Заточка зубил на станке вручную. Как заточить зубило
Заточка инструментов - Заточка инструментов

Категория:
Заточка инструментов

Заточка зубила. Инструмент устанавливают на подручник заточного станка и, слегка нажимая на него, медленно и плавно перемещают по всей ширине заточного круга. В процессе работы зубило следует переворачивать и затачивать то одну, то другую сторону, периодически охлаждая режущую часть в воде.
Режущая кромка зубила после заточки должна иметь одинаковую ширину и наклон к оси с обеих сторон инструмента. Только в этом случае зубило будет заточено правильно.
Для рубки чугуна и бронзы угол заточки, или заострения, зубила делают 70°, для стали средней твердости — 60°, меди и латуни — 45°, алюминия и цинка — 35°. Угол заострения проверяют по шаблону, представляющему собой пластинку с угловыми вырезами в 70°, 60°, 45°, 35° (рис. 2).
Рис. 1. Заточка зубила
Рис. 2. Шаблон (а) и проверка угла заточки зубила (б)
Рис. 3. Заточка чертилки
После заточки режущую кромку зубила заправляют на абразивном бруске, то есть снимают с нее неровности.
Заточка чертилки. Сначала проверяют установку подручника. Если он расположен правильно, то есть зазор между ним и абразивным кругом не превышает 2—3 мм, можно приступать к работе.
Включают электроточило, берут обеими руками чертилку и, опираясь левой рукой на подручник, прижимают рабочую часть инструмента к боковой поверхности заточного круга под небольшим углом к ней (рис. 2). Чтобы чертилка была заточена ровно и правильно, ее надо все время поворачивать вокруг своей оси.
Заточка кернера. Отрегулировав зазор между подручником и заточным кругом, берут кернер обеими руками и, располагая левую руку на подручнике, устанавливают кернер под углом 30—40° к рабочей поверхности круга (рис. 3).
Включив электроточило, прижимают к нему рабочую часть кернера и затачивают инструмент, поворачивая его вокруг своей оси.
—
С помощью заточки восстанавливают рабочую часть режущего инструмента, т. е. получают оптимальную форму, размеры и шероховатость его режущих кромок. Повторные операции заточки затупленного инструмента называют перетачиванием.
Заточка резцов. Износ по задней поверхности определяется величиной, износ по передней поверхности — шириной В и глубиной Нл лунки. В зависимости от условий обработки износ твердого сплава может происходить только по передней или только по задней поверхности или по обеим поверхностям одновременно.
Рис. 4. Заточка резца на точильно-шлифовальном станке
Если износ резцов не превышает допустимой величины, то припуск на заточку составляет 0,6—0,9 мм.
Заточку резцов производят на точильно-шлифоваль-ных станках (точилах), универсально-заточных станках и специальных резцезаточных станках. Установка резца на подручниках точила при заточке передней поверхности показана на рис. 4, а; при заточке главной задней поверхности — на рис. 4,б.
При расчетах учитывают, является ли положительным или отрицательным угол Я и подставляют его в формулы соответственно со знаком плюс или минус.
Последовательность операций заточки и доводки твердосплавного резца: 1) заточка передней поверхности; 2) заточка задней главной поверхности по державке;3) заточка задней вспомогательной поверхности по державке; 4) заточка фаски по передней поверхности; 5) заточка задней главной поверхности по пластине; 6) заточка задней вспомогательной поверхности по пластине; 7) заточка задней поверхности по радиусу вершины; 8) доводка фаски по передней поверхности; 9) доводка ленточки по задней поверхности.
Рис. 5. Схема расчета установочных углов резца при заточке в трех-поворотных тисках на универсально-заточном станке
Рис. 6. Установка резца в трехповоротных тисках при заточке передней (а и б) и задней поверхности (в и г)
Рис. 7. Контроль углов резца угломером, размещенным на стойке
Рис. 8. Схема двухплоскостной заточки сверла
Рис. 9. Характер износа и величина стачивания при заточке незатылованной (а) и затылованной (б) фрезы
Рис. 10. Затачивание незатылованной фрезы по передней (о) и задней (б) поверхностям
Рис. 11. Контроль передних (а) и задних (б) углов фрезы
Читать далее:
Плоскостная разметка по чертежу и обработка по разметке
Статьи по теме:
pereosnastka.ru
Заточка зубил на станке вручную
Заточка зубил на станке вручную
При выполнении операции рубки инструменты должны быть остро заточенными, так как применение тупого зубила приводит к соскальзыванию его с обрубаемой поверхности, при работе с таким инструментом человек устает и теряет правильность ударов.
Заточка зубил и крейцмейселей производится на заточном станке. Для этого зубило или крейцмейсель накладывают на передвижной подручник и с легким нажимом медленно передвигают по всей ширине шлифовального круга, периодически поворачивая инструмент то одной, то другой стороной.
Не нужно сильно нажимать на затачиваемый инструмент, так как это приводит к перегреву режущей кромки, в результате чего лезвие теряет первоначальную прочность.
Перед заточкой инструмента подручник устанавливают как можно ближе к заточному кругу.
Зазор между подручником и заточным кругом должен быть не более 2 – 3 мм, чтобы затачиваемый инструмент не мог попасть между кругом и подручником.
Заточку лучше всего вести с охлаждением водой, в которую добавлено 5 процентов соды, или на мокром круге.
Несоблюдение этого условия вызывает повышенный нагрев, отпуск и уменьшение твердости инструмента, а следовательно, и стойкости в работе. Боковые грани после заточки должны быть плоскими, одинаковыми по ширине и с одинаковыми углами наклона. После заточки зубила или крейцмейселя с режущих кромок снимают заусенцы.
