СПОСОБЫ ИНТЕНСИФИКАЦИИ ТВЕРДЕНИЯ БЕТОНА. Процесс твердения бетона
Процесс - твердение - бетон
Процесс - твердение - бетон
Cтраница 1
Процессы твердения бетона при отрицательной температуре не протекают, бетонная смесь замерзает. [1]
Процесс твердения бетона обусловлен гидратацией находящегося в нем минерального вяжущего и появлением новообразований, в 1 5 - 2 раза больших по объему, чем исходное вещество твердой фазы цементного клинкера. [2]
Процесс твердения бетона значительно ускоряется при повышении температуры и влажности среды. С этой целью железобетонные изделия на заводах подвергают тепловой обработке при температуре до 90 С и влажности до 100 % или же специальной автоклавной обработке при высоком давлении пара и температуре порядка 170 С. Эти способы позволяют за сутки получить бетон прочностью - 70L % проектной. Твердение бетона при отрицательной температуре резко замедляется или прекращается. [3]
Процесс твердения бетона значительно ускоряется при повышении температуры и влажности среды. С этой целью железобетонные изделия на заводах подвергают тепловой обработке при температуре до 90 С и влажности до 100 % или же специальной автоклавной обработке при высоком давлении пара и температуре до 170 С. Эти способы позволяют за сутки получить бетон, прочность которого составляет около 70 % проектной. Твердение бетона при отрицательной температуре резко замедляется или прекращается. [4]
Однако процесс твердения бетона после замораживания протекает медленнее, чем процесс твердения бетона, не подвергавшегося замораживанию. Это, по-видимому, вызывается тем, что бетон и после оттаивания имеет сравнительно низкую температуру, при которой процессы твердения крайне замедленны. При повышении температуры твердение ускоряется и на седьмые сутки наблюдается довольно высокая прочность бетона. [5]
В процессе твердения бетона при химическом взаимодействии цемента и воды выделяется тепло, которое вызывает расширение бетона. Это расширение по величине значительно больше усадки. Расширение особенно опасно в массивных конструкциях, где оно может привести к появлению трещин. Чтобы предотвратить расширение бетона, следует применять цементы с малым тепловыделением, не завышать количество цемента в 1 л3 бетона, а также делать специальные температурные швы. [6]
В процессе твердения бетона цемент выделяет тепло, количество которого зависит от состава и качества цемента, температуры бетона и срока твердения. Это тепло выделяется главным образом в первые 3 - 5 дней твердения. [7]
В процессе твердения бетона в образовавшемся цементном тесте происходит химическая реакция. Большая часть продуктов этой реакции переходит в коллоидное состояние, образуя студнеобразный цементный клей - гель, а меньшая часть продуктов реакции выделяется в виде кристаллов. Некоторые продукты гидратации цемента переходят из коллоидного состояния в кристаллическое, поглощая кристаллизационную воду. [8]
При замораживании процессы твердения бетона не протекают. После оттаивания бетонной смеси и при воздействии положительных температур твердение бетона возобновляется. [9]
Традиционные методы интенсификации процесса твердения бетона в принципе малоэффективны по ряду причин. При большом повышении температуры в процессе пропаривания в момент наибольшего экзотермического эффекта в бетонной смеси усугубляется деструкция цементного камня. Это отрицательно влияет на формирующуюся кристаллогид-ратную структуру цементного камня. [10]
Для повышения активности цемента и ускорения процесса твердения бетона увеличивают тонкость помола заводского цемента путем домола его на вибрационных мельницах. [11]
В исследованиях С. В. Шестоперова с многократной вибрацией в процессе твердения бетона [447] показано положительное влияние этих воздействий на микроструктуру цементного камня, но не определено оптимальный стабильный режим виброактивации. [12]
Повышение температуры до 15 - 20 благоприятно сказывается на процессах твердения бетона. После хранения в течение суток при температуре 15 прочность образцов составляла 349 - й от прочности образцов, хранившихся в течение 14 суток; при температуре 22 прочность образцов составляла 61 % от прочности образцов, хранившихся 14 суток. [13]
Однако процесс твердения бетона после замораживания протекает медленнее, чем процесс твердения бетона, не подвергавшегося замораживанию. Это, по-видимому, вызывается тем, что бетон и после оттаивания имеет сравнительно низкую температуру, при которой процессы твердения крайне замедленны. При повышении температуры твердение ускоряется и на седьмые сутки наблюдается довольно высокая прочность бетона. [14]
Способ термоса основан на использовании тепла, выделяемого цементом в процессе твердения бетона, и тепла, введенного в бетонную смесь путем подогрева материалов при ее приготовлении. Чтобы уменьшить тепло-потери, бетонируемая конструкция дополнительно утепляется матами или другими материалами. Запас внутреннего тепла в бетоне должен покрывать расход тепла при остывании конструкции до момента приобретения бетоном заданной прочности. Способ термоса дает хорошие результаты при бетонировании массивных конструкций. [15]
Страницы: 1 2 3 4
www.ngpedia.ru
Процесс твердения бетона
Твердение бетона или схватывание – это сложный физико-химический процесс, когда цемент взаимодействует с водой и образует новое соединение. Бетонные массы, твердеющие в обычных условиях, прочнеют с течением времени, постепенно, по мере того, как вода поступает в глубь частиц цемента. Даже спустя месяцы твердения внутренняя оболочка зерен цемента еще не до конца вступает в реакцию с водой. Поэтому при влажных условиях схватывание становится прочнее, чем на воздухе. То есть в сухих условиях сроки твердения сводится к нулю из-за отсутствия влаги, необходимой для гидратации цемента.
