Технология газобетона: производство и ключевые особенности строительства. Газобетон производства технология
особенности блоков, технические характеристики, фото
Как производится газобетон? Каким образом технические характеристики газобетонных блоков соотносятся с практическими качествами этого строительного материала? Какие особенности материала нужно учитывать при строительстве? Давайте разбираться.

Один из старейших домов из автоклавного газобетона. Постройка — 1939 год, г. Рига.
История
Она начинается с получения чешским промышленником Гоффманом патента на технологию вспенивания цементных и гипсовых растворов. Патент был выдан в 1889 году; изобретение сводилось к добавке в раствор кислоты и реагирующих с ней солей.
Цель — получение материала с уступающей бетону плотностью и улучшенными теплоизоляционными характеристиками — была достигнута; однако метод был дорогим и крайне неудобным в применении.
Идея получила развитие четвертью века позже: американцы Дайер и Аусворт использовали в качестве газообразующей добавки порошки металлов — цинка и алюминия. Собственно, современная технология производства газобетона не слишком отличается от разработанной тогда. Именно 1914 год считается годом рождения материала.
Однако: первый автоклавный газобетон начал массово производиться в Швеции еще на 15 лет позже.В 1929 году компания Ytong наладила промышленный выпуск блоков из смеси извести и кремнезема, проходивших пропарку при повышенной температуре.Ytong по сей день считается одним из ведущих производителей материала.

В 1934 году в Швеции был налажен выпуск блоков по несколько иной технологии: в качестве связующего использовалась не известь, а цемент.
В СССР производство автоклавных ячеистых бетонов стало массовым к середине 20 века. К нашему времени объем производства блоков достиг примерно 3,5 миллионов кубометров в год.
Описание
В чем причина популярности материала? Какие технические характеристики газобетона сделали его настолько востребованным?
Достоинства
- Теплоизоляционные качества газобетонных стен примерно соответствуют соответствующим характеристикам сухой древесины, в разы превосходя тяжелый бетон, силикатный и керамический кирпич. Схожий материал — пенобетон — тоже отстает по этому параметру.

Сравнение характеристик газо- и пенобетона.
- Механическая прочность превосходит пенобетон, хоть и заметно уступает более плотным материалам.
Уточним: в зависимости от марки по плотности различают конструкционные, конструкционно-теплоизоляционные и строго теплоизоляционные блоки.Прочность первых изделий позволяет использовать их для сооружения несущих стен и перекрытий; последние применяются в каркасно-монолитном строительстве в качестве заполнения стен.
- Благодаря все той же пористой структуре, производство оказывается довольно экономичным: на фиксированный объем строительного материала уходит меньше сырья.
- Структура с открытыми порами способствует естественной вентиляции стен. Эта особенность напоминает деревянные дома: часть воздухообмена с улицей и до трети парообмена осуществляется непосредственно через ограждающие конструкции.
- Простота обработки тоже напоминает о древесине: газобетон легко пилится ручной пилой, его можно сверлить и вбивать в его толщу гвозди.
Характеристики
Стоит сделать небольшое лирическое отступление и рассказать о методах классификации газобетона.
Основные характеристики, описывающие материал, выглядят так:
Характеристика | Описание |
Марка по плотности | Соответствует плотности в кг/м3 |
Класс прочности | Соответствует максимально допустимой нагрузке на сжатие в мегапаскалях (МПа) |
Морозостойкость | Количество циклов заморозки и оттаивания, которые блок может перенести без падения прочности более чем на 5% |
А теперь давайте посмотрим, какие значения эти и некоторые другие важные для строителя параметры принимают у газобетонных блоков наиболее востребованных типов.
Марка по плотности | D400 | D500 | D600 | |
Класс прочности | В 2 | В 2,5 | В 3,5 | В 3,5 |
Коэффициент теплопроводности, Вт/м*С | 0,096 | 0,12 | 0,14 | |
Морозостойкость, циклы | F75 | F75 | F100 | F100 |
Усадка при высыхании, мм/м | 0,3 и менее | |||
Паропроницаемость, мг/м*ч*Па | 0,24 | 0,28 | 0,24 | 0,23 |
Обратите внимание: марке по плотности D500 соответствуют два класса прочности.Разница между ними заключается в соотношении количества связующего и заполнителя при производстве блоков.
Что этот набор характеристик означает в практическом плане?
- Газобетон обеспечивает примерно втрое — впятеро более эффективное утепление по сравнению с керамическим кирпичом. Так, для того, чтобы обеспечить сопротивление теплопереносу в 2,5 м2*С/Вт, необходима газобетонная кладка толщиной 375 мм или кирпичная толщиной 1100 мм.

Сравнение теплоизолирующих качеств разных материалов.
- При упомянутом соотношении толщины нагрузка на фундамент, соответствующая квадратному метру кладки, в первом случае равна 205 килограммам, а во втором — 2000 кг.
- Минимальная ширина ленточного фундамента в первом случае равна 400 мм, во втором — 1200.
Производство
Из чего делают газобетон?
Сырье
В состав материала входит два основных компонента — наполнитель и связующее. Что может использоваться в этом качестве?
Наполнитель
- Тонкомолотый кварцевый песок.

Речной песок — наиболее востребованный наполнитель.
- Измельченные отходы горно-добывающей промышленности (скальные и осадочные породы).
- Зола, образующаяся при сжигании угля.
- Вторичные продукты обогащения руд.
- Металлургический шлак.
Связующее
- Известь.
- Портландцементы.
- Смешанное связующее (цемент + известь, известь + гипс и т.д.).
Технология
Технология изготовления газобетона в промышленных масштабах включает следующие основные операции:
- Наполнитель смешивается со связующим, после чего в полученную массу добавляется суспензия газообразователя — алюминиевого порошка. В чистом виде порошок не используется: он слишком легко разносится любым сквозняком.
- Смесь разливается в формы, где выделяющийся при реакции алюминия с щелочной средой водород вспучивает ее.
- После схватывания пористая масса нарезается на блоки. Для резки используются прочные струны толщиной до миллиметра; карманы для захвата и переноски блоков вырезаются фрезой.
- Последний этап — сушка в камерах с подогревом или пропаривание в автоклаве. Второй сценарий требует более дорогостоящего оборудования, зато способствует скорейшему набору газобетоном прочности. Среднее время выдержки блоков в автоклаве — 12 часов; рабочее давление — около 12 бар при температуре 190 С.

