Содержание
Испытание асфальтобетона и обследования автомобильных дорог
На начало 2021 года 80% автомобильных дорог с капитальным типом покрытия регионального, муниципального и федерального значения в Российской Федерации имеют покрытие из асфальтобетона. Асфальтобетонное покрытие является важнейшим элементом дорожной одежды автомобильной дороги, воспринимающие на себе все нагрузки от проезжающих автомобилей и изменения погодных условий. Асфальтобетон, не зависимо от внешних факторов, всегда должен обеспечивать требуемый и расчётный для данных условий уровень надежности и иметь характеристики не ниже нормативных значений, так как от этого зависит безопасность дорожного движения, а значит и жизни людей.
В процессе строительства автомобильных дорог и при сдаче их эксплуатирующим организациям необходимо контролировать качество асфальтобетонной смеси, поступающей на объект, перед её укладкой, а затем проводить лабораторные испытания асфальтобетона с целью оценки качества и установления соответствия характеристик проектной документации.
Специалисты компании МОССТРОЙЛАБ проводят все лабораторные испытания и экспертизы асфальтобетона и асфальтобетонных смесей необходимые для контроля как в процессе строительства, так и при эксплуатации автомобильных дорог. Ниже представлены ответы на часто встречающиеся вопросы от наших клиентов.
Какие компоненты входят в состав асфальтобетонной смеси? Ее основные типы.
Согласно ГОСТ 9128-2013, основными компонентами асфальтобетонных смесей являются: щебень, песок, минеральный порошок и битум.
В зависимости от вида минеральной составляющей (каменного материала) асфальтобетонные смеси разделяются на: щебеночные, гравийные и песчаные. От наибольшей крупности зерен выделяют: крупнозернистые, мелкозернистые, песчаные. От используемого битума и температуры при укладке смеси бывают горячие и холодные.
Как проводится контроль качества асфальтобетонной смеси при строительстве автомобильной дороги?
В первую очередь определяется температура асфальтобетонной смеси в месте отхода автомобиля от завода изготовителя и непосредственно перед укладкой.
Затем контроль качества асфальтобетонных смесей производится по пробам, отобранным при приготовлении на АБЗ, либо на объекте из кузовов автомобилей. Масса объединенной пробы зависит от размера зерен минерального материала.
После укладки и уплотнения асфальтобетонной смеси производится отбор образцов кернов из покрытий и проведения стандартных испытаний, таких как:
-определение средней плотности асфальтобетонной смеси;
-определение количества содержания битума в асфальтобетонной смеси;
-определение средней плотности минеральной части асфальтобетонной смеси;
-определение водонасыщения асфальтобетонной смеси;
— определение гранулометрического состава минеральной части;
-определение предела прочности при сжатии образцов асфальтобетона при температурах 50°С, 20°С, 0°С.
Какое количество проб необходимо отобрать из асфальтобетонного покрытия, и через какое время?
Для отбора проб из конструктивных слоев дорожных одежд с асфальтобетонным покрытием выбирают участок на расстоянии не менее 0,5 м от края или оси автомобильной дороги; размером не более 0,5х0,5 м. Отбор проб производят в виде вырубки прямоугольной формы или высверленных цилиндрических кернов. Цилиндрические керны высверливают на всю толщину покрытия (верхний и нижний слой вместе) с помощью буровой установки.
Вырубки или керны следует отбирать в слоях из горячих асфальтобетонных смесей не ранее, чем через 1-3 суток после их уплотнения, а из холодного – через 15-30 суток.
Размеры вырубки и количество высверливаемых кернов с одного места устанавливают по максимальному размеру зерен и исходя из требуемого для испытаний количества образцов.
Количество мест для отбора проб равно 3 пробы на каждые 7 000 м2 покрытия или на 10000 м2 при общей площади более 30 000м2 на автомобильных дорогах и 1 проба на каждые 2000 м2 при благоустройстве территории.
Как проводится контроль качества уплотнения асфальтобетонных покрытий, что такое коэффициент уплотнения асфальтобетона и чему он должен быть равен?
Для контроля качества уплотнения асфальтобетона применяются два способа: неразрушающий и разрушающий. В первом случае используется ультразвуковые и радиоизотопные приборы, во втором – метод отбора образцов при помощи буровой установки из покрытия с последующим испытанием её в лаборатории.
Коэффициент уплотнения асфальтобетона в покрытии – это отношение средней плотности образцов из покрытия (кернов или вырубки) к средней плотности образцов, переформованных из тех же кернов или вырубок.
Для определения коэффициент уплотнения асфальтобетона, как сказано выше, отбираются керны, по которым проводятся все необходимые испытания, в том числе определяется средняя плотность образца, затем они разрушаются и используются для изготовления переформованных образцов. Переформованные образцы — это образы, созданные при помощи форм и пресса из материала, взятого с покрытий автомобильных дорог и являющиеся показательными, так как были созданы идеальные условия для создания максимальной плотности. После создания переформованных образцов у него также определяется средняя плотность. Отношение средней плотности образца взятого из покрытия к средней плотности переформованного образца и называется коэффициентом уплотнения асфальтобетона.
Согласно СП 78.13330-2012 коэффициент уплотнения должен быть не менее:
-0,99 — для высокоплотного асфальтобетона из горячих смесей, плотного асфальтобетона из горячих смесей типов А и Б;
-0,98 — для плотного асфальтобетона из горячих смесей типов В, Г и Д, пористого и высокопористого асфальтобетона;
-0,96 — для асфальтобетона из холодных смесей.
Порядок работ при лабораторном контроле асфальтобетона и асфальтобетонных смесей
1- Испытание асфальтобетона и асфальтобетонных смесей
2.1- Испытание покрытия автомобильных дорог из асфальтобетонных смесей: выезд на объект строительства и отбор кернов.
2.2- Испытание асфальтобетонной смеси: Отбор проб из бункера асфальтобетонного завода или из кузова автосамосвала
3.1- Переформовывание отобранных образов и проведение базового комплекта испытаний (определение средней плотности переформованных образцов из асфальтобетона, определение водонасыщения асфальтобетона, определение коэффициента уплотнения асфальтобетонного покрытия, определения предела прочности на сжатии асфальтобетона)
3. 2- Проведение базового комплекта испытаний отобранных образцов (определение средней плотности асфальтобетона, определение водонасыщения асфальтобетона)
3.3- Формовка образцов и проведение базового комплекта испытаний смеси (определение средней плотности асфальтобетонной смеси, определение водонасыщения асфальтобетонной смеси, определения предела прочности на сжатии)
4.1- Выжигание смеси и определение гранулометрического состава и количества, вяжущего в покрытии из асфальтобетона и асфальтобетонной смеси (определение средней плотности минеральной части)
5- Проведение необходимых расчётов
6- Выдача протокола и доставка его Вам курьером
Как мы работаем со своими клиентами?