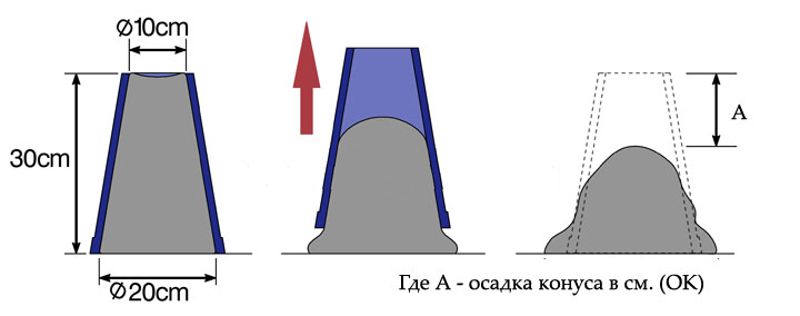
Схема усадки бетона.
При хороших условиях схватывание нарастает быстро, и в течение 7-14 дней после приготовления набирает 60-70% своей 28-дневной прочности. Потом же рост прочности уменьшается. Схватывание при температуре ниже, чем нормальная, замедляется, а при температуре ниже 0°С – почти прекращается, и наоборот, при повышенной температуре и достаточной влажности процесс схватывания ускоряется.
Во время твердения бетон изменяет свой объем: схватывание дает усадку, которая на поверхности происходит быстрее, поэтому при недостатке влаги образуются трещины. Трещинообразование также может быть связано с недостаточным и неравномерным разогревом блока, что снижает прочность и долговечность бетона.
Добавки-ускорители
Для строительных работ время твердения имеет свое значение.
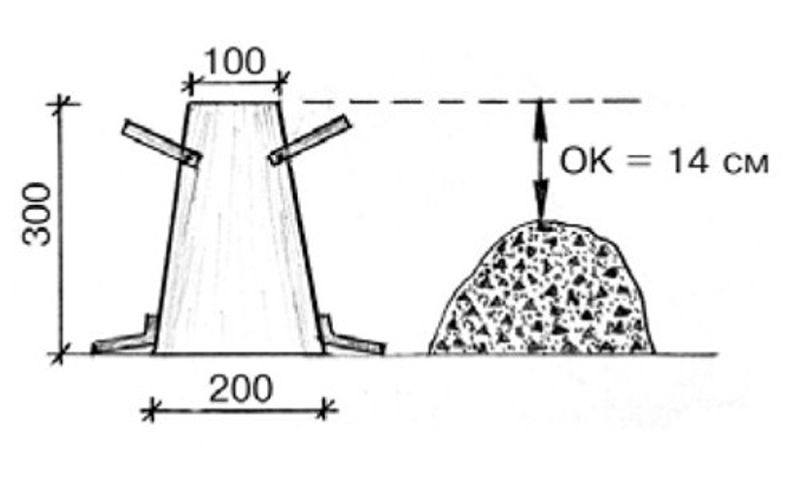
Схема твердения конуса бетонной смеси.
Нужно ускорять время твердения при зимних работах и изготовлении железобетонных изделий.
Чтобы получить быстрое твердение бетона, используются различные необходимые добавки для достижения лучшего результата причем в строгих пропорциях: нитрат натрия, нитрат кальция, нитрит-нитрат кальция, нитрит-нитрат-сульфат натрия и нитрит-нитрат-хлорид кальция – 4%, сульфат натрия – 2%, хлорид кальция в неармированных конструкций – 3%, в армированных конструкций – 2%. Добавки хлорида кальция, нитрит-нитрат хлорида кальция не применяют в предварительно-напряженных конструкциях.
Схватывание раствора
Для схватывания при низких температурах бетонную смесь готовят из подогретых материалов, используют экзотермические цементы, известь-кипелку, нагревают паром, электротоками или добавляют ускорители твердения. Каждый из способов применяют отдельно или совместно с другими.
Чтобы получить подогретую бетонную массу, ее нагревают до 80-90° С, а наполнители до 40-50° С, после чего конструкцию укрывают утеплителем, и так тепло должно сохраняться в течение двух-пяти суток.
Подогрев конструкций производят паром либо электротоком. А чтобы тепло сохранялось, работы обычно ведут под пленочным покрытием. Электропрогрев производят постепенно: сначала доводят температуру до 70, а затем увеличивают до 220 в. Также пропуская электроток, подогревают и горизонтальную поверхность конструкций.

Таблица наполнителей для различных марок бетона.
Таким образом, прочность зависит напрямую от той температуры, при которой происходит процесс твердения бетона. Схватывание прекращается при температуре ниже нормальной, то есть ниже 0°С, и наоборот, при хорошей влажности и повышенной температуре ускоряется. Часто быстрое твердение бетона обусловлено особенно работами в зимний период либо нагрузить конструкции эксплуатационной нагрузкой.
Для прочности свежеуложенных конструкций необходим следующий уход. Необходимо поддерживать их в состоянии влажности, защищать от сотрясения, ударов, повреждений, резких температурных колебаний. Очень часто низкокачественный бетон приводит к его полному разрушению, несмотря на хороший состав смесей и материалов.
Важно следить за материалом в первое время после укладки, так как в дальнейшем все недостатки только ухудшат состояние и приведут к неотвратимым последствиям. Для этого создают благоприятные температурные и влажностные условия, регулярно поливают поверхность, защищают от солнечных лучей.
Закрывают его влагоемкими покрытиями: мешковиной, брезентом или засыпают слоем опилок или песка на несколько часов после укладки и поливают водой, чтобы поверхность практически всегда оставалась в состоянии влажности. Поливают все это с помощью брандспойтов с наконечниками, разбрызгивающими струю. Все это влияет на качественное схватывание.