Загрузка автоклавов.
Любопытно: выход на рабочий режим и подготовка к разгрузке автоклава постепенны и занимают 1,5 — 2 часа.
- Последний этап — упаковка продукции в водонепроницаемую упаковку и укладка на поддоны.

Водонепроницаемая упаковка обеспечивает стабильно низкую влажность.
Когда вместо пропарки используется сушка блоков? Прежде всего, при производстве газобетона своими руками, в домашних условиях либо при полукустарном изготовлении небольших партий на продажу.
Как уже упоминалось, цена необходимого оборудования в этом случае гораздо ниже; однако качество продукции несколько ухудшится:
- Усадка в процессе сушки достигнет 3-5 мм/метр.
- Прочность бетонных изделий на сжатие не превысит 10 — 12 кгс/см2. Впрочем, постепенный набор прочности при поглощении атмосферной влаги связующим будет продолжаться несколько лет.
Особенности строительства
Какие ограничения использование газобетонных блоков накладывает на строительство?
Фундамент
Основное требование к нему — максимальная жесткость, исключающая любую деформацию несущих стен. Несмотря на относительно высокую прочность, газобетон полностью лишен эластичности и при изгибающих нагрузках дает трещины.
Какие виды фундаментов применяются при газобетонном строительстве?
- На скальных и сухих супесчаных грунтах используются мелкозаглубленные ленточные основания.
- На пучинистых грунтах (глины, суглинки) оптимальное решение — свайный фундамент на буронабивных сваях с монолитным железобетонным ростверком.
- На болотистых почвах и других нестабильных грунтах заливается бетонный плитный фундамент. Он равномерно распределяет нагрузку по значительной площади и исключает любые неравномерные просадки стен.

На фото — плитный фундамент.
Стены
Ключевое требование к стенам — высокое сопротивление теплопереносу. Оно нормируется действующими СНиП и для центра страны равно 3 — 3,2 м2 * С/Вт.
Обеспечить соответствующие тепловые характеристики, согласно заверениям производителей, могут:
- Блоки марки по плотности D500 при толщине стен в 500 мм.
- Блоки D600 — при толщине стен в 600 мм.
Для несущих стен из газобетона действуют ограничения по этажности строения.
Количество этажей | Класс прочности блоков |
1 — 2 | В 2 |
3 | В 2,5 |
4 — 5 | В 3,5 |
Более 5 | Строительство несущих газобетонных стен не допускается. Строение должно быть каркасным. |
Кроме того: в сейсмоопасных районах армирующий железобетонный каркас предназначен для повышения сейсмостойкости конструкции здания.

В опалубке — армопояс, способствующий повышению сейсмостойкости строения.
Какие правила действуют для внутренних несущих стен и ненагруженных перегородок?
- Если на стену опирается одна плита перекрытия, она возводится из блоков прочностью В 2,5 с толщиной 240 мм или из блоков прочностью В 3,5 толщиной 200 мм.
- Стена, на которую опираются две плиты, должна быть толще — 300 и 400 мм соответственно.
- Ненагруженные межквартирные перегородки выполняются из блоков ненормируемой прочности толщиной не менее 240 мм. Инструкция связана с необходимостью обеспечить качественную звукоизоляцию.
- Межкомнатные перегородки имеют толщину 100 — 150 мм. Прочность, разумеется, не нормируется и в этом случае.
Перемычки
Они могут выполняться из монолитного железобетона (в этом случае перемычка заливается на месте; кладка стен используется как часть опалубки) или из специальных U-образных блоков. В последнем случае перемычка может быть сборной.
Как обеспечивается достаточная несущая способность конструкции?
- U-образные блоки выставляются на временную подпорку полостью вверх. Они должны заходить за края проема как минимум на 10 см с каждой стороны.
- В полость блоков закладывается арматурный каркас.
- Полость бетонируется. Подпорка убирается после надежного схватывания бетона.

Устройство сборной перемычки.
Кладочный раствор
На обычный цементно-песчаный раствор, приготовленный в пропорции 1:3, выкладывается только первый ряд блоков. Следующие ряды кладутся только и исключительно на специальный клей для ячеистых бетонов, обеспечивающий толщину шва не более 3 мм.

Клей для газобетона.
Почему обычный раствор не стоит использовать для кладки?
- Толстый шов — это мостик холода, ведущий в помещение с качественной теплоизоляцией. Как вырастут потери тепла — думается, можно не объяснять.
- Кроме того, блоки обладают точными размерами и идеальной геометрией. Тонкие швы позволяют использовать это преимущество, делая внешний вид кладки безупречным.
Наружная и внутренняя отделка
Главное требование к ней вполне стандартно: паропроницаемость стен должна увеличиваться изнутри наружу. Нарушение этого несложного правила приводит к отсыреванию стен, а в перспективе — и к их ускоренному разрушению.
Поскольку паропроницаемость газобетона исключительно высока, для стен из него обычно используются специальные штукатурные смеси с повышенной паро- и воздухопроницаемостью. Не менее популярное решение — вентфасады, обеспечивающие дополнительное утепление, и не препятствующие естественной вентиляции стен.

Утепленный вентфасад с облицовкой виниловым сайдингом.
Заключение
Надеемся, что предложенная информация будет полезной как начинающим строителям, так и потенциальным производителям недорогого и практичного строительного материала. Как всегда, видео в этой статье содержит дополнительные материалы. Успехов!
masterabetona.ru
Производства газобетонных блоков: оборудование, технология
Газобетон обладает высокими прочностными и теплоизоляционными характеристиками. Строительный материал является удачным выбором застройщиков в сфере индивидуального и коллективного строительства. Его изготовление может стать выгодным бизнес-проектом, к тому же цена мини завода по производству газобетона, не отличается высокими отметками и напрямую зависит от решения предпринимателя о выпуске конкретного вида материала.