Все очень просто! Вы звоните или оставляете заявку на сайте строительной лаборатории МОССТРОЙЛАБ. Затем мы обговариваем с Вами детали и высылаем коммерческое предложение. После специалисты МОССТРОЙЛАБ выезжают к Вам на объект строительства и проводят все необходимые испытания или производят отбор проб для их дальнейшего исследования в строительной лаборатории.
После проведения всех необходимых обследований Вы получаете лабораторные заключения, оригиналы которых Вам доставляет наш курьер.
|
КОРПОРАЦИЯ
СТП 007-97 МЕТОД ИСПЫТАНИЯ АСФАЛЬТОБЕТОНА Москва 1998 СТП 007-97 СТАНДАРТ
МЕТОД ИСПЫТАНИЯ АСФАЛЬТОБЕТОНА КОРПОРАЦИЯ «ТРАНССТРОЙ» МОСКВА 1 РАЗРАБОТАН Государственным дорожным
ВНЕСЕН Научно-техническим центром Корпорации
2 ПРИНЯТ И ВВЕДЕН В ДЕЙСТВИЕ Корпорацией «Трансстрой»
3 СОГЛАСОВАН специализированной фирмой «Автодорстрой» 4 ВВЕДЕН ВПЕРВЫЕ
СТАНДАРТ ПРЕДПРИЯТИЯ
Утвержден и введен о действие распоряжением Корпорации
от
Дата введения 1998-01-01 Настоящий стандарт предприятия распространяется на
В настоящем стандарте использованы ссылки на следующие
ГОСТ
ГОСТ
ГОСТ
ГОСТ
ГОСТ
СНиП 3.06.03-85 Автомобильные дороги. ВСН 46-83
3.1 Испытания на сдвигоустойчивость проводят при
3.2 Приготовление асфальтобетонных смесей, отбор проб
Сущность метода испытаний заключается в определении
Рисунок 1 4.1 Аппаратура Испытательная машина с электромеханическим приводом
Индикатор перемещений по ГОСТ
Секундомер. Разрушающее устройство в виде двух одинаковых частей
Термометр стеклянный с ценой деления шкалы 1 °С по ГОСТ
Сосуд для термостатирования образцов вместимостью 7-8
Термостатирующее устройство, поддерживающее
4.2 Подготовка к испытанию Для испытания асфальтобетона на сдвигоустойчивость
Перед испытанием образцы выдерживают в течение 1 ч.
Образцы, перед тем как поместить их в разрушающее
4.3 Проведение испытания Максимальные разрушающие нагрузки и соответствующие
Образец 3, извлеченный из водяной бани, устанавливают
Рисунок 2 Рисунок 3 Для уменьшения потерь тепла и исключения склеиваимости
С целью повышения точности испытания рекомендуется
При установке верхнего разрушающего устройства на
Верхняя плита пресса должна находиться на расстоянии
4.4 Обработка результатов Для каждого образца, испытанного как на одноосное
где А — работа затраченная на деформирование образца
Р — разрушающее усилие, кН; l — предельная деформация, мм. Среднюю работу деформирования асфальтобетона при
Коэффициент внутреннего трения асфальтобетона tgφ
где Am. Ас — средняя работа
Лабораторный показатель сцепления Cл находят в зависимости от прочности асфальтобетона при
Лабораторный показатель сцепления зависит от скорости
Предусмотренные стандартом предприятия работы должны
Статистическая обработка результатов испытаний Среднее значение измеряемого показателя свойств
где X — среднее значение измеряемого показателя; хi — значение показателя замеренное при
n -количество
Оценку дисперсии измеряемого показателя в выборке
где S2(x)- оценка дисперсии измеряемого
Оценки дисперсий расчетных характеристик
где S2() — статистические оценки дисперсий
Прогнозирование сдвигоустойчивости асфальтобетона по Определяемые показатели свойств асфальтобетона и
В качестве основного критерия сдвигоустойчивости
где τдоп — допускаемое напряжение
τф — фактическое максимальное касательное
Сопротивление асфальтобетона пластичному сдвигу
где р — нормальное напряжение в слое от расчетной
tgφ
С — показатель когезионного сцепления асфальтобетона,
Чтобы определить параметры приведения лабораторного
Расчетный показатель сцепления С определяют исходя из
где Сл — лабораторный показатель
tл — среднее время нагружения образцов асфальтобетона в
t1— среднее время действия колесной нагрузки на
tn — максимальное непрерывное время эксплуатации
N — интенсивность движения расчетного автомобиля по
m -
U — энергия активации вязкопластичного разрушения
R — газовая постоянная, 0,008314 кДж/°К моль; Тn. — максимальная расчетная температура покрытия, °К; Тл,- абсолютная температура испытания
323,15 °К; Коэффициент пластичности m вычисляют по формуле
где Rc,R3— показатели прочности
Энергия активации вязкопластичного разрушения U в
где R20, R50 — показатели
Прогнозирование сдвигоустойчивости асфальтобетона по
Настоящее приложение рекомендуется для дополнительного
В качестве дополнительного критерия сдвигоустойчивости
где γn. γдоп — относительная деформация
Накопленную пластическую деформацию асфальтобетонного
где Ккол — коэффициент колейности
tp, — расчетный срок службы асфальтобетонного покрытия, сутки; N — интенсивность движения расчетного автомобиля по
t1, — среднее время действия колесной нагрузки на
Vл — скорость деформирования образцов при нагружении, 50
hл — высота образца, 70,4 мм; τф , — фактическое максимальное
р — нормальное напряжение в слое от расчетной
tgφ
Сл— лабораторный показатель когезионного
m — коэффициент пластичности асфальтобетона; Тмин, Тмах — соответственно
Р(Т) — частотное распределение (обеспеченность)
U — энергия активации вязкопластичного разрушения
R — газовая постоянная, 0,008314 кДж/°К моль; тл,- абсолютная температура
Ключевые слова: асфальтобетон, метод испытания, колееобразование,
|
|
HMA Performance Tests – Pavement Interactive
Эксплуатационные тесты используются для сопоставления лабораторной смеси с реальными полевыми характеристиками. В методах проектирования смеси Хвеема (стабилометр) и Маршалла (стабильность и текучесть) используется только один или два базовых теста производительности. Superpave предназначен для использования лучшего и более фундаментального теста производительности. Тем не менее, тестирование производительности — это единственная область Superpave, которую еще предстоит реализовать. Тесты производительности, обсуждаемые в этом разделе, используются различными исследователями и организациями в дополнение к существующим тестам Хвима и Маршалла, а также в качестве замены теста производительности Superpave, пока он не будет завершен. В этом разделе основное внимание уделяется лабораторным тестам; полевые испытания на месте обсуждаются в разделе «Оценка дорожного покрытия».
