Содержание
Соломобетонные блоки: изготовление своими руками
Сейчас очень многие стараются строить дома из экологически чистых материалов. Говоря о таковых, в голову сразу приходят мысли о древе. Но не стоит забывать и о той же самой глине или даже соломе. Многие могут сказать, что солома — это прошлый век и это не надежно. Но благодаря современным технологиям такой материал приобрел не только качество, но и прочность. И если нет желания тратиться на него, то соломобетонные блоки своими руками тоже можно сделать.
Соломобетонные блоки являются дешевым, прочным и экологически чистым материалом.
Но для начала нужно разобраться, что это такое. Такой материал выпускается в виде прямоугольных блоков. Блок имеет стандартную ширину (45 см) и высоту (35 см), а вот длина может варьироваться от 90 до 112 см. Весить такой блок может от 16 до 30 кг. Чтобы такой материал сохранял свою форму, блоки обвязывают (а некоторые производители и прошивают) полипропиленовыми шнурами. В сельскохозяйственных сферах такие блоки собираются в единое целое при помощи проволок или натуральных волокон. Но эти крепления подходят для хранения соломы, а никак не для построек. Ведь сама проволока железная, а железо имеет свойство ржаветь. А волокно по прошествии времени теряет свою прочность из-за гниения. Солома тоже бывает нескольких видов, поэтому для постройки лучше применять ржаную или рисовую. Они обладают оптимальными свойствами. Если останавливать свой выбор на первом варианте, то лучше, если она будет озимая. Такая солома имеет более плотную структуру.
Предъявляемые требования
Есть определенные требования к соломенным блокам, а именно:
Схема бескаркасной стены из соломенных блоков.
- Сухость. Влага, скопленная внутри, будет провоцировать гниение. Кстати, именно сухие блоки такие легкие, и если они имеют значительный вес, то есть вероятность, что солома была не доброкачественно просушена. Если ощущается запах гнили или пальцами чувствуется влажность, то такой материал некачественный.
- Качество соломы. Стебли должны быть гибкими и крепкими. Если при сгибании он не ломается, то это качественный блок.
В обратном же случае такой материал быстро рассыпется.
- Качественный пресс. Если соблюдалась правильная технология спрессовывания блока, то он не должен терять своей формы. Для этого можно попробовать просунуть под шнур пальцы, если больше 3х пальцев не помещается, то это качественный пресс.
- Одинаковые размеры.Вся партия должна быть идентичной. Если блоки разнятся по размерам между собой, то лучше отказаться от применения данного материала и найти другого производителя.
Вернуться к оглавлению
Как создать соломеннобетонный блок своими руками?
Когда вы делаете что-либо своими руками, всегда возникает огромный плюс — экономия средств. К тому же при собственноручном изготовлении всегда можно быть уверенным в качестве применяемых материалов. То же самое относится и к блокам из соломы и бетона. Цемент компонируется соломой не только по причине придания прочности. Он помогает органическим веществам соломы преобразоваться в сахар, который легко растворяется водой. Но такие преобразования мешают соломенному блоку отвердеть. Для того чтобы устранить такой отрицательный эффект, применяются физические и химические способы.
Схема перекрытия из соломобетонных блоков.
Первое, что используют — окисление. Для этого блоки выносят на открытые солнечные лучи, под воздействием которых происходит окисление веществ, и они начинают впитываться в стенки древесных клеток. В то же время часть других веществ при взаимодействии с бактериями преобразуется в кристаллы и в дальнейшем образует нерастворимые формы. Но для того чтоб все это произошло на надлежащем уровне, необходимо очень много времени. Второй способ — вымачивание водой. Если блок оставить под дождем на длительное время, то практически все водорастворимые вещества выйдут из него. С этой целью используют и специальные емкости. Но опять-таки для того чтобы обработать всю партию соломенных блоков, требуется значительное время. Самым распространенным на сегодняшний день способом является обработка растворами хлористого кальция или жидкого стекла. В среднем их надо около 9 кг на метр кубический. Эта технология популярна по ряду причин:
- Благодаря жидкому компоненту стекла и хлористому кальцию изделие быстро затвердевает. Но если сравнивать прочность готовых блоков обеих марок, вторые этот показатель имеют намного выше, чем первые. Если применять кальций, то следует знать, что лучше всего использовать выдержанную солому. А вот для применения жидкого стекла порода соломы особой роли не играет.
- Используя такие добавки, при условии, что средняя температура окружающей среды будет 20 градусов тепла, такие блоки уже через 24 четыре часа можно складывать, а через 7 дней применять и для строительства.
Есть рекомендуемый расход для изготовления блоков, ориентированный на объемный вес компонентов (кг/м3):
Сравнение теплопроводности соломобетонных блоков с другими материалами.
- цемента — 1700;
- гашеной извести — 600;
- песка — 1550;
- соломы — 80-105.
А вот на расход воды влияют несколько моментов:
- какая необходима вязкость замеса и заполнителя;
- марка бетонного раствора;
- показатель исходной влажности соломы.
Такие пропорции позволят создать блок с показателем прочности М-10. Некоторые строители заменяют бетон на глину. Изначально они рубят солому на куски (0,5 м), после чего замачивают ее в глиняном растворе. И опять-таки полученный материал прессуется.
Сам блок формируется при помощи киповальной машины.
Ее можно соорудить и самому, а можно обратиться к профессиональным киповальщикам или взять пресс в аренду. Если же все-таки решено обращаться за помощью, следует знать, что качество соломы во многом зависит и от того, как ее собирали и хранили. Немаловажным моментом является и ее помол, ведь если ее трубчатая структура будет нарушена, то такой материал потеряет все свои свойства. Сейчас солому чаще продают в виде рулонов, что слегка удлинит процесс. Ведь такие рулоны придется заново раскатать и перекиповать. А это может привести к нарушению изначальной структуры соломы. Но каждый сам выбирает, как ему удобно. Нельзя забывать и том, что готовые соломенные блоки пропитываются специальными химическими составами, которые значительно влияют на их прочностные характеристики.
Вернуться к оглавлению
Технические особенности соломенных блоков
Стройка загородного дома — это всегда какие-то проблемы, связанные то с работой, то с финансами. Но вот применение соломенных блоков помогает решить некоторые негативные моменты в строительстве.
http://ostroymaterialah.ru/www.youtube.com/watch?v=sksGhD4ckr0
А все потому, что они имеют ряд своих особенностей.
- Низкая себестоимость. В основном солома — это отходы в сельском хозяйстве. Поэтому приобрести ее не составит особого труда. Единственное, на что придется потратиться, это на перевоз такого материала. Но если на ферме, где приобреталась солома, есть киповальная машина, то везти ее никуда не надо будет.