Газобетон
Общая информация о материале
В названии строительного материала, газобетон или автоклавный ячеистый бетон, заложены его характеристики и технологии производства. Он является искусственным камнем, в полости которого расположены воздушные поры, а его изготовление подразумевает обработку сырьевого материала в условиях автоклава. Для газоблоков характерны сберегающие характеристики, которые обеспечиваются за счет пористой структуры. Они имеют небольшой вес, что выделяет их на фоне кирпичей и других видов строительной керамики.
Строительный материал может быть использован для возведения несущих конструкций сооружения или его внутренних перегородок. Он не подходит для промышленных объектов и высотных зданий, однако отлично зарекомендовал себя в сфере индивидуального строительства. Использование газоблоков обеспечивает оперативное строительство, по причине того, что они имеют большой размер. Их легкость позволяет сократить расходы на закладку фундамента, поскольку ему не нужно претерпевать большие нагрузки.
Состав
Уникальные характеристики строительного материала обусловлены его составом.
Сырьем для его изготовления являются цемент, кварцевый песок и алюминиевая пудра, выполняющая роль газообразователя. Для придания специфичных свойств газоблокам, некоторые производители в состав добавляют дополнительные ингредиенты, такие как известь, зола и гипс.

Цеховое производство
Сырье
Газобетон изготавливается на основе сухих компонентов, в смесь которых добавляется вода, с температурой не ниже 45°С. Такие условия обеспечивают быстрое твердение блоков и их прочности. Соблюдение технологии способствует увеличению производительности, улучшению качества материала и уменьшению количества используемого сырьевого цемента, поскольку соответствующий температурный режим обеспечивает стимулирование активности сухих компонентов смеси.
В производстве может быть использован карьерный или речной песок с размером зерен до 2 мм. В нем не должны содержаться илистые и глиняные включения. Сырьевой материал может быть заменен шлаком или золой, являющимися отходами металлургического производства. Такое решение производителя сократит его расходы и позволит получить продукцию с меньшей плотностью.
Планируя производство, следует закупать цемент, имеющий маркировку М 400 или М 500. Алюминиевая пудра должна быть марки ПАП-1 или ПАП – 2. Она может быть заменена на специальную пасту или суспензию, что считается более удобным для производства, ввиду упрощения этапа замешивания. Компонент вступает в реакцию в растворе, имеющем щелочной состав, в ходе которой образуется соль алюмината и выделяется водород, обеспечивающий формирование пор.
Соотношение веществ

Резка изделия
Качество строительного материала зависит от правильного подбора соотношения составляющих компонентов. Стандартные рекомендации определены только для газоблоков, изготавливаемых автоклавным способом. В них предусмотрено регламентированное соотношение сырьевых компонентов по отношению к общему объему смеси:
- цемент – 50–70 процентов;
- песок – 20–40 процентов;
- алюминиевый порошок – 0,04–0,09 процентов;
- вода – 0,25–0, 8 процентов;
- известь – 1–5 процентов.
Пример
Для получения одного кубического метра газобетона необходимо взять 90 килограмм цемента, долить до 300 литров воды. В полученную смесь добавить 35 килограмм извести, 375 килограмм песка и 50 грамм алюминиевого порошка. В условиях конкретного производства все значения могут быть скорректированы в соответствии с качественными характеристиками сырьевых материалов.
Оборудование для производства газоблоков
Несмотря на то что технология производства строительного материала не отличается сложностью, без специального оборудования и соблюдения алгоритма действий, невозможно получить газобетон хорошего качества. Для этого, до открытия цеха, необходимо приобрести автоматизированную линию. При ее покупке с завода-производителя или его официального представителя, дополнительно обычно предоставляются консультационные услуги в сфере монтажа оборудования, его настройки и подборе оптимального состава сырьевой смеси. Линия содержит оборудование и устройства:
- печь-автоклав;
- формы;
- передвижные поддоны для транспортировки;
- смесители;
- дозаторы;
- аппарат резки готового изделия.
Каждый составляющий элемент комплекса может быть приобретен отдельно, поэтому при выходе его из строя, восстановить линию не составит труда. Она также может быть сформирована из отдельных устройств, однако при таком решении предпринимателю важно учесть соответствие их параметров, которые позволили бы обеспечить гармоничное взаимодействие всей аппаратуры.

Схема производства
Оборудование для производства газобетонных блоков бывает нескольких типов. При его выборе учитывается планируемая суточная производительность, количество обслуживающего персонала и порядок организации работы.
Для стационарных линий характерна суточная производительность до 60 м3 готовых изделий. Для обеспечения бесперебойной работы, необходимо арендовать или купить производственные и складские помещения, площадью, не меньше 500 м2. Один человек вполне сможет обслужить такую линию, поскольку все операции в ней производятся в автоматическом режиме. Принцип ее функционирования заключается в подаче в стационарно расположенный смеситель сырьевых материалов, в перемешивании их и в заполнении формы смесью с последующим выполнением всех технологических этапов в автоматическом режиме.
При планировании суточной производительности до 150 м3, предпринимателю рекомендуется рассмотреть вариант приобретения конвейерных линий, позволяющих обеспечить оперативное производство строительного материала. Поскольку сроки созревания остаются прежними, необходимо позаботиться об увеличении производственного помещения в отсеке дозревания готовой продукции. Несмотря на то что большинство процессов проводится в автоматическом режиме, для обслуживания устройств понадобится штат работников в минимальном количестве до 8 человек.
Мини-линии актуальны при производстве блоков для реализации собственных потребностей при обеспечении строительных работ, а также при наличии небольшого объема заказов.
На них не получится изготавливать более, чем 15 м3 готовых изделий в сутки. В конструкции стационарно установлены формы, а подвижной частью является смеситель. Преимуществом линии является отсутствие необходимости в больших площадях. На начальном этапе достаточно до 160 м2, поэтому мини-линии пользуются популярностью в качестве стартового варианта.