Как и в случае определения характеристик битумного вяжущего, задача испытаний характеристик HMA состоит в том, чтобы разработать физические тесты, которые могут удовлетворительно охарактеризовать ключевые параметры характеристик HMA и то, как эти параметры изменяются в течение срока службы дорожного покрытия. Этими ключевыми параметрами являются:
- Сопротивление деформации (колейности) . Ключевой параметр производительности, который может в значительной степени зависеть от конструкции смеси HMA. Поэтому большая часть усилий по тестированию производительности сосредоточена на прогнозировании сопротивления деформации.
- Усталостная долговечность . Ключевой параметр производительности, который больше зависит от конструкции конструкции и поддержки грунтового основания, чем от состава смеси. Те свойства HMA, которые могут влиять на растрескивание, в значительной степени проверяются в ходе физических испытаний битумного вяжущего Superpave.
Поэтому разработке тестов на усталостную долговечность обычно уделяется меньше внимания.
- Прочность на растяжение . Прочность на растяжение может быть связана с растрескиванием HMA, особенно при низких температурах. Те свойства HMA, которые могут влиять на растрескивание при низких температурах, в значительной степени проверяются в ходе физических испытаний битумного вяжущего Superpave. Поэтому разработке тестов на прочность на растяжение обычно уделяется меньше внимания.
- Жесткость . Соотношение напряжения и деформации HMA, характеризуемое модулем упругости или упругости, является важной характеристикой. Хотя модуль упругости различных типов смесей HMA довольно точно определен, тесты могут определить, как модуль упругости и упругости изменяется в зависимости от температуры. Кроме того, многие тесты на сопротивление деформации также могут определять модуль упругости или упругости.
- Восприимчивость к влаге . Определенные комбинации заполнителя и битумного вяжущего могут быть подвержены повреждению влагой.
Для оценки восприимчивости смеси HMA к влаге можно использовать несколько испытаний на сопротивление деформации и прочность на растяжение.
Постоянная деформация (колейность)
В настоящее время ведутся исследования того, какой тип испытаний может наиболее точно предсказать деформацию покрытия HMA (колейность). Используемые в настоящее время методы можно в целом разделить на следующие категории:
- Статические испытания на ползучесть . Приложите статическую нагрузку к образцу и измерьте, как он восстанавливается после снятия нагрузки. Хотя в этих испытаниях измеряется остаточная деформация образца, результаты испытаний, как правило, не коррелируют с фактическими измерениями колейности дорожного покрытия в процессе эксплуатации.
- Повторные нагрузочные испытания . Приложите к испытательному образцу повторяющуюся нагрузку с постоянной частотой в течение многих повторений (часто более 1000) и измерьте восстанавливаемую деформацию и остаточную деформацию образца.
Результаты испытаний коррелируют с измерениями колейности дорожного покрытия в процессе эксплуатации лучше, чем результаты статических испытаний на ползучесть.
- Испытания динамического модуля . Приложите повторяющуюся нагрузку с различной частотой к испытательному образцу в течение относительно короткого периода времени и измерьте восстанавливаемую деформацию образца и остаточную деформацию. Некоторые тесты динамического модуля также могут измерять задержку между пиковым приложенным напряжением и пиковой результирующей деформацией, что дает представление о вязких свойствах материала. Результаты испытаний достаточно хорошо коррелируют с измерениями колееобразования на дорожном покрытии в процессе эксплуатации, но испытание несколько сложное и сложное в проведении.
- Эмпирические испытания . Традиционные тесты дизайна смеси Hveem и Marshall. Результаты испытаний могут хорошо коррелировать с измерениями колейности дорожного покрытия в процессе эксплуатации, но эти испытания не измеряют какой-либо фундаментальный параметр материала.
- Имитационные испытания . Лабораторные следящие устройства. Результаты испытаний могут хорошо коррелировать с измерениями колейности дорожного покрытия в процессе эксплуатации, но эти испытания не измеряют какой-либо фундаментальный параметр материала.
Каждое испытание использовалось для успешного прогнозирования характеристик остаточной деформации HMA, однако каждое испытание имеет ограничения, связанные со сложностью оборудования, стоимостью, временем, изменчивостью и связью с основными параметрами материала.
Испытания на статическую ползучесть
Испытание на статическую ползучесть (см. рис. 1) проводят путем приложения статической нагрузки к образцу HMA и последующего измерения остаточной деформации образца после разгрузки (см. рис. 2). Эта наблюдаемая постоянная деформация затем коррелируется с потенциалом колейности. Большая остаточная деформация коррелирует с более высоким потенциалом колейности.
Испытания на ползучесть широко использовались в прошлом из-за их относительной простоты и доступности оборудования. Однако результаты испытаний на статическую ползучесть плохо коррелируют с фактической колейностью дорожного покрытия в процессе эксплуатации (Brown et al., 2001 9).0061 [1] ).
Рисунок 1. Испытание на статическую ползучесть без ограничений
Рисунок 2. Участок испытаний на статическую ползучесть без ограничений
Испытание на статическую ползучесть без ограничений
Наиболее популярное испытание на статическую ползучесть без ограничений (также известное как простое испытание на ползучесть или испытание на одноосную ползучесть) , недорог и относительно прост. Испытание состоит в приложении к образцу статического осевого напряжения в 100 кПа (14,5 фунтов на кв. дюйм) в течение 1 часа при температуре 40°C (104°F). Прикладываемое давление обычно не может превышать 206,9кПа (30 фунтов на кв. дюйм), а температура испытания обычно не может превышать 40°C (104°F), иначе образец может преждевременно выйти из строя (Brown et al., 2001 [1] ). Фактические покрытия обычно подвергаются воздействию давления в шинах до 828 кПа (120 фунтов на квадратный дюйм) и температуре выше 60 ° C (140 ° F). Таким образом, неограниченный тест не очень точно имитирует полевые условия (Brown et al., 2001 [1] ).
Испытание на статическую ползучесть в ограниченном пространстве
Испытание на статическую ползучесть в ограниченном пространстве (также известное как испытание на трехосную ползучесть) аналогично испытанию на статическую ползучесть в неограниченном пространстве по процедуре, но при этом используется ограничивающее давление около 138 кПа (20 фунтов на кв. дюйм), что позволяет провести испытание условия для более точного соответствия полевым условиям. Исследования показывают, что статическое испытание на ползучесть в ограниченном пространстве лучше прогнозирует эксплуатационные характеристики, чем статическое испытание на ползучесть в неограниченном пространстве (Roberts et al., 19).96 [2] ).