- Низкая теплопроводность. Постройки из такого материала не требуют дополнительного утепления. Нет проблем и с отделочными работами, ведь, имея шероховатую поверхность, материал отлично «цепляет» к себе любые покрытия.
- Но также следует отметить, что все-таки соломеннобетонные блоки имеют определенную «мягкость», поэтому на них не кладутся плиты перекрытий, так как это приводит к деформации.
Это является основной причиной, почему такой материал применяется для построек только каркасных домов.
Вернуться к оглавлению
Положительные моменты домов из соломенных блоков
Материал имеет ряд положительных моментов, из-за которых его и применяют в современном строительстве:
Благодаря небольшому весу и крупным габаритам соломенных блоков, строительство идет очень быстро.
- Дешевизна и доступность материала. В наших широтах проблем с соломой не возникает, в любом колхозе ее достаточно.
- Экологически чистый материал. Если солома росла на полях не в радиационной зоне и не обрабатывалась вредными веществами, то такая постройка будет иметь благоприятное воздействие и на здоровье жильцов, и на саму окружающую среду.
- Легкий вес. Благодаря этой характеристике строительство идет очень быстро. В зависимости от проекта, одноэтажную постройку можно завершить в сроки от двух недель до двух месяцев.
- Форма материала.
Так как во время производства такого блока используется пресс, то даже несмотря на наличие соломы внутри, грызуны не обустроят себе дом в стенах. Еще одним из моментов, которые влияют на популярность такого строительства, является экономия строительных ресурсов и энергии, а также сама эксплуатация такой постройки. Несмотря на несерьезность материала, соломенные блоки имеют долгие сроки службы. Но это при условии, что они прошли правильную техническую обработку. Только в таком случае есть гарантия, что они не рассыпятся, не деформируются и не поддадутся гниению.
http://ostroymaterialah.ru/www.youtube.com/watch?v=zjlONLhIeyg
Даже если такой материал сравнить с древесиной, то второй вариант уступает по параметру насыщения помещения кислородом. Трубчатая структура соломенных волокон отлично держит в себе воздух, при этом внутри комнат создается свой особый климат. Также они способствуют естественному вентилированию и даже после оштукатуривания. Соломенные блоки имеют и высокую теплопроводность и энергоэффективность. Дом, построенный из такого материала, требует меньше чем 40 кВТ*ч/м2 в год. Что опять-таки при наличии счетчиков позволяет не беспокоиться о платежках. Кстати, об экономии. Как уже говорилось выше, соломенный блок имеет очень легкий вес (16-30 кг), что существенно сказывается и на выборе фундамента под застройку. Такие дома не нуждаются в монолитных основаниях.
http://ostroymaterialah.ru/www.youtube.com/watch?v=NUzkKrHGCYg
Самое интересное, что даже на уровне современного подорожания других стройматериалов такие блоки значительно в цене не прибавят. Значит, сильных финансовых утрат строительство не понесет. И конечно же, пару слов стоит сказать о пожарной безопасности. Оштукатуренный блок имеет высокие пожароустойчивые свойства. Поэтому такие дома и не боятся огня и пожаров.
Читайте также: Средняя плотность бетона
Подробнее о фракции щебня для бетона
Расход бетона — читайте здесь.
Соломобетонные блоки: изготовление своими руками
Глянул кадры из ESBG-2009, там парни закладывают в каркас блоки, а затем прессуют их домкратами.В связи с чем возникла идея, чтобы (при отсутствии соломы в блоках) прессовать солому прямо в каркасе. Монолитная солома :-)Можно закладывать блоки, предварительно подготовленные вручную (вернее, вножную, как на фотках выше).
По технологии возникает пара вопросов – перемещающиеся вверх по каркасу опалубка и упор для домкрата, а также перевязка. Она обязательна?
Немного поразмыслил.Упор для домкрата. Например, предварительно заготовленные бруски разной длины с шагом 50 см, упирающиеся в домкрат и горизонтальный элемент каркаса в перекрытии.Опалубка. Пара широких досок или сколоченные щиты.
Из стального прута делается две скобы, по ширине щитов, длиной – по толщине каркас+щиты, на концах скобы – петли. В петли продевается прут и таким образом фиксирует щит на другой стороне. Чтобы щиты не падали, подпирать можно чем угодно хоть палками, упертыми в кирпичи.Возможно, конструкция выходит немного неплотная, “гуляющая”, но, думается, что это не принципиально, т.
к. всё равно соломенная кладка перед отделкой постригается пилой, ножом, триммером, бензопилой. Обвязка в этом случае не принципиально. Она ведь для того, чтобы блоки не рассыпались при манипуляциях на пути от пресса до каркаса.
Ну а если принципиальна, то прошить уже запрессованую стену не проблема, веревка, прут и прошивай как угодно, можно сшить и по вертикали, и горизонтали (причем намертво к каркасу).
Опилкобетон – это одна из разновидностей легких бетонов, обладающих пониженной плотностью. Он был разработан в 60-х годах 20 века в Советском Союзе и прошел абсолютно все технические и качественные испытания, после чего был стандартизирован. Массовое применение в частном домостроении и потребительский спрос опилкобетон получил лишь в середине 90-х годов, после чего его уникальные свойства неизменно привлекают потребителей.
Главными преимущественными характеристиками этого стройматериала являются:
- экологическая безопасность;огнестойкость;прочность;массовое отношение влаги;паропроницаемость;теплотехнические показатели;морозостойкость;доступная стоимость материала.
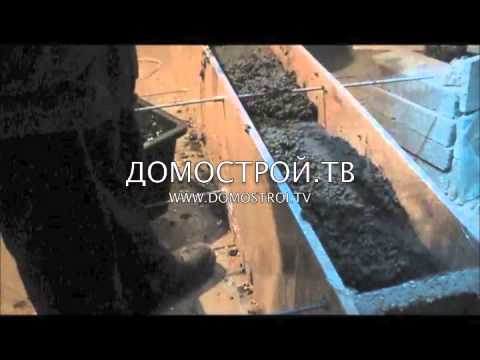
Содержание
- 1 Область применения опилкобетона
- 2 Состав опилкобетона
- 3 Изготовление опилкобетона своими руками
- 4 Производство блоков из опилкобетона
- 5 Преимущества использования арболитовых блоков
- 6 Технология изготовления арболитовых блоков
- 7 Предъявляемые требования
Область применения опилкобетона
Этот строительный материал широко применяется при строительстве домов, дач, коттеджей и хозяйственных построек. Он также используется при работах по утеплению подвалов и реконструкции зданий. При такой реконструкции не возникает необходимости в усилении фундамента.
Для строительства здания из опилкобетона подойдет любой проект, созданный для домов из других материалов. Однако затраты на строительство будут существенно ниже.