Упрощенная схема
В сфере частного строительства применяются мобильные установки, с помощью которых можно самостоятельно изготавливать газоблоки. Они продаются в комплекте с компрессором и могут функционировать от бытовой электросети. Их приобретение окупается в кратчайшие сроки, поскольку расходы на строительные работы снижаются на 30 процентов.
Технология производства газобетона
Технология производства зависит от решения производителя относительно вида и характеристики готового изделия.
Газобетон бывает автоклавный и неавтоклавный. Неавтоклавный строительный материал стоит дешевле, поскольку для него характерна хрупкость, а для обеспечения производства материала затрачивается меньше средств, поскольку не нужно приобретать дорогостоящее оборудование- автоклав, оплачивать электроэнергию на его функционирование, а также вкладывать деньги в его содержание. Неавтоклавная технология производства проводится в соответствии с определенным алгоритмом:
- Взвешивание компонентов смеси в соответствии с рецептурой.
- Перемешивание вручную или при помощи специального оборудования.
- Выгрузка в формы.
- Выдержка изделия.
- Извлечение готовой продукции из формы.
В связи с тем, что в результате химических реакций, происходящих в смеси, будет происходить газообразование, формы заполняются только наполовину. Ожидание окончания реакции занимает до четырех часов, за которое компоненты полностью занимают объем формы. После отбора из форм излишек состава, его оставляют на вызревание, которое будет длиться до 16 часов, по истечении которых происходит распалубка и перегрузка на поддоны для набирания отпускной прочности, что длиться три дня. После завершения всех операций, изделие отправляется на склад, однако продавать его можно только через месяц, когда оно наберет марочную прочность.
В бизнес-план производства газобетона следует включить расходы на приобретение профессионального оборудования.
Технология производства на первых этапах работ практически не отличается от безавтоклавного метода. Набирается необходимое количество всех компонентов при помощи дозаторов, загружается в смеситель и перемешивается. Для выполнения этой задачи допускается использование бетономешалки. Через 15 минут после окончания смешения исходных ингредиентов, вводится алюминиевый порошок, являющийся газообразователем. Вещество вступает в реакцию с базовой смесью без автоклава.
Смесь сырьевых компонентов разливают по формам и выдерживают 6 часов, после чего проводится нарезка газоблоков, которые впоследствии должны набрать плотность на протяжении 18 часов. После завершения базовых операций, проводится автоклавирование. Сформированные блоки газобетона загружаются в герметичную камеру печи, в которой при высокой температуре каждый блок обрабатывается водяным паром под давлением до 12 кг/см2.
Неавтоклавное изделие сушится в естественных условиях. Автоклавная продукция не требует сушки, однако ее все равно нужно выдержать месяц до набора прочности.
Важным этапом производства обеих видов газобетона, является сохранение целостности в процессе транспортировки к потребителю. Для реализации этой задачи необходимо готовое изделие упаковать в термоусадочную пленку и транспортировать на деревянных поддонах.
Вконтакте
Одноклассники
Google+
101biznesplan.ru
Технология производства газобетона
В данной статье мы поговорим о технологии производства газобетона. Если вы собираетесь строить дом из газобетона, то необходимо понимать не только процесс постройки дома, но и иметь основные представления о газобетоне с возможными трудностями, которые могут возникнуть при строительстве дома.
В первую очередь, что такое автоклавный газобетон? Автоклавный газобетон (АГБ) сильно отличается от обычно нами представляемого бетона. АГБ – композитный материал, в котором прочность при сжатии обеспечивается прочностью входящих в его состав заполнителей, а прочность при растяжении и изгибе, постоянства форм обеспечивается характеристиками вяжущего. Знаем цементный бетон, асфальтный бетон, полимерный бетон и в этом ряду слово газобетон выбивается. Газобетон, строго говоря, не бетон, а искусственно синтезированный минерал, причем достаточно однородный. По постоянству прочности он почти совпадает со сталью. Коэффициент вариации прочности порядка 5%, примерно также как у стальных сплавов.
Различия газобетона и газосиликата
В современном разговорном языке понятия газобетона и газосиликата перемешаны. Есть области в России, где распространен термин газосиликат. На северо-западе и центральной России чаще используется газобетон. По большинству описывается один и тот же материал – ячеистый бетон автоклавного твердения.
Смешение понятий возникло еще с 1960-1980 годов, когда производство автоклавных бетонов развивалось стремительно, параллельно существовали несколько способов производства. В частности были автоклавные бетоны на цементном, известковым и смешанном вяжущем.
В современной промышленности остались более долговечные на цементном и смешанном вяжущем, а чисто силикатные ячеистые бетоны вымерли как класс. Чистых газосиликатов современная промышленность не выпускает.
Поэтому сейчас, говоря «газосиликат», как правило, имеют в виду автоклавный газобетон.
Свойства газобетона определяется двумя технологическими переделами:
- Помол песка смалывается до тонины цемента (2000 – 3000 см²/г)
- Автоклавная обработка. Автоклав по сути большая скороварка, в которой поддерживается (нагнетается) давление 12 атм. при температуре 188°С и в течении 12 часов газобетонные массивы находятся в автоклаве
Кварцевый песок расходуется в синтезе гидросиликатов
SiO2 + h3O = h3SiO3
Синтезируется тоберморит – основной минерал, обеспечивающий прочность и долговечность газобетона. По сути силикатный кирпич, но только с ячеистой структурой.
Технология производства газобетона
Алюминиевая пудра, или любой другой металл, стоящий в электрохимическом ряду до водорода вводится в виде суспензии. Одновременно всё подается в бетономешалку известь, цемент, песчаный шлам (суспензия молотого песка) и просто вода. Компоненты проходят взвешивание, дозируются и затем отправляются на смешение в скоростную мешалку. Смешение происходит за 30 секунд в полном объеме, и за один массив выходит порядка 4,5 м³ газобетона. Заливается в формы разогретые до 40 °С, приблизительно половина от этого объема.
