Содержание
Как делают цемент: технология производства цемента
Любое строительство или ремонтные работы невозможны без использования универсального строительного материала – цемента разных видов и марок. Мы настолько привыкли к этому продукту, что даже не задумываемся над проблемой, а как делают цемент. Можно ли его можно изготовить в домашних условиях и не переплачивать?
СодержаниеСвернуть
- Состав цемента
- Производство цемента на заводах
- Сухой способ
- Мокрый способ
- Комбинированные способы
- Как делают белый цемент
- Заключение
Сразу ответим на вопрос – можно ли сделать цемент своими руками? Имея необходимое оборудование и исходные материалы – получить цемент в домашних условиях можно. На данный момент времени в Российской Федерации большим спросом пользуются мини-заводы по производству цемента, мощностью порядка 120 000 тонн цемента в год. Производить же цемент для единичной стройки экономически невыгодно. Проще и дешевле купить этот необходимый строительный материал на заводе или в магазине.
Состав цемента
Цемент получается при длительном дроблении клинкера и гипса. Клинкер — продукт равномерного обжига до спекания однородной сырьевой смеси, состоящей из известняка и глины определённого состава, обеспечивающего преобладание силикатов кальция.
При измельчении клинкера вводят добавки: гипс СaSO4·2H2O для регулирования сроков схватывания, до 15 % активных минеральных добавок (пиритные огарки, колошниковую пыль, бокситы, пески) для улучшения некоторых свойств и снижения стоимости цемента.
Производство цемента на заводах
На данный момент времени производителями цемента используются три технологии производства связующего:
- Мокрый способ.
- Сухой способ.
- Комбинированный метод.
Стоит заметить что «сухую» технологию используют зарубежные производители цемента: Египет, Турция и Китай. «Мокрая» же технология традиционно используется отечественными цементными заводами.
циклы производства цемента
Сухой способ
Здесь нет необходимости использовать воду. Исходный материал (глину и известняк) дробят на специальном оборудовании. Сушат и перемалывают в мелкодисперсную муку, смешивают пневматическим способом и подают на обжиг.
Образовавшийся в результате обжига цементный клинкер измельчается до соответствующей степени фракции, фасуется в упаковку и отправляется на склад готовой продукции. Данный способ позволяет снизить затраты на производство, однако отличается «капризностью» к однородности исходных материалов и является экологически опасным вариантом.
Мокрый способ
Неоспоримые достоинства данного метода заключается в возможности точного подбора состава исходного сырья при высокой неоднородности исходных компонентов: порода, вид породы и пр. Исходный материал (шлам) представляет собой жидкую субстанцию, содержащую до сорока процентов влаги.
Перед тем как сделать цемент, состав шлама корректируется в специальных технологических бассейнах. После выдержки сырья в бассейне, производится отжиг в специальных вращающихся печах и последующее измельчение.
Мокрый способ требует большего расхода тепловой энергии расходуемой на высушивание исходного сырья. Это существенно увеличивает себестоимость производства цемента, однако качество конечной продукции не страдает от возможной неоднородности клинкера, как при мокром варианте.
Комбинированные способы
Данная технология опирается на мокрый вид получения связующего. Промежуточную субстанцию обезвоживают по специальной технологии. Клинкер гранулируют с добавлением воды, после чего производят отжиг и последующее измельчение до той или иной марки цемента.
В числе достоинств комбинированного способа производства цемента: высокий выход «годного», возможность использования отходов металлургической промышленности.
Как делают белый цемент
Технология производства белого цемента незначительно отличается от технологии производства обычного «серого» материала. Как и обычный «серый» материал, белый цемент выпускают сухим и мокрым способом. Основное отличие технологии – обжиг исходного сырья при высокой температуре и резкое охлаждение в воде.
Клинкер белого цемента характеризуется как «маложелезистый» и содержит в своем составе: минеральные добавки, известняк, гипс, соли и другие компоненты. В качестве исходного сырья для клинкера используются карбонатная и глинистая порода (известняк, каолиновая глина, отходы обогащения, кварцевый песок).
В Российской Федерации белый цемент производится только на одном предприятии – ООО «Холсим (Рус) СМ» (до 2012 года ОАО «Щуровский цемент»). Большинство белого цемента поставляется на рынок России из-за рубежа следующими компаниями: «Холсим» (Словакия), «Cimsa иAdana» (Турция), «AalborgWhite»(Дания) и «AalborgWhite» (Египет).
Основное достоинство белого цемента его уникальная характеристика – белоснежность, а основной недостаток в разы большая стоимость по сравнению с обычным «серым» материалом.