Дом, построенный из опилкобетона, достаточно легкий: при площади в 250 м2его вес составляет около 50 тонн. Это обстоятельство позволяет не закладывать сложный фундамент. Кроме этого есть еще множество преимуществ, среди которых можно назвать хорошую звукоизоляцию, простоту сборки, экологичность, экономичность, долгий срок эксплуатации.
Состав опилкобетона
Основой этого строительного материала, как понятно из названия, являются древесные опилки. Кроме этого, в состав входят песок, вяжущие материалы (песок, известь) и вода. Благодаря санитарно-гигиеническим показателям опилкобетон является одним из оптимальных материалов для возведения стен зданий.
Плотность стройматериала зависит от соотношения песка и опилок. Соответственно, плотность тем меньше, чем меньшее количество песка пошло на изготовление опилкобетона.
В этом случае улучшаются теплотехнические свойства, но уменьшается прочность материала. С увеличением количества песка и вяжущих материалов прочность возрастает. Также улучшаются морозостойкость и водонепроницаемость, что в свою очередь препятствует воздействию коррозии на стальную арматуру.
Такая арматура применяется при укладке стен из блоков, сделанных из опилкобетона. Поэтому, прежде чем приступать к изготовлению, необходимо четко знать свойства бетонируемой конструкции. Здесь не бывает мелочей, принимается в расчет толщина стен, количество этажей, наружная, внутренняя стена это будет или несущая конструкция.
В зависимости от состава, опилкобетон подразделяется на марки. Блоки марок М5 и М10 применяются для строительства, реконструкции и утепления подвалов, поскольку им свойственны прекрасные теплоизоляционные характеристики. Марки М15 и М20 наилучшим образом подходят для возведения как внутренних, так и наружных стен домов.
Марки и пропорции опилкобетона:
М5. На 200 кг опилок берется 50 кг цемента, 50 кг песка, 200 кг извести или глины. Плотность – 500 кг/м3.М10.
На 200 кг опилок берется 100 кг цемента, 200 кг песка, 150 кг извести или глины. Плотность – 650 кг/м3.М15. На 200 кг опилок берется 150 кг цемента, 350 кг песка, 100 кг извести или глины.
Плотность – 800 кг/м3.М20. На 200 кг опилок берется 200 кг цемента, 500 кг песка, 50 кг извести или глины. Плотность – 950 кг/м3.
Изготовление опилкобетона своими руками
Заготовка необходимых материалов.Компоненты, входящие в состав опилкобетона, хороши тем, что их не нужно заготавливать заранее. Все составляющие можно купить в магазинах, торгующих стройматериалами, на рынках или складах. Благодаря этому к заготовке можно приступить практически за один день до начала изготовления.
Смешивание компонентов.
Приготовление вручную опилкобетона является очень трудоемким процессом, поэтому для смешивания компонентов по возможности желательно использовать бетономешалку или растворосмеситель. Прежде всего, высушенные опилки необходимо просеять через сито, ячейки которого должны быть по размеру 10*10 миллиметров. Затем опилки смешиваются с песком и цементом.
После этого в приготовленную смесь добавляют глиняное или известняковое тесто и тщательно перемешивают. Получившуюся смесь разводят водой, постепенно добавляя ее в малых порциях через лейку. После каждого долива смесь необходимо перемешать.
Если смесь приготовлена правильно и хорошо перемешана, то при сжатии в кулаке она образует пластичный комок, на котором видны вмятины от пальцев, при отсутствии капель воды. Это является основным признаком готовности смеси.
После этого ее можно формировать в блоки. В этом деле медлить нельзя ни в коем случае, так как по истечении 1,5-2 часов смесь начинает твердеть. Укладывая смесь в форму, ее необходимо хорошо утрамбовать, чтобы исключить наличие воздуха.
Размеры блоков.Такие размеры стандартами не установлены. Они напрямую зависят от толщины стен, ширины простенков и проемов, расстояния от проемов до углов строения, а также от способа укладки. Для наибольшего удобства при строительстве длина участков стены или ширина простенков должны быть кратными блочным размерам.
Толщина блока обычно равняется двум толщинам красного кирпича, учитывая и уложенный между ними раствор. В общем, это составляет 140 миллиметров. Учитывая то, что при кладке часто используется и красный обожженный кирпич, такой подход является очень практичным.
Большие опилкобетонные блоки сохнут достаточно долго. Для ускорения процесса высыхания в них делают 2-3 отверстия, что не только позволяет блоку быстрее высохнуть, но и улучшает теплозащитные свойства этого стройматериала.
Формы для отливки.Наиболее оптимальным вариантом является возведение стен не при помощи опалубки, а из заранее подготовленных блоков.
Они высушиваются в течение трех месяцев, после чего опилкобетон приобретает свою марочную прочность. Перед тем, как начать приготовление смеси, изготавливаются формы для отливки блоков. Форму с опилкобетонного блока снимают не сразу, а по прошествии от трех до пяти дней.
Для ускорения процесса изготовления делают 10-20 форм. Таким образом, процесс не прервется, а также не потратится время на ожидание высыхания блоков. Количество форм напрямую зависит от того количества блоков, которое вы планируете изготовить за один раз.
Формы для габаритных блоков. Для крупных блоков изготавливаются разборные одинарные или двойные формы. Они выполняются в виде сбитых из досок ящиков.
Формы являются разъемными, что позволяет очень быстро их разбирать и собирать. Делаются они из досок, толщина которых составляет 20 миллиметров. Части разъемной конструкции скрепляются при помощи стальных стержней Г-образной формы, обладающих резьбой М8, на которую накручивается барашковая гайка.Формы для небольших блоков.
Для изготовления мелкогабаритных блоков изготавливаются в собранных из 20 миллиметровых досок сотовых формах. В основном такие формы делают для производства 9 блоков из опилкобетона одновременно. По желанию количество ячеек может варьироваться.
Эти формы, состоящие из внутренних и боковых досок, так же легко и быстро собираются и разбираются. Составляющие ячейки внутренние доски крепятся между собой при помощи задвижных пазов. Торцевые же доски прикрепляются к боковым стальными Г-образными стержнями и барашковыми гайками.
Внутренние стенки форм.Чтобы доски, из которых изготавливаются формы для отливки, не впитывали влагу, внутренние стенки обивают кровельной сталью, пластиком или прокладываются полиэтиленовой пленкой. Из формы, подготовленной таким образом, блоки вынимаются очень легко и просто, не приставая к деревянным стенкам.
Учитывая то, что при высыхании происходит усушка блоков, формы делаются немного больших размеров, чем должны получиться готовые блоки. Эта разница должна составлять приблизительно 10%:
- Для цельных блоков с размерами 120*250*140 мм (ширина*длина*высота) размер ящика должен быть 132*235*154 мм.Для блоков с размерами 190*390*140 мм размер ящика составляет 209*430*154 мм.Для блоков с размерами 130*410*140 мм размер формы должен быть 143*450*154 мм.