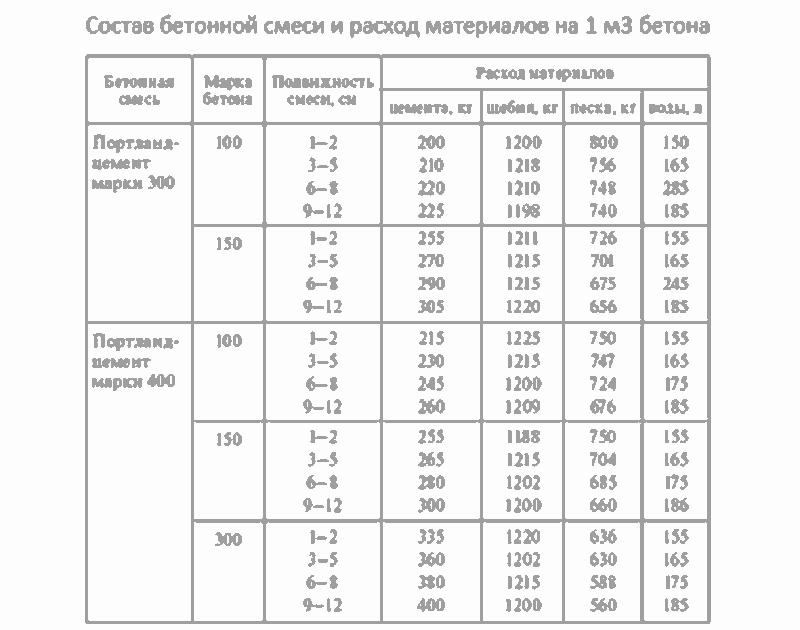
Таблица состава бетонной смеси.
Важно, чтобы свежеуложенная бетонная масса, соприкасающийся с интенсивными грунтовыми водами, должен быть изолирован путем отвода воды на время не менее, чем на трое или 14 суток в зависимости от состава цемента.
В жаркое летнее время поливают и деревянную опалубку. Крутые и вертикальные поверхности поливают непрерывным током воды через трубки с мелкими отверстиями (такой способ всегда применяется в жарких странах). Поливка и укрытие бетонных конструкций – весьма затратное дело, поэтому поверхности (дорого, площадки, перекрытия), не подвергающиеся контакту с бетоном, допустимо покрывать специальными защитными пленками (как правило, это разжиженный битум).
Движение по забетонированным конструкциям и установка на них лесов и опалубки допускается в том случае, когда бетон достигает прочности не менее 1,5 МПа. Движение же бетоноукладочных машин и автотранспорта допускается тогда, когда схватывание достигает своей прочности, заложенной проектом производственных работ. Строительная лаборатория утверждает мероприятия по уходу за массами, сроки и порядок их проведения. Регулирование температурных и влажностных условий бетонных конструкций с начала укладки и до момента замоноличивания межблочных швов регламентируются в проекте сооружений и в проекте производства работ.
o-cemente.info
6. Твердение бетона в различных условиях. Зимнее бетонирование. Способы ускорения процессов твердения бетонов.
Твердение бетона: Нормальной температурой твердения = 15-20оС. И относительной влажности воздуха 90…100%. При пониженной температуре прочность бетона нарастает медленнее. При температуре ниже нуля твердение прекращается. При повышенных температурах - твердеет быстрее (особенно при влажной среде)
Требования к бетону и бетонированию в зимних условиях Замерзание бетона в раннем возрасте влечет за собой значительное снижение его прочности после оттаивания и в дальнейшем по сравнению с нормально твердевшим бетоном. Это происходит в результате того, что свежий бетон насыщен водой, которая при замерзании расширяется, разрывает связи между поверхностью заполнителей и мало затвердевшим цементным камнем. Прочность бетона тем ближе к нормальной, чем позднее он был заморожен. При бетонировании зимой необходимо обеспечить твердение бетона в теплой и влажной среде в течение заданного срока. Это достигается двумя способами: 1)использование внутреннего запаса теплоты бетона – при помощи высокопрочного и быстротвердеющего портландцемента ; 2)дополнительной подачей теплоты бетону, если внутренней недостаточно. Также, рекомендуется использовать ускоритель твердения цемента - хлористый кальций, уменьшать количество воды в бетонной смеси, вводя в нее пластифицирующие и воздухововлекающие добавки, и уплотнять ее высокочастотными вибраторами.
Зимнее бетонирование:
-прогрев воды, песка, щебня
-электроподогрев (осуществляют с помощью переменного тока. )
-ускорители твердения (соли хлористого кальция, хлористого натрия, нитрита натрия, поташа), снижают точку замерзания воды и обеспечивают твердение бетона на морозе (хотя и медленное)
Способы ускорения процессов твердения бетонов.
- пропаривание – прогрев изделий насыщенным паром
- автоклавная обработка – прогрев изделий в автоклавах
7. Легкие бетоны на пористых заполнителях. Основные свойства и применение.
Легкие бетоны имеют объемную массу менее 1800 кг/м3. Их изготовляют на основе быстротвердеющего и обычного портландцементов, а также шлакопортландцемента. Применяют в основном неорганические пористые заполнители.
Керамзитобетон
Аглопоритобетон
перлитобетон и др.
Главные требования, предъявляемые к легкому бетону — заданная средняя плотность, необходимая прочность к определенному сроку твердения и долговечность (стойкость). Характерными особенностями легкого бетона являются его пониженные средняя плотность и теплопроводность.