Заключение
Теперь вы знаете, как делают цемент на заводе в общем случае. Информацию как правильно делать цемент во всех подробностях, цифрах, схемах, таблицах и других тонкостях смотрите в специальной литературе.
Способы производства цемента — Завод сухих строительных смесей «ВосЦем»
Процесс производства цемента состоит из следующих основных технологических операций: добычи сырьевых материалов; приготовления сырьевой смеси, обжига сырьевой смеси и получения цементного клинкера; помола клинкера в тонкий порошок с небольшим количеством некоторых добавок.
В зависимости от способа подготовки сырья к обжигу различают мокрый, сухой и комбинированный способы производства цементного клинкера.
При мокром способе производства измельчение сырьевых материалов, их перемешивание, усреднение и корректирование сырьевой смеси осуществляется в присутствии определенного количества воды. А при сухом способе все перечисленные операции выполняются с сухими материалами. Мокрый способ приготовления сырьевой смеси применяют, когда физические свойства сырьевых компонентов (пластичной глины, известняка, мела с высокой влажностью и т. д.) не позволяют организовывать экономичный технологический процесс производства сырьевой смеси по сухому способу производства. При комбинированном способе сырьевую смесь приготовляют по мокрому способу, затем ее максимально обезвоживают (фильтруют) на специальных установках и в виде полусухой массы обжигают в печи. Каждый из перечисленных способов имеет свои достоинства и недостатки.
Способ производства цемента выбирают в зависимости от технологических и технико-экономических факторов: свойств сырья, его однородности и влажности, наличия достаточной топливной базы и др.
Мокрый способ производства цемента.
Сухой способ производства цемента.
Комбинированный способ производства цемента.
Производство цемента складывается в основном из следующий операций: добыча сырья; приготовления сырьевой смеси, состоящего из дробления и ее гомогенизации; обжига сырьевой смеси; помола обожженного продукта (клинкера) в тонкий порошок.
Существуют два основных способа производства – мокрый и сухой. При мокром способе производства сырьевую смесь измельчают и смешивают сырьевые материалы с водой. Получаемая сметанообразная жидкость – шлам – содержит 32-45% воды. По сухому способу сырьевые материалы предварительно высушивают, а затем измельчают и смешивают. Полученный тонкий порошок называют сырьевой мукой.
В зависимости от физических свойств исходных материалов и ряда других факторов при получении цемента по мокрому способу применяют разные схемы производства. Схемы эти отличаются одна от другой только способом приготовления сырьевой смеси. Приводим схему производства цемента по мокрому способу из твердого материала — известняка — и мягкого — глины.
При трехкомпонентной сырьевой смеси корректирующую добавку дробят, после чего она попадает в бункер, откуда вместе с известняком поступает в мельницу. Глину до болтушки пропускают через валковую дробилку. Сырьевые материалы дозируют перед мельницей специальными питателями.
Если при производстве по мокрому способу сырьевую смесь составляют из одних твердых материалов — известняка, мергелей и глинистых сланцев, то их дробят в дробилках без добавки воды и размалывают совместно в мельнице, куда добавляют воду. В том случае в схеме отсутствует болтушка. При изготовлении цемента из одних мягких материалов (мела, глины, мягких мергелей) сырье измельчают в болтушках, после чего размалывают в более коротких шаровых мельницах. В этом случае воду добавляют в первой стадии процесса и материалы дозируют перед ,поступлением в болтушки.
При сухом способе производства выбор схемы зависит от рода поставляемого топлива, физических свойств сырья, мощности завода и ряда других факторов. При использовании для обжига клинкера угля с большим содержанием летучих обжиг ведут во вращающихся печах, — если же применяют топливо с малым содержанием летучих — то в шахтных.
Так как при соприкосновении мелкого порошка, образующегося при помоле, с влагой материала образуется пластичная масса, которая налипает на внутреннюю поверхность агрегата и препятствует дальнейшему помолу, то дробленые сырьевые материалы с естественной влажностью размалывать нельзя. Поэтому после выхода из дробилки сырьевые материалы высушивают и затем направляют в мельницу, где перемалывают в тонкий порошок. Однородные по физическим свойствам материалы можно дробить и сушить в одних и тех же аппаратах. В случае применения гранулированного шлака его подсушивают без предварительного дробления. Помол и сушку сырьевой смеси целесообразно вести одновременно в одном аппарате-мельнице — в том случае, если влажность сырьевых материалов не превышает 8-12%, например, при использовании известняков и глинистых сланцев. Если в качестве сырья используется непластичный глинистый компонент, то при сухом способе производства обжиг ведут только во вращающихся печах. При пластичном глинистом компоненте можно вести обжиг, как во вращающихся печах, так и в шахтных печах. В последнем случае сырьевую смесь вначале увлажняют в смесительных шнеках водой до 8-10%-ной влажности. Затем массу подают в грануляторы, где она вместе с дополнительно подводимой водой превращается в гранулы с влажностью 12-14%. Эти гранулы и поступают в печь.