Испытание на диаметральную статическую ползучесть
В испытании на диаметральную статическую ползучесть используется типичный испытательный образец HMA, но его переворачивают на бок так, чтобы он был нагружен в диаметральной плоскости.
Некоторые стандартные испытания на статическую ползучесть:
- AASHTO TP 9: Определение ползучести и прочности горячей асфальтобетонной смеси (HMA) с использованием устройства для испытания на непрямое растяжение
Повторные испытания под нагрузкой
Повторные испытания под нагрузкой прикладывают повторяющуюся нагрузку фиксированной величины и продолжительности цикла к цилиндрическому испытательному образцу (см. рисунок 3). Модуль упругости образца можно рассчитать, используя его горизонтальную деформацию и предполагаемый коэффициент Пуассона. Накопленная остаточная деформация как функция количества циклов нагрузки регистрируется и может быть соотнесена с потенциалом колейности. Тесты можно проводить при разных температурах и разных нагрузках. Нагрузка варьируется в виде коротких импульсов, за которыми следует период отдыха. Испытания с повторной нагрузкой по своей концепции аналогичны испытанию на трехосный модуль упругости для незамкнутых грунтов и заполнителей.
Повторные испытания под нагрузкой лучше коррелируют с фактической колейностью дорожного покрытия в процессе эксплуатации, чем статические испытания на ползучесть (Brown et al., 2001 [1] ).
Рис. 3. Схема испытаний с повторной нагрузкой
Примечание: этот пример упрощен и показывает только 6 повторений нагрузки, обычно во время испытания следуют повторения кондиционирования, за которыми следует серия повторений нагрузки при определенном уровне нагрузки и, возможно, при различных температурах. |
Чаще всего результаты повторных испытаний под нагрузкой представляются с использованием кривой кумулятивной осевой деформации, подобной показанной на рис. 4. Число текучести (FN) – это число циклов нагрузки, при котором начинается третичная текучесть. Третичный поток можно отличить от вторичного потока по заметному отклонению от линейной зависимости между кумулятивной деформацией и количеством циклов во вторичной зоне. Предполагается, что при третичном потоке объем образца остается постоянным. Число потока (FN) можно соотнести с потенциалом колейности.
Рис. 4. График результатов испытаний с повторной нагрузкой
Повторное испытание с неограниченной нагрузкой
Испытание с повторной нагрузкой без ограничений сравнительно проще в проведении, чем испытание с неограниченной нагрузкой, поскольку оно не требует ограничивающего давления или сопутствующего оборудования. Однако, как и при испытании на ползучесть без ограничений, допустимые испытательные нагрузки значительно меньше, чем при испытании покрытия на месте.
Испытание повторяющейся нагрузкой в ограниченном пространстве
Испытание повторяющейся нагрузкой в ограниченном пространстве является более сложным, чем испытание в неограниченном пространстве, из-за требуемого всестороннего давления, но, как и испытание на ползучесть в ограниченном пространстве, ограничивающее давление позволяет прикладывать испытательные нагрузки, которые более точно отражают испытанные нагрузки. по бездорожью.
Испытание на повторяющуюся нагрузку в диаметральном направлении
Испытание на повторяющуюся нагрузку в диаметральном направлении использует типичный испытательный образец HMA, но поворачивает его на бок так, чтобы он нагружался в своей диаметральной плоскости. Диаметральное испытание имеет два критических недостатка, которые препятствуют его способности определять характеристики остаточной деформации (Браун и др., 2001 [1] ):
- Напряженное состояние неоднородно и сильно зависит от формы образца. При высокой температуре или нагрузке остаточная деформация вызывает изменения формы образца, которые существенно влияют как на напряженное состояние, так и на результаты испытаний.
- Во время испытания единственным относительно однородным состоянием напряжения является растяжение по вертикальному диаметру образца. Все остальные напряженные состояния явно неоднородны.
Испытание на сдвиг повторяющейся нагрузкой
Прибор для испытания на сдвиг Superpave (SST), разработанный для Superpave, может выполнять испытание на сдвиг повторяющейся нагрузкой. Это испытание, известное как испытание на повторный сдвиг на постоянной высоте (RSCH), применяет повторяющееся гаверсинусное напряжение (обратный косинус, смещенный на половину его амплитуды — непрерывная гаверсинусная волна будет выглядеть как синусоида, отрицательный пик которой находится на нуле) напряжения сдвига к аксиально нагруженный образец и регистрирует осевую и сдвиговую деформацию, а также осевую и сдвиговую нагрузку. Было показано, что данные RSCH имеют высокую изменчивость (Brown et al., 2001 9).0061 [1] ).
Некоторые стандартные повторяющиеся испытания под нагрузкой:
- AASHTO TP 7: Определение остаточной деформации и характеристик усталостного растрескивания горячей асфальтобетонной смеси (HMA) с использованием прибора для испытания на сдвиг Superpave (SST) – Процедура F
- AASHTO TP 31: Определение модуля упругости битумных смесей методом непрямого растяжения
- ASTM D 4123: Испытание на непрямое растяжение модуля упругости битумных смесей
Тесты динамического модуля
Испытания на динамический модуль прикладывают к испытательному образцу повторяющуюся осевую циклическую нагрузку фиксированной величины и продолжительности цикла (см. рисунок 1). Образцы для испытаний можно испытывать при различных температурах и трех различных частотах нагрузки (обычно 1, 4 и 16 Гц). Прикладываемая нагрузка варьируется и обычно применяется в виде гаверсинусоидальной волны (обратный косинус, смещенный на половину его амплитуды — непрерывная гаверсинусоидальная волна будет выглядеть как синусоидальная волна, отрицательный пик которой находится на нуле). На рис. 5 представлена схема типичного теста динамического модуля.
Рис. 5. Схема испытаний на динамический модуль
Испытания на динамический модуль отличаются от испытаний с повторной нагрузкой своими циклами и частотой нагружения. В то время как при повторных испытаниях с нагрузкой одна и та же нагрузка применяется несколько тысяч раз при одной и той же частоте, при испытаниях динамического модуля нагрузка применяется в диапазоне частот (обычно 1, 4 и 16 Гц) в течение 30–45 секунд (Brown et al., 2001 [ 1] ). Испытание на динамический модуль выполнить сложнее, чем испытание на повторную нагрузку, поскольку требуется гораздо более точная система измерения деформации.