Величина угла заострения проверяется шаблоном – пластинкой с угловыми вырезами 70, 60, 45, 35 градусов.
Слесарные молотки являются инструментом для ударных работ. Они бывают с круглыми и квадратными бойками. Основной характеристикой молотка является его масса.
Молоток состоит из ударника и рукоятки. Слесарные молотки с круглым бойком изготовляют шести номеров.
Молотки N 1 массой 200 г применяют для инструментальных работ, а также для разметки и правки. Молотки N 2 массой 400 г, N 3 – 500 г и N 4 – 600 г – для слесарных работ.
Молотки с квадратным бойком изготовляют восьми номеров. Молотки с круглым бойком не оставляют вмятин на обрабатываемой поверхности при нанесении наклонных ударов.
Противоположный бойку конец молотка называется носком. Носок имеет клинообразную форму, скругленную на конце. Носком пользуются при правке, расклеивании и т.д.
Бойком наносят удары по зубилу и крейцмейселю.
Изготовляют молотки из стали 50 и 40Х и инструментальной углеродистой стали У6 и У8. В средней части молотка имеется отверстие овальной формы для крепления рукоятки.
Боек и носок молотка специально обрабатывают термически. Рукоятку делают из твердых сортов дерева – кизила, рябины, дуба, клена, граба, ясеня, березы.
Рукоятки молотков должны быть проолифлены с предварительной тщательной прошлифовкой. Закрепляют молотки на рукоятках при помощи металлических или деревянных клиньев. Деревянные клинья должны быть изготовлены из твердых пород дерева. Перед насадкой их смазывают столярным клеем, а на металлических клиньях делают насечки. Толщина клиньев в узкой части 0,8 мм, в широкой – 2,5 – 6 мм.
Если отверстие молотка имеет только боковое расширение, забивают один продольный клин; если расширение идет вдоль отверстия, то забивают два клина, если расширение отверстия направлено во все стороны, забивают три стальных или три деревянных клина – два параллельно, а третий перпендикулярно к ним. Правильно насаженным считается молоток, у которого ось рукоятки образует прямой угол с осью молотка.
Кроме обычных стальных молотков в некоторых случаях применяют мягкие молотки со вставками из меди, свинца и алюминиевых сплавов. При ударах, наносимых мягким молотком, поверхность материала заготовки почти не повреждается. Иногда медные или свинцовые вставки заменяют резиновыми, менее дорогостоящими и более эффективными в работе.
Мягкие молотки применяют в точных сборочных работах, особенно когда приходится иметь дело с деталями невысокой твердости.
При изготовлении изделий из тонких листов железа или другого металла, применяют деревянные молотки – киянки, которые бывают с круглыми и прямоугольными ударниками.
Выбирая молоток необходимо учитывать физическую силу работника. Для подростков масса молотка может быть от 400 г до 600 г, для взрослых – от 600 до 800 г.
Удар молотком осуществляют не за счет излишних мускулистых усилий, а за счет ускоренного падения молотка. В момент нанесения удара рукоятку молотка прочно сжимают пальцами. Если молоток удерживать слабо, он может при неточном ударе отскочить и нанести травму.
Поделитесь на страничкеСледующая глава >
diy.wikireading.ru
Блог слесаря-ремонтника и механика по наладке оборудования
Наконец мне удалось собрать видео и фото материал о том, как заточить сверло вручную, использую только точило. Сам файл занимает около 8 Мб, и поэтому пришлось выложить его здесь: http://depositfiles.com/files/s4380ugkj Теперь видео о том, как заточить сверло на YouTube: Немного по файлу: для заточки сверла понадобиться два круга: один алмазный круг и второй обычный. Если будут вопросы по заточке, задавайте в обсуждении.
Уважаемые читатели, я готовлю материал (с фото и видео), о том, как заточить сверло и как проверить заточку…
Ура. Материал подготовил. Видео и фото загнал в один файл. Подробнее о заточке сверла — тут.
Заточить шаберную пластину — это еще пол-дела
Самый простой и быстрый способ проверки — это проверка «на ноготь». Суть метода проста — ноготь большого пальца замеяет нам поверхность шабрения. Шабером пробуем снять небольшую стружку с ногтя — если стружечка получается при минимаьном нажиме на шабер — значит грань шаберной ластины заточена достаточна.
В ближайшее время выложу фото по этой теме.
Как и обещал, выкладываю фото, как проверить заточку шабера.

проверка заточки шабера. фото 1

проверка заточки шабера. фото 2
В данной статье я рассажу о заточке шабера,
Материал который необходимо шабрить — чугун (станина фрезерного станка).
Затачивать шаберную пластину необходимо на алмазном круге с мелким зерном. Так как пластина будет сильно нагреаться при заточке — то необходимо иметь под рукой емкость с водой — для охлаждения пластины.
Стороны «А» и»Б» затачиваем так, чтобы получилась небольшая выпуклость (как на рисунке).
А вот угол заточки граней «А» и «Б» — 90 градусов. Таким образом на каждой стороне мы получаем по две рабочие грани, а всего значит четыре рабочие грани.
Зубило — основной слесарный инструмент для таких операций: обрубка и рубка металла, срезание заклепок, вырубывание различных по форме отверстий.
