эмульсолам на основе нефтепродуктов и может быть использовано в производстве бетонных и железобетонных изделий и строительных конструкций
Изобретение относится к смазкам, к промышленности строительных материалов, а именно к смазкам для резиновых форм при производстве бетонных изделий и мелкозернистого бетона
Изобретение относится к промышленности строительных материалов, а именно к смазкам для форм и опалубок, используемых при изготовлении бетонных и железобетонных изделий и конструкций
Изобретение относится к смазкам для форм в производстве бетонных и железобетонных изделий
Изобретение относится к промышленности строительных материалов, а именно к смазкам для металлических форм при производстве бетонных и железобетонных изделий
Изобретение относится к технологии изготовления бетонных, железобетонных изделий и строений
www.findpatent.ru
Смазка для форм в производстве бетонных изделий
ОПИСАНИЕ ИЗОБРЕТЕН
К ПАТЕНТУ
Комитет Российской Федерации по патентам и товарным знакам
1 (21) 4955496/33 (22) 0805.91 (46) 15.1293 Бюд йв 45-46 (71) Научно-производственное объединение "Океанприбор" (72) Мишина О.В„Иванова В.И.; Тагильцев О.Г. (УЗ) Завод "Ладога" (54) СМАЗКА ДЛЯ ФОРМ В ПРОИЗВОДСТВЕ
БЕТОННЫХ ИЗДЕЛИЙ (57) Изобретение относится к производству строительных материалов и может быть использовано для смазки металлических форм при формовании бетонных иэделий. Цель изобретения — улучшение качества поверхности изделий при тепловой обработке бетона за счет повышения водостойкости смазки, смазывающей способности и уменьшения адгезии бетона к металлической форме. Смазка дпя форм, включающая минеральное масло, каль(в) RU (») 2004436 С1 (51) 5 В 28 В 7 38 цинированную соду, нефтяной масляный эмульсоп и моющий раствор, дополнительно содержит порошок алюминия и железа, а в качестве моющего раствора синтетические моющие препараты типа
МЛ при следующем соотношении ингредиентов, мас%: нефтяной масляной эмупьсол 15 — 20; минеральное масло 1 — 10; кальцинированная сода 5—
10, металлический порошок алюминия и железа (1:
1) с размером частиц 1 мм 1 — 5; синтетические моющие препараты 1 — 3, вода остальное. При использовании отработанных жидкостей метаплорежущего производства в качестве части исходных компонентов для получения смазки в производстве бетона появляется воэможность организовать производство по безотходной технологии и решить вопрос утилизации отходов метаглорежущего производства 2 табл.
2004436
Изобретение относится к производству строительных материалов и может быть использовано для смазки металлических форм при формовании бетонных изделий.
Известна смазка для металлических форм, включающая. мас. :
Эмульсол . 15-20
Соляровое масло. 8-10
Известковое молоко, 70-75
Недостатком такой смазки является загрязнение поверхности иэделия, а также недостаточно высокие пленкообразующие и смазывающие свойства.
Известна также смазка для форм следующего состава, мас, :
Эмульсол 58 — 60
Графитовый наполнитель 35-40
Вода Остальное
Известна также смазка для форм, мас., Эмульсол кислый синтетический 8-19,6
Сода кальцинированная 0,2-1,0
Этилсиликонат или метилсиликонат 10 — 15
Сульфанол 0,2-1,0
Вода Остальное
Применение этих смазок не устраняет прилипания бетонного изделия к форме, смазки плохо удерживаются на вертикальной поверхности, кроме того, смазки содержат дефицитные материалы — графит и кремнийорганическую жидкость, Наиболее близкой к предлагаемому техническому решению по составу ингредиентов является смазка для форм, включающая отработанное веретенное масло, отходы олеиновой кислоты, кальцинированную соду, нефтяной масляный змульсол, уксуснокислый натрий и мыло при следующем соотношении ингредиентов, мас, :
Отработанное веретенное масло 1,0 — 10,0
Кальцинированная сода 0,5-1,6
Нефтяной масляный эмульсол 2 — 10
Мыло 0,05-0.10
Отходы очистки олеиновой кислоты 0,3-3,5
Уксуснокислый натрий 0,3-5,0
Вода Остальное
Эта смазка предназначена для работы в условиях отрицательных температур. В качестве ее недостатков можно отметить, что она плохо удерживается на вертикальной поверхности и не обеспечивает полного исключения адгезии бетона к форме, что сказывается на качестве поверхности изделий, Кроме того. чтобы увеличить первоначальную прочность бетона в соответствии
СНИП5.01.23-83 "Типовые нормы расхода цемента для приготовления бетонов сборных и монолитных бетонных и железобетонных изделий и конструкций" и с требованиями чертежей на изделия при формовании бетона проводится тепловая обработка горячим паром при 60-80 С, при которой из-за низкой водостойкости эта смазка теряет свои смазывающие свойства, Это приводит к неудовлетворительному качеству поверхности изделий из бетона после распалубки из-за наличия вырывов и сколов на ней.