Теплопроводность = 0,16-0,5 Вт/м*С.
Морозостойкость F25 —F100.
Лёгкий бетон: портландцемент + заполнитель (вспененный перлит, керамзит и т. п.)
По структуре легкие бетоны подразделяют на плотные, поризованные и крупнопористые.
Легкие бетоны по обл.применения: конструкционные – 1400…1800 кг/м3, включая конструкционно-теплоизоляционные – до 1400 кг/м3, и теплоизоляционные – менее 500 кг/м3.
Природные пористые заполнители – дробление пемзы, вулканического туфа, известняка-ракушечника.
Искусственные пористые заполнители: керамзитовый гравий и песок, шлаковая пемза, гранулированный металлургический и топливный шлак, вспученный перлит и вермикулит.
Прочность легкого бетона зависит от прочности цементного камня и заполнителей. Морозостойкость легкого бетона зависит от вида и количества вяжущего и морозостойкости заполнителя.
Легкие бетоны ввиду универсальности свойств применимы в различных строительных элементах зданий и сооружений.
studfiles.net
Процесс - твердение - бетон
Процесс - твердение - бетон
Cтраница 2
Для того чтобы установить минимальную температуру, при которой начинают протекать процессы твердения бетона, были поставлены специальные испытания. [17]
Повышение температуры тешювлажностной обработки свыше 100 С еще в большей степени ускоряет процесс твердения бетона. В процессе запаривания повышенное давление обусловливает возможность сохранения воды в капельно-жидком состоянии при температуре выше 100 С. [18]
Добавка кремнефтористого натрия, вводимого в состав сложного вяжущего вещества, влияет на процесс твердения бетона, на его прочность, жароупорность и термостойкость. Оптимальная величина этой добавки, как уже указывалось выше, составляет 12 % от веса растворимого стекла. Применяемый для приготовления бетона шамотный заполнитель имеет значительную пористость. В случае недостаточной его влажности заполнитель интенсивно впитывает в себя воду из жидкого стекла, что приводит к резкому ухудшению удобообра-батываемости бетонной смеси и к снижению прочности бетона. В противном случае они должны быть увлажнены водой за 3 - 4 часа до приготовления бетонной смеси с тем, чтобы влажность их к моменту замеса была доведена до указанной величины. При большей влажности материал должен быть предварительно подсушен. Бетон указанного выше состава характеризуется следующими физико-механическими показателями. [19]
При изготовлении конструкций из высокопрочных бетонов с использованием цементов высокой активности не следует интенсифицировать процесс твердения бетона за счет прогрева. При достаточных сроках перевозки, монтажа конструкций, наличии больших производственных площадей и необходимого количества форм-опалубки рекомендуется переходить на твердение бетона в нормальных тем-пературно-влажностных условиях цеха. [20]
Особенностью действия образцов Б и В по сравнению с образцом А является заметное увеличение скорости процессов твердения бетона, что связано с положительным эффектом дополнительного ввода неорганических солей, а именно нитритов нитратов сульфатов и свидетельствует о возможности использования отработанных кислоты щелочи и нитрит-нитратных стоков при производстве суперпластификаторов. [21]
Количество воды для затворения цемента должно быть не больше необходимого для осуществления химической реакции в процессе твердения бетона. Однако при таком количестве воды приготовленная бетонная смесь достаточно жесткая и плохо поддается уплотнению, поэтому для ее изготовления требуется воды почти в два раза больше. Лишняя вода во время твердения бетона испаряется, образуя поры и пустоты в бетоне. Чем больше лишней воды, тем больше пор и пустот, которые значительно снижают прочность бетона. Количество воды оценивается водо-цементным отношением В / Ц: чем оно меньше, тем бетон прочнее. [22]
Количество воды для затворения цемента должно быть не больше, чем оно необходимо для химической реакции в процессе твердения бетона. Однако при таком количестве воды приготовленная бетонная смесь достаточно жесткая и плохо поддается уплотнению. Поэтому при изготовлении бетонной смеси приходится вводить воды почти в 2 раза больше, чем она нужна для твердения бетона. Излишняя вода во время твердения бетона испаряется, образуя поры и пустоты в бетоне. Чем больше излишней воды, тем больше пор и пустот, которые значительно снижают прочность бетона. Чем оно меньше, тем бетон прочнее. [23]
В начале щелевой камеры имеется термопригруз, который своими валками через прорезиненную ленту воздействует на бетонную массу в целях создания оптимальных условий в процессе сверхускоренного твердения бетона. По окончании тепловлажностной обработки готовое изделие автоматически освобождается от формующей ленты и с помощью обгонного транспортера перемещается на кантователь. Последний поворачивает изделие в вертикальное положение, после чего мостовым краном оно транспортируется на склад готовой продукции. [24]
К недостаткам монолитного железобетонного фундамента следует отнести большую трудоемкость работ по его сооружению, удлиняющую сроки строительства, трудность работы в зимнее время, длительность процесса твердения бетона, невозможность применения индустриализированных и комплексно-механизированных методов производства работ, большой расход леса на опалубку, сравнительно большие габариты, уменьшающие свободное пространство для размещения оборудования. [25]
Нарезчики швов служат для создания продольных и поперечных швов в монолитном покрытии с целью предупреждения образования в нем трещин, связанных с температурными деформациями покрытия в процессе твердения бетона и эксплуатации покрытия. Нарезание шва может производиться как в свежеуложенном бетоне до момента начала его схватывания, так и в затвердевшем бетоне через 8 - 12 ч после укладки. [27]
Более сильное водопонижение возможно лишь при их введении в повышенной дозировке, однако при этом наблюдаются такие нежелательные эффекты, как усадка, сильное воздухововлечение, отделение воды, расслоение смеси и ухудшение процессов твердения бетона. [28]