Испытание на динамический модуль измеряет зависимость между напряжением и деформацией образца при непрерывной синусоидальной нагрузке. Для линейных (соотношение напряжение-деформация не зависит от приложенного напряжения нагрузки) вязкоупругих материалов это соотношение определяется комплексным числом, называемым «комплексным модулем» (E*) (Witczak et al., 2002 [3] ), как показано в уравнении ниже:
где: | Э* | = | комплексный модуль |
= | динамический модуль | ||
φ | = | – угол, на который ε o отстает от σ o . Для чисто эластичного материала φ = 0, а комплексный модуль (E*) равен абсолютному значению или динамическому модулю. Для чистых вязких материалов φ = 90°. | |
я | = | мнимое число |
Абсолютное значение комплексного модуля |E*| определяется как динамический модуль и рассчитывается следующим образом (Witczak et al. , 2002 [3] ):
где: | = | динамический модуль | |
с о | = | пиковая амплитуда напряжения (приложенная нагрузка / площадь поперечного сечения образца) | |
е или | = | пиковая амплитуда восстанавливаемой осевой деформации = D L/L. Либо измеряется непосредственно с помощью тензодатчиков, либо рассчитывается на основе перемещений, измеренных датчиками линейного перемещения (LVDT). | |
л | = | расчетная длина, на которой измеряется деформация образца | |
ДЛ | = | восстанавливаемая часть изменения длины образца из-за приложенной нагрузки |
Испытание на динамический модуль может быть полезным, поскольку оно позволяет измерять также фазовый угол образца (φ), который представляет собой отставание между пиковым напряжением и пиковой восстанавливаемой деформацией. Комплексный модуль E* на самом деле является суммой двух компонентов: (1) компонента накопления или модуля упругости и (2) модуля потерь или модуля вязкости. Это показатель вязких свойств оцениваемого материала.
Испытание на неограниченный динамический модуль
Испытание на неограниченный динамический модуль проводится путем приложения осевой гаверсинусной нагрузки к цилиндрическому испытательному образцу. Хотя рекомендуемый размер образца для испытаний составляет 100 мм (4 дюйма) в диаметре и 200 мм (8 дюймов) в высоту, можно с успехом использовать образцы меньшей высоты (Brown et al., 2001 [1] ). . Неограниченные тесты динамического модуля не позволяют определить фазовый угол (φ).
Испытание на ограниченный динамический модуль
Испытание на динамический модуль в ограниченном пространстве в основном представляет собой испытание в неограниченном пространстве с приложенным боковым ограничивающим давлением. Тесты ограниченного динамического модуля позволяют определить фазовый угол (φ). Хотя рекомендуемый размер образца для испытания динамического модуля составляет 100 мм (4 дюйма) в диаметре и 200 мм (8 дюймов) в высоту, можно с успехом использовать образцы меньшей высоты (Brown et al., 2001 [1]). ). На рисунках 6 и 7 показан прототип Superpave Simple Performance Test (SPT). SPT проведет тест производительности метода расчета смеси Superpave.
Рис. 6. Прототип Superpave SPT | Рис. 7. SPT представляет собой ограниченный тест динамического модуля |
Испытание динамического модуля сдвига
Испытание динамического модуля сдвига известно как испытание частотной развертки на постоянной высоте (FSCH). Уравнения динамического модуля сдвига такие же, как рассмотренные выше, хотя традиционно термин E* заменяется на G* для обозначения динамического модуля сдвига и s o и e o заменены на t 0 и g 0 для обозначения напряжения сдвига и осевой деформации соответственно. Динамический модуль сдвига можно определить с помощью двух разных испытательных устройств:
- Устройство для испытания на сдвиг Superpave (SST) . Испытание SST FSCH представляет собой испытание на постоянную нагрузку (в отличие от испытания на постоянную нагрузку). Образцы для испытаний имеют диаметр 150 мм (6 дюймов) и высоту 50 мм (2 дюйма) (см. рис. 8). Для проведения испытания образец HMA по существу приклеивается к двум пластинам (см. рис. 9).через 11), а затем вставлен в SST. Горизонтальная деформация применяется в диапазоне частот (от 10 до 0,1 Гц) с использованием схемы нагружения гаверсинуса, в то время как высота образца поддерживается постоянной за счет сжатия или вытягивания его по вертикали по мере необходимости. SST производит постоянную деформацию около 100 микрострейн (Witczak et al., 2002 [3] ). SST довольно дорог и требует высококвалифицированного оператора для работы, что делает его непрактичным для использования в полевых условиях и требует дальнейшей разработки.
- Тестер сдвига в полевых условиях (FST) . Тест FST FSCH представляет собой постоянный стресс-тест (в отличие от теста на постоянную нагрузку). FST является производным от SST и должен быть менее дорогим и простым в использовании. Например, вместо того, чтобы сжимать или тянуть образец для поддержания постоянной высоты, как в SST, FST поддерживает постоянную высоту образца с помощью жестких прокладок, прикрепленных к концам образца. Далее ФСТ сдвигает образец в диаметральной плоскости.
Рис. 8. Прибор для испытания на сдвиг Superpave (SST) | Рисунок 9. Загрузочная камера |
Рисунок 10. Подготовленный образец | Рисунок 11. Подготовленный образец (слева) и образец после испытания. |
Стандартные тесты комплексного модуля:
- Неограниченный динамический модуль . ASTM D 3497: Динамический модуль асфальтобетонных смесей
- Динамический модуль сдвига .
AASHTO TP 7: Определение остаточной деформации и характеристик усталостного растрескивания горячей асфальтобетонной смеси (HMA) с использованием устройства для испытания на простой сдвиг (SST), процедура E – испытание частотным качанием на постоянной высоте.
Эмпирические тесты
Стабилометр и когезиометр Hveem, а также тесты стабильности и текучести по Маршаллу — это эмпирические тесты, используемые для количественной оценки способности HMA к остаточной деформации. Они обсуждаются в разделах дизайна миксов.
Симуляционные испытания – Лабораторные устройства для отслеживания колес
Лабораторные устройства для отслеживания колес (см. Видео 1) измеряют колейность путем повторного проката небольшого нагруженного колеса по подготовленному образцу HMA. Затем колейность на испытательном образце сопоставляется с фактической колейностью дорожного покрытия в процессе эксплуатации. Лабораторные устройства отслеживания колес также можно использовать для прогнозирования восприимчивости к влаге и снятия изоляции путем сравнения результатов испытаний в сухом и влажном состоянии. Некоторые из этих устройств являются относительно новыми, а некоторые используются более 15 лет, например, Центральная лаборатория мостов и дорог (LCPC). ) колесный трекер, также известный как французский тестер колейности (FRT). Кули и др. (2000 [4] ) провел обзор испытателей колес под нагрузкой в США и обнаружил:
- Результаты, полученные с помощью устройств слежения за колесами, достаточно хорошо коррелируют с фактическими эксплуатационными характеристиками, если принять во внимание рабочую нагрузку и условия окружающей среды в этом месте.