Целью изобретения является улучшение качества поверхности иэделий при тепловой обработке бетона за счет повышения водостойкости и смазывающей способности смазки и уменьшения адгезии бетона к металлической форме, а также снижению
20 себестоимости смазки, Поставленная цель достигается тем, что в состав ингредиентов для смазки кроме минерального масла, кальцинированной соды, нефтяного масляного змульсола, моющих растворов, дополнительно введен порошок алюминия и железа, а в качестве моющего раствора — синтетические препараты типа МЛ при следующем соотношении их, мас, :
Нефтяной масляный эмульсол 15-20
Минеральное масло 1-10
Кальцинированная сода 5 — 10
Металлический порошок
35 алюминия и железа в соотношении (1:1) с размерами частиц
Синтетические моющие препараты 1 — 37
40 Вода Остальное
Добавление металлических порошков в состав смазки служит для повышения ее водостойкости. B процессе варки смазки щелочь, образующаяся при гидролизе кальцинированной соды, реагирует с порошком алюминия, образуя гидроокись алюминия. Та, в свою очередь, взаимодействует с жирными кислотами нефтяного масляного змульсола и образует соответствующие соли (Al-мыла), которые, как известно, обладают хорошими водостойкими свойствами, Порошок железа при взаимодействии со щелочью образует окисленные соединения FezOg Н О,частично переходящие в гидроксиды переменного состава.
В процессе тепловой обработки паром оставшаяся часть Fz03 HzO, находясь в зоне контакта бетона с металлической формой, вступает во,взаимодействие со
2004436 свободной щелочью бетона, образуя гидроокиси переменного состава и уменьшая адгезию бетона к форме, улучшая качество поверхности изделия.
Моющие растворы, содержащие синтетические препараты типа МЛ ° как правило, имеют следующий состав, мас. :
Смачиватель ДБ 1,5 — 8,2
Сода кальцинированная 44-50
Сульфанол 1,0- 1,8
Триполифосфат натрия ЗЗ вЂ” 34
Стекло натриевое жидкое 10-20
В процессе варки смазки поверхностно-активные вещества (ПАВ) ° входящие в синтетические растворы типа МЛ в большом количестве, способствуют катализации реакции гидролиза жирных кислот с образованием коллоидной системы, которая наряду. с солями жирных кислот (R-C00Na), Al-мылами содержит кислые мыла жирных кислот (ЯСООН RCO0Na) и ионы (RCÎO и
Na ), имеющие гидрофобную и гидрофильную части и которые вместе с ПАВ моющих типа МЛ, способны адсорбироваться на поверхности раздела фаз, снижать поверхностное натяжение и улучшать смачиваемость поверхности при нанесении смазки. Кроме того. эти активные группы образуют адгезионный первичный слой мономолекулярной пленки, обращенной к металлической поверхности.
Кроме того, ПАВ взаимодействуют с минеральным маслом в присутствии соды в процессе варки и эмульгируют его. Улучшение смазывающих свойств происходит вследствие образования вторичного слоя в виде бимолекулярных наслоений, которые образуют в неполярной среде (какой является минеральное масло) молекулы жирных кислот. В результате трение твердых поверхностей заменяется трением в слое смазывающего материала, что повышает антиадгезионные свойства бетона к форме.
Пример 1. Способ получения смазки.