Сущность тепловлажностных способов обработки бетонных и железобетонных изделий заключается в том, что при повышенной относительной влажности окружающей среды ( более 95 %) и температуре 60 - 100 С и более скорость реакций гидратации цемента увеличивается ( в 10 - 20 раз), процесс твердения бетона ускоряется, и изделия в более короткий срок приобретают прочность, необходимую для их расформовки, транспортирования и монтажа. [29]
Вакуумирование способствует более полной гидратации цемента вследствие частичного удаления с поверхности твердой фазы адсорбированного воздуха. Это явление ускоряет процесс твердения бетона и повышает его прочность, особенно в ранние сроки. Отсос жидкой фазы может не сопровождаться контракцией объема цементного геля, если жидкость проталкивается через поровые каналы в направлении вакуум-полости засасываемым извне воздухом. [30]
Страницы: 1 2 3 4
www.ngpedia.ru
Схватывание и твердение бетона | Статьи
Цемент - это вещество, которое при смешивании с водой начинает твердеть и превращаться в материал, похожий на камень. Стандартный бетонный раствор содержит цемент в качестве вяжущего элемента. В роли остальных наполнителей чаще всего выступают щебень, песок и вода. Таким образом, можно сделать вывод о том, что суть процесса бетонирования состоит в понимании причин и технологии отвердевании вяжущего вещества бетонной смеси. Осознание сути всех физических стадий бетона позволяет учёным придумывать всё новые и новые добавки, которые воздействуют на процесс затвердевания этого замечательного материала. На сегодняшний день существует огромное количество разнообразных добавок, однако это совершенно другая история. Если необходимо приготовить нужное количество бетонной смеси определённой марки, подобрать компоненты поможет расчёт бетона.
Итак, суть бетонирования состоит в наборе прочности бетоном. Сам же процесс набора прочности делиться на две главные стадии, это - схватывание бетона и твердение бетона.
Первой стадией процесса является, так называемое, схватывание бетона. Схватывание происходит в начальные сутки существования бетона. Самое интересное, что время, за которое бетон будет подвержен данному процессу, напрямую зависит от температуры окружающей среды. Причём, чем выше температура воздуха - тем быстрее произойдёт схватывание бетонной смеси. Если температура держится в пределах 20 градусов, то схватывание начнётся уже спустя 2 часа после создания смеси, и продлится 1 час. В случае же, если температура держится в пределах 0 градусов, то схватывание может длиться до 20 часов и начнётся спустя 6-10 часов после замешивания смеси. В определённых условиях можно добиться схватывания за очень короткое время (пару десятков минут), однако для этого понадобятся специальные высокотермальные камеры.
На протяжении процесса схватывания бетон остаётся в подвижном состоянии, что делает возможным оказание физического воздействия на него. В этот момент в полной мере проявляется тиксотропность данного материала. Смысл тиксотропии заключается в способности материала уменьшать свою вязкость под влиянием физического воздействия, и увеличивать её в состоянии бездействия. Иными словами, пока мешается бетон, он не перейдёт в стадию твердения, что позволить продлить стадию схватывания на необходимый срок. Именно поэтому доставку бетона обычно осуществляют в специальных вертящихся резервуарах, которые не дают бетону выйти из данной стадии до момента бетонирования.
Сразу же после процесса схватывания, наступает процесс твердения бетона. Данный процесс, в равной мере с процессом набора прочности любой железобетонной конструкции, не смотря на установленный срок в 28 дней, длится не один или два месяца, а годы. График процесса набора бетоном прочности является абсолютно нелинейным, и наибольшей динамичностью отличается лишь на начальных стадиях (первые две недели).
rasschitai.ru
СПОСОБЫ ИНТЕНСИФИКАЦИИ ТВЕРДЕНИЯ БЕТОНА
ТЕХНОЛОГИЯ БЕТОННЫХ И ЖЕЛЕЗОБЕТОННЫХ ИЗДЕЛИИ
В организации производства железобетонных изделий большое значение имеет их распалубочная прочность, определяющая темп технологического процесса. Продолжительность естественного твердения бетона до получения, им распалубочной прочности, во много раз превышая суммарную длительность всех остальных операций, вызывает необходимость в большом числе форм и значительном увеличении производственных площадей.
В производстве сборного железобетона применяются различные способы интенсификации твердения бетона, которые в зависимости от основного фактора, способствующего твердению, можно разделить на три группы: технологические, химические и тепловые. Эти способы обеспечивают неодинаковую степень ускорения твердения бетона и поэтому целесообразность каждого из них определяется условиями производства. Весьма эффективно совместное применение различных способов ускорения твердения бетона.
Технологические способы ускорения твердения бетона заключаются в применении быстротвердеющих цементов, сухом и мокром вибродомоле цемента, виброактивации бетонной смеси, применении жестких смесей и эффективных способов их уплотнения.
Химические способы ускорения твердения бетона предусматривают введение в бетонную смесь различных добавок (хлористого кальция, хлористого натрия и др.). В заводских условиях добавки-ускорители твердения бетона можно рекомендовать лишь как средство сокращения продолжительности тепловой обработки.
Тепловые способы интенсификации твердения бетона являются. наиболее эффективными. Они получили широкое применение на заводах сборного железобетона. В качестве источника тепловой энергии в современных установках принимаются пар, вода, электроэнергия, инфракрасные лучи и др.; вследствие этого возможны различные режимы и условия тепловой обработки бетона в изделиях [4].