Режущую часть зубила подвергают термической обработке — сначала закаливают, потом производят отпуск так, чтобы твердость на длине 15…30 мм составляла HRC 52…57. А вот головная часть (по которой впоследствии будут бить молотком) зубила на длине 15…25 мм должна составлять (после термической обработки) HRC 32…40. Таким образом, с помощью разных режимов закалки, получают твердую режущую часть и относительно мягкую головную часть.
Головная часть зубила выполняется конической со слегка закругленным торцом для уменьшения ее расклепывания при ударе.
Геометрия режущей части зубила
При выборе угла заточки руководствуются следующими принциапми: чем меньше угол резания, тем меньшим будет усилие резания. Но при этом режущая часть зубила будет хрупкой. Из-за этого для рубки твердых материалов угол резания подбирают больше, чем при обработке более мягких материалов .
Заточка зубила (а) и шаблон для проверки угла заточки (б)
На данном рисунке представлен способ заточки рабочей части зубила и шаблон для проверки угла заточки.
wmua.ru
Заточка инструмента - Кустарь - сайт для тех, кто всё делает сам
Всякий режущий инструмент тупится в процессе работы, и поэтому его нужно время от времени затачивать. Эту операцию лучше и легче всего вести на заточном станке или другом механическом точиле.
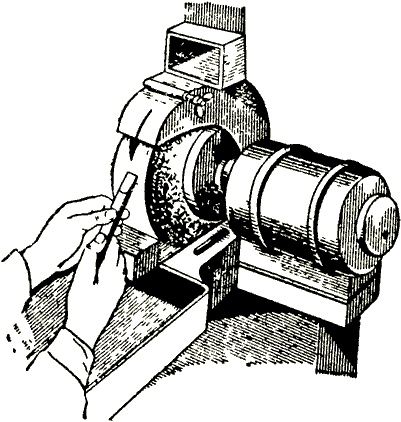
Заточка зубила на заточном станке
Заточка зубила и крейцмейселя. Взяв зубило в руки, его осторожно прикладывают к вращающемуся кругу и двигают влево и вправо с легким нажимом. Заточке подвергают попеременно обе грани. Угол между ними — угол заточки — может быть различным и изменяется в зависимости от твердости обрабатываемого материала в следующих пределах: для алюминия и цинка — 35°, меди и латуни — 45°, стали — 60°, чугуна и бронзы — 75°. Углы заточки удобнее всего проверять по шаблону.
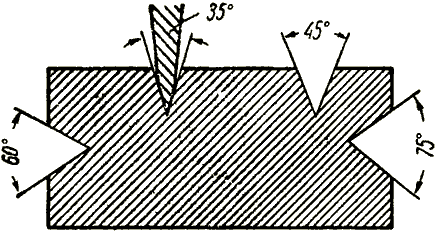
Шаблон для проверки углов заточки зубила и крейцмейселя
Правила заточки крейцмейселя те же, что и у зубила.
Заточка сверл. На рисунке ниже изображена передняя часть спирального сверла.

Передняя часть спирального сверла
Винтообразные канавки по оси сверла служат для удаления стружки. Ребро между плоскостью канавки и задней поверхностью является режущей кромкой. Угол между кромками делается обычно в 116—118°, однако он может меняться, в зависимости от твердости обрабатываемого материала, от 90 до 140°. Сверло при заточке держат левой рукой, возможно ближе к передней части, а правой рукой — за хвостовик, покачивая сверло плавным.
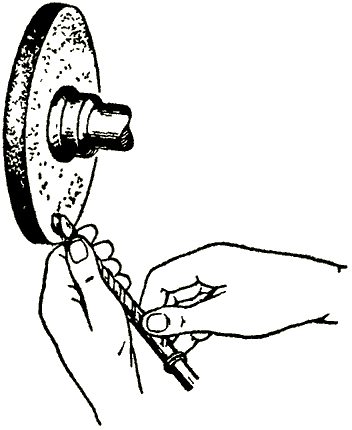
Заточка сверла
При этом нужно соблюдать следующие условия: а) режущие кромки должны быть симметричны, иметь одинаковый угол наклона и одинаковую длину; б) поперечная кромка должна составлять с режущей кромкой угол в 55°. Правильность заточки проверяется по шаблону.

Шаблон и проверка правильности заточки сверла по шаблону
Заточка кернера подобна заточке сверл. Инструмент держат левой рукой, прижимая к абразивному кругу, а правой равномерно вращают его для получения ровного конуса. Угол заточки равен 60°, для накернивания центров — 120°.
Помните, что сильно нажимать на инструмент во время заточки нельзя, иначе его рабочий конец нагреется слишком сильно и может отпуститься — потерять закалку. Во время работы от инструмента и абразивного круга отделяются раскаленные частицы, которые могут попасть в глаза. При заточке пользуйтесь защитными очками или защитным экраном!
В случае попадания частичек в глаз немедленно обращайтесь к врачу.
Автор: П.В. Леонтьев
Читайте еще:
www.sdelaysam.info
Заточка зубила, сверла.
. Рисунок 12 Заточка зубил на станке вручную. | Заточка зубил производится на заточном станке. Для заточки зубило накладывают на передвижной подручник 11 и с легким нажимом медленно передвигают по всей ширине шлифовального круга, периодически поворачивая инструмент то одной, то другой стороной. Не следует допускать сильных нажимов на затачиваемый инструмент, так как это приводит к перегреву режущей кромки, в результате чего лезвие теряет первоначальную твердость Перед заточкой инструмента подручник устанавливают как можно ближе к заточному кругу б) Зазор между подручником и заточным кругом должен быть не более 2-3 мм, чтобы затачиваемый инструмент не мог попасть между кругом и подручником в). Заточку лучше всего вести с охлаждением водой, в которую добавлено 5% соды, или на мокром круге. Несоблюдение этого условия вызывает повышенный нагрев, отпуск и уменьшение твердости инструмента, а следовательно и стойкости в работе. Боковые грани после заточки должны быть плоскими, одинаковыми по ширине и с одинаковыми углами наклона. После заточки зубила с режущих кромок снимают заусеницы. Величина угла заострения проверяется шаблоном, представляющим собой пластинки с угловыми вырезами 70, 60, 45 и 35˚ |
Затачивание спиральных сверл.