При обжиге клинкера на газообразном или жидком топливе схема производства упрощается, так как отпадает необходимость в приготовлении угольного порошка.
В ряде случаев может оказаться целесообразным комбинированный способ производства, при котором сырьевая смесь в виде шлама, полученного при обычном мокром способе производства, подвергается обезвоживанию и грануляции, а затем обжигается в печах, работающих по сухому способу.
Выбор сухого или мокрого способа производства зависит от многих причин. Как тот, так и другой способ имеют ряд преимуществ и недостатков. При мокром способе легче получить однородную (гомогенизированную) сырьевую смесь, обуславливающую высокие качества клинкера. Поэтому при значительных колебаниях в химическом составе известнякового и глинистого компонента он целесообразнее. Этот способ используется и тогда, когда сырьевые материалы имеют высокую влажность, мягкую структуру и легко диспергируются водой. Наличие в глине посторонних примесей, для удаления которых необходимо отмучивание, также предопределяет выбор мокрого способа. Размол сырья в присутствии воды облегчается, и на измельчение расходуется меньше энергии. Недостаток мокрого способа — больший расход топлива. Если используют сырьевые материалы с большой влажностью, то расход тепла, затрачиваемого на сушку и обжиг, при сухом способе будет мало отличаться от расхода тепла на обжиг шлама при мокром способе. Поэтому сухой способ производства целесообразнее при сырье со сравнительно небольшой влажностью и однородным составом. Он же практикуется в случае, если в сырьевую смесь вместо глины вводят гранулированный доменный шлак. Его же применяют при использовании натуральных мергелей и тощих сортов каменного угля ,с малым содержанием летучих, сжигаемых в шахтных печах.
При изготовлении сырьевой смеси по любому способу необходимо стремиться к наиболее тонкому помолу, теснейшему смешению сырьевых материалов и к возможно большей однородности сырьевой смеси. Все это гарантирует однородность выпускаемого продукта и является одним из необходимых условий нормальной эксплуатации завода. Резкие колебания химического со·става сырьевой смеси нарушают ход производственного процесса. Высокая тонкость помола и совершенное смешение необходимы для того, чтобы химическое взаимодействие между отдельными составными частями сырьевой смеси прошло до конца в возможно более короткий срок.
При выборе той или другой схемы производства особое внимание следует обращать на рентабельность работы предприятия и возможность снижения себестоимости продукции. Основными мероприятиями, ведущими к снижению себестоимости являются: интенсификация производственных процессов, повышение коэффициента использования оборудования, рост выпуска цемента, повышение его качества (марки), снижение расхода топлива и электроэнергии, механизация производственных процессов и всех вспомогательных работ, автоматизация управления производственными процессами и некоторые другие.
Мощность цементных заводов устанавливают в зависимости от сырьевой базы и потребности района в цементе. На новых заводах она равна обычно 1-2 млн. т цемента в год. Характерным показателем производительности труда на цементных заводах является выпуск цемента на одного рабочего в год, который в 1963 г. составил 915 т. Выработка на одного работающего была 7-62 т. На заводах, оснащенных высокопроизводительным оборудованием, выработка цемента достигла соответственно 2000 и 1600 т.
На цементных заводах, а также на заводах по производству других вяжущих материалов приходится перемещать от одного аппарата к другому большие массы кускового порошкообразного и жидкого материала. Для транспортирования их применяют ковшовые элеваторы, шнеки, ленточные, пластинчатые и скребковые транспортеры, транспортные желоба, насосы, краны с грейферами. Для транспортирования порошкообразных материалов широко используют пневмовантовые и камерные насосы, а также пневмотранспортные желоба.
Транспортирование шлама имеет ряд особенностей, так как он представляет собой сметанообразную текучую массу, содержащую 32-45% воды. Чтобы уменьшить расход топлива на обжиг, стремятся снизить влажность шлама, а чтобы улучшить его транспортабельность, необходимо увеличить содержание воды. По условиям транспортабельности шлам должен течь по желобу, имеющему уклон в 2-4 %. Чем пластичнее сырьевые материалы, тем больше приходится добавлять воды для получения шлама нужной текучести. Обычно шлам транспортируется центробежными насосами.
На заводы сырьевые материалы доставляют из карьера в виде кусков размерами до 1000-1200 мм. Иногда сырьевые отделения расположены непосредственно на карьерах, откуда шлам поступает на заводы. Так, на Балаклейском цементном заводе отделение болтушек размещено на карьере. Сырьевые материалы в виде мела и глины поступают в дробилки, а затем в болтушки. Полученный глиняно-меловой шлам нормальной влажности перекачивается по шламопроводам на завод.