На заводах и полигонах применяются следующие способы тепловой обработки бетона:
Прогрев бетона паром при атмосферном давлении в камерах различного типа, на стендах под колпаками и покрытиями;
Прогрев бетона непосредственно в формах и формующих агрегатах через формовочные поверхности (контактный прогрев), источником тепла может быть пар или электроэнергия;
Прогрев бетона горячим воздухом (с увлажнением и без увлажнения воздуха) в многоярусных туннельных камерах;
Прогрев бетона паром при повышенном давлении в автоклавах, который применяется для пено - и газобетонов, а также для различных бесцементных бетонов;
Обработка бетона горячей водой в бассейнах, получившая применение в производстве напорных труб, с целью уменьшения усадочных напряжений при твердении бетона;
Прогрев бетона электрическим током, пропускаемым через твердеющий бетон;
Обогрев бетона различными электрическими приборами и инфракрасными лучами.
При прогреве в свежеотформованном бетоне протекают конструктивные процессы, обусловленные ускорением твердения цемента и упрочнением структуры бетона новообразованиями. Одновременно в нем также развиваются деструктивные процессы, возникающие в результате физических изменений под действием температурных и влажностных факторов. К ним в основном относятся явления, вызываемые объемными изменениями, внутренними деформациями, капиллярным давлением и миграцией влаги [51, 86].
В зависимости от степени температурного воздействия и влияния деструктивных процессов происходит некоторое нарушение структуры бетона, выражающееся в ухудшении его физико-механических свойств (прочности, морозостойкости и др.) по сравнению с бетоном нормального твердения. Однако отрицательные стороны тепловой обработки бетона могут быть сведены до минимума применением правильного режима прогрева, при котором бетон, подвергнутый тепловой обработке, по своим
Свойствам лишь незначительно отличается от бетона естественного твердения.
Эффективными следует считать такие режимы тепловой обработки, которые позволяют в короткие сроки получить бетон заданной прочности без существенных нарушений его структуры. При прогреве напряженно-армированных изделий предъявляются также требования в отношении потерь предварительного напряжения в арматуре от температурных перепадов, которые не должны превышать установленных величин.
Общая эффективность ускоренного твердения бетона при тепловой обработке зависит от ряда технологических факторов, характеризующих бетон изделий, и производственных факторов, определяющих режим тепловой обработки. Технологическими факторами являются вид и минералогический состав цемента, количество цемента и воды в бетоне и др. *
Производственными факторами являются, температура и влажность среды, продолжительность отдельных периодов тепловлажностной обработки бетона.
Разборные и виброформы для бетонных колец (0.7м, 1м, 1.5м, 2м). Формы для колодезных и бетонных колец. Заказы по тел +38 050 4571330 или эл. почта: [email protected] Цены март 2015г.: Виброформы …
Для учета производственной деятельности предприятия и оформления результатов контроля необходимо ведение технических записей, журналов испытаний, лабораторных анализов и пр. Основные виды технической документации на заводах сборного железобетона следующие[14]: А) журнал …
Контроль качества готовой продукции осуществляется в соответствии с требованиями ГОСТов и технических условий. Разрешается не производить испытание готовых изделий до разрушения за счет увеличения, объема пооперационного контроля, а также применения …
msd.com.ua
Процесс твердения бетона — Я строитель!
Твердение отформованных изделий — заключительная операция технологии изготовления железобетона, в процессе которой изделия приобретают требуемую прочность. Отпускная прочность может быть равна классу бетона или меньше его. Так, прочность бетона изделий при отгрузке потребителю должна быть не менее 70% проектной (28-суточной) прочности для изделий из бетона на портландцементе или его разновидностях и 100%—для изделий из силикатного (известково-песчаного) или ячеистого бетона. Однако для железнодорожных шпал отпускная прочность должна превышать 70% и для пролетных строений мостов — 80% от класса. Допускаемое снижение отпускной прочности изделий определяется исключительно экономическими соображениями, так как в этом случае сокращается продолжительность производственного цикла и соответственно ускоряется оборачиваемость оборотных средств. При этом имеется в виду, что недостающую до проектной прочность изделия наберут в процессе их транспортирования и монтажа и к моменту загружения эксплуатационной нагрузкой прочность их будет не ниже проектной. В зависимости от температуры среды различают следующие три принципиально отличающихся режима твердения изделий: нормальный при температуре 15…20°С; тепловлажностная обработка при температуре до 100°С и нормальном давлении; автоклавная обработка — пропаривание при повышенном давлении (0,8… 1,5 МПа) и температуре 174…200°С. Независимо от режима твердения относительная влажность среды должна быть близкой к 100%. Иначе будет происходить высушивание изделий, что приведет к замедлению или прекращению роста их прочности, так как твердение бетона есть в первую очередь гидратация цемента, т. е. взаимодействие цемента с водой.