- Устройства слежения за колесами могут разумно различать классы эффективности вяжущего.
- Устройства слежения за колесами, если они должным образом соотнесены с дорожным движением и условиями окружающей среды на конкретном участке, потенциально могут позволить пользовательскому агентству выбирать критерии прохождения/непрохождения или «годен/не годен». Способность устройств слежения за колесами адекватно прогнозировать величину колеи для конкретного дорожного покрытия в настоящее время не определена.
- Устройство с возможностью проведения испытаний на отслеживание колес как в воздухе, так и в подводном состоянии предложит пользовательскому агентству больше возможностей для оценки их материалов.
Другими словами, устройства слежения за колесами потенциально могут измерять колею и другие измерения, но отдельный пользователь должен тщательно устанавливать лабораторные условия (например, нагрузку, количество проходов колеса, температуру), которые обеспечивают стабильную и точную корреляцию с полевыми характеристиками.
Видео 1: Анализатор асфальтового покрытия – Устройство слежения за колесами
Усталостная долговечность
Усталостные свойства HMA важны, поскольку одним из основных видов разрушения покрытия HMA является растрескивание, связанное с усталостью, называемое усталостным растрескиванием. Таким образом, точный прогноз усталостных свойств HMA будет полезен для прогнозирования общего срока службы покрытия.
Испытание на изгиб
Одним из типичных способов оценки усталостных свойств HMA на месте является испытание на изгиб (см. рисунки 12 и 13). Испытание на изгиб определяет усталостную долговечность небольшого образца балки HMA (380 мм в длину, 50 мм в толщину и 63 мм в ширину), подвергая его многократному изгибу до разрушения (см. рис. 14). Образец балки выпиливается либо из лабораторного, либо из уплотненного в полевых условиях HMA. Результаты обычно наносятся на график, чтобы показать циклы до отказа в зависимости от приложенного напряжения или деформации.
Рисунок 12 (слева). Устройство для испытания на изгиб | Рисунок 13 (справа). Устройство для испытания на изгиб |
Рис. 14. Схема испытания на изгиб (щелкните изображение, чтобы его оживить)
Стандартное испытание на усталость:
Прочность на растяжение
Прочность на растяжение HMA важна, поскольку она является хорошим индикатором потенциала образования трещин. Высокая деформация растяжения при разрушении указывает на то, что конкретный HMA может выдерживать более высокие деформации до разрушения, а это означает, что он с большей вероятностью будет сопротивляться растрескиванию, чем HMA с низкой деформацией растяжения при разрушении. Кроме того, измерение предела прочности при растяжении до и после кондиционирования воды может дать некоторое представление о восприимчивости к влаге. Если предел прочности при растяжении в воде относительно высок по сравнению с пределом прочности при растяжении в сухом состоянии, то HMA можно считать достаточно влагостойким. Для измерения прочности на растяжение HMA обычно используются два теста:
- Испытание на непрямое растяжение
- Испытание на термическое растрескивание
Испытание на непрямое растяжение
При испытании на непрямое растяжение используется то же испытательное устройство, что и при испытании на диаметральную повторяющуюся нагрузку, и применяется постоянная скорость вертикальной деформации до разрушения. Это очень похоже на испытание на разрывное напряжение, используемое для PCC.
Стандартное испытание на непрямое растяжение является частью следующего испытания:
- AASHTO TP 9: Определение податливости и прочности горячей асфальтобетонной смеси (HMA) с использованием устройства для испытания на непрямое растяжение
Испытание на термическое растрескивание
Испытание на термическое растрескивание определяет предел прочности при растяжении и температуру при разрушении образца HMA путем измерения растягивающей нагрузки в образце, который охлаждается с постоянной скоростью, удерживая его от усадки. Испытание прекращают, когда образец выходит из строя из-за растрескивания.
Стандартное испытание на термическое растрескивание:
- AASHTO TP 10: Метод определения предела прочности при растяжении образца при термическом напряжении
Испытания на жесткость
Испытания на жесткость используются для определения модуля упругости или упругости HMA. Хотя эти значения достаточно точно определены для многих различных типов смесей, эти тесты по-прежнему используются для проверки значений, определения значений в ходе судебно-медицинской экспертизы или определения значений для новых смесей или при различных температурах. Для определения модуля упругости также можно использовать множество повторных испытаний под нагрузкой.
Особо следует отметить, что температура сильно влияет на жесткость HMA. В таблице 1 показаны некоторые типичные значения модуля упругости HMA при различных температурах. На рисунке 15 показано, что модуль упругости HMA изменяется примерно в 100 раз при изменении температуры на 56 °C (100 °F) для «типичных» смесей HMA с плотным гранулометрическим составом. Это может повлиять на параметры производительности HMA, такие как колейность и толкание. Это одна из причин, по которой система классификации вяжущего Superpave PG учитывает ожидаемые рабочие температуры при выборе битумного вяжущего.
Таблица 1: Типичные значения модуля упругости для материалов покрытия HMA
Материал | Модуль упругости (MR) | |
МПа | фунтов на квадратный дюйм | |
HMA при 32°F (0 °C) | 14 000 | 2 000 000 |
HMA при 70°F (21°C) | 3 500 | 500 000 |
HMA при 120°F (49°C) | 150 | 20 000 |
Рисунок 15. Общая зависимость жесткости от температуры для асфальтобетона с плотным гранулометрическим составом
Влагочувствительность
Для оценки влагочувствительности HMA использовались многочисленные тесты; однако ни один тест на сегодняшний день не получил широкого признания (Roberts et al. , 1996 [2] ). Фактически практически любой тест производительности, который можно провести на влажном или погруженном в воду образце, можно использовать для оценки влияния влаги на HMA путем сравнения результатов испытаний влажного и сухого образца. Superpave рекомендует модифицированный тест Лоттмана как наиболее подходящий в настоящее время тест, поэтому этот тест будет описан ниже.
Модифицированный тест Лоттмана в основном сравнивает результаты непрямого теста прочности на растяжение сухого образца и образца, подвергнутого воздействию воды/замораживания/оттаивания. Образец воды подвергается вакуумному насыщению, дополнительному циклу замораживания, за которым следует замораживание и цикл теплой воды перед испытанием на косвенную прочность на растяжение (AASHTO, 2000a [5] ). Результаты испытаний представлены в виде коэффициента прочности на растяжение:
где: | ТСР | = | коэффициент прочности на растяжение |
С 1 | = | средняя прочность на растяжение сухого образца | |
С 2 | = | средняя прочность образца на растяжение в кондиционном состоянии |
Как правило, для этого метода рекомендуется минимальный TSR 0,70, который следует применять к образцам, полученным в полевых условиях , а не к образцам, полученным в лаборатории (Roberts et al. , 1996). Для лабораторных образцов , изготовленных в соответствии с AASHTO TP 4 (Метод подготовки и определения плотности образцов горячей асфальтобетонной смеси (HMA) с помощью гираторного уплотнителя Superpave), AASHTO MP 2 (Спецификация расчета объемной смеси Superpave) указывает минимальный TSR 0,80.