При сверлении затупившееся сверло очень быстро нагревается. При небрежном отношении сверло из быстрорежущей стали (Р9, Р18 и др.) может нагреться настолько, что произойдет отпуск стали и сверло станет негодным для работы (пережог сверла). При сверлении даже не очень твердых материалов на работающее тупое сверло требуется повышенное осевое давление, чтобы оно врезалось в металл. При сверлении текстолита и гетинакса происходит повышенное нагревание сверла и легко может образоваться пережог сверла.
Чтобы повысить стойкость режущего инструмента и получить чистую поверхность отверстия, при сверлении металлов и сплавов пользуются охлаждающими жидкостями.
Ниже приведены рекомендации выбора охлаждающей жидкости в зависимости от просверливаемого материала.
Просверливаемый материал | Рекомендуемая охлаждающая жидкость |
Сталь | Мыльная эмульсия или смесь минерального и жирных масел |
Чугун | Мыльная эмульия (или всухую) |
Медь | Мыльная эмульсия или сурепное масло |
Алюминий | Мыльная эмульсия (или всухую) |
Дюралюминий | Мыльная эмульсия, керосин с касторовым или сурепным маслом |
Силумин | Мыльная эмульсия или смесь спирта со скипидаром |
Износ сверла в первой стадии может быть обнаружен по резко скрипящему звуку. Опытный рабочий безошибочно по звуку иногда устанавливает момент, когда сверло начинает затупляться. При работе изношенным сверлом температура резко возрастает и сверло быстро изнашивается , разбивает отверстие.
Как правило, заточка сверл выполняется централизованно в специальных мастерских специальными заточниками, однако и слесарь обязан хорошо знать правила заточки и при необходимости уметь заправить сверло вручную на простом заточном станке.
Заточку выполняют в предохранительных очках (если на станке нет прозрачного экрана) Затачивают сверло вручную следующим образом.
Рисунок 13 Заточка сверла. | Левой рукой удерживают сверло за рабочую часть как можно ближе к режущей части (конусу, а правой рукой охватывают хвостовик, слегка прижимая режущую кромку сверла к боковой поверхности шлифовального круга. Затем плавным движением руки, не отнимая сверло от круга, поворачивают (покачивают) его вокруг своей оси и, выдерживая правильный наклон и слегка нажимая на сверло, затачивают заднюю поверхность. Заточку ведут с охлаждением, периодически погружая конец инструмента в водно-содовый раствор. Заточенное сверло доводят на оселке или бруске. При этом следят за тем, чтобы режущие кромки были прямолинейны, имели одинаковую длину и были заточены под одинаковыми углами. Угол заточки существенно влияет на режим резания, стойкость сверла и, следовательно, на производительность. Сверла с режущими кромками разной длины или с разными углами наклона будут сверлить отверстия больше своего диаметра, поэтому при заточке спирального сверла необходимо получить угол при вершине 116-118˚. |
При переточке спиральных сверл, особенно если это осуществляется вручную, увеличение диаметра отверстия из-за неточной заточки может достигнуть недопустимой величины. По этой причине спиральные сверла затачивают вручную только в случаях, когда их диаметр не превышает 10 мм, сверла больших диаметров затачивают только на специальных (заточных) станках.
studfiles.net
Рубка металла
Рубкой называется слесарная операция при которой с помощью режущего инструмента (зубила и др.) и ударного инструмента (слесарного молотка) с поверхности заготовки или детали удаляются лишние слои металла или заготовка разрубается на части.
Рубка производится в тех случаях, когда по условиям производства станочная обработка трудно выполнима или нерациональна и когда не требуется высокой точности обработки.
Рубка применяется для удаления (срубания) с заготовки больших неровностей, снятия твердой корки, окалины, заусенцев, острых углов кромок на литых штампованных деталях. для вырубания шпоночных пазов, смазочных канавок, для разделки трещин в деталях под сварку, срубания головок заклепок при их удалении, вырубания отверстий в листовом материале.
Кроме того, рубка применяется тогда, когда необходимо от пруткового, полосового или листового материала отрубить какую-то часть.
Заготовку перед рубкой закрепляют в тиски. Крупные заготовки рубят на плите или наковальне, а особо крупные на том месте, где они находятся.
В зависимости от назначения обрабатываемой детали рубка может быть чистовой и червовой. В первом случае зубилом за один проход снимают слой металла толщиной от 0,5 до 1 мм, во втором – от 1,5 до 2 мм. Точность обработки при рубке составляет 0,4-1 мм.