Нормальные условия твердения достигаются в естественных условиях без затрат тепла. Это важнейшее технико-экономическое преимущество указанного способа твердения, отличающегося простотой в организации и минимальными капитальными затратами. В то же время экономически оправдан он может быть только в исключительных случаях. В естественных условиях изделия достигают отпускной 70%-ной прочности в течение 7… 10 сут, тогда как при искусственном твердении — пропаривании или автоклавной обработке — эта прочность достигается за 10…16 ч. Соответственно при этом снижается потребность в производственных площадях, объеме парка форм, сокращается продолжительность оборачиваемости средств. Это и является причиной применения на большинстве заводов искусственного твердения. В то же время стремление отказаться от последнего является актуальной проблемой современной технологии бетона. Уже имеются бетоны, которые в течение одних суток при нормальных условиях твердения приобретают до 40…50% проектной прочности. Это достигается применением высокопрочных быстротвердеющих цементов, жестких бетонных смесей, интенсивного уплотнения вибрацией с дополнительным пригрузом, применением добавок — суперпластификаторов, ускорителей твердения, виброактивизации бетонной смеси перед формованием, применением горячих бетонных смесей. Дальнейшее развитие работ в этом направлении позволит, по-видимому, в ближайшие годы отказаться в ряде случаев от искусственного твердения. Тепловлажностная обработка при нормальном давлении может осуществляться несколькими способами: пропариванием в камерах; электроподогревом; контактным обогревом; обогревом лучистой энергией; тепловой обработкой изделий в газовоздушной среде; горячим формованием. Среди приведенного разнообразия технико-экономическое преимущество пока остается за пропариванием в камерах периодического и непрерывного действия, а также в среде продуктов сгорания природного газа. В камеры непрерывного действия загружают свежесформованные изделия на вагонетках, а с противоположного конца туннеля камеры непрерывно выходят вагонетки с отвердевшими изделиями. В процессе твердения изделия проходят зоны подогрева, изотермического прогрева (с постоянной максимальной температурой пропаривания) и охлаждения. В принципе камеры непрерывного действия, как и вообще всякое непрерывно действующее оборудование, обеспечивают наиболее высокий съем продукции с единицы объема камеры. Однако необходимость применения вагонеток и механизмов для перемещения изделий, а также ряд конструктивных сложностей туннельных камер в теплотехническом отношении не позволяет широко применять этот вид пропарочных камер. Используют их только при конвейерном способе производства. Перспективными являются вертикальные камеры непрерывного действия.Среди камер периодического действия основное применение находят камеры ямного типа, имеющие глубину 2 м и на 0,5…0,7 м выступающие над уровнем пола цеха. Размер камеры в плане соответствует размеру изделий или кратен им. Наиболее целесообразным является размер камеры, соответствующий размеру одного изделия в плане. В этом случае загрузочная емкость камеры и непроизводительный простой камеры под загрузкой будут минимальными. Однако при этом возрастает потребность в количестве камер. Технико-экономический анализ показал, что наиболее целесообразным оказывается размер двух изделий. Стенки камеры выкладываются из кирпича или делаются бетонными. Сверху камера закрывается массивной крышкой с теплоизоляционным слоем, предупреждающим потери тепла. Для предупреждения выбивания пара в стенках камеры сверху ее предусматривается канавка, засыпаемая песком или заливаемая водой. В эту канавку входят соответствующие выступы на крышке, камеры. Таким образом создается затвор, препятствующий выбиванию пара из камеры.Изделия загружаются в камеру краном в несколько рядов по высоте. Если изделия в формах, то каждый верхний ряд изделий устанавливают на стенки нижележащей формы (через деревянные прокладки). При формовании же изделий с частичной немедленной распалубкой поддон с изделием устанавливают на специальные откидывающиеся выступы, предусмотренные в стенках камеры.Режим пропаривания в камерах характеризуется продолжительностью подъема температуры, выдержкой при максимальной температуре, продолжительностью охлаждения, а также наибольшей температурой в период изотермического прогрева. Применяют самые разнообразные режимы твердения в зависимости от свойств цемента и его вида, свойств бетонной смеси (жесткая или подвижная), вида бетона (тяжелый или легкий), размеров изделий (тонкие или массивные).В качестве усредненного можно привести следующий режим: подъем температуры со скоростью 25,..35°С/ч, снижение температуры — 30…40 °С/ч, изотермическая выдержка 6…8 ч и максимальная температура 80…90°С. Таким образом, общая продолжительность пропаривания для изделий на обыкновенном портлаНдцементе в среднем составляет 12… 15 ч. Твердение изделий — наиболее продолжительная операция, в десятки раз превышающая все другие. Это требует изыскания путей снижения продолжительности пропаривания, для чего необходимо знать определяющие факторы. В первую очередь на режим твердения оказывает влияние вид цемента. Применение быстротвердеющих цементов (алитовых и алитоалюминатных портландцементов) позволяет до 2 раз сократить продолжительность изотермической выдержки. Кроме того, оптимальная температура прогрева изделий на этих цементах 70…80°С существенно сокращает время, потребное на нагрев и охлаждение изделий. В совокупности общая продолжительность тепловлажностной обработки изделий на алитовых и алитоалюминатных, быстротвердеющих портландцементах снижается до 6…8 ч. За этот период получают изделия с прочностью бетона, равной 70…80% от проектной.Медленнотвердеющие цементы (пуццолановые и шлакопортландцементы) требуют более продолжительной изотермической выдержки (до 10… 14 ч) и более высокой температуры изотермического прогрева (до 95…100°С). Таким образом, общая продолжительность пропаривания бетонных изделий, приготовленных на пуццолановых или шлакопортландцементах, составляет 16…20 ч.Применение жестких бетонных смесей, имеющих низкое начальное водосодержание, позволяет на 15…20% уменьшить продолжительность пропаривания. Если учесть, что дополнительные затраты энергии и труда на формование жестких смесей не превышают 10… 15% и компенсируются снижением расхода цемента при этом, то экономическая целесообразность применения жестких смесей становится очевидной и в данном случае. Изделия из легких бетонов, как, например, медленно прогревающиеся в силу их повышенных теплоизоляционных качеств, требуют и более продолжительного режима тепловлажностной обработки.