При выпуске цемента обычных марок сырьевые материалы и клинкер размалываются до остатка на сите №008 порядка 8-10%. Для получения цемента более высоких марок материалы размалываю тоньше — до остатка на том же сите около 5% и даже меньше. Измельчать сырьевые материалы до получения тонкого порошка в одном аппарате невозможно. Поэтому сначала материал подвергают в дробилках двyx — тpex стадийному дроблению до величины кусков, не превышающей 8-20 мм, а затем измельчают в мельницах в гонкий порошок с размерами зерен не более 0,06-0,10 мм, глину поступающую из карьера в кусках размером до 500 ММ, измельчают в валковых дробилках до кусков не больше 100 мм, а затем отмучивают в болтушках до получения глиняного шлама с влажностью 60-70%. Этот шлам и подают в сырьевую мельницу.
Удельный расход сырья зависит от его химического состава и зольности топлива и составляет 1,5-2,4 т на 1 т клинкера. Расход электроэнергии на 1 т выпускаемого цемента составляет 80-100 квт/ч.
Процесс производства цемента
Для производства цемента необходимо добывать различные полезные ископаемые. Большую часть составляют известняк (содержащий минерал кальцит), глина и гипс. Геологическая служба США отмечает, что цементное сырье, особенно известняк, геологически широко распространено и (к счастью) в изобилии. Внутреннее производство цемента неуклонно растет: с 66,4 млн тонн в 2010 году до примерно 80,5 млн тонн портландцемента в 2014 году, согласно данным Геологической службы США за 2015 год о цементных и минеральных товарах. Общая стоимость реализации цемента составила около $8,9.миллиардов, большая часть которых была использована для производства бетона на сумму около 48 миллиардов долларов. В большинстве строительных проектов используется бетон в той или иной форме.
Существует более двадцати видов цемента, используемых для изготовления различных специальных бетонов, однако наиболее распространенным является портландцемент.
Производство цемента представляет собой сложный процесс, который начинается с добычи и последующего измельчения сырья, включающего известняк и глину, в мелкий порошок, называемый сырьевой мукой, который затем нагревается до температуры спекания до 1450 °C в цементной печи . В этом процессе химические связи сырья разрушаются, а затем они рекомбинируются в новые соединения. Результат называется клинкером, который представляет собой округлые узелки диаметром от 1 мм до 25 мм. Клинкер измельчают в мелкий порошок на цементной мельнице и смешивают с гипсом для получения цемента. Затем порошкообразный цемент смешивают с водой и заполнителями для получения бетона, который используется в строительстве.
Качество клинкера зависит от состава сырья, который необходимо тщательно контролировать для обеспечения качества цемента. Избыток свободной извести, например, приводит к нежелательным эффектам, таким как увеличение объема, увеличение времени схватывания или снижение прочности. Можно использовать несколько лабораторных и онлайн-систем для обеспечения контроля процесса на каждом этапе процесса производства цемента, включая образование клинкера.
Для обеспечения контроля процесса можно использовать несколько лабораторных и онлайн-систем
Лабораторные рентгенофлуоресцентные (XRF) системы используются лабораториями контроля качества цемента для определения основных и второстепенных оксидов в клинкере, цементе и сырье, таком как известняк, песок и бокситы. Прочтите Анализ клинкера и цемента с помощью последовательного спектрометра Thermo Scientific ARL OPTIM’X WDXRF, чтобы узнать, почему XRF является предпочтительным методом для элементного анализа в цементной промышленности. Комбинированные рентгенофлуоресцентные (XRF) и рентгеновские дифракционные (XRD) системы выполняют химический фазовый анализ для более полной характеристики образца. Фазовый анализ клинкера обеспечивает постоянное качество клинкера. Такое оборудование может быть оснащено несколькими монохроматорами XRF для анализа основных оксидов и системой компактной дифракции (XRD), которая позволяет измерять кварц в сырьевой муке, свободную известь (CaO) и фазы клинкера, а также кальцит (CaCO 9).0013 3 ) в цементе.
Прочтите Комбинированные приборы XRF/XRD могут обеспечить полный контроль качества клинкера и цемента , чтобы узнать больше о технологии, которая сочетает в себе преимущества как XRF, так и XRD.