В результате реакции происходят газовыделения, когда алюминий вытесняет h3. Алюминий превращается в гидроксид, а затем участвует в гидросиликатах, где получаются алюминаты кальция и силикаты алюминия и т.д. Алюминий в окисленном состоянии, как в земной коре.
После заливания смесь отправляется в камеру созревания. Там происходит процесс парообразования. Образуется большое количество пор, массив возрастает до требуемого объема, набирая прочность, называемую транспортной. Затем массив при помощи тележки выезжает из камеры и отправляется на линию резки. Массив достаточно большой 4,5 метра по объему. Здесь происходит нарезка на блоки.
Далее из отдельных массивов формируются автоклавные поезда, которые поступают на автоклав. Здесь в течение 12 часов обрабатываются при высоком давлении в среде насыщенного водяного пара.
После автоклавной обработки блоки поступают на разделительную машину, т.к. в автоклаве могли слипнуться. На некоторых заводах разделение происходит до автоклавирования.
После разделения блоки упаковываются сверху в термоусадочную пленку или полиэтилен, это помогает сохранить влажность газобетона до начала строительства. Газобетон на заводах хранится на открытых площадках до 2-3 лет.
Далее со склада материал отправляется на строящийся объект.
mainstro.ru
Технология производства газобетона
Газобетонные блоки, как и пенобетонные изделия, являются одной из разновидностей ячеистых бетонов. Пористая структура придает этому материалу хорошие тепло и шумоизоляционные свойства, малый вес при больших размерах и достаточную прочность, что качественно выделяет его среди остальных стеновых материалов, широко использующихся при строительстве перегородок, гаража, дачи и др. Кроме этого, сама технология производства газобетона довольно проста, при этом она не требует больших затрат, а цена готового продукта приятно удивляет.
Виды изготовления
Существует 2 разновидности технологии производства газобетонных блоков, а именно: автоклавного твердения и естественной выдержки. В первом случае используют специальные камеры – автоклавы, снабженные регулятором давления и температуры. Газобетон, получаемый таким способом более качественный и прочный, нежели тот, который был высушен в естественных условиях, но зато вторая технология приемлема для тех, кто хочет изготовить блоки в домашних условиях, хоть он получится не настолько надежный как хотелось бы, но он все равно будет пригоден для строительства малоэтажных частных домов.
Сырьевые компоненты
Для изготовления газобетонных блоков по любой технологии понадобятся следующие его составляющие:
Вода
Для блоков пригодна любая питьевая и техническая чистая вода, однако она должна отвечать всем требованиям ГОСТ 23732-79. Вода с температурой 45, качественно увеличит скорость твердения, прочность и производительность линии изготовления. Подогрев воды поможет снизить количество применяемого цемента, за счет искусственной стимуляции его активности.
Песок
Подойдет любой речной или карьерный, главное, чтобы в нем содержалось минимальное количество глинистых и илистых частиц, а максимальная крупность зерен не превышала 2 мм.
Портландцемент
Предпочтительно вяжущее марок М 400 и М 500, лучший цемент тот, который по всем критериям удовлетворяет требования ГОСТ 10178-85.
Газообразователь
В его качестве используется алюминиевая пудра марок ПАП-1 или ПАП-2.
Оборудование
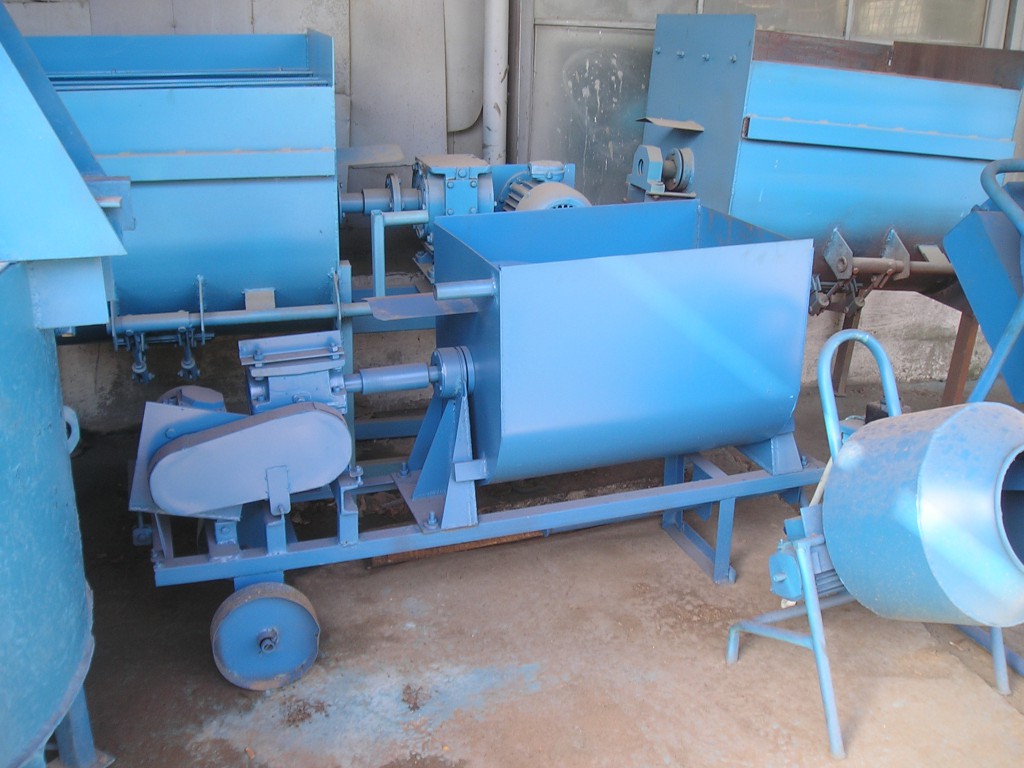
Технологическая линия изготовления газоблоков подразумевает наличие специального оборудования, которое приобретается в комплексе у производителя. Как правило, такой комплекс представляет собой автоматизированный мини–завод, который имеет довольно компактные размеры. Некоторые производители, бонусом к приобретаемому оборудованию предоставляют услуги временного технолога, который обучит вас, настроит производственную линию и подберет оптимальный состав газобетонной смеси.
Основные этапы
Конкретный алгоритм производства зависит от специфики приобретенного оборудования, но в общем он подразумевает 3-этапное производство газоблоков:
- Первым делом происходит точная дозировка компонентов и их перемешивание, в среднем этот цикл длится не более 10 минут.
- После чего, приготовленную бетонную массу, посредством специального оборудования, выгружают в заранее смазанные формы ровно до половины. Далее, в течении 4-часов смесь «растет» и заполняет весь объем форм, еще через 2 часа излишки смеси убираются.
- И третий, завершающий этап – распалубка изделий после 16-часовой выдержки и складирование их на поддоны для дальнейшего набора отпускной прочности, которая происходит в течение 2 или 3 суток, после чего изделия отправляются на склад. Марочной прочности газобетонные блоки достигают на 28 сутки.
Познавательное видео о производстве газоблока
Вывод
Чтобы получить на выходе хороший газобетон, нужно приобрести надежное оборудование и качественное сырье. Также обязательно следование всем правилам технологии, и только три эти составляющие в совокупности помогут не только окупить вложения, но и принести хорошую прибыль.
Удачной стройки!
oblokax.ru
производство и ключевые особенности строительства
Как производится газобетон? Каким образом технические характеристики газобетонных блоков соотносятся с практическими качествами этого строительного материала? Какие особенности материала нужно учитывать при строительстве? Давайте разбираться.
Один из старейших домов из автоклавного газобетона. Постройка — 1939 год, г. Рига.
История
Она начинается с получения чешским промышленником Гоффманом патента на технологию вспенивания цементных и гипсовых растворов. Патент был выдан в 1889 году; изобретение сводилось к добавке в раствор кислоты и реагирующих с ней солей.
Цель — получение материала с уступающей бетону плотностью и улучшенными теплоизоляционными характеристиками — была достигнута; однако метод был дорогим и крайне неудобным в применении.