Производство блоков из опилкобетона
Деревянные формы, перед тем как заполнить их опилкобетонной смесью, устанавливают на поддоны, изготовленные из стали или пластика, предварительно посыпанные тонким слоем опилок. В форме располагают обернутые толем деревянные пробки, необходимые для получения сквозных отверстий.
После этого подготовленную смесь плотно укладывают в форму, трамбуя при этом специально изготовленной ручной трамбовкой. После проведения этих работ формы с опилкобетоном оставляют на 3-4 дня. В течение этого времени стройматериал приобретает прочность, процентная доля которой составляет 30-40 процентов от марочной.
По истечении указанного срока вынимают пробки и толь, сами формы разбирают, а блоки оставляют на том же месте еще на 3-4 дня, чтобы их прочность еще возросла.
Теперь она составляет 60-70% от марочной прочности. После этого блоки следует перенести под навес для последующей сушки. Для достижения лучшего результата необходимо соблюдать некоторые условия:
- опилкобетонные блоки при сушке лучше всего расположить на сквозняке. Так их сушка будет более равномерно осуществляться;при укладывании блоков для сушки оставляйте между ними зазоры;если нет навеса, то блоки необходимо укрыть полиэтиленовой пленкой в случае дождливой погоды.
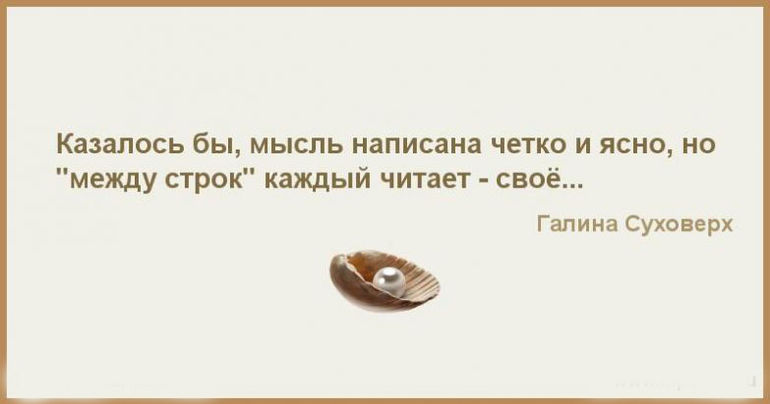
Для окончательной сушки из блоков сооружают столбы.
Это происходит так: на предварительно обожженные кирпичи укладывают два блока, на них располагают поперек еще два, затем поперек еще пару и так далее. Расположенные так, блоки окончательно просохнут и затвердеют. 90% прочность стройматериал приобретает уже через месяц, однако для достижения стопроцентной прочности потребуется три месяца.
Полностью готовые блоки очень прочны, тверды и не имеют трещин. Доказательством прочности стройматериала является то, что блок не разбивается при падении с высоты, достигающей 1 метра.
Арболитовые блоки — это материал, который активно используется в малоэтажном строительстве.
Если говорить о его составе, то он состоит из опилок (деревянной стружки) и цементного раствора обычно серии М-200, М-400. Говоря о истории арболитовых блоков, то их использование было реализовано еще в 1940 годах прошлого века, тогда множество заводов производили данные блоки и стоит отметить, что они пользовались большой популярностью не только для временного, но и для капитального жилья. Говоря о применении опилкобетонных блоков, то их целесообразно применять в малоэтажном строительстве или например при возведении дома на ленточном фундаменте.
Арболитовые блоки — образец
Преимущества использования арболитовых блоков
Опилкобетонные блоки обладают удивительными качествами во первых — это безусловно дешевый вид производства блоков для последующего строительства дома.
Во-вторых арболитовые блоки обладают хорошими теплоизоляционными качествами, да-да именно так, они прекрасно удерживают и аккумулируют тепло внутри дома. Третье преимущество — это легкость производства опилкобетонных блоков даже для начинающих строителей. И наконец к четвертому и пятому преимуществу можно отнести пожаробезопасность данного материла и его прочность и долговечность при соответствующем уровне соблюдения технологии.
Технология изготовления арболитовых блоков
Для, того чтобы блоки получились правильной формы и не разрушались под воздействием времени необходимо делать стружку от 3 до 15 см в длину и от 0,5 см до 2 см в ширину.
Разумеется сначала нам будет необходимо огромное количество деревянных опилок, процесс получения опилок может быть у всех разный, у кого-то они остаются после токарных работ, кто-то пропускает их через рубильную машину, кто-то заказывает опилки с лесопилок, но говоря о простом получении деревянной стружки советуем вам заехать на вашу местную лесопилку и договориться о покупке отходов (стружки) т. к обычно их все равно выкидывают или просто напросто сжигают.Вторым этапом после заготовки древесной стружки будет ее выдержка на улице — это придаст очищение стружки от сахара, который будет оказывать негативное влияние на ее состав, выдержка на уличных условиях производится около 40-80 дней при этом необходимо переворачивать и шарудить вашу кучу с опилками, чтобы воздух проникал и в нижние слои, а не задерживался на поверхности.
Кстати, чтобы был максимальный эффект кучу необходимо обильно поливать окисью кальция.После того, наш заготовочный материал отлежался на поверхности его необходимо пропустить через крупное сито — это избавит его от остатков земли и прочих органических материалов, которые будут служить разрушающим фактором при формировании блоков. Следующий шаг — это замачивание опилок водой с добавлением жидкого стекла, готовую смесь необходимо замешивать в специальной бетономешалке, но обратите внимание, что когда происходит замес он зависит от того, какую прочность арболитовым блокам вы хотите придать, в стандартном классическом применении используется пропорция — 1:2:6 то есть, на 1 мешок цемента приходится 2 мешка песка и 6 мешков опилок.Арболитовые блоки обладают малым весомОбратите внимание, что минусом строительства дома из опилкобетона является его подверженность крысиным и мышиным «атакам», но не отчаивайтесь существует несколько способов его защитить: первый это после возведения фундамента сделать бетонную заливку около — полуметра в высоту и второй способ — это залить прямо вплотную к арболитовым блокам обыкновенную сетку — рабицу, чтобы грызуны не имели доступа к нашим блокам.Процесс перемешивания раствора в бетономешалкеПосле того, как наш раствор готов, остается заключительная часть — это создание специальной формы арболитовых блоков.
Форма придается с помощью специального шаблона, который имеет форму прямоугольника. Кстати обратите внимание, что площадь внутри блока обшивается линолеумом,для того чтобы раствор не прилипал к стенкам блока.Форма для арболитовых блоковПосле того, как наш раствор залит в форму его нужно, как следует взболтать, для того чтобы участки не завоздушились по стенкам формы постепенно стучат молотком, а лучше проходят вибратором, что несомненно даст лучший эффект.