В бак для варки смазки обьемом 400 л наливают расчетное количество воды. Воду нагревают водяным паром (с 85 — 90 С), пропуская его через слой жидкости (барботируя) и нагревая жидкость до 50-60 С. Водяной пар подают через трубудиаметром 20 мм с отверстиями ЯЗ вЂ” 5 мм по всей длине, расположенную в нижней части бака на расстоянии 150 мм от днища. Затем загружают кальцинированную соду небольшими порциями (в 3-4 приема), перемешивают смесь
10-15 мин. После чего загружают металлический порошок Al u Fe в соотношении 1:1, синтетический моющий препарат типа МЛ, перемешивают смесь 5 мин. Затем добавляют минеральное масло, перемешивают смесь до исчезновения масляной пленки.
После этого добавляют расчетное количество нефтяного масляного эмульсола, пер".мешивают до полного его растворения. Затем
5 смесь компонентов нагревают водяным паром благодаря барботажу(температуру поднимают в течение 1 ч) и варят смесь при этой температуре 20 мин, пропуская пар. После чего полученную смазку охлаждают.
10 Используемые в примере составы l u ll приведены в тай. 1 (приведены после примера 2).
Пример 2. При приготовлении смазки использованы отходы металлорежущего
15 производства: отработанные смазочно-охлаждающие жидкости (СОЖ), содержащие нефтяной масляный эмульсол и металлические порошки алюминия и железа, отработанное индустриальное масло в качестве
20 минерального и отработанные моющие растворы.
Способ приготовления смазки с использованием отходов металлорежущего производства.
25 Отработанные смазочно-охлаждающие жидкости, отработанные моющие растворы типа МЛ и отработанное индустриальное масло собирают вместе в емкость-накопитель объемом 5 м, оборудованную устройэ
30 ством бярботером) для подачи сжатого воздуха. Это труба с внутренним диаметром
25 мм и с отверстиями С>2 мм. расположенными друг от друга на расстоянии 50 мм.
Барботер расположен на расстоянии 100 мм
35 от днища и проходит по всей длине емкостинакопителя, Затем определяют процент содержания масел в эмульгированной, отстоявшейся части смеси отработанных жидкостей по мето40 дике ГОСТ 2477-65 методом отгонки, причем учитывая большое содержание воды в смеси, для анализа берут 10 мл отстоя через делительную воронку.
Как правило, отработанные жидкости
45 металлорежущего производства содержат компоненты в следующем соотношении;
Эмул ьсол Э ГТ ТУ38-101-145-75 7
Индустриальное масло ИС-20 8
Металлический порошок
50 алюминия и железа в соотношении (.1) 3
Сода кальцинированная 3
Синтетические моющие -препараты типа МЛ 2
Вода Остальное
Полученную. смесь перемешивают сжатым воздухом до исчезновения поверхностной масляной пленки и переливают в бак для варки смазки и нагревают до 50-60 С.
Затем в бак добавляют рассчитанное коли2004436
Таблица 1
Значение инг е иентов, мас., в составе смазки
Ингредиент
Добавляемое стандартное в - во
Соотношение компонентов состав отраб. жидкостей механозаготов, и изв.
Нефтяной масляный эмульсол
Сода кальцинирован15
10
10 ная
Металлический лорошок А! и Fe (соотношен. 1:1) Синтетические моашие препараты типа
2
63
МЛ
Минеральное масло
Во а
77 чество кальцинированной соды до получения соотношения Ill, указанного в табл. 1.
При этом кальцинированную соду добавляют небольшими порциями по 3 — 4 кг при постоянном перемешивании. После этого в бак добавляют рассчитанное количество стандартного эмульсола до получения соотношения lll, укаэанного в табл. 1, и смесь перемешивают. Практически на бак емкостью 400 л к отработанным жидкостям металлорежущего производства добавляют (кг) кальцинированную соду 15; эмульсол
ЭКС 40.
После загрузки всех компонентов смесь нагревают до 85 - 5 С водяным паром (как .в примере 1) и варят в течение 20 мин.
Полученную смазку охлаждают до комнатной температуры.
Результаты проведенных сравнительных испытаний смазки представлены в табл.
2.
Таким образом, из данных табл. 2 следует, что заявляемая смазка обладает лучшими, по сравнению с известной, смазывающими и антиадгезионными свойствами при тепловой обработке паром, что улучшает качество поверхности изделий, формуемых из бетона.