Анализаторы поперечной ленты, основанные на технологии оперативного гамма-нейтронно-активационного анализа (PGNAA), устанавливаются непосредственно на конвейерную ленту для непрерывного измерения всего потока материала в режиме реального времени для устранения неполадок при контроле запасов перед смешиванием и управлении карьером, дозировании сырьевой смеси контроль и сортировка материалов. Читать PGNAA улучшает процесс и контроль качества в производстве цемента , чтобы узнать, что делает PGNAA особенно подходящим для анализа цемента.
Точное производство цемента также зависит от систем конвейерных весов, которые контролируют производительность и запасы или регулируют выгрузку продукции, а также от металлодетекторов для защиты оборудования и обеспечения бесперебойной работы. Блок-схема процесса производства цемента показывает, где в процессе каждый тип технологии имеет значение.
ПРИМЕЧАНИЕ:
Нужны конвейерные весы для обработки сыпучих материалов? Чтобы помочь вам решить, какая система конвейерных весов лучше всего подходит для вашей горнодобывающей деятельности, мы описали варианты в удобном для чтения руководстве по выбору системы конвейерных весов, чтобы вы могли решить, какая система конвейерных весов подходит именно вам. Нажмите на изображение, взгляните на диаграмму и посмотрите, поможет ли она вам принять решение.
Обновление: посетите Центр производства цемента на нашем веб-сайте, где вы найдете бесплатные ресурсы, которые помогут вам оптимизировать процесс производства цемента.
Цемент – Анализ – IEA
Ведущие авторы
Дэвид Ходжсон
Пол Хьюз
Авторы
Тиффани Васс
IEA (2022), Cement , IEA, Paris https://www.iea.org/reports/cement, Лицензия: CC BY 4.0
- Поделиться в Твиттере Твиттер
- Поделиться на Facebook Facebook
- Поделиться в LinkedIn LinkedIn
- Поделиться по электронной почте Электронная почта
- Выложить в печать Печать
Выбросы CO2
Сокращение выбросов CO 2 при одновременном производстве достаточного количества цемента для удовлетворения спроса будет сложной задачей. Ожидается возобновление роста спроса, поскольку замедление активности в Китае компенсируется расширением на других рынках. Кроме того, с 2015 года интенсивность выбросов при производстве увеличилась, в основном из-за более высокого глобального отношения клинкера к цементу, хотя в последнее время темпы роста замедляются.
Выбросы цемента продолжают расти — необходимы дополнительные инвестиции для разработки и внедрения новых технологий, чтобы соответствовать сценарию Net Zero
Интенсивность прямых выбросов при производстве цемента в сценарии Net Zero, 2015-2030 гг.
Открытьразвернуть
Ключевые стратегии по сокращению выбросов углерода при производстве цемента включают повышение энергоэффективности, переход на топливо с более низким содержанием углерода, повышение эффективности использования материалов (для снижения отношения клинкера к цементу и общего спроса) и продвижение инновационных способов производства с практически нулевым уровнем выбросов. Последние два вносят наибольший вклад в прямое сокращение выбросов в сценарии чистого нуля. Согласование с этим сценарием потребует разработки и развертывания технологии, которая в настоящее время недоступна. Поскольку это может занять некоторое время, соответствующие инвестиции в течение следующего десятилетия будут иметь решающее значение для обеспечения выбросов цемента в соответствии со сценарием Net Zero.
Энергия
Во всем мире теплоемкость и электроемкость производства цемента за последние десятилетия постепенно снижались по мере того, как печи сухого способа, включая ступенчатые подогреватели и предкальцинаторы (считающиеся самой современной технологией), заменяли печи мокрого способа, а также развернуто более эффективное шлифовальное оборудование. Согласно оценкам, глобальная теплоемкость клинкера оставалась относительно неизменной в течение последних пяти лет и составляла 3,4–3,5 ГДж/т.
Интенсивность тепловой энергии должна значительно снизиться, а использование биоэнергии должно увеличиться, чтобы цемент соответствовал сценарию Net Zero
Глобальная теплоемкость и расход топлива при производстве клинкера в сценарии Net Zero, 2015-2030 гг.
Открытьразвернуть
В сценарии Net Zero теплоемкость производства клинкера снижается чуть менее чем на 1% в год до среднемирового уровня около 3,3 ГДж/т, а электроемкость производства цемента в целом снижается до менее 95 кВтч/т (по сравнению с примерно 105 кВтч/т сегодня), без учета дополнительной энергии, необходимой для технологий сокращения выбросов, таких как улавливание и хранение углерода (CCS).
Ископаемые виды топлива по-прежнему обеспечивают большую часть энергии в цементном секторе, при этом биоэнергия и отходы на основе биомассы составляют лишь около 4% тепловой энергии, используемой в 2021 году. Доля биоэнергии и возобновляемых отходов значительно вырастет до 14% в 2030 году в сценарии Net Zero. Между тем, доля отходов на основе ископаемого топлива (таких как пластик, отработанное масло и промышленные отходы на основе ископаемого топлива) остается на уровне около 5% от использования топлива, примерно на том же уровне, что и в 2021 году.