Арболитовые (опилкобетонные) блоки своими рукамиСсылка на основную публикацию
- Дата: 11-03-2015Просмотров: 326Комментариев: Рейтинг: 30
Сейчас очень многие стараются строить дома из экологически чистых материалов. Говоря о таковых, в голову сразу приходят мысли о древе. Но не стоит забывать и о той же самой глине или даже соломе.
Многие могут сказать, что солома — это прошлый век и это не надежно. Но благодаря современным технологиям такой материал приобрел не только качество, но и прочность. И если нет желания тратиться на него, то соломобетонные блоки своими руками тоже можно сделать.
Соломобетонные блоки являются дешевым, прочным и экологически чистым материалом.
Но для начала нужно разобраться, что это такое.
Такой материал выпускается в виде прямоугольных блоков. Блок имеет стандартную ширину (45 см) и высоту (35 см), а вот длина может варьироваться от 90 до 112 см. Весить такой блок может от 16 до 30 кг.
Чтобы такой материал сохранял свою форму, блоки обвязывают (а некоторые производители и прошивают) полипропиленовыми шнурами. В сельскохозяйственных сферах такие блоки собираются в единое целое при помощи проволок или натуральных волокон. Но эти крепления подходят для хранения соломы, а никак не для построек.
Ведь сама проволока железная, а железо имеет свойство ржаветь. А волокно по прошествии времени теряет свою прочность из-за гниения. Солома тоже бывает нескольких видов, поэтому для постройки лучше применять ржаную или рисовую.
Они обладают оптимальными свойствами. Если останавливать свой выбор на первом варианте, то лучше, если она будет озимая. Такая солома имеет более плотную структуру.
Предъявляемые требования
Есть определенные требования к соломенным блокам, а именно:
Схема бескаркасной стены из соломенных блоков.
Сухость.
Влага, скопленная внутри, будет провоцировать гниение. Кстати, именно сухие блоки такие легкие, и если они имеют значительный вес, то есть вероятность, что солома была не доброкачественно просушена. Если ощущается запах гнили или пальцами чувствуется влажность, то такой материал некачественный.Качество соломы.
Стебли должны быть гибкими и крепкими. Если при сгибании он не ломается, то это качественный блок. В обратном же случае такой материал быстро рассыпется.Качественный пресс.
Если соблюдалась правильная технология спрессовывания блока, то он не должен терять своей формы. Для этого можно попробовать просунуть под шнур пальцы, если больше 3х пальцев не помещается, то это качественный пресс.Одинаковые размеры.Вся партия должна быть идентичной. Если блоки разнятся по размерам между собой, то лучше отказаться от применения данного материала и найти другого производителя.
Вернуться к оглавлению
Когда вы делаете что-либо своими руками, всегда возникает огромный плюс — экономия средств. К тому же при собственноручном изготовлении всегда можно быть уверенным в качестве применяемых материалов. То же самое относится и к блокам из соломы и бетона.
Цемент компонируется соломой не только по причине придания прочности.Он помогает органическим веществам соломы преобразоваться в сахар, который легко растворяется водой. Но такие преобразования мешают соломенному блоку отвердеть. Для того чтобы устранить такой отрицательный эффект, применяются физические и химические способы.
Схема перекрытия из соломобетонных блоков.
Первое, что используют — окисление. Для этого блоки выносят на открытые солнечные лучи, под воздействием которых происходит окисление веществ, и они начинают впитываться в стенки древесных клеток.
В то же время часть других веществ при взаимодействии с бактериями преобразуется в кристаллы и в дальнейшем образует нерастворимые формы. Но для того чтоб все это произошло на надлежащем уровне, необходимо очень много времени. Второй способ — вымачивание водой.
Если блок оставить под дождем на длительное время, то практически все водорастворимые вещества выйдут из него. С этой целью используют и специальные емкости. Но опять-таки для того чтобы обработать всю партию соломенных блоков, требуется значительное время.
Самым распространенным на сегодняшний день способом является обработка растворами хлористого кальция или жидкого стекла. В среднем их надо около 9 кг на метр кубический. Эта технология популярна по ряду причин:
Благодаря жидкому компоненту стекла и хлористому кальцию изделие быстро затвердевает.
Но если сравнивать прочность готовых блоков обеих марок, вторые этот показатель имеют намного выше, чем первые. Если применять кальций, то следует знать, что лучше всего использовать выдержанную солому. А вот для применения жидкого стекла порода соломы особой роли не играет.Используя такие добавки, при условии, что средняя температура окружающей среды будет 20 градусов тепла, такие блоки уже через 24 четыре часа можно складывать, а через 7 дней применять и для строительства.
Есть рекомендуемый расход для изготовления блоков, ориентированный на объемный вес компонентов (кг/м3):
Сравнение теплопроводности соломобетонных блоков с другими материалами.
- цемента — 1700;гашеной извести — 600;песка — 1550;соломы — 80-105.
А вот на расход воды влияют несколько моментов:
- какая необходима вязкость замеса и заполнителя;марка бетонного раствора;показатель исходной влажности соломы.
Такие пропорции позволят создать блок с показателем прочности М-10.
Некоторые строители заменяют бетон на глину. Изначально они рубят солому на куски (0,5 м), после чего замачивают ее в глиняном растворе. И опять-таки полученный материал прессуется.
Сам блок формируется при помощи киповальной машины.
Ее можно соорудить и самому, а можно обратиться к профессиональным киповальщикам или взять пресс в аренду. Если же все-таки решено обращаться за помощью, следует знать, что качество соломы во многом зависит и от того, как ее собирали и хранили.
Немаловажным моментом является и ее помол, ведь если ее трубчатая структура будет нарушена, то такой материал потеряет все свои свойства. Сейчас солому чаще продают в виде рулонов, что слегка удлинит процесс. Ведь такие рулоны придется заново раскатать и перекиповать.
А это может привести к нарушению изначальной структуры соломы. Но каждый сам выбирает, как ему удобно. Нельзя забывать и том, что готовые соломенные блоки пропитываются специальными химическими составами, которые значительно влияют на их прочностные характеристики.
Вернуться к оглавлению
Стройка загородного дома — это всегда какие-то проблемы, связанные то с работой, то с финансами. Но вот применение соломенных блоков помогает решить некоторые негативные моменты в строительстве.
А все потому, что они имеют ряд своих особенностей.
Низкая себестоимость. В основном солома — это отходы в сельском хозяйстве.
Поэтому приобрести ее не составит особого труда. Единственное, на что придется потратиться, это на перевоз такого материала. Но если на ферме, где приобреталась солома, есть киповальная машина, то везти ее никуда не надо будет.Низкая теплопроводность.