Экономический эффект от использования предлагаемой смазки состоит в использовании отработанных жидкостей металлорежущего производства в качестве части исходных дорогостоящих компонентов. При этом за счет использования СОЖ расход стандартного эмульсола сокращает5 ся на 40-50, минеральное масло полностью заменено отработанным индустриальным, а вместо использования синтетических препаратов типа МЛ использованы отработанные моющие растворы, 10 содержащие эти препараты, Кроме того, в настоящее, время СОЖ, индустриальные масла и моющие растворы металлорежущего производства для обезвреживания и утилизации требуют дорого15 стоящих сложных очистных сооружений или захоронения на специальных полигонах.
Использование предлагаемой смазки в производстве бетона позволяет организовать производство по безотходной техноло20 гии и значительно улучшить экологическую обстановку. (56) Балатьев П.Н. Инструкция по приготовлению эмульсионной смазки 07-2 для форм при производстве железобетонных иэде25 лий. М.: ВНИИЖелезобетон, 1965..
Авторское свидетельство СССР
М 414110, кл. В 28 В 7/38, 1974.
Авторское свидетельство СССР
N. 619344, кл. В 28 В 7/38, 1975.
30 Авторское свидетельство СССР
N 1350032, кл. В 28 B 7/38, 1986.
2004436
Таблица 2
Физико-механические показаХарактеристика смазки
Состав смазки тели изделий из бетона после тепловой об аботки па ом
Наличие мас- Степень адгеляных пятен зии, наличие на поверхно- вырывов и шеВодородный Вязкость по Способность удерживаться на вертикальной поверхноВЗ-4, с показатель рН роховатостей на поверхности после распалубки о мы сти изделия сти.Предлагаемый
Наличие отНет
Есть дельных шероховатостей
Отдельные Отсутствуют
Есть пятна небольшого размера
8,5
Отсутствуют
Есть
Нет
Известный (прототип) Стекает с верт. поверхности
Отдельные Поверхность пятна неболь- шероховата, шаго размера наличие отдельных вы10
ывов
1-5
Остальное
Составитель В, Лебедева
Техред M. Моргентал Корректор M. Петрова
Редактор В. Трубченко
Заказ 3372
Тираж . Подписное
НПО "Поиск" Роспатента
113035, Москва, Ж-35, Раушская наб., 4/S
Производственно-издательский комбинат "Патент", г. Ужгород, ул.Гагарина, 101
Формула изобретения
СМАЗКА ДЛЯ ФОРМ В ПРОИЗВОДСТВЕ БЕТОННЫХ ИЗДЕЛИЙ, включающая нефтяной масляный эмульсол, минеральное масло, кальцинированную соду, моющее средство и воду, отличающаяся тем, что, с целью повышения качества поверхности изделия и снижения адгезии бетона к форме при тепловой обработке в среде пара, она дополнительно содержит смесь порошка алюминия и железа в соотношении 1: 1, а в качестве моющего средствамоющий синтетический препарат типа МЛ . состава, мас.7:
Смачи ватель 1,5-8,2
Кальцинированная сода 44-50
Сульфанол 1-1,8
Триполифосфат натрия 33-34
Натриевое жидкое стекло 10- 20 при следующем соотношении компонентов смазки, мас. :
Нефтяной масляный змульсол 15 - 20
Минеральное масло 1-10
Кальцинированная сода 5- 10
Указанное моющее средство 1-3
Смесь порошка А! и Fe(1. 1) с размерами частиц s 1 мм . 50 Вода !