Идея получила развитие четвертью века позже: американцы Дайер и Аусворт использовали в качестве газообразующей добавки порошки металлов — цинка и алюминия. Собственно, современная технология производства газобетона не слишком отличается от разработанной тогда. Именно 1914 год считается годом рождения материала.
Однако: первый автоклавный газобетон начал массово производиться в Швеции еще на 15 лет позже.В 1929 году компания Ytong наладила промышленный выпуск блоков из смеси извести и кремнезема, проходивших пропарку при повышенной температуре.Ytong по сей день считается одним из ведущих производителей материала.
Продукция компании завоевала популярность на российском рынке.
В 1934 году в Швеции был налажен выпуск блоков по несколько иной технологии: в качестве связующего использовалась не известь, а цемент.
В СССР производство автоклавных ячеистых бетонов стало массовым к середине 20 века. К нашему времени объем производства блоков достиг примерно 3,5 миллионов кубометров в год.
Описание
В чем причина популярности материала? Какие технические характеристики газобетона сделали его настолько востребованным?
Достоинства
- Теплоизоляционные качества газобетонных стен примерно соответствуют соответствующим характеристикам сухой древесины, в разы превосходя тяжелый бетон, силикатный и керамический кирпич. Схожий материал — пенобетон — тоже отстает по этому параметру.
Сравнение характеристик газо- и пенобетона.
- Механическая прочность превосходит пенобетон, хоть и заметно уступает более плотным материалам.
Уточним: в зависимости от марки по плотности различают конструкционные, конструкционно-теплоизоляционные и строго теплоизоляционные блоки.Прочность первых изделий позволяет использовать их для сооружения несущих стен и перекрытий; последние применяются в каркасно-монолитном строительстве в качестве заполнения стен.
- Благодаря все той же пористой структуре, производство оказывается довольно экономичным: на фиксированный объем строительного материала уходит меньше сырья.
- Структура с открытыми порами способствует естественной вентиляции стен. Эта особенность напоминает деревянные дома: часть воздухообмена с улицей и до трети парообмена осуществляется непосредственно через ограждающие конструкции.
- Простота обработки тоже напоминает о древесине: газобетон легко пилится ручной пилой, его можно сверлить и вбивать в его толщу гвозди.
Характеристики
Стоит сделать небольшое лирическое отступление и рассказать о методах классификации газобетона.
Основные характеристики, описывающие материал, выглядят так:
Характеристика | Описание |
Марка по плотности | Соответствует плотности в кг/м3 |
Класс прочности | Соответствует максимально допустимой нагрузке на сжатие в мегапаскалях (МПа) |
Морозостойкость | Количество циклов заморозки и оттаивания, которые блок может перенести без падения прочности более чем на 5% |
А теперь давайте посмотрим, какие значения эти и некоторые другие важные для строителя параметры принимают у газобетонных блоков наиболее востребованных типов.
Марка по плотности | D400 | D500 | D600 | |
Класс прочности | В 2 | В 2,5 | В 3,5 | В 3,5 |
Коэффициент теплопроводности, Вт/м*С | 0,096 | 0,12 | 0,14 | |
Морозостойкость, циклы | F75 | F75 | F100 | F100 |
Усадка при высыхании, мм/м | 0,3 и менее | |||
Паропроницаемость, мг/м*ч*Па | 0,24 | 0,28 | 0,24 | 0,23 |
Обратите внимание: марке по плотности D500 соответствуют два класса прочности.Разница между ними заключается в соотношении количества связующего и заполнителя при производстве блоков.
Что этот набор характеристик означает в практическом плане?
- Газобетон обеспечивает примерно втрое — впятеро более эффективное утепление по сравнению с керамическим кирпичом. Так, для того, чтобы обеспечить сопротивление теплопереносу в 2,5 м2*С/Вт, необходима газобетонная кладка толщиной 375 мм или кирпичная толщиной 1100 мм.
Сравнение теплоизолирующих качеств разных материалов.
- При упомянутом соотношении толщины нагрузка на фундамент, соответствующая квадратному метру кладки, в первом случае равна 205 килограммам, а во втором — 2000 кг.
- Минимальная ширина ленточного фундамента в первом случае равна 400 мм, во втором — 1200.
Производство
Из чего делают газобетон?
Сырье
В состав материала входит два основных компонента — наполнитель и связующее. Что может использоваться в этом качестве?
Наполнитель
- Тонкомолотый кварцевый песок.
Речной песок — наиболее востребованный наполнитель.
- Измельченные отходы горно-добывающей промышленности (скальные и осадочные породы).
- Зола, образующаяся при сжигании угля.
- Вторичные продукты обогащения руд.
- Металлургический шлак.
Связующее
- Известь.
- Портландцементы.
- Смешанное связующее (цемент + известь, известь + гипс и т.д.).
Технология
Технология изготовления газобетона в промышленных масштабах включает следующие основные операции:
Загрузка автоклавов.
Любопытно: выход на рабочий режим и подготовка к разгрузке автоклава постепенны и занимают 1,5 — 2 часа.
Водонепроницаемая упаковка обеспечивает стабильно низкую влажность.
Когда вместо пропарки используется сушка блоков? Прежде всего, при производстве газобетона своими руками, в домашних условиях либо при полукустарном изготовлении небольших партий на продажу.
Как уже упоминалось, цена необходимого оборудования в этом случае гораздо ниже; однако качество продукции несколько ухудшится:
- Усадка в процессе сушки достигнет 3-5 мм/метр.
- Прочность бетонных изделий на сжатие не превысит 10 — 12 кгс/см2. Впрочем, постепенный набор прочности при поглощении атмосферной влаги связующим будет продолжаться несколько лет.
Особенности строительства
Какие ограничения использование газобетонных блоков накладывает на строительство?
Фундамент
Основное требование к нему — максимальная жесткость, исключающая любую деформацию несущих стен. Несмотря на относительно высокую прочность, газобетон полностью лишен эластичности и при изгибающих нагрузках дает трещины.
Какие виды фундаментов применяются при газобетонном строительстве?
- На скальных и сухих супесчаных грунтах используются мелкозаглубленные ленточные основания.
- На пучинистых грунтах (глины, суглинки) оптимальное решение — свайный фундамент на буронабивных сваях с монолитным железобетонным ростверком.