Активность
В 2021 году было произведено около 4 300 млн тонн цемента, поскольку отрасль восстанавливается после небольшого спада в 2020 году. Китай внес наибольший вклад в мировое производство, на его долю приходится около 55% от общего объема, за ним следует Индия с 8%.
Производство цемента в последние годы оставалось относительно стабильным – в сценарии Net Zero эта тенденция сохраняется благодаря политике повышения эффективности использования материалов
Мировое производство цемента в сценарии Net Zero, 2010–2030 гг.
Открытьразвернуть
Производство в Китае, вероятно, сократится в долгосрочной перспективе, но ожидается его увеличение в Индии, других развивающихся странах Азии и Африке по мере развития инфраструктуры этих регионов. Прогнозируется, что это увеличение более чем компенсирует спад в Китае, что приведет к росту мирового производства цемента до 2030 года по базовой траектории.
Это отличается от сценария Net Zero, в котором мировое производство цемента остается относительно неизменным до 2030 года благодаря более эффективному использованию материалов и альтернативным строительным материалам. Действия по снижению спроса на цемент включают оптимизацию использования цемента в бетонных смесях, более эффективное использование бетона, минимизацию отходов в строительстве и максимальное увеличение расчетного срока службы зданий и инфраструктуры.
Развертывание технологий
Клинкер является основным ингредиентом цемента, и используемое количество прямо пропорционально выбросам CO 2 , образующимся при производстве цемента в результате как сжигания топлива, так и разложения известняка в процессе производства клинкера. По оценкам, с 2015 по 2020 год глобальное отношение клинкера к цементу увеличивалось в среднем на 1,6% в год, достигнув примерно 0,72 в 2020 году; это увеличение было основной причиной увеличения прямого CO 2 интенсивность производства цемента за период.
И наоборот, отношение клинкера к цементу падает на 1,0% в год до среднемирового значения 0,65 к 2030 году в сценарии Net Zero из-за более широкого использования смешанных цементов и заменителей клинкера. В долгосрочной перспективе более важными станут заменители клинкера, изготовленные из широкодоступных материалов, таких как кальцинированная глина в сочетании с известняком, поскольку декарбонизация других секторов снижает доступность промышленных побочных продуктов, которые в настоящее время используются в качестве альтернативы, таких как летучая зола из угольных электростанций и измельченный гранулированный доменный шлак сталелитейного сектора.
Соотношение клинкера и цемента в мире за последние годы увеличилось — для реализации сценария Net Zero
потребуется более широкое использование заменителей клинкера и инновационных технологий.
Развертывание CCS в сценарии Net Zero, 2015–2030 гг.
Открытьразвернуть
Другая технология, которая широко применяется в сценарии Net Zero, — это CCS. Улавливая около 0,1 млн тонн выбросов цемента сегодня, развертывание CCS должно резко увеличиться в течение десятилетия, а к 2030 году — почти 180 млн тонн.
Инновации
Для сокращения выбросов при производстве цемента необходимы технологические инновации. УХУ, вероятно, сыграет решающую роль в обезуглероживании цемента, поскольку позволит улавливать технологические выбросы. Альтернативы могут включать производство клинкера из некарбонатных источников, чтобы полностью избежать этих выбросов. Среди достижений прошлого года:
- Проект LEILAC-2, целью которого является использование технологии CCS прямого разделения на заводе по производству цемента в Ганновере, получил финансирование в размере 16 миллионов евро в рамках программы EU Horizon и в настоящее время находится на стадии реализации. планируется ввести в эксплуатацию в 2023 г. Другие проекты CCS продолжают развиваться, в том числе Norcem Brevik, использующий химическую абсорбцию, который планируется ввести в эксплуатацию к 2024 г.
- Достигнут прогресс в использовании электрических печей для производства клинкера, и в 2022 году компания VTT Decarbonate запустит первый крупный прототип.
- Компания Brimstone, базирующаяся в США, объявила о разработке нового процесса производства цемента с использованием извести из силиката кальция вместо известняка, что позволило бы избежать образования технологических выбросов в процессе кальцинирования и производить магний- на основе отходов, которые могут даже поглощать выбросы от сжигания топлива. Компания сообщает, что этот процесс будет дешевле, чем традиционные методы производства, и химически идентичен обычному портландцементному клинкеру. Процесс находится на относительно ранней стадии разработки — в лаборатории было произведено около 1 кг — но в 2022 году они объявили о планах построить первый в своем роде демонстрационный завод в Соединенных Штатах.