Рисунок 14 Типы молотков | Слесарные молотки – инструмент для ударных работ – изготавливают двух типов: 1 – молотки с круглым бойком и 2 – молотки с квадратным бойком. Основной характеристикой молотка является его масса. Молоток состоит из ударника и рукоятки (ручки). Слесарные молотки с круглым бойком изготавливают шести номеров. Молотки №1 массой 200 г рекомендуется применять для инструментальных работ, а также для разметки и правки; молотки №2 массой 400 г, №3 –500 г и ; №4 – 600 г – для слесарных работ, рубки, гибки, клепки и др; №7 – 800 г и №8 – 1000 г применяют редко (при выполнении ремонтных работ). Для тяжелых работ применяют молотки массой от 4 до 16 кг, называемые кувалдами. Противоположный бойку 1 конец молотка называется носком 3. Носок имеет клинообразную форму, скругленную на конце. Носком пользуются при правке, расклепывании и т.д. Бойком наносят удары по зубилу или крейцмейселю. Изготавливают молотки из стали 50 и 40Х и инструментальной углеродистой стали У7 и У8. В средней части молотка имеется отверстие овальной формы, служащее для крепления рукояти. Рабочие части молотка – боек квадратной или круглой формы и носок клинообразной формы – термически обрабатывают до твердости HRC 49-56. Рукоятку 4 молотка делают из твердых пород дерева (кизила, рябины, дуба, клена, граба, ясеня, березы или синтетических материалов) Рукоятка имеет овальное сечение, отношение малого сечения к большому 1:1,5, т.е. свободный конец в 1,5 раза толще конца на котором насаживается молоток. Помимо обычных стальных молотков в некоторых случаях, например при сборке машин, применяют так называемые мягкие молотки со вставками из меди, фибры, свинца и алюминиевых сплавов. При ударах, наносимых мягким молотком, поверхность материала заготовки почти не повреждается. Из-за дефицитности меди, свинца и быстрого износа эти молотки мало эффективны и не всегда удобны в эксплуатации. В целях экономии металлов, медные или свинцовые вставки заменяют резиновыми, более дешевыми и эффективными в работе. |
Рисунок 15 Схемы расклинивания ручек. | Конец, на который насаживается молоток, расклинивается деревянным клином, смазанным столярным клеем, или металлическим клином, на котором делают насечки. Толщина клиньев в узкой части 0,8-1,5 мм, а в широкой – 2,5 – 6 мм. Если отверстие молотка имеет только боковое расширение, забивают один продольный клин; если расширение идет вдоль отверстия, то забивают два клина, и, наконец, если расширение отверстия направлено во все стороны, забивают три стальных или три деревянных клина, располагая два параллельно, а третий перпендикулярно к ним. Правильно насажанным считается молоток, у которого ось рукоятки образует прямой угол с осью молотка. |
Рисунок 16 Техника рубки | Для рубки используют, возможно, более прочные и тяжелые тиски (предпочтительно стуловые). Правильное положение корпуса, держание (хватка) инструмента при рубке – существенные условия высокопроизводительной работы. Для слесарной рубки используют поворотные и неповоротные параллельные тиски с шириной губок 100-140 мм. Для тяжелой кузнечной рубки применяют стуловые тиски с шириной губок от 130 до 150 мм, которые крепят на специальной тумбе. При рубке металла зубилом решающее значение имеет положение рабочего (установка корпуса и ног), которое должно создавать наибольшую устойчивость центра тяжести тела при ударе. Положение корпуса тела и ног. Установка корпуса тела рабочего при рубке зубилом будет правильной, если корпус выпрямлен и обращен в пол-оборота у оси тисков, левая нога выставлена на полшага вперед, а угол, образуемый линиями осей ступней, будет составлять 60-75˚ в зависимости от силы удара. |
Держание (хватка) зубила. Зубило берут в левую руку за среднюю часть на расстоянии 15-20 мм от конца ударной части. Удары наносят правой рукой. Левая рука только держит зубило в определенном положении; сильно сжимать в руке зубило не следует. При движениях правой руки, наносящей удары по зубилу, левая рука играет роль балансира при последовательных установках инструмента.
Рисунок 17 Держание (захват) молотка. | Держание (захват) молотка. Молоток берут правой рукой за рукоятку на расстоянии 15-30 мм от конца, обхватывая четырьмя пальцами и прижимая к ладони, большой палец накладывая на указательный, крепко сжимая всеми пальцами. Все пальцы остаются в таком положении при замахе и ударе. Этот способ называется «нанесение кистевого удара без разжатия пальцев. При другом способе хватки в начале замаха мизинец, безымянный и средний пальцы постепенно разжимают и рукоятку молотка охватывают только указательным и большим пальцами. Затем разжатые пальцы сжимают и ускоряют движение руки вниз. В результате получается сильный удар молотка. Этот способ называется «нанесение удара с разжатием пальцев». |
Рисунок 18 Удары молотком. | Удары молотком. Существенное влияние на качество и производительность рубки оказывает характер удара (замаха) молотком. Удар может быть кистевым, локтевым или плечевым. При кистевом ударе замах осуществляют молотком только за счет изгиба правой руки. При этом замахе сгибают кисть в запястье до отказ, разжав слегка пальцы, кроме большого и указательного, при этом мизинец не должен сходить с рукоятки молотка. Затем пальцы сжимают и наносят удар. Кистевой удар применяют при выполнении точных работ, легкой рубке, срубании тонких слоев металла и т. д. При локтевом ударе правую руку сгибают в локте. При замахе действуют пальцы руки, которые разжимаются и сжимаются, кисть (движение её вверх, затем вниз) и предплечье. Для получения сильного удара руку разгибают достаточно быстро. Этим ударом пользуются при обычной рубке, при срубании слоя металла средней толщины или при прорубании пазов и канавок. |
При плечевом ударе рука движется в плече, при этом получается большой замах и максимальной силы удар с плеча. В этом ударе участвуют плечо, предплечье и кисть. Плечевым ударом пользуются при снятии толстого слоя металла и обработке больших поверхностей.