- На болотистых почвах и других нестабильных грунтах заливается бетонный плитный фундамент. Он равномерно распределяет нагрузку по значительной площади и исключает любые неравномерные просадки стен.
На фото — плитный фундамент.
Стены
Ключевое требование к стенам — высокое сопротивление теплопереносу. Оно нормируется действующими СНиП и для центра страны равно 3 — 3,2 м2 * С/Вт.
Обеспечить соответствующие тепловые характеристики, согласно заверениям производителей, могут:
- Блоки марки по плотности D500 при толщине стен в 500 мм.
- Блоки D600 — при толщине стен в 600 мм.
Для несущих стен из газобетона действуют ограничения по этажности строения.
Количество этажей | Класс прочности блоков |
1 — 2 | В 2 |
3 | В 2,5 |
4 — 5 | В 3,5 |
Более 5 | Строительство несущих газобетонных стен не допускается. Строение должно быть каркасным. |
Кроме того: в сейсмоопасных районах армирующий железобетонный каркас предназначен для повышения сейсмостойкости конструкции здания.
В опалубке — армопояс, способствующий повышению сейсмостойкости строения.
Какие правила действуют для внутренних несущих стен и ненагруженных перегородок?
- Если на стену опирается одна плита перекрытия, она возводится из блоков прочностью В 2,5 с толщиной 240 мм или из блоков прочностью В 3,5 толщиной 200 мм.
- Стена, на которую опираются две плиты, должна быть толще — 300 и 400 мм соответственно.
- Ненагруженные межквартирные перегородки выполняются из блоков ненормируемой прочности толщиной не менее 240 мм. Инструкция связана с необходимостью обеспечить качественную звукоизоляцию.
- Межкомнатные перегородки имеют толщину 100 — 150 мм. Прочность, разумеется, не нормируется и в этом случае.
Перемычки
Они могут выполняться из монолитного железобетона (в этом случае перемычка заливается на месте; кладка стен используется как часть опалубки) или из специальных U-образных блоков. В последнем случае перемычка может быть сборной.
Как обеспечивается достаточная несущая способность конструкции?
Устройство сборной перемычки.
Кладочный раствор
На обычный цементно-песчаный раствор, приготовленный в пропорции 1:3, выкладывается только первый ряд блоков. Следующие ряды кладутся только и исключительно на специальный клей для ячеистых бетонов, обеспечивающий толщину шва не более 3 мм.
Клей для газобетона.
Почему обычный раствор не стоит использовать для кладки?
- Толстый шов — это мостик холода, ведущий в помещение с качественной теплоизоляцией. Как вырастут потери тепла — думается, можно не объяснять.
- Кроме того, блоки обладают точными размерами и идеальной геометрией. Тонкие швы позволяют использовать это преимущество, делая внешний вид кладки безупречным.
Наружная и внутренняя отделка
Главное требование к ней вполне стандартно: паропроницаемость стен должна увеличиваться изнутри наружу. Нарушение этого несложного правила приводит к отсыреванию стен, а в перспективе — и к их ускоренному разрушению.
Поскольку паропроницаемость газобетона исключительно высока, для стен из него обычно используются специальные штукатурные смеси с повышенной паро- и воздухопроницаемостью. Не менее популярное решение — вентфасады, обеспечивающие дополнительное утепление, и не препятствующие естественной вентиляции стен.
Утепленный вентфасад с облицовкой виниловым сайдингом.
Заключение
Надеемся, что предложенная информация будет полезной как начинающим строителям, так и потенциальным производителям недорогого и практичного строительного материала. Как всегда, видео в этой статье содержит дополнительные материалы. Успехов!
rusbetonplus.ru
Технология производства газобетона — АлтайСтройМаш
С изобретения технологии начал свою работу весь завод. А сейчас её легко приобретают все заказчики в комплекте со своим оборудованием. Для начала расскажем о преимуществах нашей технологии перед аналогами:
- быстро окупает производство – от пары недель до нескольких месяцев;
- производит газобетон высшего качества - по ГОСТ;
- даёт отличный результат с минимальными ресурсами - даже без ускорителей твердения и фиброволокна.
Технология как план действий
Для каждой линии описан свой порядок работы. Его соблюдение – одна их составляющих наивысшего качества. Соблюдать технологию просто, потому что она похожа на план:
- подготовить формы – монтаж и смазка;
- приготовить смеси из компонентов;
- заполнить формы смесью;
- нарезать застывший массив;
- прогреть блоки;
- разобрать массив и упаковать блоки – обернуть полиэтиленом.
При покупке линии вы получаете массу подробностей по каждому этапу и приступаете к практике - она важнее любых советов.
Об особенностях работы с каждой линией читайте в разделах:
- мини-линии;
- стационарное оборудование;
- конвейерное производство.
Линии отличаются по производительности и степени автоматизации, поэтому для каждой линии - своя технология. Мы также делаем линии на заказ, по индивидуальным пожеланиям клиента. Таких примеров на сайте нет, но знайте, что заказы на оборудование по вашей задумке мы тоже принимаем. В таких случаях технологию пишем специально под изготовленную линию.
Главное преимущество технологии «АлтайСтройМаш»
Это простота.
Технология считается совершенной, когда её можно объяснить даже ребёнку. И сейчас вы уже понимаете, что производство газобетона на оборудовании «АлтайСтройМаш» - действительно простой процесс.
Заказчики оборудования сами справляются и со сборкой линии, и с запуском производства. Кроме иллюстраций и видео-инструкций, у каждого клиента есть свой технолог. Он контролирует запуск, отвечает на все вопросы, а при необходимости – лично налаживает производство.
Прочитайте, какие минимальные требования нужно соблюсти для производства. Может у вас уже всё готово к производству?
Читать о Требованиях к производству
asm.ru
Технология производства газобетона г. Санкт-Петербург