Постройки из такого материала не требуют дополнительного утепления. Нет проблем и с отделочными работами, ведь, имея шероховатую поверхность, материал отлично «цепляет» к себе любые покрытия.Но также следует отметить, что все-таки соломеннобетонные блоки имеют определенную «мягкость», поэтому на них не кладутся плиты перекрытий, так как это приводит к деформации. Это является основной причиной, почему такой материал применяется для построек только каркасных домов.
Вернуться к оглавлению
Материал имеет ряд положительных моментов, из-за которых его и применяют в современном строительстве:
Благодаря небольшому весу и крупным габаритам соломенных блоков, строительство идет очень быстро.
Дешевизна и доступность материала. В наших широтах проблем с соломой не возникает, в любом колхозе ее достаточно.Экологически чистый материал.
Если солома росла на полях не в радиационной зоне и не обрабатывалась вредными веществами, то такая постройка будет иметь благоприятное воздействие и на здоровье жильцов, и на саму окружающую среду. Легкий вес. Благодаря этой характеристике строительство идет очень быстро. В зависимости от проекта, одноэтажную постройку можно завершить в сроки от двух недель до двух месяцев.Форма материала.
Так как во время производства такого блока используется пресс, то даже несмотря на наличие соломы внутри, грызуны не обустроят себе дом в стенах. Еще одним из моментов, которые влияют на популярность такого строительства, является экономия строительных ресурсов и энергии, а также сама эксплуатация такой постройки.
Несмотря на несерьезность материала, соломенные блоки имеют долгие сроки службы. Но это при условии, что они прошли правильную техническую обработку. Только в таком случае есть гарантия, что они не рассыпятся, не деформируются и не поддадутся гниению.
Даже если такой материал сравнить с древесиной, то второй вариант уступает по параметру насыщения помещения кислородом. Трубчатая структура соломенных волокон отлично держит в себе воздух, при этом внутри комнат создается свой особый климат. Также они способствуют естественному вентилированию и даже после оштукатуривания.
Соломенные блоки имеют и высокую теплопроводность и энергоэффективность. Дом, построенный из такого материала, требует меньше чем 40 кВТ*ч/м2 в год. Что опять-таки при наличии счетчиков позволяет не беспокоиться о платежках.
Кстати, об экономии. Как уже говорилось выше, соломенный блок имеет очень легкий вес (16-30 кг), что существенно сказывается и на выборе фундамента под застройку. Такие дома не нуждаются в монолитных основаниях.
Самое интересное, что даже на уровне современного подорожания других стройматериалов такие блоки значительно в цене не прибавят. Значит, сильных финансовых утрат строительство не понесет.
И конечно же, пару слов стоит сказать о пожарной безопасности. Оштукатуренный блок имеет высокие пожароустойчивые свойства. Поэтому такие дома и не боятся огня и пожаров.
Источники:
- straw.z42.ru
- sekretystroyki.ru
- stroyvopros.
net
- ostroymaterialah.ru
Почему цемент никогда не следует использовать в естественных постройках
Опубликовано 10 февраля 2016 г.
Меня часто просят помочь с дизайном других людей, но один из моих принципов — никогда не проектировать из цемента. Не все знают это обо мне, и недавно меня спросили, каков мой общий опыт работы со стволовыми стенами из бетона (цемент плюс заполнитель), что нужно учитывать или возможные проблемы при строительстве на них соломенных тюков. Далее мой клиент сказал: «Большинство производителей соломенных тюков или компаний по строительству тюков соломы, которые я видел в Интернете, используют бетон для своих стволовых стен!? Значит, это работает?»
Хммм. То, что большинство людей что-то делают, не означает, что это работает или это хорошая идея. Тем не менее, это подчеркивает одну из основных проблем с цементом: проблемы, которые он вызывает, не видны или очевидны сразу, на самом деле они могут проявиться через много лет. Я сам был обучен использованию современных материалов и методов в рамках своего обучения в строительной отрасли, и я думал, как и большинство людей, что фундаменты должны быть сделаны из цемента, а кирпичи должны быть уложены с помощью цементного раствора. Так что я знаю, как класть цементные полы и строить кирпичные и каменные стены, и многое сделал в свое время — но все, к счастью, теперь уже давно.
Когда я начал изучать природные материалы в 1990-х годах, а также строительство из соломенных тюков, я изучал известковые и глиняные штукатурки, а также строительство из самана. У меня тоже был интерес к старым домам, и я понял, что все наши старые дома (построенные до 1900 года) построены полностью из натуральных материалов, да и все старые дома во всем мире тоже. Это показывает, насколько невероятно, что кто-то может думать, что натуральные материалы недолговечны, но мы все склонны думать, что то, что все делают сейчас, лучше, чем то, что люди делали в прошлом. Существует распространенное заблуждение, что цемент заменил известь и глину, потому что он лучше справляется со своей задачей, но я отвлекся…
Основная проблема с цементом и бетоном заключается в том, что они притягивают или «впитывают» воду. Если вы поместите бетонный блок в воду на дюйм и оставите его на пару дней, весь блок промокнет. Если вы поместите кусок дерева (или тюк соломы) в воду на дюйм, они оба станут мокрыми до уровня чуть выше дюйма, но не более. Они не впитывают воду. Таким образом, использование цемента для строительных растворов и штукатурок означает, что во время дождя цемент переносит влагу через себя к тому, что находится за ним. Обычно, когда дождь прекращается, большая часть этого снова высыхает, но не все, и не во влажных условиях или там, где большую часть времени присутствует влага. Вот почему цемент никогда не следует использовать в естественных постройках.
В цементных фундаментах цемент находится в контакте с влажной землей, поэтому стандартная практика заключается в защите вышележащего здания от влажного цемента с помощью гидроизоляционного слоя. Что еще более важно, внешние стены всегда содержат определенное количество влаги из-за внешнего дождя и внутреннего присутствия (горячий душ, приготовление пищи и т. д.). В зданиях, построенных из цементных растворов, эта влажность увеличивается, так как дождь проникает через растворные швы. Эта влага всегда движется вниз из-за гравитации и заканчивается у основания стены. Опять же, стандартной практикой является использование влагонепроницаемого слоя полого поддона, чтобы направить внутреннюю влагу наружу здания. Основная причина, по которой люди не осознают, что цемент на самом деле увеличивает влажность здания, заключается в том, что движение влаги происходит очень медленно. Может пройти 30 или 40 лет, прежде чем начнут проявляться проблемы, которые примут форму влаги, скопившейся у основания стены, что в конечном итоге проявится как проблемы с влажностью внутри.