Чтобы реализовать сценарий Net Zero, технологии производства цемента с практически нулевым уровнем выбросов должны быть коммерциализированы до 2030 года. например, минимизация потребности в энергии для улавливания CO 2 .
Продвигаются низкоуглеродные инновации благодаря значительным недавним разработкам в области CCS, электрических печей и альтернативных процессов производства клинкера
Вспомогательная инфраструктура
Поскольку CSS, вероятно, сыграет важную роль в сокращении выбросов при производстве цемента, правительства должны разработать планы строительства инфраструктуры для транспортировки и хранения уловленного CO 2 , поскольку отсутствие вспомогательной инфраструктуры может значительно замедлить внедрение технологий и эффективность. Трубопроводы уже являются наиболее распространенным способом транспортировки CO 2 , и это, вероятно, будет продолжаться. Важным первым шагом для правительств будет получение общественной поддержки для строительства этих трубопроводов, а также CO 2 складских помещений, чтобы обеспечить безотлагательное развертывание в будущем. Поскольку прогнозируется снижение использования ископаемого топлива в сценарии Net Zero, правительства со значительной нефтегазовой инфраструктурой могут также захотеть изучить возможность перепрофилирования трубопроводов для транспортировки CO 2 .
Потребуются значительные инвестиции в расширение инфраструктуры CO2 для реализации сценария Net Zero
Политика
Многие штаты ввели политику, касающуюся промышленных выбросов в целом, что более подробно обсуждается на странице отслеживания МЭА для промышленности. Важные изменения для цемента включают следующее:
Выбросы цемента регулируются схемами ценообразования в ряде юрисдикций, включая Европейский Союз (вместе с Европейской ассоциацией свободной торговли), Канаду и Корею. Совсем недавно Китай, на долю которого в 2020 г. приходится более половины мирового производства цемента, объявил, что установит цену на выбросы цемента, возможно, уже в 2023 г.
Европейский союз находится в процессе разработки механизма корректировки углеродных границ для отраслей промышленности, включая цемент, который будет применять тарифы на товары с интенсивными выбросами из иностранных юрисдикций со слабой или отсутствующей политикой выбросов, чтобы ограничить утечку углерода и стимулировать более сильные меры по выбросам в зарубежных странах.
Франция и Япония недавно выпустили дорожные карты по обезуглероживанию цементного сектора, установив конкретные цели по обезуглероживанию и наметив конкретные шаги по обезуглероживанию своих цементных секторов. Французский план предусматривает сокращение выбросов на 35 % к 2030 году. В 2015 году Великобритания выпустила дорожную карту обезуглероживания цемента.
Многие страны начинают уделять больше внимания проблемам обезуглероживания цемента
Международное сотрудничество
Разработчики политики все больше координируют свою работу для решения проблем, связанных с декарбонизацией цементной и бетонной промышленности, включая угрозу утечки углерода и потребность в дополнительных инвестициях в разработку и внедрение экологически чистых технологий. Важным событием в 2021 году стала COP26, на которой Великобритания и Индия возглавили инициативу Министерства чистой энергетики по глубокой промышленной декарбонизации, направленную на поощрение государственных закупок стали и бетона с низким уровнем выбросов с целью создания рынка для этих товаров.
Расширение международного сотрудничества обнадеживает, но предстоит еще много работы
Стратегии частного сектора
Ряд организаций выпустили планы по достижению нулевого уровня выбросов к 2050 году. Наиболее примечательной является Глобальная ассоциация производителей цемента и бетона (GCCA), чьи компании-члены несут ответственность за 40% мирового производства цемента (80% за пределами Китая), установив цель достижения нулевого уровня выбросов к 2050 году. Европейская ассоциация производителей цемента выпустила собственную дорожную карту выбросов, к которой присоединились несколько национальных ассоциаций, включая Великобританию, Индию, Бразилию и Ассоциацию портландцемента США.
Существуют программы, помогающие повысить энергоэффективность производства цемента на пути к появлению прорывных технологий, в том числе Программа анализа пробелов и поддержки в области оценки предприятий (PEGASUS) и база данных отчетов GNR Глобальной ассоциации цемента и бетона для использования в бенчмаркинг. Другие программы нацелены на инновации, например, программы Innovandi GCCA.
Инициатива Climate Group ConcreteZero, запущенная 5 июля 2022 года с участием 17 фирм, объединяет ведущие компании для создания рынка бетона с почти нулевым уровнем выбросов, при этом участники обязуются закупать бетон с низким уровнем выбросов 30% к 2025 году и 50% к 2030 году. Коалиция первопроходцев — группа компаний, использующих свою покупательную способность для создания ранних рынков инновационных чистых технологий, — также планирует выступить с инициативой по обезуглероживанию бетона на COP27 в Египте.