Газобетонные изделия изготовляют тремя способами: литьевым, вибрационным и резательным. Наиболее распространена в настоящее время литьевая технология производства газобетона. Ячеистобетонную смесь из отдозированных компонентов перемешивают в газобетоносмесителях. Первоначально загружают песчаный или зольный шлам затем воду, вяжущее и суспензию газообразователя. При вибрационной технологии перемешивание осуществляют в процессе вибрации корпуса смесителя. По окончании перемешивания смесь в возможно более короткий срок загружают в формы. Температура смеси для приготовления газобетона должна быть не ниже 35 °С. При литьевой технологии производства газобетона изделия формуют из жидкотекучих смесей, содержащих до 50...60% воды от массы сухих компонентов. На стадии формования образуется поризованная масса: при литьевой технологии ее получают в неподвижных формах в течение 25...30 мин, при вибровспучивании - в вибрируемых формах в течение 3...6 мин.
Вспучивание смесей кремнеземистого компонента с известесодержащими вяжущими или цементом при введении алюминиевой пудры происходит в результате выделения водорода при взаимодействии ее с гидроксидом кальция. Вследствие незначительной растворимости водорода в воде раствор быстро пересыщается и частички алюминиевой пудры становятся центрами образования пузырьков. По мере газовыделения пузырьки увеличиваются в размере. На газообразующую способность смеси влияет ряд факторов. Основные из них - начальная вязкость, текучесть смеси, ее температура, скорость образования структуры с определенными механическими свойствами, дисперсность алюминиевой пудры и ее количество, химический состав среды.
Жидкотекучие смеси, формуемые по литьевой технологии производства газобетона, обладают недостаточной газоудерживающей способностью, что ухудшает структуру бетона. Вибрационное воздействие при изготовлении ячеистых смесей способствует увеличению поверхности взаимодействия частиц сырьевых компонентов, интенсифицирует процессы гидратации вяжущего и сокращает длительность газовыделения. Вибрационная технология производства газобетона позволяет использовать высоковязкие смеси с низким водотвердым отношением (0,35...0,4), использовать более грубодисперсные композиции, повысить плотность и прочность бетона, его трещиностойкость. Для оптимизации структуры газобетона важно привести в соответствие скорости процессов вспучивания и схватывания смеси. При преждевременном схватывании не достигается требуемая плотность, в бетоне образуются микротрещины.
Изготовление изделий с помощью литьевой технология производства газобетона осуществляют поточно-агрегатным методом. Формы устанавливают вдоль пути передвижения газобетоносмесителя, в результате создаются условия, предотвращающие их перемещение или сотрясение после заливки смесью до завершения ее вспучивания и схватывания. При вибрационной технологии изделия формуют стендовым или конвейерным способом.
На заводах ячеистого бетона применяют также резательную технологию производства газобетона, а именно формования изделий. Она предусматривает формование больших объемов-10... 12 м3 (высотой до 2 м). После приобретения бетоном структурной прочности массив разрезают в горизонтальном и вертикальном направлениях на прямоугольные элементы, направляемые на тепловлажностную обработку. При резательной технологии обеспечивается высокая точность размеров, прямолинейность граней, ровность поверхностей без масляных пятен; повышается заполнение автоклавов; снижается металлоемкость производства; резко уменьшается количество ручных операций. Из готовых элементов собирают на клею или растворе плоские или объемные конструкции, используя стяжную арматуру. Составные стеновые панели изготавливают размером на одну или две комнаты и высотой на этаж.
Технология производства газобетона, а именно технологический процесс получения пенобетона отличается тем, что поризация производится на стадии получения смеси, т. е. до формования изделий. Пену получают в специальном пеновзбивателе, куда заливают необходимое количество пенообразователя. Техническая пена возникает в результате значительного снижения поверхностного натяжения воды вследствие адсорбции мельчайших частиц поверхностно-активных веществ на поверхностях раздела твердой, жидкой и газообразной фаз. Пену перемешивают с предварительно-подготовленным раствором и направляют на формование.
Эффективным способом тепловлажностной обработки ячеистых бетонов является их автоклавирование при давлении 0,8...1,3 МПа и температуре 175...191°С в среде насыщенного или перегретого пара. Различают три стадии автоклавной обработки (запаривания). Эта технология производства газобетона включает в себя две стадии.
В первой стадии по мере повышения температуры в автоклаве изделия подвергают комплексу деструктивных физических процессов. В первый период запаривания одновременно с повышением температуры происходит дополнительное насыщение ячеистого бетона влагой за счет конденсации на его поверхности насыщенного пара. Первая стадия заканчивается при выравнивании температуры теплоносителя и изделий. При этом изделия нагревают как за счет теплопроводности, так и теплоты, выделяющейся при конденсации пара.
Вторая стадия автоклавной обработки - изобарическая выдержка. При достижении бетоном максимальной температуры происходит интенсивное взаимодействие вяжущего с кремнеземистым компонентом с образованием цементирующих новообразований. В результате возрастает прочность, которая через определенное время достигается примерно одинаковой величины по всему сечению. Продолжительность изобарической выдержки зависит от дисперсности, активности и соотношения компонентов, водотвердого отношения, температуры. Уменьшение влажности изделий можно достичь применением насыщенного пара в сочетании с перегретым. Перегретый пар с температурой до 400 °С подают в автоклав за 3...5 ч до окончания выдержки. Кроме того, уменьшения влажности в изделиях можно достичь путем вакуумирования после автоклавной обработки. В течение третьей стадии температура и давление снижаются.
В результате процесса интенсивного парообразования в бетоне развиваются значительные напряжения, которые могут вызывать образование трещин. Для предотвращения трещинообразования при коротких режимах охлаждения применяют ступенчатые режимы снижения давления. Продолжительность сброса давления на одну ступень устанавливают с учетом плотности и размеров изделий. Перед каждым последующим снижением давления производится выдержка, в течение которой уменьшается перепад давления по сечению изделия.
szs-group.ru