Когда эти проблемы из-за использования цемента впервые начали проявляться, в промышленности заявили, что это вызвано повышением влажности, и была изобретена химическая инъекция домов против сырости. На самом деле теперь мы знаем, что поднимающаяся влажность встречается очень редко, и большинство проблем с сыростью вызвано другими причинами. У Общества защиты древних зданий (SPAB) есть отличные исследования и информация по этому вопросу. См. http://www.spab.org.uk/advice/technical-qas/technical-qa-20-rising-damp/ 9.0009
Еще одна начавшаяся тенденция заключалась в том, чтобы перекрашивать дома из цемента, которые были построены с использованием извести, и ремонтировать старые известковые штукатурки с помощью цементных штукатурок. Никто не знал, что это была грубая ошибка в течение многих лет, потому что проблемы, которые она вызвала, проявлялись очень долго. Только после впечатляющего обрушения нескольких глинобитных зданий, которые были заштукатурены цементом, мы начали понимать, что цемент повреждает наши здания, особенно старые, построенные из природных материалов. Опять же, печальный показатель того, почему цемент никогда не следует использовать в естественных постройках. Сегодня по этой причине организация English Heritage запретила использование цемента в зданиях наследия.
Многие современные здания страдают от проблем с конденсацией, и это является прямым результатом использования цементных блоков, растворов и гипсокартона, хотя это также связано с другим их свойством, а именно непроницаемостью, они препятствуют прохождению пара. Эта непроницаемость является еще одной причиной, по которой цемент никогда не следует использовать в естественных постройках. С другой стороны, известь и глина фактически регулируют влажность и могут удерживать избыточную влагу внутри себя, не становясь «мокрыми», и высвобождать ее при снижении уровня влажности — они гигроскопичны. Это также помогает поддерживать здоровое качество воздуха в помещении. Известь, используемая в качестве раствора или штукатурки снаружи, поглощает воду, когда идет дождь, и, когда она становится насыщенной, это фактически предотвращает проникновение влаги через нее и, таким образом, защищает здание позади нее. Когда дождь прекращается, эта влага выбрасывается в атмосферу.
Итак, я возвращаюсь к вопросу моего клиента. Тот факт, что так много людей используют цемент, не означает, что он «работает»! Это просто означает отсутствие осознания. Большинство людей не проектируют жизнь на 200 лет, как мы. Мы видим, что дома, построенные в 1970-х годах (из цемента), сносят и признают непригодными для проживания, в то время как дома, построенные в викторианскую эпоху или ранее (цемент стал широко использоваться в строительстве после Первой мировой войны), разрушаются. отремонтирован (о нет, часто с цементом) и продолжает служить хорошо… до тех пор, пока последствия новой гипсовой штукатурки или цемента не начнут вызывать проблемы с влажностью или конденсацией.
Наконец, есть много способов построить фундамент, не требующий цемента. Все наши старые дома имеют фундаменты без цемента — как же иначе? Я разработал несколько типов фундаментов, которые не требуют цемента, они доступны для использования на нашем сайте в разделе «Бесплатная информация». Все эти проекты являются законными, одобрены планировщиками и соответствуют действующим строительным нормам.
Всем рекомендую начать разбираться в чудесах извести и глины. Я ожидаю, что если вы, как и я, захотите стать Строителем Природы!
Если вы хотите узнать больше о цементе и причинах проблем, с которыми он сталкивается, вот три сообщения в блоге, которые я бы порекомендовал:
http://surveyingproperty.blogspot.co.uk/2014/11/concrete- part-1-understanding-basics.html#.VGyGQvmsWxI
http://surveyingproperty.blogspot.co.uk/2014/11/concrete-part-2-carbonation.html#.VGyGWfmsWxI
http://surveyingproperty. blogspot.co.uk/2014/11/cohttp://surveyingproperty.blogspot.co.uk/2014/11/concrete-part-3-understanding-basics.html#.VGyGb_msWxIncrete-part-3-understanding-basics.html #.VGyGb_msWxI
Спасибо Оливеру из Naturalhomes.org за изображение.
Хотите узнать больше о строительстве из тюков соломы от Барбары Джонс?
Барбара Джонс — звезда нашего онлайн-курса по строительству из соломенных тюков. Курс содержит ряд документов и видео, охватывающих все аспекты строительства из соломенных тюков, от фундамента, стен и крыш до инструментов, внутренней отделки и штукатурки, с множеством советов и внутренней информации. Пожизненный доступ всего за 30 фунтов стерлингов. На сегодняшний день это наш самый популярный онлайн-курс.
Мнения, выраженные в нашем блоге, принадлежат автору и не обязательно принадлежат lowimpact.org.
Почему «утрамбованная земля» не содержит цемента
Смена карьеры: как я бросил разработку программного обеспечения, чтобы стать естественным строителем
Если ваш дом не старый, у вас, вероятно, нет восходящей сырости, а если она есть, то современные методы защиты от влаги, вероятно, не сработают.
Можете ли вы принять природного строителя на 3 ночи в обмен на бесплатный VIP-билет в Ecobuild?
Хотите помочь построить 9м с разворотом с ответной, дерновой крышей для благотворительной организации «Фермы для городских детей»?
Сиги Коко об основах пассивного солнечного дизайна
Просьба о помощи в строительстве ответной развязки для экологической благотворительности: отличная возможность обучения, и это бесплатно
Clayfest, 12-17 июня: давайте строить больше домов из земли, а не из кирпича и цемента
Лагеря общественного строительства: станьте волонтером в общественных проектах и приобретите естественные строительные навыки.
Как сделать японского гипсового ястреба для штукатурки из глины
Выходящий на юг дом с утрамбованной землей и утеплением из соломенных тюков не нуждается в отоплении; почему не все новые дома так строят?
Европейское собрание соломенных тюков пройдет в 2019 году в Йоркшире.Как новые дома из соломенных тюков могут помочь решить жилищный кризис
Фундаменты для автомобильных шин: малоударное и доступное решение?
Похожие темы
Глиняно-земляные штукатурки
Самодельное здание
сделай сам
Укрытые от земли дома
Здание из мешков с землей
Земляные полы
Конопляное здание
Лайм
Здание с низким уровнем воздействия
Грядет авария – пощечина Матери-природы. Это не пессимистично; это реалистично.
Воздействие человека на природу и друг на друга ускоряется и требует системных изменений, чтобы обратить его вспять.
Мы не пропагандируем нищету или власяницу. Мы выступаем за изменения, которые будут означать лучшую жизнь почти для всех.
Последние комментарии
Я провел много вечеров в походах, используя одиночную печь друзей — это небольшой газификатор размером с жестяную банку, и когда он хорошо накормлен…
Здравствуйте, у меня еще вопрос по поводу использования ракетной печи в помещении для приготовления пищи, в экстренных случаях.
У меня есть Solo Stove, которым я пользовался…Хм… Я думаю, ты все-таки был прав; наш топорик нужно периодически затачивать, чтобы мы могли продолжать безопасно его использовать.