Вместо того, чтобы реагировать на политику правительства, многие крупные производители цемента и отраслевые ассоциации берут на себя ответственность
Рекомендации для политиков
Как и в промышленности в целом, обезуглероживание цемента потребует множества мер, в том числе: На национальном уровне это может включать цены на углерод и коммерческие стандарты с низким уровнем выбросов, в то время как корректировки углеродных границ или международные отраслевые соглашения могут рассматриваться для ограничения утечки углерода.
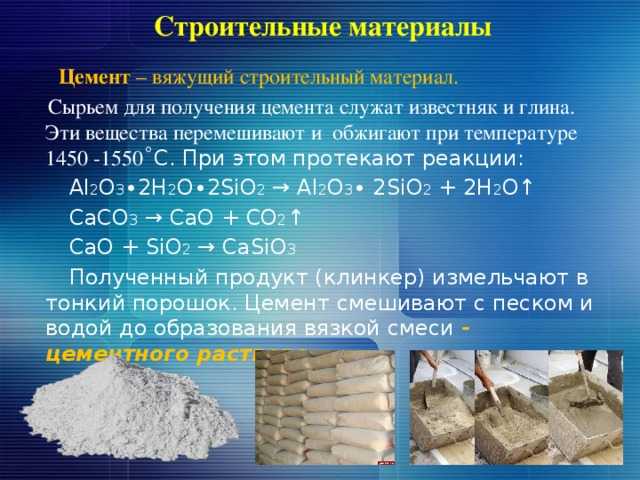
Продвижение комплексной амбициозной политики по сокращению выбросов в промышленности
Рекомендации для политиков и частного сектора
Более широкому внедрению альтернативных видов топлива можно способствовать, перенаправляя отходы со свалок на цементную промышленность и координируя поставки биомассы из устойчивых источников в разных секторах, чтобы обеспечить конкурентоспособный по стоимости доступ к производству цемента.
В долгосрочной перспективе широко доступные заменители клинкера и дополнительные заменители вяжущих материалов, такие как кальцинированная глина в сочетании с известняком, станут более важными, поскольку обезуглероживание производства электроэнергии и производства чугуна и стали снизит доступность этих промышленных побочные продукты. Правительствам следует пересматривать и пересматривать соответствующие строительные нормы, политику закупок и стандарты, чтобы гарантировать, что предписывающие требования не являются препятствием для максимального использования заменителей клинкера.
Расширение использования альтернативных видов топлива и заменителей клинкера
Создание спроса на цемент с почти нулевым уровнем выбросов будет иметь решающее значение. Цемент имеет особую потребность в политике, которая стимулирует использование клинкера с почти нулевым уровнем выбросов, в отличие от более широкой политики, которая могла бы вместо этого поощрять переход на другие материалы или использование цемента только с постепенным сокращением выбросов и, таким образом, не закладывая основу для производства с почти нулевым уровнем выбросов. в долгосрочной перспективе. Это важно, поскольку в мире с нулевыми выбросами потребуется значительное количество клинкера, поскольку цемент очень трудно перерабатывать, заменители клинкера могут составлять лишь около половины цемента для большинства применений, а альтернативные вяжущие, которые могут полностью заменить клинкер, либо на самых ранних стадиях разработки, либо могут использоваться только в определенных приложениях.
Кроме того, остаются значительные препятствия для разработки необходимых технологий, строительства производственных предприятий и создания цепочек поставок для производства клинкера, поэтому необходима адресная поддержка. Примерами могут служить политика государственных закупок, в которой конкретно указывается, что часть цемента должна поступать из производства клинкера с практически нулевым уровнем выбросов, или предварительные рыночные обязательства, гарантирующие закупку цемента с практически нулевым уровнем выбросов. Углеродные контракты на разницу также могут сыграть свою роль.
Внедрение стратегий по созданию спроса на цемент с почти нулевым уровнем выбросов для стимулирования дальнейшего развития и внедрения
Дополнительные ресурсы
Благодарности
- Роб ван дер Меер, CEMBUREAU, обозреватель
- Нур Амрани, FLSmidth, обозреватель
- Коди Финке, Brimstone, обозреватель
Связанные отрасли и технологии
Промышленность стрелка вправо |
Подача водорода стрелка вправо |
Улавливание и утилизация CO2 стрелка вправо |
Химикаты стрелка вправо |
Железо и сталь стрелка вправо |
Исследователи данных
Все обозреватели данныхcircle-arrow
набор данных карты
Ссылки
Геологическая служба США, статистика и информация по цементу, https://www.