В дополнение к модифицированному тесту Лоттмана некоторые государственные учреждения используют гамбургское устройство слежения за колесами (HWTD) для проверки на чувствительность к влаге, поскольку тест можно проводить в ванне с теплой водой.
Стандартный модифицированный тест Лоттмана:
- AASHTO T 283: Устойчивость уплотненной битумной смеси к повреждениям, вызванным влагой
Сноски (↵ возвращается к тексту)
- Brown, E.R.; Кандал, П.С. и Чжан, Дж. (2001). Эксплуатационные испытания горячей асфальтобетонной смеси . Отчет NCAT № 01-05. Национальный центр асфальтовых технологий.
Оберн, А.Л. http://www.eng.auburn.edu/center/ncat/reports/rep01-05.pdf.↵
- Roberts, FL; Кандхал, PS; Браун, ER; Ли, Д.Ю. и Кеннеди, Т.В. (1996). Асфальтовые материалы для горячих смесей, проектирование смесей и строительство . Образовательный фонд Национальной ассоциации асфальтобетонных покрытий. Lanham, MD.↵
- Witczak, M.W.; Калуш, К .; Пелинен, Т .; Эль-Басюни, М. и фон Квинтус, Х. (2002). Отчет NCHRP 465, Простой тест производительности смеси Superpave . Совет по исследованиям в области транспорта, Национальный исследовательский совет. Вашингтон, округ Колумбия http://gulliver.trb.org/publications/nchrp/nchrp_rpt_465.pdf.↵
- Cooley, L.A.; Кандхал, PS; Бьюкенен, MS; Фи, Ф. и Эппс, А. (2000). Испытатели нагруженных колес в США: состояние практики . Отчет NCAT № 2000-4. Национальный центр асфальтовых технологий. Оберн, А.Л. http://www.eng.auburn.edu/center/ncat/reports/rep00-04.pdf. По состоянию на декабрь 2004 г. ↵
- Американская ассоциация государственных служащих автомобильных дорог и транспорта (AASHTO).
(2000а). Стандартные технические условия на транспортные материалы и методы отбора проб и испытаний, двадцатое издание: Часть I – Технические условия . Американская ассоциация государственных служащих автомобильных дорог и транспорта. Вашингтон, округ Колумбия↵
Удельный вес насыпного материала – Интерактивное дорожное покрытие
Обзор
Испытание на удельный вес насыпного веса используется для определения удельного веса уплотненного образца HMA путем определения отношения его веса к весу равного объема воды.
Испытание на объемный удельный вес измеряет массу образца HMA в трех различных условиях (рис. 1):
- Сухой (без воды в образце).
- Насыщенная поверхность сухая (SSD, вода заполняет воздушные пустоты HMA).
- Погруженный в воду (подводный).
Используя эти три веса и их отношения, можно рассчитать кажущийся удельный вес образца, объемный удельный вес и объемный удельный вес SSD, а также абсорбцию.
Объемный удельный вес HMA необходим для определения отношения веса к объему и для расчета различных величин, связанных с объемом, таких как воздушные пустоты и пустоты в минеральном заполнителе (VMA).
Стандартный тест удельного веса в массе:
- AASHTO T 166: Объемный удельный вес уплотненных битумных смесей с использованием насыщенных образцов с сухой поверхностью
- ASTM D 2726: Объемный удельный вес и плотность невпитывающих уплотненных битумных смесей
Рис. 1. Образцы HMA в трех условиях.
Общие сведения
Удельный вес — это мера плотности материала (масса на единицу объема) по сравнению с плотностью воды при температуре 73,4°F (23°C). Следовательно, по определению вода при температуре 73,4°F (23°C) имеет удельный вес 1,9.0003
Удельный вес насыпного материала Использование
Состав смеси Superpave представляет собой объемный процесс; ключевые свойства выражаются в единицах объема. Однако прямые измерения объема затруднены, поэтому обычно производятся измерения веса, а затем они преобразуются в объем на основе удельного веса материала. Объемный удельный вес используется в большинстве ключевых расчетов состава смеси, включая воздушные пустоты, VMA и, косвенно, VFA. Правильное и точное определение удельного веса сыпучих материалов жизненно важно для правильного состава смеси. Неправильное значение объемного удельного веса приведет к неправильному расчету воздушных пустот, VMA, VFA и, в конечном итоге, к неправильному составу смеси.
Методы определения объемного удельного веса
Несмотря на то, что в разделе «Описание испытаний» описывается стандартный метод вытеснения воды насыщенной поверхностно-сухой водой (SSD) AASHTO T 166, существует ряд других доступных методов. В каждом из них используется несколько иной способ определения объема образца, что может привести к различным значениям объемного удельного веса.
Методы вытеснения воды
Эти методы, основанные на принципе Архимеда, рассчитывают объем образца путем взвешивания образца (1) в водяной бане и (2) вне водяной бани. Затем разницу в весе можно использовать для расчета веса вытесненной воды, который можно преобразовать в объем, используя удельный вес воды.
Насыщенная поверхность, сухая (SSD)
Наиболее распространенный метод (и метод, описанный в разделе «Описание испытаний») рассчитывает объем образца путем вычитания массы образца в воде (рис. 2) из массы образца SSD. . SSD определяется как состояние образца, когда внутренние воздушные пустоты заполнены водой, а поверхность (включая воздушные пустоты, связанные с поверхностью) сухая. Это условие SSD позволяет учитывать внутренние воздушные пустоты как часть объема образца и достигается путем замачивания образца в водяной бане в течение 4 минут, затем его извлечения и быстрого промокания насухо влажным полотенцем.
Рисунок 2. Метод SSD.
Одна из критических проблем с этим методом заключается в том, что если воздушные пустоты в образце большие и, таким образом, потенциально взаимосвязаны (для HMA с плотной градацией это происходит при 8-10 процентах воздушных пустот), вода быстро стекает из них при удалении образца. из водяной бани, что приводит к ошибочно заниженному измерению объема пробы HMA и, таким образом, к ошибочно высокому объемному удельному весу.