Я…
сбор средств
Будьте в курсе
Подписка на рассылку новостей временно отключена
Lowimpact.org — это рабочий кооператив. Зарегистрирован в Англии. Номер компании: 4205021
Все права защищены © lowimpact 2022
Толстостенные методы строительства — Строители Semmes & Co. — Соломенные тюки — Утрамбованная земля — Бетонные опалубки с теплоизоляцией PISE
Наши специальности
Несмотря на то, что каркас из дерева может быть эффективным дизайнерским решением, у нас есть много других выдающихся методов строительства отточенный годами. Каждый материал представляет свои сильные стороны и проблемы.
Строение из тюков соломы
Строительство из тюков соломы – это многовековая технология, которая была возрождена в последние десятилетия людьми, которым нужна здоровая и экологичная альтернатива деревянному каркасному строительству. Этот метод толстостенной конструкции может втрое или вчетверо увеличить теплоизоляционные свойства экономичным и красивым способом. В сочетании с пассивной солнечной энергией этот метод строительства практически исключает расходы на отопление и охлаждение, а также имеет много других преимуществ.
Конструкция из соломенных тюков является естественным дополнением к пассивному солнечному энергосберегающему дому. Толстые стены добавляют компонент изоляции и массы, которые трудно получить в здании с деревянным каркасом. Хорошо спроектированный дом из соломенных тюков сохраняет прохладу в самые жаркие летние дни без кондиционера и исключительно экономичен при обогреве зимой.
Semmes & Co. Builders, Inc. использует рисовую солому (отходы сельского хозяйства Калифорнии), которая имеет высокое содержание кремнезема, что делает ее устойчивой к гниению и термитам. Штукатурка с высоким содержанием извести также используется для герметизации стен, поскольку она «дышит», позволяя влаге выходить изнутри стен и блокируя воду снаружи. Сейсмические исследования доказали, что конструкция из тюков соломы очень хорошо работает при землетрясениях. Стеновая система на бетонной основе также действует как антипирен, что является важным фактором в зонах с высокой пожароопасностью.
Эти красивые стены подходят как для Старого Света, так и для современного стиля. Стена из тюков соломы может быть построена относительно просто, что способствует участию домовладельцев и сообщества. Мы проводим мастер-классы по сборке соломенных тюков в большинстве построенных нами домов, приглашая друзей владельцев, а также местных жителей принять участие в праздничном мероприятии по укладке соломенных тюков. Приходите на один из наших семинаров по строительству соломенных тюков, чтобы узнать о технике и принять участие в строительстве натурального дома!
Утрамбованная земля
В методе утрамбованной земли используется смесь земли и цемента, но эта смесь уплотняется в двухстороннем виде. Используя местные материалы с минимальным углеродным следом, мы добавляем стальную арматуру для создания красивых несущих стен. Эти стены обеспечивают тепловую массу, которая стабилизирует внутреннюю температуру, становится источником тепла зимой и сохраняет прохладу летом. Текстура отделки более гладкая, чем у PISE, а утрамбованные земляные стены имеют больше внешнего вида и «зернистости» древнего осадочного песчаника. После того, как стены завершены, деревянные опалубочные материалы используются для обшивки крыши для экономии материалов.
PISE
Стабилизированный грунт с пневматическим ударом (PISE) использует одностороннюю опалубку и метод наложения под высоким давлением. Обученные бригады могут возвести до 1200 кв. футов стен толщиной 18 дюймов за один день. Цемент смешивают с землей (желательно с участка) и отбивают в плоскую форму, обрезают с одной стороны и оставляют застывать. Когда плоская фанерная форма удаляется и сохраняется для повторного использования, в результате получается красивая, законченная стена из натуральной земли с цветом и ощущением родной почвы. Преимущества этой техники включают термическую массу и использование местных материалов.
Отскок, собранный из брызг, уплотняется, как утрамбованная земля, в большие блоки, которые позже используются для ландшафтного дизайна. При таком методе строительства практически нет отходов. Какие бы отходы ни были, они возвращаются в землю.
«Жить в зданиях с толстыми земляными стенами есть какое-то волшебство… Здесь тихо, кажется невероятно прочным и прочным… даже вне времени». – Дом из утрамбованной земли Дэвида Истона
Залитый бетон
Нынешняя современная эстетика, а также забота об огнестойкости делают эту форму конструкции очень востребованной в нашем районе. Конечный вид может быть гладким, в форме доски или какой-то промежуточной адаптацией. У нас есть методы эффективного добавления изоляции в стены, когда это необходимо для удовлетворения энергетических требований Калифорнии. Кроме того, мы используем смесь с высоким содержанием летучей золы, чтобы компенсировать воплощенную энергию цемента, необходимую для традиционного бетона.
Кирпичные блоки
Бетонные блоки местного производства представляют собой огнеупорный строительный материал, устойчивый к гниению и вредителям. Детали утопленного окна внутри и/или снаружи оживляют детали дома, а масса может усилить пассивные солнечные элементы дизайна. Сейчас мы также работаем с блоком Watershed, еще более плотной кладочной единицей, в которой больше цемента замещается земляным материалом, что делает дом еще более устойчивым.
Утепленные бетонные опалубки
Строительство с утепленными бетонными опалубками (ICF) — это метод возведения стен, в котором используются предварительно изготовленные, легкие, блокирующие полистироловые блоки, заполненные железобетоном. Этот материал может создать длинную толстую стену, прямую и ровную, которая будет стоять в течение нескольких поколений.
Эта система обеспечивает структурную целостность, энергоэффективность, значительное снижение уровня шума и пожаробезопасность. Это отличный способ получить высокий уровень изоляции вместе с тепловой массой, а также устойчивость к землетрясениям, термитам и плесени. ICF можно использовать для наружных стен в пассивном солнечном здании, но не использовать для тепловой массы в пассивном солнечном дизайне. Эти стены обычно имеют толщину около 12 дюймов, обеспечивая привлекательную глубину и исключительную звукоизоляцию. Практически любая отделка может быть применена к внутренней или внешней части этого участка стены с помощью традиционных креплений. Результаты могут варьироваться от тонкого, причудливого сайдинга до лепного шедевра, напоминающего о старой архитектуре.
Структурно-изолированные панели
Структурно-изолированные панели (SIP) представляют собой промышленные панели, используемые для полов, стен и крыш. Из этих панелей, прикрепленных к вертикальным стойкам, можно построить целые конструкции. Панели бывают толщиной от 4 до 12 дюймов и обеспечивают теплоизоляцию до R-5,5 на дюйм*. Сердцевина из вспененного полистирола (EPS) зажата между двумя листами OSB или фанеры, заготавливаемой экологически безопасным способом, что придает этой «композитной» конструкции значительную прочность на сдвиг.