Сила удара должна соответствовать характеру работы, а также массе молотка, длине рукояти, длине руки работающего. При рубке действуют обеими руками согласованно, метко наносят удары правой рукой, перемещая в определенные промежутки времени зубило левой рукой.
Рисунок 19 Установка зубила | Угол установки зубила при рубке в тисках регулируют так, чтобы лезвие находилось на линии снятия стружки, а продольная ось стержня зубила находилась под углом 30-35˚ к обрабатываемой поверхности заготовки и под углом 45˚ к продольной оси губок тисков. При меньшем угле наклона зубило будет соскальзывать, а не срезать, а при большем – излишне углубляться в металл и давать большую неровность. Угол наклона зубила при рубке не измеряют, опытный слесарь по навыку ощущает наклон и регулирует его положение движением левой руки. Во время рубки смотрят на режущую часть зубила, а не на боек, как это часто делает ученик-слесарь, и следят за правильным положением лезвия зубила. Удары наносят по центру бойка сильно, уверенно и метко. Этот навык приходит после тренировки. |
Выбор массы молотка. Массу слесарного молотка выбирают в зависимости от размера зубила и толщины снимаемого слоя металла (обычно толщина стружки составляет 1-2 мм) из расчета 40 г на 1 мм длины лезвия зубила. При работе крейцмейселем массу молотка принимают из расчета 80 г. на 1 мм длины лезвия.
При выборе молотка учитывают также и физическую силу рабочего. Удар осуществляют не за счет излишних мускульных усилий, ведущих к быстрому утомлению, а за счет ускоренного падения молотка. В момент нанесения удара рукоятку молотка прочно сжимают пальцами: слабо удерживаемый молоток при неточном ударе может отскочить в сторону, что очень опасно.
studfiles.net
Заточка режущего инструмента
Любой режущий инструмент в процессе эксплуатации рано или поздно тупится. Если он «одноразовый», у него одна дорога – на свалку. Если же инструмент реально восстановить, почему бы не воспользоваться такой возможностью? Исходя из этого, мы решили подготовить статью о том, как «приводят в чувство» режущий инструмент.
Уточним терминологию. Режущая кромка инструмента образуется двумя сходящимися плоскостями (или кривыми, как у сверл). Угол заточки есть угол при вершине схождения этих плоскостей. Остроту кромки можно представить как величину, обратную ширине «площадки» на вершине или диаметру вписанного в нее круга. Практически же чем глаже сходящиеся поверхности, тем более острой будет РК. Углы заточки у разных инструментов различаются и в зависимости от качества стали и разрезаемого материала составляют: у стамески – 17–25 градусов, у рубаночного железка – 25–40, у долота – 30–40, у зубила по металлу – до 60, у ножниц – 45–60, у ножей – 20–30 градусов.
Все режущие инструменты с точки зрения приемов заострения можно условно разделить на «ножи» (то есть то, что длиннее ширины точильного камня) и «резцы» (то, что уже камня: пилы, фрезы, резцы и сверла). Приемы заточки последних отличаются от всего остального.
К категории «ножей», кроме собственно ножей, отнесем ножницы, ножи электрофуганков и рейсмусов, а также прочий длинномер. Важное замечание: ножницы и ножи деревообрабатывающего оборудования точатся только с одной стороны. Перед заточкой инструмент надо очистить от грязи, опилок, смолы и прочего, так как эти субстанции легко и необратимо забивают точильный камень.
Заточка ножей
Сначала надо рассмотреть режущую кромку и решить, с какого абразива стартовать. Если нож новый или сильно затупленный, возможно, стоит начать с грубого камня. Хорошая заточка режущего инструмента – это всего лишь умение выдержать один и тот же угол при движениях по камню. Важное замечание: никогда не точите ножи на высокооборотном точильном круге – он мгновенно отпускает и пережигает режущую кромку.
Соблюдение угла заточки поможет сделать лезвие ножа оптимально острым.После применения точильного круга по режущей кромке лезвия ножа нужно пройтись наждачной бумагой, чтобы сточить оставленные абразивом царапины и мелкие заусенцы.
Итак, намочим точильный камень водой, положим его на старые газеты или лучше в углубление, выдолбленное в доске по форме камня, и водим ножом вдоль камня, соблюдая угол заточки. Нож должен набегать на камень под углом, как можно более близким к прямому. Но так как камень узкий, придется делать некое наклонное движение, перемещая нож по диагонали, то есть одновременно вдоль камня и вдоль ножа.
Большой ошибкой будет точить режущую кромку участками. Абсолютно точного перехода не получится – образуется ступенька, и нож будет плохо резать. Необходимо точить до тех пор, пока на кромке не появится завернутый вверх заусенец, который выявляется легким движением пальца поперек ножа от обуха к кромке (вдоль делать этого не стоит – можно порезаться). Когда заусенец появится по всей длине, нож нужно перевернуть и точить другую сторону.
Не пытайтесь доточить только те участки, где нет заусенца. Непрерывный заусенец показывает, что одна фаска режущей кромки ножа получила по всей длине плоскость. Когда при заточке второй стороны заусенец появится на уже заточенной, надо опять перевернуть нож и перейти на более мелкий абразив.
Чем меньше зерна абразива, тем более гладкие фаски и острее кромка. После мелкого камня надо перейти к наждачной бумаге, постеленной абразивом вверх на гладкую поверхность, например на кусок стекла или стали либо на ровную часть верстака.
Ножницы следует затачивать только с фаски.