www.findpatent.ru
смазка для металлических форм - патент РФ 2035300
Использование: при изготовлении бетонных и железобетонных изделий, в качестве смазки для металлических форм. Сущность изобретения: смазка содержит следующие компоненты, мас.%: отработанное моторное масло 15-25, эмульгатор отход масложирового комбината 1-3, кальцинированная сода 0,004-0,2, мел 0,6-0,9 воду - остальное. 1 табл. Изобретение относится к смазкам для форм, применяемых в производстве бетонных и железобетонных изделий. Известна смазка для металлических форм [1] включающая мел и машинное масло при следующем соотношении компонентов, мас. Машинное масло 57-91 Мел 9-43 Однако такая смазка, обладая малой вязкостью, при ее нанесении стекает с бортов формы, не обеспечивая равномерной толщины покрытия, вследствие чего на поверхности готовых изделий образуются жирные пятна. Наиболее близкой к заявляемому составу является смазка [2] для металлических форм при изготовлении бетонных и железобетонных изделий, включающая отработанное масло, эмульгатор погоны-отход масложирового комбината, кальцинированную соду и воду при следующем соотношении компонентов, мас. Отработанное масло 25-50 Эмульгатор-погоны-отход масложирового комбината 4-5 Кальцинированная сода 0,2-0,3 Вода Остальное Эта смазка из-за присутствия в эмульгаторе жирных кислот при нанесении на металлические поверхности, особенно холодные, распределяется неравномерным толстым слоем, что при относительно большом расходе масляного компонента ведет к образованию масляных пятен на готовых изделиях. Цель изобретения исключение образования на поверхности готовых изделий масляных пятен и снижение стоимости смазки. Поставленная цель достигается тем, что смазка для металлических форм при изготовлении бетонных и железобетонных изделий, включающая отработанное моторное масло, эмульгатор отход масложирового комбината, кальцинированную соду и воду, отличающаяся тем, что дополнительно содержит мел при следующем соотношении компонентов, мас. Отработанное моторное масло 15-25 Эмульгатор -отход масложирового комбината 1-3 Кальцинированная сода 0,04-0,2 Мел 06-0,9 Вода Остальное Отход масложирового комбината представляет собой омыленные жирные кислоты, получаемые при рафинировании масел. Смазку готовили путем эмульгирования расчетных количеств компонентов в отработанном моторном масле. Для приготовления смазки использовали отработанное моторное масло, эмульгатор-отход масложирового комбината. Эмульгиpование компонентов осуществляли при комнатной температуре механическим перемешиванием. Полученную смазку наносили на поверхность металлических форм кистью. Однородность смазки определяли визуально по отсутствию расслаиваемости. Для определения качества поверхности бетона формовали образцы кубы с ребром 10 см, которые подвергали пропариванию. Наличие масляных пятен на образцах определяли при осмотре всех граней. В таблице представлены полученные свойства смазки предлагаемого состава с различным содержанием компонентов и известного состава. Из таблицы следует, что смазка предлагаемого состава позволяет исключить образование жирных пятен на поверхности бетона, а также снизить стоимость смазки в 1,5-2 раза по сравнению с прототипом. При расходе отработанного масла менее 15% происходит расслоение смазки, при увеличении свыше 25% на образцах появляются следы масляных пятен. Эмульгатор-отход масложирового комбината способствует образованию более однородных и стабильных смазок. Снижение эмульгатора ниже 1% не обеспечивает стабильности системы, свыше 3% на образцах появляются следы масляных пятен. Кальцинированная сода, вступая в химическую реакцию со свободными жирными кислотами эмульгатора, образует соответствующие мыла, обеспечивающие получение стабильных эмульсий. Как уменьшение, так и увеличение количества соды от оптимальной дозировки приводят к снижению стабильности. Использование мела в количестве менее 0,6% ведет к более длительному перемешиванию, что приводит к удорожанию смазки, свыше 0,9% не способствует дальнейшему улучшению смазки. Использование заявляемого способа смазки для металлических форм позволяет повысить качество готовых изделий за счет исключения образования жирных пятен, рационально использовать отходы производства и снизить стоимость смазки за счет сокращения расхода эмульгатора в 1,5-2 раза.ФОРМУЛА ИЗОБРЕТЕНИЯ
СМАЗКА ДЛЯ МЕТАЛЛИЧЕСКИХ ФОРМ при изготовлении бетонных и железобетонных изделий, включающая отработанное моторное масло, эмульгатор отход масложирового комбината, кальцинированную соду и воду, отличающаяся тем, что дополнительно содержит мел при следующем соотношении компонентов, мас. Отработанное моторное масло 15 25 Эмульгатор отход масложирового комбината 1 3 Калицинированная сода 0,04 0,2 Мел 0,6 0,9 Вода Остальноеwww.freepatent.ru