Способ формования предварительно подогретой до 75…85°С бетонной смеси получил название «горячего формования», при котором изделия поступают в камеру в подогретом виде и не требуют, таким образом, времени на их подогрев до максимальной температуры пропаривания. Этот способ предусматривает отказ от пропаривания. Свежесформованные горячие изделия укрывают (способ термоса) и оставляют на 4…6 ч, в течение которых бетон набирает необходимую прочность. Подогрев бетонной смеси производят электрическим током в течение 8…12 мин.Электропрогрев изделий по своим техническим свойствам и санитарно-гигиеническим условиям производства имеет несравнимое преимущество перед всеми другими способами. Тормозят его развитие недостаток и все еще высокая стоимость электроэнергии. Расход электроэнергии при электротермической обработке бетона в среднем составляет 80… 100 кВт-ч на 1 м3 изделий. Электропрогрев изделий достигается путем прохождения nepеменного тока через бетон. Последний, обладая электрическим сопротивлением большим, чем подводящие к нему ток электроды разогревается в результате преобразования электрической энергии в тепловую.Электропрогреву в открытых формах подвергают изделия массивные, так как тонкостенные изделия при этом способе могут пересыхать, поэтому их целесообразно прогревать электрическим током в кассетах. Напряжение тока в начале электропрогрева принимают равным 65…90 В, а в конце — до 150…220 В. По мере отвердения электропроводность бетона понижается и для прохождения через него электрического тока требуется большое напряжение. Контактный обогрев изделий достигается путем непосредственного их контакта с нагревательными приборами, например обогреваемыми стенками формы, основанием стенда. При этом изделие плотно укрывают, чтобы предупредить потери испаряющейся из него влаги в окружающую среду. Необходимая влажность вокруг изделия достигается за счет избыточной воды, т. е. сверх потребной на твердение цемента, которая вводится для получения удобоукладываемой смеси. В качестве теплоносителя применяют острый пар, горячую воду, нагретое масло. Наиболее эффективно использование контактного обогрева тонкостенных изделий при достаточной их герметизации. Это наблюдается, например, в кассетах, в которых изделие заключено в узких, но глубоких отсеках. В этом случае возможен очень быстрый подъем температуры до максимальной (за 15…30 мин) без нарушения структуры бетона. Кроме того, образуется насыщенная паровая среда с несколько большим, чем атмосферное, давление пара, что благоприятно сказывается на процессах твердения бетона. Температурная обработка в термобассейнах применяется в том случае, когда требуется получить изделие высокой плотности водонепроницаемости (трубы, кровельные материалы). Твердение в горячей воде — наиболее благоприятный в этом отношении лежим. Предварительно отвердевшие изделия помещают в бассейн с горячей водой и выдерживают в нем до приобретения необходимой прочности. Этот способ имеет хорошие технико-экономические показатели — низкий расход тепла обеспечивает наиболее благоприятные условия твердеющему бетону, но необходимость последующей сушки изделий является причиной практического отказа от обработки изделий в термобассейнах.Автоклавная обработка. Скорость большинства химических реакций, в том числе и взаимодействие цемента с водой, обеспечивающая твердение бетона, возрастает с повышением температуры, и тем она больше, чем выше температура. Кроме того, для твердения бетона необходима влажная среда. Сочетание этих двух факторов успешно достигается при обработке изделий паром высокого давления. С повышением давления соответственно возрастает температура насыщенного пара; при 100%-ной относительной влажности среды температуру выше 100°С получить нельзя. Сверх этой температуры относительная влажность среды будет меньше 100%, и помещенные в нее бетонные изделия начнут высыхать. Наиболее распространенный режим автоклавной обработки: давление пара 0,8…1,5 МПа, температура насыщенного пара 170…200°С. При таком режиме получают изделия с проектной прочностью бетона в течение 8… 10 ч, что дает большой технико-экономический эффект.Важным достоинством автоклавной обработки бетона является следующее: при высокотемпературных условиях песок, будучи инертным при нормальной температуре и пропаривании, становится активным, энергично взаимодействует с известью и обеспечивает получение бетона прочностью 20 МПа и более. Это позволяет широко использовать дешевые бесцементные известково-песчаные бетоны для изготовления способом автоклавной обработки прочных, водостойких и долговечных изделий. При использовании портландцементов обычно применяют медленно твердеющие цементы. Их преимущество в данном случае не только в несколько пониженной стоимости, но и в большом приросте прочности, получаемом при автоклавной обработке по сравнению с другими видами портландцементов. Кроме того, в автоклавных портландцементных бетонах часть цемента (до 30…40%) может быть успешно заменена молотым песком. При этом прочность бетона не только не снижается, но даже наблюдается улучшение физико-механических свойств бетона, что имеет большую технико-экономическую значимость.
http://iambuilder.ru/%d0%bf%d1%80%d0%be%d1%86%d0%b5%d1%81%d1%81-%d1%82%d0%b2%d0%b5%d1%80%d0%b4%d0%b5%d0%bd%d0%b8%d1%8f-%d0%b1%d0%b5%d1%82%d0%be%d0%bd%d0%b0/2015-04-23T12:20:44+00:00DroZD_MANСтроительные материалыТвердение отформованных изделий — заключительная операция технологии изготовления железобетона, в процессе которой изделия приобретают требуемую прочность. Отпускная прочность может быть равна классу бетона или меньше его. Так, прочность бетона изделий при отгрузке потребителю должна быть не менее 70% проектной (28-суточной) прочности для изделий из бетона на портландцементе или его...DroZD_MAN1 [email protected]Я строитель!
Понравилось это:
Нравится Загрузка...
Похожее
iambuilder.ru