Обычно используют сначала дешевый двухсторонний точильный камень и затем, последовательно, наждачные бумаги с зернистостью 120, 400, 600 (или 800) и иногда 1200. Самое сложное и простое в этом процессе – выдерживать одинаковый угол при всех движениях ножа. Стоит отметить, что постоянная практика лучше всяких хитроумных приспособлений – они ломаются и к тому же стоят намного дороже камня, который, кстати, в них тоже присутствует. Хитрость заключается в том, чтобы двигать затачиваемый инструмент при неподвижном запястье и внимательно смотреть на верхнюю плоскость инструмента. Тогда угол выдерживается весьма точно.
Ножницы точат только с фаски, прилегающую к другой бранше плоскость лишь выравнивают на мелкой наждачке.
Ножи фуганков тоже точат только с фаски. Их особенность в том, что нужно часто прикладывать кромку к линейке или стеклу, чтобы видеть прямизну режущей кромки и избегать ее скругления.
Заточка стамесок и рубаночных железок
Стамески и рубаночные железки имеют много общего. При сильном затуплении или выбоинах на режущей кромке, которые возникают из-за сучков или гвоздей, надо сначала ее спрофилировать. К слову, так же поступают при изготовлении резца по дереву из закаленной заготовки.
Наиболее эффективный способ заточки железко для рубанка – с помощью электроточила.
Здесь нам понадобится высокооборотистое электроточило. Часто макая железко в воду для остывания, нужно сделать фаску с углом немного острее 25 градусов. Ни в коем случае не утончайте кромку железка до появления режущей кромки, так как огромное трение абразива о металл нагревает последний, и при попытке заточки на высокооборотном камне режущая кромка будет немедленно отпущена и инструмент испорчен.
Когда толщина кромки станет около полумиллиметра, надо угольником проверить перпендикулярность режущей кромки оси или боковой стороне рубаночного железка.
Окончательно заострять железко можно двумя способами. Лучше всего – на низкоскоростном электроточиле с мокрым камнем (налив воды в поддон и равномерно прижимая железко к камню). Если ширина последнего недостаточна, то необходимо водить железком из стороны в сторону.
Болт с двумя гайками поможет соблюсти необходимый угол при заточке железко для рубанка.
Если такого точила у вас нет, придется работать вручную на абразивном бруске, смоченном водой. Его лучше положить в углубление в доске – так удобнее держать. Железко ставят на камень под выбранным углом или проще – фаской на камень, покачивая вперед и назад, пока он не встанет всей фаской. Заостряют движениями вдоль камня и обратно, а лучше – описывая будущей режущей кромкой восьмерки, чтобы достичь равномерного износа камня и сохранить его плоскостность. Когда появится заусенец, кладут железко плоскостью на камень и парой движений удаляют его, после чего переходят к более мелкому абразиву, например, перевернув двухсторонний камень.
Окончательная заточка производится положенными на стекло наждачными бумагами разной степени зернистости.
Маленькая хитрость. Болт с гайкой и двумя большими шайбами можно использовать как нехитрое приспособление для держания правильного угла наклона рубаночного железка (см. рисунок).
Заточка пил по дереву
Пилы по дереву, как правило, продаются не всегда достаточно острыми (а крупнозубые в большинстве своем – просто тупыми). Опять возникает необходимость заточки, причем для каждого вида работ она своя.
Если пила недостаточно разведена, сначала ее разводят. Если под рукой нет специализированной разводки, можно обойтись плоскогубцами. Пилу зажимают в тисках зубьями вверх, садятся так, чтобы смотреть вдоль полотна, и отгибают зубья в разные стороны через один, при каждом движении наклоняя плоскогубцы на один и тот же угол. Обычно небольшая разводка всегда есть изначально, и ее надо просто увеличить, если дело имеешь с сырым деревом или большими пилами. Если пила небольшая и для точных работ, вполне можно оставить и заводскую разводку.
При заточке пилы по дереву используется трехгранный напильник.
Для заточки зубьев используется треугольный напильник. Им точат с внутренней (по отношению к разводке) стороны зубьев пилы. Напильник держат так, чтобы угол режущей кромки был 60–45 градусов. На деле легче и быстрее заострить сначала одну сторону зубьев, а потом, перевернув пилу, заточить зубья другой стороны. В этом случае движения более однотипные – пила получается более острой.
При заточке пил лучше работать одному и в тишине, отключив помехи в виде радио и телевизора, так как неосторожное движение либо портит инструмент, либо наносит трудно заживающую рану. Совет: если при резке пила стремится уйти в сторону, это означает, что зубья разведены неравномерно – нужно увеличить их отклонение с той стороны, в которую пилу уводит.
Заточка пильных дисков
Дисковые пилы затачивают с задней поверхности, при работе обращенной к обрабатываемому материалу. Передняя, которая при пилении набегает на материал, остается как есть.
Диск можно точить или прямо в станке (если речь идет об оснастке для станка), или вынув из станка или циркулярной пилы. В первом случае сначала нужно выдернуть вилку из розетки, чтобы избежать случайного пуска станка. Диск следует подклинить, положив с двух сторон от него по тонкой деревяшке и прижав их к зубьям. Зуб, с которого начинается заточка, надо пометить фломастером по боковой стороне, чтобы не ошибиться в работе. Затачивая первый зуб, запоминайте количество движений напильником или алмазным надфилем – все остальные зубья предстоит точить с тем же усилием и тем же количеством движений абразивного инструмента, что и первый.
Если диск был снят со станка, зажмите его в тисках и проделайте те же процедуры, что описаны выше.