Парафин
Этот метод определяет объем аналогично методу вытеснения водой, но для заполнения внутренних воздушных пустот образца вместо воды используется расплавленный парафин (рис. 3). Следовательно, после затвердевания воска нет возможности его вытекания, и теоретически можно рассчитать более точный объем. На практике парафин трудно правильно нанести, а результаты испытаний несколько противоречивы.
Рисунок 3. Образец HMA, покрытый парафином.
Парафильм
В этом методе образец оборачивается тонкой парафиновой пленкой (рис. 4), а затем взвешивается в воде и вне ее. Поскольку образец полностью завернут, когда он погружен в воду, в него не может попасть вода, и теоретически возможно более точное измерение объема. Однако на практике нанесение парафиновой пленки довольно сложно, а результаты испытаний противоречивы.
Рисунок 4: Покрытие образца HMA парафильмом.
CoreLok
В этом методе подсчитывается объем образца, как и в парафиновом методе, но используется вакуумная камера (рис. 5), чтобы завернуть образец в высококачественный пластиковый пакет (рис. 6), а не покрывать его парафиновой пленкой (видео 1). Этот метод показал себя многообещающим как по точности, так и по прецизионности.
Рисунок 5: Вакуумная камера CoreLok с образцом внутри. | Рис. 6: Образец CoreLok, запаянный в пластиковый пакет. |
Видео 1: Устройство CoreLok.
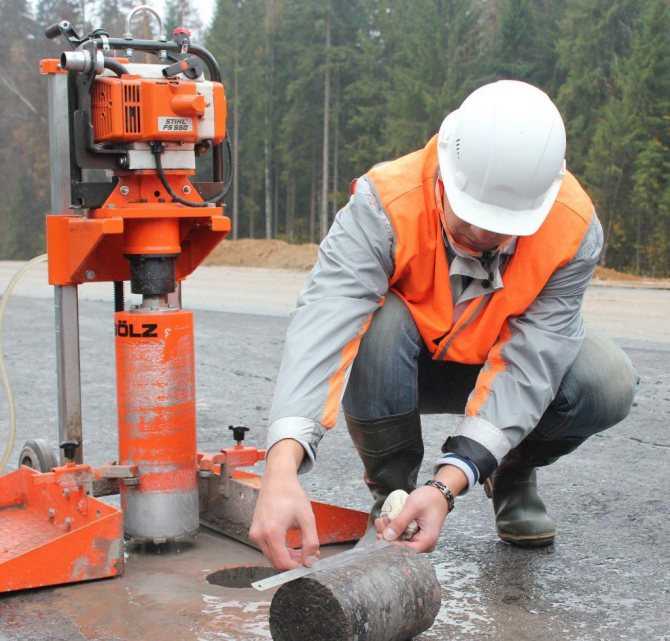
Размерный
Этот метод, самый простой, вычисляет объем на основе измерений высоты и диаметра/ширины. Хотя он позволяет избежать проблем, связанных с состоянием SSD, он часто бывает неточным, поскольку предполагает идеально гладкую поверхность, тем самым игнорируя неровности поверхности (например, шероховатую текстуру поверхности типичного образца).
Гамма-излучение
Метод гамма-излучения основан на свойствах рассеяния и поглощения гамма-лучей веществом. Когда источник гамма-излучения с первичной энергией в комптоновском диапазоне помещается рядом с материалом, а для подсчета гамма-излучения используется детектор гамма-излучения, селективный по энергии, можно подсчитывать исключительно рассеянные и нерассеянные гамма-лучи с энергиями в комптоновском диапазоне. При правильной калибровке количество гамма-излучения напрямую преобразуется в плотность или объемный удельный вес материала (Troxler, 2001 9).0061 [1] ). На рис. 7 показано устройство Troxler.
Рис. 7. Считыватель Troxler модели 3660 CoreReader.
Описание теста
Следующее описание представляет собой краткий обзор теста. Это не полная процедура, и ее не следует использовать для выполнения теста. Полную процедуру можно найти в:
- AASHTO T 166: Объемный удельный вес уплотненных асфальтовых смесей с использованием насыщенных образцов с сухой поверхностью
- ASTM D 2726: Объемный удельный вес и плотность невпитывающих уплотненных битумных смесей
Другие стандартные тесты, доступные для определения объемного удельного веса, которые не описаны в этом разделе:
- AASHTO T 275: Объемный удельный вес уплотненных битумных смесей с использованием образцов, покрытых парафином
- AASHTO TP 69: Объемный удельный вес и плотность уплотненных асфальтовых смесей с использованием метода автоматического вакуумного уплотнения
Резюме
Уплотненный образец HMA (обычно уплотненный лабораторный образец SGC или керн HMA, полученный в полевых условиях) взвешивают в сухом состоянии, насыщают сухую поверхность (SSD) и погружают в воду (рис. 1). Эти веса используются для расчета удельного веса и процента воды, поглощенной образцом.
Приблизительное время тестирования
Проведение каждого теста занимает примерно 7 минут, не считая времени на подготовку. При тестировании нескольких образцов время тестирования одного образца может быть сокращено. Может потребоваться значительное время на подготовку, если загрязнение должно быть удалено со дна образца.
Основная процедура
- Высушите образец до постоянной массы и охладите до комнатной температуры.
Лабораторные образцы обычно сухие в начале теста; однако полевые образцы обычно будут влажными.
- Запишите сухую массу (рис. 8).
Рисунок 8: Взвешивание образца.
- Погрузите образец в воду с температурой 77°F (25°C) на 4 минуты и запишите погруженную массу. Это можно сделать с помощью наполненного водой контейнера на верхней части весов или с помощью корзины, подвешенной в воде под весами (рис.
2).
- Быстро промокните образец влажным полотенцем и запишите сухую массу поверхности.
Любая вода, вытекающая из образца во время взвешивания, считается частью насыщенного образца. Если эту воду не взвешивать, может возникнуть значительная ошибка.
Результаты
Измеренные параметры
Объемный удельный вес (Gmb) и процент поглощенной воды по объему.
Спецификации
Спецификации удельного веса навалом отсутствуют, но они используются для расчета других заданных параметров, таких как воздушные пустоты, VMA и VFA.
Типичные значения
Типичные значения удельного веса насыпного материала находятся в диапазоне от 2,200 до 2,500 в зависимости от удельного веса заполнителя, содержания битумного вяжущего и степени уплотнения.
Поглощение обычно не должно превышать 2 процентов. Если образец поглощает более 2 процентов воды по объему, этот метод не подходит. В этом случае используйте AASHTO T 275, Объемный удельный вес уплотненных битумных смесей с использованием образцов, покрытых парафином, или AASHTO TP 69, Объемный удельный вес и плотность уплотненных асфальтовых смесей с использованием метода автоматического вакуумного уплотнения.