Далее диск нужно вернуть в станок и распилить ненужную деревяшку. При сильном шуме или неровной подаче надо проверить, одинакова ли высота зубьев. Для этого к режущему краю подносят фломастер и медленно проворачивают диск рукой на один оборот в сторону, обратную направлению вращения. На каждом зубе останется отметина. Осмотрев диск, можно обнаружить зубья, которые выше или ниже других. Если разница велика, необходимо аккуратно уменьшить высоту слишком длинных зубьев.
Заточка фрез
Заточку фрез ведут по задней или передней поверхности.
Перед заточкой от фрезы необходимо предварительно отделить направляющий подшипник, иначе можно испортить инструмент.
Фасонные концевые фрезы проще затачивать по передней поверхности – либо тонким алмазным бруском, либо (при узкой стружковыводной канавке) наждачной бумагой, обернутой вокруг рейки из твердого дерева или полоски стали. По мере стачивания передней поверхности кромка заострится, а диаметр фрезы уменьшится (незначительно).
С фрез с направляющим подшипником сначала надо снять подшипник и только потом затачивать их. Попытка сэкономить минуту закончится загубленным подшипником и испорченной фрезой.
Заточка токарных резцов
Токарные резцы заостряют со стороны передней и задней поверхностей. Нюанс там только один – резец сужается вниз, поэтому, чтобы его боковые плоскости ни в коем случае не соприкасались с заготовкой, контакт должен быть только по режущей грани.
Резцы из быстрореза и с твердосплавными напайками точат на точильном круге. Если на станке подачи воды не предусмотрено, почаще макайте резец в емкость с водой.
Заточка сверла
При заточке сверла нужно держать его так, чтобы получить желаемый угол схождения режущих граней. При этом режущая кромка должна быть симметричной.
Затачивать сверло необходимо с особой точностью.
Проще всего провести на подручнике электроточила линию фломастером и держать сверло параллельно ей. Однако просто положить сверло по линии недостаточно, следует еще и повернуть его на нужный угол вокруг оси, а потом на 180 градусов относительно первого положения.
Нужен угол между кромкой сверла и плоскостью стола, то есть внешний край должен быть ниже центра, иначе сверло будет не резать материал, а ехать по нему задней поверхностью. Для контроля этого угла есть разные приспособления, но проще стоять или сидеть за столом так, чтобы блик от освещения был на внешней части режущей кромки, а потом, не меняя положения тела, повернуть сверло в пальцах и опять поймать блик – кромки будут заострены под одним углом.
Заточка сверла по задней поверхности называется одинарной, при ней остается довольно большая перемычка в центре, которая не режет, а скоблит металл. Если ее подточить, скорость сверления возрастет. Способов подточки перемычки много. На заводах ее подтачивают тонкими абразивными или алмазными кругами либо на углу широкого камня. Но можно подтачивать перемычку так, как показано на фото. Защитные очки при выполнении заточки строго обязательны.
Электроточила
Для облегчения труда при заточке инструмента существуют различные электроточила и заточные станки.
Выбор электроточила крайне прост. Такой станок состоит из асинхронного двигателя (подобные моторы в совершенстве освоены промышленностью), точильных кругов (они сменные и меняются при помощи гаечного ключа) и кожухов. Если точило берется не для промышленного применения, то марка не имеет такого уж большого значения. Подобное оборудование включают ненадолго, и ресурс его будет расходоваться крайне медленно – даже недорогой станок прослужит много лет.
Диаметр круга прямо влияет на цену точила, поэтому мастеровому-любителю или маленькому предприятию не стоит гнаться за большими диаметрами.
Осматривая электроточило перед покупкой, попробуйте пошевелить вал. Если он не только вращается, но и ходит – перед вами брак. Крутаните камень рукой и посмотрите на свободный конец вала, не вибрирует ли он? Лучше всего, конечно, включить точило, но не во всех магазинах позволяют это сделать.
Заточные станки
Заточные станки делятся на три группы.
Первая – фактически высокоскоростное электроточило (около 3000 об/мин), оборудованное сменными держателями для разных видов инструмента.
|
Вторая – узкоспециализированные станки, например для заточки сверл. Зачастую на них нельзя заточить никакой другой режущий инструмент.
Третья – станки, оборудованные низкоскоростными кругами с водяным охлаждением («мокрые»). Скорость вращения – 80–150 оборотов в минуту. На них можно затачивать и править любой режущий инструмент, от сверл из быстрорежущей стали до ножей из углеродистой стали. Низкая скорость и водяное охлаждение – необходимые условия для выведения тончайшей и острейшей режущей кромки. Часто такие станки имеют и полировальный круг для полировки режущей кромки.
Работа с электроточилом и заточным станком
После работы на станке с «мокрым» кругом не забывайте выливать воду из поддона и не оставляйте камень в воде одним боком на продолжительное время – камень напитывается водой, теряет прочность и превращается в эксцентрик, разбивающий станок.
После работы с мокрым кругом нужно удалять воду из поддона станка.
Абразивные круги всегда должны «набегать» на режущую кромку затачиваемого инструмента, а полировальные (кожаные, войлочные, вулканитовые) – «убегать», то есть вращаться «от рабочего». Не пытайтесь полировать вращением круга «на себя» – обрабатываемый объект врежется в круг, будет им захвачен и выброшен в сторону оператора. Кроме порчи круга, можно получить серьезную травму.
Если вы устанавливаете полировальный круг на высокоскоростное электроточило, поверните кожух на 180 градусов. Для работы на полировальнике либо разверните станок, либо подойдите к нему с другой стороны.
library.stroit.ru